ЦЕЛИ И ЗАДАЧИ МАТЕРИАЛОВЕДЕНИЯ. ОСНОВНЫЕ ПОНЯТИЯ О МАТЕРИАЛАХ И ИХ СВОЙСТВАХ 5 страница
Высокопрочными чугунами называют чугуны, в которых графит имеет шаровидную форму. Их получают модифицированием магнием, который вводят в жидкий чугун в количестве 0,02-0,08 %. Ввиду того, что модифицирование чугунов чистым магнием сопровождается сильным пироэффектом, чистый магний заменяют лигатурами (например, сплавом магния и никеля).
По структуре высокопрочный чугун может быть ферритным, ферритно-перлитным или перлитным (рис.7.7).
Рис. 7.7. Микроструктура высокопрочного чугуна, (х 300): а – ферритный; б - ферритно-перлитный; в – перлитный
Шаровидный графит – менее сильный концентратор напряжений, чем пластинчатый графит, и поэтому меньше снижает механические свойства основы. Чугуны с шаровидным графитом обладают более высокой прочностью и некоторой пластичностью. Маркируют высокопрочные чугуны по пределу прочности и относительному удлинению (таблица 7.2).
Таблица 7.2
Механические свойства некоторых высокопрочных чугунов
(ГОСТ 7293-85)
Чугун | sв, МПа | d, % | НВ | Структура металлической основы |
ВЧ 38-17 ВЧ 42-12 ВЧ 50-7 ВЧ 60-2 ВЧ 80-2 ВЧ 120-2 | 1400-1700 1400-2000 1710-2410 2000-2800 2500-3300 3020-3800 | Феррит с небольшим количеством перлита Перлит с небольшим количеством феррита |
Высокопрочные чугуны применяют в различных отраслях техники, эффективно заменяя сталь во многих изделиях и конструкциях. Из них изготовляют оборудование прокатных станов (прокатные валки массой 12 т), кузнечно-прессовое оборудование (траверса пресса, шабот ковочного молота), в турбостроении – корпус паровой турбины, лопатки направляющего аппарата, в дизеле-, тракторо- и автомобилестроении – коленчатые валы, поршни и многие другие ответственные детали, работающие при высоких циклических нагрузках и условиях изнашивания.
В некоторых случаях для улучшения механических свойств применяют термическую обработку отливок; для повышения прочности – закалку и отпуск при 500-600 оС; для увеличения пластичности – отжиг, способствующий сфероидизации перлита.
Ковкими называют чугуны, в которых графит имеет хлопьевидную форму. Их получают отжигом белых доэвтектических чугунов. По этой причине графит ковких чугунов называют углеродом отжига. Такой графит, в отличие от пластинчатого, меньше снижает механические свойства металлической основы, вследствие чего ковкий чугун по сравнению с серым обладает более высокой прочностью и пластичностью.
Отливки из белого чугуна, подвергаемые отжигу на ковкий чугун, изготовляют тонкостенными. Они не должны иметь сечение более 50 мм, иначе в сердцевине при кристаллизации выделяется пластинчатый графит, чугун становится непригодным для отжига.
По структуре металлической основы, которая определяется режимом отжига, ковкие чугуны бывают ферритными и перлитными (рис. 7.8).
Рис. 7.8. Микроструктура ковких чугунов, (х 300): а – ферритный; б – ферритно – перлитный; в - перлитный
Отжиг на ферритные чугуны проводят по режиму 1 (рис. 7.9), обеспечивающему графитизацию всех видов цементита белого чугуна. Перлитный ковкий чугун получают отжигом, который проводят в окислительной среде по режиму 2 (рис. 7.9).
Рис. 7.9. Схема отжига белого чугуна на ковкий: 1 – на ферритный;
2 – на перлитный
Графитизация цементита перлита практически не происходит, чугун приобретает структуру, состоящую из перлита и углерода отжига. Отсутствие литейных напряжений, которые полностью снимаются во время отжига, компактная форма и изолированность графитных включений обусловливают высокие механические свойства ковких чугунов. Принцип их маркировки тот же, что и высокопрочных чугунов : КЧ sв - d (таблица 7.3).
