Сдвоенные прямодействующие насосы имеют общие четырехкамерные клапанные коробки.
8.Клапаны (самодействующие):
· металлические (латунь, бронза, сталь),
· неметаллические (кожа, резина, пластмассы), композитные (металлические клапаны с облицовкой из кожи, пластмассы, бакаута и др.). Резиновые клапаны не выдерживают высокой температуры и разрушаются под действием масла, попадающего в конденсат.
9. По конструкции клапаны бывают:
· тарельчатые,
· конические,
· пластинчатые (одна или несколько пластин волнистых или плоских толщиной 2—5 мм, набор латунных пластин толщиной 1—1,5 мм, нижние пластины имеют отверстия диаметром 4 мм, сдвинутые одни относительно других),
· кольцевые (одно- и многокольцевые),
· шаровые.
· откидные.
К.п.д. и мощность поршневого насоса.
Полезную мощность N (кВт) поршневого насоса определяют по формуле:
N=QρgH/1000,
где (Q — подача насоса, м3/с; ρ — плотность перекачиваемой жидкости, кг/м3;
g - ускорение силы тяжести, м2/с;
Н — напор, создаваемый насосом, м; 1000 — переводной коэффициент).
Полезную мощность насоса в условиях эксплуатации можно определить по выражению
Nп= pмQс
Где: pм = рман + pвак— манометрический напор, развиваемый насосом кПа;
рман и pвак — показания манометра и мановакуумметра, кПа;
Qc — подача насоса, м2/с.
Для определения мощности насоса необходимо знать величины
гидравлических, объемных и механических потерь в насосе.
Гидравлические потериhвызваны вихреобразованием в жидкости и трением ее о стенки
проточных полостей насоса. У поршневых насосов скорости жидкости в проточной части и
гидравлические потери малы, поэтому гидравлический КПД достаточно высок и составляет
0,6—0,98. Объемные потери q складываются из щелевых qщ и чисто объемных qч.о., т. е.
q = qщ + qч.о.
Щелевые потери qщ, представляют собой протечки жидкости через зазоры в уплотнениях
клапанов, поршней и сальников.Чисто объемные потери qч.о. характеризуют степень заполнения
цилиндра перекачиваемой жидкостью вследствие выделения из жидкости растворенных в ней
газов, отрыва жидкости от поршня при чрезмерно большом числе двойных ходов поршня и т.п.
Чисто объемные потери qч.о. по сравнению со щелевыми вызывают несущественные потери
энергии, чем практически пренебрегают, тогда q ≈ qщ.
Действительная подача насоса с учетом объемных потерь составитQ = Qт - q,
Где: Qт — идеальная (теоретическая) подача.
По ГОСТу величина объемного КПД поршневого насоса должна находиться в пределах
0,82— 0,99. Раздельное определение щелевых и чисто объемных потерь опытом или расчетом
крайне затруднительно. Поэтому у поршневых насосов вместо объемного КПД определяют
коэффициент подачи ηп = Q/Qт.
Механические потери энергии Nм от механического трения в сальниках, поршнях, подшипниках
и кривошипно-шатунном механизме зависят от конструкции насоса, его технического состояния
и работы системы смазки. У прямодействующих насосов трущихся деталей меньше, чем у
кривошипных, и механический КПД у таких насосов более высок и обычно составляет 0,85 —
0,95, тогда как у кривошипных насосов он составляет 0,65 — 0,90.
Рис. 22 Графики подачи поршневых насосов.
В условиях эксплуатации на судах поршневые насосы имеют ряд преимуществ по сравнению с насосами других типов.
К достоинствам поршневых насосов относятся:
· способность самовсасывания («сухого» всасывания);
· возможность достижения высоких давлений;
· способность перекачивания разнообразных жидкостей при различных температурах, в том числе многокомпонентных сред большой вязкости;
· к. п. д.; простота конструкции и надежная работа прямодействующих насосов, которые при наличии на судне парового котла не требуют специальных двигателей.
К недостаткам поршневых насосов относятся:
· неравномерность подачи и колебание давления; большие габариты и масса;
· большой расход пара (20--60 кг/ч на 736 Вт) у прямодействующих насосов;
· необходимость применения воздушных колпаков и контроля работы;
· резкое снижение подачи при работе на жидкостях, отличающихся высоким давлением насыщенных паров.
Объёмная производительность (подача) поршневого насоса определится по формуле:
Q = F*s*n*k*ηн ,
где: Р - площадь поршня М2 S - ход поршня, м;
n - частота вращения коленчатого вала, об/мин ;
к - коэффициент подачи насоса.
Поршневой насос (конструкция рис. 21). Насос предназначен для перекачки воды и нефтепродуктов. У насосов, перекачивающих нефтепродукты, поршни 2 чугунные с текстолитовыми уплотнительными кольцами, а у перекачивающих воду, поршни латунные с эбонитовыми кольцами.
Роторными называются насосы, у которых механическая энергия равномерно вращающегося ротора-вытеснителя, создаёт энергию перемещающегося потока жидкости.
РОТОРНО - ШЕСТЕРЁНЧАТЫЕ НАСОСЫ
Конструктивно роторы выполняются в виде сопрягаемых зубчатых шестерен (шестеренные насосы), в виде одного или нескольких сопрягаемых винтов (винтовые насосы), с одной или
![]() |
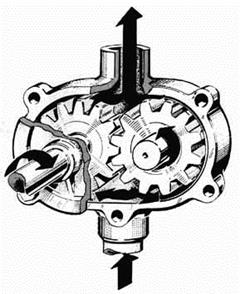
Рис. 23 Роторные насосы.
несколькими вращающимися пластинами (пластинчатые насосы). Подача роторных насосов равномерная, им не нужны клапаны для обеспечения всасывания или нагнетания. Роторные насосы используются для перекачивания чистых вязких жидкостей, не приводящих к износу трущихся поверхностей и большим утечкам через зазоры. Насос (рис 23.) состоит из ведущей 4 и ведомой 9 шестерен, входящих в зацепление и вращающихся в корпусе 3. При вращении шестерен, раскрываются их впадины, и в полости всасывания создаётся пониженное давление Р1. Жидкость заполняет впадины и переносится в полость нагнетания, где вытесняется из неё зубьями входящими в зацепление и отводится при давлении нагнетания Р2.
Рис.24. Запирание жидкости во впадинах шестерён.
![]() |
В шестеренном насосе возникают явления запирания жидкости (рис.24). Во впадине зубьями создаётся давление до 40 МПа и жидкость нагревается. При выходе зуба из зацепления давление со стороны всасывания падает и жидкость вскипает, что может сорвать всасывание насоса. Предупреждают закипание жидкости различными конструктивными мерами: создают зазор 0,2-0,5 мм в зацеплении; соединяют впадины ведомой шестерни разгружающими сверлениями; делают соединительные полости на торцевых крышках.
