Медь и её сплавы
Цветные металлы и сплавы на их основе.
Медь - один из самых распространенных материалов высокой проводимости. Медь - химический элемент I группы побочной подгруппы периодической системы, d-элемент, порядковый номер 29, атомный вес 63,54. Химический знак - Сu. Она носит латинское название «купрум», которое происходит от наименования острова Кипр, богатого залежами медьсодержащих ископаемых. Русское слово «медь», по мнению некоторых исследователей, происходит от слова «смида» - так древние племена, населявшие европейскую часть территории нашей страны, называли вообще металл.
Массовая доля меди в земной коре составляет всего лишь 0,01 %, это столько же, что и вольфрама, но намного меньше, чем марганца, циркония и ванадия вместе взятых. Однако она не является рассеянным металлом и содержится во многих рудах, где концентрация ее достигает порядка 5 %, а именно сульфидных и оксидных. Медь является полублагородным металлом и встречается помимо руд в самородном состоянии. Свободная медь состоит из двух природных изотопов 63Сu (69,1 %) и 65Сu (30,9 %).
Для получения меди применяют пиро- и реже гидрометаллургические процессы. Пирометаллургический способ извлечения металла основан на частичном окислении сернистых руд до оксидов меди, которые далее восстанавливаются до свободного состояния, реагируя с избытком своего сульфида.
Образующийся при пирометаллургической переработке руды сернистый газ идет на производство серной кислоты, а шлак используется для производства каменных изделий и шлаковаты.
Получаемая описанным способом черновая медь обычно содержит 95,0 – 98,0 % Сu. Для удаления вредных примесей и извлечения ценных элементов ее далее подвергают рафинированию - сначала огневому, затем электролитическому. При огневом рафинировании черновую медь переплавляют в токе воздуха. Железо, цинк, кобальт, частично никель и другие примеси удаляются в шлак, и содержание меди повышается до 99,7 %.
Для производства меди высокой степени чистоты проводится электролитическое рафинирование. При этом рафинируемая медь играет роль анода; в качестве катода используются тонкие медные пластины, электролитом служит раствор медного купороса - CuSO4. При электролизe благородные металлы, селен, теллур и другие ценные спутники меди концентрируются в анодном шламе, откуда их и извлекают специальной переработкой.
Полученные после электролизa катодные пластины меди переплавляют в болванки массой 80 - 90 кг, которые прокатывают и протягивают в изделия требующегося поперечного сечения. При изготовлении проволоки болванки, сначала подвергают горячей прокатке в так называемую катанку диаметром 6,5 - 7,2 мм; далее ее протравливают в слабом растворе серной кислоты, чтобы удалить с ее поверхности окись меди СuО, образовавшуюся при нагреве, и уже потом протягивают без подогрева в проволоку нужных диаметров - до 0,03 - 0,02 мм.
Гидрометаллургические методы извлечения меди основаны на селективном растворении медных минералов обычно в разбавленных водных растворах серной кислоты H2SO4 или аммиака NH3. Из полученных растворов металл вытесняют железом либо выделяют электролизом.
Производство меди приобрело широкое развитие в связи с ростом электрификации и электротехнической промышленности.
Медь – это металл, который кристаллизуется в гранецентрированной кубической решетке с периодом а равным 0,31607 нм и имеет розовато-красный цвет. Это тяжелый и высокоплавкий металл, так плотность меди составляет 8,9 г/см3; а температура плавления равна 1084,5 °С. Важнейшимифизико-механическими свойствами данного металла являются: значительные электро- и теплопроводность, по которым он после серебра занимает второе место. Медь высокопластична и способна подвергаться пластической деформации в холодном и нагретом состояниях (прокатывается в листы, ленты и протягивается в проволоку, толщина которой может быть доведена до тысячных долей миллиметра). Металл обладает достаточно высокой механической прочностью. Медь относительно легко паяется и сваривается (табл. 1.6).
Таблица 1.6 - Основные физико-механические показатели меди
Параметр | Значение |
Валентные электроны | 3d104s1 |
Условный радиус иона Э+, нм | 0,096 |
Условный радиус иона Э2+, нм | 0,080 |
Сродство к электрону, эВ | 1,2 |
Удельная теплоемкость, кал/град | 0,092 |
Теплопроводность, ккал/м·час·град | |
Скрытая теплота плавления, кал/г | 43,3 |
Коэффициент линейного расширения, град-1 | 0,000017 |
Удельное электросопротивление, Ом·м | 1,78∙10-4 |
Энергия ионизации, эВ: Э0 ® Э+ Э+ ® Э2+ Э2+ ® Э3+ | 7,724 20,29 36,9 |
Предел текучести при 20 °С, кГ/мм2 | |
Модуль упругости, кГ/мм2 | |
Модуль сдвига, кГ/мм2 | |
Временное сопротивление, кГ/мм2: деформированной отожженной | 40 - 50 20 - 24 |
Относительное удлинение, %: деформированной отожженной | 4 - 6 40 - 50 |
Предел упругости, кГ/мм2: деформированной отожженной | |
Твердость НВ, кГ/мм2: деформированной отожженной | 90 - 120 35 - 40 |
Она хорошо сопротивляется коррозии (окисляется на воздухе даже в условиях высокой влажности значительно медленнее, чем, например, железо; интенсивно процесс происходит только при повышенных температурах). Чистый металл диамагнитен.
В зависимости от чистоты получаемой меди производят следующие марки металла: М00 (99,99 % Cu), М0 (99,97 % Cu), М1 (99,90 % Cu), М2 (99,70 % Cu) и М3 (99,50 % Cu). Металл марки M1 содержит 99,9% Cu, а в общем количестве примесей (0,1 %) кислорода должно быть не более 0,08 %. Лучшими механическими свойствами обладает медь марки М0, в, которой содержится не более 0,05 % примесей, в том числе не свыше 0,02 % кислорода. В качестве проводникового материала из перечисленных марок меди применяют М1 и М0. Еще более чистым проводником является вакуумная медь марки МВ, выплавляемая в вакуумных индукционных печах.
Постоянными примесями в меди являются висмут, сурьма, мышьяк и другие элементы. Все они понижают ее электропроводность. Температура плавления, плотность, пластичность и другие свойства металла также значительно изменяются от присутствия в нем примесей.
Висмут и свинец образуют с медью легкоплавкие твердые растворы с ограниченной растворимостью (эвтектики), которые при кристаллизации затвердевают последними и располагаются по границам ранее выпавших зерен основного метала. При нагревании до температур, превышающих точки плавления эвтектик (270 и 327 °С соответственно), зерна меди разъединяются жидкой эвтектикой. Такой металл является красноломким и при прокатке в горячем состоянии разрушается. Красноломкость меди может вызываться присутствием в ней тысячных долей процента висмута и сотых долей процента свинца. При повышенном их содержании она становится хрупкой и в холодном состоянии.
Сера и кислород образуют с медью тугоплавкие эвтектики, основу которых составляют хрупкие оксид и сульфид меди(I) – Сu2O и Cu2S, с точками плавления выше температур горячей обработки металла (1065 и 1067 °С). Поэтому присутствие небольших количеств серы и кислорода не сопровождается появлением красноломкости. Однако значительное повышение содержания кислорода приводит к заметному понижению механических, технологических и коррозионных свойств меди; она становится красноломкой и хладноломкой. Медь, содержащая кислород, при отжиге ее в водороде или в атмосфере, содержащей водород, делается хрупкой и растрескивается. Это явление известно под названием «водородной болезни». Растрескивание меди в этом случае происходит в результате образования значительного количества водяных паров при взаимодействии водорода с кислородом меди. Водяные пары при повышенных температурах имеют высокое давление и разрушают медь. Наличие трещин в меди устанавливается путем испытаний на изгиб и кручение, а также микроскопическим методом. В меди, пораженной водородной болезнью, после полировки хорошо видны характерные темные включения пор и трещин. Сера снижает пластичность меди при холодной и горячей обработке давлением и улучшает обрабатываемость резанием. Однако в отличие от кислорода она не влияет на электропроводящие свойства металла.
