НА РЕМОНТ ИЛИ ИЗГОТОВЛЕНИЕ ЗАДАННОГО УЗЛА.
Полная ревизия.
Полную ревизию осуществляет слесарь, имеющий квалификацию не ниже 5-го разряда и соответствующее удостоверение
Полную ревизию букс с роликовыми подшипниками производят при полном освидетельствовании колесных пар:
а) при деповском и текущем отцепочном ремонтах вагонов выкатываемым и подкатываемым колесным парам, проходившим последнее полное освидетельствование четыре и более лет для пассажирских и рефрижераторных вагонов и пять и более лет для грузовых вагонов, а также колесным парам, срок службы которых 15 лет и более кроме колесных пар, ранее проходивших последнее полное освидетельствование не более 3-х месяцев;
б) при повреждении вагона от динамических ударов при падении груза;
в) через две обточки по предельному прокату или другим неисправностям поверхности катания колес грузовых вагонов и через обточку для колес пассажирских вагонов;
г) при каждой обточке колесных пар, работающих с редуктором, и колесных пар, выкаченных из-под шестиосных вагонов;
д) после схода вагона с рельсов у колесных пар сошедшей тележки;
е) при капитальном ремонте вагона;
ж) при всех видах планового ремонта подкатываемым колесным парам РУ-950 и РУ-1050 в соответствии с Инструктивным указанием 3-ЦВРК;
з) при формировании и ремонте колесной пары со сменой элементов;
и) при неясности клейм и знаков последнего полного освидетельствования на торце шейки оси;
к) после удаления волосовин, плен неметаллических включений и др.;
л) у поврежденных вагонов после крушения, аварии, маневровой работы;
м) при наличии на поверхности катания колес колесных пар;
- грузовых вагонов - неравномерного проката 2 мм и более, ползуна и навара 1 мм и более, разности диаметров колес на одной оси 3 мм и более;
- пассажирских вагонов - ползуна 1 мм и более, навара -0,5 мм и неравномерного проката 2 мм и более, а у колесных пар с приводом генераторов всех типов (кроме плоскоременных) - неравномерного проката 1 мм и более;
н) при отсутствии бирки или неясности клейм на ней, обнаруженных при ремонте или подкатке колесной пары;
о) при сварочных работах на вагоне или тележке, если подшипники были включены в сварочную цепь;
п) при недопустимом нагреве буксы или повреждении буксового узла, требующего демонтажа букс, а также отказе в работе привода редуктора от торца шейки оси, требующего его демонтажа;
р) при обнаружении в буксе пассажирского вагона редукторного масла. При неисправности одной буксы обязательно производить полную ревизию второй буксы колесной пары.
При полной ревизии букс производят:
а) демонтаж букс с роликовыми подшипниками со снятием внутренних и лабиринтных колец в соответствии с действующими нормативно-техническими документами. Замену колец марки ШХ15СГШ на кольца марки ШХ4 производить при фактическом наличии колец марки ШХ4 на предприятии (основание-указание МПС РФ от 09.06.2003 № П-5693).
б) промывка, осмотр, проверка и дефектоскопирование деталей роликовых подшипников, других деталей буксового узла и колесных пар;
в) ремонт деталей буксового узла и колесных пар;
г) измерение радиальных и осевых зазоров, посадочных отверстий внутренних колец при их установке, посадочных поверхностей корпусов букс;
д) монтаж букс. Рис.3. Бирки
При полной ревизии буксовых узлов - а) для двух болтов, б) для одного болта.
При промежуточной ревизии буксовых узлов -
в) 1 - месяц, год, условный номер (клеймо) пункта, производившего полное освидетельствование колесной пары;
2 - индивидуальный номер колесной пары;
3 - знак "О", месяц, год, условный номер (клеймо) пункта, производившего обточку колесной пары без демонтажа буксовых узлов;
4 - код Государства-собственника колесной пары.
После полной ревизии и монтажа букс на бирке выбивают:
- индивидуальный номер колесной пары, который включает в себя условный номер предприятия-изготовителя черновой оси, порядковый номер черновой оси и год изготовления черновой оси;
- дату полного освидетельствования (месяц и две последние цифры года);
- условный номер, присвоенный пункту, производившему освидетельствование колесной пары и монтаж букс;
- код Государства-собственника колесной пары (определяется по клейму, нанесенному на боковой поверхности ободов с наружной стороны колес).
У колесных пар с торцевым креплением подшипников тарельчатой шайбой и болтами М20 при новом формировании, ремонте со сменой элементов и полном освидетельствовании колесных пар, кроме маркировки на бирке, на стопорной шайбе правой шейки оси выбивают индивидуальный номер колесной пары, знак формирования, условный номер предприятия сформировавшего или производившего ремонт со сменой элементов и дату (месяц и две последние цифры года) производства этих работ.
Промежуточная ревизия.
Промежуточную ревизию производят:
а) при обточке колесных пар без демонтажа букс;
б) при обыкновенном освидетельствовании колесных пар;
в) при единовременной технической ревизии пассажирских вагонов;
г) в качестве профилактической меры по отдельным указаниям (профилактическая ревизия).
Ревизию осуществляет слесарь, имеющий квалификацию не ниже 4-го разряда и соответствующее удостоверение.
Перед промежуточной ревизией у выкаченных колесных пар производить обкатку прокручивание колесных пар на установке СКБУ-01 с частотой вращения 220-250 об/мин в течении 5 мин без приложения внешней нагрузки. Буксы проворачивают для определения неисправностей (раковин и др.). По результатам проверки на СКБУ принимается решение о виде ревизии данной колесной пары. При вращении буксы с толчками и ненормальным шумом обязательно производят полную ревизию.
