Тема 4.Прессование изделий из термореактивных материалов
Процесс прессования изделий из реактопластов основан на способности связующего при нагревании в матрице пресс-формы переходить в вязко-текучее состояние, течь под давлением пуансона, заполняя оформляющие гнезда с последующим отверждением для фиксирования формы изделия.
Под действием температуры в связующем пресс-материал начинается химическая реакция отверждения. Например, пресс-материалы, содержащие резольные смолы, при нагревании образуют неплавкие и нерастворимые продукты трехмерной структуры (резиты), благодаря наличию в их макромолекулах реакционноспособных метильных групп: образование трехмерных химических связей происходит через атом кислорода.
При прессовании не нагретый или предварительно нагретый материал загружается в нагретую до необходимой температуры формующую полость (матрицу) пресс-формы. Пресс-форма состоит из матрицы и пуансона (рис.1). Конфигурация пресс-формы соответствует форме изделия. Пресс-форма имеет нагревающие элементы и выталкиватели (рис.4).
Рис 5. Схема изготовления изделий методом прямого прессования
Литьевое прессование
Рис. 6. Пресс-формы для литьевого прессования с верхней (а) и нижней (б)
загрузочными камерами:
1 - нижняя плита; 2 - матрица; 3 - воздушные каналы; 4 - изделия,
5 - верхняя плита; 6 - литниковые каналы; 7 - пресс-остаток;
8 - камера; 9 - шток; 10 - стержень толкателя; 11- выталкиватель
Материал в виде таблеток, порошка после предварительного нагрева подается в загрузочную камеру, нагретую до необходимой температуры, где дополнительно нагревается при опущенном штоке. Затем штоком через литниковые каналы под давлением 80¸120 МПа передавливается в оформляющую полость формы.
Вследствие того, что материал течет через нагретые литниковые каналы и вследствие выделения теплоты от вязкого течения температура материала повышается. При наличии скорости сдвига в литниковых каналах материал тщательно перемешивается и становится более равномерно прогретым. При поступлении нагретого материала в форму, где давление равно атмосферному, происходит интенсивное выделение газообразных продуктов и удаление их через воздушные каналы. После заполнения формующей полости пресс-материал затекает в них, а так как каналы имеют небольшую глубину, материал в них быстро отверждается и они перекрываются. В результате создается замкнутый объем и давление в форме растет до 25-30 МПа, что обеспечивает уплотнение материала.
Стадии прессования
1.Подготовка сырья
1.1Дозировка
1.2Таблетирование
1.3Предварительный нагрев
-предварительный нагрев между горячими металлическими поверхностями;
-предварительный нагрев в печи;
-предварительный нагрев в инфракрасных лучах;
-высокочастотный предварительный нагрев;
-микроволновый предварительный нагрев;
2. Формование
-смыкание пресс-формы,
-подпрессовка,
-выдержка под давлением для отверждения,
-размыкание пресс-формы,
-извлечение изделия,
- очистка пресс-формы
3 Обработка изделий
-термическая обработка
- механическая обработка изделий
4. Переработка отходов
Подготовка сырья к прессованию
Начинается с разборки по партиям, имеющим близкие технологические показатели. Это необходимо для сокращения потерь времени и сырья при перестройке технологического процесса, связанного с переходом на другую партию сырья.
Если сырье влажное - сушат при температурах: 100°С для новолачных пресс-порошков, 80°С - резольных и волокнита. Высушенное сырье хранят в герметичной таре.
Предварительный нагрев материала
Рис 7.Высокачастотный нагрев |
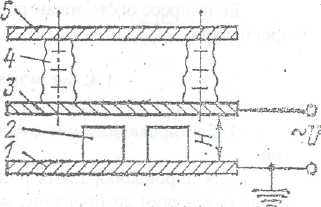
Преднагрев можно проводить в сушильных шкафах, в высокочастотных установках и с помощью инфракрасных нагревателей (лампы, трубчатые элементы или нихромовые спирали).