Железо растворяется в меди в твердом состоянии весьма незначительно. Под влиянием примесей железа резко снижаются электро- и теплопроводность меди, а также ее коррозионная стойкость. Структура меди под влиянием примесей железа измельчается, что повышает ее прочность и уменьшает пластичность. Под влиянием железа медь становится магнитной.
Бериллий является раскислителем по отношению к меди, несколько снижает электропроводность ее, повышает механические свойства и значительно уменьшает окисление при повышенных температурах.
Мышьяк значительно уменьшает электро- и теплопроводность меди. Одновременно с этим мышьяк в значительной мере нейтрализует вредное влияние примесей висмута, кислорода, сурьмы и повышает жаростойкость меди. Поэтому мышьяковистая медь с содержанием 0,3 - 0,5 % As применяется для изготовления деталей специального назначения, используемых для работы в условиях восстановительной атмосферы при повышенных температурах. Мышьяк растворим в меди в твердом состоянии до 7,5 %.
Сурьма очень сильно понижает электро- и теплопроводность меди. Поэтому металл, предназначенный для изготовления проводников тока, должен содержать ее минимальное количество (не выше 0,002 %). Растворимость сурьмы в меди при температуре образования эвтектики (645 °С) составляет 9,5 %. При снижении температуры она резко падает. С этим связано отрицательное влияние сурьмы при прокатке меди. Поэтому содержание сурьмы при этом не должно быть более 0,06 %. В металле, используемом для штамповки, допускается концентрация Sb до 0,2 %.
Фосфор значительно уменьшает электро- и теплопроводность меди, но положительно влияет на ее механические свойства и жидкотекучесть. Он широко применяется в литейном деле в качестве раскислителя меди и оказывает положительное влияние при сварке изделий из нее.
Алюминий повышает коррозионную стойкость меди при различных температурах, значительно понижает ее окисляемость, электро- и теплопроводность, а также оказывает отрицательное влияние при пайке и лужении медных изделий. На механические свойства и обрабатываемость Cu давлением примесь алюминия не оказывает заметного влияния. Растворимость его в меди в твердом состоянии составляет 9,8 %.
В зависимости от способа производства различают твердый и мягкий металл. Твердая (твердотянутая) медь (МТ) благодаря влиянию наклепа имеет высокий предел прочности при растяжении и малое относительное удлинение перед разрывом, а также обладает твердостью и упругостью при изгибе; проволока из нее несколько пружинит. Мягкая (отожженная) медь (ММ) получается после отжига с последующим охлаждением. Она сравнительно пластична, имеет малую твердость и прочность, но весьма большое удлинение при разрыве и удельную проводимость. Последняя служит электротехническим стандартом, по отношению к которому при нормальной температуре выражают удельную электропроводность металлов и сплавов.
По своей химической природе медь - малоактивный металл. Он легче всего взаимодействует с галогенами при обычной температуре, с кислородом и серой реагирует только при нагревании, образуя оксид и сульфид соответственно. С водородом и углеродом медь не взаимодействуют. Сухой воздух практически не вызывают окислительного разрушения металла. Незначительное влияние на химическую стойкость меди оказывают ряд органических кислот, спирты и фенольные смолы.
Поскольку медь находится в ряду напряжений после водорода, кислоты окисляют ее лишь за счет аниона: она растворяется только в азотной НNО3 (любой концентрации) и концентрированной H2SO4, но не реагирует с хлороводородной (соляной) и разбавленной серной кислотами. Также она не взаимодействует как с чистой пресной, так и с морской водой и растворами щелочей.
Металл плохо сопротивляется действию аммиака, аммиачных солей и щелочных цианистых соединений. Коррозию меди вызывают также хлористый аммоний и окислительные минеральные кислоты. На воздухе во влажной атмосфере, содержащей диоксид углерода, она покрывается плотной серо-зеленой пленкой основного карбоната - Cu(OH)2·CuCO3.
Более 50 % добываемой меди применяется в электротехнической промышленности. Благодаря высокой теплопроводности и коррозионной стойкости она широко используется в теплообменниках, холодильниках, вакуумных аппаратах и является одним из важнейших проводниковых материалов. Из нее изготовляют монтажные и обмоточные провода, токопроводящие детали, приборы и аппараты. Большое применение она находит также в электровакуумной технике.
Твердую медь употребляют там, где надо обеспечить особо высокую механическую прочность, твердость и сопротивляемость истиранию: для контактных проводов, шин распределительных устройств, коллекторных пластин электрических машин и пр. Мягкую медь в виде проволок круглого и прямоугольного сечения применяют главным образом в качестве токопроводящих жил кабелей и обмоточных проводов, где важна гибкость и пластичность (не должна пружинить при изгибе), а не прочность. Она также широко применяется в производстве фольги. Из специальных электровакуумных сортов меди изготавливают аноды мощных генераторных ламп, детали СВЧ устройств, магнетронов, клистронов, некоторых типов волноводов и др. Чистую медь широко применяют для пайки изделий из углеродистых, конструкционных и быстрорежущих сталей и никельсодержащих сплавов.
Медь является сравнительно дорогим и дефицитным материалом. Поэтому она должна расходоваться весьма экономно. На электротехнических предприятиях ее отходы необходимо тщательнособирать; важно не смешивать их с другими металлами, а также с менее чистой (не электротехнической) медью, чтобы можно было подвергнуть их переплавке и вновь использовать в качестве электротехнической меди.
Представляет интерес еще одна сторона деятельности меди, но уже не как металла. Она принадлежит к числу так называемых биоэлементов, необходимых для нормального развития растений и животных. В ее «обязанности» входит ускорение химических процессов, протекающих внутри клеток.
При отсутствии или недостатке меди в растительных тканях уменьшается содержание хлорофилла, листья желтеют, растение перестает плодоносить и может погибнуть. Не случайно, медный купорос широко применяют в сельском хозяйстве.
Из представителей животного мира наибольшие количества меди содержат осьминоги, каракатицы, устрицы и некоторые другие моллюски. В крови ракообразных и головоногих медь, входящая в состав их дыхательного пигмента - гемоцианина (0,33 - 0,38 %), - играет ту же роль, что железо в крови других животных и человека. Соединяясь с кислородом воздуха, гемоцианин синеет (потому-то у улиток и «голубая кровь»), а отдавая кислород тканям, - обесцвечивается. У животных, стоящих на более высокой ступени развития, и у человека медь содержится главным образом в печени. Ежедневная потребность человеческого организма – примерно 0,005 грамма этого элемента. При недостаточном поступлении меди с пищей у человека развивается малокровие, появляется слабость.
Должно быть, поэтому многие народы приписывают меди целебные свойства. Непальцы, например, считают медь священным металлом, который способствует сосредоточению мыслей, улучшает пищеварение и лечит желудочно-кишечные заболевания (больным дают пить воду из стакана, в котором лежат несколько медных монет).
Вследствие недостаточной прочности технически чистую медь в качестве конструкционного материала применяют крайне редко. Примерно 30 - 40 % всего производимого металла употребляется в виде сплавов.
В ряде случаев, когда от проводниковых материалов требуется не только высокая проводимость, но и повышенные механическая прочность, коррозионная стойкость и сопротивляемость истиранию, употребляют широко известные сплавы меди с небольшой концентрацией легирующих добавок.