Таблица 7.3
Механические свойства некоторых марок ковких чугунов (ГОСТ 1215-79)
Чугун | sв, МПа | d, % | НВ | Структура металлической основы |
КЧ 30-6 КЧ 35-10 КЧ 37-12 КЧ 45-7 КЧ 60-3 КЧ 80-1,5 | 1,5 | 1000-1630 1000-1630 1100-1630 1500-2070 2000-2690 2700-3200 | Феррит + (10-3 %) перлита Перлит + (20-0 %) феррита |
Из таблицы видно, что ферритные чугуны имеют более высокую пластичность, а перлитные – более высокую прочность и твердость.
Ковкие чугуны нашли широкое применение в сельскохозяйственном, автомобильном и текстильном машиностроении, в судо-, котло-, вагоно- и дизелестроении. Из них изготовляют детали высокой прочности, работающие в тяжелых условиях износа, способные воспринимать ударные и знакопеременные нагрузки. Большая плотность отливок ковкого чугуна позволяет изготовлять детали водо- и газопроводных установок; хорошие литейные свойства исходного белого чугуна – отливки сложной формы.
Недостаток ковких чугунов – повышенная стоимость из-за продолжительного дорогостоящего отжига.
8. ОСНОВЫ ТЕОРИИ ТЕРМИЧЕСКОЙ ОБРАБОТКИ
Свойства сплавов определяются его структурой (внутренним строением), которая зависит от температуры нагрева и скорости охлаждения. Основной способ изменить структуру, а, следовательно, свойства – это термическая обработка.
Термическая обработка – это совокупность операций нагрева, выдержки и охлаждения, проводимых в определенной последовательности с целью изменения внутреннего строения сплава и получения необходимых физико-механических свойств.
В основе термической обработки лежат фазовые превращения в твердом состоянии.
8.1. Четыре основные превращения в сталях
В сталях основными являются три структуры: аустенит – твердый раствор углерода в γ – Fe [Fe γ(С)]; мартенсит – пересыщенный, частично упорядоченный твердый раствор углерода в α – Fe [Fe γ(С)]; перлит – эвтектоидная смесь феррита и цементита [Feα + Fe3 С]. Переход из одной структуры в другую характеризует основные превращения при термической обработке:
- первое превращение – это превращение перлита в аустенит, которое происходит при нагреве: П→А (рис. 8.1).
Рис. 8.1. Изменение энергии фаз в зависимости от температуры
- второе превращение – это превращение аустенита в феррито-цементитные смеси разной дисперсности в зависимости от скорости охлаждения: А→Ф+Ц;
- третье превращение заключается в превращении аустенита в мартенсит А→М при быстром охлаждении (при закалке);
- четвертое превращение заключается в разложении мартенсита при отпуске закаленной стали (М → продукты распада).
Любой технологический процесс термической обработки состоит из определенных комбинаций этих четырех превращений.
8.2. Превращения в стали при нагреве - образование аустенита (I превращение)
Превращение П → А - процесс кристаллизационного типа и подчиняется закономерностям кристаллизации, т. е. зарождаются центры новой фазы (А) и они растут (рис. 8.2). Перекристаллизация перлита в аустенит сопровождается размельчением зерен. Размер зерен вновь образовавшегося аустенита, который называется начальным, не зависит от размера исходного зерна, а зависит от степени дисперсности фаз в перлите. Чем выше дисперсность, тем мельче получается аустенитное зерно.
Превращение П→А носит диффузионный характер и сопровождается значительным перемещением атомов углерода.
Рис. 8.2. Превращение перлита в аустенит: а - зарождение новой фазы аустенита в зерне перлита; б, в - рост фазы аустенита и степень растворения цементита (Fe3С) в аустените Feγ(С); г - получение гомогенного начального зерна аустенита
Превращение состоит из двух параллельно идущих процессов:
- полиморфного Feα→ Feγ превращения;
- растворения цементита (Fe3С) в аустените Feγ(С).
Превращение П→А может идти изотермически при температуре 727 °С (см. рис. 7.1, т. Ас1 и при непрерывном нагреве (рис. 8.3)
Рис. 8.3. Диаграмма изотермического превращения перлита в аустенит для стали с 0,8 % С
Процесс перехода П →А при непрерывном нагреве со скоростью V1 и V2 (рис. 8.3) изучают путем построения диаграммы изотермического образования аустенита. Образцы нагревают до температур выше А1 последовательно и выдерживают сплав при этих температурах, фиксируя начало и конец превращения;
Н - начало превращения П→А;
К - конец превращения П→А;
Р - конец растворения углерода в аустените;
Г - конец гомогенизации аустенита.
