Теплофзические свойства углеметалопластиков
характеристики | материалы | ||
УМП-1 | УМП-2 | УМП-3 | |
Теплопроводность | 4,2 | 3,5 | |
Теплоемкость кДж(кг·К) | 1,05 | 0,97 | 1,26 |
Температуропроводность, м2/с | 3·10-6 | 2,2·10-6 | 2·10-6 |
Если сравнивать теплофизические характеристики, такие, как теплопроводность и температуропроводность, то углеметаллопластики имеют большие их значения, чем углепластики, т. е. на первый взгляд, первые менее предпочтительны, чем вторые для работы в условиях РДТТ. Однако за счет меньшего уноса углеметаллопластики в массовом отношении лучше углепластиков, т. е. конструкции из них легче.
К недостаткам углеметаллопластиков нужно отнести следующее:
- у них хуже формуемость по сравнению с углепластиками, поэтому нужно применять более высокие давления прессования; метод вакуумирования для УМП совсем неприемлем;
- значительно хуже, чем для неармированных вольфрамовой нитью пластиков, обрабатываемость резанием;
- в случае применения вольфрамовой нити расходуется дефицитный материал.
6.8. УГЛЕРОД-УГЛЕРОДНЫЕ КОМПОЗИЦИОННЫЕ МАТЕРИАЛЫ
Среди главных задач развития современной ракетно-космической техники на первом месте стоит решение проблемы полезной нагрузки, доставляемой к цели или выводимой на заданную орбиту, при минимальной стартовой массе ракеты. На втором месте - совершенствование твердотопливных двигателей, на третьем - материалы и на четвертом - технология. Но если хорошо проанализировать, то окажется, что две первые проблемы не могут быть решены без внимания к третьей и четвертой.
Кроме того, создание конструкций из композиционных материалов никак нельзя отделить от технологии. Если говорить о материалах, то ни один из классических материалов не может удовлетворить всем требованиям, предъявляемым к конструкциям РКТ, авиации и других областей техники. В последние три - четыре десятилетия очень быстро развивается направление в материаловедении - композиционные материалы, сочетающие в себе все лучшие качества входящих и полученных новых компонентов.
В настоящее время трудно даже назвать количество вновь созданных композиционных материалов, о некоторых было сказано выше.
В течение последних 10... 15 лет начали применяться так называемые углерод-углеродные' материалы, т. е. такие, у которых и матрица и наполнитель являются углеродными. Обычные углепластики, кроме ракетной техники, уже нашли применение в авиации, например, в США и в Украине (НПО им. Антонова). Из них изготовляются крылья самолетов, пропеллеры и т.п. Часто углепластики применяются в сочетании с другими полимерными пластиками (стеклопластиками, органопластиками).
Чем вызвано появление углерод-углеродных материалов? Как известно, при очень высоких температурах наилучшим образом могут реализовать эффективную энтальпию углеродные материалы, т. к. они при этом не плавятся, поскольку тройная точка их находится примерно при температуре 4 500 К и давлении 10 МПа. При создании всех теплозащитных покрытий стремятся к тому, чтобы в связующем было как можно больше углерода, чтобы при работе ТЗП образовался твердый коксовый остаток. Но этот остаток, вследствие удаления продуктов гидролиза и коксования, имеет большую пористость, которая обусловливает повышенный эрозионный унос в газовых потоках больших скоростей и температур. Покрытие считается работоспособным, если его пористость, выраженная через газопроницаемость, была меньше 10-17 м2. В верхнем слое покрытия или эрозионностойкого материала она, конечно, выше.
Как сделать, чтобы она не менялась? Для этого нужно, чтобы в матрице при высоких температурах не происходил процесс коксования, т. е. чтобы этот процесс был осуществлен раньше, при получении эрозионностойкого материала.
Таким материалом и является углерод-углеродный композиционный материал (УУКМ), у которого матрицей является плотный кокс или даже графит, а наполнителем - те же углеродные волокна, что и в углепластике. В этом материале матрица и наполнитель имеют один и тот же химический состав, но находятся в разных формах (фазах). Ценным является и то, что оба компонента КМ имеют одинаковые или близкие коэффициенты термического расширения и другие физико-химические и теплофизические свойства.
Приведем некоторые из них.
