Высокомолекулярные соединения
Высокомолекулярные соединения (ВМС) — химические вещества, молекулярные массы которых составляют величину от нескольких сотен до десятков миллионов углеродных единиц.
Свойства ВМС определяются химическим составом, строением, взаимным расположением молекул (так называемой надмолекулярной структурой) в конденсированной фазе. В зависимости от этих факторов свойства ВМС могут меняться в очень широких пределах. Подавляющее большинство ВМС получают из низкомолекулярных соединений — мономеров, которые способны многократно соединяться друг с другом. Степень полимеризации п в ходе реакции возрастает и может достичь значительной величины. Поэтому разные макромолекулы имеют различный состав, и в общем полимер характеризуется средним значением п. Именно поэтому в отличие от низкомолекулярных соединений полимеры не являются индивидуальными веществами со строго определенными физическими константами и, в частности, с определенной молекулярной массой.
КЛАССИФИКАЦИЯ ВМС
В основе классификации высокомолекулярных соединений лежат многие признаки: происхождение, химический состав основной цепи, структура макромолекул, метод получения, отношение к нагреванию и др.
По происхождению различают природные, искусственные и синтетические полимеры.
Природные полимеры получаются в процессе биосинтеза в клетках живых и растительных организмов. Примерами таких ВМС являются целлюлоза, крахмал, различные белки и аминокислоты, ферменты, гормоны. С помощью экстракции, дробного осаждения и других методов они могут быть выделены из животного и растительного сырья.
Искусственные полимеры получают из природных материалов путем выделения, очистки и переработки природных полимеров. Таким образом, технологический процесс, как правило, не меняет свойств собственно ВМС, а связан с их выделением в наиболее чистом виде. К этому типу полимеров относятся целлюлоза, лигнин, различные белки, нуклеиновые кислоты, натуральный каучук, шерсть, шелк и др.
Синтетические полимеры производят из различных низкомолекулярных соединений с ненасыщенными связями, напряженными циклами, подвижными функциональными группами, благодаря которым эти низкомолекулярные соединения и способны объединяться в линейные цепи разной длины или блоки различной разветвленности и степени сшитости в трехмерные макромолекулы. Так получают многочисленные полимерные материалы — полиэтилен, полиоксиэтилен, полистирол, полиакрилонитрил, каучук, капрон и пр.
По химическому составу основной цепиполимеры делят на карбоцепные, гетероцепные и элементорганические.
Карбоцепные полимеры содержат в основной цепи звенья в виде углерода.
Гетероцепные полимеры имеют в основной цепи атомы углерода, чередующиеся с атомами кислорода, азота, серы и др.
Элементорганические полимеры не содержат углерода в основной цепи, но боковые ветви R представляют собой углеродсодержащие группы.
По строению макромолекулразличают линейные, разветвленные и трехмерные полимеры Примером линейного строения служат макромолекулы полиэтилена и ряда других термопластичных полимеризационных смол.
Разветвленные макромолекулы имеют длинную основную цепь, к которой присоединены короткие ветви. В них элементарное звено может быть связано с двумя, тремя и четырьмя соседними звеньями. Полимеры, состоящие из разветвленных молекул, как правило, менее эластичны, при нагревании размягчаются, но трудно плавятся, в растворителях набухают. Примером таких полимеров может служить крахмал.
Макромолекулы трехмерной структуры получаются в результате связывания, сшивания линейных и разветвленных цепей поперечными химическими связями. В зависимости от степени разветвления они тверды или каучукоподобны, при повышенной температуре не плавятся, но могут разрушаться, не растворяются ни в каких растворителях и лишь в некоторых случаях могут ограниченно набухать. В качестве примеров можно привести резольные фенолоформальдегидные смолы в конечной стадии смолообразования и ряд других поликонденсационных смол.
По методу полученияполимеры подразделяют в зависимости от того, какая реакция лежит в основе их образования — полимеризации или поликонденсации, — на полимеризационные и поликонденсационные. Типичными полимеризационными ВМС являются полиэтилен, поливинилхлорид, полистирол, полибутадиен, фторопласт, полиоксиэтилен и др. Поликонденсационные ВМС образуют большую группу смол: фенолформальдегидные, а также полиуретан, полиамид, полиацеталь, полисилоксапы и др.