Обширное распространение в промышленности нашли сплавы меди с другими элементами - бронзы и латуни.
Бронзами называют сплавы меди с различными элементами, кроме цинка. Первыми и самыми древнейшими из всех полученных и применяемых человеком сплавов (3 – 1 век до н. э.) были оловянные бронзы (массовая доля Sn 4,0 – 30,0 %). Слово «бронза» произошло от названия небольшого итальянского городка Бриндизи, расположенного на берегу Адриатического моря. Этот торговый порт славился своими бронзовыми изделиями. Латинское слово «Эс Брундуси», что означает медь из Бриндизи, легло в основу названия сплава.
Бронзовый век, пришедший на смену медному, - это целая эпоха в развитии мировой культуры на нашей планете. Однако долгое время из бронзы изготавливали лишь предметы роскоши и украшения. Далее люди научились отливать статуи из бронзы. И лишь немного позже сплав вытесняет медь как основной металл для изготовления орудий труда и занимает данные позиции до открытия железа.
В процессе кристаллизации меднооловянистых сплавов в твердом состоянии возможно образование следующих фаз: a-твердый раствор олова в меди; Sn - почти чистое олово (рис. 1.73). Растворимость меди в олове, вероятно, меньше 0,01 % и на диаграмме не указана; b-твердый раствор на базе b-электронного соединения Cu5Sn. Пунктирная линия показывает процесс его упорядочения; d-электронное соединение Cu31Sn8; g-твердый раствор на основе химического соединения меди и олова. Кристаллическая решетка его подобна d; e-электронное соединение Cu3Sn; h - химическое соединение Cu6Sn5.
Структура литых меднооловянных сплавов значительно отклоняется от равновесного состояния, поэтому уже в системе, содержащей 5 % Sn и более, в литом виде обнаруживается d-фаза, представляющая эвтектоидную составляющую (эвтектоид образуется при 520 °С и имеет концентрацию 26,8 % Sn). Строение отожженной бронзы с количеством олова до 14 % должно состоять из однородного a-твердого раствора (рис. 1.74, а). В литом же виде структура бронзы, содержащей до 5,0 – 6,0 % олова, представляет неоднородный твердый раствор a, имеющий дендритное строение (рис. 1.74, б). При концентрации Sn более 6,0 % наряду с неоднородным раствором a внутри его светлыx участков, богатых оловом, располагается эвтектоид a + d (рис. 1.75). Сплавы медь-олово обладают хорошими механическими, антифрикционными и технологическими свойствами.
Рис. 1.73 - Диаграмма состояния медь-олово
По твердости оловянные бронзы намного превосходят отдельно взятые металлы. При содержании олова более 22,0 % сплавы очень хрупки из-за наличия в структуре большого количество b-фазы и не имеют практического применения (рис. 2.4). Сплав более легкоплавок, чем сама медь. Оловянные бронзы имеют большой интервал температур кристаллизации и поэтому склонны к ликвации и образованию рассеянной пористости. При резко выраженной обратной ликвации на поверхности отливок появляются хрупкие выделения в виде белых пятен (оловянного пота), отрицательно влияющих на качество отливок.
|
|
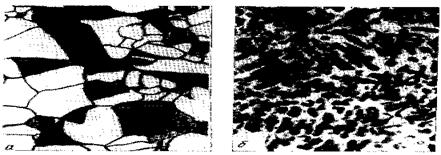
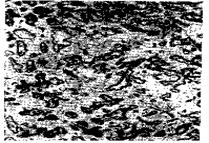
Рис. 1.74. Структура литой бронзы с 6,0 % Sn: а - отожженная; б - до отжига | Рис. 1.75. Структура литой бронзы с 10% Sn |
Оловянные бронзы имеют очень малую усадку и не дают сосредоточенной усадочной раковины. Они также мало чувствительны к перегреву, отлично воспринимают пайку и сварку, не дают искры при ударах, немагнитны и морозостойки. Сплавы медь-олово обладают высокой коррозионной стойкостью в атмосферных условиях, в сухом и влажном водяном паре, в пресной и морской воде, в сухих газах и кислороде при нормальной температуре. Однако все оловянные бронзы быстро разрушаются под воздействием рудничных вод, содержащих соли-окислители, и в растворах аммиака. Скорость коррозии сплавов в газах возрастает при высоких температурах в присутствии хлора, брома, йода, а также во влажном сернистом газе.
Значительное влияние на свойства оловянных бронз оказывают примеси. Цинк улучшает технологические свойства сплава и удешевляет его. Фосфор повышает литейные и механические характеристики: твердость, прочность, износостойкость, упругость и антифрикционость. В сплавах, обрабатываемых давлением, содержание фосфора допускается не более 0,5 %. При повышении концентрации фосфора оловянные бронзы не поддаются горячей обработке давлением. Свинец улучшает антифрикционные свойства сплавов медь-олово и их обрабатываемость резанием. Железо при его содержании до 0,03 % является полезной примесью, так как способствует образованию мелкозернистой структуры, повышает механические свойства и задерживает рекристаллизацию. Более высокая концентрация железа уже отрицательно влияет на некоторые характеристики оловянных бронз: резко снижаются их коррозионные и технологические свойства. Никель увеличивает механические свойства, коррозионную стойкость и уменьшает ликвацию. Он также повышает их жаропрочность и практически не снижает тепло- и электропроводность. Такими же эффектами обладают еще хром, магний и цирконий. Магний наряду с алюминием и кадмием усиливает жаростойкость (окалиностойкость) оловянных бронз. Вредными примесями в данных сплавах являются алюминий, кремний, магний, висмут, мышьяк и сера.
Сплавы меди с другими элементами, кроме олова, называют специальными (безоловянными) бронзами. По литейным свойствам они хуже оловянных бронз. Однако по другим качествам специальные сплавы обладают более высокими показателями. Кристаллизация алюминиевых бронз осуществляется в узком интервале температур (рис. 1.76).
Сплавы, содержащие 10 % алюминия и более, имеют в структуре эвтектоид (a + g), полученный в результате разложения b-фазы и медленного охлаждения с температурой выше критической (рис. 1.77). При быстром остывании она переохлаждается, и распад ее сопровождается образованием более мелкодисперсных частиц (a + g). Скорость распада твердого раствора b зависит от температуры. Доэвтектоидный сплав состоит из кристаллов a (светлые) и эвтектоида a + g (темные). Мартенситная структура алюминиевой бронзы (рис. 1.77, б) получена в результате закалки в воде с 900 °С.
Рис. 1.76. - Диаграмма состояния Сu - Аl
|
|

Рис. 1.77 - Микроструктура алюминиевой бронзы с 10,5 % Al: а – после медленного охлаждения с 900 °С (a + эвтектоид); б - после быстрого охлаждения (мартенсит)
Алюминиевые бронзы (до 12 % Al) превосходят оловянные по механическим свойствам и приближаются по этим параметрам к сталям. Они обладают высокой жидкотекучестью, не склонны к ликвации, морозостойки, немагнитны и не дают искры при ударах. В наклепанном состоянии прочность сплавов значительно возрастает. В широком диапазоне изменяются их механические свойства в результате термической обработки. Сходство термической обработки алюминиевых бронз с ТО стали дополняется тем, что при охлаждении с критической скоростью b-фаза трансформируется в игольчатую структуру. Превращение происходит по мартенситному типу. К их недостаткам следует отнести то, что они трудно поддаются пайке мягкими и твердыми припоями, имеют повышенную объемную усадку и недостаточно устойчивы к воздействию перегретого пара. Они наиболее коррозионно-стойки в атмосферных условиях, морской воде, углекислых растворах, а также во многих органических кислотах (лимонной, уксусной и молочной).