Теплота сублимации Qs = 60 000 кДж/кг.
Теплопроводность λ= 0,75...0,85 Вт/(м К).
Коэффициент термического расширения ɑ = 5 10'6 1/К.
Излучательная способность е = 0,8...0,9.
Модуль упругости Е = (1,6.. .2,2)-104 МПа.
Ниже будут приведены свойства некоторых конкретных углерод - углеродных КМ. Углеродное волокно (УВ) в них сохраняет свои прочностные характеристики вплоть до температуры активной сублимации > 3 000 °С (~ 3 300 К), а также прочное сцепление с углеродной матрицей, которая также не теряет своей механической прочности.
Углеродная матрица - кокс полимерного связующего или пека, либо пироуглерод, осажденный из газовой фазы или то и другое.
При создании УУКМ много внимания должно уделяться вопросу совместимости матрицы и наполнителя, плотности каркаса и его структуре, выбору технологических приемов изготовления их. Как и в случае получения других КМ, углерод-углеродные тоже формуются вместе с изделием или по форме, близкой к нему.
Существует ряд способов получения изделий из УУКМ. Рассмотрим некоторые из них:
1. Сначала изготовляются объемные каркасы из углеродных нитей или трикотажных сеток по форме изделия на графитовой оправке путем плетения или выкладки и подпрессовки. Иногда первичное формование каркаса производится на стальной оправке, а затем заготовка переносится на графитовую оправку и помещается в специальную печь для насыщения пироуглеродом.
Печь представляет собой закрытый стальной сосуд с контролируемой атмосферой, которая сама создается при пиролизе метана или другого углеродсодержащего газа. Стенки стального каркаса обычно футеруются графитовыми блоками. Нагрев осуществляется с помощью графитовых нагревателей сопротивления или индукторов, но тоже с графитовыми нагревателями. Для высокочастотного индукционного нагрева, как правило, применяются машинные генераторы. Нагрев печи осуществляется с контролируемой атмосферой или вакуумом внутри.
После достижения на поверхности каркаса температуры примерно 1 100 °С (1 373 К) в печь подается газ метан, который разлагается и «оставляет» углерод внутри каркаса по реакции:
СН4 →С + 2Н2Т↑.
Выделившийся водород сжигается на выходе из печи (рис. 55).
Процесс разложения метана на горячей поверхности называется пиролизом. После первого насыщения производится графитация углерод-углеродной заготовки при температуре выше 2 500 К. Время графитации определяется температурой, но длится не менее 24 часов. Чем выше температура, тем меньше продолжительность процесса графитации. В этом процессе образуется кристаллическая гексагональная структура углерода, происходит дальнейшее удаление продуктов разложения углеводородов, уплотнение углеродного
|
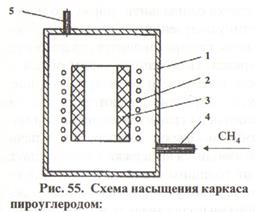
1 - корпус печи с футеровкой;
2 - нагреватель;
3 - насыщаемый каркас;
4 - устройство подачи метана;
5 - выходной патрубок водорода
каркаса берутся с некоторым припуском. В принципе перед последним насыщением - графитацией, - изделие можно довести до необходимых линейных размеров.
Полный цикл производства УУКМ толщиной до 50 мм по данному методу составляет примерно 700 часов.
Конечно, изделия из такого материала стоят очень дорого, это как правило, наиболее ответственные детали твердотопливного двигателя (вкладыш критического сечения сопла) или головной части.
Так, созданный по указанной технологии углерод-углеродный материал УПА-3 и его модификации позволили с успехом заменить псевдосплавы вольфрама с медью - АВМГ и ВНДС, ранее применявшиеся в критическом сечении сопла РДТТ. Это дало значительное снижение массы сопловых блоков и позволило заменить дефицитные материалы. Для сравнения: плотность АВМГ, содержащего 85 % вольфрама, - 18 000 кг/м3, а УУКМ имеют плотность ρ <2 000 кг/м3.
