ПРОИЗВОДСТВО ПЛАСТИЧЕСКИХ МАСС
Пластическими массами называют материалы, содержащие в качестве основного компонента высокомолекулярные смолы, способные при повышенных температурах и давлении переходить в пластическое состояние, формоваться под действием внешних сил и сохранять форму при эксплуатации. Многие пластмассы представляют собой композиционные материалы, в состав которых кроме связующей смолы (или смол) входят наполнители, пластификаторы, стабилизаторы, смазывающие вещества, пигменты и красители, отверждающие добавки. Каждый из этих компонентов придает пластмассе определенные свойства.
Связующая смола, обладающая в процессе переработки текучестью и вязкостью, обусловливает сцепление компонентов в способную формоваться массу, переходящую через короткий промежуток времени в твердое состояние. Применяемые смолы различают по ряду признаков. По происхождению их делят на природные и синтетические. Последние составляют свыше 90% всех смол, применяемых в производстве пластмасс. По способу получения различают полимеризационные и поликонденсационные смолы. По свойствам и зависящим от них способам переработки в изделия смолы делят на термопластичные и термоактивные. Содержание смолы в композиции обычно составляет 40—50%. Многие полимеризационные пластмассы состоят почти целиком из смолы и не содержат наполнителей.
Наполнители являются важным компонентом смеси; они придают пластмассе ценные эксплуатационные свойства — прочность, термостойкость и пр., а также снижают стоимость пластмассовых изделий. В качестве наполнителей обычно применяют дешевые, доступные органические и неорганические материалы в виде порошков, волокон, слоистых материалов: древесную муку, сажу, целлюлозу, текстильные очесы, стекловолокно, бумагу, асбест, графит, слюду. Волокнообразные наполнители (хлопковый линтер, стеклянное волокно) обеспечивают высокие прочностные свойства: графит повышает антифрикционные свойства; асбест и слюда обусловливают повышенную термостойкость. Наполнители составляют до 60 масс. % пластмассы.
Пластификаторы — вещества, совмещающиеся со смолой (совместимость — это способность смолы растворяться в пластификаторе), снижающие температуру перехода смолы в текучее пластическое состояние и тем самым облегчающие переработку в изделия. Пластификаторы также влияют на механические свойства материалов и повышают долговечность изделий из пластмасс. Увеличение количества пластификатора понижает прочность полимера на растяжение и сжатие, но при этом резко повышаются прочность на удар и способность к растяжению. В качестве пластификаторов применяют высококипящие жидкие, реже твердые вещества, такие, как фталаты, алкил- и арилфосфаты и др.
Смазывающие вещества вводят в композицию для облегчения выталкивания готовых изделий из прессформы (предупреждения прилипания), к таким относят соли стеариновой кислоты, воски.
Отверждающие вещества способствуют переходу смолы в неплавкое и нерастворимое (отвержденное) состояние. Сущность отверждения заключается в сшивке линейных цепей макромолекулы в трехмерную форму с поперечными связями. В качестве отвердителей применяют полиамины и другие вещества в зависимости от природы исходной смолы.
Пластические массы представляют собой материалы с комплексом ценных свойств, позволяющих решать и сложные задачи современной техники, и обеспечение обилия товаров бытового назначения. Пластмассы сочетают в себе низкую плотность (900—1900 кг/м3, а у пенопластов до 100 кг/м3) с высокой механической прочностью; они также прекрасные диэлектрики, устойчивы к действию агрессивных сред, имеют низкую тепло- и звукопроводность. Имеются пластмассы, обладающие малым коэффициентом трения (антифрикционные материалы), и пластмассы с высокими фрикционными свойствами. Существенное достоинство пластмасс — это простота переработки их в изделия с высоким коэффициентом использования материала — до 0,90—0,95 (для металлов 0,5—0,6). Однако пластмассы имеют некоторые специфические недостатки, ограничивающие области их применения. Наиболее существенный недостаток — низкая термостойкость. У большинства пластмасс рабочая температура 60—150°С, выше которой они деформируются, теряют прочностные свойства (увеличивается процент удлинения, рис. 1). Потеря прочности связана также с их склонностью к старению под действием света, окислителей, агрессивных сред.
|
|
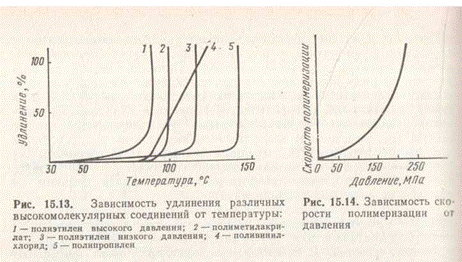
Полимеризационные пластмассы.К ним относятся полиэтилен, полистирол, поливинихлорид, полиметилметакрилат, фторопласты и др.
