Главные критерии работоспособности передачи.Опыт эксплуатации ременных передач показал, что их работоспособность ограничена тяговой способностью и долговечностью ремня.
Расчет ременных передач на тяговую способность основан на показателях тяговой способности и долговечности.
Для расчета используют условие работоспособности передачи в виде
(23.2)
где – удельная окружная сила, называемая полезным напряжением;
A – площадь поперечного сечения ремня (комплекта ремней);
– допускаемое полезное напряжение.
Удельная окружная сила – параметр, характеризующий тяговую способность передачи.
Расчет тяговой способности передач с нормальными и узкими клиновыми ремнями сводится к определению требуемого числа ремней по соотношению, вытекающему из условия (23.2):
где Cz – коэффициент, учитывающий неравномерность распределения нагрузки между ремнями в комплекте (технологическое ограничение), Cz = 0,85–1;
A1 – площадь сечения одного ремня.
Расчет тяговой способности плоскоременной передачи сводится к определению ширины ремня:
где Ср – коэффициент динамичности, учитывающий режим работы передачи.
h – толщина ремня.
Глава 24. ЦЕПНЫЕ ПЕРЕДАЧИ
24.1. Общие сведения. Цепи. Материалы
Цепными называют передачи с помощью цепей. Обычно передача состоит из ведущей 1 и ведомой 2 звездочек, связанных между собой приводной цепью 3 (в машиностроении применяют также грузовые и тяговые цепи) (рис. 24.1).
Рис. 24.1. Цепные контуры
Цепные передачи используют в качестве понижающих или повышающих для передачи вращения между параллельными валами. Передаваемая мощность обычно не превышает 100 кВт, межосевое расстояние до 6–8 м.
Цепные передачи в сравнении с ременными имеют значительно меньшие габариты и нагрузки на валы, более высокий КПД (η = 0,96–0,98), в них исключено окружное проскальзывание цепи по звездочке.
Недостатки передачи: «вытягивание» цепей (увеличение шага цепей вследствие износа шарниров) и, как следствие, необходимость применения натяжных устройств, необходимость ухода при эксплуатации (смазка, регулирование), шум, неравномерность хода.
Роликовая цепь состоит из последовательно чередующихся внутренних 1 и внешних 2 звеньев, которые шарнирно соединены между собой. Каждое звено выполнено из двух пластин, напрессованных на втулки 3 (у внутренних звеньев) или оси 4 (у наружных звеньев). Втулки и оси образуют шарниры, которые обеспечивают «гибкость» цепи. Для уменьшения износа зубьев звездочек на втулку перед сборкой звена надевают ролик 5, свободно вращающийся на ней (рис. 24.2).
Рис. 24.2. Роликовая цепь
Основным параметром приводных цепей является шаг t – расстояние между осями двух смежных роликов наружного или внутреннего звена, от которого зависит несущая способность цепи. Основные размеры и характеристики цепей зависят от шага.
Материалы. Пластины (2, 1 на рис. 24.2) цепей изготовляют из среднеуглеродистых и легированных сталей 45, 50, 40Х, 40ХН и др. и затем закаливают до твердости не менее 32 HRC. Оси, втулки и ролики (4, 3, 5 на рис. 24.2) обычно изготовляют из сталей 15, 15X, 20Х, 12XH3A и др., цементуют и подвергают закалке до твердости не менее 45 HRC. Звездочки тихоходных слабонагруженных передач изготовляют из чугуна СЧ 20 с закалкой или из других антифрикционных высокопрочных марок чугуна.
Звездочки быстроходных и тяжелонагруженных передач изготовляют из углеродистых легированных сталей (45, 40Х, 40ХН) или из сталей 15, 20, 12X2H4A.
Для обеспечения удовлетворительной работы цепи на средних и повышенных скоростях минимальное число зубьев ведущей звездочки ограничивают. На основании экспериментальных исследований, опыта проектирования и эксплуатации передач во многих странах принято z1min ≥ 19 при υц> 2 м/с, где υц – скорость цепи. В тихоходных передачах допускается z1min = 13–15.
24.2. Усилия в элементах передачи. Расчет передачи
Натяжение от силы тяжести
где q – масса цепи длиной 1 м;
a – межосевое расстояние;
fц – стрела провисания.
Провисание обеспечивает более плавную работу передачи и меньшее изнашивание в шарнирах цепи. Стрелу провисания ведомой ветви новой цепи на основании практического опыта назначают равной fц = 0,02а при γ ≤ 40° и (0,015–0,01)а при γ > 40°, где γ – угол наклона ветви к горизонту.
В процессе работы под нагрузкой ведущая ветвь растягивается силой
где Ft – окружная сила;
Fq – натяжение в ведомой ветви от силы тяжести;
–натяжение цепи от действия центробежных сил;
Fд –динамическая нагрузка в передаче от неравномерного хода цепи.
В расчетах цепных передач влияние Fдна работоспособность учитывают с помощью специальных коэффициентов.
Ведомая ветвь под нагрузкой растягивается силой
Окружная сила
где Р – мощность, передаваемая цепью;
d1 – диаметр делительной окружности ведущей звездочки.
Нагрузка на валы цепной передачи при средних скоростях движения цепи (υц < 15 м/с)
где k = 1,15 (для горизонтальной передачи) и 1,05 (для вертикальной).