Наряду с простыми применяют сложные алюминиевые бронзы. Для повышения механических свойств и коррозионной стойкости в алюминиевые бронзы чаще всего добавляют железо, никель, марганец. Железо способствует измельчению структуры и повышает механические свойства сплава. Никель значительно увеличивает предел текучести, прочность, твердость, коррозионно- и жаростойкость алюминиевых бронз. Алюминиевоникелевые сплавы еще легче по отношению к чистой меди: их плотность составляет 7,5 - 7,7 г/см3. Однако они имеют более низкие тепло- и электропроводность в сравнении с медью. Такие сплавы удовлетворительно переносят обработку давлением и применяются для деталей ответственного назначения как сплавы высокой прочности. Марганец также повышает коррозионно- и жаростойкость алюминиевых бронз. Примеси висмута и серы ухудшают механические и технологические свойства. Цинк тоже оказывает отрицательное влияние на технологические и антифрикционные свойства сплавов. Все три элемента являются вредными примесями.
Особый интерес представляют бериллиевые бронзы. Сплав с 2,0 % Be, как видно из диаграммы (рис. 1.78), дисперсионно твердеющий. Растворимость бериллия в меди при комнатной температуре не превышает 0,2 %, но закалка с 800 °С фиксирует пересыщенный раствор a. Если закаленный сплав подвергнуть затем искусственному старению при 300 - 350 °С, то твердость повысится до НВ 350 - 400. Бериллиевые бронзы (до 2,85 % Be) имеют значительные пределы прочности, упругости, текучести и усталости, а также высокую электро- и теплопроводность, твердость, износоустойчивость, сопротивление ползучести, коррозионную стойкость и большое сопротивление коррозионной усталости. Они немагнитны, морозостойки и обладают высокой усталостной прочностью. Отличительной их особенностью является способность подвергаться термообработке. В связи с этим, они получили широкое применение в технике для изготовления пружин, мембран, пружинящих контактов и т. д. Кроме того, бериллиевую бронзу можно применять как безыскровый инструмент. При ударе бериллиевой бронзы о металл или камень не получаются искры, как у стали. Поэтому инструменты из этих сплавов применяются при взрывоопасных горных работах. Ухудшают качество сплавов примеси железа, алюминия, кремния, магния и фосфора. Весьма вредными примесями для них являются свинец, висмут и сурьма.
Рис. 1.78 - Диаграмма состояния системы медь-бериллий
Ограниченное применение бериллиевых бронз в промышленности частично объясняется высокой их стоимостью. Добавки таких металлов, как никеля, марганца и кобальта, не только позволяет несколько уменьшить куонцентрацию в них бериллия (снижение стоимости), но и улучшить качество сплава. Так введение кобальта (до 0,65 %) повышает их механические свойства, износо- и коррозионную стойкость. Никель (до 1,2 %) способствует увеличению предела прочности при растяжении и твердости образцов из таких сплавов. Добавление совместно с никелем магния делает сплав самым жаропрочным из всех электропроводных бериллиевых бронз.
Высококачественным антифрикционным материалом, широко применяемым в машиностроении, является свинцовистая бронза, содержащая 30 % Pb (Бр.С30). Структура такого сплава состоит из отдельных зерен меди и свинца (рис. 1.79). Равномерное вкрапление свинца в медь обеспечивает высокие антифрикционные свойства сплава. Однако получить надлежащую структуру свинцовистой бронзы трудно, так как большой температурный интервал кристаллизации (954 – 326 °С) (см. диаграмму состояния Сu - Pb, рис. 1.80) при различии в плотности меди и свинца благоприятствует усиленной ликвации по плотности. Это явление можно предупредить ускорением охлаждения расплава в процессе кристаллизации.
Рис. 1.79 - Микроструктура свинцовистой бронзы БрС30
Рис. 1.80 - Диаграмма состояния системы медь-свинец
Свинцовые бронзы применяются для изготовления высоконагруженных подшипников с большим удельным давлением.
Кремнистые бронзы (до 3,5 % Si) имеют высокую пластичность и хорошие литейные свойства. Для повышения механических характеристик и коррозионной стойкости в них обычно добавляют марганец и никель. Одновременно при этом улучшаются и антифрикционные свойства сплавов. Они также отлично свариваются и паяются, немагнитны, в значительной мере сохраняют свои свойства при низких температурах, не дают искры при ударах, хорошо обрабатываются давлением как в горячем, так и в холодном состояниях, обладают хорошей коррозионной стойкостью в пресной и морской воде, в атмосфере таких сухих газов как: сернистого, хлора, брома, фтора, фтористого и хлористого водорода, аммиака. В присутствии влаги коррозионная стойкость кремнистых бронз снижается. Они удовлетворительно сопротивляются воздействию разбавленных растворов щелочей в условиях низких температур.Сплавы коррозируют в кислых рудничных водах, содержащих сернокислую окисную соль железа, а также в растворах солей хромовых кислот и хлорного железа. При этом в бронзах, обрабатываемых давлением, содержание железа не должно быть выше 0,2 - 0,3 %, так как при более высоких значениях концентраций оно заметно снижает коррозионную стойкость сплава. Под влиянием свинца кремнистые бронзы легко разрушаются при обработке давлением в горячем состоянии, поэтому содержание данного металла в сплавах, предназначенных для горячей обработки давлением, не должно быть более 0,01 %. Примеси висмута, мышьяка, сурьмы, серы, фосфора являются очень вредными и их концентрации не следует увеличивать выше 0,002 %.
Состав бронзы, способы ее получения и изготовления готовых изделий выбираются в зависимости от назначения, условий эксплуатации и предъявляемых к ним требований.
По способу производства все бронзы делят на две группы: литейные и деформируемые.
Литейные сплавы предназначены для получения деталей путем литья в песчаные формы, в кокиль, центробежным способом и по выплавляемым моделям. Они широко применяются для изготовления различной арматуры, антифрикционных деталей, для художественного литья и других целей. Это в основном оловянные бронзы.
Деформируемые сплавы - это материал для производства поковок, фасонных профилей, прутков различного сечения, полос, лент, листов, проволоки и труб. Их изготавливают путем ковки, прессования, горячей и холодной прокаткой. Из оловянистых бронз в качестве деформируемых материалов применяются сплавы, содержащие до 8,0 % Sn. Легко обрабатываются давлением алюминиевые бронзы с концентрацией алюминия до 12,0 %: алюминиевожелезные, алюминиевомарганцевые, алюминиевожелезоникелевые и др. Хорошо поддаются обработке давлением кремнемарганцовистые (Бр.КМц3-1) и бериллиевые бронзы. Бериллиевые сплавы в закаленном состоянии обладают высокой пластичностью, а после отпуска приобретают повышенную упругость, прочность и твердость.
В зависимости от назначения, физических, механических и других свойств деформируемую бронзу разделяют на жаропрочную, износостойкую, конструкционную, приборную, пружинную и т. д.
К жаропрочным сплавам относится целый ряд специальных: хромистые, хромоциркониевые, хромо-кадмиевые, хромоцинковые и др., а также кремнистоникелевые марки Бр.КН1 - 3 и алюминиевые – Бр.АЖН10 – 4 - 4. Они обладают хорошей прочностью при высоких температурах.
Износостойкая бронза применяется для изготовления деталей трения. В эту группу сплавов входят оловянистые, алюминиевые, кремнистые и бериллиевые бронзы. Прутки из сплавов медь-олово марки Бр.ОФ6,5 - 0,15 применяются для подшипников, изготовляемых в виде втулок, работающих в условиях средней трудности по удельным давлениям и скоростям скольжения или при повышенных нагрузках и малых скоростях скольжения. По сравнению с литейными оловянистые деформируемые бронзы имеют более низкую износостойкость.