Полиэтилен получают цепной полимеризацией этилена:
nСН2=СН2 ® [–CH2–CH2–]n
Различают полиэтилен низкой и высокой плотности, получаемый соответственно при высоком и низком давлениях. При высоком давлении полимеризация этилена протекает по радикальному механизму, инициируемому кислородом или другими инициаторами (пероксидными), а при низком давлении — по ионному механизму с участием катализаторов. Для получения полиэтилена низкой плотности осуществляют полимеризацию в массе при давлении 150 МПа, температуре 180—200°С, в присутствии небольших количеств инициатора — кислорода (0,002%). Скорость полимеризации и выход полиэтилена зависят от степени чистоты мономера (не ниже 99,9%), количества инициатора, температуры и давления. На рис. 2 показано влияние давления на скорость полимеризации.
|
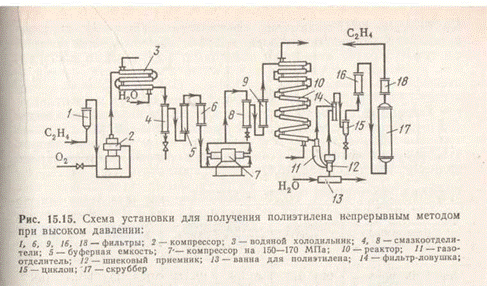
Схема производства полиэтилена при высоком давлении непрерывным методом представлена на рис. 3. Этилен (смесь свежего и обратного) проходит тканевый фильтр 1 для очистки от механических примесей, смешивается с кислородом, поступает в четырехступенчатый компрессор 2, где сжимается до 35 МПа иохлаждается в водяном холодильнике 3. Сжатый этилен проходит систему очистителей — смазкоотделитель 4, буферную емкость 5 и фильтр 6 — и подается в одноступенчатый компрессор 7, где сжимается до 150—170 МПа, вновь очищается в смазкоотделителе 8 и фильтре 9. Очищенный сжатый этилен поступает в трубчатый реактор 10, конструкция которого позволяет поддерживать оптимальный режим процесса. Полученный в реакторе полимер и непрореагировавший этилен поступают в газоотделитель 11, затем в шнековый приемник 12, где давление снижают до 0,5 МПа. Полиэтилен из шнекового приемника выдавливается в виде жгута, охлаждается и гранулируется в ванне. Непрореагировавший этилен очищают и возвращают в процесс.
Полимеризацию этилена при низком давлении проводят с участием катализатора — суспензии триэтилалюминия и тетрахлорида титана в низкокипящем бензине. Этилен и свежеприготовленный катализатор поступают в реактор, где под давлением 0,3—0,4 МПа, при 80°С происходит полимеризация. Получаемый в виде суспензии в бензине полиэтилен отделяют на герметичной центрифуге, многократно промывают метиловым, n-пропиловым спиртами для разложения катализатора и полной отмывки его следов и окончательно отжимают на центрифуге. Порошкообразный полиэтилен сушат (содержание остаточной влаги 0,15%) и гранулируют. Указанным способом получают полиэтилен высокой плотности (0,94—0,96 кг/м3) с молекулярной массой 17 000—25 000, отличающийся от полиэтилена низкой плотности структурой макромолекул, обусловливающей кристалличность полимера, а следовательно, и его свойства (табл. 15.2).
Таблица 1. Основные свойства полиэтилена
Полиэтилен | Плотность, кг/м3 | Степень кристалличности, % | Молеку-лярная масса, Mr×10–3 | Температура размягчения, °С | Прочность на разрыв, кг/см2 |
Низкой плотности Высокой плотности | 920—930 940—960 | 40—65 80—90 | 17—35 35—70 | 105—120 126—135 | 120—160 220—400 |
Полиэтилен имеет ряд ценных технических свойств, обеспечивающих разнообразное применение его в промышленности. Высокая влагостойкость, химическая стойкость, высокая прочность на разрыв, устойчивость к действию микроорганизмов — все это в сочетании с эластичностью, сохраняющейся при понижении температуры до —60°С, позволяет применять полиэтилен для изготовления труб, блоков, емкостей, в качестве упаковочного материала, защитных покрытий, для электроизоляции кабелей. Полиэтиленовые трубы используют для транспортировки различных жидких и газообразных веществ: воды, молока, кислот, щелочей и др. Полиэтилен — термопластичный материал и перерабатывается в изделия главным образом методами экструзии и литья под давлением.
