ЦЕЛИ И ЗАДАЧИ МАТЕРИАЛОВЕДЕНИЯ. ОСНОВНЫЕ ПОНЯТИЯ О МАТЕРИАЛАХ И ИХ СВОЙСТВАХ 3 страница
Ан = Р * l1( cos b - cos a),
где Р - масса маятника, кг;
l1 – расстояние от оси маятника до его центра тяжести;
b - угол после удара;
a - угол до удара
4.2.4. Циклическая долговечность характеризует работоспособность материала в условиях многократно повторяющихся циклов напряжений. Цикл напряжений – совокупность изменения напряжения между двумя его предельными значениями smax и smin в течение периода Т (рис. 4.9).
Рис. 4.9. Синусоидальный цикл изменения напряжений
Различают симметричные циклы (R = -1) и асимметричные (R изменяется в широких пределах). Различные виды циклов характеризуют различные режимы работы деталей машин.
Процессы постепенного накопления повреждений в материале под действием циклических нагрузок, приводящие к изменению его свойств, образованию трещин, их развитию и разрушению, называют усталостью, а свойство противостоять усталости – выносливостью (ГОСТ 23207 – 78).
На усталость деталей машин влияют ряд факторов (рис. 4.10).
Рис. 4.10. Факторы, влияющие на усталостную прочность
Разрушение от усталости по сравнению с разрушением от статической нагрузки имеет ряд особенностей:
- оно происходит при напряжениях, меньших, чем при статической нагрузке, меньших пределах текучести или временного сопротивления;
- разрушение начинается на поверхности (или вблизи от нее) локально, в местах концентрации напряжений (деформации). Локальную концентрацию напряжений создают повреждения поверхности в результате циклического нагружения либо надрезы в виде следов обработки, воздействия среды;
- разрушение протекает в несколько стадий, характеризующих процессы накопления повреждений в материале, образования трещин усталости, постепенное развитие и слияние некоторых из них в одну магистральную трещину и быстрое окончательное разрушение;
- разрушение имеет характерное строение излома, отражающее последовательность процессов усталости. Излом состоит из очага разрушения (места образования микротрещин) и двух зон – усталости и долома (рис. 4.11).
Рис. 4.11. Схема излома усталостного разрушения: 1 – очаг зарождения трещины; 2 – зона усталости; 3 – зона долома
4.3. Конструкционная прочность металлов и сплавов
Конструкционная прочность металлов и сплавов – это комплекс прочностных свойств, которые находятся в наибольшей корреляции со служебными свойствами данного изделия.
Сопротивление материала хрупкому разрушению является важнейшей характеристикой, определяющей надежность работы конструкции.
Переход к хрупкому разрушению обусловлен рядом факторов:
- природой сплава (типом решетки, химическим составом, величиной зерна, загрязнением сплава);
- особенностью конструкции (наличием концентраторов напряжений);
- условиями эксплуатации (температурным режимом, наличием нагрузки на металл).
Существует несколько критериев оценки конструкционной прочности металлов и сплавов:
- критерии, определяющие надежность металлов против внезапных разрушений (критическая температура хрупкости; вязкость разрушения; работа, поглощаемая при распространении трещины; живучесть при циклическом нагружении);
- критерии, определяющие долговечность материала (усталостная прочность; контактная выносливость; износостойкость; коррозионная стойкость).
Для оценки надежности материала используют также параметры: 1) ударную вязкость KCV и КCT; 2) температурный порог хладноломкости t 50. Однако эти параметры только качественные, непригодные для расчета на прочность.
Параметром KCV оценивают пригодность материала для сосудов давления, трубопроводов и других конструкций повышенной надежности.
Параметр KCT, определяемый на образцах с трещиной усталости у основания надреза, более показателен. Он характеризует работу развития трещины при ударном изгибе и оценивает способность материала тормозить начавшееся разрушение. Если материал имеет KCT = 0, то это означает, что процесс его разрушения идет без затраты работы. Такой материал хрупок, эксплуатационно ненадежен. И, наоборот, чем больше параметр KCT, определенный при рабочей температуре, тем выше надежность материала в условиях эксплуатации. KCT учитывают при выборе материала для конструкций особо ответственного назначения (летательных аппаратов, роторов турбин и т. п.).
Порог хладноломкости характеризует влияние снижения температуры на склонность материала к хрупкому разрушению. Его определяют по результатам ударных испытаний образцов с надрезом при понижающейся температуре.