Медно-алюминиевые сплавы уступают оловянистым по сопротивлению заеданию и износостойкости. Однакоони обладают большей прочностью и твердостью. В условиях средней трудности и при хорошей смазке алюминиевые бронзы работают надежно. Из них изготовляют червячные передачи, направляющие втулки, неответственные подшипники в виде втулок и другие детали. Из алюминиевой бронзы также делают медные монеты.
Бериллиевые сплавы успешно применяется в условиях трения-качения, где недопустимы остаточные деформации материала (в шаровых сочленениях приборов и агрегатов и др.).
Бронза кремнистомарганцовистая в качестве коррозионно- и износостойкого материала используется для изготовления сеток и решеток, работающих в сточных водах, испарителях, дымовых фильтрах и т. д.
Конструкционные сплавы употребляются для производства деталей, которые в процессе эксплуатации испытывают силовую нагрузку и от которых одновременно требуются коррозионная стойкость и специальные физические свойства. В данную группу входят алюминиевые, алюминиевожелезные и кремнемарганцовистые бронзы.
Полуфабрикаты из алюминиевых бронз, легированных железом, никелем и марганцем, нашли широкое применение для нагруженных деталей в различных конструкциях химических аппаратов, в судостроении, в авиации и общем машиностроении. Этому способствует сочетание в указанных сплавах высоких прочностных характеристик при наиболее значительных пластических свойствах иударной вязкости с повышенной коррозионной стойкостью.
Бронзы кремнемарганцовистая (Бр.КМц3-1) и кремнистоникелевая (Бр.КН1-3) при хорошей коррозионной стойкости и достаточно высокой прочности обладают значительной пластичностью. Из первых в отожженном состоянии изготовляют очень тонкие ленты (толщиной до 0,05мм). При холодной прокатке этот сплав нагартовывается и приобретает высокие упругие свойства. Кремнистые бронзы, например марка Бр.КЦ4-4 (4 % кремния и 4 % цинка), назначаются как заменители меднооловянистых сплавов (БрОЦС5–5-5). Уступая последней по величине усадки, кремнистые сплавы превосходят их по коррозионной стойкости, механическим свойствам и плотности отливки.
Алюминиевожелезные (типа Бр.АЖН10–4-4) и кремнистоникелевые (Бр.КН1-3) бронзы, обладающие высокой жаропрочностью, применяются для изготовления деталей, работающих при повышенных температурах. Из приборной бронзы делают детали, приборы и аппараты. В зависимости от условий их эксплуатации в качестве материалов могут применяться различные высокопрочные конструкционные и пружинные сплавы.
Пружинная бронза идет на производство пружин и пружинных деталей различного типа и назначения. В данном качестве могут выступать оловянистые Бр.ОФ6,5-0,15, Бр.ОФ4-0,25. Бр.ОЦ4-3, алюминиевые А7 и бериллиевые бронзы марок Бр.Б2, Бр.БНТ1,9 и Бр.БНТ1,7. Оловянистые и алюминиевые сплавы обладают повышенной упругостью и прочностью в нагартованном состоянии. Бериллиевые бронзы, мягкие и пластичные в закаленном виде, получают высокую упругость и твердость после отпуска.
Мягкие сплавы легко штампуются и гнутся. Мягкость бронз достигается обработкой давлением и отжигом при высокой температуре для полного снятия внутренних напряжений и восстановления структуры. Их применяют тогда, когда по условиям технологии изготовления детали подвергаются дополнительной деформации (штамповке, гибке и так далее).
Полутвердая бронза используется для изготовления мембран, флянцев, тросов и других деталей крепления, от которых требуется повышенная прочность. Сплавы этой группы при повышенной прочности и твердости сохраняют достаточную пластичность для обработки штамповкой. Для получения необходимых свойств их подвергают обработке давлением со средними степенями деформации 10,0 – 30,0 %.
Твердая бронза обрабатывается давлением со степенями деформации 30,0 – 50,0 %. Она обладает повышенной прочностью, твердостью и упругостью, низкой пластичностью и применяется для изготовления пружин, контактов, втулок и других деталей.
Особо твердые сплавы имеют высокие пределы упругости, прочности и твердости и пониженную пластичность. Требуемые свойства они приобретают после обработки давлением с высокой степенью деформации (более 50,0 %).
Бронзы широко используются для изготовления троллейных проводов, коллекторных пластин, контактных ножей, скользящих контактов, токоведущих пружин, упругих контактов и т. п. Наибольшее употребление приходится на кадмиевую, бериллиевую и фосфористую бронзы. Кадмиевый сплав (0,9 % кадмия; остальное медь) применяют для контактных проводов и коллекторных пластин особо ответственного назначения, а также сварочных электродов при контактных методах сварки. Бериллиевую бронзу применяют в производстве ответственных токоведущих пружин для электрических приборов, щеткодержателей, токоштепсельных и скользящих контактов. Фосфористая бронза (6,5 % олова; 0,15 % фосфора; остальное медь) хотя и имеет низкую электропроводность, но находит использование при изготовлении различных малоответственных токопроводящих пружин.
Латунями называют сплавы, в которых основными компонентами являются медь и цинк. Латунь, также как и оловянные бронзы, является древним сплавом в истории человечества. Однако египетские жрецы были, пожалуй, единственными кому был известен этот сплав. В рукописях, найденных при раскопках одной из гробниц в Фивах, содержались секреты «получения» золота из меди. Оказывается, стоило лишь добавить к меди цинк, как она превращалась в «золото» (латунь действительно напоминает по цвету золото). Правда, у такого металла был существенный недостаток: в атмосфере воздуха на его поверхности появлялись зеленоватые «язвы» и «сыпь», которые представляли продукты окисления меди.
Диаграмма состояния латуней сложная, на первый взгляд, фактически составлена из пяти простых перитектических диаграмм (рис. 1.81).
Рис. 1.81 - Диаграмма состояния Cu - Zn
У сплавов меди и цинка в твердом состоянии возможно образование шести фаз:
- a-твердый раствор цинка в меди: растворимость цинка в меди при комнатной температуре равна 39,0 %, она не изменяется практически до 454 °С и убывает до 32,0 % при 902 °С;
- b-твердый раствор на базе соединения CuZn с электронным типом связи число электронов/число атомов = 3/2 имеет простую кубическую объемноцентрированную решетку. Упорядоченное расположение атомов сохраняется лишь не выше 454 – 468 °С. При более высокой температуре атомы меди и цинка в кристаллической решетке располагаются статистически;
- g-твердый раствор на базе соединения Cu5Zn8 электронного типа 21/13 имеет сложную кубическую решетку. Температура упорядочения этой фазы равна 270 °С;
- e-твердый раствор на базе соединения CuZn3 электронного типа 7/4 гексагональной плотноупакованной решеткой;
- d-твердый раствор; природа химического соединения, лежащего в основе этого твердого раствора, не установлена;
- h-твердый раствор меди в цинке.
При комнатной температуре латуни либо состоят из одних a-кристаллов, либо являются их смесью с b (рис. 1.82, а и б).
Рис. 1.82 - Микроструктуры медноцинковых сплавов: а - a-; б - a + b-латунь
Механические свойства сплавов Сu - Zn сильно зависят от концентрации цинка. Цинк повышает прочность и пластичность сплава. Максимальной пластичностью обладает сплав с 32,0 % Zn, а наибольшей прочностью – сплав с концентрацией цинка 45 %. Переход через границу однофазной области (39,0 % Zn) резко снижает пластичность; b-латунь обладает максимальной прочностью (sв = 42 кгс/мм2) при относительно низкой пластичности (d = 7,0 %); g структура является весьма хрупкой.