Из диаграммы (рис. 8.3) видно: время превращения П→А зависит существенно от степени перегрева (нагрева выше А1).
С увеличением перегрева уменьшается размер критического зародыша аустенита, увеличивается скорость возникновения зародышей и скорость их роста, происходит измельчение зерна стали, что используется в практике термической обработки (отжиг, закалка). При обработке токами высокой частоты (ТВЧ) можно получить очень мелкие зерна аустенита.
Влияние нагрева на продолжительность (τпрев) превращения показывают лучи скоростей V1 и V2. При меньшей скорости нагрева (V1 < V2< V3) (рис. 8.3) превращение происходит при более низких температурах, за больший промежуток времени.
В доэвтектоидных сталях при нагреве от А1 до А3 происходит превращение избыточного феррита в аустенит (рис. 8.4).
В заэвтектоидных сталях при нагреве от А1 до Аст происходит растворение цементита вторичного (Fe3С) в аустените (рис. 8.4). При этом выравнивается концентрация углерода и укрупняется зерно аустенита. С повышением температуры нагрева, в результате собирательной рекристаллизации, аустенитное зерно растет (рис. 8.4). Крупные зерна растут, поглощая мелкие. Скорость роста зерен при перегреве зависит от способа выплавки стали, полноты раскисления и наличия легирующих элементов. Природным зерном называется зерно аустенита, образующееся после трехчасовой выдержки при 930°С.
Рис. 8.4. Часть диаграммы Рис. 8.5. Схема изменения размера
«железо-углерод» зерна перлита в зависимости
от нагрева в аустенитной области
По склонности к росту аустенитного зерна стали делят на две группы: наследственно-крупнозернистые и наследственно - мелкозернистые.
При последующем охлаждении стали зерна аустенита не измельчаются. Размер зерна при комнатной температуре называется действительным зерном и зависит от температуры нагрева, продолжительности выдержки, склонности стали к росту зерна при нагреве. Это необходимо учитывать при назначении режимов термической обработки. Температура нагрева под закалку для доэвтектоидной стали не должна превышать: А3 + (30…50°С) (рис. 8.4). Для заэвтектоидной стали не должна превышать А1 + (30...50°С). Нагрев заэвтектоидной стали до температуры, значительно превышающий А3 и Асm, приводит к образованию крупного действительного зерна. Такой нагрев называют перегревом.
Нагрев до еще более высоких температур в окислительной атмосфере сопровождающийся образованием по границам зерен окислов железа с частичным оплавлением, называется пережогом.
Перегрев и пережог являются браком при термической обработке. Причем перегрев можно исправить охлаждением и последующим повторным нагревом до необходимой температуры, а пережог является неисправимым браком. Свойства стали зависят от размеров действительного зерна.
Мелкозернистые стали имеют значительно более высокую вязкость, несколько более высокую прочность и твердость в сравнении с крупнозернистыми.
Крупнозернистые стали имеют также ряд преимуществ. Эти стали имеют лучшую прокаливаемость; жаропрочные аустенитные стали с крупным зерном лучше сопротивляются ползучести. Магнитомягкие стали имеют меньшую коэрцитивную силу и тем самым меньшие потери.
8.3. Превращения в стали при охлаждении (II превращение)
При медленном охлаждении происходит эвтектоидное превращение аустенита
Feγ(С)→ Feα + Fe3С; А→Ф+ЦII
0,8 %С 0,2 %С+6,67 %С
Рассмотрим закономерность превращения переохлажденного аустенита эвтектоидного состава (0,8 % С) на n-ом количестве образцов. Для этого:
1) образцы нагревают до однородного аустенита выше Ас1+ (30…50 °С)≈770 °С, дают выдержку;
2) образцы переносятся в термостаты с заданной температурой ниже линии А1 (727 °С), интервал между изотермами 25-50°С;
3) в процессе изотермической выдержки наблюдают за происходящими в аустените превращениями (измеряют твердость, плотность, магнитную восприимчивость);
4) строят серию кинетических кривых в координатах «время - количество расплавившегося аустенита».