При промежуточной ревизии снимают крышку. Места прилегания крышки предварительно очищают от грязи и протирают. Снятую крышку укладывают в закрываемый ящик внутренней стороной вверх. Из передней части буксы смазку перекладывают в снятую крышку для дальнейшего использования (для закладки обратно в буксу). При этом необходимо соблюдать условия, исключающие попадание в буксу и крышку различных загрязнений.
Загрязнение смазки определяют визуально после растирания небольшой порции смазки на тыльной стороне руки, суконном материале, или зеркале. Букса с загрязненной и обводненной смазкой (стальные, латунные включения, механические и другие примеси) подлежат полной ревизии. При хорошем состоянии смазки (потемнение смазки не является браковочным признаком) производят дальнейший осмотр. Прежде всего, проверяют состояние переднего подшипника. При обнаружении масла от редукторно-карданного привода, излома или износа сепаратора, приставного упорного кольца или других дефектов буксу подвергают полной ревизии. При ревизии, выполняемой по подпунктам «в» и «г», и при удовлетворительном состоянии подшипника остукиванием контролируют болты стопорной планки или тарельчатой шайбы. Производится дефектоскопирование упорного кольца, после его снятия специальными клещами. Производство промежуточной ревизии производится только колесным парам РУ-1Ш. Ослабшие болты М12 подтягивают, неисправные заменяют. Неисправную проволоку болтов стопорной планки заменяют, под болты стопорной планки ставят пружинные шайбы. Надежность крепления торцевой гайки проверяют ударами слесарного молотка по оправке, упираемой в одну из граней коронки или в шлиц гайки. Проверку производят в обе стороны вращения гайки. При ослаблении гайки торцевого крепления колесную пару выкатывают и снимают гайку. Колесная пара и гайка с поврежденной резьбой к дальнейшей эксплуатации не допускаются.
При ревизии, выполняемой по подпунктам «а» и «б», у букс с подшипниками при торцевом креплении гайкой независимо от состояния крепления снимают стопорную планку для дефектоскопирования и клеймения, торцевую гайку и упорное кольцо - для визуального осмотра резьбы шейки оси и гайки. Колесные пары или гайки с поврежденной резьбой к дальнейшей эксплуатации не допускаются. При исправном состоянии резьбы и удовлетворяющем зазоре в резьбовом соединении производят затяжку гайки с последующей установкой стопорной планки. При торцевом креплении тарельчатой шайбой болты М20 освобождают от стопорения и динамометрическим ключом проверяют их затяжку (вращением по часовой стрелке). При наличии хотя бы одного из болтов с крутящим моментом менее 5 кгс/м все болты вывертывают и проверяют визуально состояние резьбы отверстий в торце оси и болтов крепления, а также состояния места перехода стержня болта к головке.. При изломе головки или стержня болта оставшуюся часть болта вывертывают из оси без повреждения резьбы резьбового отверстия. Поврежденные болты заменяются. При обнаружении срыва более трех ниток резьбы в резьбовых отверстиях оси или затруднений при завертывании болтов крепления допускается резьбовые отверстия исправлять метчиком. При повреждении более шести первых ниток резьбы в резьбовых отверстиях оси колесная пара не допускается к дальнейшей эксплуатации до восстановления резьбы. Болты, имеющие затяжку крутящим моментом более 5 кгс/м, подтягивают с усилием 23-25 кгс/м. Затяжка болтов должна быть равномерной. Для этого завинчивание трех болтов производят дважды по периметру, а четырех - по схеме 1-2-3-4-3-4-2-1 с последующим стопорением.
При обточке поверхности катания колес с торцевым креплением шайбой применяют центр колесно-токарного станка. Взамен снятой смотровой или крепительной крышки устанавливают специальную временную крышку с отверстием для прохода центра станка.
Колесную пару устанавливают на станок для обточки поверхности катания.
После обточки колесной пары снимают временную крышку проверяют состояние смазки, надежность крепления торцевой гайки. Ослабленные гайки (вращающиеся от руки) снимают и осматривают состояние резьбы шейки оси и гайки. Колесные пары и гайки с поврежденной резьбой к дальнейшей эксплуатации не допускают.
При торцевом креплении тарельчатой шайбой и болтами М20 проверку состояния такого крепления после освобождения болтов от стопорения, осмотр резьбовых отверстий в оси и болтов, а также последующую их затяжку.
После обточки с промежуточной ревизией под правый верхний болт М20 крепительной крышки устанавливают бирку (рис. 3 в), на которой выбивают 01 или 02, условный номер, присвоенный ремонтному предприятию, производившему обточку, и дату. Затем смотровую или крепительную крышку устанавливают и закрепляют болтами, под которые устанавливают пружинные шайбы. Между крышками ставят резиновую прокладку новую или бывшую в употреблении, но исправную. Между фланцевой поверхностью крепительной крышки и корпусом буксы устанавливают резиновое кольцо, а свободное пространство заполняют смазкой применяемой в буксовом узле. Крышки устанавливают и закрепляют.
При промежуточной ревизии после проведения указанных в операций в случае необходимости в буксу добавляют свежую (не бывшую в употреблении) смазку, которую укладывают валиком на видимую часть переднего подшипника, уплотняя ее пальцами так, чтобы смазка смогла проникнуть между сепаратором и бортом наружного кольца. Затем устанавливают смотровую или крепительную крышку.
