МЕХАТРОННЫХ И РОБОТОТЕХНИЧЕСКИХ СИСТЕМ
4.1. Место и роль информационных систем, связь с системами управления
Информационная система (ИС) представляет собой совокупность функционально объединенных измерительных, вычислительных и других вспомогательных технических средств, предназначенных для получения измерительной и другой информации, необходимой для нормального функционирования мехатронного или робототехнического устройства, передачи, хранения и преобразования этой информации (в том числе осуществления логических функций контроля, диагностики, идентификации) в целях представления информации потребителю (системе управления или человеку-оператору) в виде, удобном для принятия решения [1].
ИС являются важнейшей составной частью МС и занимают в них особое место: именно они обеспечивают координацию и синхронизацию работы всех других систем. Например, на летательных космических и авиационных аппаратах количество датчиков составляет от 250 до 2000 в зависимости от типа объекта [2].
Благодаря ИС объект приобретает новые системные свойства (целостности, организованности, иерархичности структуры), которые не являются простой суммой свойств составляющих систем.
Любая мехатронная или робототехническая система должна иметь возможность контролировать состояние своих подсистем, а также значимые для ее нормального функционирования параметры внешней среды. Такая информация позволяет, например, мобильному роботу следить за своим состоянием, правильно ориентироваться в окружающем пространстве, выбирать оптимальный маршрут движения и рабочие объекты, своевременно избегать опасных ситуаций (перегрева, опрокидывания, причинения вреда человеку и т.п.). Робот, лишенный возможности получать информацию о состоянии своих подсистем и окружающем пространстве подобен человеку, лишенному не только пяти органов чувств, но информации от многочисленных биологических сенсоров, расположенных, например, в наших суставах (чтобы убедиться в их наличии, закройте глаза и вы без труда сможете описать положение любого сустава руки или ноги!). Чтобы подсистема управления робота смогла принимать адекватные решения, поступающая к ней из внешней среды (от датчиков очувствления) и от блоков самого робота (в том числе и хранящаяся в запоминающих устройствах) информация должна быть достаточно полной и достоверной. При этом, чем выше «интеллектуальный уровень» мехатронной системы, тем в большей степени работа ее подсистемы управления основана на текущей информации, поступающей от датчиков и обрабатываемой в реальном масштабе времени.
В настоящем пособии в качестве примеров рассмотрены информационные системы и конкретные конструкции различных датчиков, в том числе и тех, в разработке которых принимали участие сотрудники кафедры «Робототехника и мехатроника».
4.2. Подсистемы информационных систем
Основными процессами, позволяющими ИС получать необходимую информацию, являются обнаружение событий и объектов, измерение их параметров, обработка результатов измерения, в том числе контроль, диагностика, распознавание образов. В соответствии с этим можно классифицировать ИС по составу, выполняемым функциям и уровню интеллектуальности.
По мере развития ИС качество получаемой с их помощью информации и расширение функциональных возможностей все чаще связывается с их интеллектуализацией. При этом понятие интеллектуальности непосредственно связано с наличием процессора и программной части. Именно переход к созданию процессорных ИС явился главным шагом по формированию предпосылок для появления интеллектуальных ИС.
Однако само наличие процессора и программной части еще не определяет уровня интеллекта ИС. За основу определения этого уровня примем следующее положение: уровень интеллекта обусловливается возможностями использования априорной (банк знаний и банк данных) и текущей информации для синтеза и выполнения алгоритмов, характеризующихся наилучшим для принятых условий и ограничений метрологическим качеством результатов измерений и синтезированной на их основе управляющей информации.
В ИС низших уровней развития процессы измерения и обработка их результатов производится по заранее заданным алгоритмам. В высокоразвитых ИС в той или иной степени используется искусственный интеллект.
Измерительная подсистема осуществляет процесс получения информации, заключающийся в сравнении опытным путем измеряемых и известных величин или сигналов, выполнения необходимых логических операций и представления информации в численной форме. Остановимся на некоторых определениях, используемых в МС. Измерение - нахождение значения физической величины опытным путем с помощью специальных технических средств. Объектом измерения является та или иная физическая величина - особенность физического объекта, характеризующая его свойства, состояние или происходящий в нем процесс и имеющая количественное и качественное содержание. Измерительная информация - количественная информация о свойствах физических объектов (о значениях физических величин), получаемая в результате измерений.
В общем случае под сигналом подразумевают материальный носитель информации, а измерительным называют сигнал, несущий информацию о значении измеряемой величины. Входной измерительный сигнал, т.е. сигнал, воздействующий на вход средства измерения, является физическим процессом, параметры которого являются той или иной функцией времени. Измеряемая величина- определенный параметр этого процесса. Информативным параметром входного сигнала называется параметр физического процесса, который является измеряемым, либо функционально с ним связан. Неинформативным параметром называется параметр входного сигнала, который функционально не связан с измеряемой величиной. Однако такой параметр может оказывать воздействие на измерительной средство и может быть источником погрешности. Выходным сигналом называется сигнал, возникающий на выходе средства измерения. Это - физический процесс или явление, несущее сообщение о каком-либо событии или состоянии объекта наблюдения. В общем случае выходной сигнал может обладать многими параметрами, как информативными, так и неинформативными. В МС выходной сигнал практически всегда имеет электрическую природу.
Приведенные определения можно проиллюстрировать следующим примером. Одним из параметров, значение которого определяется измерительной подсистемой мобильного робота, является давление масла в гидросистеме привода. На мембрану датчика давления, помимо давления, оказывают воздействие также температура, вибрация, радиация и т.п., являющиеся функциями времени. Все эти воздействия и являются входным сигналом для рассматриваемого датчика, но информативным параметром здесь является только давление, остальные воздействия являются неинформативными параметрами. Повышенная температура может уменьшать жесткость мембраны, что приведет к снижению чувствительности датчика, т.е. к искажению результата измерения. Поэтому выходной электрический сигнал датчика содержит составляющую, определяемую воздействием повышенной температуры. Эта составляющая и определяет дополнительную температурную погрешность датчика давления.
Зависимость между значениями величин на выходе и входе средства измерения называется функцией преобразования. Представленная в виде таблицы, графика или формулы эта зависимость для конкретного средства измерения, называется градуировочной характеристикой. Градуировочная характеристика является индивидуальной, т.е. описывает свойства конкретного экземпляра средства измерения. При серийном выпуске однотипных средств измерений используется понятие номинальной функции преобразования. В отличие от градуировочной характеристики, номинальная функция преобразования является типовой, а ее использование сопровождается погрешностями, вызванными отличиями типовой (номинальной) функции преобразования от индивидуальной градуировочной характеристики.
