Поверхностная закалка.
Конструкционная прочность многих деталей машин зависит от состояния материала в поверхностных слоях деталей.
Долговечность деталей, работающих в условиях изнашивания (валы, шестерни), зависит от сопротивления поверхности износу.
Разрушение деталей, работающих при изгибающих нагрузках в условиях циклических нагружений, начинается в поверхностных слоях детали. В этих случаях делают поверхностную закалку (при сохранении вязкой сердцевины), либо химико-термическую обработку (ХТО).
При поверхностной закалке нагрев только поверхности можно проводить :
- в расплавленных металлах или солях;
- пламенем ацетелено-кислородной или газовой горелки;
- в электролитах;
- лучом лазера;
- электротоком, индуцируемым в поверхностных слоях детали. Такая закалка называется индукционной или высокочастотной закалкой.
Режим поверхностной закалки: нагрев поверхностного слоя детали до температуры закалки (выше Aс3), быстрое охлаждение в закалочной среде (в воде). В результате такой обработки увеличивается твердость поверхностного слоя детали и повышается его сопротивление истиранию.
Толщина закаленного слоя определяется глубиной нагрева (рис. 9.4).
Рис. 9.4. Изменение температуры по сечению детали к моменту закалки
Участок I, нагретый выше Ас3, получает полную закалку. Участок II , нагретый между Ас1 и Ас3, получает неполную закалку. Участок III не нагревается и не получает закалки.
Схема индукционного нагрева для закалки токами высокой частоты (ТВЧ) представлена на рис.9.5.
Рис. 9.5.Схема индукционного нагрева: а – распределение магнитного потока в индукторе; б – напрвление токов в индукторе и детали;
1 – нагреваемая деталь; 2 – виток индуктора; 3 – магнитные силовые линии; 4 – направление тока в индукторе; 5 – направление тока в детали
Толщина закаленного слоя при поверхностной закалке определяется по формуле:
δ = 500 √ ρ / μ * f,
где ρ - удельное сопротивление детали, Ом*см;
μ - магнитная проницаемость, Гс/э;
f - частота тока, Гц.
Для нагрева детали используют специальные машинные генераторы (с частотой тока от 500 до 15 000 Гц) или ламповые генераторы (с частотой тока до 10 000 000 Гц).
Время нагрева при поверхностной закалке составляет 3-5 с. После нагрева следует охлаждение в закалочной среде (в воде).
В результате быстрого душеобразного охлаждения (закалки) получают мелкоигольчатый мартенсит с малой хрупкостью и повышенной прочностью. Для закалки ТВЧ используют углеродистые стали с содержанием углерода более 0,40 % С. Температура нагрева при ТВЧ выше, чем в обычных случаях и при такой обработке получается мелкое действительное зерно аустенита.
К преимуществам закалки ТВЧ относятся:
- высокая производительность;
- отсутствие окисления поверхности;
- мелкозернистая структура (тонкий мартенсит) в поверхностном слое;
- автоматизация процесса;
- выборочная закалка элементов детали.
Недостатками закалки ТВЧ являются высокая стоимость оборудования и применение только в крупносерийном производстве.
9.4. Закаливаемость и прокаливаемость
Выбор охлаждающей среды при термической обработке определяется закаливаемостью и прокаливаемостью стали.
Закаливаемость - способность стали принимать закалку, т.е. приобретать при закалке высокую твердость поверхности (определяется содержанием углерода в стали; при содержании углерода ниже 0,2 % сталь практически не закаливается).
Прокаливаемость - способность стали получать закаленный слой с мартенситной или троостито-мартенситной структурой с высокой твердостью на ту или иную глубину. Глубиной считают расстояние от поверхности до слоя, где в структуре содержится 50 % мартенсита + 50 % троостита.
Чем больше устойчивость переохлажденного аустенита, чем меньше критическая скорость закалки, тем больше прокаливаемость стали (рис. 9.6).
Рис. 9.6. Схемы, показывающие различную скорость охлаждения по сечению
Характеристикой прокаливаемости является критический диаметр (Дкр).
Критический диаметр - это максимальный диаметр прутка, прокаливающийся насквозь в данном охладителе.
Определяют прокаливаемоеть экспериментально. Основной способ определения прокаливаемости - стандартный метод торцевой закалки (ГОСТ 5657-69 ) (рис.9.7).
|
|
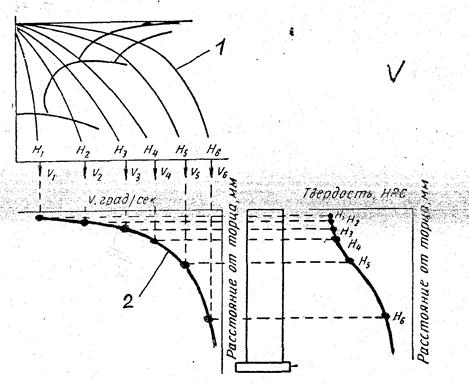
Рис. 9.7. Количественная связь термокинетической -диаграммы(1) с графиком прокаливаемости, построенным методом торцевой закалки (2)
Метод торцевой закалки для определения прокаливаемости заключается в следующем:
- нагревают образец до заданной температуры;
- охлаждают с торца. При таком охлаждении нижний торец охлаждается с максимальной скоростью и скорость охлаждения убывает по мере удаления от торца;
- измеряют твердость по длине образца, начиная от торца;
- изображают графически результаты промера твердости на торце и по длине образца, определяют зону, содержащую 50 % мартенсита + 50 % троостита;
- определяют Дкр по номограммам (рис. 9.8).
Рис. 9.8. Номограмма прокаливаемости (М.Е.Блантер)
Прокаливаемость стали прямо пропорциональна содержанию в ней углерода. Легирующие элементы, входящие в состав стали, уменьшают критическую скорость закалки и увеличивают прокаливаемость.
10. ВНУТРЕННИЕ НАПРЯЖЕНИЯ
Напряжения, возникающие между микро- или макроэлементами тела, вследствие воздействия на это тело внешних (давление) или внутренних (при тепловом воздействии, фазовом превращении) сил, вызывающих деформацию, называются внутренними напряжениями.
Термические напряжения возникают при неравномерном нагреве или охлаждении. В соответствии с названием технологического процесса напряжения бывают литейные, сварочные, закалочные, шлифовочные.
Закалочные напряжения возникают в материале при охлаждении его с температуры закалки; их величина зависит от состава материала и условий закалки. Закалочные напряжения делятся на напряжения I, II и III рода.
Напряжения nepвoгo рода - это зональные остаточные напряжения, уравновешивающиеся в зонах, соизмеряемых с размерами всего тела или отдельных макрочастей. Образуются такие напряжения из-за разницы температур по сечению детали при охлаждении и различных по времени протекания фазовых превращений в разных частях детали.
Напряжения второго рода – это остаточные напряжения, уравновешивающиеся в объемах, соизмеримых с размерами зерна металла.
Напряжения третьего рода – это напряжения, возникающие при фазовых превращениях в металлах и сплавах в твердом состоянии, вследствие различий в удельных объемах образующихся и исходных фаз. Удельный объем аустенита при содержании углерода от 0,2-1,4 % составляет 0,12227-0,12528 см3/г, а мартенсита - 0,12708-0,13061 см3/г.
Для снятия внутренних напряжений после закалки проводят отпуск.
