Дәріс. Қобылау. Соғудың технологиялық үрдісін жасау
Қобылау.Қобылау деп негізгі ұсталық операцияны айтады. Ол арқылы дайындамада тесікті алады. Қобылау үшін тұтас және қуысты қобылағыш қолданылады (19 және 20 суреттер). Қобылағыштың диаметрін дайындаманың сыртқы диаметрінің 0,3 – 0,5–не тең етіп таңдайды. Дайындаманы қобылау үшін оны 180 0 бұрмай бір жағынан жүргізуге болады. Ондай қобылау үшін сақинаны қолданады.
|
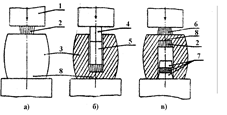
Қобылау дайындаманың түрін өзгертумен және жұлынғы ретінде металдың қалдығымен қошталады.
Қобылаудың алдында дайындаманы шөктіреді. Шөктірген кезде қобылағышты дәл қою үшін бүйіржағын тегістейді.
|
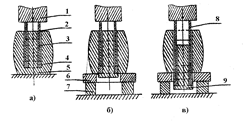
Қобылау операциясында майлайтын материалдарды қолданады (қарамай немесе машина майының графитпен қоспасы, ұнтақ тәрізді графит немесе графитпен кокстың қосындысы). Майлайтын материалды жағу үшін кобылағышты металға 10 – 30 мм тереңдікке басып еңгізеді. Пайда болған үңгілтте майлайтын материалды орналастырады, содан кейін ары қарай қобылағышты басып еңгізеді.
Ірі соғылмаларда далдашаның соңғы қалыңдығы h = 150 – 170 мм болады. Тұтас қобылағышпен өтпелі тесікті алу үшін қобылауды толық жүргізбейді. Өйткені күш тез үлкейеді. Бірақта h – ті 50 – 60 мм дейін жеткізуге болады. Содан кейін дайындаманы 180 0 аударады, жалғамаларды шығарады және бірінші қобылағышпен салыстырғанда диаметрі бірнеше есе кіші қобылағышпен өтпелі тесікті жасайды. Тескенде жұлынғы пайда болады. Дайындамаға қабылағышты ені үлкен бүйір жағымен қояды. Өтпелі тесік жасайтын қобылағыштың дұрыс центрленуін далдашаның қараюымен және бүйіржағының ісінуімен тексеруге болады. Осы уақытта бірінші қобылағышты алып тастайды. Нашар қасиеті бар дайындаманың бөлімін жұлынғыға кетіру үшін тұтас қобылағышпен дайындаманы аударып қобылаған кезде қосылма бөлімін бастапқы уақытта төмен қаратып қояды.
Қуысты қобылағышпен қобылауды (19- сурет) диаметрі бойынша үлкен тесіктерді алу үшін (диаметрі >500 мм) және құймакесектің ортаңғы ликвация бөлімін кетіру үшін қолданады.
Қуысты қобылағышты қолдану қобылау күшін тез азайтады.
Терең қобылау қуысты жалғамамен жүргізіледі. Жалғаманың диаметрі дайындама тесігінің диаметрінен 15 – 30 мм үлкен болады, ал жалғаманың ішкі диаметрі қобылағыштың сыртқы диаметрінен 10 – 15 мм үлкен болады.
Қуысты қобылағышпен қобылау тұтас қобылағышпен қобылау сияқты түбінің қалыңдығы 100 – 150 мм–ге жеткенге дейін жүреді. Осыдан кейін дайындаманы қобылаумен және жалғамен бірге сақинаға қояды.Сақина тесігінің диаметрін қобылағыштың диаметрінен 30 – 40 мм үлкен етіп таңдайды.Қобылаудан кейін алдымен дайындаманы жұккөтергішпен түсіреді, содан кейін жалғаманы алады.
Қобылаудың алдында қобылағышты 150 0С дейін қыздыру керек. Қыздыру қо-былағышты жарылаудан сақтайды. Қобылаудан кейін қобылағышты бірдей етіп ауада суыту үшін тұғыртыққа орналастыру керек.
Ірі дайындаманы қобылағанда оны қолайлы қозғалту үшін қобылауды тесігі бар тақтада жасауға болады. Тақтаның тесігіне бастапқы уақытта төрткілшені қояды. Ішпегі бар тақтада дайындаманы шөктіріп және қобылағаннан кейін тақтаны дайындамамен бірге жүккөтергішпен көтереді, ал ішпек үстелде қалады. Содан кейін үстелді ішпекпен бірге дайындамасы бар тақтаның астынан шығарады да тақтаны төмен түсіреді. Енді тақтадағы тесік ашық болады және баспақ жалғаманы және қуысты қобылағашты басқанда жұлынғы дайындамадан толық бөлінеді.
