Применение мехатронных и робототехнических систем в
оборудовании для автоматизации технологических процессов;
Несмотря на непрерывное расширение сферы применения мехатронных систем (МС) основной областью их применения по-прежнему пока остается промышленность и, прежде всего, машиностроение и приборостроение. Здесь появились первые средства автоматизации и сосредоточено до 80% всего мирового парка робототехнических средств.
К МС производственного назначения относятся машины с компьютерным управлением, предназначенные для выполнения технологических, транспортных и вспомогательных функций на производстве. Это - промышленные роботы (ПР), станки с ЧПУ, технологические машины – гексаподы, транспортно-складские системы и т.п.
Функционирование ПР как мехатронного объекта достаточно подробно рассмотрено в литературе [1-3].
При изучении вопросов применения МС в промышленности следует определить вид технологического процесса (комплекс: механообработки, холодной штамповки, ковки, литья, прессования пластмасс, термической обработки, сварки, транспортный, контроля и испытаний и т.д.).
Роботизированным участкам, линиям и цехам присущи следующие качества: наличие транспортно-складской системы и единой системы управления. Эти системы материально и информационно связывают отдельные технологические ячейки, автоматизированные склады (материалов, заготовок, инструмента, отходов производства, готовой продукции) и другие части комплекса в одну согласованно действующую систему. Кроме того, такие комплексы должны включать помимо систем управления в реальном времени непосредственно технологическим оборудованием расположенные над ними уровни иерархии управления, решающие задачи программирования и оперативно-календарного планированиях[4].
На рис. 5.1 показан пример простой линейной компоновки однопоточной роботизированной технологической линии холодной штамповки [4]с непосредственной связью между составляющими линию ячейками. В ней отсутствует межоперационная транспортная система, а предметы производства передаются от одной ячейки к другой непосредственно входящими в них вспомогательными ПР. Такие линии с непосредственной жесткой связью между ячейками просты, однако требуют строго определенного взаимного расположения основного технологического оборудования.
Рис. 5.1. Схема однопоточной роботизированной технологической линии холодной штамповки с линейной компоновкой: ТО — основное технологическое оборудование; ПР — промышленный робот; М — магазин поштучной выдачи заготовок
Данная компоновка характерна для технологических процессов с малым циклом обработки предметов производства на технологическом оборудовании (единицы, десятки секунд), что свойственно, в частности, процессам холодно-листовой штамповки. Для технологических процессов с большей длительностью обработки на технологическом оборудовании часто применяют другой тип построения комплексов с обслуживанием одним ПР нескольких единиц технологического оборудования.
На рис.5.2 показан вариант такого комплекса с круговой компоновкой, в котором один ПР обслуживает 3 металлорежущих станка, расположенных вокруг него.
Рис. 5.2.Схема роботизированного технологического участка механической обработки с круговой компоновкой
По мере совершенствования МС происходит устойчивый рост доли ПР, применяемых на основных технологических операциях. Хотя внедрение ПР на основных промышленных операциях требует значительно больших (в 3-4 раза) затрат, чем на вспомогательных операциях, именно здесь достигается наибольшая эффективность применения ПР при высвобождении рабочих мест. Велик и социальный эффект в связи с вредностью для человека ряда таких операций (например окраска, сварка) или их монотонностью (например, сборка на конвейере). В машиностроении основными типами технологических комплексов в которых ПР получили распространение на основных операциях, являются комплексы сборки, сварки, нанесения покрытий, шлифования, зачистки, клепки. К таким комплексам относятся комплексы для бурения в горном деле, монтажа огнеупоров в металлургии, для монтажа и облицовочных работ в строительстве, упаковки штучной продукции в легкой и пищевой промышленности.
Сборочные робототехнические комплексы.Этот тип робототехнических комплексов по своему значению является, пожалуй, наиболее важным. Сборочные операции в машиностроении составляют до 40% себестоимости изделий, а в приборостроении больше — до 50—60%. Вместе с этим, степень автоматизации сборочных работ сегодня весьма низка в связи с ограниченными возможностями, которые имеют здесь традиционные средства автоматизации в виде специальных сборочных автоматов. Такие автоматы применимы главным образом в массовом производстве, в то время как, например, в машиностроении до 80% продукции относится к серийному и мелкосерийному производству. Поэтому создание гибких сборочных комплексов на ПР является одним из основных направлений в автоматизации сборочных операций.
К сборочным операциям относятся механическая сборка, электрический монтаж, микроэлектронная сборка. Процесс сборки состоит из следующих последовательных взаимосвязанных операций:
- загрузка собираемых деталей в загрузочные и транспортные устройства (обычно с их ориентацией);
- перемещение деталей к месту сборки;
- базирование, т. е. фиксация в строго определенной позиции, с ориентацией деталей на сборочной позиции;
- собственно операция сборки, т. е. сопряжения деталей, включая закрепление;
- контрольно-измерительные операции в ходе сборки;
- удаление собранного узла со сборочной позиции для перемещения на следующую позицию, если сборка не закончена.