Кроме погрешностей к числу важных параметров средств измерений относятся также предел измерения, параметры номинальной функции преобразования (чувствительность, линейность), предельно допускаемые значения отклонений параметров от их номинальных значений. Эти параметры нормируются и указываются в технической документации на средства измерения. Нормирование метрологических характеристик заключается в установлении границ для отклонений реальных значений параметров средств измерений от их номинальных значений. Нормирование погрешностей средств измерения заключается в установлении для каждого вида допускаемой погрешности предела, под которым понимается наибольшая абсолютная величина погрешности средства измерения, при которой оно может быть признано годным и допущено к применению. Нормирование обеспечивает взаимозаменяемость средств измерения.
Важной характеристикой средств измерений является их надежность. При этом ненадежными считаются не только те средства измерений, которые теряют способность нормально функционировать из-за механических, электрических или иных повреждений, но также и те, у которых характеристики выходят за допустимые пределы. Поэтому надежность средств измерений можно определить, как свойство сохранять нормируемые метрологические характеристики в определенных условиях эксплуатации.
Подсистема автоматического контролявыполняет функцию установления соответствия между состоянием (свойством) объекта контроля и заданной нормой, определяющей качественно различные области его состояния. В результате контроля выдается суждение о состоянии объекта контроля (т.е. к какой из нормированных областей относится рассматриваемое состояние объекта контроля).
В принципе, при контроле нет необходимости знать значения контролируемых величин. С этой точки зрения контроль является операцией сжатия информации, поступающей на вход мехатронного устройства, устранения ненужных для системы управления или человека-оператора сведений об объекте контроля.
Контроль может быть осуществлен везде, где имеются установленные нормы. Нормы задаются самым разнообразным образом, чаще всего в виде области количественных значений, определяющих нормальное состояние объекта (например, при контроле знаний студентов нормы могут задаваться в виде объема конкретных знаний предусмотренных программой обучения).
Затраты труда на выполнение операций контроля в современном высокотехнологичном производстве очень велики, многие изделия подвергаются полному контролю. Сейчас, когда одним из решающих направлений развития производства является обеспечение конкурентоспособности отечественных товаров за счет существенного повышения их качества, роль подсистем автоматического контроля в производственных МС существенно возрастает.
Процессы контроля и измерения, роднит наличие операций сравнения входных или производных от них величин: при измерении - с мерами (овеществленными единицами измерения), а при контроле - с уставками. В подсистемах автоматического контроля описания норм и контрольно-измерительная информация могут быть представлены либо в виде абсолютных значений либо в виде отклонений от номинального значения, при этом второй способ более экономичен.
Следует различать специализированные (предназначенные для выполнения узконаправленных операций) и универсальные подсистемы контроля, а также встроенные в объект контроля и внешние по отношению к нему. Встроенные подсистемы контроля используются в сложных МС и часто входят в состав таких систем [3, 4].
Подсистема технической диагностики ИСпозволяет выявить элементы, послужившие причиной неправильного функционирования какого-либо объекта. Установление факта и места неисправности в МС, а также ошибок в программах путем определения состояния всех элементов и связей обычно нецелесообразно или невозможно. Это объясняется тем, что для такого «стопроцентного» контроля требуются большие затраты времени и труда. Особенно это относится к сложным МС, характеризующимся большим количеством элементов и сложными связями между ними. Такие МС могут насчитывать миллионы и миллиарды элементов (например, специализированные микропроцессоры). В этих случаях используются специальные методики и программы, позволяющие решать задачи диагностики с допустимыми затратами времени и средств. Они основаны на изучении объекта диагностики, сборе необходимых статистических данных, оценке затрат труда на проверку, исследовании форм и закономерностей появления неисправностей и ошибок. При разработке методов диагностики сложных МС разрабатываются и исследуются математические модели объектов диагностики.
Совокупность проверок, достаточная для различения состояния объекта носит название диагностического теста. Например, после включения персональный компьютер производит тестирование ячеек своей оперативной памяти.
Сложные и распределенные в пространстве цифровые МС представляют особую трудность для диагностики. При контроле таких систем на их входы подаются последовательности известных двоичных кодоимпульсных сигналов, а выходные сигналы сопоставляются с образцовыми сигналами, соответствующими правильной работе диагностируемого объекта. Анализ результатов такого сопоставления используется для решения задач диагностики.
Эффективность диагностических процедур можно существенно повысить, если при проектировании объекта учесть необходимость его последующего диагностирования. Поэтому грамотно спроектированная сложная МС должна иметь встроенную подсистему диагностики. Примером может служить персональный компьютер, при каждом включении которого производится самодиагностика с выдачей на экран текущих сообщений; при сбоях в работе или некорректном завершении работы включается диагностическая программа Scandisk, обнаруживающая и устраняющая ошибки в записанных на диске данных. Сам термин «диагностика» пришел в технику из медицины, где также применяются специальные диагностические тесты (например, введение внутрь организма больного специальных химических веществ и наблюдение за реакцией организма на эти вещества; предложение сотрудника автоинспекции подозреваемому водителю ровно пройти по прямой линии или подышать в алкотестер также можно рассматривать как диагностический тест на состояние опьянения).
Подсистема распознавания образовопределяет принадлежность данного объекта к одному из заранее выделенных классов объектов.
Под образом понимается наименование области в многомерном пространстве признаков, в которой отображаются свойства объекта или множества объектов, а под распознаванием образов – процесс, в результате которого определяется соответствие между распознаваемыми объектами и образами. Это соответствие устанавливается путем сравнения объектов и образов по признакам, характеризующим свойства образов, и принятия по определенному алгоритму решения о принадлежности распознаваемых объектов к тому или иному образу.
Образами могут быть «круг», «буква К», «шестерня», «отпечатки пальцев конкретного человека», «отраженный от ракеты сигнал радара» и т.п.
Так же как и норма при контроле, при распознавании образ может быть задан в виде образцового изделия или в виде перечня определенных свойств и значений параметров (признаков) с указанием полей допуска (при выполнении практических задач понятия контроля и распознавания могут совпадать).
