ПРОИЗВОДСТВО МЕТАЛЛОВ
Металлургией называют отрасль промышленности, производящую металлы из руд и другого сырья.
Все металлы делят на черные и цветные. К черным металлам относятся железо, марганец, хром и сплавы на их основе; к цветным — все остальные. Цветные металлы делятся на четыре группы: 1) тяжелые: медь, свинец, олово, цинк и никель; 2) легкие: алюминий, магний, кальций, щелочные и щелочноземельные; 3) драгоценные, или благородные: платина, иридий, осмий, палладий, рутений, родий, золото и серебро; 4) редкие (все остальные): а) тугоплавкие: вольфрам, молибден, ванадий, титан, кобальт, цирконий иниобий; б) рассеянные: германий, галлий, таллий, индий и рений; в) редкоземельные: лантаноиды; г) радиоактивные: торий, радий, актиний, протактиний и уран; д) искусственные полоний, астат, нептуний, плутоний и др.
Сырье цветной и черной металлургии. По извлекаемому металлу руды называют железными, медными, марганцовыми, свинцовыми, медноникелевыми, урановыми и т. п. По составу их делят насульфидные, окисленные и самородные. Сульфидными рудами называются породы, в которых получаемый металл находится ввиде сульфидов. Это медные, цинковые, свинцовые и полиметаллические руды (халькопирит CuFeS2, галенит PbS, сфалерит ZnS и др.) Если извлекаемый металл находится в виде оксидов или другихкислородсодержащих минералов (силикаты, карбонаты), то такие руды относят к окисленным. Железные, марганцовые, алюминиевые руды чаще бывают окисленными. Руды, содержащие природные сплавы металлов, называют самородными.
На современном уровне развития технологии считается рентабельной переработка железных руд с содержанием не менее 30 % Fe, цинковых — 3% Zn имедных — 0,5 % Си.
Для получения металла из руды, кроме отделения пустой породы, необходимо отделить металл от химически связанных с ним элементов. Эта стадия называется металлургическим процессом. Металлургический процесс, осуществляемый с применением высоких температур, называется пирометаллургическим, с использованием водных растворов — гидрометаллургическим. В отдельную группу выделяют электрометаллургические процессы.
Первая стадия производства — обогащение сырья. Следующая стадия заключается в разложении концентрата обжигом, в обработке его хлором, а также оксидом серы (IV) или жидкими реагентами(кислотами, щелочами, комплексообразователями). Последними двумя способами извлекаемый металл переводят в раствор, из которого выделяется оксид или соль редкого металла осаждением в виде малорастворимого соединения или кристаллизацией. Завершающая стадия — получение чистого металла или сплававосстановлением углеродом или водородом, термическим разложением, вытеснением (цементация), электролизом растворов или расплавов.
В производстве тугоплавких металлов (вольфрам, молибден – завод «Победит») применяется метод порошковой металлургии, заключающийся в восстановлении оксидов порошкообразных металлов. Затем металлический порошок прессуют под большим давлением испекают в электрических печах, получая металл безперевода его в жидкое состояние. Температура спекания металлического порошка обычно на 1/3 ниже температуры плавления металла.
ПРОИЗВОДСТВО ЖЕЛЕЗА И ЕГО СПЛАВОВ
Среди используемых человеком металлов железо и его сплавы по объему и сферам применения занимают первое место. В практике обычно используют не чистое железо, а его сплавы, и в первую очередь с углеродом. В технике железом называют черный металл с содержанием углерода менее 0,2%. По количеству углерода все сплавы делят на стали и чугуны. К сталям относятся железные сплавы с содержанием углерода от 0,2 до 2%, к чугунам — с содержанием углерода выше 2% (обычно от 3,5 до 4,5%).
На рисунке 1 приведена диаграмма фазового состояния системы железо — углерод.
|
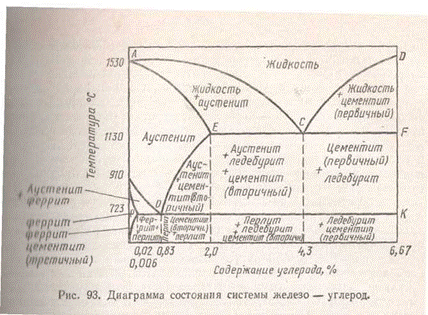
Как следует из диаграммы, температура начала плавления сталей снижается с ростом содержания углерода до точки Е. Эта точка соответствует предельной растворимости углерода в твердом железе (2% С). Для чугуна независимо от количества углерода температура плавления остается постоянной.