На переход от вязкого разрушения к хрупкому указывают изменения строения излома и резкое снижение ударной вязкости (рис.4.12), наблюдаемое в интервале температур (tв – tх) (граничные значения температур вязкого и хрупкого разрушения).
Рис. 4.12. Влияние температуры испытания на процент вязкой составляющей в изломе (В) и ударную вязкость материала KCV, KCT
Строение излома изменяется от волокнистого матового при вязком разрушении (t > tв) до кристаллического блестящего при хрупком разрушении (t < tх). Порог хладноломкости обозначают интервалом температур (tв – tн) либо одной температурой t50, при которой в изломе образца имеется 50 % волокнистой составляющей, и величина КСТ снижается наполовину.
О пригодности материала для работы при заданной температуре судят по температурному запасу вязкости, равному разности температуры эксплуатации и t 50. При этом, чем ниже температура перехода в хрупкое состояние по отношению к рабочей температуре, тем больше температурный запас вязкости и выше гарантия от хрупкого разрушения.
4.4. Пути повышения прочности металлов
Принято различать техническую и теоретическую прочность. Техническую прочность определяют значением свойств: предела упругости (s0,05); предела текучести (s0,2); предела прочности (sв); модуля упругости (Е); предела выносливости (sR).
Под теоретической прочностью понимают сопротивление деформации и разрушению, которое должны были бы иметь материалы согласно физическим расчетам с учетом сил межатомного взаимодействия и предположения, что два ряда атомов одновременно смещаются относительно друг друга под действием напряжения сдвига.
Исходя из кристаллического строения и межатомных сил можно ориентировочно определить теоретическую прочность металла по следующей формуле:
tтеор » G / 2p,
где G – модуль сдвига.
Теоретическое значение прочности, рассчитываемое по указанной формуле, в 100 – 1000 раз больше технической прочности. Это связано с дефектами в кристаллическом строении, и прежде всего с существованием дислокаций. Прочность металлов не является линейной функцией плотности дислокаций (рис. 4.13).
|
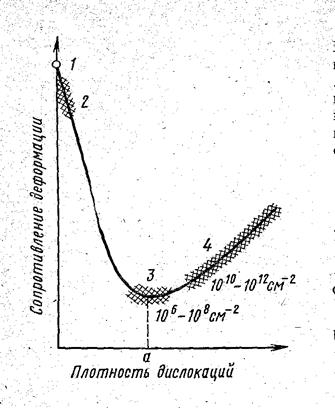
Рис. 4.13. Схема зависимости сопротивления деформации от плотности и других дефектов в металлах:1 – теоретическая прочность; 2-4 – техническая прочность (2 – усы; 3 – чистые неупрочненные металлы; 4 –сплавы, упрочненные легированием, наклепом, термической или термомеханической обработкой)
Как видно из рисунка 4.13, минимальная прочность определяется некоторой критической плотностью дислокаций а, приближенно составляющей 106 – 108 см-2. Эта величина относится к отожженным металлам. Величина s0,2 отожженных металлов составляет 10-5 – 10-4 G. Если а > 1012 – 1013 см-2, то в этом случае могут образоваться трещины.
Если плотность дислокаций (количество дефектов) меньше величины а (рис.4.13), то сопротивление деформации резко увеличивается и прочность быстро приближается к теоретической.
Повышение прочности достигается:
- созданием металлов и сплавов с бездефектной структурой, т.е. получение нитевидных кристаллов («усов»);
- повышение плотности дефектов, в том числе дислокаций, а также структурных препятствий, затрудняющих движение дислокаций;
- создание композиционных материалов.
4.5. Влияние нагрева на строение и свойства деформированного металла (рекристаллизация)
Пластическая деформация (рис. 4.14) приводит к созданию неустойчивого состояния материала из-за возросшей внутренней энергии (внутренних напряжений). Деформирование металла сопровождается его упрочнением или так называемым наклепом. Самопроизвольно должны происходить явления, возвращающие металл в более устойчивое структурное состояние.