Распознавание образов используется, например, сборочными роботами для нахождения нужных деталей на сборочном столе, мобильными роботами для определения объектов или участков пути, специализированными МС для идентификации личности по отпечаткам пальцев, ладоней, радужной оболочки глаза, изображению лица и т.п. В сложных случаях для идентификации личностей могут использоваться элементы искусственного интеллекта. Например, в Лондонском аэропорту установлена система идентификации личности, предназначенная для выявления террористов, фотографии которых занесены в базу данных. Обрабатывая информацию от нескольких телекамер, направленных навстречу потоку проходящих пассажиров, система выделяет изображения одних и тех же лиц, снятых под разными ракурсами. Затем эти изображения сравниваются с образами из базы данных. Если степень совпадения достаточно велика, включается подсистема слежения за подозрительным субъектом, и дальнейшую проверку производит полиция. Система обладает колоссальной пропускной способностью, что позволяет ей работать в режиме реального времени. Для сравнения используются 83 геометрических признака человеческого лица, привязанные к «базе» - расстоянию между центрами зрачков глаз. Используемые алгоритмы распознавания позволяют достаточно уверенно идентифицировать изображения даже в случаях, когда на сделанных телекамерой снимках лицо человека снято под углом или закрыто бородой.
4.3.Датчики внешней и внутренней информации
4.3.1. Основные определения
Измерительный преобразователь (ИП) - средство измерения, предназначенное для преобразования входного измерительного сигнала (измеряемой величины) в выходной сигнал, более удобный для дальнейшего преобразования, передачи, обработки вычислительными устройствами и хранения, но не пригодный для непосредственного восприятия наблюдателем. Например, ИП давления масла в гидроприводе мобильного робота имеет выход в виде электрического напряжения, которое после соответствующего преобразования используется для управления гидронасосом. ИП являются основой для построения ИС.
ИП, расположенный первым в цепи последовательно соединенных преобразователей, называется первичным. Первичный ИП непосредственно взаимодействует с объектом измерения. Все остальные измерительные преобразователи, расположенные в измерительной цепи после первичного, называют вторичными. Именно свойствами первичного преобразователя в значительной степени определяется качество работы всей ИС. Например, в измерительной цепи, позволяющей получить информацию о степени нагрева двигателя мобильного робота, ИП температуры является первичным, а расположенные за ним нормирующий усилитель и АЦП - вторичными.
Вторичные преобразователи используются для масштабирования, усиления, математической обработки, аналого-цифрового и цифро-аналогового преобразования сигналов первичных преобразователей, корректировки их характеристик и т.п.
Наряду с термином измерительный преобразователь используется термин датчик, который обычно обозначает конструктивно завершенное устройство, размещаемое непосредственно в зоне измерения (например, датчик температуры помещен в защитный корпус, имеющий выход для электрического кабеля и отверстия для монтажа). Последние годы в технической литературе по мехатронике получает распространение термин сенсор, которым может обозначаться как первичный ИП, так и датчик.
4.3.3. Виды средств очувствления, контактные и бесконтактные датчики
Основное назначение средств очувствления МС состоит в том, чтобы существенно снизить объем необходимой априорной информации. Кроме того, их включение в состав систем управления позволяет существенно упростить процедуру обучения МС, повысить динамическую точность и быстродействие исполнительных органов. Представим, что перед нами робот, перемещающий деталь из кассеты на сборочный стол и работающий по жесткой программе (без датчиков). Если детали не будет в том месте, откуда робот должен ее взять, он все равно сделает хватательное движение и будет перемещать пустой схват в место назначения на рабочем столе. Если на пути движения руки такого робота встретится препятствие, движение руки не будет остановлено (что может привести к поломке робота или повреждению препятствия). Робот, снабженный датчиками очувствления, сможет взять деталь, даже, если она находится не точно в заданном месте или иначе ориентирована, при движении рука робота остановится перед препятствием, т. е. очувствленный робот учитывает изменения внешней среды и корректирует свои действия в соответствии с этими изменениями.
В зависимости от принципа действия датчики с электрическим выходным сигналом можно разделить на две группы: генераторные или активные и параметрические или пассивные. В генераторных датчиках преобразование измеряемой величины осуществляется непосредственно в электрический сигнал (т.е. такие датчики генерируют электрическую энергию). К ним, например, относятся пьезоэлектрические, индукционные, фотоэлектрические (использующие появление ЭДС в полупроводниковом pn-переходе при его освещении), термоэлектрические. В параметрических датчиках измеряемая величина преобразуется в параметр электрической цепи – сопротивление, индуктивность, емкость и т.п., причем для питания датчика необходим источник электрической энергии. К таким датчикам, например, относятся емкостные, индуктивные, электроконтактные, потенциометрические, тензорезисторные.
По используемым физическим явлениям и эффектам можно выделить следующие виды датчиков, получивших наибольшее распространение в ИС мехатронных устройств: тензорезисторные (для измерения усилий, давлений, моментов, малых перемещений, ускорений и пр.), реостатные (для измерения усилий, давлений, перемещений, линейных и угловых скоростей и ускорений), индуктивные и индуктивно-трансформаторные (для измерения усилий, давлений, линейных перемещений), индукционные (для измерения линейных и угловых скоростей), пьезоэлектрические (для измерения вибраций, динамических усилий, давлений), емкостные (для измерения линейных и угловых перемещений, давлений, состава вещества), магнитоупругие (для измерения усилий, давлений, моментов), фотоэлектрические (для измерения линейных и угловых перемещений, линейных и угловых скоростей, положения объектов, линейных размеров и пр.) [5].
Поскольку ИС мехатронного устройства предназначена для получения и обработки информации о состоянии как самого мехатронного устройства, так и внешней среды, в состав ИС входят датчики внутренней и внешней информации.
Датчики внутренней информации служат для измерения величин, характеризующих внутреннее состояние МС, т.е. для определения положений и скоростей перемещения исполнительных органов, усилий в их звеньях, а также параметров внутренней среды, обеспечивающей нормальное функционирование устройства. Датчики внешней информации предназначены для контроля наличия, формы, положения и ориентации в пространстве объектов манипулирования, свойств внешней среды и параметров возмущений, влияющих на функционирование МС в этой среде.
По способности воспринимать информацию на различных расстояниях от ее источника средства очувствления могут быть условно разделены на бесконтактные и контактные(рис. 4.1).
Средства очувствления |
Бесконтактные |
Контактные |
Локационные системы очувствления |
Силомомент- ные системы очувствления |
Тактильные системы очувствления |
Системы технического зрения |
Рисунок 4.1. - Виды средств очувствления МС. |
Бесконтактные средства очувствления, оперирующие с геометрическими характеристиками объектов внешней среды, включают два класса устройств: системы технического зрения и локационные системы очувствления.