Отрезки ОН1, ОН2 (рис.8.6) и т.д. называются инкубационным или подготовительным периодом.
|
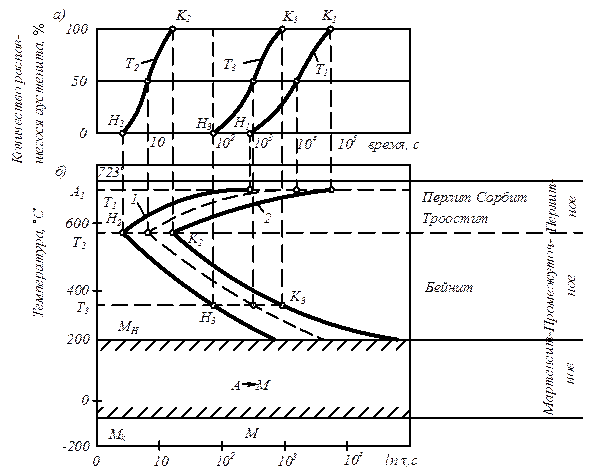
Рис. 8.6. Кинетические кривые изотермического превращения аустенита (а) и построенная по ним диаграмма (б)
Превращение протекает с различной скоростью и достигает максимума при 50 % распавшегося аустенита.
С увеличением переохлаждения устойчивость аустенита уменьшается (ОН1 > ОН2), минимум устойчивости приходится на переохлаждение в 150-200 °С ниже А1 (500 - 550 °С).
При дальнейшем увеличении переохлаждения устойчивость растет (ОН3).
Строят диаграмму изотермического превращения переохлажденного аустенита в координатах t° - lgτ. Такая диаграммы в координатах называется диаграммой изотермического превращения аустенита или С- образной диаграммой:
- левая кривая - начало превращения переохлажденного аустенита в зависимости от степени переохлаждения;
- правая кривая - конец превращения аустенита. Она показывает время, необходимое при данном переохлаждении для полного превращения аустенита в феррито-цементитную смесь;
- точка Н2 соответствует переохлаждению 150-200 °С ниже А1 и показывает интервал минимальной устойчивости аустенита.
8.4. Перлитное превращение
Распад аустенита состоит из двух одновременно протекающих процессов:
- перехода Feγ→ Feα (бездиффузионного процесса) и образования цементита Fe3С (диффузионного процесса).
При перлитном превращения ведущей фазой является цементит (Fe3С). Зарождение зародыша Fe3С происходит на границе зерна, далее пластинка прорастает в середину зерна, а соседние участки обедняются углеродом и образуется феррит (рис. 8.7).
С увеличением степени переохлаждения увеличивается разность энергии аустенита и перлита (ΔF = FА – FП) (рис. 8. 1). Это приводит к повышению дисперсности образующихся фаз. Структуру феррито-цементитной смеси различной дисперсности называют перлитом, сорбитом, трооститом.
Рис. 8.7. Последовательность образования перлита в аустенитном зерне:
а - первичные пластинки цементита в феррите; б - вторичные пластинки цементита в феррите; в – колонии перлита
Рис. 8.8. Микроструктура перлита, (×1500)
На рисунке 8.8 по ориентировке пластин можно различить два зерна перлита (две колонии).
Дисперсность - суммарная толщина соседних пластинок Feα + Fe3С (рис. 8.9).
Рис. 8.9. Схема расположения пластинок цементита (а) и феррита (б) в перлите на поверхности протравленного шлифа. Стрелкой показано направление освещения под микроскопом
Дисперсность структуры определяет механические свойства стали: перлит имеет твердость 200НВ, сорбит – 300НВ, троостит – 400НВ
8.5. Бейнитное превращение
Бейнитное промежуточное превращение идет в интервале температур 550 – Мн. Образующаяся структура представляет собой двухфазную смесь кристаллов феррита к цементита. Основная особенность промежуточного превращения состоит в том, что полиморфный переход Feγ→ Feα происходит по мартенситному механизму – бездиффузионно, а образование цементита (Fe3С) – идет диффузионным путем.
Превращение начинается в интервале температур 550 – Мн с перераспределения углерода в аустените. Диффузионное перераспределение приводит к обеднению одних и обогащению других зон (скорость диффузии углерода в интервале 550 - Мн достаточна, а скорость диффузии железа стремится к нулю).
Уменьшение количества растворенного углерода приводит к повышению температуры мартенситного превращения, поэтому в обедненных углеродом зонах γ - твердого раствора происходит мартенситное превращение.