В шестеренном насосе жидкость перекачивается посредством вращающихся шестерен, находящихся в зацеплении. Шестеренные насосы выполняют с внутренним или внешним зацеплением, с прямозубыми, косозубыми и шевронными шестернями. У косозубых и шевронных шестерен зацепление происходит не сразу по всей ширине, как у прямозубых, а постепенно. Такие насосы менее чувствительны к погрешностям изготовления и монтажа, меньше изнашиваются и работают плавно и бесшумно, обладают высокой равномерностью подачи.
На судах распространены шестеренные насосы с внешним зацеплением. Шестерни насоса находятся под действием разности давлений в полостях нагнетания и всасывания. Кроме того, на них действует реакция от вращающего момента на ведущей шестерне. Результирующая этих сил определяет радиальную нагрузку подшипников насоса. Наиболее нагруженными оказываются подшипники ведомой шестерни.
В шестеренных насосах с коэффициентом перекрытия зацепления, большим единицы, и в насосах, не имеющих зазоров при зацеплении, происходит запирание жидкости во впадинах. При таком зацеплении часть жидкости оказывается запертой во впадине шестерни входящим в нее зубом.
Уменьшение запертого объема, сопровождающееся сжатием жидкости, приводит к появлению дополнительной радиальной пульсирующей нагрузки на шестерни, валы и подшипники. Объемный КПД шестеренного насоса равен 0,7--0,85.
По мере изнашивания деталей это значение уменьшается. Потери энергии на трение также велики; они обусловлены трением торцов шестерен о боковые диски, трением в подшипниках и уплотнении.
Развитые поверхности трения вызывают значительные механические потери, поэтому механический КПД не превышает 0,6--0,7.
РОТОРНО - ВИНТОВЫЕ НАСОСЫ
Рис. 25. Винтовой насос.
1 — ведущий вал; 2 — ведомые винты; 3 — предохранительно-перепускной клапан.
Эксплуатация роторных насосов (пуск и работа насоса, неполадки в работе насоса). Правила технической эксплуатации.
Перед пуском насоса производят следующие операции:
1. Осматривают насос и его привод;
2. Насос заливают перекачиваемой жидкостью;
3. Открывают приёмный и напорный клапаны на трубопроводе;
4. Открывают арматуру на трубопроводах;
5. Запускают приводной двигатель.
ВНИМАНИЕ! Пуск насоса при закрытом нагнетательном клапане категорически запрещён.
Во время работы насоса следят за показаниями:
1.вакуумметра на приёмном патрубке;
2.манометра на нагнетательном патрубке;
3.амперметра приводного электродвигателя;
4.состоянием сальников и соединительной муфты.
Насос не обеспечивает напора и подачи:
1. Подсос воздуха в приёмном трубопроводе или через сальник;
2. Засорена сетка приёмного фильтра;
3. Нарушена регулировка перепускного (предохранительного) клапана (при ослаблении его пружины жидкость перепускается из нагнетательной во всасывающую полость);
4. Большие зазоры в радиальном и торцевых, направлениях и в зацеплении.
Насос греется или потребляет завышенную мощность:
1. Повышенное давление нагнетания;
2. Имеются механические повреждения в роторе;
3. Нарушены зазоры в зацеплении роторов.
Остановка насоса.
Остановить приводной двигатель. Закрыть напорный и приёмный клапаны.
Для высоких давлений применяют нерегулируемые пластинчатые насосы двукратного действия. Применяют на судах в гидравлических рулевых машинах и гидравлических приводах палубных механизмов.
Рис. 26. Пластинчатый насос.
ПЛАСТИНЧАТЫЕ НАСОСЫ
Пластинчатые насосы (простейшая схема рис. 26). В корпусе насоса однократного действия (рис. 26.а и 26.6) с эксцентриситетом вращается двухпластинчатый ротор 1. Пластины 3 размещены в сквозном пазу ротора и прижимаются к корпусу пружинами 2. При вращении ротора пластины образуют с ротором и корпусом две полости: всасывающую и нагнетательную. Полости постоянно разобщены благодаря плотному прилеганию ротора к корпусу за счёт эксцентриситета. Для увеличения равномерности подачи насосы выполняются с большим числом пластин. Изменение направления потока осуществляется изменением направления вращения ротора. Насосы применяются главным образом в гидравлических системах.
Основные характеристики пластинчатых насосов:
Подача = Q н м3/ час ,0,3 –50
Напор =H н м вод. ст, до 70
Высота всасывания Рв, м. вод.ст. (МПа) , до 6,5 (0,65)
Частота вращения nн, об/мин ,до 3000
РОТОРНО-ПОРШНЕВЫЕ НАСОСЫ
В гидравлических передачах мощности механизмам судна наиболее широкое применение получили роторно-поршневые насосы.
Роторно-поршневым насосом называют роторно-поступательный насос с рабочими органами в виде поршней или плунжеров. Различают насосы радиально-поршневые, у которых ось вращения перпендикулярна осям поршней, и аксиально-поршневые, у которых ось ротора параллельна осям поршней.
РАДИАЛЬНО - ПОРШНЕВЫЕ НАСОСЫ
![]() |
Рис. 27. Радиально-поршневой насос.
Внутри цилиндрического корпуса 1 расположен звездообразный блок 2 цилиндров с поршнями (плунжерами) 4, которые могут совершать возвратно-поступательное движение. Поршни опираются на ползуны 3, которые при вращении ротора скользят по внутренней поверхности направляющего кольца (обоймы) 6, перемещаемого в поперечном направлении относительно корпуса насоса тягами 7. При этом создаётся эксцентриситет между осью ротора и кольца. Центральная неподвижная часть насоса имеет перемычку 5, отделяющую верхнюю полость насоса а от нижней б, которые соединены с полостями цилиндров ротора. При работе насоса ротор вращается с постоянным числом оборотов в неизменном направлении. Производительность (подача) насоса будет меняться в зависимости от положения обоймы в корпусе. «0» подачи соответствует концентричному расположению обоймы в корпусе, а неполная или полная подача зависит от величины эксцентриситета. В зависимости от положения обоймы (сдвинута вправо или влево) в корпусе, насосные полости а,б будут менять своё назначение, становясь всасывающей или нагнетательной, при этом поток создаваемый насосом в присоединённых к этим полостям трубах будет менять своё направление.
Рабочая жидкость насоса - минеральное масло.
Радиально - поршневые насосы имеют высокий к.п.д. (объемный 0.96-0,98 и механический 0,80--0,95) и ресурс работы до 40 000 ч, в связи с чем их широко применяют в различных отраслях промышленности, а также на судах.