Средства очувствления контактного действия, которые измеряют действующие на манипулятор силы и моменты, а также фиксируют координаты точек их приложения, представлены системами силомоментного и тактильного очувствления [6]. Создание силомоментных систем вызвано необходимостью измерения сил и моментов в процессе взаимодействия схвата или инструмента с объектом манипулирования при выполнении, например, механической обработки, абразивной зачистки и шлифовки изделий. Применение силомоментных систем очувствления позволяет автоматизировать указанные технологические операции при минимуме затрат на разработку и создание дополнительного оборудования, например, конвейеров и позиционеров, обеспечивающих высокую точность начальной установки собираемых деталей. Эти же системы очувствления могут быть с успехом использованы также и для решения многих манипуляционных задач, особенно при работе с жесткими деталями, когда незначительные погрешности позиционирования могут вызвать большие усилия, которые трудно проконтролировать другими средствами.
Силомоментные системы очувствления состоят из датчика и устройства предварительной обработки информации. В общем случае они обеспечивают измерение трех проекций силы и трех проекций векторов моментов, возникающих при взаимодействии схвата или инструмента с обрабатываемой деталью. Датчики силомоментного очувствления размещают либо непосредственно на губках схвата, либо между последним звеном манипулятора и схватом.
Бесконтактные средства очувствления. Системы технического зрения (СТЗ) представляющие собой бесконтактный тип систем очувствления, находят широкое применение в промышленном производстве на операциях распознавания и сортировки деталей, разборки деталей из навала, для измерения координат движущихся деталей, подлежащих захватыванию, определения положения характерных точек в ориентации деталей на сборочных участках, контроля качества обработки или покрытия поверхностей деталей и т. п.
Локационные системы очувствления используют для измерения координат изделия в тех случаях, когда применение СТЗ нецелесообразно или невозможно. Посредством локационных датчиков обеспечивается измерение таких параметров, как расстояние до объектов, скорость движения, размеры объектов, обнаружение препятствий, а также исследование механических, электрофизических, акустических и других параметров объектов. В качестве дополнительных параметров измерения могут выступать зазоры, перекосы, проскальзывания наличие внутренних дефектов, толщина материала или покрытия, площадь, ориентация и другие. Локационные системы также применяют для простейшего распознавания деталей, имеющих различную отражательную способность, в качестве датчиков безопасности для предотвращения столкновения подвижных частей манипулятора с предметами и людьми, случайно оказавшимися в зоне обслуживания. Установка локационных датчиков на схвате манипулятора может обеспечить, например, возможность точного слежения сварочной головки за траекторией шва, а также позволяет захватывать и устанавливать изделия на подвесном или ленточном конвейерах.
Ультразвуковые локационные системы в основном они используются для определения местоположения мобильных роботов и обеспечения безопасности движения тележек внутрицехового транспорта. Работа таких систем основана на способности упругих волн высокой частоты (выше 20 кГц) распространяться в жидких, газообразных и твердых средах и отражаться от неоднородностей или границ раздела этих сред. Наиболее часто используются эхометод и метод, использующий эффект Доплера.
Эхометод основан на излучении в среду коротких акустических импульсов и приеме эхосигналов от неоднородностей среды или находящихся в ней предметов. Этот метод используется для обнаружения предметов, измерения расстояний и перемещений, его также используют в ультразвуковых системах технического зрения (например, медицинская аппаратура для ультразвукового исследования, которая позволяет видеть на экране монитора состояние внутренних органов человека) [6]. Создаваемые излучателем короткие импульсы (длительностью около 1 мс), промодулированные ультразвуковой частотой (40 кГц), посылаются в направлении исследуемого объекта. Отраженные импульсы улавливаются приемником ультразвуковых сигналов, и после преобразования в электрический сигнал и усиления обрабатываются процессором. Процессор выделяет полезный сигнал среди помех и вычисляет расстояние L до исследуемого объекта в соответствии с формулой
L=(V∙t)/2,
где V – скорость распространения звуковой волны в данной среде;
t – промежуток времени, прошедший между моментом появления переднего фронта излучаемого импульса и моментом прихода переднего фронта отраженного импульса на приемник.
В качестве излучателя и приемника обычно используется керамический пьезоэлектрический или магнитострикционный преобразователь. Чаще всего это один и тот же элемент (т. к. пьезоэлектрический и магнитострикционный эффекты являются обратимыми), поочередно подключаемый быстродействующим коммутатором в промежутках между импульсами то к каналу излучения, то к измерительному каналу. В качестве пьезоэлектрических ультразвуковых преобразователей часто используются пластины пьезокерамики ЦТС-19.
Локационные системы, использующие эффект Доплера, помимо расстояния позволяют определять также составляющую скорости VO перемещения объекта, направленную вдоль оси излучатель-объект. Напомним, что эффект Доплера заключается в изменении частоты звуковых (или электромагнитных) волн, регистрируемых приемником, в зависимости и от направления и величины взаимного перемещения объекта и приемника. При их сближении наблюдается увеличение частоты, при удалении друг от друга – уменьшение.
Акустические локационные системы обеспечивают измерение расстояний и скоростей перемещения объектов в воздухе и в воде. Такие системы используются, например, автоинспекторами для фиксации превышения скорости автомобилей, рыбопромысловыми судами для нахождения косяков рыб, подводными лодками для определения удаления, скорости и направления движения подводных объектов.
Наряду с ультразвуковыми используются и оптические локационные системы, однако из-за высокой скорости распространения оптического излучения, описанные выше методы используются главным образом для определения расстояний, превышающих несколько метров,
Рисунок 4.2. - Вихретоковый датчик проскальзывания. |
Современные тактильные датчики на интегральных схемах с применением кремния, кварца и поликристаллической керамики могут обеспечить измерения в диапазоне 0,01-40 Н (т.е. динамический диапазон составляет 4000:1). В качестве чувствительных элементов таких датчиков используется также электропроводный эластомер на основе силиконовых каучуков с наполнителем (графитом, сажей, металлическим мелкодисперсным порошком).
4.3.4. Принципы построения, параметры и особенности применения основных видов датчиков
Преобразование сил, возникающих при физическом контакте схвата с объектом, в электрический сигнал может осуществляться силомоментными датчиками двумя путями. Первый из них заключается в непосредственном измерении упругих деформаций чувствительных элементов датчиков. Наиболее часто для этого применяют тензорезисторные, пьезоэлектрические и магнитоупругие датчики. Второйспособ заключается в измерении перемещений калиброванных пружин датчика, деформируемых под действием измеряемой величины в процессе контакта схвата с объектом. При этом используют емкостные и электромагнитные (главным образом индуктивные) датчики.