Нагревание в сушильных шкафах происходит за счет конвективной теплопередачи от нагретого воздуха, поэтому процесс длителен и не обеспечивает равномерности температуры. Применяется для нагрева полимеров с высокими диэлектрическими характеристиками, когда невозможно использовать высокочастотный нагрев, а также прозрачных листов, когда инфракрасный нагрев неэффективен.
Высокочастотный нагрев осуществляется следующим образом.
Верхняя пластина 1 (рис. 7) закрепляется на корпус 2, с помощью высокочастотных изоляторов, и к ней подводится ток напряжением 8-10 кВ с частотой 40 и 80 МГц. Нагреваемый материал (чаще в виде таблеток) помещают в электрическое поле на заземленную пластину 5, расположенную на расстоянии Н от другой пластины. При подключении пластин к генератору высокой частоты между ними создается электрическое поле с напряженностью Е 200-250 кВ/м (если больше, то может быть пробой)
,
где U – подводимое напряжение.
Способность полимеров к высокочастотному нагреву зависит от их строения. Неполярные полимеры (ПЭ, ПС, фторопласт) практически в электрическом поле не нагреваются и могут применяться для изготовления высокочастотных изоляторов. Полимеры, имеющие полярное строение (ПВХ, ФФС и др.), очень быстро нагреваются. Склонность полимеров к нагреву ТВЧ можно определить по значению фактора диэлектрических потерь e×tg d, где e - диэлектрическая проницаемость пресс-материала; tg d -тангенс угла диэлектрических потерь. Чем больше e×tg d, тем больше электрической энергии переходит в тепловую. Мощность генератора, преобразуемая в теплоту, определяется Р=5,5-10 -e×tg d×f×E , где f - частота переменного тока.
При использовании высокочастотных установок достаточной мощности время нагревания 20-30 с, а температура материала после прогрева 120-130°С. Несмотря на высокие тепловые потери в окружающую среду (коэффициент потерь 0,4-0,5), применение высокочастотного нагрева экономически выгодно, так как сокращается время отверждения (~20-30%), давление формования (~ вдвое).
Применяют генераторы, работающие при частоте 15-50 МГц и имеющие рабочую поверхность конденсатора 300x300 мм.
При применении инфракрасного нагрева интенсивность излучения зависит, главным образом, от температуры излучателя, а количество поглощающей энергии - от степени черноты нагреваемого тела, а также от расстояния до излучателя.
Инфракрасный нагрев не эффективен при нагревании прозрачных полимеров (ММА, ПЭТФ), так как большая часть лучистой энергии рассеивается в окружающую среду.
Если пресс оборудован шнековым пластикатором, то преднагрев не проводится.
1.4. Загрузка пресс-материала в форму
Таблетированные материалы чаще всего дозируются по числу таблеток.
Для порошкообразных наполнителей применяется объемное или весовое (массовое) дозирование, для нетаблетированных волокнистых - весовое.
Объемное дозирование производится с помощью мерного сосуда или бункера. Рационально объемное дозирование использовать только для загрузки многогнездных форм. Недостаток заключается в том, что партии материала отличаются по насыпной плотности и поэтому необходимо часто изменять мерный объем, что на практике довольно сложно.
При массовом дозировании, если использовать электронные дозаторы, то обеспечивается высокая точность навески и хорошее качество изделия.
Если в изделие устанавливается арматура (резьба, болты и др.), то ее устанавливают до загрузки пресс-материала, и лишь в редких случаях впрессовывают в уже сформованное изделие сразу после прессования или в не полностью отвержденное изделие. Арматуру крупных размеров перед установкой в форму нагревают.