Мощность отдельных радиально-поршневых насосов достигает 3000 кВт, а подача -- 500 м3ч. Они рассчитываются на номинальное давление 10--20 МПа.
АКСИАЛЬНО - ПОРШНЕВЫЕ НАСОСЫ
Рис.28. Аксиально-поршневой насос.
Аксиально-поршневые нерегулируемые насосы с постоянным направлением потока, наклонным блоком и двойным карданом выпускаются отечественной промышленностью трех типоразмеров:
Н71Н, Н140Н и Н250Н (Н - насос, цифра - рабочий объем, см3, Н - нерегулируемый).
При работе на номинальном режиме они имеют до первого капитального ремонта ресурс более 5000 ч. Причем через каждые 2000 ч работы необходимо заменять уплотнительные манжеты, утечка жидкости через которые не должна превышать 0,5 см3/ч. В конце ресурса объемный к.п.д. не должен снижаться более чем на 10%. Привод насоса предусмотрен через упругую муфту. Корпус должен быть ниже уровня рабочей жидкости в системе. На валу 1 приводного двигателя на шпонке сидит фланец, соединённый шарнирно 8 шатунами 3 с блоком цилиндров 7 с поршнями 6, который при работе насоса вращается. При отклонении оси блока от оси вала на угол α, поршни начинают совершать возвратно-поступательное движение в своих цилиндрах, обеспечивая перекачивание жидкости по каналам неподвижного распределительного диска 12 из области всасывания 4 в область нагнетания 5. Вращающийся блок цилиндров опирается на распределительный диск 12 с разделённой полостью, которая каналами 10 и 11 сообщается с полостями цилиндров блока. При работе насоса в зависимости от знака угла αнаклона блока в полостях цилиндров будет происходит всасывание или нагнетание, при этом поток создаваемый насосом будет менять своё направление. Производительность насоса зависит от величины угла α наклона блока.
АПН по сравнению с РПН имеют более высокие значения объёмного и механического КПД, потребляют меньшее усилие для изменения угла наклонения оси блока, чем для перемещения направляющего кольца.
Роторно-поршневые гидравлические машины широко используют в качестве гидродвигателей. Гидродвигатели используются в гидроприводах палубных механизмов.
Вопросы для повторения и самопроверки:
1. Дайте определение понятию «насос» и объясните принцип его действия.
2. Объёмные насосы вытеснения, их виды и принцип действия.
3. Лопастные насосы, их виды и принцип действия.
4. Струйные насосы, их виды и принцип действия.
5. Дайте определение понятию «производительность» насоса.
6. Дайте определение понятию «напор» насоса.
7. Дайте определение понятию «полезная или гидравлическая мощность насоса» и запишите её выражение.
8. Дайте определение понятию «эффективная мощность насоса» и запишите её выражение.
9. Дайте определение понятию «коэффициент полезного действия насоса» и запишите его выражение.
10. Охарактеризуйте гидравлический, объёмный и механический КПД насоса.
11. Запишите уравнение Д.Бернулли для полной энергии удельной единицы массы жидкости.
12. Записать и объяснить характер изменения величины Е, из условий движения жидкости.
13. Запишите уравнение Д.Бернулли для полного гидродинамического напора в любом сечении трубопровода и объясните значение его членов.
14. Рассмотрите работу насоса, расположенного ниже уровня перекачиваемой жидкости и определите величину напора всасывания для этой установки.
15. Рассмотрите работу насоса, расположенного выше уровня перекачиваемой жидкости и определите величину напора всасывания для этой установки.
ВОДОКОЛЬЦЕВОЙ НАСОС
Водокольцевой насос (простейшая схема рис.29). Насос состоит из цилиндрического корпуса 4 с патрубками 1 и 2 для подвода и отвода перекачиваемой среды (газ, жидкость или паровоздушная смесь). Внутри корпуса эксцентрично смонтирован ротор 3 (лопаточное рабочее колесо).
![]() |
Перед пуском насос заливают водой. При вращении лопасти ротора отбрасывают воду к стенкам корпуса, образуя вращающийся водокольцевой слой (водяное кольцо).
Рис.29. Водокольцевой насос.
Вследствие несжимаемости воды, вращающейся кольцевой слой имеет постоянную толщину и располагается концентрично по отношению к корпусу насоса. Серповидное пространство между внутренней поверхностью водяного кольца и ступицей ротора составляет рабочую камеру насоса. Если ротор вращается по часовой стрелке, то справа поверхность водяного кольца удаляется от ступицы ротора и между каждыми смежными лопастями и боковыми стенками корпуса образуется свободный объём, который через серповидное окно 5 будет заполняться перекачиваемой средой. Слева водяное кольцо приближается к ступице, объём уменьшается, и перекачиваемая среда через серповидное окно 6 выталкивается в нагнетательный патрубок. Роль окон будет меняться при изменении направления вращения ротора. Вверху внутренняя поверхность водяного кольца - касается ступицы рабочего колеса и препятствует перетеканию среды с нагнетательной стороны во всасывающую.
Очень важно, чтобы при работе насоса, не было утечек воды из него и чтобы толщина водяного кольца, оставалась постоянной.
Утечки жидкости из насоса происходят постоянно в результате вихре- и брызгообразования на внутренней поверхности водяного кольца и уноса брызг через нагнетательное отверстие. Кроме того, от постоянного перемешивания и трения жидкость в кольце нагревается и ухудшается работа насоса. Поэтому центробежные насосы оборудуются собственной системой с напорным бачком для постоянной замены части воды в кольце.
Основные характеристики водокольцевых насосов:
Подача= Qн, м /час 0,3-12
Напор = Нн м. вод. ст. до 70 (7,0) (МПа)
Вакуум % = 98-99 %
Частота вращенияnн, об/мин - до 960
Вопросы для повторения и самопроверки:
1. Конструкция поршневого насоса.
2. Работа поршневого насоса.
3. Подача поршневого насоса. Воздушные колпаки.
4. Производительность поршневого насоса.
5. Преимущества и недостатки поршневого насоса
6. Эксплуатация поршневого насоса.
7. Роторные насосы. Типы насосов. Принцип работы.
8. Шестеренные насосы. Схема насоса, работа насоса, основные параметры.
9. Винтовые насосы. Схема насоса, работа насоса, основные параметры.
10. Пластинчатые насосы. Схема насоса, работа насоса, основные параметры.
11. Водокольцевые насосы. Схема насоса, работа насоса, основные параметры.
12. Радиально-поршневые насосы. Схема насоса, работа насоса, основные параметры.
13. Аксиально-поршневые насосы. Схема насоса, работа насоса, основные параметры.
14. Эксплуатация роторных насосов (пуск и работа насоса, неполадки в работе насоса).