Рис. 4.14. Влияние нагрева на механические свойства и структуру нагартованного металла
К самопроизвольным процессам, которые приводят пластически деформированный металл к более устойчивому состоянию, относятся снятие искажения кристаллической решетки, другие внутризеренные процессы и образование новых зерен. Для снятия напряжений кристаллической решетки не требуется высокой температуры, так как при этом происходит незначительное перемещение атомов. Уже небольшой нагрев (для железа 300 –400 оС) снимает искажения решетки, а именно уменьшает плотность дислокаций в результате их взаимного уничтожения, слияния блоков, уменьшения внутренних напряжений, уменьшения количества вакансий и т.д.
Исправление искаженной решетки в процессе нагрева деформированного металла называется возвратом или отдыхом. При этом твердость металла снижается на 20-30 % по сравнению с исходным, а пластичность возрастает.
Параллельно с возвратом при температуре 0,25 – 0,3 Тпл происходит полигонизация (сбор дислокаций в стенки) и образуется ячеистая структура.
Одним из способов снятия внутренних напряжений при деформации материалов является рекристаллизация. Рекристаллизация, т.е. образование новых зерен, протекает при более высоких температурах, чем возврат, может начаться с заметной скоростью после нагрева выше определенной температуры. Чем выше чистота металла, тем ниже температура рекристаллизации. Между температурами рекристаллизации и плавления существует связь:
Трек = а * Тпл,
где а – коэффициент, зависящий от чистоты металла.
Для технически чистых металлов а = 0,3 – 0,4, для сплавов а = 0,8.
Температура рекристаллизации имеет важное практическое значение. Чтобы восстановить структуру и свойства наклепанного металла (например, при необходимости продолжить обработку давлением путем прокатки, протяжки, волочения и т.п.), его надо нагреть выше температуры рекристаллизации. Такая обработка называется рекристаллизационным отжигом.
Процесс рекристаллизации можно разделить на два этапа:
- первичную рекристаллизацию или рекристаллизацию обработки, когда вытянутые вследствие пластической деформации зерна превращаются в мелкие округлой формы беспорядочно ориентированные зерна;
- вторичную или собирательную рекристаллизацию, заключающуюся в росте зерен и протекающую при более высокой температуре.
Первичная кристаллизация заключается в образовании новых зерен. Это обычно мелкие зерна, возникающие на поверхностях раздела крупных деформированных зерен. Хотя в процессе нагрева и происходят внутризеренные процессы устранения дефектов (возврат, отдых), все же они, как правило, полностью не заканчиваются, с другой стороны, вновь образовавшееся зерно уже свободно от дефектов.
К концу первой стадии рекристаллизации можно получить структуру, состоящую только из очень мелких зерен, в поперечнике имеющих размер в несколько микрон. Но в этот момент наступает процесс вторичной кристаллизации, заключающийся в росте зерна.
Возможны три существенно различных механизма роста зерна:
- зародышевый, состоящий в том, что после первичной кристаллизации вновь возникают зародышевые центры новых кристаллов, их рост приводит к образованию новых зерен, но их меньше, чем зерен в исходном состоянии, и поэтому после завершения процесса рекристаллизации зерна в среднем станут крупнее;
- миграционный, состоящий в перемещении границы зерна и увеличении его размеров. Крупные зерна растут за счет «поедания» мелких;
- слияние зерен, состоящее в постепенном «растворении» границ зерен и объединении многих мелких зерен в одно крупное. При этом образуется разнозернистая структура с низкими механическими свойствами.
Реализация одного из основных механизмов роста зависит:
- от температуры. При низких температурах рост идет за счет слияния зерен, при высоких – за счет миграции границ зерен;
- от исходного состояния ( от степени деформации). При малой степени деформации (3-8%) первичная рекристаллизация затруднена, и рост зерна идет за счет слияния зерен. В конце процесса образуются гигантские зерна. При большой степени деформации (более 10 %) слияние зерен затрудняется, и рост идет за счет миграции границ зерен. Образуются более мелкие зерна. Таким образом, после отжига получается равновесная структура, изменяются механические свойства, снимается наклеп металла, повышается пластичность.
5. ОСНОВЫ ТЕОРИИ СПЛАВОВ
5.1. Строение сплавов
Чистые металлы обладают низкой прочностью и не обеспечивают требуемых механических и технологических свойств, поэтому наиболее широко в технике (промышленности) используют сплавы.
Металлическим сплавом называется вещество, полученное сплавлением двух и более исходных веществ, преимущественно металлических, и обладающее металлическими свойствами.