11. ОТПУСК
Отпуском называется нагрев закаленной стали до температуры ниже критической точки А1 (рис.7.1), выдержка при этой температуре с последующим охлаждением на воздухе. В данном случае исходной структурой является структура закаленной стали, состоящая из тетрагонального мартенсита и остаточного аустенита, которые являются неустойчивыми структурными составляющими. Переход стали в устойчивое состояние сопровождается превращениями мартенсита и остаточного аустенита. Эти превращения имеют диффузионный характер и скорость их протекания в основном определяется температурой нагрева при отпуске.
Отпуск относится к окончательной термической обработке.
Целью отпуска являются: изменение строения и свойств закаленной стали, повышение вязкости и пластичности, уменьшение твердости, снижение внутренних напряжений.
В зависимости от температуры нагрева различают три вида отпуска:
- низкотемпературный отпуск, при котором проводят нагрев стали до 150-250 оС и выдерживают 1-3 часа. В результате получают структуру отпущенного (кубического) мартенсита и снимают закалочные напряжения.
Низкий отпуск проводят для инструментальных сталей, сталей после цементации, сталей после поверхностной закалки;
- среднетемпературный отпуск, при котором проводят нагрев стали до 250-400 оС и выдерживают около 1 часа. В результате получают структуру троостита (бейнита). Такой отпуск проводят при изготовлении пружин и рессор;
- высокотемпературный отпуск, при котором проводят нагрев до 450-650 оС и выдерживают около 1 часа. В результате получают структуру сорбита. Проводят такой отпуск для деталей машин, работающих в условиях ударных нагрузок.
При закалке без полиморфного превращения применяется отпуск, который называется старением. Главный процесс при старении – это распад пересыщенного твердого раствора, полученного при закалке. После старения увеличиваются прочность и твердость, уменьшается пластичность, стабилизируются свойства.
Основными видами старения являются:
- естественное (выдержка при комнатной температуре);
- искусственное (выдержка при повышенной температуре);
- деформационное (сплав после закалки подвергают деформации).
Применяют старение при термической обработке алюминиевых сплавов, сплавов меди, жаропрочных сплавов.
12. ХИМИКО-ТЕРМИЧЕСКАЯ ОБРАБОТКА (ХТО)
Химико-термическая обработка (ХТО) - это термическая обработка, сочетающая тепловое воздействие с химическим, в результате чего изменяется состав и структура в поверхностных слоях, а иногда и по всему объему изделия.
В результате ХТО происходит изменение свойств поверхностного слоя детали, т.е. повышаются твердость, износостойкость, жаростойкость, окалиностойкость, коррозионная стойкость.
Обычно при ХТО деталь помещают в среду, богатую элементом (карбюризатор), который диффундирует в металл.
При ХТО происходят три элементарных процесса:
- диссоциация, когда под действием температуры в карбюризаторе происходит распад молекул и образование активных атомов диффундирующего элемента;
- адсорбция, которая происходит на границе карбюризатор – деталь и состоит в поглощении (растворении) поверхностью свободных активных атомов, получившихся после диссоциации;
- диффузия, в результате которой происходит проникновение насыщающего элемента вглубь металла.
В зависимости от диффундирующего насыщающего поверхность элемента различают следующие виды ХТО:
- цементацию (углерод);
- азотирование (азот);
- нитроцементацию (азот + углерод);
- сульфаазотирование (сера + азот);
- алитирование (алюминий);
- хромирование (хром).
12.1. Цементация стали
При цементации происходит поверхностное насыщение стали углеродом, в результате чего получается высокоуглеродистый поверхностный слой, а сердцевина стали остается мягкой и вязкой, несмотря на то, что сталь после цементации подвергается закалке.
Цементация выгодно распределяет углерод от поверхности, а термическая обработка (закалка) упрочняет деталь, поверхность и сердцевину.
Поверхность стали после такой обработки имеет высокую твердость и износостойкость при вязкой сердцевине.
Цементации подвергают низкоуглеродистые и легированные стали с содержанием углерода меньше 0,3 %, которые должны обладать:
- закаливаемостью на 29-43 HRC (углеродистые 08, 10, 15, 20; легированные 20ХГТ, 12ХН2);
- прокаливаемостью, обеспечивающей требуемую структуру сердцевины;
- наследственно-мелкозернистостью;
- хорошей технологичностью при насыщении углеродом и последующей термической обработке и обработке резанием.
Различают два вида цементации: твердую и газовую.
Долговечность и надежность цементированных деталей и допустимый уровень их нагружения при эксплуатации определяются следующими параметрами:
- составом стали;
- толщиной и структурой цементированного слоя (рис.12.1);
- наличием дефектов в слое;
- твердостью поверхностных слоев и сердцевины.
Рис. 12.1. Толщина и структура цементированного слоя
На цементацию детали поступают с припуском на шлифование 0,05- 0,1мм; температура цементации выше Ас3 (930-950 оС). В твердом карбюризаторе 1 мм слоя образуется в течение 8-10 ч, в газовом - 1 мм образуется за 6 - 7 ч.
Твердый карбюризатор - древесный активированный уголь, каменноугольный полукокс и торфяной кокс с добавками активизаторов (BаCО3 и Na2СО3) в количестве 10 - 40 % от веса угля.
Газовый карбюризатор - природный газ и жидкие углеводороды.
Для неответственных деталей закалка их может производиться сразу с температур цементации (рис. 12.2,а) или после повторного нагрева до температуры выше Ас1 на 30 оС и охлаждении в воде (рис. 12.2, б).
Для ответственных деталей после цементации делают двойную закалку с нагревом выше Ас1 + 30 оС и охлаждением в воде (рис. 12.2, в).
После любого режима термической обработки делается низкий отпуск (160-180 оС).
Глубина цементированного слоя составляет 0,5 - 2,0 мм (иногда до 4 мм) с концентрацией углерода 0,8 - 1,2 % ( рис. 12.1).
За глубину цементированного слоя принимают глубину слоя со структурой заэвтектоидной, эвтектоидной и доэвтектоидной стали с содержанием углерода более 0,4 % (рис.12.1).
|
|
|
|
|
|
|
|
|
|
|
|
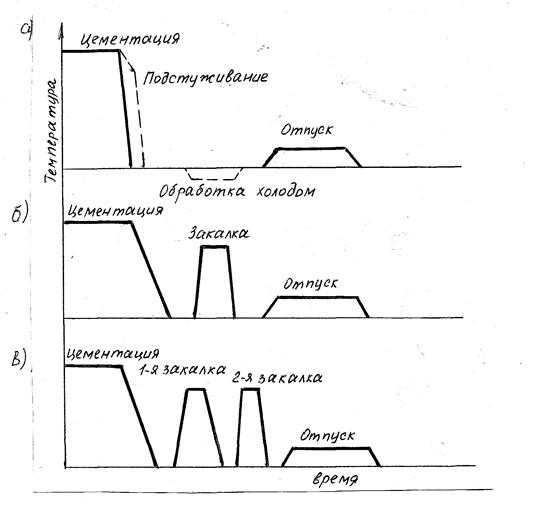
Рис. 12.2. Режимы термической обработки цементированных деталей
При цементации получаем твердость поверхностного цементированного слоя углеродистой стали 60-64 HRC (900HV), для легированной 58-61HRC (снижение твердости происходит за счет наличия в структуре остаточного аустенита); твердость сердцевины составляет 20-35HRC.
12.2. Азотирование стали
Азотирование – это процесс насыщения поверхностного слоя азотом.