ЦЕНТРОБЕЖНЫЕ НАСОСЫ
Характеристики центробежных насосов при их совместной работе.
В практике может возникнуть необходимость увеличения производительности или напора в насосной установке. Если два насоса, имеющие отдельные всасывающие трубопроводы, нагнетают жидкость в общую магистраль, работа их называется параллельной.
Суммарная характеристика двух параллельно работающих насосов (рис.30.а) получается сложением их подач при одинаковых напорах. Удваивая абсциссы кривой 1, получим характеристику 2, которая с характеристикой трубопровода 3 будет пересекаться не в точке А1 а в точке А2. Абсцисса точки А2 пересечения суммарной характеристики 2 с характеристикой 3 трубопровода будет соответствовать общей подаче двух параллельно работающих одинаковых насосов, а ордината развиваемому этими насосами напору Н, причём, совместная их производительность Q`` v = 2 Q` v .
А Б
Рис. 30. Построение характеристик совместно работающих насосов.
Если один насос подаёт жидкость во всасывающий патрубок другого насоса, а последний нагнетает её в напорную магистраль, то такая работа насосов называется последовательной (рис. 30.б). При последовательном соединении центробежных насосов их суммарная характеристика 5 получается сложением ординат характеристик 1 и 2. Координаты точки А пересечения кривой 5 с характеристикой трубопровода 4 будут соответствовать суммарной подаче и развиваемому напору. Точки пересечения характеристики 1 и 2 насосов с характеристикой 4 трубопровода определяют параметры работы каждого из насосов в отдельности. Поэтому в общем случае:
Q v``` ≠ Qv + Qv", Н3 = Н1+Н2.
Вопросы для повторения и самопроверки:
1. Дайте определение понятию «насос» и объясните принцип его действия.
2. Объёмные насосы вытеснения, их виды и принцип действия.
3. Лопастные насосы, их виды и принцип действия.
4. Струйные насосы, их виды и принцип действия.
5. Дайте определение понятию «производительность» насоса.
6. Дайте определение понятию «напор» насоса.
7. Определение «полезная или гидравлическая мощность насоса» и запишите её выражение.
8. Дайте определение понятию «эффективная мощность насоса» и запишите её выражение.
9. Определение «коэффициент полезного действия насоса» и запишите его выражение.
10. Охарактеризуйте гидравлический, объёмный и механический КПД насоса.
11. Запишите уравнение Д.Бернулли для полной энергии удельной единицы массы жидкости.
12. Запишите и объясните характер изменения величины Е, из условий движения жидкости.
13. Запишите уравнение Д.Бернулли для полного гидродинамического напора в любом сечении трубопровода и объясните значение его членов.
14. Рассмотрите работу насоса, расположенного ниже уровня перекачиваемой жидкости и определите величину напора всасывания для этой установки.
15. Рассмотрите работу насоса, расположенного выше уровня перекачиваемой жидкости и определите величину напора всасывания для этой установки.
Глава 2
ВОЗДУШНЫЕ КОМПРЕССОРЫ И СУДОВЫЕ ВЕНТИЛЯТРОЫ
ПОРШНЕВОЙ ВОЗДУШНЫЙ КОМПРЕССОР
Сжатый воздух широко применяется на судах, например, для пуска дизелей или для очистки механизмов при уходе за ними. Воздух под давлением 2,5 МПа и выше обычно получают в многоступенчатом компрессоре.
Двухступенчатый воздушный компрессор:
1— масляный насос; 2 — ручной клапан продувания; 3 — поршень второй ступени; 4 — всасывающий клапан второй ступени; 5 — нагнетательный клапан второй ступени; 6 —всасываю - щий клапан первой ступени; 7 — нагнетательный клапан первой ступени в компрессоре.
Воздух в компрессоре сжимается сначала в первой ступени, охлаждается и затем сжимается до более высокого давления во второй ступени, затем снова охлаждается и сжимается в следующей ступени. Наиболее часто применяется двухступенчатый компрессор; (один из таких компрессоров показан на рисунке.
При ходе всасывания воздух заполняет цилиндр первой ступени через глушитель, фильтр и всасывающий клапан первой ступени. Всасывающий клапан закрывается, когда поршень будет в н. м. т., после чего начинается сжатие воздуха. Когда давление воздуха достигает значения, заданного для первой ступени, начинается нагнетание воздуха через нагнетательный клапан в холодильник первой ступени. Таким же образом происходит всасывание и сжатие в цилиндре второй ступени, в котором благодаря его меньшему объему достигается более высокое давление. После выхода через нагнетательный клапан второй ступени воздух снова охлаждается и подается в баллон сжатого воздуха.
Компрессор имеет жесткий картер, в котором устанавливают три рамовых подшипника коленчатого вала. Блок цилиндров имеет сменные цилиндровые втулки. К движущимся частям компрессора относятся поршни, шатуны и цельный двухколенный коленчатый вал. Сверху на блок цилиндров устанавливается головка цилиндра первой ступени, а на нее — головка цилиндра второй ступени. В обеих головках помещаются всасывающие и нагнетательные клапаны. Приводимый от коленчатого вала цепным приводом масляный зубчатый насос обеспечивает подачу смазки к рамовым подшипникам, а через сверления в коленчатом валу — к обоим шатунным подшипникам. Вода для охлаждения компрессора подается от собственного насоса или от системы охлаждения в машинном отделении. Вода поступает в блок цилиндров, в котором помещаются холодильники обеих ступеней, в головку первой ступени, а затем в головку второй ступени.
Предохранительный клапан на блоке цилиндров служит для предотвращения аварии компрессора в случае, если разорвется трубка холодильника и сжатый воздух начнет поступать в полость охлаждения. Воздушные предохранительные клапаны устанавливают на выходе воздуха из первой и второй ступеней. Клапаны рассчитываются на 10%-ное избыточное давление. На выходе из холодильника второй ступени устанавливается плавкая предохранительная пробка для контроля за температурой подаваемого компрессором воздуха, благодаря чему осуществляется защита воздушных баллонов и трубопроводов от чрезмерно нагретого воздуха. Из-за того что приводные электродвигатели компрессоров работают на переменном токе и имеют постоянную частоту вращения, для уменьшения подачи применяют различные виды устройств, разгружающих цилиндры компрессора. Такое устройство осуществляет удержание всасывающих клапанов компрессора в открытом положении.
На холодильниках устанавливают краны продувания. При их открытии компрессор разгружается и воздуха не подает. При пуске компрессор должен работать без нагрузки. В этом случае пусковой момент будет небольшим, а воздушные каналы будут очищаться от накопившейся влаги, которая может оказывать отрицательное воздействие на смазку, вызывать образование водомасляной эмульсии внутри воздушных трубок, что в свою очередь может привести к воспламенению и взрыву в трубках.