Полистирол — очень распространенный термопластичный полимер. В промышленности его получают полимеризацией стирола в массе, в эмульсиях и суспензиях по реакции
nCH2=CH ® –CH2–CH–
C6H5 C6H5 n
На рис. 4 представлена схема непрерывной полимеризации стирола в массе.
Процесс полимеризации стирола начинается в алюминиевом реакторе 3 (форполимеризатор), где при помощи змеевика поддерживают температуру 75—85°С и обеспечивают перемешивание лопастными мешалками; для предотвращения окисления стирола в реактор подают азот. Из реактора частично полимеризованная масса (содержание полимера 18—20%) стекает в полимеризационную колонну 4 из хромоникелевой стали. Секционное устройство полимеризатора позволяет регулировать температурный режим, постепенно повышая температуру до 235°С. Для обогрева используется высококипящий органический теплоноситель. Расплавленный полистирол выдавливают при помощи червячного пресса в ванну 6; получаемые при этом твердые прутки или ленты режут в измельчителе 7.
Полистирол обладает прозрачностью, низкой плотностью (1,05 кг/м3), очень малым влагопоглощением (0,04%), хорошей химической стойкостью и высокими диэлектрическими и оптическими свойствами; он хорошо окрашивается. В изделия полистирол перерабатывают главным образом литьем под давлением и экструзией. Применяют его для изготовления деталей и изделий электроизоляционного назначения, оптической аппаратуры, предметов бытового потребления, фотооборудования, в строительной технике. На основе полистирола получают синтетические ионообменные смолы. Полистирол используют также для получения пенопластов.
Поливинилхлорид получают главным образом полимеризацией винихлорида в эмульсии или суспензии в водной среде в присутствии небольших количеств эмульгаторов и инициаторов:
nCH2=CH ® –CH2–CH–
Cl Cl n
На рис. 5 представлена схема производства поливинилхлорида непрерывным эмульсионным способом.
|
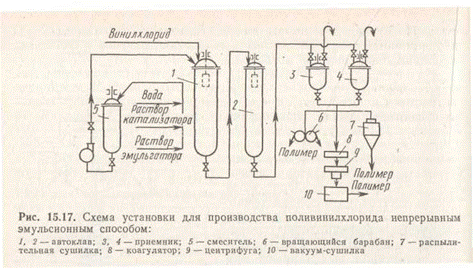
В никелированный автоклав 1 с рубашкой и мешалкой из смесителя 5 подают воду, растворы эмульгатора и инициатора, а затем при разрежении вводят винилхлорид. В начале процесса поддерживают температуру около 45°С пропусканием через рубашку теплой воды, затем теплоту экзотермической реакции отводят циркулирующим в рубашке и мешалке рассолом с температурой —20°С; давление в автоклаве около 0,5 МПа; продолжительность процесса 40—60 ч. Эмульсию полимера из автоклава 1 перемещают в автоклав 2 и непрерывно собирают в приемниках 3, 4, куда добавляют при перемешивании стабилизатор (соду). Выделение поливинилхлорида из эмульсии может быть осуществлено распылением на вращающихся барабанах 6, в распылительной сушилке 7 или в коагуляторе 8. Коагуляцию осуществляют добавкой в эмульсию коагулянтов (A12(SO4)3 и др.) с последующей промывкой полимера водой, отжимом на центрифуге 9 и сушкой в вакуумсушилке 10. Полученная твердая поливинилхлоридная смола измельчается.
Поливинилхлорид представляет собой порошкообразный термопластичный материал аморфной структуры плотностью 1,4 кг/м3. На основе поливинилхлорида получают винипласт (непластифицированный поливинилхлорид) и пластикат (пластифицированный поливинилхлорид). Для получения винипласта поливинилхлорид последовательным вальцеванием при 70°С и каландрованием преобразуют в пленку, из которой горячим прессованием получают винипластовые листы различной толщины. Винипласт перерабатывают механическими способами, горячим формованием, он легко сваривается и склеивается. Винипласт — коррозионноустойчивый материал; его применяют для футеровки аппаратов, работающих в агрессивных средах.