Демонтаж букс
Демонтаж букс с роликовыми подшипниками типа 232726 и 42726 может осуществляться на механизированной полуавтоматической линии или ручным способом. При демонтаже буксы не допускается сбрасывать ее с шейки оси. Категорически запрещается использовать любой ударный инструмент для удаления подшипников из корпуса. Подшипники из корпуса буксы необходимо удалять только при помощи специальных прессов или устройств.
При демонтаже букс работы с выполняются в следующем порядке:
а) отвернуть болты крепительной крышки, а затем снять крепительную крышку вместе со смотровой;
б) удалить смазку из крышки и передней части буксы;
в) отвернуть и снять болты стопорной планки или тарельчатой шайбы. Планку или шайбу снять;
г) отвернуть и снять торцевую гайку, а также упорное кольцо переднего подшипника;
д) снять корпус буксы вместе с блоками подшипников (наружное кольцо с сепаратором и роликами) с внутренних колец, насаженных на шейку оси;
е) при помощи пресса вынуть из корпуса буксы блоки подшипников;
ж) снять внутренние и лабиринтное кольца с шейки с предподступичной части оси.
Подготовка к монтажу.
Промывка подшипников и деталей букс.
А) Обмывка деталей буксовых узлов от смазки ЛЗ-ЦНИИ.
Подшипники после демонтажа промывать в автоматической машине мыльной эмульсией, подогретой паром до t 90°-95°C, и просушить подогретым воздухом, пропускаемым через змеевик, размещенный внутри ванны моечной машины. Новые роликовые подшипники и подшипники, покрытые консервационной смазкой, также промыть в автоматической машине. В том случае, если осмотр подшипников будет производиться не ранее, чем через сутки после промывки, их необходимо смазывать жидким маслом.
Обмывка деталей буксового узла от смазки ЛЗ-ЦНИИ.
Промывка подшипников и деталей букс производится в моечной машине 1-2% раствором в воде технических моющих средств РИК по ТУ 2381-002-31559149-00, РИК-Н по ТУ 2381-002-54376405-03 или ЦИТОМ по ТУ 2381-003-57170644-02 при давлении 2-4 атм. и температуре 70-950С. После промывки обязательны продувка сжатым воздухом и нанесение на поверхности подшипника тонкого слоя минерального масла.
Осмотр, неразрушающий контроль и комплектовка подшипников.
Подшипники после промывки и просушки осматривать визуально с помощью лупы при рассеянном свете для определения их пригодности к дальнейшему использованию. Неисправные подшипники направить в ремонт. При выпадании отдельных роликов из гнезд сепаратора направлять их в ремонт для измерения диаметра и длины всех роликов.
У цилиндрических подшипников осматривают отдельно внутренние, наружные и упорные кольца, а также ролики и сепараторы.
Подшипники с заусенцами направляются в ремонт для их удаления.
Подшипники, имеющие на бортах наружных колец и торцах роликов задиры и повреждения типа «елочка», ремонтируют зачисткой.
Ролики перед дефектоскопированием осматривают визуально.
Все полиамидные сепараторы (как новые, так и б/у) подвергаются растяжению на специальной установке. Растяжение осуществляется до увеличения наружного диаметра каждого основания сепаратора на 0,5 мм (или 0,25 при одностороннем контроле индикатора часового типа).
Перечень деталей подшипников, подвергаемых неразрушающему контролю, с указанием зон и методов контроля а также видов работ, при которых проводится контроль, приведен в таблице 2.
Таблица 2
Перечень деталей подшипников буксового узла, подвергаемых неразрушающему контролю.
Наименование детали | Зоны контроля | Методы контроля* | Виды работ, при которых проводится контроль |
Внутренние кольца свободные | Наружная и внутренняя поверхность | ВТК | При полном освидетельствовании колесной пары |
Наружные кольца свободные | Наружная и внутренняя поверхность | ВТК | То же |
Упорные кольца | Вся поверхность | ВТК | То же |
Ролики | Цилиндрическая поверхность | ВТК | То же |
ВТК по РД 32.150 - 2000 - вихретоковый контроль;
Результаты неразрушающего контроля деталей заносят в специальный журнал.
Подшипники новые и бывшие в эксплуатации после промывки, просушки, остывания осмотра или ремонта комплектуются по радиальным и осевым зазорам, по диаметрам отверстии внутренних колец.
Измерения подшипников производить после выдержки их в комплектовочном отделении не менее 8 часов. При этом эталонные кольца и измерительные средства должны храниться в комплектовочном отделении.
Новые подшипники дополнительно к указанному выше осмотру подвергаются входному контролю.Контроль заключается в проверке качества обработки колец, роликов и сепараторов; соответствия геометрии отверстий внутренних колец требованиям ТУ; радиальных и осевых зазоров, разности длин и диаметров роликов; наличия трещин и других видимых дефектов в кольцах роликах и сепараторах; качества упаковки.
Осмотр корпусов букс.
После промывки корпуса осматривают на соответствие установленным требованиям. Внутреннюю посадочную поверхность корпуса буксы, упорный буртик (платик) и лабиринтную часть зачищают от коррозии, заусенцев и протирают концами, смоченными керосином, а затем сухими. На посадочной поверхности корпуса буксы после устранения коррозионных повреждений допускаются темные пятна, т. е. нельзя зачистку поверхности доводить до металлического блеска.
Корпуса букс, имеющие износ по посадочной поверхности (диаметру отверстия) выше допускаемой нормы, а также с повреждениями лабиринтной части, резьбовых отверстий, со сквозными отверстиями под термодатчики, с оставшимися в буксе оборванными болтами и другими повреждениями подлежат ремонту.