В настоящее время сплавы получают:
- сплавлением;
- спеканием (порошковая металлургия);
- электролизом;
- возгонкой (сублимацией);
- плазменным напылением и др.
Вещества, образующие сплав, называются компонентами.
В сплавах компоненты могут различно взаимодействовать друг с другом, образуя те или иные фазы.
Фазой называется однородная по химическому составу, кристаллической структуре, физическим свойствам часть гетерогенной термодинамической системы, отделенная от других ее частей поверхностью раздела, при переходе через которую химический состав или структура изменяются скачком.
Система – это совокупность фаз, находящихся в равновесии и разграниченных поверхностями раздела.
При кристаллизации сплавов могут образовываться следующие основные твердые фазы: твердые растворы, химические соединения, механические смеси.
Твердыми растворами называют фазы, в которых один из компонентов сплава сохраняет свою кристаллическую решетку, а атомы другого или других компонентов располагаются в кристаллической решетке первого компонента (растворителя), изменяя ее размеры (периоды).
Твердые растворы имеют металлический тип связей. По характеру распределения атомов растворенного вещества в кристаллической решетке растворителя различают твердые растворы: замещения, внедрения, вычитания (рис. 5.1).
Рис. 5.1. Схема строения кристаллических решеток: а – твердый раствор замещения; б – твердый раствор внедрения.
Твердые растворы замещения образуются при замене атомов в кристаллической решетке растворителя атомами растворенного компонента (рис. 5.1а). Твердые растворы замещения могут быть с ограниченной и
неограниченной растворимостью и могут быть образованы при соблюдении следующих условий:
- компоненты должны обладать одинаковыми по типу кристаллическими решетками;
- различие в атомных радиусах компонентов не должно быть больше 8-13 % (при разности атомных радиусов меньше 8 % происходит полная взаимная растворимость одного компонента в другом и образуется неограниченный твердый раствор; при разности атомных радиусов в пределах 8-13 % получаются растворы ограниченной растворимости одного компонента в другом; при разности атомных радиусов больше 15 % имеет место полная взаимная нерастворимость и образование механической смеси или химического соединения);
- компоненты должны принадлежать к одной и той же группе периодической системы элементов или к смежной, обладать близким строением валентной оболочки атомов (чем больше разница в валентности элементов, вступающих во взаимодействие, тем меньше растворимость).
Например: В одновалентной меди (Cu), имеющей гранецентрированную кубическую решетку (ГЦК) растворяется 38 % Zn (2-валентного), 9 % Al (3 – валентного), 6 % As ( 5 – валентного). В системе Au – Ag существует полная взаимная растворимость.
Твердые растворы внедрения (рис.5.1б)образуются только в том случае, если внедряемые атомы имеют малые размеры и проникают в поры кристаллической решетки растворителя (H, C, N, B).
Твердые растворы вычитания образуются на базе металлических соединений (интерметаллидов), в структуре которых имеются узлы кристаллической решетки, не занятые атомами одного из компонентов.
Твердые растворы обозначаются малыми буквами греческого алфавита (рис.5.2)
Рис. 5.2. Схема структуры твердого раствора (компонента В в А)
При определенных условиях атомы растворенного элемента могут занимать определенные места в решетке, т.е. упорядоченно располагаться. Такие твердые растворы называются упорядоченными твердыми растворами (рис.5.3).
Рис. 5.3. Кристаллические решетки упорядоченных твердых растворов в системе Cu – Au
При упорядочении решетки (диффузионный отжиг) изменяется период решетки, но тип решетки остается. Например, упорядоченный раствор CuAu (1:1) имеет гранецентрированную тетрагональную решетку с отношением периодов с / а = 0,935, а неупорядоченный раствор – кубическую гранецентрированную с отношением периодов с / а = 1.
Твердые растворы составляют основу большинства промышленных конструкционных и инструментальных сплавов и обладают хорошей технологической пластичностью.
5.2. Химические соединения
Характерными особенностями химических соединений являются:
- кристаллическая решетка отличается от решеток компонентов, образующих соединение (рис.5.4). Атомы в решетке химического соединения располагаются упорядоченно, т.е. атомы каждого компонента расположены закономерно и по определенным узлам решетки. Большинство химических соединений имеют сложную кристаллическую структуру;
- в соединении всегда сохраняется простое кратное соотношение компонентов. Это позволяет выразить их состав простой формулой АnBm, где А и В – соответствующие элементы; n и m – простые числа. Например, у CuAl2 соотношение количества атомов Cu и Al – 1: 2;
- свойства соединения резко отличаются от свойств образующих его компонентов;
- температура плавления (диссоциации) постоянная;
- образование химического соединения сопровождается значительным тепловым эффектом.
