Электрофизические и электрохимические методы обработки
Электрофизические и электрохимические методы обработки используют для изготовления сложного рабочего контура прессовых матриц, матриц и пуансонов вырубных, пробивных и обрезных штампов, а также инструмента для горячей объемной штамповки. Они характеризуются рядом следующих особенностей: возможность обработки независимо от физико-механических свойств обрабатываемых материалов; небольшие механические усилия при осуществлении процесса обработки; отсутствие необходимости в более твердых инструментах, чем обрабатываемый материал; значительное уменьшение расхода обрабатываемого материала; высокая точность обработки; высокая производительность.
Для размерной обработки при изготовлении деформирующего инструмента широкое применение нашли электроискровая, электроимпульсная, электрохимическая и ультразвуковая обработка. Суть электроискрового метода состоит в следующем (рисунок 35, а). Конденсатор С заряжается через сопротивление R
![]() |
Рисунок 35 - Схема электроискрового (а) и электроимпульсного (б) методов изготовления инструмента: 1 — электрод-инструмент; 2 — диэлектрик жидкий; 3 — ванна; 4 — обрабатываемая деталь; 5 — столик; 6 — генератор импульсов |
от источника постоянного тока. По достижении на конденсаторе напряжения, равного напряжению пробоя, через зазор между электрод-инструментом и деталью происходит разряд. После этого конденсатор заряжается, и процесс повторяется. В результате воздействия, электрического разряда происходит разрушение обрабатываемой детали. Электрический удар, обрушивающийся на электроды в виде эффекта торможения электронов на аноде и ионов на катоде, создает на электродах кратковременно действующие источники тепла, распределенные в области ограниченных размеров. Нестационарный процесс распространения тепла от этих источников вызывает локальное плавление и частичное испарение металла поблизости от источника. Связи пораженных разрядом участков электродов с основной массой металла резко ослабляются, и под действием сил ударной волны расплавленный металл выбрасывается в мёжэлектродное пространство, где и застывает.
С целью увеличения интенсивности электрической эрозии между электродами помещается жидкий диэлектрик (обычно керосин или минеральное масло).
Длительность искрового электрического разряда составляет около тысячной доли секунды. Температура разряда — свыше 10000СС. Съем металла 400—12000 мм/мин. Чистота поверхности—5-7 класс частоты. Материалом для электрода-инструмента могут служить латунь, медь, графит или меднографитовая композиция.
Причины, сдерживающие развитие электроискрового метода, следующие:
форма инструмента-электрода должна соответствовать форме наружного контура обрабатываемой детали или отверстия, а изготовление электрода сложной конфигурации трудоемко;
электрод должен изготавливаться точнее обрабатываемой детали;
одним электродом изготовить несколько деталей невозможно вследствие быстрого износа электрода.
Более производительной по сравнению с электроискровой является электроимпульсная обработка инструмента (рисунок 35, б).
При этом резко уменьшается износ электрод-инструмента (примерно в триста раз). Полярность тока изменена на обратную (катодом является обрабатываемая деталь). Длительность импульса увеличивается до 500...10000 мкс. Температура разряда значительно снижается. Съем обрабатываемого металла происходит не в парообразном, а, в основном, в капельно-жидком состоянии.
Контуры отверстий в матрицах вырезают с помощью электрода в виде тончайшей медленно движущейся проволочки из латуни. Таким образом получают поверхность любого профиля с точностью 0,002 мм и обеспечивают шероховатость поверхности Ra = 1,б...0,8мкм и точность размеров по 7—9 квалитету.
Схема вырезания показана на рисунке 36. Заготовку закрепляют на столе станка, имеющем форму скобы. Заготовка должна иметь предварительно обработанное отверстие для пропускания через него электрода-проволоки. Электрод-проволока вводится в отверстие и во время работы станка сматывается е барабана на барабан, который вращается двигателем через редуктор. Скоба может перемещаться в горизонтальной плоскости в двух взаимно перпендикулярных направлениях с помощью суппортов, которые приводят в действие автоматические регуляторы подачи.
|
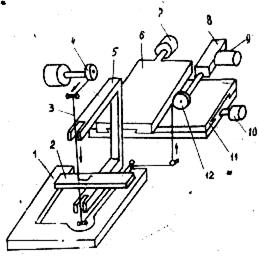
![]() |
![]() |
Рис. 30. Характер разрушения пуансонов штампов холодной штамповки |
Рис. 30. Характер разрушения пуансонов штампов холодной штамповки |
Рис. 30. Характер разрушения пуансонов штампов холодной штамповки |
Автоматические регуляторы работают по программе и обеспечивают вырезание детали требуемого контура.
Электрохимический метод основан на явлении анодного растворения, благодаря которому на изделии воспроизводится профиль катода инструмента в негативной форме (рисунок 37). Специфической особенностью метода является высокая скорость движения электролита (преимущественно раствора NaCl) в зазоре между электродами, величина которого изменяется в пределах 0,1...0,5 мм. Движение электролита обеспечивает удаление продуктов анодного растворения, образующихся в большом количестве, и его охлаждение.
Электроды-инструменты изготавливают из меди, латуни или коррозионно-стойкой стали. Метод характеризуется высокой производительностью и нулевым износом электрода-инструмента, но требует применения источников тока большой силы. При его использовании возникают трудности по вымыванию осадков и образующихся газов. Отмечаются также затруднения управлением процесса при обработке сложнопрофилированных инструментов высокой точности.
Освоение электрохимической обработки профильного инструмента позволило в 15—18 раз сократить время их изготовления и уменьшить стоимость обработки.
![]() |
|
|
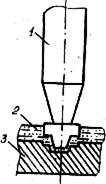
При ультразвуковом методе изготовления электрические колебания высокой частоты 16...25 кГц передаются на торец мастер-инструмента (рисунок 38). Одновременно в зону обработки под торец инструмента поступает суспензия зерен абразива в воде. Колеблющийся с ультразвуковой частотой мастер-инструмент ударяет по зернам абразива, последние выкалывают частицы металла штампа, осуществляя на нем копирование формы мастер-инструмента. В качестве абразива применяют карбид бора, карбид кремния или корунд. Этот метод используется для обработки хрупких материалов с точностью до 0,08 мм и чистотой поверхности Ra = 0,32 мкм.
Дата добавления: 2015-12-10; просмотров: 1180;