Категорически запрещается сдавать в металлический лом корпуса букс, подлежащие ремонту.
При поступлении новых корпусов букс производить 100%-ный контроль резьбы М20 проходными и непроходными калибрами.
Осмотр деталей букс.
Лабиринтные кольца после зачистки и промывки протирают и проверяют. На посадочных поверхностях и в лабиринте не допускаются трещины, вмятины, забоины, заусенцы и другие неисправности. Размеры проверяют в соответствии с нормами.
Крепительные и смотровые крышки после зачистки и промывки осматривают. Соединенные между собой крепительные и смотровые крышки разъединяют для замены уплотнения и вновь собирают. На крышках не допускаются трещины, вмятины, забоины, задиры, заусеницы, изгибы, перекосы и другие дефекты. Смотровые крышки, деформированные по привалочной поверхности, выравнивают. Перед монтажом крепительные крышки проверяю по плоскости прилегания к корпусу буксы с целью недопущения к монтажу крышек с ушками, имеющими деформации.
Торцевые гайки с выточкой, а также стопорные планки, шайбы и болты после промывки должны быть осмотрены.
Стопорные планки подлежат обязательному дефектоскопированию с постановкой клейм предприятия и личного клейма дефектоскописта и даты производства дефектоскопирования.
Резиновые кольца, устанавливаемые между крепительной крышкой и буксой, а также прокладки между крышками независимо от их состояния заменяют при каждой полной ревизии букс.
Монтаж буксового узла
К монтажу допускаются подшипники и колесные пары имеющие температуру окружающей среды. Поэтому монтаж букс необходимо производить не ранее, чем через 12 часов после обмывки колесных пар в моечных машинах и не ранее, чем через 2 часа после обточки кругов катания колес при ремонте, а подшипники – не ранее, чем через 8 часов после обмывки их в моечной машине.
За техническое состояние шеек, предподступичных частей осей колесных пар нового формирования и их размеры отвечают работники прессового участка.
При монтаже все резьбовые соединения деталей буксового узла покрывают тонким слоем смазки ЛЗ-ЦНИИ кроме резьбы на осях типа РУ1 и гайках М110.
Перед монтажом внутренние кольца маркируются. На торцы колец со стороны конусной фаски (со стороны стыка колец) наносится порядковый номер (начиная с первого числа каждого месяца), год и месяц постановки клейма и условный номер ремонтного предприятия. Запись маркировки внутренних колец в журнале формы ВУ-90 производить в графе «Примечание». Запрещается производить постановку внутренних колец подшипников из насквозь прокаленной стали ШХ15СГ (ШХ15, ШХ15СГШ) и колец не имеющих отличительных признаков стали марки ШХ4 с отличительными признаками. В связи с не обеспечением поставок внутренних колец из стали ШХ4 для роликовых подшипников грузовых вагонов замена всех снимаемых колец из стали ШХ15СГ (ШХ15, ШХ15СГШ) производится при фактическом их наличии в депо.
При монтаже буксового узла обязательно использование клея-герметика «Стопор-6А» (Трибопласт-6А) при навинчивании гайки М110х4.
Установка внутренних и лабиринтного кольца методом «холодной» напрессовки.
Запрессовка внутренних колец подшипников на ось должна производиться на гидравлическом прессе, обеспечивающем скорость движения плунжера 2,5…4мм/с.
За один ход плунжера гидравлического пресса должна обеспечиваться одновременная запрессовка на ось всего комплекта колец: двух внутренних колец подшипников и лабиринтного кольца.
Запрессовка на ось должна обеспечивать:
А) Натяги внутренних колец на шейке 0,040…0,065мм.
Допускается для типового подшипника натяг 0.070мм при условии, что радиальный зазор в нем более 0,12мм.
Б) Натяги лабиринтного кольца на предподступичной части 0,02…0,15мм.
В) Конечные усилия запрессовки на ось всего комплекта колец: двух внутренних колец подшипников и лабиринтного кольца, 63,8…176,6кН (6,5…18,0тс)
Г) Усилия запрессовки на ось двух внутренних колец подшипников 44,1…127,4кН (4,5…13,0тс)
Д) Предельные усилия обжатия запрессованных на ось всего комплекта колец: двух внутренних колец подшипников и лабиринтного кольца 245,2…294,3кН (25,0…30,0тс).
Предельные усилия обжатия должны поддерживаться при упоре в торец предподступичной части оси всего комплекта напрессованных на ось деталей монтируемых буксовых узлов в течении 3…5 секунд.
В корпус буксы после покрытия его посадочной поверхности тонким слоем масла последовательно вручную вставляют блок (наружное кольцо с роликами) заднего подшипника так, чтобы сторона кольца с маркировкой была обращена к лабиринтной части буксы, и блок переднего подшипника 2 так, чтобы его торец с маркировкой был обращен к передней части корпуса. Запрещается постановка в буксу колесной пары подшипников с латунными сепараторами. При монтаже буксового узла запрещается установка в корпус буксы роликовых подшипников из которых один новый а второй отремонтированный и обеспечивается установка в корпус буксы двух отремонтированных или двух новых роликовых подшипников. При монтаже буксового узла заправка обеих букс производится одним типом смазки ЛЗ-ЦНИИ.
Рис.4 – Расположение корпуса буксы при установке блоков подшипника
1 – задний подшипник, 2 – передний подшипник
Рис.5 – Расположение корпуса буксы при установке на шейку оси
Перед установкой блоков подшипников в корпус буксы ролики дорожки качения и борта наружных колец смазывают препаратом-модификатором эМПи-1.