Төсем сақинада қобылауды (21-сурет) негізінен биіктігі салыстырмалы аласа дайындамаларға (Н/D = 1/3 – 1/4) қолданады. Дайындаманы сақинаға орналастырады. Оған қобылағышты үлкен диаметрімен төмен қояды. Сақинаның тесігінің диаметрі қобылағыштың диаметріне бірнеше рет үлкен болуы керек. Жоғарғы соққышпен қобылағышты сақинаның тесігіне жұлынғы құлағанша басып енгізіледі. Бұндай жағдайда қобылағыштың биіктігін дайындаманың қалыңдығынан үлкен етіп алады. Бастапқы уақытта металға қобылағыш кіреді, ал содан кейін қиық пайда болады. Тұтас қобылағышпен қобылағанға қарағанда жұлынғы қалдығы көп болады. Бірақта өлшемнің бұрмалануы аз болады. Сақина және қобылағыштың осьтестігін қөзбен, белгілеу бойынша және айлабұйымның көмегімен анықтайды.
|
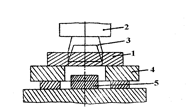
Соғудың технологиялық үрдісін жасау.Соғудың технологиялық үрдісі нақтылы жағдай негізінде және еңбектің алдыңғы әдістерін қолданып, осы өндірістің нақтылы мүмкіншілігіне байланысты жасалады.
Соғылманы дайындаудың технологиялық үрдісін жасағанда соғу операциясының тізбегі және оны таңдау, соғылманың түрімен анықталады. Соғылманың түрі күрделі болған сайын, оны дайындау күрделі болады.
Ұсталық соғумен жасалынатын соғылмалар тоғыз топқа бөлінген. Топтар соғылманы дайындаудың күрделігін ескеріліп орналастырылған.
Бірінші топқа ұзартумен жасалынатын түрі жай соғылмалар кіреді. Түрі ең күрделі соғылмалар типі (ернемегі бар қосиінді біліктер, қисық сызықты иінтіректер және т.б.) тоғызыншы топты құрайды. Осы топтың соғылмаларын жасау үшін біраз ұсталық операциялар және әр түрлі технологиялық құрал-саймандар қолданылады.
Жасалынған технологиялық үрдіс технологиялық карта деп аталынатын техникалық құжат түрінде дайындалады. Технологиялық үрдісті жасаған кезде соғылманың сериялығын, тетіктің қаншалықты керектілігі ескеріледі. Осы мәліметтер арнайы технологиялық жабдықтарды жасаудың орынды екендігіне әсер етеді.
Соғудың технологиялық үрдісін жасау мынандай негізгі бөлімдерге бөлініп кетеді: соғылманың сызбасын жасау және оның массасын анықтау; дайындаманың өлшемін есептеу (шөктеу мөлшерін ескеріп) және оның массасын анықтау; бастапқы металды таңдау; өңдеудің жылу режимін белгілеу; соғу операциясын және оларды орындау тізбегін таңдау; жабдықты таңдау; жұмысшы бригаданың құрамын және өндіру мөлшерін белгілеу; техникалық жағдайды және соғылманың сапасын тексеру туралы ережені белгілеу.
Соғылманың сызбасын құрылымдаушы жасаған дайын тетіктің сызбасын негізге алып технолог жасайды. Кесумен өңделетін соғылмалар дайын тетіктерден әдіп және кенермемен айырмашылықта болады. Соғылманың сызбасын жасаған кезде өлшемдерге тағыда шақтаманы белгілейді. Соғылманың сызбасын дайындаған кезде құрылым құжаттамасының бірыңғай жүйесі (ҚҚБЖ) талабын басшылыққа алады.
Өлшем аймағындағы терминологиялар оқулық [6] келтірілген.
Шекті ауытқу ескерілген соғылманың сыртқы өлшемінің сұлбасы 22, а суретте көрсетілген.