Если в чугуне значительная часть углерода находится в виде цементита Fe3C, то такой чугун называется белым. Из-за высокой твердости и хрупкости его трудно обрабатывать на станках, поэтому белый чугун перерабатывается в сталь. По этому признаку он получил еще название передельного чугуна. При медленном охлаждении расплавленного чугуна часть Fe3C распадается с выделением свободного углерода в виде графита. Такой чугун называется серым или литейным. Он более мягок, менее хрупок и хорошо обрабатывается на станках.
По составу стали могут быть углеродистыми и легированными. Углеродистыми называют стали, свойства которых определяются углеродом, а другие примеси существенного влияния не оказывают. По содержанию углерода эти стали делят на: малоуглеродистые (до 0,3% С), среднеуглеродистые (от 0,3 до 0,65%) и высокоуглеродистые (от 0,65 до 2% С). Из иизкоуглеродистой стали изготовляют кровельное железо, стальной лист, черную и белую жесть (широко используемую для изготовления тары), мягкую проволоку и т. д.; среднеуглеродистые стали используют для производства рельсов, труб, проволоки, деталей машин; высокоуглеродистая служит в основном для изготовления разнообразного инструмента.
Легированными называют стали, содержащие, кроме углерода, другие специально введенные для изменения свойств добавки (Cr, Mn, Ni, V, W, Мо и др.). Сталь, содержащую до 3—5% легирующих элементов, считают низколегированной, 5—10%—среднелегированной, 10% и более — высоколегированной. Никель придает стали повышенную пластичность и вязкость, марганец — прочность, хром — твердость и коррозионностойкость, молибден и ванадий — прочность при высоких температурах и т. д. Например, марганцовистые стали (8—14% Мп) обладают высокой ударостойкостью, их используют для изготовления дробилок, шаровых мельниц, рельсов и других ударонапряженных изделий. Хромомолибденовые и хромованадиевые стали идут на изготовление колонн синтеза, работающих под высоким давлением и при повышенной температуре. Из хромоникелевой или нержавеющей стали изготавливают химические реакторы, трубопроводы, кухонную посуду, вилки, ножи и т. д. Стали также классифицируют по назначению: строительная (конструкционная), машиностроительная, инструментальная и стали с особыми (специальными) свойствами. Некоторые примеси заметно ухудшают свойства стали. Так, сера придает стали красноломкость — хрупкость при красном калении, фосфор — хладноломкость, т. е. хрупкость при обычной и низкой температуре, азот и водород — газопористость, хрупкость.
ПРОИЗВОДСТВО ЧУГУНА
В настоящее время главный процесс металлургического производства черных металлов осуществляется по двухступенчатой схеме: получение чугуна в доменной печи и его передел в сталь. Чугун используют также для отливки станин, машин, тяжелых колес, труб и т. д. Основными исходными материалами для производства чугуна являются железные руды, флюсы и топливо.
Промышленные типы железных руд классифицируюг по виду преобладающего рудного минерала: 1) магнитные железняки состоят в основном из минерала магнетита Fe3O4 (с наиболее высоким содержанием железа — 50—70% и низким содержанием серы), который трудновосстановим; 2) красные железняки содержат 50—70% железа в виде минерала гематита — Fe2O3, небольшие примеси серы, фосфора и восстанавливаются легче, чем магнетит; 3) бурые железняки представляют собой гидроксиды железа состава Fe2O3 × пН2О с переменным количеством адсорбированной воды. Эти руды в основном бедные по содержанию железа (от 25 до 53%), часто загрязнены вредными примесями — серой, фосфором, мышьяком. Встречаются хромоникелевые бурые железняки (2% Cr и 1% Ni), используемые для выплавки природнолегированных чугуна и стали; 4) шпатовые железняки содержат 30—37% Fe, а также FeCO3 и незначительные примеси серы и фосфора. После обжига содержание железа возрастает до 50—60%. Для сидеритов часто характерна примесь марганца от 1 до 10%.
Сырьем служат также отходы производства черных и цветных металлов, но их доля в общем потреблении руд невелика. Для перевода тугоплавких оксидов в легкоплавкий шлак, не смешивающийся с чугуном, в процессе доменной плавки используют флюсы — породы основного характера: известняк или доломит (СаСО3, MgCO3). Обычно на выплавку 1 т чугуна расходуется 0,4—0,8 т флюсов.