Роликовые подшипники установленные в буксы, и проточки лабиринтной части буксы или лабиринтного кольца полностью заполняют по всему периметру смазкой. При этом в подшипниковые блоки и свободное пространство между задним подшипником и лабиринтным кольцом закладывают 0,5-0,6 кг смазки ЛЗ-ЦНИИ, а в лабиринтное уплотнение – 0,1 кг.
Корпус буксы с установленными блоками подшипников надвигают на внутренние кольца .Тугое перемещение корпуса буксы означает, что были допущены нарушения в подборе радиальных зазоров. Корпус буксы с блоками подшипников на внутренние кольца должен устанавливаться свободно, без особого усилия. При этом запрещается устанавливать на одну колесную пару буксы, корпуса которых изготовлены из алюминиевого сплава и стали.
Перед надеванием корпуса буксы с блоками подшипников необходимо раздвинуть ролики втулкой. При перемещении корпуса втулка выйдет из буксы.
После установки корпуса буксы на шейку надевают упорное кольцо переднего подшипника маркировкой, обращенной к передней части корпуса буксы, на резьбовую часть оси навинчивают гайку М110х4 высотой 51 мм .
Гайки предварительно подбирают по резьбе шейки оси для обеспечения наименьшего зазора в резьбовом соединении.
Затянуть гайку до соприкосновения с плоским упорным кольцом лююнеего подшипника и туго поджать при применении стенда или вручную при помощи гаечного ключа и молотка массой 3-5 кг двумя – четырьмя ударами, прилагаемыми на плече 0,5 м до получения чистого металлического звука.
Затем в паз оси устанавливают стопорную планку, не вводя ее хвостовик в шлиц гайки. Планку устанавливают в такое положение, чтобы при последующей затяжке гайки для ввода хвостовика планки в шлиц гайка повернулась бы от половины до одной коронки.
Затяжку гайки производят только поворотом по часовой стрелке. При затяжке гайки буксу слегка поворачивают для того, чтобы убедиться в отсутствии заклинивания подшипников. После этого устанавливают и закрепляют болты стопорной планки. Болты и отверстия под них смазывают смазкой. Под болты устанавливают пружинные шайбы. Болты связывают мягкой (отожженной) проволокой диаметром 1,5-2,0 мм проходящей через раззенкованные отверстия в их головках, независимо от установки пружинных шайб. Проволоку увязывают по форме цифры «8».
При торцевом креплении подшипников шайбой тарельчатой, последнюю после установки плоского упорного кольца переднего подшипника надевают на шейку оси. Тарельчатую шайбу прикрепляют к торцу шейки оси четырьмя или тремя болтами М20х60.4.8 с головкой, выполненной с ложной шайбой на опорной поверхности. При монтаже торцевого крепления подшипников шайбой должны использоваться болты без следов коррозии. Поврежденные болты заменяют.
Под болты правой и левой шеек оси устанавливают стопорные шайбы, на которые набивают клейма. При торцевом креплении шайбой тарельчатой болты М20 стопорят стопорной шайбой .Затягивать болты М20 тарированным или динамометрическим ключом усилием с крутящим моментом 230-250 Нм (23-25 кгс/м). Затяжка болтов должна быть равномерной. Для этого завинчивание трех болтов производят дважды по периметру, а четырех – по схеме в следующем порядке 1-2-3-4-3-4-2-1. Затем лепестки стопорной шайбы загибают клещами на грань головки каждого болта и доводят до плотного прилегания лепестков шайбы к граням головки болта.
После закрепления подшипников в осевом направлении производят установку буксовых крышек. Между крепительной и смотровой крышками при их сборке ставят новую резиновую прокладку толщиной 3 мм. Болты затягивают крутящим моментом 10-12 кгс*м. Внутренние поверхности крепительной и смотровой крышек, а также цилиндрическую посадочную поверхность крепительной крышки и соответствующую поверхность корпуса буксы, болты М20 и М12 и отверстия под них смазывают тонким слоем смазки ЛЗ-ЦНИИ. Крышки скрепляют между собой четырьмя болтами М12, под которые устанавливают пружинные шайбы, при этом запрещается устанавливать болты с различными размерами головок. Болты затягивают с применением стенда или гаечного лююча.
Смазку ЛЗ-ЦНИИ массой 0,2 кг укладывают на внешнюю поверхность гайки по всему периметру и на переднюю видимую часть подшипника и уплотняют пальцами так, чтобы смазка проникла между сепаратором и бортом наружного кольца. Общее количество смазки, закладываемой в буксы, должно быть в пределах 0,8-0,9 кг при применении смазки ЛЗ-ЦНИИ, при этом смазку можно дозировать мерной емкостью вместо взвешивания.
Между торцом корпуса и фланцем крышки устанавливают новое резиновое кольцо, имеющее сечение диаметром 4 мм, фланцевую поверхность крышки смазывают смазкой из расчета заполнения всего зазора между этой поверхностью и торцом корпуса буксы после затяжки болтов. После этого буксу закрывают крышками, прикрепляемыми к корпусу болтами М20, под которые также устанавливают пружинные шайбы. Под два болта (или один болт, если это предусмотрено конструкцией) крепительной крышки буксы правой шейки оси с левой стороны устанавливают бирку. Затягивание всех болтов крышки должно быть равномерным. Болты затягивают крутящим моментом 18-20 кгс*м. Категорически запрещается устанавливать болты с различными размерами головок.