Қосылу (d1) («+» белгісімен белгіленген) және алыну (d2) («-» белгісімен белгіленген) ауытқулары сұлбада көрсетілген. Симметриялық ауытқулар үшін d1 = d2. Басқа варианттарда болуы мүмкін, мысалы: d1 < d2 және керісінше d1 > d2 немесе d2 = 0. Соңғы жағдай үшін қосылу ауытқулары d1 шақтамаға тең. Алынатын жоңқаның әдіпі (ақаулы қабатты кетіру) және соғудың дәлсіздік шақтамасы ескерілген жонумен өңделетін соғылманың сыртқы өлшемінің сұлбасы 22, б суретте берілген. Сызықтап тасталған бөлім соғылманың бір жағындағы әдіптің ең аз мөлшері болып саналады (0,5 ).
|
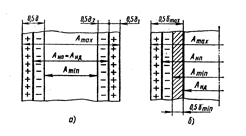
Мүмкін болатын ауытқудың салдарынан (соғылманы номиналды өлшемі бойынша дәл жасау мүмкін емес) соғылманың бір жағындағы ең үлкен әдіптің мөлшері 0,5 болады. Жонумен өндеуді талап етпейтін соғылмалар үшін олардың және тетіктің номинальды өлшемдері бірдей екендігі сыртқы өлшемнің сүлбесінен (22, а сурет) көрініп тұр (Анп = Анд). Жонумен өнделетін соғылмалар үшін соғылманың және тетіктің номинальды өлшемдері әр түрлі болады (Анп > Анд). Әдіп және шақтаманың өлшемдері мынандай факторлармен байланысты болады: тетіктің өлшемі және құрама пішіні; соғылманы жасау әдісі; ұсталық жабдықтың жұмыс істеу дәлдігі; бастапқы материалдың сапасы (мысалы, құймакесек сыдырылған немесе сыдырылмаған); тетік бетінің кедір-бұдырлығына қойылатын талап және т.б (әдіп және шақтама қосымшада келтірілген).
Соғылманың сызбасында көрсетілген номинальды өлшем бойынша оның көлемі анықталады, ал осы көлем бойынша масса есептелінеді. Күрделі соғылманың көлемін есептеу үшін оны дұрыс геометриялық фигураны құрастырушы жеке элементерге бөледі.
Сәйкесті геометриялық формулалар бойынша осы элементердің көлемін анықтайды, ал содан кейін табылған көлемді қосып соғылманың толық көлемін есептейді:
Vпок = V1 + V2 +… + Vхп. (24)
Соғылманың массасын мынандай формуламен анықтайды:
Gпок = , (25)
мұндағы – соғылма материалының тығыздығы (меншікті масса) (көпшілік болаттардың таңбасы үшін γ = 7,85 г/см3). Жалпы жағдай үшін соғылманы жасауға қолданылатын илемделген дайындаманың көлемі мынандай формуламен анықталады:
Vзаг = , (26)
мұндағы Vобр – шабу көлемі (аяққы қалдықтың); Vв – жұлынғы көлемі (қобылағыш қалдықтары); Уг – отқабыршық түріндегі шығын (дайындаманың көлемінен % алынады).
Соғылманы жасау үшін құймакесектің көлемін мынандай формуламен анықтайды:
, (27)
мұндағы Vпр – кұймакесектің қосылма бөлімі; VД – құймакесектің түп жағы.
Шабу көлемі қалдықтарын жуықты түрде диаграммамен анықтайды, ал тағыда мынандай формуламен табуға болады:
Диаметрі d болатын дөңгелек қимаға:
Vобр = 0,23d3 – тоқпақпен соққанда;
Vобр = 0,21 d3 – баспақпен соққанда;
Қабырға жақтары h және b болатын тіктөртбұрышты қимаға:
Vобр = 0,3 b2h – тоқпақпен соққанда;
Vобр = 0,28b2h – баспақпен соққанда.
Жалынды пештерде қыздырғанда отқабыршық түріндегі шығын бір рет қыздырғанда орташа 1,5 – 3 % болады және келесі жылытуда 1 – 1,5 % болады.
Отқабыршық шығындары пайызын дайындама массасына қатысты есепке алады.
Дайындаманы бұрып тұтас қобылағышпен қобылау жасағанда жұлынғы көлемін мынандай формуламен табады:
(28)
Қуысты қобылағышпен қобылау жасағанда жұлынғы көлемін мынандай формуламен анықтайды:
(29)
мұндағы dот – қобылау тесігінің диаметрі; hзаг – қобылауға дейінгі дайындама биіктігі; dвн –қобылағыштың ішкі диаметрі.
Кұймакесектен соғылманы жасаған кезде оның қосылма бөлімінен және түп жағынан бөлінетін шығынды есепке алады. Болат металының құймакесегіндегі шығын мөлшері мынаған тең: қоспаланған конструкциялық болат: құймакесектің қосылма бөлімі 20 – 25 %; құймакесектің түп жағы 3 – 5 %; қоспаланған болат: құймакесектің қосылма бөлімі 25 – 30 %; құймакесектің түп жағы 5 – 7 %.