Измерение упругих деформаций с помощью тензорезисторных датчиков – наиболее распространенный метод. Полупроводниковые и металлические тензорезисторы имеют широкую номенклатуру, что позволяет использовать их в тактильных и силомоментных датчиках. В основе работы тензорезисторов лежит явление тензоэффекта, заключающееся в изменении активного сопротивления проводников при их механической деформации.
В известной формуле для величины сопротивления проводника
R= (ρ·l)/S, (где ρ – удельное электрическое сопротивление материала, S – площадь поперечного сечения) при возникновении механических деформаций могут изменяться все три параметра (ρ, l и S).
Тензорезисторы представляют собой решетку из проволоки или фольги (рис. 4.3), наклеенную на специальную подложку, которая, в свою очередь наклеивается на упругий элемент, деформации в котором исследуются. Тензорезисторы имеют простую конструкцию, легко монтируются на упругих элементах тактильных или силомоментных датчиков.
Рисунок 4.3 - Различные формы тензорезисторов |
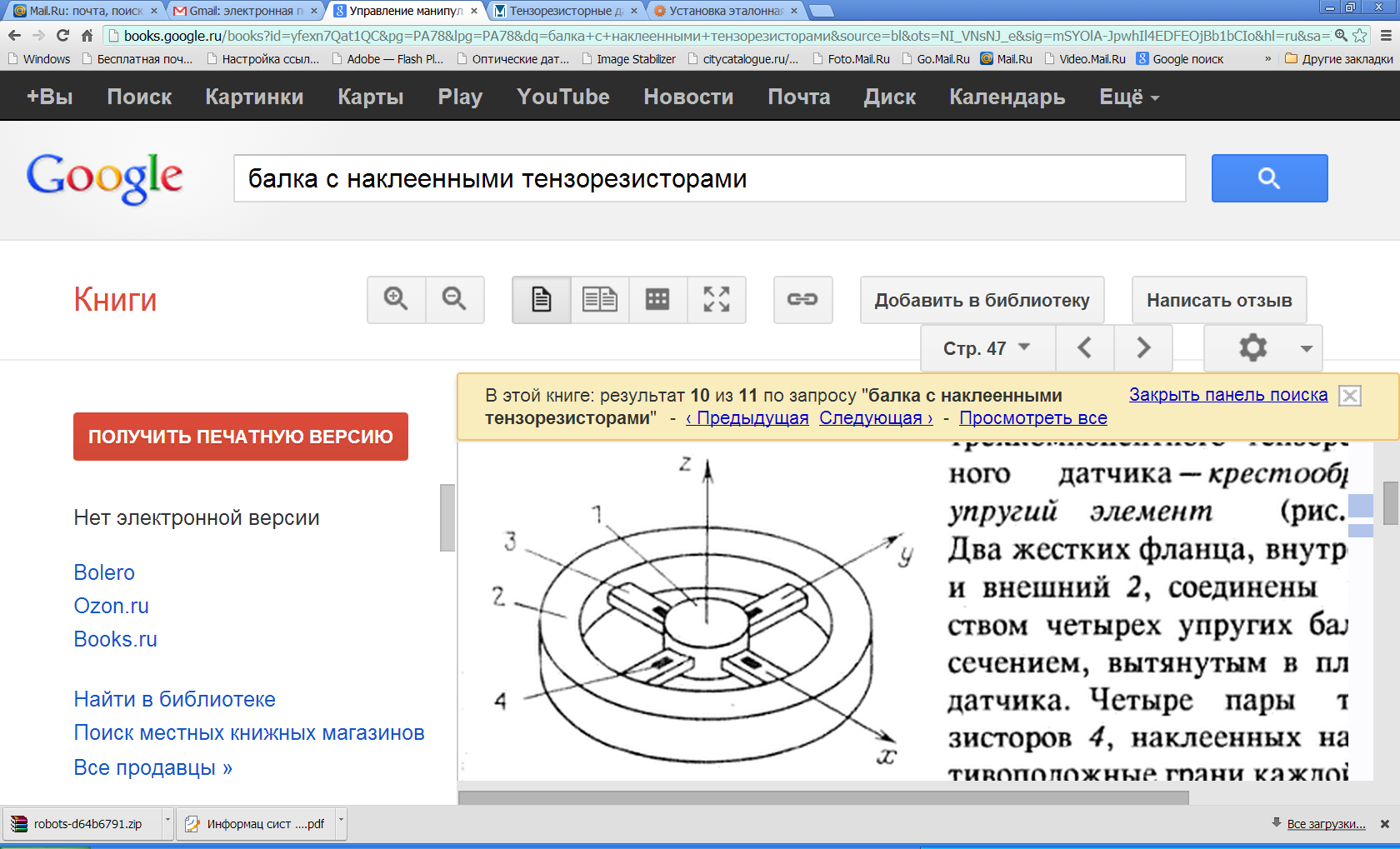
Рисунок 4.4 - Тензорезисторы на крестообразном чувствительном элементе |
Одна из наиболее распространенных и давно применяемых конструкций упругого элемента трехкомпонентного тензорезисторного датчика – крестообразный упругий элемент (рис. 4. 4). Два жестких фланца, внутренний 1 и внешний 2, соединены посредством четырех упругих балок 3. Четыре пары тензорезисторов 4, наклеенных на противоположные грани каждой балки, включены в четыре полумоста. Такой датчик чувствителен к осевому усилию Fz и двум боковым моментам Mx и My, действующим в плоскости датчика.
Рисунок 4.5 - Датчик усилия фирмы немецкой фирмы Haehne |
![]() |
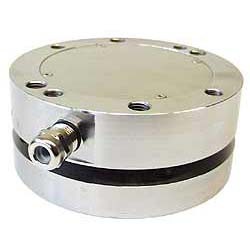
Рисунок 4.5 - Датчик усилия фирмы немецкой фирмы Haehne |
Кварцевые датчики, хотя и менее чувствительны, чем пьезокерамические, обладают высокой стабильностью свойств.
Пьезоэлектрический акселерометр ВТК 1 фирмы «Пьезо» (рис. 4.7) обладает следующими параметрами.