Резиновые прокладки или резиновые кольца, бывшие в эксплуатации, независимо от их состояния, заменяют на новые.
После монтажа буксовых узлов производить обкатку прокручивание колесных пар на установке СКБУ-01 с частотой вращения 220-250 об/мин в течении 5 мин без приложения внешней нагрузки.
Правильность сборки буксы контролируют по наличию зазора между фланцевой поверхностью крепительной крышки и торцевой поверхностью буксы и по легкости ее вращения на шейке оси, которое должно быть совершенно свободным (букса вращается вручную).
Вручную проверяют осевое смещение буксы. Букса должна свободно перемещаться вдоль шейки оси в пределах осевого разбега. Не допускается защемление роликов в осевом направлении.
Буксы после монтажа подшипников окрашивают черной краской. Тщательно должны быть окрашены места соединения лабиринтного кольца с предподступичной частью оси, а также предподступичная часть между лабиринтным кольцом и колесом во избежание образования коррозионных повреждений.
ВОЗМОЖНЫЕ НЕИСПРАВНОСТИ ПОДШИПНИКОВ, КОРПУСОВ БУКС, ОСЕЙ И УСЛОВИЯ ИХ ДАЛЬНЕЙШЕГО ИСПОЛЬЗОВАНИЯ
Таблица 3
Виды возможных неисправностей, повреждений или отступлений от норм | Условия дальнейшего использования | ||
.1 Роликовый подшипник | |||
1.1 Подшипник в собранном виде Радиальный зазор меньше или больше установленной нормы. Осевой зазор меньше установленной нормы. Наличие повреждений, перечисленных ниже, в деталях подшипников | Необходимо перекомплектовать подшипник с заменой наружного кольца. Подшипник используют после зачистки торцевой поверхности нерабочего (маркированного) борта у наружных колец на значение до 0,03 мм. Зачистку производят шлифовальной шкуркой №10 на тканевой основе, а затем №6 с маслом или притиркой пастой ГОИ. Допускается перекомплектовать подшипник с заменой наружного кольца или роликов. Замена негодных деталей или устранение дефектов зачисткой с полной (при необходимости) разборкой и перекомплектовкой подшипника. | ||
1.2 Наружное и внутреннее кольца Трещины, разрывы, отколы. Раковины и шелушение (усталостные повреждения) на дорожках качения цилиндрического подшипника. Шелушение дорожек качения внутреннего кольца. Рифление дорожки качения наружного кольца подшипника. Коррозионные пятна на дорожках качения по шагу ролика. Поверхностная и точечная коррозия на дорожках качения. Задиры и заусенцы фасок бортов наружных и внутренних колец. Коррозионные раковины на дорожках качения в виде точек. Коррозионные повреждения на посадочных поверхностях. | Кольца бракуют. То же. Кольца бракуют. Кольца используют с установкой рифленой поверхностью в нерабочую зону при длине рифленого участка не более половины длины дорожки качения. Кольца бракуют. Кольца используют после зачистки пораженных коррозией поверхностей шлифовальной шкуркой №6 с маслом. Кольца используют после зачистки фасок. Зачистку производят на приспособлении или шлифовальной шкуркой №10, а затем №6 с маслом. Кольца бракуют. Кольца используют со следами коррозионных повреждений после зачистки шкуркой №6 с маслом. | ||
Потемнение поверхности качения от серого до черного цвета. Намины и мелкие риски на дорожке качения. Следы перегрева (цвета побежалости). Кольцевые риски, задиры, вмятины и забоины на нерабочих поверхностях. Монтажные забоины и задиры на поверхностях качения. Отсутствие фасок на кромках бортов наружных колец. Надиры типа елочка на бортах наружных колец, внутренних колец, плоских упорных колец. Повреждения электрическим током дорожек качения. | То же. Кольца допускаются к дальнейшему использованию. Кольца бракуют (кроме колец, имеющих соломенный цвет). Кольца используют после зачистки и сглаживания выступающих краев. Кольца бракуют. То же. Кольца используют со следами от надиров после обработки бортов на приспособлении шлифовальной шкуркой № 6 с маслом или притиркой пастой ГОИ. Допускается снимать слой по каждому борту толщиной не более 0,05 мм. Снятие слоя контролируют щупом между торцом одного из роликов и бортами колец. Кольца бракуют. | ||
.1.3 Ролики Трещины, отколы, ползуны. Вмятины на поверхности качения. Кольцевой след без разрушения поверхности металла. Коррозионные раковины на поверхности качения. | Ролики бракуют. Ролики используют. Тоже. Ролики бракуют. | ||
Потемнение поверхности качения от серого до черного цвета. Коррозия пятнами. Раковины на поверхности качения цилиндрического ролика. Точечная коррозия на нерабочих поверхностях (торцы скосы). Повреждения торцов цилиндрических роликов - надиры типа «елочка». Точки в результате повреждения электрическим током. | Ролики используют. Ролики бракуют. Тоже. Ролики используют. Ролики используют со следами от надиров после обработки на приспособлении, имеющем вертикальное перемещение ручки, шлифовальной шкуркой № 6 с маслом. Снимать допускается с каждой стороны ролика слой толщиной не более 0,005 мм. Толщину снятого слоя проверяют по высоте ролика на приборе В901. Ролики бракуют. | ||
1.4 Сепараторы Повреждение «чеканки» приводящее к выпадению роликов. | Сепараторы используют после восстановления «чеканки». | ||
2 Кoрпус буксы | |||
Продольные задиры или риски на посадочной цилиндрической части. Местная выработка на цилиндрической посадочной поверхности от проворачивания наружных колец. Коррозия на внутренней цилиндрической части. | Корпуса используют после зачистки кромок, задиров или рисок. Корпуса с выработкой, превышающей норму на овальность, ремонтируют. Корпуса используют со следами коррозии после зачистки. | ||
Местная выработка стенок отверстия под шпинтон в корпусе буксы. | Корпуса используют. | ||
Ослабление посадки отъемного лабиринта и его повреждение. | Корпус ремонтируют. | ||
Ржавчина, заусенцы, забоины на лабиринтных проточках. | Корпуса используют после зачистки лабиринтных проточек. | ||
Сквозные отверстия и поврежденная резьба под термодатчик и оставшиеся в буксе оборванные болты М20 крепительной крышки. | Корпуса ремонтируют. | ||
РЕМОНТ РОЛИКОВЫХ ПОДШИПНИКОВ
Предназначенные для ремонта подшипники промывают и осматривают для определения ремонта. Ремонт подшипников делится на два вида: первый - без переборки роликов, второй - с переборкой (измерением и подборкой роликов по диаметру и длине).