Цель такой обработки изделия: получение высокой твердости, износостойкости, повышенной усталостной прочности, сопротивления коррозии. Карбюризатором является аммиак (NH3 → 3H + N).
Азотированию при температуре 500 - 600 оС с выдержкой до 60 часов подвергают готовые изделия, прошедшие механическую и окончательную термическую обработку (закалку и высокий отпуск).
К азотируемым сталям относятся среднеуглеродистые стали, легированные хромом, молибденом, алюминием (38Х2МЮА, 35ХМА, 38Х2Ю).
Глубина азотированного слоя составляет 0,3 - 0,6 мм, скорость азотирования – 0,01 мм/ч и менее.
Твердость азотированного слоя по Виккерсу составляет ~ 1200HV.
Азотированию подвергают мерительный инструмент, гильзы, цилиндры, зубчатые колеса, шестерни, втулки, коленчатые валы.
13. ТЕРМОМЕХАНИЧЕСКАЯ ОБРАБОТКА
Термомеханическая обработка стали (ТМО) заключается в сочетании пластической деформации стали в аустенитном состоянии ("аусформинг") с закалкой.
Различают два способа ТМО - это высокотемпературная термомеханическая обработка (ВТМО) и низкотемпературная термомеханическая обработка (НТМО) (рис.13.1).
Рис. 13.1. Схема термомеханической обработки стали: а – ВТМО; б – НТМО (заштрихованная зона – интервал температур рекристаллизации)
ТМО обоих видов заканчивается низким отпуском при 100-200 оС. При ТМО повышается весь комплекс механических свойств и особенно пластичность и вязкость, что наиболее важно для высокопрочного состояния. По сравнению с обычной обработкой прирост прочности при ТМО составляет 200-500 МПа, т.е. 10-20 %. Характеристики пластичности и вязкости повышаются в 1,5-2 раза.
Улучшение комплекса механических свойств обусловлено формированием специфического структурного состояния. Деформация создает в аустените высокую плотность дислокаций, образующих из-за процесса полигонизации устойчивую ячеистую субструктуру, которая наследуется мартенситом при закалке. При этом субграницы тормозят движение дислокаций и локализируют деформацию внутри зерна; в результате прочность повышается. В то же время субграницы ведут себя как полупроникаемые барьеры. Они допускают прорыв дислокаций, их передачу из мест скоплений в соседние субзерна. Это вызывает пластическую релаксацию локальных напряжений и служит причиной повышенных пластичности и вязкости.
Наибольшее упрочнение (σв ≤ 2800 МПа) достигается при НТМО. Однако ее проведение технологически более сложно, чем ВТМО. Она требует мощных деформирующих средств и пригодна для легированных сталей с большой устойчивостью переохлажденного аустенита.
ВМТО обеспечивает меньшее упрочнение (σв ≤ 2400 МПа ), но более высокие пластичность и вязкость. Она уменьшает также чувствительность к трещине, снижает порог хладноломкости, повышает сопротивление усталости и затрудняет разупрочнение при отпуске, что связано с устойчивостью ячеистых дислокационных структур мартенсита. Особенно эффективна ВТМО для чистого вакуумированного металла. Кроме того, ВТМО более технологична и для неё пригодны любые конструкционные стали.
Область ВТМО расширяет явление обратимости эффекта упрочнения. Оно состоит в том, что свойства, полученные при ВТМО, наследуются после повторной закалки. Это позволяет закладывать определенный ресурс свойств в стальные полуфабрикаты (поковки, прутки, листы и т.п.), подвергая их ВТМО на металлургическом заводе.
14. ЛЕГИРОВАННЫЕ СТАЛИ И СПЛАВЫ
Легирование - целенаправленное изменение состава материала путем введения легирующих элементов для изменения структуры и получения требуемых свойств.
14.1. Влияние легирующих элементов на превращения в сталях
Все элементы, которые растворяются в железе, влияют на температурный интервал существования его аллотропических модификаций, т.е. сдвигают точки А3 и А4 по температурной шкале (рис.14.1). Элементы, которые только растворяются в феррите или цементите, не образуя специальных карбидов, оказывают лишь количественное влияние на процессы превращения. Карбидообразующие элементы вносят не только количественные, но и качественные изменения в кинетику изотермического превращения.
Рис. 14.1. Влияние легирующих элементов на полиморфизм железа: а – Ni, Mn (аустенитные); б – Mn; в – V, Si, Al, Cr, W, Mo (ферритные); г – B, Zn, Nb
Легирующие элементы оказывают большое влияние на положение точек S (0,8 % С) и E (2,14 % С) диаграммы «железо-цементит» (рис. 7.1):
Ni, Co, W, Cr, Mn снижают, а V, Ti, Nb повышают.
Легирующие элементы в стали могут быть в твердом растворе, карбидной фазе или в виде интерметаллических соединений и влияют на свойства феррита и аустенита по мере увеличения их содержания в сталях (рис. 14.2).
Рис. 14.2. Влияние легирующих элементов на свойства феррита
При высоком содержании легирующих элементов часто образуются интерметаллические соединения: Fe7Mo6, Fe2Mo6, Fe2W, Fe7W6; силициды: FeSi, Fe3Si, Fe5Si3 (η - фаза), Fe Cr (σ - фаза).
По отношению к углероду легирующие элементы делятся на три группы:
- графитизирующие - Si, Ni, Си, Al ;
- нейтральные - Со ;
- карбидообразующие (по возрастающей степени сродства к углероду и устойчивости карбидных фаз располагаются в следующем порядке: Fe → Mn → Cr → Mo → W→ Nb → V → Zn → Ti).
При малом содержании Mn, Сr, W, Mo карбидообразующие растворяются в цементите и образуют легированный карбид типа (FeMn)3С; (FeCr)3С. Более сильные карбидообразующие - Ti, Zn, V, Nb - образуют специальные карбиды (TiС, NbС, ZnС, VС).
Карбиды в легированных сталях можно разделить на две группы: карбиды типа (М - металл) - М3С2, М7,С3 , M23C6 и M6C (M4C), которые легко растворяются в аустените при нагреве и карбиды типа MC (TiС, NbС, ZnC), W2C и Мо2C, являющиеся фазами внедрения и которые в реальных условиях не растворяются в аустените.
Все карбиды обладают высокой температурой плавления и высокой твердостью. Чем дисперснее карбиды, тем выше прочность и твердость.
14.2. Влияние легирующих элементов на кинетику распада аустенита
Некарбидообразующие элементы, кроме Со, замедляют кинетику распада аустенита (рис.14.3,а).
Карбидообразующие элементы вносят не только количественные, но качественные изменения в кинетику изотермического превращения аустенита (рис.14.3,б).
Рис. 14.3. Диаграммы изотермического распада аустенита:
а – углеродистая (1) и легированная некарбидообразующими элементами (2);б – углеродистая (1) и легированная карбидообразующими элементами (2)
Наиболее важной способностью легирующих элементов является замедление скорости распада аустенита в районе перлитного превращения (смещение линии вправо). Это снижает критическую скорость закалки и способствует глубокой прокаливаемости.
Сильно увеличивается прокаливаемость стали при легировании Cr, Ni, Mo, Mn, и особенно она увеличивается при совместном легировании несколькими элементами (Cr + Ni + Mo).
Эффективно влияют на прокаливаемость малое количество бора (оптимально 0,002 - 0,006 %). При большом содержании бора образуются бориды и прокаливаемость уменьшается.