2. Второй способ получения углерод-углеродного материала применяется для крупногабаритных конструкций со сравнительно тонкими стенками, не более 20 мм, например, выходного конуса соплового блока РДТТ. В этом случае УУКМ создаются из углеродного волокнистого наполнителя в форме тканей, лент, жгутов и матрицы на основе кокса фенольно-формальдегидной или фурфуроль- ной (фурановой) смолы, пека, пироуглерода или пирографита.
ТЕХНОЛОГИЯ ПОЛУЧЕНИЯ. На металлическую оправку, изготовленную по форме изделия, наматывается каркас нужной толщины с применением предварительно пропитанной ленты или жгута. Если каркас представляет собой конус или слегка оживальную форму, то могут наматываться сразу два каркаса по типу получения углепластиков. После намотки оправка помещается в печь, где производится отверждение смолы и образование твердого каркаса. Полученный таким образом каркас обрабатывается по наружной поверхности на токарном станке, разрезается по большему диаметру, и с оправки снимаются два конуса (раструба). Затем эти конуса надеваются на графитовую оправку и помещаются в печь с контролируемой атмосферой. Температура в печи поднимается до 1 000... 1 100 °С, производится выдержка в течение двух часов или больше в зависимости от толщины стенки. При этом происходит карбонизация связующего, т. е. получение углеродного вещества - кокса, улетучиваются газообразные составляющие, за счет чего образуется пористый углеродный каркас. Этот каркас в этой же печи насыщается пироуглеродом до полного закрытия пор. Время насыщения составляет несколько суток в зависимости от толщины стенки изделия. Полученные контуры подвергаються механической обработке для получения требуемых размеров и формы детали.
В начале описания было сказано, что таким методом можно получать детали с толщиной до 20 мм, но потеем набора можно создавать изделия с толщиной стенки и до 100 мм.
Если менять наполнитель, т.е. применять другое волокно, то по этому же способу можно получать изделия с несколько другими механическими и теплофизическими свойствами, например, воля углеродную ткань с пироуглеродным покрытием. Кроме того, насыщенные пироуглеродом каркасы при необходимости подвергают ещё и графитации при температуре 2 500 0С и выше.
В табл. 27 приведены показатели плотности некоторых углерод-углеродных КМ.
Плотности углеродо - углеродных КМ Таблица 27
Состав УУКМ по исходным материалам | Плотность, кг/м3 |
Вискозное волокно + фурановая смола Вискозное волокно + пек Вискозное волокно + фурановая смола + пироуглерод Вискозное волокно + пироуглерод ПАН-волокно + пироуглерод ПВН-волокно + пек | 1500…1600 1700…1800 1550…1650 1550…1650 1700…1900 1950…2050 |
Есть и другие возможности создания УУКМ. Так, американская фирма SEP создала материал, углеродная матрица которого армирована углеродными волокнами по четырём диагоналям. Объём, занятый нитями, составляет 68…75%. Эта сетка пропитывается пеком, карбонизуется под давлением, затем графитируется. Цикл повторяется несколько раз, полученный материал имеет плотность γ= 2 000кг/м3 . Можно применять и другие смолы, имеющие высокое коксовое число.
Плотность некоторых углеродных матриц:
- кокс феноло-формальдегидный - 1 650 кг/м3 ;
- кокс фурановой смолы – 1 800 кг/м3;
- кокс пека – 2 100 кг/м3 ;
- пироуглерод – 1 600…2 100 кг/м3
Наиболее широко применимы: феноло-формальдегидные, фурфуроло-формальдегидные и фурановые смолы, каменноугольный пек.
Феноло-формальдегид – это продукт поликонденсации фенола с формальдегидом, представляющий собой вязкую жидкость (бакелит) или твёрдое вещество.
Фурфурол.
Фурфуроло-формальдегидные смолы – это то же, что и фурановые. В них вместо фенола имеется кольцо фурфурола. Мы сделали некоторое отступление, чтобы показать роль матрицы в УУКМ. Продолжим рассмотрение методов получения этих материалов. Это – ещё один из изотермических методов получения УУКМ.
3. Речь идёт о композиционном материале, в состав которого входят углеродная ткань из нити с пироуглеродным покрытием, кокс феноло-формальдегидной смолы и кокс среднетемпературного каменноуогольного пека.