а) Первый вид ремонта
Подшипники ремонтируют без переборки роликов (без измерения роликов по диаметру и по длине) при замене сепаратора, зачистке (шлифовке) бортов колец, замене наружного или внутреннего колец, зачистке (шлифовке) дорожек качения колец. Внутренние кольца подвергают неразрушающему контролю.
б) Второй вид ремонта.
Ремонт подшипников с переборкой роликов (с измерением роликов по диаметру и длине) производят при замене роликов (независимо от количества сменяемых роликов), выпадении отдельных роликов из гнезд сепаратора вследствие повреждения чеканки, зачистке (шлифовке) образующих роликов и торцов роликов. Все подшипники со сроком изготовления старше 10 лет подвергать второму виду ремонта.
Кольца и ролики подвергают неразрушающему контролю.
При втором виде ремонта подшипник полностью разбирают. Чтобы разобрать подшипники, у которых расчеканка сепараторов произведена по перемычкам и наружные кольца скомплектованы вместе с роликами, например, у подшипников 42726 и 232726, надо ролики выдвинуть из бортов наружного кольца внутрь подшипника (рис.6а) и, сняв наружное кольцо (рис.6б), вынуть ролики из гнезд сепараторов (рис.6в). Сборка производится в обратном порядке.
У подшипников с облегченными сепараторами ролики извлекаются специальными щипцами, захватывая их по длине. Сборка подшипника производится следующим образом: а) Корпус подшипника укладывается на стол; б) В корпус подшипника свободно вставляется сепаратор; в) В гнезда сепаратора незначительным усилием вставляются ролики подшипника.
3.4. Собранный подшипник устанавливается в вертикальное положение и обрабатывается перед монтажом в буксу препаратором- модификатором ЭМПИ-1.
Разборка подшипника осуществляется путем выемки роликов из гнезд сепаратора специальными щипцами захватывая их по длине.
При выпадении отдельных роликов из гнезд сепаратора проверяют диаметр и длину всех роликов и подшипник вновь собирают. При этом разность диаметров роликов в подшипнике должна быть не более 5 мкм, а разность длин роликов - не более 12 мкм.
После разборки все детали осматривают. Особое внимание обращают на состояние сепараторов. При необходимости ролики и кольца шлифуют. Полиамидные сепараторы осматриваются визуально на наличие трещин, разрывов, сколов и механических повреждений. Сепараторы с данными неисправностями бракуют.
|
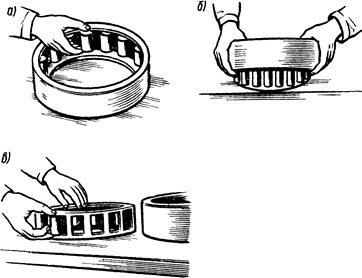
Годные для комплектования подшипников ролики сортируют (измеряют) по диаметру.
Измерение роликов по длине и диаметру может производиться на электронно-механических приборах, утвержденных ОАО «РЖД" в установленном порядке.
Устанавливается следующий порядок сортировки роликов:
а) по среднему сечению одного из роликов, принятому за эталон для данной группы роликов, настраивают прибор на нулевое положение измерительной головки;
б) остальные ролики измеряют и сортируют на группы по среднему сечению в пределах 5 мкм.
При комплектовании подшипников ролики в одном подшипнике должны быть одной группы по диаметру. Затем ролики проверяют по длине. Запрещается комплектовать цилиндрический подшипник 2726 с разными по форме роликами.
Сепараторы, применяемые при ремонте подшипника, должны иметь гладкую поверхность без срезов, отколов, трещин и повреждений.
При комплектовании подшипников необходимо следить за тем, чтобы маркировка на сепараторе (товарный знак завода-изготовителя и условное обозначение года выпуска или буквы «Ж»), торцы роликов, имеющие различные отличительные признаки, были обращены в ту же сторону, что и маркировка на наружном кольце.
Отремонтированные подшипники осматривают и проверяют по радиальному зазору, который должен быть 0,09-0,25 мм.
На отремонтированные подшипники наносят следующую надпись: на наружном кольце подшипника после номера ставят букву PI или PII в зависимости от вида ремонта (месяц римскими цифрами и две последние цифры года) и условный номер вагоноремонтного предприятия, производившего ремонт.
Учет отремонтированных подшипников ведется по журналу ф.ВУ-93.