Пластикат получают смешением поливинилхлорида с пластификатором (35—50%), наполнителем (20%) и другими компонентами и обработкой смеси на вальцах. Пластикат, как и винипласт, обладает коррозионной стойкостью, имеет высокие диэлектрические свойства, но отличается от винипласта большей эластичностъю. Пластикат используют для нанесения защитных и электроизоляционных покрытий, из него изготовляют искусственную кожу, линолеум, непромокаемую тару, плащи.
Фторопласты относятся к ценным фторсодержащим полимерам. Фторопласт-4 (политетрафторэтилен) и фторопласт-3 (политрифторхлорэтилен) получают водноэмульсионной полимеризацией соответствующих мономеров по уравнениям реакции:
nCF2=CF2 ® [–CF2–CF2–]n
nCF2=CFCI ® [–CF2–CFCl–]n
Фторопласты обладают исключительной устойчивостью к действию сильно коррозийных сред: кислот, щелочей, окислителей; они имеют низкий коэффициент трения, превосходные диэлектрические свойства. Фторопластовые изделия (подшипники, вкладыши, электроизоляторы, детали контрольно-измерительных приборов) длительное время работают в условиях агрессивных сред и в широком интервале температур от —190 до +260°С.
Поликонденсационные пластмассы. Важную для промышленности группу полимеров составляют поликонденсационные смолы, к которым относят фенолоальдегидные, полиамидные, полиэфирные, эпоксидные и другие смолы.
Фенолоальдегидные смолы, являющиеся основой фенопластов, получают поликонденсацией фенолов (фенол, крезолы, резорцин) и альдегидов (формальдегид, фурфурол) в присутствии катализаторов. Кроме основного вещества — смолы — в процессе реакции выделяется также вода. Строение, а, следовательно, и свойства полимера обусловлены главным образом молярным соотношением исходных реагентов и характером применяемого катализатора. Так, из одного и того же сырья — фенола и формальдегида — получают разные смолы: новолачную (термопластичную) и резольную (термореактивную).
Новолачная смола, образующаяся при взаимодействии избытка фенола с формальдегидом (молярное соотношение 7:6) в присутствии кислого катализатора (НС1), имеет линейную структуру макромолекулы, является термопластичным материалом с обратимой плавкостью и растворимостью.
Резольная смола (резол) — термореактивный материал; получают ее при взаимодействии фенола с избытком формальдегида (6:7) в присутствии щелочного катализатора. В этих условиях образуется сначала полимер линейной структуры, который при дальнейшем нагревании вследствие наличия активных групп и подвижного водорода переходит в полимер трехмерной структуры, называемый резитом. Резит — неплавкий и нерастворимый материал. Технология фенолоальдегидных смол однотипна и состоит из следующих основных операций: подготовки сырья; дозировки и загрузки в реактор; варки смолы; сушки и слива смолы; охлаждения; переработки.
Варку смолы ведут в реакторе (рис. 6) из нержавеющей стали или никеля; он представляет собой цилиндрический котел 6 со сферической крышкой 2 и шаровым днищем 4. Внутри котла находится якорная мешалка 5, соединенная с электродвигателем 1. Нижняя половина котла снабжена рубашкой с двумя штуцерами для подачи пара и слива воды. На крышке реактора расположен ряд штуцеров для подачи сырья, вывода паров, для термометра. В нижней части реактора имеется приспособление для отвода смолы. Дозированная смесь фенола и формальдегида вместе с катализатором поступает в реактор, где происходит процесс поликонденсации. Реакционную массу вначале подогревают до 70—75°С паром, поступающим во внешнюю рубашку 3, а когда развивается экзотермический процесс, в рубашку подают охлаждающую воду. Разделение смолы и воды осуществляют или осторожной отгонкой воды в вакууме, или отстаиванием в отстойнике.
Фенолоальдегидные смолы выпускают в виде сухих смол, эмульсий и лаков; применяют их для производства пресспорошков, слоистых пластиков, клеев, ионообменных материалов, в качестве защитных покрытий.
Производство фенолоформальдегидных смол осуществляют периодическим и непрерывным методом. При периодическом методе используют вышеописанные аппараты с мешалкой. Непрерывную поликонденсацию осуществляют в аппаратах колонного типа с мешалками. Эти аппараты также работают в режиме, близком к полному смешению на каждой полке.
<== предыдущая лекция | | | следующая лекция ==> |
Высокомолекулярные соединения | | | ПРОИЗВОДСТВО МЕТАЛЛОВ |
Дата добавления: 2016-01-20; просмотров: 1109;