По отношению к нагреваниюполимеры подразделяют на термопластичные и термореактивные. Термопластичные полимеры могут многократно размягчаться при нагревании и затвердевать при охлаждении. Термореактивные полимеры при нагревании плавятся, но затем макромолекулы связываются между собой поперечными мостиками; образующийся полимер затвердевает, становится неплавким и нерастворимым.
ОСНОВНЫЕ МЕТОДЫ ПОЛУЧЕНИЯ ВМС
В промышленной практике процессы поликонденсации и полимеризации осуществляются различными методами.
Полимеризация. В промышленности применяют следующие основные методы: полимеризация в массе; полимеризация в растворах; полимеризация в эмульсии и суспензии.
Полимеризация в массе — наиболее простая по методу ее осуществления. При периодическом способе в реакционный сосуд подают газообразный или жидкий мономер вместе с инициатором или катализатором и нагревают до нужной температуры. В результате полимеризации образуется сплошная масса полимера в виде пластины, стержня, цилиндра (полистирол, бутадиеновый каучук). Недостаток метода — сложность регулирования температурного режима в массе с высокой вязкостью, что приводит к образованию неоднородного продукта.
На современных установках полимеризацию в массе производят непрерывным методом в системе полимеризаторов. Применение перемешивания в реакторе обеспечивает оптимальный температурный режим и получение однородного полимера в виде крупки или гранул.
Полимеризация в растворах проводится в инертном растворителе; если в нем растворимы и мономер, и образующийся полимер, то получают готовый продукт — лак; когда же растворим только мономер, полимер выпадает в осадок; его отфильтровывают, промывают и высушивают. Полимеризацию в растворах применяют в производстве синтетических лаков и клеев.
Полимеризация в эмульсии применяется наиболее часто. Полимеризация мономера происходит в водной среде (инертнодисперсионная среда, содержащая 30—60% мономера) в присутствии эмульгатора, водорастворимых инициаторов и некоторых других компонентов. Эмульгаторы (мыла, соли сульфокислот) снижают поверхностное натяжение на границе раздела фаз мономер — вода, обеспечивая диспергирование в воде мономера и создание устойчивой эмульсии. К важным преимуществам метода эмульсионной полимеризации относятся легкость регулирования температуры, большая скорость процесса, однородность полимера, а также дешевизна дисперсионной среды (вода), ее негорючесть; кроме того, возможность получения мелкоизмельченного полимеризационного продукта, непосредственно пригодного к дальнейшей переработке. Реакцией полимеризации в промышленности получают полиэтилен, полипропилен, поливинилхлорид, полистирол, различные каучуки и др.
Поликонденсация. Ее проводят в расплаве, растворе, на границе раздела фаз, в твердом состоянии.
Поликонденсацию в расплаве проводят при 200— 400°С в атмосфере инертного газа. В конце операции в реакторе создается глубокий вакуум для наиболее полного удаления низкомолекулярных продуктов реакции. Таким способом осуществляют линейную поликонденсацию для получения полиамидов, полиэфиров и др.
При поликонденсации в растворе реакция происходит гораздо медленнее, чем в расплаве, возникает большая вероятность образования циклических продуктов, усложняется удаление низкомолекулярных соединений.
При межфазной поликонденсации полимер образуется на границе двух несмешивающихся жидкостей, например водного раствора гликоля или диамина и раствора хлорангидрида двухосновных органических кислот в органическом растворителе. Этот способ подобен эмульсионной полимеризации. Взаимодействие мономеров происходит быстро, при низких температурах и практически необратимо. Выделяющийся при этом НС1 сразу же поглощается водной фазой. Таким способом получают полимеры с большой молярной массой — полиэфиры, полиамиды, полиуретаны, полимочевины и др.
Твердофазная поликонденсация протекает, когда мономеры находятся в твердой фазе или стеклообразном состоянии. При таком способе поликонденсации можно сразу получить изделие нужной формы, хотя сам процесс протекает медленнее.