Таблица 4.1 - Основные параметры датчикаВТК 1
Диапазон измерения виброускорений, мс-2 | 0.5 … 1400 | |||||||
Диапазон частот, Гц | 5 … 30000 | |||||||
Максимальное значение неразрушающего удара, g | ||||||||
Диапазон рабочих температур, °C | - 60+ 250 | |||||||
Дополнительная погрешность, вызванная изменением температуры окружающей среды %/°C, не более | 0,1 | |||||||
Емкость датчика, пФ | ||||||||
Сопротивление изоляции при 20°C, Ом | 1013 | |||||||
Габаритные размеры, мм | Ø22 x 27 | |||||||
Масса датчика (без кабеля), г | ||||||||
Пьезоэлектрический материал | тип 850, APC | |||||||
Рисунок 4.7 - Пьезоэлектрический датчик ускорений |
![]() |
Рисунок 4.8 - Конструкция магнитоанизотропного датчика усилий |
Работа магнитоупругих датчиков основана на эффекте магнитоупругости, заключающемся в изменении магнитной проницаемости ферромагнитного материала под действием механических напряжений. На рис. 4.8 схематически показан наиболее распространенный вариант конструкции магнитоупругого датчика - магнитоанизотропный датчик.
В магнитопроводе из ферромагнитного материала, обладающего достаточной магнитоупругой чувствительностью, имеются 4 сквозных отверстия, через которые намотаны первичная обмотка 2, питаемая переменным током повышенной частоты, и вторичная (измерительная) обмотка 3. Плоскости обмоток образуют между собой угол 90°, а с направлением измеряемого усилия F – угол 45°. При отсутствии измеряемого усилия вектор магнитного потока, создаваемого первичной обмоткой, перпендикулярен плоскости витков вторичной обмотки, силовые линии этого потока не пересекают витков обмотки 3, поэтому наводимая в ней ЭДС равна нулю (рис. 4.9).
W1 |
W2 |
ФРАБ |
Ф0 |
ФF |
F |
Рисунок 4.9 - Поворот вектора магнитного потока при нагружении сердечника датчика измеряемым усилием F. |
Рисунок 4.10 - Магнитоупругий датчик давления: слева – чувствительный элемент датчика (магнитопровод с обмотками), справа – вторичная аппаратура и датчик в корпусе. |
В емкостных, электромагнитных (гл. образом индуктивных) и оптических датчиках часто используется предварительное преобразование измеряемой величины в перемещение калиброванной пружины.
Емкостные датчики используют зависимость емкости конденсатора от изменения его параметров под действием измеряемой величины. В качестве емкостного преобразователя широко используют плоский конденсатор, емкость которого описывается известной формулой C= ε0εS/δ,
где ε0 – диэлектрическая постоянная вакуума (8,85∙10-12 Ф/м), ε - относительная диэлектрическая проницаемость среды между обкладками конденсатора, S – площадь обкладки, δ – расстояние между обкладками.
Измеряемая неэлектрическая величина может быть функционально связана с любым из этих параметров. Например, для измерения уровня жидкостей и сыпучих тел используют цилиндрические конденсаторы (рис. 4.11), для измерения малых перемещений, изменяющихся сил и давлений – преобразователи с переменным зазором между обкладками. Внешний вид емкостного датчика давления показан на рис. 4.12.
Рисунок 4.12 - Торцевые емкостные датчики перемещений |
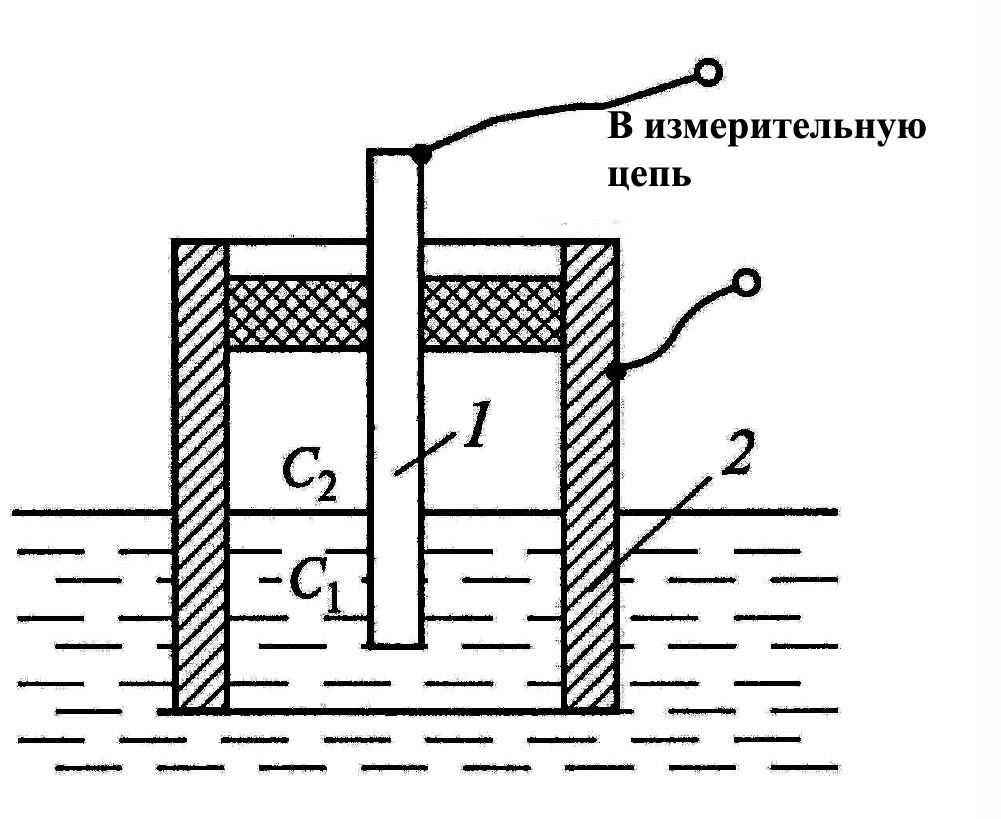
Рисунок 4.11 - Конструкция емкостного датчика уровня жидкости |
Одним из важных достоинств емкостных датчиков является возможность получения частотного выхода. При этом датчик включается в колебательный контур автогенератора, частота колебаний которого определяется изменением емкости C под воздействием измеряемой величины. Возможность частотного выхода облегчает передачу результатов измерений по линиям связи при наличии помех (поскольку частотно-модулированный сигнал наиболее устойчив к помехам).