Дайындаманың немесе құймакесектің көлемі бойынша олардың өлшемдерін есептейді (технологиялық процесте ескерілген шөктеу мөлшерін есепке алып).
Дайындаманың массасын мынандай формуламен анықтайды:
Gзаг = (30)
Құймакесектің массасы мынандай формуламен анықтайды:
. (31)
Бүйіржағынан шөктіріп жасалынатын соғылмаға дайындаманың қимасын таңдағанда hзаг = (1,25 – 2,5)d қатнасын есепке алады, мұндағы hзаг – дайындаманың биіктігі (ұзындығы); d – дайындаманың диаметрі (немесе қвадраттың қабырға жағы). Кішкентай шектеме (1,25) шыбықтан дайындаманы кесу шартын есепке алады. Мынандай жағдай hзаг ≤ d металдың көлденең қимасының үлкен болуын талап етеді және бөлуге қуатты жабдықты керек етеді (дайындаманы қайшыда кескенде). Екінші шектеме (2,5) шөктіруді бойлық июсіз жүргізуді қамтамасыз етеді. Көпшілік жағдайда hзаг 3d шартын қабылдайды.
Жуықты есептеулер үшін илемделген металдан кесілген дайындаманың массасын соғылманың түріне және соғудың негізгі әрекетіне байланысты іріленген көрсеткіш бойынша былай анықтайды: Gзаг= КрасGпок, мұндағы Крас – шығын коэффициенті (оқулық [6] қараңыз).
Бастапқы металды таңдауды соғылманың массасын, түржиында керекті пішін және өлшемнің бар болуын, соғылманың керектігін, және оны өңдеудің ретін бірыңғайлаудың мүмкіндігін, тағы да басқа факторларды ескеріп жүзеге асырады. Ірі соғылманы құймакесектен жасайды. Осы құймакесектің массасы жүз тоннаға дейін жетіп, енді ауқымда тербеледі.
Салыстырмалы кіші соғылманы жасағанда түржиынды илемді қолданады (әдетте көлденең қимасы дөңгелек немесе квадратты болады), ал орташа өлшемі бар соғылманы жасағанда жаншылған кеспелтек (блюмс) немесе квадратты дайындама қолданады.
Есептеу бойынша керекті металдың қимасын түржиындық МЕСТпен қамтылған жақын үлкен қимаға дейін түзетеді. Түржиынды илемнің бастапқы ұзындығын (номерлік, еселік, қалдығы бар өлшемдік және басқа варианттар) технико-экономикалық есептеудің негізінде таңдайды (құймакесектің өлшемдері қосымшада келтірілген).
Өңдеудің жылу режимін болаттың таңбасына, дайындаманың көлденең қимасына, нақты қыздыру шартына, соғу операциясына байланысты белгілейді. Мысалы, ию операциясына қарағанда біраз жоғарғы температурада қыздыруды шөктіру және ұзарту операцияларында қолданады.
Осыдан кейін керекті операцияларды және әрекетті (операциялардың бөлімін) таңдайды, оларды орындаудың ретін, құралды және технологиялық әбселді белгілейді. Операцияларды және әрекетті эскиз түрінде технологиялық суреттемеге бейнелейді. Тоқпақтың ең үлкен құлайтын бөлімінің массасын немесе баспақтың ең үлкен күшін талап ететін операция бойынша соғуға керекті жабдықтың типтік өлшемін анықтайды. Басқа операциялармен салыстырғанда шөктіру үлкен күшті талап етеді.
Керекті жағдайда баспақтың күшін немесе тоқпақтың құлайтын бөлімінің массасын формула, диаграмма, кесте бойынша анықтайды. Металдардың деформацияға кедергісі мынандай бірсыпыра факторлармен байланысты болады: металдың таңбасы, соғуды жүргізетін температура, деформацияның дәрежесі және жылдамдығы, жанасу үйкелісі, дайындаманың өлшемдерінің қатнасы, соғылманың құрама пішіні.
Негізгі анықтаушы фактор болып металл таңбасы және деформациялау процесі өтетін температура есептеледі (оқулық [6] қараңыз).