Латуни обладают достаточно высокими механическими и технологическими свойствами и коррозионной стойкостью. Механическая прочность латуней невысока. Для a-структур характерны следующие значения механических свойств: sв = 30 кгс/мм2, d = 40,0 %, a + b-сплавы имеют несколько большую прочность (sв = 35 кгс/мм2), но меньшую пластичность (d = 20,0 %). Латуни, структура которых состоит только из a-pacтвора, хорошо обрабатываются давлением в горячем и холодном состоянии. Сплавы, имеющие двухфазное строение a + b, имеют повышенную твердость, хорошо обрабатываются в горячем состоянии, но в холодном - пластичность их очень мала.
В силу отмеченных обстоятельств не только g- и g + b-, но и b-латуни не имеют практического применения.
Температуры начала и конца кристаллизации медноцинковых сплавов лежат близко друг от друга. Этим объясняется особенность их литейных свойств - малая склонность к ликвации, хорошая жидкотекучесть, способность к образованию концентрированной усадочной раковины. Обработка латуней давлением имеет ряд особенностей.
b-Твердый раствор при температуре выше 500 °С обладает большей пластичностью и меньшей прочностью, чем a-сплавы, в то время как при комнатной температуре наоборот. В связи с этим для прокатки в горячем состоянии наиболее пригодны латуни, структура которых состоит из b- или a + b-раствора.
В холодном состоянии латуни получают значительный наклеп и для снятия напряжений их подвергают отжигу. Свойства сплавов и величина зерна находятся в зависимости от температуры и продолжительности процесса, а также от степени предшествующей деформации. Для получения мелкого зерна в a-латунях требуется температура в пределах 350 - 450 °С. В интервале температур 200 - 600 °С у сплавов появляется хрупкость, связанная с образованием примесями свинца, сурьмы и висмута хрупких межкристаллитных прослоек. С повышением температуры эти прослойки растворяются, и пластичность латуней резко возрастает.
Атмосферные условия, сухой пар, пресная и морская вода, сухие газы, уксусная кислота в спокойном состоянии, сухой четыреххлористый углерод, фторированные органические соединения, хлористый метил и бромозамещенные соединения при отсутствии влаги не вызывают заметной коррозии сплавов. Они сильно корродируют при действии рудничных вод, растворов йодистых солей, азотной, соляной, фосфорной и жирных кислот, серного ангидрида, сероводорода, растворов едких щелочей и аммиака. Их скорость коррозии резко возрастает при повышении температуры в морской и пресной воде и других перечисленных средах, а также в газах с увеличением их влажности.
Большой ущерб промышленности наносится обесцинкованием и коррозионным растрескиванием латуней, которое происходит при одновременном воздействии коррозионной среды и растягивающих напряжений, Склонность сплавов к коррозионному растрескиванию возрастает с повышением содержания цинка и с увеличением до известного предела растягивающих напряжений. Мало чувствительны к нему латуни, содержащие менее 7,0 % Zn. В сплавах с высоким содержанием цинка оно наблюдается относительно редко, если только внутренние напряжения менее 6 кГ/мм2.
Коррозионное растрескивание нагартованной латуни может наблюдаться и при лежании во влажной атмосфере. Этот вид коррозии в сильной степени зависит от влажности атмосферы и проявляется во все времена года не одинаково интенсивно, поэтому ее иногда называют «сезонным растрескиванием».
Медноцинковые сплавы, содержащие кроме меди и цинка, добавки алюминия, железа, марганца, свинца, никеля и других элементов, называют специальными латунями. Они обладают повышенной коррозионной стойкостью, лучшими технологическими и механическими свойствами, а также особыми специальными свойствами. В зависимости от основного легирующего компонента они обычно носят и соответствующие названия: алюминиевая, кремнистая, марганцовистая, никелевая, свинцовистая и т. д.
Алюминиевые латуни находят применение в качестве коррозионно- и жаростойкого материала. Алюминий резко повышает прочность, твердость и коррозионную стойкость сплава в отношении атмосферной коррозии, но понижает его пластичность. Однако такие сплавы менее устойчивы к морской воде. Кроме того, они сравнительно сильно подвержены коррозионному растрескиванию. Поэтому их не рекомендуют для длительного хранения. Также введение алюминия ухудшает способность латуней к пайке и лужению. Алюминиевые латуни употребляются в качестве материала для конденсаторных трубок, шестерней, различных труб, втулок, всевозможных деталей в авиационной и других отраслях промышленности. Наибольший практический интерес представляют сплавы, содержащие до 4,0 % А1, которые хорошо обрабатываются давлением.
Кремнистые латуни обладают более высокой коррозионной стойкостью в атмосферных условиях и морской воде, чем простые сплавы данного типа. Под влиянием кремния значительно повышаются их механические и литейные свойства, а также улучшается технологический процесс сварки и пайки. В латунях с повышенным содержанием цинка кремний значительно увеличивает твердость и уменьшает пластичность. Примеси алюминия, железа, сурьмы, мышьяка и фосфора в кремнистых сплавах являются вредными, так как ухудшают антифрикционные, коррозионные, литейные и другие их свойства. Из них изготавливают поковки и штамповки, литую арматуру, шестерни и детали морских судов, литые подшипники и втулки.
Марганцовистые латуни характеризуются более высокой прочностью, твердостью и коррозионной стойкостью по сравнению с простыми медноцинковыми сплавами. Содержание марганца до 4,0 % значительно повышает временное сопротивление, пределы пропорциональности и упругости без уменьшения пластичности. Понижение относительного удлинения, ударной вязкости наблюдается при концентрации марганца выше 4,0 %. Марганцевые латуни хорошо обрабатываются давлением в горячем и холодном состоянии. Стойкость их к воздействию хлоридов, морской воды и перегретого пара значительно выше, чем у обычных латуней. Склонность таких сплавов к коррозионному растрескиванию весьма значительна. Их используют в виде полос, листов, прутков, а также поковок в судостроении и в других отраслях промышленности.
Никелевые латуни обладают хорошей коррозионной стойкостью, повышенными механическими свойствами и выносливостью против истирания, хорошо обрабатываются давлением в горячем и холодном состояниях. Под влиянием никеля повышается коррозионная стойкость в атмосферных условиях, морской воде и в условиях бактериологической коррозии, а также резко уменьшается склонность к коррозионному растрескиванию. Они применяются для изготовления конденсаторных трубок морских судов, манометрических трубок, сеток бумагоделательных машин и других изделий.
Вредное влияние свинец оказывает только на a-латунь, не испытывающую фазовых превращений (Zn < 32 %). При более высоких значениях концентрации второго компонента сплавов добавляемый металл, располагающийся по границам зерен, в результате перекристаллизации a ® b оказывается внутри зерен и не мешает обработке давлением. Поэтому в латунях с концентрацией цинка 32,0 – 38,0 % загрязнение свинцом можно допустить в значительно больших пределах, а при количестве выше 38,0 – 40,0 % его вводят умышленно до 1,0 – 2,0 %, так как такие латуни обрабатываются давлением в однофазном b-состоянии и свинец не препятствует латуни пластически деформироваться. Одновременно обособленные включения свинца повышают обрабатываемость режущим инструментом, так как облегчают стружколомание. Такие латуни называют свинцовистыми и относят к числу автоматных сплавов. Они хорошо обрабатываются резанием, обладают повышенными антифрикционными свойствами и хорошо деформируются в холодном состоянии. Значительная часть существующих марок свинцовистых сплавов относится к группе специальных, носящих название мунц-металл.