Рис. 5.4. Кристаллические решетки: а - Na; б – химического соединения NaCl
Химические соединения делятся на две группы:
- соединения с нормальной валентностью, т.е. соединения металлов с типичными неметаллами. Такими соединениями являются оксиды, сульфиды, хлориды. В сплавах эти соединения присутствуют в виде так называемых неметаллических включений;
- металлические соединения, которые отличаются разнообразием типов межатомных связей (металлической, ковалентной, ионной) и благодаря этому характеризуются металлическим блеском, электропроводностью и в отдельных случаях сверхпроводимостью. Металлические соединения при обычных температурах тверды и хрупки, однако при нагреве до температур, равных 70…90 % от температуры плавления, эти соединения очень пластичны, что объясняется увеличением при нагреве доли металлической связи между атомами.
При промежуточных значениях разности атомных размеров также возможно образование химических соединений. К ним относятся:
- Фазы Лавеса ( устойчивое химическое соединение с ионным типом связи), образующееся между элементами различной природы, атомные диаметры которых находятся приблизительно в соотношении 1: 1,2. Эти фазы удовлетворяют условиям, характеризующим химическое соединение с соотношением атомов, которое укладывается в формулу АВ2. Например: MgZn2, MgNi2..
Фазы Лавеса встречаются как упрочняющие интерметаллидные фазы в жаропрочных сплавах.
- Фазы внедрения, которые образуют металлы переходных групп с металлоидами, имеющими малый атомный радиус. Фазы внедрения образуются, если отношение атомного радиуса металлоида к атомному радиусу металла равно или меньше 0,59. В отличие от фаз Лавеса, при образовании фаз внедрения металлы образуют простые кристаллические решетки (обычно ОЦК, ГЦК, ГПУ). В этом случае образуются химические соединения, которые имеют соотношение атомов, укладывающиеся в простые формулы. Например:
Ме4Х: Fe4N, Mn4N;
Ме2Х: W2C, Mo2C, Fe2N;
МеХ: WC, VC, TiC, NbC, TiN.
Карбиды и нитриды, встречающиеся в сталях, являются фазами внедрения.
5.3. Электронные соединения (фазы Юм – Розари)
Этот вид соединений образуется между двумя металлами группы: Cu, Ag, Au, Fe, Co, Ni, Pt, Pd c металлами группы Be, Zn, Cd, Al, Sn, Si. Соединения этого типа имеют определенное отношение числа валентных электронов к числу атомов, т.е. определенную электронную концентрацию. Каждому соотношению числа валентных электронов и числу атомов соответствует определенный тип кристаллической решетки: при соотношении 3 : 2 (1,5) образуется ОЦК-решетка (b - фаза). Например, химические соединения Cu-Zn, Cu-Be, Cu5Sn, NiAl; при соотношении 21: 13 (1,62) образуется сложная кубическая решетка (g - фаза). Например, химические соединения Cu5Zn8, Cu3Cd8, Cu81Sn8; при соотношении 7: 4 (1,75) образуется гексагональная решетка (e - фаза). Например, химические соединения CuZn3, CuCd3, Cu3Si, Cu3Sn.
При сплавлении переходных металлов, имеющих близкие размеры атомов, образуются фазы переменного состава (s - фаза). Эти фазы имеют частично упорядоченную сложную решетку.
В железных сплавах, содержащих больше 20 % Cr, которые используются как коррозионно-стойкие конструкционные материалы, очень медленное охлаждение из области твердого раствора или изотермические выдержки при 800-600 оС приводят к образованию кристаллов s - фазы, которое сопровождается резким увеличением твердости и охрупчиванием сплавов.
5.4. Механические смеси
Механические смеси образуются при сплавлении компонентов с большим различием атомных радиусов, значительным различием электромеханических свойств, когда их взаимная растворимость очень мала и они не вступают в химическую реакцию с образованием химического соединения. При этих условиях сплав будет состоять из кристаллов (рис. 5.5) исходных компонентов (например: сплавы Pb-Sb, Zn-Sn, Pb-Bi и др.).