После пуска приводного электродвигателя частота вращения вала компрессора постепенно увеличивается. В это время необходимо следить за тем, чтобы давление смазочного масла поднялось до заданного значения. Прекращается продувка холодильника первой, а затем второй ступени, и компрессор начинает работать. Проверяют краны к манометрам ступеней, чтобы показания манометров были правильными. Если продувка холодильников осуществляется вручную, то краны продувки необходимо периодически приоткрывать для удаления влаги из холодильника.
Во время работы, компрессора периодически контролируется подача охлаждающей; воды и температура воздуха, воды и масла.
При остановке компрессора вначале открывают краны продувки первой и второй ступеней, а затем дают компрессору поработать на холостом ходу в течение 2—3 мин. За это время холодильники очищаются от конденсата. После этого двигатель компрессора останавливают, а краны продувки оставляют открытыми.
Если компрессор останавливают на длительное время, разобщительные клапаны охлаждения компрессора следует закрыть.
В последнее время на судах компрессоры работают обычно в автоматическом режиме. В этом случае требуется лишь немного дополнительного оборудования. Необходимо наличие разгрузочного устройства, которое гарантировало бы пуск компрессора без нагрузки, и включение его под нагрузку лишь после того, как будет достигнута необходимая частота вращения.
ВИНТОВОЙ КОМПРЕССОР.
Конструкция винтового компрессора запатентована в 1934 году. Надёжность в работе, малая металлоёмкость и габаритные размеры предопределили их широкое распространение. Кроме того, использование винтовых компрессоров позволяет экономить электроэнергию до 30 %.
Винтовые компрессоры успешно конкурируют с другими типами объёмных компрессорных машин, практически полностью вытеснив их в передвижных компрессорных станциях, судовых холодильных установках.
Рис. 32. Винты компрессора.
Типовая конструкция компрессора сухого сжатия, работает без подачи масла в рабочую полость. Компрессор имеет два винтовых ротора. Ведущий ротор с выпуклой нарезкой соединён непосредственно или через зубчатую передачу с двигателем. На ведомом роторе нарезка с вогнутыми впадинами. Роторы расположены в разъёмном корпусе, имеющем один или несколько разъёмов. В корпусе выполнены расточки под винты, подшипники и уплотнения, а также камеры всасывания и нагнетания.
Высокие частоты вращения винтовых компрессоров определяют применение в них опорных и упорных подшипников скольжения.
Между подшипниковыми камерами и винтовой частью роторов, в которых сжимается газ, расположены узлы уплотнений, состоящие из набора графитовых и баббитовых колец. В камеры между группами колец подаётся запирающий газ, препятствующий попаданию масла из подшипниковых узлов в сжимаемый газ, а также газа в подшипниковые камеры.
Касание винтов роторов при отсутствии смазки недопустимо, поэтому между ними оставляют минимальный зазор, обеспечивающий безопасную работу компрессора, а синхронная частота вращения ведущего и ведомого роторов обеспечивается наружными синхронизирующими шестернями. Винтовые поверхности роторов и стенок корпуса образуют рабочие камеры. При вращении роторов объём камер увеличивается, когда выступы роторов удаляются от впадин и происходит процесс всасывания. Когда объём камер достигает максимума, процесс всасывания заканчивается и камеры оказываются изолированными стенками корпуса и крышками от всасывающего и нагнетательного патрубков.
При дальнейшем вращении во впадину ведомого ротора начинает внедряться сопряженный выступ ведущего ротора. Внедрение начинается у переднего торца и постепенно распространяется к нагнетательному окну. С некоторого момента времени обе винтовые поверхности объединяются в общую полость, объем которой непрерывно уменьшается благодаря поступательному перемещению линии контакта сопряжённых элементов в направлении к нагнетательному окну. Дальнейшее вращение роторов приводит к вытеснению газа из полости в нагнетательный патрубок. Из-за того, что частота вращения роторов значительна и одновременно существует несколько камер, компрессор создаёт равномерный поток газа.
Отсутствие клапанов и неуравновешенных механических сил обеспечивают винтовым компрессорам высокие рабочие частоты вращения, то есть позволяют получать большую производительность при сравнительно небольших внешних габаритах.
Маслозаполненные компрессоры допускают меньшие скорости вращения, чем компрессоры «сухого сжатия». Масло в рабочую полость винтового компрессора подается с целью уменьшения перетечек через внутренние зазоры, смазки винтового зацепления роторов и охлаждения сжимаемого газа.
Есть несколько типов винтовых компрессоров: с прямым приводом и ременным.
ВОЗДУХОХРАНИТЕЛИ.
Каждый вновь изготовленный баллон подвергают первоначальному освидетельствованию; гидравлическому испытанию на прочность давлением, равным 1,5 рабочего давления - для сварных и цельнотянутых с любым рабочим давлением, рабочему плюс 1,4 МПа - для клепаных с давлением больше 2,8 МПа; воздушному испытанию (после гидравлического) рабочим давлением в течение 4 часов.
После установки на судне, воздухохранители со всеми трубопроводами и арматурой подвергают воздушному испытанию в течение 24 часов.
При этом допускается снижение давления не более 0,5%первоначального в течение 1 часа.
Во время эксплуатации судна, воздушные испытания воздухохранителей проводят ежедневно, внутренние освидетельствования - один раз в четыре года, гидравлические испытания - каждые восемь лет.
Запрещается эксплуатация сосудов в следующий случаях:
- если отсутствует либо не работает предохранительное устройство, не позволяющее увеличить давление выше допустимого;
- при неисправности манометров или отсутствии пломб на них и невозможности определить давление по другим приборам;
- если в основных элементах сосуда будут обнаружены трещины, выпучины, значительные пропуски в арматуре, пропуски в сварных швах, заклепочных и болтовых соединениях;
-
при наличии механических либо коррозионных дефектов (трещин).
Рис. 33. Головка пускового баллона.
От плотности клапанов зависит утечка сжатого воздуха из баллона. Поэтому клапаны следует затягивать усилием руки без использования дополнительного рычага. Большие усилия при закрытии клапана вызывают повреждение его рабочей поверхности и поверхности гнезда.
При расходовании воздуха из баллонной станции, состоящей из нескольких баллонов, и одновременном заполнении одного или нескольких баллонов воздухом от работающего компрессора, целесообразно брать воздух из баллона, который в данный момент не подключен к компрессору. Это позволяет снизить вероятность попадания воды и масла в пусковой
трубопровод.
В процессе пополнения баллонов сжатым воздухом, а также сразу после окончания этой операции, необходимо продувать баллон для удаления воды и масла.
При выполнении работ вблизи баллонов заполненных воздухом, нельзя наносить удары по поверхности баллонов металическими предметами.