ПРОИЗВОДСТВО
ВАЖНЕЙШИХ ПОЛИМЕРНЫХ МАТЕРИАЛОВ
ПРОИЗВОДСТВО ЦЕЛЛЮЛОЗЫ
Целлюлоза относится к природным высокомолекулярным соединениям, представляя собой нерастворимый линейный полисахарид [С6Н10О5]n, молекулярная масса которого колеблется от 50 000 до нескольких миллионов. Целлюлоза входит в состав древесины, хлопка, льна и других растительных материалов. В наибольшем количестве целлюлоза находится в волокнах хлопка (до 98%); содержание ее в древесине составляет в среднем около 50% от массы сухой древесины. В состав древесины кроме целлюлозы входят гемицеллюлозы (более низкомолекулярные полисахариды, пентозаны и гексозаны), лигнин, смолы, эфирные масла. Гемицеллюлозы и лигнин отличаются от целлюлозы меньшей химической стойкостью. Это отличие и используется при производстве древесной целлюлозы. Наиболее распространенные промышленные способы получения целлюлозы: сульфитный — обработка древесины при нагревании раствором гидросульфита кальция, магния, натрия, аммония; сульфатный способ — обработка древесины при нагревании разбавленным раствором гидроксида и гидросульфида натрия.
Производство целлюлозы включает следующие основные стадии: подготовка древесины (удаление коры, сучьев, измельчение); приготовление варочного раствора; варка древесины (обработка древесины реагентом); отделение целлюлозы от раствора и обработка ее.
Сульфитный способ производства древесной целлюлозы.Древесина малосмолистых пород — ели, пихты, бука — поступает на переработку в виде щепы длиной 15—20 мм и толщиной до 3 мм. Основные процессы переработки: приготовление варочной кислоты и варка древесины.
Варочную кислоту получают пропусканием очищенного сернистого газа через башни, заполненные известняком и орошаемые водой. По составу варочная кислота представляет собой водный раствор гидросульфита кальция с избытком растворенного SO2:
SO2+H2O D H2SO3 2H2SO3 + CaCO3 D Ca (HSO3)2 + CO2 + H2O
|
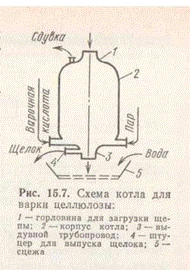
нагрева массы. Режим варки — температуру, концентрацию SO2, время — подбирают так, чтобы максимальное количество примесей древесины (гемицеллюлозы, лигнина и др.) переходило в раствор при сохранении целлюлозы без изменения. Обычно варку проводят при 135— 145°С, давлении 0,5—0,7 МПа в течение 8—10 ч. По окончании варки всю массу из котла сливают в сцежу — резервуар с ложным дном (фильтрующей перегородкой), где целлюлозу отделяют от варочного раствора и промывают водой. Затем целлюлозу освобождают от механических примесей и получают так называемую сульфитную целлюлозу.
О качестве получаемой целлюлозы судят по количеству оставшегося лигнина: при содержании лигнина более 3% целлюлоза называется жесткой, менее 2 % —мягкой.
Целлюлоза, используемая для химической переработки и для получения качественных сортов бумаги, подвергается дополнительно отбелке и облагораживанию. Отбелкапроводится при помощи гипохлоритов натрия или кальция, хлора, диоксида хлора, пероксида водорода. Отбеленную целлюлозу затем облагораживают обработкой разбавленным раствором NaOH.
Сульфатный способ производства целлюлозы.Древесная щепа обрабатывается в варочном котле щелоком при нагревании острым паром. Щелок содержит до 4,5% гидроксида натрия, а также сульфид и гидросульфид натрия
Щелочную варку ведут при 165—175°С, давлении 0,8—1,0 МПа втечение 4—6 ч. В результате варки древесина освобождается от гемицеллюлоз, лигнина, переходящих в раствор (черный щелок). Последующие операции отделения целлюлозы от раствора, содержащего примеси, те же, что при сульфитном способе.
Использование отходовпроизводства необходимо для охраны окружающей среды и получения продуктов, ценных для народного хозяйства. Так, при производстве 1 т сульфитной целлюлозы получают 10—12 тщелока, содержащего ценные органические соединения.