1.5. Смыкание пресс-формы
Процесс прессования изделия осуществляется в результате опускания пуансона, закрепленного на подвижной плите пресса, и создания необходимого удельного давления. Удельным давлением прессования называют эффективное усилие пресса, приходящееся на единицу площади прессования. Слишком быстрое смыкание формы может привести к выбросу материала и резко увеличивает износ формы, поэтому перед соприкосновением пуансона и матрицы необходимо замедлить ход пуансона. В некоторых случаях задерживают подачу высокого давления и после соприкосновения пуансона с матрицей дают выдержку при небольшом давлении. К этому приему прибегают при повышенной текучести материала, при формовании сложных по конструкции изделий с тонкими стенками. Задержка давления позволяет снизить текучесть, за счет частичного отверждения, улучшить условия заполнения формы и условия прессования.
1.6. Подпрессовка, выдержка под давлением, отверждение
В целях удаления летучих из полости пресс-формы используют специальный прием - подпрессовку. Когда материал нагреется, начинается процесс поликонденсации, сопровождающийся выделением летучих продуктов. Кроме того, удаляется влага, находящаяся в пресс-материале.
Для удаления образовавшихся летучих пресс-форму размыкают, поднимая на высоту 10-20 мм на 3-5 с для быстро отверждающихся и 5-10 с для медленно отверждающихся пресс-материалов. При этом из нагретого, но еще вязко- пластичного материала легко удаляются летучие.
Если материал был предварительно нагрет, то подпрессовку проводят сразу же после смыкания пресс-формы, так как процесс отверждения протекает очень интенсивно.
Если изделие имеет большую толщину, а преднагрев осуществлялся до невысокой температуры, то подпрессовку проводят через 30-60 с после смыкания пресс-формы.
Подпрессовка для быстро отверждающихся материалов проводится не позднее, чем через 10 с после полного смыкания формы, а для медленно отверждающихся - через 10-30 с. Число подпрессовок обычно не превышает 3-4. Если подпрессовка проводится после частичного отверждения материала, то выходящие из объема изделия газообразные продукты разрывают отвержденный поверхностный слой, нарушая монолитность поверхности изделия.
Без подпрессовок, как правило, формуются небольшие изделия с металлической арматурой или знаками. С ростом числа подпрессовок снижают продолжительность отверждения на 30-40%. При прессовании изделий на основе эпоксидных и полиэфирных смол подпрессовки не применяют, так как при отверждении летучие не образуются.
Выдержка производится в сомкнутой пресс-форме под давлением. При этом завершается процесс отверждения с формированием трехмерной структуры. На стадии отверждения давление необходимо лишь для исключения раскрытия формы под действием выделяющихся продуктов и может быть снижено до 8-9 МПа. Однако из-за конструктивных особенностей гидропресса давление сохраняется на уровне давления в момент смыкания формы. После отверждения изделие извлекается из формы без охлаждения.
1.7. Промежуточный контроль качества изделия
Контроль качества изделия проводится на рабочем месте непосредственно после извлечения его из формы. Отбраковываются изделия недо-прессованные, имеющие трещины, вздутия, разводы, и изделия с толстым гратом. При наличии требований по однотонности изделий, количеству включений и размерной точности изделий проводится проверка и по этим показателям.
1.8. Термическая обработка изделия
Термическая обработка изделий, полученных методом прессования, заключается в их отжиге при повышенных температурах с целью уменьшения уровня внутренних напряжений. Причиной появления внутренних напряжений в основном является неравномерность отверждения материала в элементах изделия, имеющих различную толщину. Внутренние напряжения приводят к растрескиванию и короблению изделий. Отжиг осуществляют путем нагревания изделия на воздухе или в масле до 120-150°С с последующим медленным охлаждением.
1.9. Механическая обработка изделия
Проводится с целью удаления механическим путем излишков материала (облоя, грата), образующихся из-за затекания расплава в плоскости разъема форм; с целью обеспечения требуемой конфигурации изделия, изготовления резьбы или доводки размеров изделия, если формование механически сложно или экономически невыгодно, а также для отделки изделий (шлифовка, полировка и т.д).