Техническое обслуживание баллонов предусматривает контрольные осмотры, испытания и ремонт арматуры, очистку внутренних поверхностей баллонов от загрязнений, освидетельствование и испытание их на прочность, нанесение антикоррозионных покрытий на внутренние и наружные поверхности корпусов баллонов. Особое внимание уделяют предохранительному клапану. Их регулирование производится исходя из технических условий эксплуатации сосудов под давлением.
Для предупреждения взрывов в системе сжатого воздуха необходимо: своевременно продувать холодильники ступеней сжатия компрессора, водо-маслоотделители и воздушные баллоны; использовать для смазки компрессора только масло, которое указано в инструкции по эксплуатации; своевременно очищать трубопроводы от масляных отложений путем пропаривания и применения химических растворов, постоянно вести контроль за температурой воздуха в пусковом трубопроводе.
Вопросы для повторения и самопроверки:
1. Назначение и типы судовых компрессоров, параметры их работы.
2. Поршневые компрессоры. Конструкция и работа, особенности эксплуатации.
3. Винтовые компрессоры. Конструкция и работа, особенности эксплуатации.
4. Воздухохранители, устройство, арматура, эксплуатация.
СУДОВЫЕ ВЕНТИЛЯТОРЫ
(назначение, конструкции, принцип действия и Правила технической эксплуатации).
Вентиляторы применяют на судах для подачи воздуха в топки паровых котлов, вентиляции МКО, трюмов и других грузовых помещений, служебных и жилых помещений.
Вентиляторы бывают:
- центробежные и
- осевые.
Вентиляторы делят на:
- высокого давления 3-15 кПа - Центробежные вентиляторы
- среднего давления 1 - 3 кПа - Центробежные вентиляторы
- низкого давления до 1 кПа - Осевые вентиляторы.
Расход воздуха у вентиляторов от 2 до 180 м 3 мин -1.
Частота вращения от 1000 до 5000 об/мин.
Потребляемая мощность от 0.05 до 135 кВт.
Вследствие малой плотности перемещаемой среды, вентиляторы выполняются с радиальными лопатками и с лопатками загнутыми вперёд.
Последние создают в 2-3 раза более высокий напор, чем вентиляторы с лопатками загнутыми назад, но имеют меньший КПД. Промежуточное положение занимают вентиляторы с радиальными лопатками.
ЦЕНТРОБЕЖНЫЕ ВЕНТИЛЯТОРЫ.
Рис. 34. Центробежный и осевой вентиляторы.
Воздух, проходящий через всасывающий патрубок 3, поступает на лопатки 2 колеса вентилятора (рис. 34.а).
При вращении колеса, вследствие силового воздействия лопаток на воздух, воздух приобретает окружную скорость вращения вокруг оси колеса, относительную скорость вдоль профиля лопатки и абсолютную скорость, полученную как результат геометрического сложения окружной и относительной скоростей.
При движении в межлопаточном пространстве от окружности входных кромок до окружности выходных кромок лопаток колеса, воздуху передаётся энергия двигателя 5, подведённая к колесу вентилятора.
Таким образом, вышедший с колеса поток воздуха поступает в неподвижную спиральную камеру 1, где вследствие снижения скорости будет происходить преобразование динамического напора в статический, чем достигается величина статического напора воздуха при выходе из вентилятора.
ОСЕВЫЕ ВЕНТИЛЯТОРЫ.
Воздух, всасываемый через патрубок поступает к рабочему колесу 1, идёт вдоль его оси, проходит между лопастями колеса и затем поступает в нагнетательный патрубок и выходит наружу (рис. 34.б). Осевые вентиляторы создают незначительный напор, поэтому на судах их применяют для вентиляции трюмов, жилых и служебных помещений.
Эксплуатация вентиляторов.
Подача (расход) воздуха вентилятором Q изменяется прямо пропорционально изменению частоты вращения n, т.е.:
Q2/Q1 = n2/n1
Напор (давление) Н, создаваемый вентилятором, изменяется прямо пропорционально частоте вращения n в квадрате, т.е. :
H2/H1 = n22/n12
Мощность N, потребляемая вентилятором, изменяется прямо пропорционально частоте вращения n в кубе, т.е.:
N2/N1 = n32/n31
Исходя из приведенных соотношений, при эксплуатации вентиляторов следует регулировать их подачу изменением частоты вращения лопастного колеса.
При подготовке вентилятора к пуску необходимо снять крышку со стороны притока воздуха. Вентиляторы с большим расходом воздуха рекомендуется пускать при открытой заслонке.
При подготовке вентилятора к работе после монтажа или ремонта, необходимо проверить отсутствие на лопастях трещин, вмятин, прогиба, ослабления посадки колеса.
Во время работы вентилятора нельзя допускать ударов и толчков по кожуху вентилятора во избежание вмятин и перекосов, которые приводят к задеванию рабочего колеса за кожух и выводу его из строя.
Причинами малой подачи воздуха могут быть: неправильное положение заслонок, засорение и неплотность в воздуховодах, недостаточная частота вращения или неправильное направление вращения рабочего колеса.
При появлении стуков и ударов, увеличении вибрации, вентилятор останавливают. В момент остановки следует прослушивать механизм вентилятора, чтобы убедиться в отсутствии шумов, стуков и задевания.
При аварийной остановке вентилятора следует проверить крепление вентилятора, состояние амортизаторов и муфт, крепление рабочего колеса и его балансировку, отсутствие посторонних предметов внутри вентилятора.
Вопросы для повторения и самопроверки:
1. Назначение и типы судовых вентиляторов, параметры их работы.
2. Центробежные вентиляторы. Конструкция и работа.
3. Осевые вентиляторы. Конструкция и работа.
4. Эксплуатация вентиляторов.
Глава 3
СЕПАРАТОРЫ ТОПЛИВ И МАСЕЛ. ФИЛЬТРЫ.
ЦЕНТРОБЕЖНЫЙ СЕПАРАТОР.
Топливо и смазочные масла перед их использованием в дизеле необходимо обработать. Для этого применяются отстаивание и подогрев с целью удаления воды, грубая и тонкая фильтрация для удаления плотных частиц, а также сепарация.
Центробежный сепаратор (Рис.35) используется для разделения двух жидкостей, например топлива и воды, или для разделения жидкости и твердых (плотных) частиц, которые встречаются в масле. Разделение этих сред ускоряется с помощью центробежного сепаратора и может осуществляться непрерывно. Если сепаратор предназначен для разделения двух жидкостей, его называют пурификатором (очистителем). Если сепаратор устроен (собран) так, что может выделять примеси и небольшое количество воды из топлива или масла, то его называют кларификатором (тонким очистителем-осветлителем).