Коррозионная стойкость латуней резко повышается в условиях воздействия морской воды при добавке в них 0,5 - 1,5 % Sn «морские латуни». Они имеют удовлетворительные механические, технологические и литейные свойства и по химическому составу относятся к оловянным латуням. Наибольшее применение имеют латуни марок ЛО70-1 и ЛО62-1. Из первых производят трубки конденсаторов морских судов и различной теплотехнической аппаратуры. Сплав марки ЛО62-1 используется для изготовления деталей, от которых требуется повышенная коррозионная стойкость. Выпускается он в виде полос, листов и прутков. Добавка в сплавы железа повышает его механические и технологические свойства главным образом вследствие того, что задерживает рекристаллизацию и способствует получению мелкого зерна. При содержании железа более 0,03 % латуни становятся магнитными. Поэтому для получения антимагнитных сплавов концентрация железа допускается не выше указанного значения. Особо благоприятное влияние на повышение механических свойств и улучшение коррозионной стойкости оказывает железо в сочетании с марганцем, никелем и алюминием.
Сурьма и сера сильно ухудшают качество латуней. Примеси сурьмы вызывают разрушение сплавов при обработке давлением как в горячем, так и в холодном состояниях. Под влиянием сурьмы увеличивается склонность латуней к коррозионному растрескиванию.
При большом содержании As (более 0,5 %) сплавы в значительной мере теряют пластичность за счет образования на границах зерен хрупких прослоек химического соединения. Вместе с тем концентрация мышьяка до 0,02 % предохраняет латуни от обесцинкования, что повышает коррозионную стойкость их в морской воде.
Небольшие количества фосфора повышают механические свойства сплавов и способствуют измельчению зерна в литье. При большом его содержании он выделяется в виде отдельной фазы, увеличивая твердость и снижая пластичность латуней.
В зависимости от способа изготовления изделий и полуфабрикатов из латуни их разделяют на литейные и деформируемые.
Литейные сплавы предназначаются для отливки различных коррозионностойких, антифрикционных и других деталей.
Деформируемые латуни подвергают всем видам горячей и холодной обработки давлением.
Изменяя режимы обработки давлением, получают сплавы с различными механическими свойствами: мягкие, твердые и мягко-твердые.
Мягкая латунь обладает высокой пластичностью. Достигается это обработкой давлением в отожженном состоянии. Степень мягкости характеризуется величиной предела прочности и относительного удлинения, а для лент и листов - глубиной продавливания по Эриксону.
Твердая латунь характеризуется повышенной прочностью (твердостью) и пластичностью. Первая достигается обработкой давлением с высокими степенями обжатия (упрочнением). Обычно требуемые механические свойства полуфабрикатов получаются при степени нагартовки не менее 30,0 %.
Особо твердая латунь изготавливается холодной обработкой давлением (прокаткой и волочением) с высокой степенью деформации. Таким путем из латуни производят ленты и полосы с временным сопротивлением не менее 62 кГ/мм2 и относительным удлинением не менее 2,5 %.
В электротехнике более широкое применение находит латунь, обрабатываемая давлением. Она используются для изготовления различных токопроводящих деталей электрооборудования, стержней короткозамкнутых роторов асинхронных электродвигателей, прижимных контактов электрических аппаратов.
Для контактов, отключающих токи 30 - 100 кА, используются композиции медь - графит. Изделия из систем медь - вольфрам и серебро - вольфрам отличаются более высокой износостойкостью, стойкостью к свариванию и оплавлению. Чаще всего они применяются в качестве контактов высоковольтных масляных выключателей.
Чистая медь из-за склонности к атмосферной коррозии с образованием оксидных и сульфидных пленок непригодна для слаботочных контактов, однако применяется в сильноточных аппаратах.
В качестве пружинных металлических контактных материалов применяют твердотянутую электролитическую медь, специальные сорта бронз (кадмиевые, кадмиево-оловянистые, бериллиевые). Основное применение они находят в проволочных потенциометрах, реостатах и переключателях.
Медноникелевые сплавы также широко применяются, их условно разделяют на конструкционные и электротехнические. К конструкционным материалам относятся системы типов мельхиор и куниаль.
Мельхиоры с примерным составом – 68,0 % меди, 30,0 % никеля, 1,0 % марганца и 1,0 % железа - обладают высокой коррозионной стойкостью в пресной и морской воде,сухих газах и в атмосферных условиях, они хорошо противостоят действию щелочных растворов солей и органических соединений. По структуре они представляют собой твердые растворы металлов-добавок в меди, и поэтому хорошо обрабатываются давлением в холодном и горячем состояниях.
Мельхиор марки МНЖМц30-0,8-1,0 имеет большую стойкость в среде парового конденсата. По устойчивости против действия ударной (турбулентной) коррозии он превосходит практически все другие известные сплавы. Благодаря этим свойствам он применяется для конденсаторных труб морских судов, работающих в особо тяжелых условиях. Сплав марки МН19 используется для изготовления монет, деталей точной механики, медицинских инструментов, сеток, столовой посуды и других изделий.
Куниаль – сплав меди с никелем и алюминием. Он существует двух типов: А и Б. Примерный состав куниаля А – 84,0 % меди; 13,0 % никеля и 3,0 % алюминия.Он хорошо обрабатывается давлением в холодном и горячем состояниях. Полуфабрикаты из него производят в виде спрессованных прутков с временным сопротивлением и относительным удлинением не менее 70 кГ/мм2 и 7,0 % соответственно. Куниаль Б (92,5 % Cu; 6,0 % Ni; 1,5 % Al) обладает хорошей коррозионной стойкостью. Полуфабрикаты из данного сплава изготовляют в виде полос толщиной 0,5 – 3 мм; имеющих соответственно временное сопротивление и относительное удлинение не менее 56 кГ/мм2 и 3,0 %. Их используют для производства различных пружин.
Группу электротехнических медноникелевых сплавов составляют таковые типов ТП, ТБ, копель, манганин, константан и нейзильбер.
Сплав ТП (МН0,6 - 0,6 % никеля и остальное медь) применяется для производства компенсационных проводов к платина-платинородиевой термопаре, а из ТБ (МН16 – 16,0 % никеля) – к платина-золотой и палладий-платинородиевой термопарам.
Копель – сплав, содержащий наряду с основными компонентами еще и марганец (56,5 % Cu; 43,0 % Ni; 0,5 % Mn) и употребляемый, в качестве отрицательного термоэлектрода термопар хромель-копель и железо-копель, а также в виде компенсационных проводов. Он имеет максимальную термоэлектродвижущую силу (термоэ.д.с) по сравнению с другими медноникелевыми системами такого же назначения и практически нулевой температурный коэффициент электросопротивления (ar). Этот сплав является также хорошим материалом для реостатов и нагревательных устройств с рабочей температурой до 600 °С.
Манганин. Его примерный состав: Сu – 83,0 – 85,0 %; Mn – 12,0 %; Ni – 3,0 – 5,0 %. Данное название происходит от наличия в нем марганца (латинское «manganum») в достаточно большом количестве. Желтоватый цвет сплава объясняется высоким содержанием меди. Он широко применяется в качестве прецизионного материала с высоким омическим сопротивлением, а также для изготовления образцовых резисторов. При 200 °С удельное электросопротивление манганиновых лент, полос и проволоки составляет 0,42 - 0,48 ом·мм2/м; ar весьма мал, (6 - 50)·10-6·К-1; коэффициент термо-э. д. с. в паре с медью всего лишь 1 мкВ/К, что позволяет почти полностью избавиться от термотоков. Манганин может вытягиваться в тонкую (до диаметра 0,02 мм) проволоку, выпускаемую очень часто с эмалевой изоляцией. Манганиновый микропровод используется для конструирования миниатюрных высокоточных элементов, в том числе прецизионных резисторов больших номиналов. Недостатками такого микропровода являются невысокая воспроизводимость характеристик и пониженная гибкость из-за хрупкости изоляции. Для обеспечения малого значения ar и стабильности r во времени она подвергается специальной термообработке (отжиг в вакууме при температуре 550 - 600 °С с последующим медленным охлаждением; намотанные катушки иногда дополнительно отжигаются при 200 °С). Предельная длительно допустимая рабочая температура сплавов не более 200 °С; механические свойства: sr равен 450 – 600 МПа, d составляет 15,0 – 30,0 %, плотность равна 8,4 мг/м3.