1.10. Переработка отходов прессования
Заключается в сборе и измельчении бракованных изделий, удаленного облоя (грата), стружки, образующейся при механической обработке. Отходы пресс-материалов сортируются по маркам материала и иногда по цвету. Измельчение отходов проводят последовательно на дробилках ножевого и ударного типов до порошкообразного состояния. Полученные порошкообразные отходы могут быть добавлены в количестве 15-20% к первичному сырью и использованы для получения неответственных изделий бытового назначения.
Конструкции пресса
Рис. 8. Автоматический пресс с объемным дозированием: 1 — нижняя плита; 2 — верхняя плита; 3 — кожух концевого выключателя; 4— устройство управления; 5 — привод; 6 — гидравлический плунжер |
Основными технологическими параметрами компрессионного (прямого) прессования являются температура прессования, давление прессования и время выдержки под давлением. Технологические параметры зависят от технологических свойств перерабатываемого пресс-материала, тесно взаимосвязаны между собой и их выбирают по справочным данным с учетом размеров и сложности конфигурации изделия (табл. 1).
Выбор температуры пресс-формы зависит от скорости отверждения пресс-материала, его текучести, содержания влаги и летучих, конфигурации и размеров изделия.
Температуру прессования обычно устанавливают опытным путем в зависимости от его технологических свойств для перевода связующего в вязко-текучее состояние и последующее достаточно быстрое отверждение изделия.
Нижние пределы рекомендуемых температурных интервалов следует применять для пресс-материалов с высокой скоростью отверждения, малой текучестью и большом времени смыкания формы, большим содержанием влаги и летучих, крупногабаритных толстостенных изделий.
С увеличением температуры прессования снижается необходимое удельное давление, сокращается время выдержки под давлением, улучшаются физико-механические свойства изделий. Ограничения на повышение температуры связаны с ухудшением текучести пресс-материала и высокой экзотермичностью процесса отверждения, что способствует повышению температуры материала, особенно при формовании толстостенных крупногабаритных изделий. Однако при очень высокой температуре возможно появление вздутий, трещин на поверхности изделия из-за слишком быстрого отверждения поверхностных слоев и невозможностью удаления газообразных изделий, находящихся внутри изделия.
При малой толщине стенки изделия рекомендуется сочетать высокую температуру пресс-формы с высоким давлением прессования; при большой толщине стенки – низкую температуру пресс-формы с невысоким давлением.
Давление прессования, действующее на материал в форме, необходимо для его уплотнения и придания конфигурации. Уровень давления определяется типом формуемого материала, его вязкостью на стадии заполнения формы, высотой и толщиной стенок изделия, наличием знаков и арматуры в формуемом изделии, скоростью опускания пуансона. Так, с ростом текучести материала и температуры пресс-формы давление снижается, а ростом отношения высоты значения заполнения к толщине стенки изделия давление прессования повышается.
При выборе давления прессования имеется ввиду удельное давление – эффективное усилие, создаваемое прессом и приходящееся на 1 см2 площади горизонтальной проекции детали. Оно зависит от текучести материала и должно обеспечить течение размягченного материала, заполнение оформляющей полости формы. Поэтому для прессования деталей сложной конфигурации требуются более высокие давления.
Время цикла прессования (tц) складывается из времени, необходимого для опускания пуансона (tоп), загрузки пресс-материала (tз), выдержки его в форме под давлением (tвыд), выталкивания готового изделия (tвыт) и подготовке формы к следующей запрессовки (tподг):
tц=tз+tоп+tп+tвыд+tподг.
Время выдержки материала в пресс-форме зависит от вида и марки пресс-материала, скорости нагревания материала до температуры отверждения, скорости отверждения, толщины изделия.
Оно влияет на качество изделий и производительность пресса.
Вопросы для закрепления знаний
1. Устройство пресса?
2. Стадии прессования?
3. Что такое подпрессовка?
4. Способы предварительного нагрева материала?
Дата добавления: 2017-09-19; просмотров: 607;