Механическая смесь может быть образована:
- в результате кристаллизации, когда из жидкости одновременно кристаллизуются компоненты А и В (эвтектика – ж ® А + В)
- в результате кристаллизации, когда из жидкости одновременно кристаллизуются твердые растворы a и b (эвтектика – ж ® a + b );
- в результате распада твердого раствора на две твердые фазы (эвтектоид – g®a + А nBm).
Рис. 5.5. Условное обозначение механических смесей
6. ДИАГРАММА СОСТОЯНИЯ
Диаграмма состояния – это графическое изображение фазового состояния сплавов в зависимости от температуры и концентрации компонентов в условиях равновесия.
Между тем, следует помнить, что абсолютное отсутствие взаимной растворимости в реальных сплавах не встречается. Компоненты в сплаве обозначают символами их элементов.
Диаграмма состояния позволяет:
- определить для каждого сплава, какие фазы, при каких температурах находятся в равновесии;
- установить состав и количественное соотношение находящихся в равновесии фаз;
- предсказать приблизительно структуру сплава, а иногда определить количественное соотношение структурных составляющих.
Общие закономерности сосуществования устойчивых фаз, отвечающих условиям равновесия, могут быть выражены в математической форме, называемой правилом фаз или законом Гибса.
Правило фаз (или закон Гибса) дает количественную зависимость между степенью свободы системы и количеством фаз и компонентов:
C = K – F + 2,
где (если считать для металлов давление постоянным, т.е. Р - const )
C – число степеней свободы, т.е число внешних ( температура и давление) и внутренних ( концентрация) факторов, которые можно изменить без изменения числа фаз;
K – число компонентов в системе;
F – число фаз.
Пример: если С = 0, то любое изменение температуры вызывает изменение числа фаз; если С = 1, то возможно изменение температуры без изменения числа фаз.
В жидком состоянии:
F = 1 – одна фаза;
К = 1 – один компонент (чистый металл);
С = 1- 1 + 1 = 1 – можно изменять температуру без изменения агрегатного состояния.
В момент кристаллизации:
F = 2 – две фазы (жидкость + кристаллы)
K = 1 – один компонент (чистый металл);
C = 1 – 2 + 1 = 0 – равновесие при строго определенной температуре (Тпл)
Определив степень свободы для чистого металла и сплава в жидком состоянии и в момент кристаллизации, можно построить кривые нагрева в координатах температура – время (рис.6.1, 6.2).
Рис. 6.1. Кривая нагрева Рис. 6.2. Кривая нагрева
чистого металла сплава
Степень свободы для сплава в момент кристаллизации:
F = 2 - две фазы;
K = 2 – два компонента;
С = 2 – 2 + 1.
6.1. Построение диаграмм состояния (равновесия)
Для построения диаграмм состояния, особенно для определения температур затвердевания сплава, используется термический анализ. Для изучения превращений в сплаве в твердом состоянии используют методы физико-химического анализа:
- микроанализ;
- рентгеноструктурный;
- дилатометрический;
- электросопротивления;
- акустический.
Последовательность построения диаграмм термическим методом (компоненты А и В, фазы a , L):
- изготавливают несколько сплавов с известной концентрацией (сплав I, II, III, компоненты А и В) (рис. 6.3);
Рис. 6.3. Диаграмма состояния с образованием неограниченных твердых растворов, построенная термическим методом (диаграмма II рода)
- для каждого сплава строят кривые охлаждения в координатах температура – время, по которым определяют температуры начала и конца кристаллизации сплава;
- строят диаграмму состояния в координатах температура – концентрация, где отмечают точки начала и конца кристаллизации, найденные на кривых охлаждения.
Диаграмма состояния получается при соединении критических точек tA, t1, t3, t5, tB, t6, t4, t2, tA плавными кривыми. Полученная кривая tA t1 t3 t5 tB - геометрическое изображение на диаграмме состояния (точка, линия или поверхность) зависимости температур начала кристаллизации (или завершения расплавления) от химического состава сплава. Такая линия называется линия ликвидус. Кривая tA t2 t4 t6 t8 – геометрическое изображение (точка, линия или поверхность) на диагрмме состояния зависимости температуры конца кристаллизации (или начала плавления) от химического состояния сплава Такая линия называется линия солидус.
Дата добавления: 2016-06-02; просмотров: 1038;