Образование концентрационной неоднородности приводит к возникновению напряжения, и процесс полиморфного превращения носит сдвиговый характер. Кристаллы феррита (Feα) пересыщены углеродом до 0,1-0,2 % получают тетрагональную решетку. При этом структура верхнего бейнита получается перистой, а нижнего - игольчатой.
8.6. Превращение аустенита при непрерывном охлаждении
Сталь, нагретая до аустенитного состояния, может быть охлаждена с различной скоростью. Наложим кривые охлаждения образцов углеродистой эвтектоидной стали на диаграмму изотермического распада аустенита (рис. 8.6) построена в координатах “температура - время”, поэтому на нее можно наложить графики скоростей охлаждения V1 < V2 < V3< Vкр < V4 (рис. 8.10)
Рис. 8.10. Наложение графиков скоростей непрерывного охлаждения на диаграмму изотермического распада аустенита. Увеличение скорости охлаждения от V до Vкр
8.7. Мартенситное превращение ( III превращение)
При больших степенях переохлаждения и скоростях, превышающих Vкр, скорости диффузии железа и углерода равны нулю, ЕА>>ЕМ, поэтому превращение Feγ(С)→ Feα(С) происходит бездиффузионным путем (без изменения концентрации реагирующих фаз) за счет сдвига. Образуется мартенсит - пересыщенный, частично упорядоченный, твердый раствор внедрения углерода в альфа - железо (Feα) с тетрагональной решеткой (с/а >1) (рис. 8.11).
Рис. 8.11. Объемно-центрированная тетрагональная решетка мартенсита
Степень искажения решетки с/а прямо пропорциональна концентрации углерода. Поскольку мартенситное превращение состоит в перестройке решетки аустенита, в которой атомы не меняются местами (бездиффузионно), а смещаются (сдвигаются) друг относительно друга, то кристаллы имеют ориентационную связь (рис. 8.12). В углеродистых сталях существует две ориентационные связи, получившие название ориентировка Курдюмова-Закса и ориентировка Нишияма. Ориентировка кристаллов мартенсита (пластин или линз) идет по определенным плоскостям и направлениям (рис. 8.12) (направление (111) // (101)), плоскости ([101] // [111]). Следствием сдвигового механизма превращения на полированной поверхности шлифа является характерный рельеф.
Рис. 8.12. Атомно-кристаллический механизм перестройки
Согласно теории, мартенситный кристалл образуется на плоскости сдвига в момент ее образования. Главную роль играют напряжения. Источниками напряжений являются: градиент температур по сечению; анизотропия механических свойств; неоднородность химического состава; структурные несовершенства; разная ориентировка кристаллов в пространстве; различный удельный объем аустенита и мартенсита; различные коэффициенты линейного расширения фаз.
Удельный объем аустенита при количестве углерода от 0,2-1,4 % составляет 0,12227 – 0,12528 см3/г; мартенсита – 0,12708 – 0,13061 см3/г.
Напряжения, возникающие в результате изменения температуры концентрируются в отдельных участках аустенита, образуя энергетические флуктуации. Релаксация (разряжение) напряжений происходит путем сдвига по определенным плоскостям и направлениям (рис. 8.12). В момент сдвига образуется порция мартенситных пластин (игл). Время образования порции мартенситных пластин (игл) изменяется в пределах от 0,5×10-7 до 5,7×10-8 в зависимости от размера пластин. Средняя скорость роста составляет около 103 м/с (1 км/с), близка к скорости звука в твердом теле и не зависит от температуры превращения. Кристаллы растут до определенных размеров, после чего рост прекращается.
Аустенитно-мартенситное превращение (рис. 8.13, б) проходит в интервале температур Мн – Мк (Мн, Мк – мартенситные точки: н – начало, к – конец превращения). При данной температуре с огромной скоростью образуется только определенное количество (порция) мартенсита, остается остаточный аустенит. Для возобновления процесса нужно дополнительное охлаждение.
Рис. 8.13. Мартенситная кривая (а) и зависимость мартенситных точек от содержания углерода (б)
Мартенситное (А →М) превращение не идет до конца, в стали всегда остается остаточный аустенит (рис. 8. 13, а).
Положение точек мартенситного превращения зависит от состава стали. Сильно снижает положение точек Мн и Мк концентрация углерода (рис. 8.13, б).