14.3 Влияние легирующих элементов на мартенситное превращение
Легирующие элементы, меняя температурный интервал Мн и Мк (рис.14.4), уменьшают или увеличивают количество остаточного аустенита.
Все легирующие элементы уменьшают склонность аустенитного зерна к росту; исключение составляют марганец (Мn) и бор (В).
Рис. 14.4. Влияние легирующих элементов на температуру мартенситного превращения (а) и количество остаточного аустенита в стали с 1,0 % С (б)
Легирующие элементы замедляют распад мартенсита при отпуске (весьма существенно Сг, Mо, Si, Ti) и повышают температуры фазовых превращений, тем самым повышая красностойкость стали.
14.4. Классификация легированных сталей
Классификация легированных сталей производится по следующим признакам:
- по равновесной структуре;
- по структуре после охлаждения на воздухе;
- по составу;
- по назначению.
Поравновесной структуре легированные стали делятся на:
- доэвтектоидные стали, имеющие в структуре избыточный феррит;
- эвтектоидные, имеющие перлитную структуру;
- заэвтектоидные, имеющие в структуре избыточный вторичный карбид;
- ледебуритные стали, имеющие в структуре первичные карбиды, выделяющиеся из жидкой фазы.
Пример: При содержании 5 % Сr сталь с 0,6 % С является заэвтектоидной, а с 1,5 % С - ледебуритной.
Поструктуре после охлаждения на воздухе (рис.14.5) выделяют три основных класса легированных сталей: перлитный, мартенситный, аустенитный.
Рис. 14.5. Диаграмма изотермического распада аустенита сталей:
а - перлитного класса (0,1 - 1,5 % С), содержащих менее 5 - 7 % легирующих элементов; б - мартенситного класса (0,3 - 0,6 % С), содержащих 10 - 15 % легирующих элементов; в - аустенитного класса (0,1 - 0,5 % С), содержащих более 15 % легирующих элементов
Посоставу стали делятся на:
- никелевые;
- хромистые;
- кремнистые;
- хромоникельмолибденовые.
По назначению легированные стали делятся на:
- конструкционные (цементуемые, улучшаемые), строительные низколегированные;
- инструментальные: для режущего инструмента (быстрорежущие); для штампового инструмента; для мерительного инструмента;
- стали и сплавы с особыми свойствами: нержавеющие, жаростойкие, теплостойкие, с особенностями теплового расширения, с особыми магнитными свойствами.
14.5. Принципы комплексного легирования
Всё чаще в промышленности разрабатываются и применяются новые комплексно легированные стали и сплавы. Такой подход позволяет сократить расход дорогостоящих легирующих элементов (например, вольфрам) не снижая, а, как правило, повышая многие свойства сталей и сплавов.
Комплексное легирование проводится для того, чтобы:
- повысить устойчивость аустенита к переохлаждению и распаду, так как легирующие элементы снижают критическую скорость закалки;
- увеличить прокаливаемость;
- уменьшить склонность стали к pocту аустенитного зерна;
- увеличить степень дисперсности карбидных фаз после закалки и отпуска;
- упрочнить феррит;
- повысить температуру рекристаллизации;
- уменьшить склонность стали к отпускной хрупкости;
- улучшить обрабатываемость сплава;
- уменьшить склонность стали к деформации (короблению) при термической обработке (так как используются "мягкие" охлаждающие среды);
- увеличить запас вязкости и сопротивление хладноломкости;
- увеличить эксплуатационную надежность детали;
- улучшить свариваемость.
Легированные стали без термической обработки не применяются.
14.6. Технологические особенности термической обработки легированной стали
Легирование, изменяя скорости и температуры фазовых превращений, а также тепловые характеристики (теплопроводность) стали, существенно влияет на режим термической обработки.
Нагрев под закалку необходимо проводить медленно, так как легирование уменьшает теплопроводность стали. Время выдержки увеличивается для завершения фазовых превращений и выравнивания состава. Температура нагрева под закалку легированной стали выше, чем у нелегированной углеродистой при одинаковом содержании углерода.
Охлаждение легированных сталей после нагрева и выдержки проводится со значительно меньшей скоростью (масло, воздух), чем нелегированных углеродистых.
Так кaк легирующие элементы снижают Мн и увеличивают количество остаточного аустенита, для более полного превращения аустенита в мартенсит дополнительно проводят обработку стали холодом, либо проводят два или три отпуска. Такая обработка повышает твердость после отпуска за счёт распада остаточного аустенита на мартенсит отпуска.
14.7. Особенности отпуска легированной стали
Легирующие элементы оказывают количественное и качественное влияние на фазовые превращения при отпуске.
Количественное влияние заключается в изменении скоростей и температурных интервалов фазовых пpeвращений при отпуске.
I превращение в стали (П→ А) сопровождается выделением углерода из мартенсита ( с/а → 1). В углеродистых сталях тетрагональность решетки стали исчезает при 300 °С. С введением Сг, V, Ti, W, Mo, Si эта температура поднимается до 450 – 500 оС и повышается красностойкосгь стали.
При II - ом превращении в стали (А → Ф + Ц) легирующие элементы повышают устойчивость переохлажденного аустенита, тем самым увеличивая кoличество остаточного аустенита (до 30 %), который при отпуске превращается в мартенсит отпуска при более высокой температуре, чем у не легированных сталей. Вольфрам (W) и хром (Cr) повышают температуру коагуляции до 450 оС, молибден (Mo) - до 550 °С. Карбидообразующие элементы замедляют процесс коагуляции.
Качественное влияние легирующих элементов при отпуске легированных сталей заключается в появлении новых эффектов при отпуске закаленных сталей: карбидного превращения и вторичной твердости.
После III –го превращения (А → М), которое идет при более высокой температуре (450-500 оС), некарбидообразующие элементы (Co, Ni, Si) диффундируют из цементита в перлит (Ц→ П), карбидообразующие (Cr, Mn, W, Mo) из феррита в цементит (Ф → Ц).
В момент предельного насыщения цементита легирующим элементом происходит карбидное превращение; легированный цементит превращается в специальный карбид (Fe Ме)3С, (Cr Fe)23C6.
Явление вторичной твердости заключается в повышении твердости после отпуска в интервале достаточно высоких температур 500 - 600 °С. Это явление связано с превращением остаточного аустенита в мартенсит и образованием высоко дисперсных спецкарбидов, которые заклинивают плоскости скольжения и повышают твердость.
15. КОНСТРУКЦИОННЫЕ МАТЕРИАЛЫ
Конструкционными называют материалы, предназначенные для изготовления деталей машин, приборов, инженерных конструкций, подвергающихся механическим нагрузкам.
Выбор стали для изготовления деталей определяется:
- условиями работы;
- величиной и характером напряжений, возникающих в процессе эксплуатации;
- размерами и формой детали.
Выбранная сталь должна удовлетворять эксплуатационным, технологическим и экономическим требованиям.
Эксплуатационные требования имеют первостепенное значение, так как должны обеспечить работоспособность, надежность и конструктивную прочность материала.
Конструктивная прочность - это определенный комплекс механических свойств, обеспечивающий длительную и надежную работу материала в условиях его эксплуатации.
Конструктивная прочность определяется четырьмя основными критериями: жесткостью, прочностью, сопротивлением хрупкому разрушению, надежностью.