Удаление примесей и воды из топлива имеет большое значение для обеспечения хорошего сгорания топлива. Благодаря удалению загрязняющих примесей из смазочного масла удается уменьшить изнашивание деталей дизелей и предотвратить возможные неполадки и поломки. Поэтому сепарация масла и топлива совершенно необходима.
![]() |
Центробежный сепаратор состоит из электродвигателя с вертикальным валом. В верхней части сепаратора смонтирован барабан. На корпусе, в котором помещен барабан, расположены различные питательные (входные) и нагнетательные (выпускные) трубопроводы. Барабан может быть цельным и работать периодически. В нем скапливаются отсепарированные примеси, которые необходимо периодически удалять. Процесс пурификации.
В других конструкциях барабан имеет раздельные верхнюю и нижнюю половины. В этом случае отсепарированные примеси можно удалять из работающего сепаратора, т. е. не выключая его. При этом неочищенное (загрязненное) топливо поступает в центральную часть барабана, поднимается вверх по пакету (набору) дисков (тарелок) и выходит из барабана в верхней его части (рис.35).
В результате центробежного разделения двух жидкостей, таких как топливо и вода, образуется цилиндрическая поверхность раздела между ними. Расположение этой поверхности раздела внутри барабана имеет очень большое значение для нормальной эффективной работы сепаратора. Устойчивое требуемое расположение поверхности раздела фаз поддерживается посредством применения регулировочных шайб или гравитационных дисков (тарелок) соответствующего диаметра, устанавливаемых на выпускном канале из сепаратора. Эти кольца и шайбы различного диаметра имеются в наличии для каждого сепаратора, чтобы можно было подобрать шайбу или кольцо соответствующего размера в зависимости от плотности сепарируемого топлива. Чем меньше плотность сепарируемого топлива, тем больше должен быть внутренний диаметр регулирующей шайбы.
Процесс кларификации.
Его применяют для очистки топлива, которое мало содержит или совсем не содержит воду. При этом удаляемые из топлива примеси скапливаются в грязевой камере, расположенной на периферии барабана. Барабан кларификатора имеет только одно выпускное отверстие (рис. 35.б). Гравитационные диски здесь не применяют, так как поверхность раздела жидких фаз не образуется. Поэтому барабан работает с максимальной разделяющей способностью, так как топливо подвергается воздействию максимальной центробежной силы.
Тарелки барабана.
Барабаны пурификаторов и кларификаторов содержат каждый по пакету конических дисков (тарелок). В каждом таком пакете может быть до 150 тарелок, отделенных одна от другой небольшим зазором (просветом). Процесс отделения примесей и воды из топлива происходит между этими тарелками.
Ряды центрированных отверстий, расположенных в каждой тарелке около ее наружной кромки, служат для поступления в межтарельчатые пространства грязного топлива, т. е. топлива, подлежащего обработке. Под действием центробежной силы легкие компоненты (чистое топливо) перемещаются к оси вращения барабана, а вода и примеси (более тяжелые компоненты) отбрасываются к периферии барабана, т. е. к его стенкам. Вода и примеси образуют отстой (шлам), который движется к периферии барабана вдоль нижних сторон (поверхностей) тарелок.
Периодическая работа сепаратора.
Некоторые сепараторы сконструированы так, что имеют непродолжительный период работы. Затем их выключают для очистки отсепарированных примесей (плотных частиц). После очистки тарелок и удаления шлама из барабана сепаратор опять включают. При такой периодической работе используются барабаны двух различных конструкций: длинный узкий и короткий широкий барабаны. Для сепараторов с узким барабаном требуется очистка после непродолжительного периода работы. Для этого барабан необходимо разбирать. Очистка такого узкого барабана, не имеющего пакета тарелок, намного проще, чем барабана с тарелками. Сепаратор с широким барабаном и с тарелками можно чистить на месте, хотя и имеются дополнительные трудности в очистке пакета конических тарелок.
Непрерывная работа сепаратора.
Сепараторы с широкими барабанами современных конструкций могут эффективно работать в течение длительного периода. Это достигается путем выброса (выстреливания) через определенные промежутки времени шлама из барабана. Шлам скапливается по периферии барабана в процессе непрерывкой его сепарации из топлива. Через определенные промежутки времени шлам выбрасывается из барабана наружу, прежде чем он начнет отрицательно влиять на процесс сепарации топлива. В начале процесса выброса шлама (автоматическая очистка барабана) подачу топлива в сепаратор прекращают и топливо, оставшееся в барабане, удаляют впуском промывочной воды. Вода заполняет гидравлическую систему, расположенную в нижней части барабана, и открывает пружинные клапаны. Затем под воздействием воды движется вниз подвижная нижняя часть барабана. В результате этого открываются выпускные окна, расположенные по периферии барабана в его средней части. Шлам выталкивается через эти окна центробежной силой. Затем под воздействием воды поднимается подвижная часть барабана опять вверх (в исходное положение). В результате этого выпускные окна закрываются. Затем в барабан подается вода для восстановления жидкостного уплотнения (водяного затвора), необходимого для процесса сепарации. После этого возобновляют подачу в сепаратор необработанного топлива и процесс сепарации продолжается.
Выброс шлама длится всего несколько секунд и сепаратор при этом работает непрерывно. В существующих конструкциях сепараторов применяются разные способы удаления шлама из барабана, например полное удаление, частичное управляемое удаление и т. д. При частичном управляемом удалении подачу топлива в сепаратор не прекращают и весь шлам выталкивается. При этом процесс сепарации непрерывен. Какой бы метод сепарации не применялся, но сепаратор должен быть устроен так, чтобы процесс удаления шлама осуществлялся или вручную, или посредством автоматического программного регулятора (таймера).
Техническое обслуживание сепаратора. Барабан и пакет тарелок нуждаются в периодической очистке, если сепаратор сконструирован без подвижных поршневых затворов, т. е. с несамоочищающимся барабаном. При разборке барабана должны быть приняты меры предосторожности. Следует пользоваться только специальным инструментом, предназначенным для этой цели.
Нужно учитывать, что у некоторых деталей сепаратора имеются резьбы левого вращения (против часовой стрелки). Барабан является точно сбалансированным устройством, имеющим высокую частоту вращения. Поэтому все его детали должны быть тщательно осмотрены и подогнаны.
Сепарация смазочного масла циркуляционных систем дизелей.
Смазочное масло при циркуляции в дизеле загрязняется частицами изнашивающихся деталей, продуктами сгорания топлива и водой. В данном случае для непрерывного удаления из масла этих примесей применяются центробежные сепараторы, работающие по принципу пурификации.
Пропускание большого количества масла, циркулирующего в. системе, т. е. всего потока масла, будет стоить слишком дорого.