ТЕХНОЛОГИЯ ПОЛУЧЕНИЯ. На прессах, обеспечивающих уденьное давление прессования 10…15 МПА (100…150 кг·с/см2) формуются заготовки ‹сырого› (заполимеризованного) пластика, геометрические размеры которых определяются размерами деталей и величиной упрессовки при термомеханической обработке, осуществляемой при давлении 6 МПа (60 кг·с/см2) и температуре 1 500 0С. При этом удаляются летучие вещества и происходит превращение заполимеризованной матрицы в кокс. Этот процесс называется карбонизацией. Заготовки деталей при этом приобретают повышенную пористость. Полученная структура заполняется смолой под давлением 0,5…0,6 МПа при температуре 300 0С в течении трёх часов. Окончательная обработка – при температуре 2 600 0С с одновременной подпрессовкой до 20 МПа. До нужных размеров детали доводятся с помощью механической обработки.
Данная технология близка к технологии получения графита. Конечно, такой вариант технологии УУКМ, очень сложен и применяется редко.
4. Одним из недостатков изотермического метода является то, что, несмотря на применения многократных попыток – насыщения каркасов, плотность по сечению деталей получается неравномерной.
Термоградиентный метод получения углерод – углеродных КМ, устраняющий этот недостаток, применяется для производства толстостенных деталей с центральным отверстием. Схема его представлена на рис. 56.
В варианте (а) через молибденовый или графитовый стержень пропускаеться большой силы ток для получения температуры 1 000 0С или 2 200 0С в зависимости от того, насыщается ли заготовка пироуглеродом или пирографитом. В варианте (б) частота индуктора подбирается таким образом, чтобы нагревался центральный графитовый стержень. Конечно, при этом нагревается и гильза, но до более низкой температуры. В обоих вариантах она служит теплоизолятором и каналом для прохождения газообразного метана. Отличительной чертой этого метода является наличие градиента температуры направленного внутрь детали, т.е. к нагревателю. Отложение пироуглерода начинается от центра детали, где температура выше, чем снаружи. Таким образом, граница насыщения движется к периферии и закрытия пор не происходит.
Теоретически метод – идеален, но на практике появляется трудность, состоящая в том, что по мере накопления пироуглерода меняется сопротивление нагревателя, по этому нужно увеличить силу тока при омическом нагреве или мощность и частоту генератора – при индукционном.
Процесс осуществляется в восстановительной атмосфере: сначала камера вакуумируется, а при пиролизе метана выделяется водород, который создаёт восстановительную атмосферу и, конечно, непрерывно отводится из объема камеры. Плотность полученного материала в изделиях равна примерно 1 800 кг/м3 . Таким методом можно получать не все изделия, т.к. трудность заключается в создании равномерной температуры по всей детали, особенно, если сечение её в разных местах неодинаковы.
С помощью термоградиентного метода получают детали ракет, которые подвергаются воздействию высокотемпературных скоростных газовых потоков, а так же элементы ТВЭЛов для гомогенных реакторов. В одном элементе имеется внутри делящееся вещество, например, уран или оксид урана, а сверху – замедлитель из углерода. Можно надеяться, что такие ТВЭЛы будут применятся в новых атомных реакторах.
Есть перспектива получения вкладышей критического сечения РДТТ больших размеров и даже блока, включающие самые напряженные части сопла: вход в него, его критическое сечение и выходной конус. Уже сейчас получают плотные тигли для плавки плутония, урана и других металлов.
Известно, что скорость уноса УУКМ в газовых потоках понижается с уменьшением межцентрового расстояния между волокнами, т.е. зависит от их ‹упаковки›, плотности и пористрости. Лучшие результаты могут дать волокна с квадратным поперечным сечением. В любом случае скорость абляции УУКМ с пироуглеродной матрицей вдвое меньше, чем с карбонизованной смолой. Высокая прочность УУКМ сохраняется при рабочих температурах деталей ракет, и составляет не ниже 11 кгс/мм2
(Т˃ 3000 0С).
При создании УУКМ нужно правильно выбирать структуру и плотность углеродного каркаса, температуру и скорость осаждения пироуглерода, а так же другие параметры, т.к. вместо пироуглерода можно получить сажу или слишком напряженную конструкцию, неравномерное распределение компонентов, а отсюда – низкие термостойкость, и т.д.
Дата добавления: 2015-07-10; просмотров: 3743;