В качестве топлива в производстве чугуна применяют кокс с содержанием 80—86% С, 2—7% Н2О, 1,2—1,7%S, до 15% золы и природный газ.
Подготовка железной руды к доменной плавке заключается в
дроблении, грохочении, усреднении и обогащении. Обогащение ведут в зависимости от типа руды восстановительным обжигом, электромагнитной сепарацией, флотацией. В нашей стране практически всю добываемую руду на последнем этапе подготовки подвергают агломерации. Это процесс спекания измельченной руды с коксовой мелочью (5—8%) и обожженным известняком (3—6%) в агломерационной машине транспортерного типа. Наряду с агломерацией применяют и окомковывание пылевидной руды со связующим веществом во вращающихся обжиговых печах с получением окатышей.
Процесс доменной плавки. Чугун выплавляют в металлургических реакторах шахтного типа, называемых доменными печами или домнами. Описание доменной печи дано в лекции 4.
В зоне горна за счет интенсивной подачи воздуха поддерживается окислительная среда и углерод кокса сгорает:
С + О2 = СО2 + 401 кДж
Воздух, подаваемый в доменную печь, нагревается в регенерагивных воздухоподогревателях (кауперах) до 900—1200 °С (рис. 2).
|
2С + СО2 = 2СО — 166 кДж
Образовавшийся в горне восстановительный газ поднимается в верхнюю часть печи, нагревает и восстанавливает компоненты шихты. Наивысшая температура в горне доменной печи 1800 °С, низшая в колошнике 250 °С. Давление газа в горне 0,2—0,35 МПа.
По мере опускания шихты последовательно протекают следующие процессы: разложение нестойких компонентов шихты, восстановление оксидов железа и других соединений, науглероживание железа (растворение углерода), шлакообразование и плавление. Разложение компонентов шихты начинается в колошнике, одновременно (до 200 °С) удаляется влага. При нагревании шихты от 400 до 600 °С идет интенсивное разложение карбонатов железа, марганца, магния, а при 800—900 °С — известняка. Оксиды кальция и магния взаимодействуют с ингредиентами пустой породы, образуя силикаты и алюминаты. Из кокса удаляются остатки летучих компонентов.
Восстановление железа представляет собой процесс последовательного перехода от высших оксидов к низшим до элементарного железа по схеме:
Fe2O3 ® Fe3O4 ® FeO ® Fe
В основу восстановительного процесса заложены реакции оксида углерода с оксидами железа:
2Fe2O3 + CO = 2Fe3O4 + CO2 + 63 кДж
Fe3O4 + CO = 3FeO + CO2 — 22 кДж
FeO + CO = Fe + CO2 + 13 кДж
Восстановление железа оксидом углерода (II) принято называть косвенным (непрямым), а при помощи твердого углерода – прямым.
Прямое восстановление железа протекает не только за счет углерода кокса, но и углерода, образующегося при термической диссоциации оксида углерода (II) на поверхности руды:
2СО = СО2 + С
Применение природного газа в качестве дополнительного топлива способствует повышению температуры процесса и косвенному восстановлению руды водородом:
СН4 + 2О2 = СО2 + 2Н2 + 803 кДж
Н2О + С = Н2 + СО — 126 кДж
Кроме железа, в условиях доменного процесса восстанавливаются и другие элементы, входящие в состав шихты. Однако значительная часть марганца не восстанавливается и переходит в шлак.
Гетерогенное восстановление руды заканчивается получением губчатого железа, в порах которого оксид углерода (II) разлагается. Образовавшийся при этом сажистый углерод с железом дает цементит:
3Fе + С = Fe3C
Одновременно идет науглероживание железа и за счет растворения углерода. Повышение содержания углерода в железе приводит к снижению температуры его плавления. Примерно при 1200 °С науглероженное железо плавится, стекает по кускам кокса и флюсов, дополнительно растворяя углерод, кремний, марганец, фосфор и другие элементы. Расплавленный чугун накапливается в горне. Шлакообразование начинается при температуре около 1000 °С за счет взаимодействия оксида кальция с оксидом кремния (IV), оксидом алюминия, марганца. При 1250—1350 °С шлаки плавятся и накапливаются в горне над расплавленным чугуном. Для предупреждения перехода FeO в шлак и выведения серы необходимо повышать основность шлака (избыток СаО):
FeO × SiO2 + СаО = CaSiO3 + FeO
FeO + CO = Fe + CO2
FeS + CaO = FeO + CaS
MnS + CaO = MnO + CaS
Образовавшийся сульфид кальция растворим в шлаке, но нерастворим в чугуне.