Подшипники следует хранить в чистом сухом отапливаемом помещении с температурой воздуха не ниже +100С без резких колебаний температуры.
Подшипники не следует хранить в помещениях, в которые могут проникнуть пар, газы, кислоты и пыль. Запрещается брать подшипники грязными, влажными или потными руками, так как это способствует образованию коррозии.
В монтажном отделении разрешается хранить детали буксового узла промытые, проверенные, отремонтированные и годные к монтажу.
Подшипники, транспортируемые на другие предприятия, следует подвергать консервации, обертывать в парафинированную бумагу и плотно укладывать в деревянные ящики с защитой от атмосферных воздействий.
СЕПАРАТОРЫ
При входном контроле подшипников, поступающие в вагоноколесные мастерские, а также осмотрах при плановых видах ремонта подшипников типа 30-42726Е2М и 30-23276Е2М, осмотр и проверка сепараторов из стеклонаполненного полиамида (как новые, так и б/у) производится на приборе КС221.А или специальном приспособлении.
При осмотре сепараторов не допускается к эксплуатации сепараторы, имеющие трещины, разрывы, сколы.
При каждом осмотре сепаратора производится испытание его на статическую прочность на вышеуказанном приспособлении, при этом сепаратор должен быть равномерно растянут так, чтобы его наружный диаметр увеличился на 0,5 мм.
ОХРАНА ТРУДА
1 Вагоноколесные мастерские имеют устройства для отопления и вентиляции, обеспечивающие микроклиматические условия в соответствии с требованиями “Санитарных норм проектирования предприятий”.
2 Оборудование, где происходит образование пыли и газов должно быть оборудовано вентиляцией.
3 Осветительная арматура и лампы должны очищаться от загрязнений не реже 2-х раз в месяц, а стекла световых проемов 2 раза в год.
Освещение на рабочих местах должно быть как общее, так и местное.
Применение одного местного освещения не допускается.
4 Уровень шума в ВКМ не должен быть выше:
- низкочастотный - 100дб.
- среднечастотный - 85-90дб.
- высокочастотный - 75-85дб.
Нормы освещенности - общее -местное -500 лк.
Участки осмотра и приемки колесных пар - 750 лк.
5 Курение в цехах запрещено.
6 Средне суточная температура в ВКМ должна быть +18 ,+20 .
7 Не допускается загромождение и захламление служебных проходов, проходов к электрощитам, пожарным щитам.
8 Шкафы, ящики и стеллажи для инструмента и деталей устанавливается так, чтобы хранимые в них предметы находились в устойчивом положении и не могли упасть.
9 Полы на рабочих местах должны быть ровными, гладкими, отходы, стружка должны своевременно убираться.
10 У металлорежущих станков окрашиваются движущиеся части в желтый цвет. Трубопровод окрашивают в зеленый цвет, паропровод окрашивают в ярко-красный цвет, воздухопровод окрашивают в голубой цвет, маслопровод окрашивают в коричневый цвет.
Требования к инструменту.
1 Слесарные молотки должны иметь слегка выпуклую поверхность бойка и надежно укреплены на ручке путем расклинивания.
2 Ударные инструменты-зубила, крейцмейсели, бородки не должны иметь трещин, заусенец, наклепа на ударной части. При работе обязательно пользоваться защитными очками, во время работы зубило располагать от себя, т.е. направление полета металла при ударе должно осуществляться в противоположную сторону от себя.
3Весь ручной инструмент должен быть исправным и очищенным от масла.
4 К работе с пневматическим инструментом допускаются только специально обученные работники.
Требования к оборудованию.
1 Расположение оборудования в ВКМ должно соответствовать нормам технологического проектирования.
2 Границы проходов, места укладки грузозахватов и тары должны быть отмечены белой краской.
3 Запрещается производить замер деталей во время работы станка.
4 По завершении работ оборудование должно быть отключено.
5 Металлические кожухи должны быть заземлены.
6 Все оборудование и его части должны быть заземлены. Все открытые вращающиеся части станков должны быть закрыты кожухами.
7 Для защиты глаз от попадания стружки, рабочий обязан работать в защитных очках.
8 Станок должен содержаться в чистоте, стружку следует убирать после каждой смены, в случае образования ленточной стружки для ее ломки можно применить металлический крюк с гладкой рукояткой.
8 Каждый работник должен быть обеспечен средствами индивидуальной защиты .Работникам запрещается работать в не застегнутой одежде.
9 У каждого станка должен быть вывешен список работников, допущенных для работы на данном станке.
Слесарные работы.
К работе по ремонту колёсных пар грузовых вагонов, допускаются лица достигшие возраста восемнадцати лет, прошедшие обучение и проверку знаний по специальности и охране труда, прошедшие обязательный предварительный при поступлении на работу медицинский осмотр, вводный и первичный инструктажи на рабочем месте по охране труда, противопожарный инструктаж, стажировку и первичную проверку знаний требований охраны труда.
В процессе работы слесарь должны проходить в установленном порядке периодические медицинские осмотры, повторный инструктаж не реже одного раза в три месяца, а также внеплановый и целевой инструктажи по охране труда, обучение по охране труда, периодическую и внеочередную проверку знаний требований охраны труда.
При обнаружении нарушений требований охраны труда
или неисправностей оборудования, механизмов, инвентаря, инструмента,
защитных приспособлений, средств индивидуальной защиты и пожарной
безопасности, слесарь должен сообщить об этом мастеру (бригадиру), а в его отсутствие - вышестоящему руководителю и далее выполнять его указания.
Дата добавления: 2015-02-19; просмотров: 3820;