Жесткость конструкции - структурно не чувствительная характеристика, зависящая только от природы материала (межатомных связей). Показателем жесткости является модуль продольной упругости (Е) (модуль жесткости). Обычно в совокупности с Е учитывают плотность (γ ) материала и используют критерий удельной жесткости (Е / γ) , что очень важно в самолетостроении.
Прочность - способность конструкции сопротивляться деформациям и разрушениям. Характеристики прочности определяют в результате статического испытания на растяжение (σв ; σ0,2). Эти характеристики зависят от структуры стали и термической обработки. Прочность изменяется в широких пределах от 100 до 3500 МПа. Как и в случае жесткости, обычно учитывают плотность материала и оперируют понятиями удельной прочности:
σв / γ ; σ0,2 / γ.
По этим показателям высшие значения имеют титановые сплавы.
Модуль упругости Е и предел текучести σ0,2 являются расчетными характеристиками, определяющими допустимую нагрузку.
Надежность - свойство изделия выполнять заданные функции, сохраняя свои эксплуатационные показатели в заданных пределах в течение требуемого промежутка времени или требуемой наработки (в часах). Главный показатель надежности - запас вязкости материала.
Сопротивление материала хрупкому разрушению является важнейшей характеристикой, определяющей надежность.
Долговечность - свойство изделия сохранять работоспособность до предельного состояния (невозможность дальнейшей эксплуатации). Долговечность зависит от условий эксплуатации и определяется:
- сопротивлением износу при трении;
- состоянием поверхности;
- коррозионной стойкостью материала.
15.1. Классификация конструкционных сталей
Конструкционные стали по условиям работы делятся на автоматные, улучшаемые, высокопрочные, цементуемые, азотируемые, пружинно-рессорные, шарикоподшипниковые.
- автоматные стали отличаются высокой обрабатываемостью резанием при изготовлении деталей на станках-автоматах в массовом производстве (винты, болты, гайки).
Для улучшения обрабатываемости в углеродистых сталях допускается повышенное количество серы и фосфора (0,08-0,3 % S и 0,06 % Р). Марки автоматной стали – А11, А12, A30, А35 (А - автоматная, цифры - сотые доли процентов углерода). Для улучшения обрабатываемости, повышения стойкости инструмента, повышения скорости резания легированных сталей дополнительно вводят Pb, Са, Se (селен), Те (теллур).
Марки сталей: AC38Г2, АС20ХГНМ (с добавками свинца 0,15- 0,3 %), АЦ30,АЦ20ХН3 (с добавками Са 0,002 - 0,008 %), АС40ХЕ (с добавкой Se).
- улучшаемые легированные стали содержат углерода 0,3-0,5 % и не более 5 % легирующих элементов. Улучшение сталей достигается закалкой и высоким отпуском. Из этих сталей изготовляют ответственные детали машин и механизмов, работающие в условиях циклических и ударных нагрузок, концентрации напряжений, при низких температурах.
Улучшаемые стали должны иметь:
- высокий предел текучести (σ0,2);
- высокую пластичность с малой чувствительностью к надрезу;
- глубокую прокаливаемость;
- мелкое зерно;
- отсутствие развития отпускной хрупкости.
По прокаливаемости улучшаемые стали делятся на 4 группы:
Глубина закаленного слоя, мм Марка стали
25-35 30X, 40X, 40ХМНА, 40ХФА;
50 - 75 40ХГТР, З0ХГС, 35ХГСА;
70 - 100 30ХН3А, 40XH2MA, 30ХГСНА;
более 100 36Х2Н2МФА, 38ХН3МФА, 18Х2Н4МА.
- высокопрочные стали . К ним относятся среднеуглеродистые, комплекснолегированные стали с пределом прочности (σв) более 1400 - 2000 Мпа:
- полученные при помощи закалки и низкого отпуска;
- термомеханической обработки;
- мартенситостареющие стали.
Si, Mo, W, V снижают разупрочнение при отпуске и измельчают зерно; Сr, Мn обеспечивают глубокую прокаливаемость; Ni снижает чувствительность к надрезам.
Марки высокопрочных сталей 30ХГСНА, 40XГCН3BА, 30X2ГН2BM применяются в самолетостроении в силовых сварных конструкциях, деталях фюзеляжа, шасси.
Высокотемпературная термомеханическая обработка (ВТМО) и низкотемпературная термомеханическая обработка (НТМО) дополнительно обеспечивают следующие свойства:
- более высокую пластичность и вязкость;
- снижают порог хладноломкости;
- снижают чувствительность к отпускной хрупкости;
- повышают усталостную прочность;
- повышают устойчивость к разупрочнению при отпуске;
- цементуемые легированные стали. эти стали содержат малое количество углерода (0,1-0,25 %). Легирование (Сr, Ni, Mо, V, Mn, Ti) укрепляет сердцевину, карбидообразущие увеличивают степень науглероживания поверхностного слоя, измельчают зерно, повышают твердость, износостойкость и контактную выносливость.
Обработка стали проводится в следующей последовательности: цементация + закалка + низкий отпуск. При этом твердость поверхности составляет 58 - 62 HRC, а сердцевины - 20 - 35 HRC.
Марки цементуемых сталей: 15Х, 20X, 15ХФ. Из них изготавливают мелкие валики, шестерни, зубчатые колеса.
Стали марок 12ХН3А, 20ХН3А, 12X2H4A, 20Х2H4A применяют для изготовления крупных деталей (до 100 мм) ответственного назначения.
Стали марок 18Х2Н4МА, 18Х2Н4ВА имеют высокий комплекс механических эксплуатационных свойств и применяются для изготовления зубчатых колес судовых редукторов, валов.
Стали марок 18ХГТ, 30XГT, 25ХГМ используют для изготовления зубчатых колес самолетов, автомобилей, шатунов, шпилек;
- азотируемые легированные стали. Азотирование проводится после улучшения.
Цель азотирования: повысить износостойкость деталей, контактную выносливость, коррозионную стойкость, разгаростойкость.
Сталь марки 38ХМЮА применяется в самолетостроении для зубчатых колес, гильз цилиндров, валиков, роликов; сталь марки 38Х2Ю применяется для изготовления валиков водяных насосов, плунжеров, копиров.
- пружинно-рессорные стали. Эти стали должны иметь особые свойства в связи с условиями работы пружин (цилиндрических, плоских) и рессор.
Основные требования к этим сталям:
- высокий предел упругости (сопротивление малым пластическим деформациям);
- высокий предел выносливости.
Этим условиям удовлетворяют стали с содержанием углерода 0,5 - 0,7 % и стали, легированные Si, Mn, Cr, V, W.
Упрочнение этих сталей достигается закалкой и отпуском при 420 - 520 оС с поверхностным наклепом (обдувкой дробью). Полученная после такой обработки структура троостита обеспечивает отношение σупр / σв приблизительно 0,8 , что повышает надежность работы пружин.
Марки рессорно-пружинных сталей: 70, 65Г, 60С2, 50ХГ, 65С2ВА, 70СЗА. Легированные рессорно-пружинные стали имеют повышенную релаксационную стойкость, обеспечивают длительную работу машин и приборов.
- шарикоподшипниковые стали - заэвтектоидные стали, содержащие более 0,8 % углерода. После отжига, закалки в масло и низкого отпуска получают твердость стали 62 – 65HRC, а структуру - скрытокристаллический мартенсит с мелкими равномерно распределенными карбидами, который обеспечивает:
- равномерную твердость;
- устойчивость против истирания;
- необходимую прокаливаемость;
- достаточную вязкость.