Сульфатный способ варки целлюлозы находит теперь все большее применение в связи с тем, что он применим для переработки любой древесины, в том числе отходов лесопиления и деревообработки. Хорошо разработанная система регенерации щелока с последующим возвращением его в производство позволила свести до минимума сброс загрязненных вод, который гораздо больше в производстве сульфитной целлюлозы.
Переработка целлюлозыпроводится разнообразными методами. Целлюлоза, выделяемая из древесины, поступает на изготовление бумаги, на химическую переработку, в результате которой неплавкая и нерастворимая в обычных растворителях целлюлоза переходит в легко перерабатываемые соединения — простые и сложные эфиры.
Простые эфиры целлюлозы (метилцеллюлоза, этилцеллюлоза и пр.) получают действием алкилирующих веществ — галогенидных алкилов, спиртов — на алкалицеллюлозу. Применяют их для получения пластмасс и других материалов. Этилцеллюлозу используют, в частности, вместо свинцовой изоляции электрокабелей. Технически важные сложные эфиры целлюлозы (нитроцеллюлозу, ацетилцеллюлозу, ацетобутилатцеллюлозу) получают обработкой целлюлозы ацилирующими средствами: кислотами, ангидридами, галогенангидридами кислот. Их применяют в производстве химических волокон, пластмасс, взрывчатых веществ и др.
Различные способы химической модификации целлюлозы применяют для придания хлопчатобумажным изделиям специальных свойств — несминаемости, огнестойкости и др. Так, несминаемость достигается сшиванием молекул целлюлозы с помощью обработки целлюлозы формальдегидом; огнестойкость достигается сшиванием целлюлозы с помощью так называемых антипиренов (огнезащитных веществ)— органических соединений, содержащих фосфор, азот, бор. Большое количество сульфитной целлюлозы используют для производства вискозных волокон.
ПРОИЗВОДСТВО ХИМИЧЕСКИХ ВОЛОКОН
Химические волокна имеют большое значение в развитии народного хозяйства; из них вырабатывают товары бытового назначения (ткани, трикотаж, заменители кожи и пр.) и высококачественные технические материалы — корд, транспортерные ленты, спецткани (фильтрующие, ионообменные и др.).
Химические волокна в зависимости от исходного волокнообразующего полимера делят на искусственные, получаемые химической переработкой природных полимеров (целлюлозы, белков), и синтетические, вырабатываемые из высокомолекулярных соединений, синтезируемых из мономеров.
Технология химических волокон складывается из приготовления прядильного раствора или расплава полимера, формования (прядения) волокна и его отделки. Прядильный раствор определенной концентрации (7—25%) и вязкости приготовляют растворением полимера в растворителе; прядильный расплав получают нагреванием до температуры плавления полимера, плавящегося без разложения (полиамиды и полиэфиры). Перевод полимера в растворенное или расплавленное состояние обеспечивает при последующем формовании ориентирование молекул вдоль оси образующихся волокон. Растворы и расплавы тщательно очищают фильтрованием от механических примесей и пузырьков воздуха и затем подают на формование.
|
|
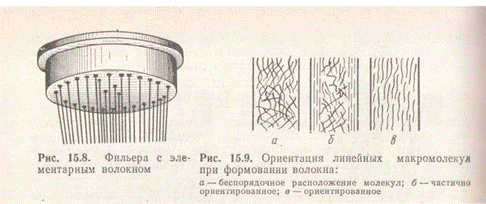
Формование волоконпроизводится продавливанием прядильной массы (раствора или расплава) через фильеру-нитеобразователь (рис. 2), представляющий собой металлический колпачок, в донышке которого имеется множество мельчайших отверстий (до 25 000 диаметром 0,04—0,25 мм). Каждая струйка, выходящая из отверстия фильеры, затвердевает с образованием элементарного волокна.
Различают три способа формования (прядения): мокрое прядение из раствора; сухое прядение из раствора и из расплава. В процессе мокрого прядения отвердение струек происходит в осадительной ванне (раствор электролитов) вследствие коагуляции полимера. Мокрое прядение применяют, например, при формовании вискозного волокна.