Дөңгелек немесе квадратты дайындаманы шөктіргенде қос әрекетті тоқпақтың құлайтын бөлімінің массасын төменде келтірілген формулаларымен (1 сараптамалық сабақты қараңыз) немесе мынандай теңдеумен есептеуге болады:
, (32)
мұндағы Vзаг – дайындаманың көлемі, см3; (t) – деформациялау температурасындағы беріктік шегі, МПа (кгс/мм2);
– соңғы соққыдағы деформациялау дәрежесі (болаттар үшін 0,025-0,060 қабылданады); Ктр – жанасу үйкелісінің әсерін және дайындама өлшемінің қатынасын ескеретін коэффициент. Осы коэффициент мынандай формуламен анықталады:
, (33)
мұндағы – жанасу үйкелісінің коэффициенті; Dср – шөктірілгеннен кейінгі соғылманың орташа диаметрі; Нк – шөктірілген соғылманың биіктігі. Болаттар үшін жанасу үйкелісінің коэффициенті 0,25 – 0,45 шегінде қабылданады. Оның мөлшері құралдың жұмысшы бетінің күйімен байланысты болады. Майлау μ мөлшерін 15 – 20 % азайтады. Деформациялау жылдамдығын үлкейткенде жанасу үйкелісі тағыда азаяды. Сондықтан баспақта соққанмен салыстырғанда тоқпақта соққанда μ мөлшері аз болады.
Тоқпақты жуықты түрде таңдау үшін диаграмманы қолданады. Шөктіргенде, тоқпақтың құлайтын бөлімінің массасын Gп.ч таңдауға керекті диаграмма П1.22-суретте көрсетілген (сараптамалық сабақ № 1 қараңыз). Осы диаграмма оралдың ауыр машинажасау заводы практикасы негізінде істелген. Диаметрі Dср 200 – ден 800 мм дейін және биіктігі Нк 100 – ден 420 мм дейін болатын соғылмаға диаграмманы қолдануға болады. Үлкен өлшемдері бар тістегеріш типті соғылманы гидравликалық баспақта жасайды, ал кіші өлшемдері бар соғылмаларды құлайтын бөлімінің массасы 750 кг артпайтын тоқпақта жасайды. Диаграммадағы соғылманың өлшеміне сәйкесті а нүктесі шөктіруге құлайтын бөлімінің массасы 3 т болатын тоқпақтың керектігін көрсетеді.
Соғу баспағының астында шөктіруге керекті күшті төменде келтірілген формуламен (сараптамалық № 1 қараңыз) немесе мынандай теңдеумен анықтайды:
(34)
мұндағы U – жылдамдық коэффициенті (соғу баспағы үшін U = 1÷2); m – деформациялайтын металдың массасын немесе көлемін ескеретін масштабтық коэффициент; – деформациялау температурасындағы беріктік шегі; Ктр – жанасу үйкелісінің әсерін ескеретін коэффициент (жоғарыда көрсетілген формула бойынша); Fср – шөктірілген дайындаманың көлденең қимасының ауданы.
Құрылымдық көміртекті, аз қосполанған және қоспаланған болаттардан жасалған, диаметірі 800 мм – ге дейін жалпыға белгіленген соғылмалар үшін техникалық шарт және сынау әдістері стандартта белгіленген. Қолдануына байланысты соғылмаларды сынау түрлеріне, топты жинақтау шартына және тапсыру сипаттамасына қарап бес топқа бөледі [6].
Негізгі әдебиеттер: [1] (тарау 12, бет 416 – 491); [2] (тарау 6, бет 81 – 116, тарау 7, бет 118 – 138); [4] (тарау 4, бет 128 – 233).
Бақылау сұрақтары
1. Қандай операция қобылау деп аталады?
2. Қобылаудың қандай тәсілдерін білесіздер?
3. Қобылаудың алдында қандай операцияны орындайды?
4. Тұтас қобылағышпен қобылауды қалай іске асырады?
5. Қуыс қобылағышпен қобылауды қалай іске асырады?
6. Ұсталық соғудың технологиялық процесін жасаған кезде соғылманың сызбасын қалай жасайды және оның массасын қалай анықтайды?
7. Ұсталық соғудың технологиялық процесін жасаған кезде дайындаманың өлшемін есептеуді қалай іске асырады?
8. Ұсталық соғудың технологиялық процесін жасаған кезде ұсталық соғудың операциясын және оның орындалу ретін қалай таңдайды?
9. Соғудың технологиялық процесін жасаған кезде жабдық қалай таңдалады?
10. Әдіп, шақтама және кенерме дегеніміз не?
11. Соғылманың массасы және көлемі қандай формуламен анықталады?
12. Ұсталық соғудың жылулық режімдері қалай белгіленеді?
13. Соғылманың сапасы қалай бақыланады?
Дата добавления: 2014-12-08; просмотров: 3210;