Усилия, возникающие в месте контакта схвата с деталью, преобразованные в перемещение калиброванной пружины, могут измеряться также различного рода электромагнитными датчиками,среди которых наиболее распространены индуктивные и индуктивно-трансформаторные. Последние отличаются лишь наличием вторичной обмотки. В индуктивных датчиках перемещение ферромагнитного сердечника (якоря) вызывает соответствующее изменение индуктивности обмотки, а в индуктивно-трансформаторных - изменение взаимной индуктивности обмоток. В качестве якоря может выступать и ферромагнитная деталь, к которой прикасается схват манипулятора. Конструкции индуктивных преобразователей перемещений очень многообразны. Основными их разновидностями являются преобразователи с переменной длиной воздушного зазора, преобразователи плунжерного типа, зубчатые преобразователи и преобразователи с распределенными параметрами [9, 10].
Наиболее простую конструкцию имеет преобразователь малых перемещений с переменной длиной воздушного зазора (рис. 4.13). В индуктивном датчике при приближении подпружиненного якоря к магнитопроводу сопротивление магнитной цепи уменьшается, индуктивность обмотки w1 возрастает, ток в ней падает. В индуктивно-трансформаторном датчике в этом случае возрастает взаимная индуктивность обмоток и, соответственно, напряжение Uвых, наводимое во вторичной обмотке. Наличие обмотки w2 хотя и усложняет изготовление датчика, позволяет гальванически разделить входные и измерительные цепи. Это делает более удобной обработку выходного сигнала датчика, поэтому трансформаторные варианты электромагнитных датчиков более распространены. Индуктивные преобразователи с переменной длиной зазора обладают высокой чувствительностью к изменению измеряемой величины, незначительной чувствительностью к внешним электромагнитным полям (поскольку магнитопровод датчика почти полностью замкнут), высокой надежностью, обусловленной простотой конструкции.
Рисунок 4.13 - Индуктивно-трансформаторный датчик. |
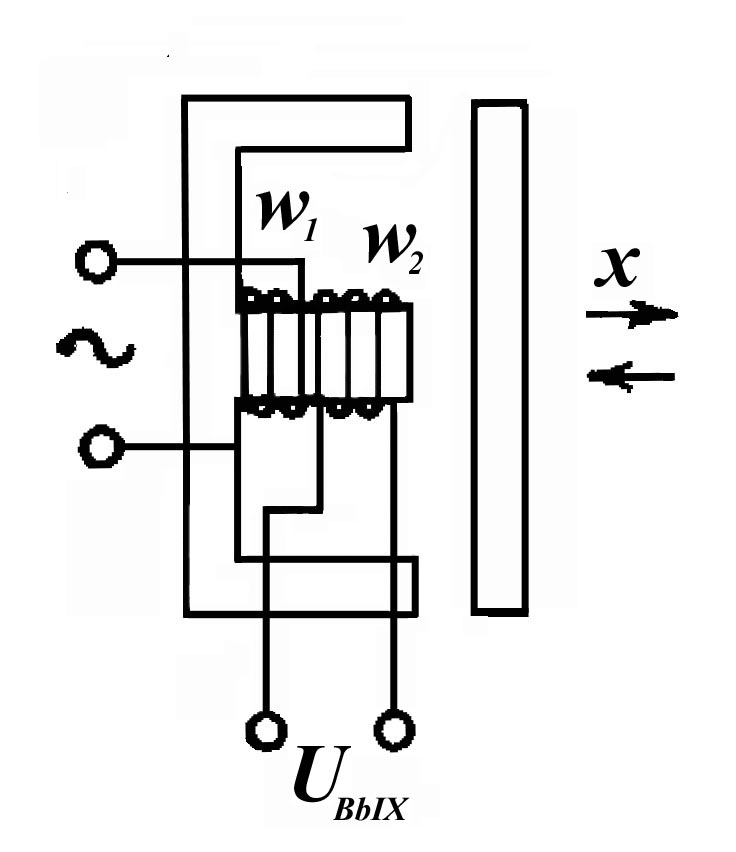
Рисунок 4.14 - Пример конструкции подшипника со встроенными датчиками. |
4.3.5. Дифференциальное включение датчиков
Улучшить метрологические характеристики датчиков позволяет использование дифференциальной схемы включения, которую рассмотрим на примере индуктивного дифференциально-трансформаторного датчика перемещений (рис. 4.15). Такой датчик состоит из двух близких по характеристикам одиночных датчиков, расположенных таким образом, что приближение якоря к магнитопроводу одного датчика вызывает удаление его от магнитопровода другого датчика. Вторичные обмотки обоих датчиков включены последовательно встречно. В исходном состоянии якорь находится на одинаковом расстоянии от обоих магнитопроводов, ЭДС вторичных обмоток обоих датчиков одинаковы
Рисунок 4.15 - Схема дифференциально-трансформаторного датчика. |
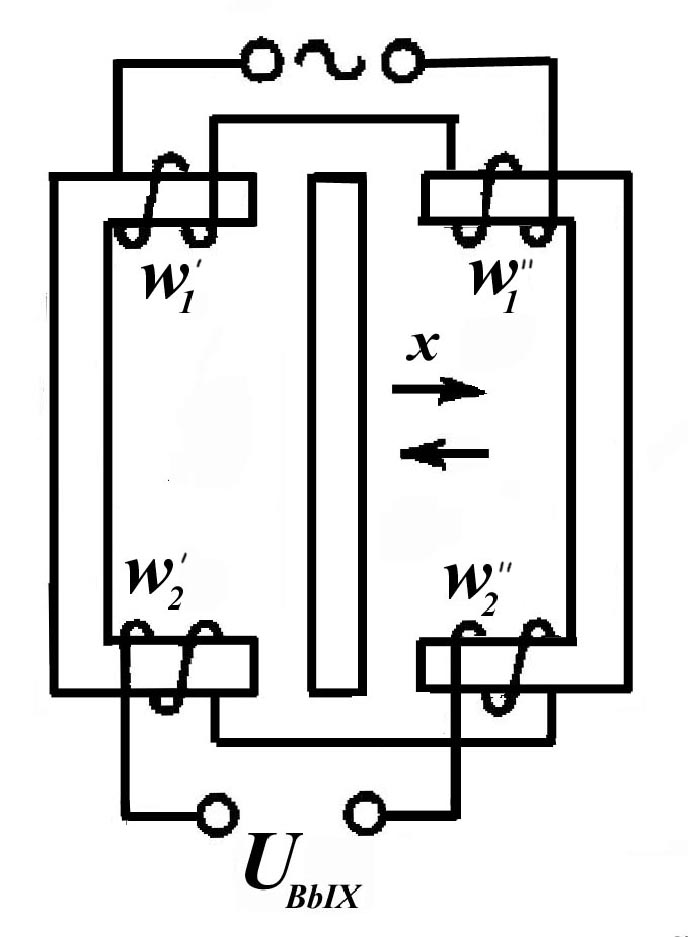
и выходное напряжение Uвых=0.