Для обеспечения непрерывности процесса доменную печь обслуживают несколько воздухонагревателей. Применение в доменном процессе нагретого воздуха в пределах 1000—1350 °С дает возможность на каждые 100° увеличивать производительность на 2% и на столько же снизить расход кокса.
В результате доменной плавки получают литейный чугун, направляемый на изготовление изделий методом литья; передельный и специальный чугуны (ферросилиций — 10—12% Si, зеркальный — 12 — 20% Мn и ферромарганец — 60—80% Мn), перерабатываемые в сталь; доменный шлак, из которого производят различные строительные материалы: шлакопортландцемент, шлакобетон, шлаковату, ситаллы для дорожного строительства; доменный газ (до 30% СО) отделяют от колошниковой пыли и используют как топливо в воздухонагревателях,, коксовых печах, для нагрева металла перед прокатом.
ПРЯМОЕ ПРОИЗВОДСТВО ЖЕЛЕЗА ИЗ РУД
Это такой металлургический процесс, когда восстановление руды идет в твердом состоянии, минуя стадию получения чугуна. Полученное методом прямого восстановления губчатое железо перерабатывается в сталь в электродуговых печах. Прямое восстановление железа осуществляется в шахтных и вращающихся печах, в реакторах с кипящим слоем. Сырьем служат окатыши с высоким содержанием железа, рудная мелочь, восстановителем — природный газ, жидкое и пылевидное твердое топливо. В России на базе Лебединского месторождения действует Оскольский электрометаллургический комбинат с прямым получением железа из руды по следующей схеме. Из рудника мелкораздробленную и обогащенную руду по трубопроводу с водой подают на комбинат. Здесь руда отделяется от воды, смешивается со связующими веществами и небольшим количеством извести, во вращающихся барабанах окусковывается в окатыши определенного размера. Окатыши непрерывно загружают в верхнюю часть шахтного реактора (высота — 50 м, диаметр —8 м), в котором при 1000 — 1100 °С осуществляется противотоком восстановление предварительно нагретым и конвертированным природным газом (смесью водорода и оксида углерода). Из нижней части реактора непрерывно отводятся восстановленные окатыши с 90—95% содержанием железа. Они поступают в дуговую электропечь для выплавки стали.
ПРОИЗВОДСТВО СТАЛИ
Передел чугуна в сталь заключается в уменьшении в нем углерода (окислением), в понижении в металле содержания кремния, марганца и других элементов, в возможно полном удалении серы и фосфора. В качестве окислителей используют кислород и оксиды железа. В настоящее время сталь выплавляют в мартеновских печах, кислородных конвертерах и электрических печах периодического действия.
|
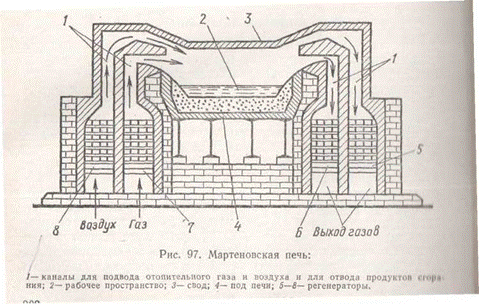
Выплавка стали в мартеновских печах. Мартеновская печь (рис. 3) представляет собой ванную отражательную печь, в которой используют регенерацию теплоты отходящих газов. Она состоит из свода 3, передних, задних и боковых стен, пода 4 и регенераторов 5—8. В передней стенке расположены окна для загрузки шихты, в задней — отверстие для выпуска стали и шлаков, боковые отверстия служат для ввода газового топлива и воздуха и вывода продуктов горения с температурой 1600 °С. Для регенерации теплоты печь снабжена четырьмя камерами с насадкой из огнеупорного кирпича. Через одну пару нагретых насадок 7, 8 в печь направляют газ и воздух, а через вторую проходят продукты горения, нагревающие насадку 5, 6. Затем потоки меняются. Исходными материалами для мартеновского процесса служат жидкий или твердый передельный чугун, металлолом (скрап), высококачественная железная руда и флюсы. Отапливается печь газообразным топливом. По окончании плавки в сильно разогретую печь загружают жидкий чугун, скрап, флюсы и руды. При высокой температуре металлолом плавится, кислород воздуха окисляет железо до оксида железа, одновременно высшие оксиды железа восстанавливаются железом:
2Fe + O2 = 2FeO + 556 кДж
Fe2O3 + Fe = 3FeO
Оксид железа (II), хорошо растворяясь в чугуне, окисляет растворенные в нем другие компоненты:
Si + 2FeO = SiO2 + 2Fe + 264 кДж
Mn + FeO = MnO + Fe + 100 кДж
2P + 5FeO = P2O5 + 5Fe + 199 кДж