Итак, особенностями мартенситного превращения являются:
1) бездиффузионный сдвиговый механизм;
2) ориентированность кристаллов в пространстве;
3) ультразвуковая скорость образования порции кристаллов мартенсита;
4) тетрагональность решетки (с/а);
5) незаконченность превращения А → М;
6) необратимость превращений А → М;
7) очень высокая твердость мартенсита (HRC 55-65) и хрупкость из-за повышенной плотности дефектов (дислокаций) внутри кристалла мартенсита.
8.8. Превращения в закаленной стали при нагреве (IV превращение)
Различают 4 основных превращения при нагреве закаленной стали (рис. 8.14). Все процессы идут внутри мартенситных пластин (игл) поэтому характер игольчатой структуры сохраняется до высоких температур.
Первое превращение при отпуске происходит в интервале 80-200°С и называется «двухфазным» или «гетерогенным» расплавом мартенсита. Выделяются тончайшие пластины карбида (ε - карбид или FexС), уменьшается степень тетрагоналъности с/а→1, образуется «отпущенный мартенсит». Это превращение сопровождается сокращением объема образца.
Рис. 8.14. Дилатометрическая кривая отпуска закаленной стали
Второе превращение происходит в интервале от 200 - 300°С. Одновременно идут процессы:
- образуются ε - и FexС – карбиды, когерентно связанные с решеткой мартенсита;
- остаточный аустенит переходит в «отпущенный мартенсит» (рис. 8.15) (бейнит нижний). Процесс сопровождается увеличением объема (рис. 8.14);
- продолжается выделение углерода из мартенсита (с/а→1);
- начинается карбидное обособление - образование карбида железа по схеме:
FexС→ Fe2С→ Fe5С→ Fe3С
Третье превращение происходит в интервале от 350-450°С. Увеличивается скорость диффузии, карбид железа выделяется из решетки мартенсита. Степень тетрагональности с/а →1. Образуется дисперсная смесь феррита и цементита (троостит отпуска).
Четвертое превращение происходит выше 400-450°С. Растут частицы карбида (коагуляция) и сливаются, округляются (сфероидизация). Тонкая феррито-цементитная структура троостита отпуска превращается при температуре 500-550°С в сорбит отпуска, а при более высоких температурах (600-650°С) - в перлит.
Рисунок 8.15 - Схема процессов, совершающихся при отпуске: 1 – выделение углерода из тетрагонального мартенсита; 2 – распад остаточного аустенита; 3 – снятие внутренних напряжений; 4 – коагуляция карбидных частиц
Возврат и рекристаллизация в α – Фазе (Feα) происходят в широком интервале температур отпуска. Развитие этих процессов сдерживается частицами карбидных выделений, закрепляющих отдельные дислокации, дислокационные стенки. После длительного отпуска при температуре 600°С, когда в результате коагуляции цементитных частиц закрепление границ ослабевает, происходит рекристаллизационный рост зерен миграцией высокоугольных границ. Микроструктура при этом теряет характерные морфологические признаки реечного мартенсита. Закалка + высокий отпуск называется улучшением.
9. ТЕХНОЛОГИЯ ТЕРМИЧЕСКОЙ ОБРАБОТКИ
9.1. Основные составляющие технологического процесса термической обработки
При разработке технологии термической обработки необходимо установить:
- режим нагрева детали или заготовки, в который входят температура нагрева, допустимые скорость и время нагрева;
- характер среды, где должен идти нагрев;
- условия охлаждения (выбор охлаждающей среды);
- производительность труда при термообработке;
- экономичность выбранного процесса.
Режим термообработки назначают до критическим точкам (Ас1, Ас3, Асm) диаграммы Fe-Fe3С (рис.7.1) и С - образной диаграммы превращения аустенита (рис.8.6).
Условия нагрева определяются видом нагревательного устройства, к которым относятся нагревательные печи (топливные или электрические), соляные ванны или ванны с расплавленным металлом, установки индукционного нагрева токами промышленной частоты или токами высокой частоты.
9.2. Классификация видов термической обработки
Схема классификации основных видов термической обработки показана на рис. 9.1.
Рис. 9.1. Классификация основных видов термической обработки
Вид термической обработки определяется не характером изменения температуры во времени, а типом фазовых и структурных изменений в металле.
Собственная термообработка заключается только в термическом воздействии на металл или сплав.
Химико-термическая обработка заключается в сочетании термического и химического воздействия на поверхность.
Термомеханическая обработка заключается в сочетании термического воздействия и пластической деформации.
Дата добавления: 2016-06-02; просмотров: 944;