При перемещении якоря под воздействием измеряемой величины ЭДС на выходе одного датчика возрастает на величину Δеи, а другого на такую же величину падает. При встречном включении вторичных обмоток приращения ЭДС складываются, поэтому
Uвых= е0+Δеи-(е0-Δеи) = 2Δеи.
Поскольку ЭДС левой и правой вторичных обмоток находятся в противофазе, фаза выходного напряжения Uвых будет зависеть от того, в какую сторону отклонится якорь от нейтрального положения. Таким образом, абсолютная величина и фаза выходного напряжения будет определяться величиной и направлением перемещения якоря под действием измеряемой величины.
Дифференциальная конструкция обладает следующими преимуществами:
1) удвоение выходного напряжения (это следует из последней формулы);
2) компенсация дополнительных погрешностей (например, температурной ΔеД): Uвых= е0+Δеи+ΔеД -(е0-Δеи+ΔеД) = 2Δеи.
3) расширение линейного участка характеристики преобразования;
4) компенсация ненулевого начального сигнала на выходе датчика.
Эти преимущества характерны для дифференциальных конструкций датчиков всех видов (тензорезистивных, емкостных, оптических и т. д.) независимо от используемого принципа преобразования измеряемой величины в выходной электрический сигнал [1, 9].
4.3.6. Оптические датчики
В основу принципа действия оптических датчиков положена зависимость параметров потока оптического излучения от значения измеряемой величины. Оптический датчик состоит из источника излучения, оптического канала и приемника излучения (рис. 4.16). Измеряемая величина может воздействовать непосредственно на источник излучения и модулировать тот или иной параметр излучаемого им потока Ф1, либо, воздействуя на оптический канал, модулировать соответствующий параметр потока Ф1, преобразуя его в поток Ф2. Выходная величина Y формируется в результате воздействия потока Ф2 на приемник излучения.
Рисунок 4.16 - Структурная схема оптического датчика. |
Источник излучения |
Оптический канал |
Приемник излучения |
Х1 |
Ф1 |
Ф2 |
Х2 |
Y |
В оптических датчиках в качестве источника излучения наиболее часто применяются светодиоды и лазеры. При этом светодиоды применяются в датчиках со сравнительно небольшой частотой модуляции светового потока (от единиц Герц до нескольких килогерц). Лазеры допускают гораздо более высокую частоту модуляции потока и, следовательно, позволяют передавать и принимать измерительную информацию с большей скоростью [9, 10].
Лазер - источник электромагнитного излучения видимого, инфракрасного, ультрафиолетового и рентгеновского диапазонов, основанный на вынужденном излучении атомов и молекул. Важными свойствами лазерного луча являются большая мощность и высокая направленность излучения, монохроматичность, когерентность и поляризация. Эти свойства обусловили широкое распространение лазеров в качестве источников излучения в оптических датчиках, а также для передачи информации в МС по оптическим линиям связи.
Среди лазеров видимого и инфракрасного диапазонов полупроводниковые лазеры занимают особое положение по ряду своих характеристик. Размеры полупроводникового лазера могут быть сделаны очень малыми — порядка долей миллиметра. В полупроводниковых лазерах активным веществом обычно является арсенид галлия, арсенид индия, кремний с примесью индия. Основными преимуществами полупроводниковых лазеров являются малые габариты, высокий к.п.д., удобство возбуждения, высокое быстродействие, технологическая совместимость с элементами оптических интегральных схем. Общим недостатком всех полупроводниковых лазеров является сравнительно невысокая направленность излучения, связанная с их малыми размерами, и трудность получения высокой монохроматичности.
В качестве приемников оптического излучения наиболее часто используются фотодиоды. Применяются также фоторезисторы, фототранзисторы, фототиристоры. Выходной сигнал фотоприемника определяется не только интенсивностью падающего на них излучения, но и его спектральным составом. Основными характеристиками фотоприемников являются световая, спектральная, статическая вольтамперная и частотная [9].
Простейшим и самым распространенным оптическим датчиком является оптопара: светодиод, подвижная непрозрачная заслонка и фотодиод. Заслонка механически связана с подвижным звеном МС, положение которого нужно контролировать. Такой датчик может работать в дискретном режиме (открыто-закрыто) и в аналоговом (степень освещенности фотоприемника определяется положением заслонки). Конструктивно объединенные в одном корпусе и согласованные по спектральным характеристикам источник и приемник (чаще всего это светодиод и фотодиод) называют оптроном.
Применение оптических датчиков. На рис. 4.17 представлена схема фотоэлектрического датчика, который преобразует абсолютное значение угла поворота контролируемого вала в многоразрядный двоичный код.
Кодирующий диск 1 жестко закреплен на контролируемом валу 2. Диск 1 представляющий собой стеклянное основание, на котором фотоспособом нанесена кодовая маска, образованная несколькими (по количеству разрядов) концентрическими кодовыми дорожками с прозрачными и непрозрачными для света сегментами (рис. 4.18). В датчике угла поворота осветитель, состоящий из источника излучения 3 и конденсора 4, формирует световой поток, падающий на кодирующий диск 1. Луч света, проходя через прозрачные сегменты кодовых дорожек диска и щелевую диафрагму 5, освещает фотоприемники 6, усиленные сигналы с которых принимаются за двоичные единицы. Отсутствие сигналов с других фотоприемников, перекрытых непрозрачными сегментами кодовой маски, соответствует двоичным нулям. В результате каждому значению угла соответствует определенная комбинация единиц и нулей, являющаяся цифровым кодом измеряемого угла. Внешний вид таких датчиков показан на рис. 4.19.
Достоинством фотоэлектрического преобразователя угловых перемещений в код является высокая разрешающая способность, соответствующая 12-16 двоичным разрядам на один оборот вала, т. е. от 5` до 20`` [10]. Примеры промышленного применения фотоэлектрических датчиков показаны на рис. 4.20.
Рисунок 4.20 - Примеры применения оптических датчиков |
Дата добавления: 2015-08-11; просмотров: 24029;