Марки шарикоподшипниковой стали: ШХ15, ШХ15СГ, ШХ6, ШХ9. Для крупногабаритных подшипников (диаметром более 400 мм), работающих в тяжелых условиях при больших ударных нагрузках, применяют цементуемую сталь 20Х2Н4А (цементация проводится при t = 930-950 оС, выдержка 50-170 ч; затем следуют закалка и отпуск). Глубина полученного цементированного слоя составляет 5-10 мм.
- высокомарганцовистые износостойкие стали - стали аустенитного класса, которые имеют высокие сопротивление износу, высокую прочность и низкую твердость.
Марка высокомарганцовистой стали: 110Г13Л.
Высокая износостойкость стали 110Г13Л объясняется упрочнением (наклепом) аустенита при пластической деформации в процессе работы. В поверхностном слое аустенит превращается в мартенсит. По мере износа поверхностного слоя, мартенсит образуется в следующем слое. Сталь 110Г13Л применяют для трамвайных стрелок, щек камнедробилок, козырьков ковшей, черпаков.
- мартенсито-стареющие. Это безуглеродистые стали (С < 0,03 %), имеющие в основе Fе и Ni (8 – 25 % Ni) и легированные Co, Мo Ti, Al, Cr, Nb.
Высокая прочность таких сталей достигается совмещением двух механизмов упрочнения: мартенситного превращения (γ → α) и старения мартенсита.
Ni - стабилизирует γ- твердый раствор, сильно снижая температуру (γ → α) превращения, и оно протекает по мартенситному механизму (сдвиг). Ti, Be, Al, Cu, Mo ограниченно растворяются в α - Fe. Мартенсито-стареющие стали закаливают с температуры 800 – 860 оС на воздухе. Закалка фиксирует пересыщенный железоникелевый мартенсит, который очень пластичен. Упрочнение достигается при старении с t = 450 – 500 °С, когда из мартенсита выделяются высокодисперсные вторичные фазы (Ni3Ti, NiAl, Fe2Mo, Ni3Mo), когерентно связанные с матрицей.
Для мартенсито-стареющих сталей характерны:
- высокий предел текучести;
- низкий порог хладноломкости;
- высокое сопротивление распространению трещин;
- малая чувствительность к надрезам;
- высокое сопротивление хрупкому разрушению;
- высокая конструктивная прочность в широком диапазоне температур от криогенных до 450 - 500 оС;
- высокая технологичность.
Марки мартенсито-стареющих сталей: 03H18K9M5T, 03Н12К15М10, 03Х11H10M2T.
Мартенсито-стареющие стали используют для ответственных деталей в авиации, ракетной технике, приборостроении, судостроении как пружинный материал.
16. ИНСТРУМЕНТАЛЬНЫЕ СТАЛИ И СПЛАВЫ
Инструментальными называют углеродистые и легированные стали, содержащие более 0,7-1,25 % С, обладающие высокой твердостью ( 60-65HRC), прочностью, износостойкостью и применяемые для различного инструмента.
Классификацию инструментальных сталей проводят по двум признакам: по назначению и по свойствам.
По назначению инструментальные стали делятся на режущие (быстрорежущие), ударно-штамповые, мерительные.
По свойствам инструментальные стали делятся на нетеплостойкие (У11, У12, 9ХС, ХВГ, рабочая температура которых 200 –300 оС), полутеплостойкие (средне- и высоколегированные стали, рабочая температура которых 300 - 500 °С); теплостойкие (высоколегированные, быстрорежущие и твердые сплавы и металлокерамика, рабочая температура которых 500-625 оС).
Теплостойкость (красностойкость) - способность материалов сохранять служебные свойства (твердость, прочность) при нагреве до рабочих температур.
16.1. Режущие стали
В процессе работы режущий инструмент работает на износ поверхности.
К износостойким материалам предъявляются требования:
- высокая твердость и мелкозернистая равномерная структура, обеспечивающая большое сопротивление истиранию на контактных поверхностях;
- высокая горячая твердость и горячая прочность при отсутствии склонности к пластической деформации;
- достаточная вязкость при большом сопротивлении внешним силам, действующим на трибосистему;
- термодинамическая устойчивость компонентов структуры (твердых фаз);
- высокая прочность границ зерен между кристаллами твердой фазы и между твердой фазой и связкой;
- незначительная склонность к адгезии с материалом -партнером, особенно при пиковых параметрах нагружения.
Различные механизмы износа часто действуют одновременно (абразивный и диффузионный). Какой из них доминирует, тот и определяет время эффективной работы режущего инструмента (срок службы).
Режущие стали содержат углерода 0,8 –1,25 % . К ним относят:
- углеродистые стали небольшой прокаливаемости: У9,У10, У11, У12. Из этих сталей изготовляют резцы, сверла, напильники;
- легированные стали, основными легирующими элементами которых являются Сr,W, V (9ХФ, 9ХС, 9ХВГ, ХВГ, XВГС).
16.2. Быстрорежущие стали
Быстрорежущие стали применяются для .разнообразного инструмента, работающего при высоких скоростях резания в тяжелых условиях.
Качество (стойкость) инструмента зависит от:
- качества стали;
- тщательности и правильности изготовления;
- правильной термической обработки.
Быстрорежущие стали обладают высокой теплостойкостью и высокой износостойкостью (за счет V, Со, W). К ним относятся стали ледебуритного класса: PI8, Р12, Р6М5, Р6М5К5, Р10К5Ф5, Р9К10, РОФ2К8М6АТ, РОМ5Ф1, Р12М3К8Ф2-МП.
В вольфрамомолибденовых сталях вольфрам заменен молибденом в отношении Мо: W (1:1,4-1,5). Молибден придает стали большую пластичность и плотность; кобальт повышает теплостойкость; ванадий повышает износостойкость, так как карбиды ванадия самые твердые структурные составляющие.
Упрочнения (повышения стойкости) быстрорежущих сталей можно добиться особой термической обработкой (дисперсионное твердение мартенсита), цианированием поверхности (0,02-0,07мм), низкотемпературной термомеханической обработкой (НТМО), плазменным напылением.
16.3. Твердые peжyщие сплавы
Твердые режущие сплавы получают методом порошковой металлургии путем спекания предварительно спрессованного металлического порошка; они обладают исключительной красностойкостью и высокой твердостью. К таким сплавам относятся:
- литые сплавы - стеллиты, сормайты;
- металлокерамические сплавы - победиты.
Компонентами спекаемых твердых сплавов являются:
- кобальт (Со) как связка;
- карбиды вольфрама (WC), титана (TiС), тантала (TаС), ниобия (NbC), ванадия (VС), хрома (СrС).
Функцией кобальта является регулирование вязкости твердого сплава. Карбид вольфрама хорошо смачивается кобальтом, что влияет на схватывание с твердой фазой.
Карбид вольфрама является основой сплавов, обеспечивает прочность на изгиб и кромочную прочность в системе WC – Со.
Карбид титана значительно тверже карбида вольфрама, менее растворим и снижает вязкость сплава.
Карбид тантала замещает карбид вольфрама, повышает теплостойкость, незначительно снижает вязкость сплава по сравнению с карбидом титана.
Промышленностью выпускаются три труппы металлокерамических твердых сплавов:
- WC + Со – группа ВК (ВК6, ВК8);
- WC + ТiС + Со – группа ТК (Т15К6)
- WС + TiC + TaC + Со – группа ТТК (ТТ7К15).