Сухое прядение из раствора характеризуется отвердением струек в токе теплого воздуха вследствие удаления растворителя из прядильного раствора. Таким способом прядения получают ацетатное волокно, а также некоторые синтетические волокна. Сухое прядение из расплава производится в токе холодного воздуха или инертного газа; при охлаждении происходит отвердение струек полимера. Дальнейший процесс формования независимо от способа отвердения струек осуществляют вытягиванием элементарных волокон при помощи наматывающих приспособлений (бобина, ролик, центрифуга). При формовании и вытягивании происходит ориентация линейных цепей макромолекул вдоль оси волокна, что и обусловливает прочностные свойства волокна (рис. 3). Сформованные пучки элементарных волокон скручиваются в непрерывную нить или режутся на короткие отрезки (30—150 мм), образуя штапельное волокно, из которого затем прядут нити так же, как из хлопка.
Отделка волокнавключает удаление примесей тщательной промывкой, отбелку, окрашивание, сушку и некоторую текстильную подготовку (замасливание, кручение, перематывание).
Производство вискозного волокна.Вискозное волокно, представляющее собой регенерированную целлюлозу, — наиболее дешевое искусственное волокно, и получают его в промышленности в больших количествах, причем сырьем служит древесная сульфитная целлюлоза, поступающая в виде листов размером 600— 800 мм. Схема производства вискозного волокна представлена на рис. 4.
Исходная целлюлоза подвергается мерсеризации — обработке 18—20 %-ным раствором гидроксида натрия. В результате образуется новое химическое соединение — щелочная целлюлоза (алкалицеллюлоза)
[С6Н7О2(ОН)3]n + nNaОН ® [С6Н7О2(ОН)2ONа] + Н2О
Набухшие листы щелочной целлюлозы отжимают от избытка гидроксида натрия (щелочь регенерируется и возвращается в производственный цикл) и измельчают. Затем измельченная, рыхлая масса выдерживается при 60°С в течение 3 ч (процесс предсозревания). При этом целлюлоза окисляется кислородом воздуха, что сопровождается понижением степени полимеризации (с 800—1000 до 500). Такая деполимеризация целлюлозы обусловливает возможность регулирования вязкости получаемого в дальнейшем прядильного раствора. После предсозревания щелочную целлюлозу обрабатывают в смесителе сероуглеродом при 25—30°С в течение 2—3 ч, в результате чего образуется оранжево-желтый ксантогенат целлюлозы (процесс ксантогенирования):
[С6Н7О2(ОН)2ONa]n + nCS2 ® [С6Н7О2(ОН)2OCS2Na]n
|
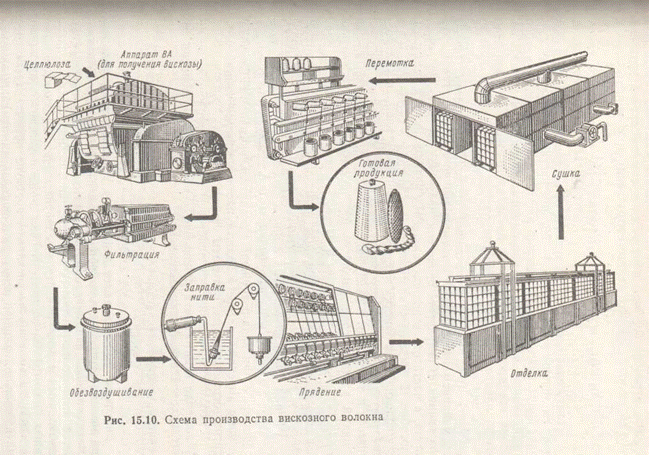
Ксантогенат целлюлозы в отличие от исходной и щелочной целлюлозы хорошо растворим в 4—7%-ном растворе гидроксида натрия; получаемый вязкий щелочной раствор ксантогената целлюлозы называют вискозой. На современных заводах вискозного волокна все процессы получения прядильного раствора — мерсеризация, предсозревание, ксантогенирование и растворение ксантогената целлюлозы — проводят в одном аппарате ВА (вискозный аппарат. Полученный прядильный раствор перед формованием выдерживают в течение 16—20 ч при 14—17°С для созревания. В результате процессов, протекающих во время созревания, в частности неполного омыления ксантогената, повышается способность вискозы к коагуляции при мокром способе формования волокна. Для очистки и удаления пузырьков воздуха прядильный раствор в период созревания фильтруют на рамных фильтрпрессах и отстаивают в баках под вакуумом. Подготовленный прядильный раствор, содержащий 6—9% целлюлозы, 6—7% гидроксида натрия, 2,2—2,3% серы и 82—83% воды, поступает на прядильную машину (процесс формования волокна).