Поэтому применяется байпасная система, при которой загрязнённое масло забирается из нижней части картера сточной масляной цистерны, в отдаленном от всасывающего патрубка месте н возвращается очищенным в месте, расположенном вблизи от всасывающего патрубка. Так как это байпасная (перепускная) система, то следует руководствоваться принципом: меньшая загрязненность масла, содержащегося в циркуляционной системе, будет при работе сепаратора со значительно меньшей производительностью по сравнению с паспортной (максимальной).
По желанию можно принять схему очистки масла с промывкой его водой во время сепарации. Однако некоторые масла содержат водорастворимые присадки, которые будут утеряны, если такое масло промывать водой.
Преимущество промывки масла водой в процессе сепарации заключается в том, что происходит растворение и удаление водорастворимых кислот, улучшается процесс сепарации, так как плотные частицы увлажняются и непрерывно обновляется гидравлический водный затвор в барабане. Промывочная вода должна иметь температуру подогрева немного большую, чем температура масла.
Детергентные масла также пригодны для сепарации.
Их применяют в тронковых дизелях и в некоторых малооборотных двигателях.
Присадки к детергентным маслам обычно растворимые в масле и не могут вымываться водой в процессе сепарации с промывкой.
Вертикальные валы судовых сепараторов.
В практике эксплуатации сепараторов возникает необходимость разборки и ремонта вертикального вала, в частности для замены подшипников, пружин.
Рис. 37. Конструкция вертикального вала сепаратора серии МАРХ207S-00.
Позиции соответствуют следующим деталям:
1-резиновое кольцо (уплотнительное) для верхнего маслоотбрасывателя; 2-болт верхней крышки; 3-крышка подшипника; 4-болт; 5-амортизатор; 6-пружина; 7-гайка пружины; 8-крышка верхнего подшипника; 9-резиновое кольцо крышки; 10-шайба; 11-кольцевая гайка со стопорной шайбой; 12-нижний шарикоподшипник; 13-кольцевая гайка, червяка; 14-червяк; 15-вал барабана; 16-шайба; 17-осевой амортизатор; 18-резиновое кольцо; 19-болт; 20-корпус подшипника; 21-верхний шарикоподшипник; 22-маслоотбрасыватель; 23-корпус пружин; 24-верхний маслоотбрасыватель,
Данный вал отличается от других валов. Отсутствует средняя опора и упрощена конструкция нижней опоры, вместо упорного подшипника установлен сферический подшипник 12, который воспринимает радиальные и осевые нагрузки. Схема детальной компоновки в данном случае не приводится. Она, как правило, даётся в фирменной инструкции по эксплуатации сепаратора.
Одним из важных узлов сепаратора, от которого в большой степени зависит надёжность его работы, является привод. Наибольший интерес представляет конструкция вертикального вала. Имеется ряд отличий в исполнении валов различными фирмами.
Функция вертикального вала заключается в передаче крутящего момента барабану сепаратора с помощью червячно - винтового механизма от горизонтального вала, соединенного с электродвигателем.
Барабан, как правило, имеет относительно большую массу Она всегда имеет остаточный дисбаланс и, следовательно, конструкция опор вертикального вала должна учитывать это обстоятельство.
Рассмотрим конструкцию и компоновку деталей вертикального вала сепаратора серии МАРХ309В-00, которые представлены далее.
Рис 38. Вертикальный вал сепаратора серии МАРХ309В-00 в сборе.
Обозначения на рис. 38 соответствуют следующим деталям:
1-маслоотбрасыватель; 2-кожух верхнего подшипника; 3-заглушка пружины; 4-пружина; 5-упорная втулка червяка; 6-подшипник; 7-червяк; 8-подшипник; 9-упорная шайба; 10-корпус упорного подшипника; 11-сферическая упорная шайба; 12-регулировочная шайба; 13-упорный подшипник; 14-качающийся шарикоподшипник; 15-вал барабана; 16-верхний подшипник; 17-дефлектор; 18-корпус пружин; 19-корпус подшипника.
Цифры в скобках соответствуют позициям тех же деталей на рис. 37.
На рис. 38 видно, что вертикальный вал 15, установлен в 3-х опорах верхней 19, обычно называемой горловой, средней 6, и нижней, заключенной в корпусе 10.
Верхняя (горловая) опора состоит из корпуса 19, в котором находится шарикоподшипник 16 и радиально расположенные амортизаторы. Пружины 4 прижимаются одним концом к наружной обойме подшипника 16, а другим упирается в гайку 3. Корпус пружин 18 с помощью болтов крепится к станине сепаратора.
Наиболее важными элементами верхней опоры являются пружины 4. Совместить идеально центр тяжести барабана с геометрической осью его вращения невозможно (всегда имеется некоторый дисбаланс). При разгоне вращающаяся система сепаратора проходит через критические числа оборотов. При этом биение системы (амплитуда колебаний) значительно возрастает. Пружины 4 демпфируют эти колебания. Упругость пружин устанавливают таким образом, чтобы, с одной стороны, дать системе возможность самобалансировки, а, с другой стороны, обеспечить безаварийное вращение барабана при разгоне и различных кренах судна (исключить возможность задевания вращающихся деталей о неподвижные).
Средняя опора 6 также предназначена для уменьшения вибрации вертикального вала.
Червяк 7 передает вращение от червячного колеса валу барабана 15. Конструктивной особенностью червяка является его свободная посадка на вал 15. Это обеспечивает постоянные зазоры в червячном зацеплении, чем достигается уменьшение износов в процесс эксплуатации.
Узел нижней опоры заключен в корпус 10. Вал нижней пятой опирается на упорный подшипник 13 и через промежуточные (регулировочные) шайбы 12 - на сферическую упорную шайбу 11. Она воспринимает вертикальные осевые нагрузки. Уменьшению этих нагрузок способствует выбранное направление вращения червячного колеса. Оно принимается таким образом, чтобы осевое усилие от передачи крутящего момента было направлено вверх по оси вертикального вала.
Рис. 39 Схема детальной компоновки вертикального вала сепаратора серии МАРХ309В-00
СЕПАРАТОРЫ ФИРМЫ АЛЬФА - ЛАВАЛЬ (серия МАРХ)
1. Компоновка сепараторов
Одним из наиболее распространенных типов сепараторов, устанавливаемых на судах мирового флота, являются сепараторы Альфа - Лаваль. Особенностью сепараторов этой фирмы является увеличенное количество тарелок в барабане без увеличения его габаритов за счет уменьшения межтарелочного зазора на 17 - 22% и применение специальных напорных дисков с профилированными каналами, работающими как центростремительные насосы. Они заменяют откачивающие насосы топлива (масла), воды.
Общий вид сепараторов фирмы Альфа - Лаваль показан на рис. 40 и 41.
Дата добавления: 2015-12-08; просмотров: 1923;