Константан - сплав, содержащий 58,5 % меди, 40,0 % никеля и всего лишь 1,5 % марганца. Этот состав отвечает минимуму ar в системе Сu - Ni при довольно высоком значении удельного электросопротивления. Название «константан» объясняется значительным постоянством r при изменении температуры (ar при нормальной температуре составляет - (5 - 25)·10-6К-1 при r = 0,48 - 0,52 мкОм·м, в интервале 20-100 °С -2·10-6К-1). По механическим свойствам константан близок к манганину (sr = 400 – 500 МПа, d = 20,0 – 40,0 %, плотность равна 8,9 мг/м3), однако его нагревостойкость выше. Он может применяться для изготовления реостатов, термопар и электронагревательных элементов, длительно работающих при температуре 450 – 500 °С. Существенным отличием этих сплавов является высокая термоэлектродвижущая сила константана в паре с медью; его ar составляет 45 – 55 мкВ/К. Это является недостатком при использовании константановых резисторов в измерительных схемах. При наличии разности температур в местах контакта проводников из сплава с чистыми медными возникают термоэлектродвижущие силы, которые могут явиться источником ошибок, особенно при мостовых и потенциометрических методах измерений. Зато константан с успехом может быть использован при изготовлении термопар, служащих для измерения температуры, если последняя не превышает нескольких сотен градусов. Широкому применению константана препятствует большая концентрация в его составе дорогого и дефицитного никеля.
Для изготовления контактных пружин находит применение нейзильбер. Нейзильбер - сплав, обладающий наилучшими свойствами из группы тройных систем меди с никелем и цинком (65,0 % Cu; 20,0 % Zn; 15,0 % Ni). Он представляет собой твердый раствор данных элементов в меди, имеет хорошую коррозионную стойкость, красивый серебристый цвет, повышенную прочность и удовлетворительную пластичность в холодном и горячем состояниях. На воздухе нейзильбер не окисляется и достаточно стоек в растворах солей и органических кислот. Применяется этот сплав для изготовления медицинских инструментов, технической посуды, телефонной, паровой и водяной аппаратуры, изделий санитарной техники, точной механики, бытовой посуды и художественных изделий. Полуфабрикаты из нейзильбера поставляются в виде полос, лент, прутков и проволоки. Мягкие нейзильберовые полосы имеют временное сопротивление не менее 55 кГ/мм2 и относительное удлинение 1,0 %. Особо твердые ленты обладают временным сопротивлением более 70 кГ/мм2. Данный параметр мягкой нейзильберовой проволоки составляет не менее 35 кГ/мм2, полутвердой - не менее 45 кГ/мм2 и твердой - не менее 65 кГ/мм2.
Наиболее широкое применение в качестве твердых припоев получила чистая медь марок М0, Ml, M2 и некоторые ее сплавы, основой которых являются системы медь - цинк, медь - никель, медь - фосфор и медь - марганец - никель.
Чистую медь широко применяют для пайки изделий из углеродистых, конструкционных и быстрорежущих сталей и никельсодержащих сплавов. Соединения, паянные такими припоями, имеют высокую коррозионную стойкость, и многие из них выдерживают большие механические нагрузки. При пайке расплав хорошо растекается по поверхности и проникает в узкие зазоры, образуя прочные и пластичные соединения. Недостатком меди как припоя является возникновение в соединениях, выполненных кислотосодержащей маркой (Ml, M2 и др.), газовых пор и трещин при осуществлении процесса в окислительной среде (вследствие образования эвтектики Cu - Cu2O).
Пайку чистым металлом выполняют обычно при индукционном нагреве или в печах с защитной атмосферой. Стали, легированные хромом, алюминием и кремнием, паяют медью только в водороде, очищенном от кислорода и влаги. Никельсодержащие сплавы с марганцем хорошо паяются в атмосфере чистого водорода и диссоциированного аммиака без флюса. В защитной среде, содержащей до 10,0 % водорода, медь плохо растекается по поверхности металла, в этом случае требуется применение флюса. Температура пайки 1150 - 1200 °С.
Сплавы порошка меди с жидким галлием используют для изготовления припоев-паст при сложной монтажной пайке без флюса, а также для изготовления сложнонагруженных узлов, деталей электровакуумных приборов, работающих до температуры 1000 °С без нарушения вакуумной плотности. Наполнителем припоев-паст служат тонкодисперсные порошки меди, никеля с добавками индия и олова.
Латуни широко применяют для пайки большинства металлов. Наибольший интерес в данном качестве представляют сплавы, содержащие менее 39,0 % цинка и имеющие однофазную структуру (a-твердый раствор). С увеличением концентрации цинка в припое его пластичность значительно снижается. Сравнительно низкая температура плавления медноцинковых припоев дает возможность применять их для пайки изделий, которые нельзя нагревать до высоких температур. Низкая температура пайки ограничивает образование диффузионной зоны и делает соединение более прочным. В качестве наиболее легкоплавких припоев используются сплавы с концентрацией меди от 36,0 до 54,0 %. Из-за высокого содержания цинка они отличаются большой хрупкостью и недостаточной пластичностью, поэтому их используют при пайке изделий, не подвергающихся ударным нагрузкам, изгибу и вибрации. Одним из недостатков медноцинковых припоев, препятствующих применению их для пайки соединений, работающих в вакууме при повышенных температурах, является испарение цинка с образованием вредного для здоровья оксида ZnО с температурой плавления 1975 °С. В результате этого ухудшается прочность паяных соединений при повышенных температурах (200 - 600 °С), припой становится более тугоплавким и менее жидкотекучим, что приводит к плохому заполнению зазора и снижению надежности работы паяного соединения. Для уменьшения испарения цинка паяние латунью производят обычно с применением флюса, вспомогательного материала, или в припой добавляют кремний, алюминий, бор. Флюсом обычно служат боросодержащие соли, которые после пайки остаются на изделии в виде тонкой стекловидной пленки, прочно сцепленной с основным металлом. Образование оксида цинка также значительно уменьшается, если пайку вести быстро, с небольшой выдержкой или применять окислительное пламя.
Более высокими механическими свойствами обладают некоторые, используемые в качестве припоев, многокомпонентные латуни, легирующими элементами которых являются олово, кремний, никель, марганец и железо. Введение больших количеств олова (5,0 - 10,0 %), кремния (0,2 - 3,0 %), никеля (5,0 - 25,0 %) и марганца (2,0 - 32,0 %) увеличивает прочность и относительное удлинение паяного соединения. Небольшие добавки данных элементов (до 1,0 %) понижают температуру плавления, повышают коррозионную стойкость в морской воде и увеличивают жидкотекучесть и растворимость припоя. Наличие никеля также обеспечивает отсутствие хрупкой диффузионной прослойки на границе металл - припой и делает паяное соединение прочным. Последним качеством обладают также железо (0,1 - 5,0 %) и марганец. Применение же латуней с оловом в качестве припоев ограничивается их недостаточной пластичностью. Выгорание цинка уменьшается при добавлении в медноцинковые припои кремния. Это связано
Дата добавления: 2015-09-21; просмотров: 7086;