16.4. Штамповые стали
Для обработки металлов давлением применяют следующие инструменты, деформирующие металл: штампы, пуансоны, ролики, валики.
Стали, применяемые для изготовления инструмента такого рода, называют штамповыми сталями.
Штамповые стали делятся на две группы:
- деформирующие металл в холодном состоянии;
- деформирующие металл в горячем состоянии.
Особая группа штамповых сталей - стали для пресс-форм литья под давлением.
Стали для деформирования в холодном состоянии должны обладать высокой твердостью, прочностью, сопротивлением пластической деформации, износостойкостью, вязкостью, теплостойкостью.
Стали с небольшой прокаливаемостъю, имеющие вязкую сердцевину (У10, У11, У12, ХВ, 9С) применяет после закалки и отпуска, цианирования или хромирования, что повышает их износостойкость.
Для крупных штампов применяют стали с повышенной прокаливаемостью (ХГС, ХГСВФ).
Стали для штампов, работающих при ударных нагрузках, содержат 0,4-0,6 % углерода (4ХС, 6ХC, 4ХВ2С, 5ХВ2С, 6ХВ2С).
Стали для деформирования в горячем состояния работают в сложных условиях и должны иметь высокую износостойкость, прочность, сопротивление пластической деформации, повышенную теплостойкость, хорошую окалиностойкость, высокое сопротивление термической усталости.
Деформация сталей происходит при ударе (ковка, штамповка), а при медленном приложении нагрузки (вытяжка, прессование, выдавливание) штамп сильнее нагревается.
В зависимости от условий работы штампы делятся на три группы:
- ковочные;
- для горячей протяжки, высадки и прессования;
- для пресс-форм литья под давлением.
Стали ковочных штампов должны иметь высокую ударную вязкость, теплостойкость и хорошую прокаливаемость. Для таких штампов применяют стали среднеуглеродистые (0,5-0,6 %С), легированные Mn, Ni,.Cr, V, W (5XHМ, 5ХНВ, 5ХГМ, 5ХНСВ, 5ХНТ).
Стали для горячей протяжки, высадки и прессования -высоковольфрамовые с 8-12 % W и 2 % Сг (4Х5В2ФС, 4Х2В5ФМ, 4Х4В4ФМ, 4ХВ2С, 5ХВГ). Эти стали подвергаются особой термической обработке.
Стали для пресс-форм литья под давлением подвергаются износу, коррозии, эррозии и разгару (образованию сетки трещин на поверхности). К таким сталям относятся 3X2B8, 4ХВ2С (тепло - разгаростойкие).
16.5. Стали для измерительных инструментов
Стали для измерительных инструментов должны длительное время сохранять заданные (точные) размеры. Изменение размеров может возникать по трем причинам:
- износ;
- объемные изменения из-за структурных превращений при длительном вылеживании;
- тепловое расширение из-за колебаний температур.
Высокая износостойкость сталей для измерительного инструмента обеспечивается высокой твердостью стали ( 58-64HRC) после термообработки.
Для стабилизации размеров производится специальная термическая обработка (обработка холодом и стабилизирующий отпуск при низких температурах).
Для изготовления измерительного инструмента применяют стали марок: X, XГ, 120ХГ, 50, 55, 38XBФЮA.
17. СТАЛИ И СПЛАВЫ С ОСОБЫМИ СВОЙСТВАМИ
К этой группе относят стали:
- с особыми химическими свойствами (нержавеющие, жаростойкие, жаропрочные);
- с особыми физическими свойствами (магнитные, с малым коэффициентом расширения).
17.1. Нержавеющие (коррозионностойкие) стали
К этой группе относятся стали, обладающие стойкостью против электрохимической коррозии.
Антикоррозионными свойствами обладает сталь в том случае, если она содержит большое количество хрома ( > 12 %) или хрома и никеля.
Применяют три типа хромистых нержавеющих сталей: с содержанием хрома 13, 17 и 27 %, содержащих углерода от 0,1 до 0,04 %.
Стали с содержанием хрома 17-18 % и 25-28 % имеют добавки Ti, Ni, которые вводят для измельчения зерна.
По виду равновесной структуры нержавеющие стали делятся на пять классов:
- ферритные;
- мартенсито-ферритные;
- мартенситные;
- аустенитные;
- аустенито-мартенситные.
Например: сталь 12Х13 – мартенсито-ферритного класса (клапаны гидравлических насосов); сталь 40Х13 – мартенситного класса (хирургический инструмент); сталь 12Х17 – ферритного класса (оборудование азотнокислых заводов и пищевой промышленности); 12Х18Н9Т – аустенитного класса с большой коррозионной стойкостью (химическая, пищевая, нефтяная промышленность, авиастроение, транспортное машиностроение).
17.2. Жаростойкие и жаропрочные стали и сплавы
К жаростойким (окалиностойким) относят стали и сплавы, обладающие стойкостью против химического разрушения поверхности в газовых средах при температуре выше 550 °С и в слабонагруженном состоянии.
Способность стали сопротивляться окислению при высокой температуре называется жаростойкостью (окалиностойкостью).
На интенсивность окисления влияет состав стали и строение окисной (защитной) плёнки, плотность которой повышают такие химические элементы, как Cr, Si, Al.
Сталь 15X5 (5 % Сr) жаростойка до 700 оС, сталь 12X17 (17 % Сr) -до 900 оС, стала 15X28 (28 % Сr) - до 1100 - 1150 оС. Сплавы на никелевой основе с Сr и Al ( ХН70Ю с 26-29 % Сr и 2,8-3,5 % Al ) обладают жаростойкостью до 1200 °С.
Жаропрочность - способность материала сохранять необходимую длительную прочность при высоких температурах.
Ползучесть - это деформация, непрерывно увеличивающаяся и завершающаяся разрушением под действием постоянной нагрузки при длительном воздействии температуры.
Предел ползучести - это напряжение, вызывающее деформацию заданной величины (обычно от 0,1 до 1 %) за определенный промежуток времени (100, 300, 500, 1000 ч) при заданной температуре.
Факторами, способствующими жаростойкости, являются:
- высокая температура плавления основного металла;
- наличие в сплаве твердого раствора и мелкодисперсных упрочняющих фаз;
- пластическая деформация, вызывающая наклеп;
- высокая температура рекристаллизации;
- рациональное легирование;
- термическая и термомеханическая обработка;
- введение в жаропрочные стали бора, церия, ниобия, циркония, (в десятых, сотых и даже тысячных долях).
По температуре эксплуатации жаропрочные стали разделяют на группы:
- для работы при температуре до 350 – 400 оС (обычные конструкционные стали - углеродистые и малолегированные) ;
- для работы при температуре 400 - 550 оС (стали перлитного класса 15ХМ, 12Х1МФ для деталей котлов, труб паропроводов и пароперегревателей, нагруженные сравнительно мало, но работающие до 100 000 ч);
- для работы при температуре 500 - 600 оС (стали мартенситного класса: высокохромистые 15Х11МФ для лопаток паровых турбин; сильхромы 40Х9C2 для клапанов моторов; 20Х12ВНМФ для дисков, роторов, валов);
- для работы при температуре 500 - 750 оС (стали аустенитного класса: нестареющие 09Х14Н16В для труб пароперегревателей высокого давления; стареющие 40Х15Н7Г7Ф2МС для лопаток газовых турбин);
- для работы при температуре 800 - 850- 1200 °С (жаропрочные сплавы на никелевой основе ХН77ТЮР, ХН55ВМТФКЮ для лопаток турбин).