На рис. 5.3 показан пример сборочного робототехнического комплекса, построенного на базе универсального ПР. Комплекс включает несущую раму, поворотный стол, загрузочные и ориентирующие устройства, устройства крепления оснащения, кабельные узлы, устройство управления комплексом, блоки синхронизации и связи с ЭВМ[4].
Рис. 5.3. Робототехнический комплекс для сборки контурных катушек радиоприемников: 1 — загрузочное устройство (тара); 2 — промежуточная точка;
3 — разгрузочное устройство; 4 — устройство группового управления;
5 — роторный стол; 6 — загрузочное устройство; 7 — ванна для очистки;
8 — ванна для пайки; 9 — ванна для флюсования
Для выполнения собственно операций сборки применены универсальные пневматические ПР типа МПС-9С. Комплекс предназначен для сборки контурных катушек бытового радиоприемника, ПР в его составе выполняют следующие операции:
- выборку каркасов катушек из кассеты; - флюсование выводов обмоток
- пайку выводов;
- промывку выводов;
- установку каркасов на ложементы поворотного стола;
- надевание кольца;
- навинчивание буксы;
- закручивание сердечника;
- надевание экрана;
- маркировку катушки;
- установку в кассеты готовой контурной катушки.
Смена кассет на рабочих позициях автоматизирована с помощью разгрузочно-загрузочных устройств. Сборочные элементы подаются на рабочие позиции с помощью вибробункеров, в которых выполняются их ориентация, накапливание и поштучная выдача. Для обеспечения условий собираемости и снижения требований к точности изготовления сборочных элементов, оснастки и приспособлений манипуляторы ПР оснащены вибромодулями. За один рабочий цикл 10 ПР выполняют все технологические операции по принципу параллельно-последовательной сборки. В конце цикла происходит перемещение координатного устройства, которое подает в позицию захвата первого ПР и в позицию сброса десятого ПР соответствующие ячейки подающей и приемной кассет, а также перемещение на один шаг роторного стола, на специальных ложементах которого производится сборка контурной катушки. Длительность работы комплекса — 10 с.
Применение подобных сборочных комплексов на порядок повышает производительность труда, дает экономию производственной площади, позволяет осуществить комплексную автоматизацию сборочного производства в целом. Переналадка комплекса осуществляется заменой рабочих органов ПР и их управляющих программ.
Мехатронный подход положен в основу создания различных типов металлорежущих станков нетрадиционной компоновки с ЧПУ на базе ограниченного набора унифицированных мехатронных модулей вращательного и линейного перемещений, предназначенных для высококачественной обработки изделий со сложной поверхностью [5-9]. При разработке таких станков использованы принципы блочно-модульного построения и управления. Предусмотрены возможности измерения текущих параметров деталей и записи управляющих технологических программ по модели изделия.
На рис. 5.4 представлен общий вид вертикального обрабатывающего центра, предназначенного для высокоскоростной механической обработки деталей из различных материалов, имеющих сложную геометрическую форму (прессформы, штампы и т.д.), а также тонкостенных деталей сложного профиля.
Рис. 5.4. Общий вид вертикального обрабатывающего центра МС 5-700
Обрабатывающий центр выполняет операции сверления, прямолинейного, контурного и объемного фрезерования, растачивания, нарезания резьбы, Благодаря 2-координатному поворотному столу возможна полная обработка заготовки (с пяти сторон) за одну установку, что обеспечивает высокую точность обработки и производительность.
В качестве привода главного движения применен мехатронный узел - электрошпиндель с бескорпусным синхронным двигателем модели 1FE1093-4WNII фирмы SIEMENS. Электродвигатель при небольших габаритах имеет высокую мощность, оптимальную для главного привода систему регулирования частоты вращения и позволяет получить высокую производительность во всем диапазоне частот вращения шпинделя.
Отсутствие в приводе передаточных звеньев (шкивов, ремней, зубчатых передач) позволяет добиться высокой надежности и долговечности работы обрабатывающего центра.
Цифровое УЧПУ Sinumerik 840DЕ в комплекте с цифровыми приводами Simodrive 611D с высокодинамичными серводвигателями типа 1FT6, не требующими технического обслуживания, обеспечивают отличные динамические характеристики вертикальных обрабатывающих центров, высокую точность обработки и большую надежность [10-11].
На рис.5.5 представлены пяти- и шестикоординатные многоцелевые станки моделей 500/V5 и 800/VF6 соответственно. Станки выпущены ОАО «Стерлитамакский станкостроительный завод». Они предназначены для изготовления лопаток и моноколес газотурбинных двигателей, а также сложнофасонных инструментов [10]. Эти станки имеют компоновку с подвижной колонной и обладают высокой жесткостью и термостабильностью. В них реализована концепция высокоскоростной обработки заготовок с использованием использованию мехатронных модулей.