Частично эти элементы окисляются и кислородом воздуха. Образующиеся оксиды SiO2, MnO, P2O6 взаимодействуют с флюсами и превращаются в шлак. В шлак частично переходит сера, так как сульфид кальция нерастворим в металле:
СаО + FeS = FeO + CaS
С появлением над поверхностью металла шлака жидкий металл изолируется от непосредственного действия кислорода, но процесс окисления не прекращается, а лишь замедляется. Содержащийся в шлаке оксид FeO на поверхности окисляется в Fe2O3, который диффундирует через шлак к металлу, окисляя его. С ростом температуры до 1600 °С и выше начинает интенсивно окисляться углерод:
FeO + С =± Fe + СО — 153 кДж
Процесс выделения из жидкого металла оксида углерода (II) называют «кипением» стали. После достижения в расплаве установленного содержания углерода шлак удаляют и вводят в сталь раскислители — ферросилиций или ферромарганец для восстановления растворенной в стали FeO:
2FeO + Si = 2Fe + SiO2
FeO + Mn = Fe + MnO
При необходимости в конце плавки вводят легирующие элементы. В связи с высокими технико-экономическими показателями переделки чугуна в сталь кислородно-конверторным способом, строительство новых мартеновских печей прекращено.
Выплавка стали в кислородных конвертерах. Применяемый ранее бессемеровский и томассовский конверторные способы переделки чугуна в сталь имели существенные недостатки — невозможность использования металлолома и низкое качество стали вследствие растворения в ней азота воздуха по сравнению с мартеновским методом. Замена воздуха на кислород дала возможность устранить эти недостатки, и в настоящее время прирост производства стали происходит преимущественно за счет строительства высокопроизводительных и экономичных кислородных конвертеров с основной футеровкой.
В России действуют глуходонные конвертеры с введением технически чистого кислорода (99,5%) вертикально сверху через водоохлаждаемые фурмы. Кислородные струи под давлением 0,9—1,4 МПа пронизывают металл, вызывая его циркуляцию и перемешивание со шлаком. При кислородно-конверторном способе передела чугуна в сталь протекают те же реакции, что и при мартеновском, но более интенсивно, что дает возможность вводить в конвертер металлолом, руду, флюсы. Плавка в конвертере длится 35—40 мин, а скоростная мартеновская плавка 6—8 ч. При равной производительности капитальные затраты на строительство кислородно-конверторного цеха на 25—35% ниже, а себестоимость стали на 5—7% меньше, чем при мартеновском способе.
Выплавка стали в электропечах относится к электротермическим производствам. В электрических печах можно выплавлять стали практически любого состава, с добавлением легирующих элементов, с низким содержанием серы, в восстановительной, окислительной или нейтральной атмосфере, а также в вакууме. Электросталь отличается низким содержанием газов и неметаллических примесей.
Качество стали, полученной любым из трех рассмотренных методов, может быть улучшено путем внепечного рафинирования. Наиболее широко распространены в производстве все три метода рафинирования: аргонно-кислородная продувка металла для выплавки нержавеющих сталей, вакуумная обработка жидкой стали для ее очистки от неметаллических включений и водорода, обработка стали жидкими синтетическими шлаками (53% СаО, 40% А12О3, до 3% SiO и до 1 % FeO).
Основная часть стали перерабатывается в изделия путем механической обработки. Традиционная схема: разлив стали в чугунные формы — изложницы, кристаллизация в виде слитка, обрезка и зачистка слитка, превращение слитка в обжимных станах (блюминг, слябинг) в заготовку, далее заготовка перерабатывается в изделия прокатом, штамповкой или ковкой. В настоящее время в металлургии все шире внедряется непрерывная разливка стали в специальных установках с превращением металла непосредственно в заготовку, а также точное (корковое) литье. Перспективным направлением развития металлургии стала порошковая металлургия, открывающая большие возможности для создания новых материалов, экономии металлов, энергии и повышения производительности труда.
<== предыдущая лекция | | | следующая лекция ==> |
ПРОИЗВОДСТВО ПЛАСТИЧЕСКИХ МАСС | | | Промышленное производство должно быть безотходным». |
Дата добавления: 2016-01-20; просмотров: 10817;