17.3. Криогенные стали и сплавы
Под криогенными сталями и сплавами подразумевают металлические материалы для машин и оборудования, предназначенные для получения, перевозки и хранения сжиженных газов и, следовательно, эксплуатируемых до температур кипения: кислорода (-183 оС), азота (-196 оС), неона (-247 оС), водорода (-253 оС) и гелия (-269 оС), а также сжиженных углеводородов (метила, бутана) (-80...-180 °С).
Стали, работающие при низких климатических температурах (до -50оС), - это стали северного исполнения; от комнатной температуры до -80 оС (4,2 К - температура кипения жидкого гелия) - это криогенные стали аустенитного класса, одновременно нержавеющие.
Сталь 12X18H20 - сталь со стабильным аустенитом, который не претерпевает превращений при низких температурах. При всех температурах σ0,2 / σв = 0,5 (12Х18H10, 12X13AГ19).
Хромоникелевые стали имеют:
- высокую ударную вязкость KCV > 2000 кДж/м2 при комнатной температуре и всех температурах вплоть до –253 °С (кипение жидкого водорода);
- вязкий излом.
Никель снижает порог хладноломкости, повышает прочность стали (σв), увеличивает ударную вязкость (KСV) при -196 °С.
Стали 07Х21Г7АН5 с σ0,2 = 400 МПа и 03Х13Н9Д2ТМ с σ0,2 = 800 МПа являются высокопрочными криогенными сталями.
17.4. Магнитные стали и сплавы
Основными характеристиками магнитных сталей и сплавов являются магнитные свойства:
- остаточная индукция Br (измеряется в гауссах (Гс));
- коэрцетивная сила Нс (измеряется в эрстедах (Э));
- магнитная проницаемость (измеряется в Гc/Э).
Магнитная проницаемость определяется по формуле: μ = В /Нс. Если μ > 1, то материал парамагнитен, если μ < 1 – материал диамагнитный.
К ферромагнитным материалам относятся Fe, Co, N1, имеющие μ »1.
Магнитные сплавы в зависимости от коэрцетивной силы (Нс ) и магнитной проницаемости (μ ) делятся на:
- магнитотвердые сплавы с большой Нс и малой μ, применяющиеся для изготовления постоянных магнитов. Эти высокоуглеродистые, легированные сплавы (ЕХ, ЕХ3, ЕХ5К5, сплав ЮНДК24) имеют высокую твердость, хрупкость и не обрабатываются резанием. Магниты из магнитотвердых сплавов изготавливают литьём или спеканием из порошков;
- магнитомягкие сплавы с малой Нс и высокой μ.
К ним относятся :
- электротехническое железо (Армко) марок Э, ЭА, ЭАА для изготовления сердечников, полюсных наконечников электромагнитов, реле;
- электротехническая сталь, которая по содержанию кремния делится на низколегированную (0,8 – 1,8 % Si) (динамная сталь), среднелегированную (1,8 - 2,8 % Si), повышенно-легированную (2,8 – 3,8 % Si) и высоколегированную (3,8 – 4,8 % Si) (трансформаторная сталь);
- железоникелевые сплавы (пермаллои), содержащие 45-80 % Ni, дополнительно легированные Cr, Si, Mo и имеющие высокую магнитную проницаемость. Пермаллой 79НМ (79 % N1, 4 % Мо) после специальной термической обработки имеет магнитную проницаемость μ0 - 30 000 и μmax - 22O 000 Гс/Э. Применяют эти сплавы в телефонах и радио (слабые электромагнитные поля).
- ферриты, получаемые спеканием порошков ферромагнитной окиси железа Fe2O3 и окислов двухвалентных металлов МО (ZnO, NiО, MgO). В отличие от других магнитомягких материалов у ферритов очень высокое электросопротивление (1012 0м * см), и работают они в области высоких и сверхвысоких частот.
17.5. Сплавы с особенностями электросопротивления
Сплавы с особенностями электросопротивления делятся на три группы:
- проводниковые;
- с высоким электросопротивлением;
- диэлектрики.
К проводниковым сплавам предъявляются следующее эксплуатационные и технологические требования:
- малое электрическое сопротивление;
- высокая прочность (для предохранения от провисания);
- высокая пластичность и способность к холодному и горячему деформированию;
- хорошая коррозионная стойкость;
- легкость пайки и сварки (при монтаже).
Этим требованиям удовлетворяют (в различной степени) Ag, Си, А1, Fe.
Одним из важнейших проводниковых материалов является медь (Сu), которая по свойствам близка к серебру ( плотность ρ = 8,9 г/см2 при 20 оС, удельное электросопротивление – 0,017( Ом*мм)/м2. Кристаллическая решётка меди – ГЦК с параметром а = 0,36 Нм. Удельное электросопротивление меди принимается за эталон.
Марки меди: M1 (99,9 %), Тпл = 1083 оС; МО (99,95 %), Ткип = 2360 °С; МОО (99,99 %). В технической меди могут присутствовать вредные примеси: висмут (≤ 0,002 %), свинец (≤ 0,005 %), сера, кислород, которые уменьшают пластичность меди.
Чистая медь имеет малую прочность, поэтому её легируют кадмием (Cd), что приводит к незначительной потере электропроводности при сохранении достаточно высокой прочности. Проводимость таких сплавов составляет 80-90 % от проводимости чистой меди. Сплав, упрочненный наклепом, имеет проводимость 98 % от проводимости меди.
Алюминий (А1) имеет электросопротивление больше, чем у меди в 1,7 раза, но он легче. Для линий передач применяют сплав альдрей (0,4 % Mg, 0,6 % Si, 0,25 % Fe). К таким сплавам относятся АД000, АД0.
Большую прочность имеют биметаллы системы Fe - A1. Биметаллический провод (стальной провод, покрытый медью) используют при передаче переменных токов повышенной частоты.
Железо (Fe) имеет электросопротивление в 6-7 раз ниже электросопротивления меди. Сплавы железа (сталь с 0,1 – 0,15 % С) применяются для шин, рельсов электрических железных дорог и метро.
17.6. Сплавы с высоким электросопротивлением
Сплавы с высоким электросопротивлением применяют для изготовления элементов сопротивления реостатов и нагревательных элементов. Структура таких сплавов формируется на базе твердых растворов и к ним предъявляются следующие требования:
- они должны обладать высоким удельным электросопротивлением;
- должны иметь малый температурный коэффициент электросопротивления;
- должны обладать высокой окалиностойкостью (жаропрочностью);
- в них должны отсутствовать структурные превращения при нагревах и охлаждениях.
Для элементов сопротивления реостатов применяются сплавы:
- манганин – МНМц 3-12 (11,5-13 % Mn, 2,5-3,5 % Ni,остальное Сu);
- константан - МНМц 40-1,5 (1-2%. Mn, 39-41 % Ni, остальное Сu).
Эти сплавы имеют малый коэффициент электросопротивления: манганин в интервале температур от – 60 до +80 °С и константан в интервале температур от - 60 до + 350 °С.
Для нагревательных элементов применяют сплавы:
- железоалюминиевые: фехраль - Х13Ю4 (≤ 0,15 % С, 13 % Сu, 4 % Al), хромалъ - ОХ23Ю5 (≤
Дата добавления: 2016-06-02; просмотров: 6969;