Рис.5.5. Компоновка многоцелевых станков 500V/5 (a) и 800VF6 (б) (буквами обозначены оси координат и направления перемещения исполнительных органов)
На рис.5.6 представлен станок фирмы «Sodick" (Япония) в котором использованы мехатронные модули линейных перемещений.
Рис.5.6. Станок для проволочно-вырезной электроискровой обработки
Лазерный робототехнический комплекс
Робототехнический комплекс предназначен для лазерной резки сложных контуров на горизонтальной плоскости. В состав комплекса входят: манипулятор с кинематической схемой SCARA, твердотельный лазер как рабочий орган, компьютер типа IBM со встроенным контроллером движения и системой графического программирования в среде Lab View[12].
Робот используется для контурного перемещения резака в рабочей зоне. Выбранная кинематическая схема обеспечивает высокую точность движения манипулятора (отклонение от программной траектории не более 0,05 мм при максимальной скорости 0,7 м/с), привод – электрический.
Компактный лазер типа АИГ-Nd изготовлен на основе алюмоиттриевого граната и обладает следующими основными характеристиками: длина волны 1,06 мкм, мощность излучения 150 Вт, фокусное расстояние 50 мм, потребление воды 5 л/мин, потребление электроэнергии 25 кВт/час.
Управление функциональными движениями мехатронной системы (т. е. совместно исполнительными электроприводами многостепенного манипулятора и режимами работы лазера) осуществляется устройством управления, которое включает:
компьютер типа IBМ PC промышленного исполнения;
контроллер движения типа Tech 80 серии 5650 на базе цифрового
сигнального процессора (время квантования 100 мкс, 8 каналов ввода/вывода, управление приводом через 16-битный ЦАП или ШИМ);
силовые преобразователи типа CPCR-MR05.
Программное обеспечение системы управления разработано в среде графического программирования LabView, которая представляет собой мощное инструментальное средство для организации интерфейса пользователя, разработки алгоритмов для контроллера движения, автоматической генерации управляющих программ для робота и вспомогательного технологического оборудования.
Создана специальная библиотека управления сложным движением, которая имеет более 150 команд для следующих основных функций:
начальной инициализации системы;
планирования траектории движения лазера по компьютерному чертежу заготовки (подготовленному, например, в среде AutoCAD);
расчета оптимальных законов движения приводов во времени;
управления контурным движением манипулятора в реальном времени;
математических функций;
калибровки механической части системы;
конфигурации блоков управления, инкодеров, ограничителей;
связи устройства управления с внешним оборудованием.
Робототехнический комплекс механообработки
Робототехнический комплекс (РТК) предназначен для выполнения операций механообработки деталей из пластмасс и легких сплавов. К числу типичных операций относятся зачистка заусенцев, снятие облоя, шлифование контуров и поверхностей, сверление отверстий, снятие фасок. [5].
В состав РТК входят: промышленный робот РМ-01, включающий манипулятор PUMA-560 и устройство управления «Сфера-36», компьютер верхнего уровня типа IBM PC, блок пневмоэлектроаппаратуры, сменные рабочие органы (схваты, инструментальные пневмоголовки), комплект режущего инструмента (фрезы, напильники, металлические щетки), устройство силомоментного очувствления с блоком ввода аналоговых сигналов в устройство управления и многофункциональный адаптер ввода-вывода сигналов в компьютер.
Рис. 2.2. Рабочий орган технологического робота |
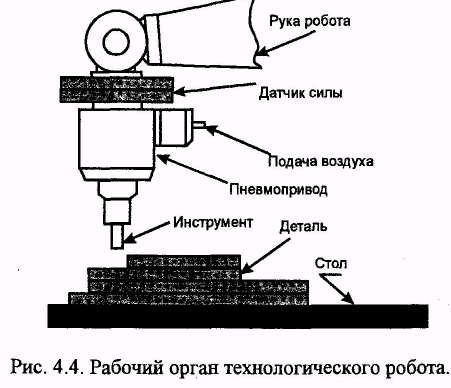
Устройство силомоментного очувствления состоит из двух функциональных модулей: датчика силы и блока обработки силомоментной информации. Датчик силы конструктивно выполнен в виде плоских крестообразных пластин, на грани которых наклеены тензорезисторы. Конструкция датчика предусматривает измерение трех компонент вектора силы, действующей на рабочий орган робота: силы, перпендикулярной фланцу датчика силы (Fz), и двух моментов в плоскости фланца (Mx и My). В качестве чувствительных элементов выбраны фольговые тензорезисторы типа КФ 5П1-3200-А12. Датчик изготовлен из алюминиевого сплава Д16-Т, обладающего высоким значением модуля Юнга и малой удельной массой. Блок обработки силомоментной информации предназначен для преобразования сигналов с тензоусилителя в три информационных сигнала о векторе сил, действующем на рабочий орган. Блок выполнен в виде отдельной платы и установлен в корпус тензоусилителя. Технические характеристики устройства силомоментного очувствления:
- количество измеряемых компонент вектора сил – 3 (осевая нагрузка до 50 Н; поперечные силы по осям X и Y до 25 Н на плече 0,12 м);
- диапазон выходных сигналов для ввода в компьютер от -5 В до + 5 В,
- для ввода в «СФЕРУ-36» 0–5 В;
- погрешность выходного сигнала не более 2 % от номинала.