|
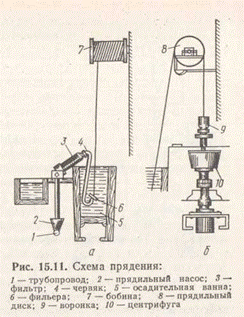
На рис. 5, а, б представлены схемы прядения бобинным и центрифугальным способами. Прядильный раствор из трубопровода 1 при помощи зубчатого прядильного насоса 2 продавливают через фильтр 3 и по стеклянной трубке — червяку 4 подводят к фильере 6. Фильера погружена в осадительную ванну 5. Струйки вискозы вытекают из нее в водный раствор коагулирующих реагентов (серная кислота, сульфаты натрия и цинка).
В осадительной ванне под действием электролитов происходит разложение ксантогената целлюлозы с образованием волокон из регенерированной целлюлозы.
Вискозные волокна далее подвергают вытягиванию и укладке при помощи центрифуг или бобин. При центрифугальном прядении из осадительной ванны волокна подхватываются прядильным диском 8 и через направляющую непрерывно опускающуюся и поднимающуюся воронку 9 поступают в центрифугу 10 (скорость вращения 6000—10 000 об/мин). На центрифуге волокна закручиваются и укладываются на ее стенке, образуя «кулич». На бобинной прядильной машине некрученые волокна наматывают на вращающуюся бобину 7, а крутку производят после отделки. Отделка волокна производится на бобинах и в куличе и включает операции: промывку умягченной водой для удаления электролитов, обработку растворов сульфита натрия для удаления серы (десульфурация), отбелку, замасливание, сушку, перематывание, сортировку и упаковку.
На основе вискозы промышленность выпускает широкий ассортимент материалов: шелковые, штапельные и кордные ткани, пленочный целлофан, искусственный каракуль
Синтетические волокна.Ихполучают из синтетических полимеров – гетероцепных (полиамидов, полиэфиров, полиуретанов и др.) и карбоцепных (полиакрилонитрила, политетрафторэтилена, полипропилена и др.). Волокно капрон получают из полиамидной смолы (поликапроамид) путем формования из расплава; исходную смолу получают термической полимеризацией циклического мономера капролактама (лактам e-аминокапроновой кислоты). Процесс идет в присутствии воды, инициирующей раскрытие цикла и полимеризацию с образованием линейной макромолекулы полимера. Полимеризация, вероятно, протекает по ступенчатому механизму; молекулярную массу полимера (рост цепи) регулируют добавкой уксусной кислоты.
Капрон и другие полиамидные волокна обладают высокой прочностью на разрыв, превосходной устойчивостью к истиранию, эластичностью, устойчивостью к действию микроорганизмов. Капрон используют для изготовления высококачественного корда, парашютов, приводных ремней и других технических изделий, а также предметов бытового назначения.
Полиакрилонитрильное волокно (н и т р о н) получают радикальной полимеризацией акрилонитрила (мономер) в водной суспензии в присутствии пероксидных соединений:
nСН2=СН ® [ –СН2–СН– ]n
CN CN
Раствор полимера в диметилформамиде подвергают формованию мокрым или сухим способом. Волокно, полученное из полиакрилонитрила, плохо окрашивается и недостаточно эластично; эти недостатки успешно устраняются получением волокна из сополимеров. Акрилонитрильные волокна по виду очень похожи на шерсть и применяются для производства трикотажных изделий, ковров, мехов и др.
<== предыдущая лекция | | | следующая лекция ==> |
Химико-технологический процесс | | | ПРОИЗВОДСТВО ПЛАСТИЧЕСКИХ МАСС |
Дата добавления: 2016-01-20; просмотров: 11098;