При управлении роботом на операциях механообработки основная функция компьютера состоит в обработке сигналов от датчика силомоментного очувствления и выработке сигналов коррекции движения.
Если датчик сил и моментов содержит встроенный микропроцессор, то организация обмена информацией с компьютером не представляет труда. В противном случае необходимо использовать многофункциональный адаптер (МА), который осуществляет согласование аналоговых и цифровых сигналов с системной шиной компьютера. МА представляет собой электронный модуль (плату), вставляемый в слот IBM PC. Адаптер содержит следующие функциональные узлы: аналого-цифровой преобразователь с коммутатором на входе, цифро-аналоговый преобразователь, устройство параллельного ввода-вывода и таймер. Серийный комплект устройства управления «Сфера-36» не имеет возможности ввода и обработки аналоговой информации. Поэтому на базе стандартного модуля аналогового ввода (МАВ) этой стойки управления был реализован контроллер ввода аналоговых сигналов с силомоментного датчика. Шесть каналов модуля МАВ служат для ввода сигналов с потенциометрических датчиков, расположенных в степенях подвижности манипулятора. Оставшиеся два канала АЦП, которые в штатном режиме используются для тестирования системы, переведены в режим связи с внешними задатчиками сигналов. Связь между устройством управления «СФЕРА» и компьютером обеспечивается специальными драйверами.
Программирование движений технологического робота проводится автоматизированно с помощью специально разработанного комплекса подготовки управляющих программ. Таким образом, данный робототехнический комплекс механообработки реализует современную концепцию построения производственных систем типа CAD/CAM, когда автоматизированное проектирование изделия и его автоматическое изготовление интегрированы в единую систему и задача пользователя состоит только в подготовке исходной компьютерной модели детали. Можно провести аналогию между мехатронным принципом объединения элементов и концепцией CAD/CAM, где методология интеграции воплощена на высоком системном уровне.
Применение промышленных роботов, особенно для механической обработки, знаменует появление на производстве относительно новых технологий.
На сегодняшний день промышленные роботы, помимо задач «взять и положить» могут успешно выполнять целый ряд технологических операций мехобработки, включая типичные задачи многоосевых фрезерных станков, объемную резку лазером, плазмой, водяной струей, а также покраску, пескоструйную чистку, щлифовку, полировку, контактную и дуговую сварку и т.д. Поставщики робототехники уже начали выпускать модели, полностью ориентированные на выполнение операций мехобработки. На многих предприятиях роботы успешно фрезеруют детали даже из материалов высокой твердости, причем с достаточной точностью. На сегодняшний день «сотка» - уже не предел для робота, такая точность вполне достаточна для половины всех задач. По стоимости оборудования рабочая ячейка на базе промышленного робота (рис.5.10) может оказаться дешевле в несколько раз, особенно в случае крупногабаритных 5-осевых станков [7].
Рис.5.10. Полностью сконфигурированная роботизированная ячейка с поворотным столом
Преимуществом робота является наличие 6 степеней свободы при движении манипулятора. Создавая рабочие ячейки на базе роботов можно задействовать еще и 3 дополнительные линейные оси плюс разного рода комбинации двух наружных поворотных осей. В сумме количество степеней свободы может достигать 11.
Рис. 5.11. Робот размещен на линейной направляющей, а деталь – на поворотной оси.
Рис.5.12 Робот размещен на линейной направляющей для обработки длинных деталей.
Помимо задач обработки робот в состоянии выполнять и традиционные операции, т.е. может самостоятельно взять деталь, установить ее в рабочей зоне, затем обработать ее и убрать (переместить к готовым деталям или передать на следующий участок). Дополнительные возможности открывает способность робота выполнять задачи по схеме « деталь к инструменту» Это означает, что робот может, взяв деталь в свою «руку», подносить ее к различным инструментам, установленным неподвижно (рис.5.13 ).
Рис. 5.13.Пример реализации схемы «деталь к инструменту»
Дата добавления: 2015-08-11; просмотров: 6153;