Число зубьев z1и z2 звездочек выбирают из условия обеспечения минимальных габаритов и более плавного хода цепи.
На практике стремятся к тому, чтобы a = (30–50)t.
В основу расчета износостойкости шарниров положено условие триботехнической надежности в форме
где Pии [Pи] – соответственно расчетное и допускаемое по износостойкости давление (удельная нагрузка) в шарнире.
Расчетное давление в шарнире связано с внешней нагрузкой и геометрическими параметрами цепи очевидным соотношением, вытекающим из уравнения равновесия звена цепи:
где –номинальное давление в шарнире;
Kд – коэффициент динамичности;
Km – коэффициент, учитывающий число рядов цепи (равен 1; 1.7; 2.5; 3 соответственно для m = 1; 2; 3; 4);
Aоп – опорная поверхность шарнира.
Коэффициенты Kд и Km представляют собой ограничения эксплуатационного и конструктивного характера.
Глава 25. НЕСУЩИЕ ДЕТАЛИ И ОПОРныЕ
УСТРОЙСТВА МЕХАНИЗМОВ
25.1. Валы и оси. Классификация.
Расчет на прочность. Материалы
Для поддержания вращающихся деталей и передачи вращающего момента от одной детали к другой (в осевом направлении) в конструкциях используют прямые валы в форме тел вращения, устанавливаемые в подшипниковых опорах.
В зависимости от воспринимаемых сил различают простые валы, торсионные валы и оси.
Расчет на прочность. Этот расчет является основным для валов приводов, поэтому его выполняют в три этапа.
На первом этапе (предварительный расчет) при отсутствии данных об изгибающих моментах диаметр вала (в миллиметрах) приближенно может быть найден по известному вращающему моменту Т из условия прочности по заниженным значениям допускаемых напряжений при кручении:
где Т – вращающий момент, Н∙м;
– допускаемое напряжение на кручение (12–20 МПа для стальных валов);
Р – передаваемая мощность, кВт;
n – частота вращения вала, мин–1.
На втором этапе разрабатывают конструкцию вала, обеспечивая условия технологичности изготовления и сборки.
На третьем этапе производят проверочный расчет – оценку статической прочности и сопротивления усталости. Здесь же выполняют расчеты на жесткость, устойчивость и колебания.
На статическую прочность валы рассчитывают по наибольшей возможной кратковременной нагрузке (с учетом динамических и ударных воздействий), повторяемость которой мала и не может вызвать усталостного разрушения (например, по нагрузке в момент пуска установки). Валы могут быть нагружены постоянными напряжениями, например, от неуравновешенности вращающихся деталей.
Так как валы работают в основном в условиях изгиба и кручения, а напряжения от осевых сил малы, то эквивалентное напряжение в точке наружного волокна по энергетической теории прочности определяют по формуле
где и
– соответственно наибольшее напряжение в расчетном сечении вала от изгиба моментом Mии кручения моментом Mк.
Напряжения
где Wx и Wp – соответственно осевой и полярный момента сопротивления сечения вала.
Моменты сопротивления сечений валов
Форма сечения | Эскиз | Момент сопротивления |
Круглое | ![]() | ![]() |
Форма сечения | Эскиз | Момент сопротивления |
Кольцевое | ![]() | ![]() |
Co шпоночной канавкой | ![]() | ![]() |
Co шлицами | ![]() | ![]() |
Так как , то можно записать
где d – диаметр вала.
Обычно крутящий момент Mz (внутренний силовой фактор) в расчетном сечении вала равен вращающему моменту T (внешней нагрузке на вал).
Запас прочности по пределу текучести
Обычно принимают =1,2–1,8.
Сечение (сечения), в котором следует определить запас nт, находят после построения эпюр изгибающих и крутящих моментов. Если нагрузки действуют на вал в разных плоскостях, то сначала силы проецируют на координатные оси и строят эпюры моментов в координатных плоскостях. Далее производят геометрическое суммирование изгибающих моментов.
Если угол между плоскостями действия сил не более 30º, то для простоты считают, что все силы действуют в одной плоскости.
Технические условия на изготовление валов зависят от требований к конструкции. Обработку валов обычно производят в центрах.
Наиболее жесткие требования по точности и шероховатости поверхности предъявляются к шейкам валов, на которые устанавливают подшипники качения. Шероховатость Ra шеек назначают равной 0,32–1,25 мкм. Овальность и конусность мест посадки определяются допуском на диаметр шейки.
Для изготовления валов используют углеродистые стали марок 20, 30, 40, 45 и 50, легированные стали марок 20Х, 40Х, 40ХН, 18X2H4A, 40XH2MA и др., титановые сплавы BT3-1, ВТ6 и ВТ9.
Выбор материала, термической и химико-термической обработки определяется конструкцией вала и опор, условиями эксплуатации. Так, например, быстроходные валы, вращающиеся в подшипниках скольжения, требуют высокой твердости цапф (посадочных хвостовиков валов), поэтому такие валы изготовляют из цементуемых сталей 12X2H4A, 18ХГТ или азотируемых сталей 38Х2МЮА и др. Валы-шестерни по этой же причине выполняют из цементуемых сталей 12XH3A, 12X2H4A и т. п. Валы под насадные зубчатые колеса серийных редукторов изготовляют из улучшенной стали 45 (255–285 НВ) и 40Х (269–302 НВ). Участки валов, контактирующие с уплотнительными манжетами, должны иметь твердость поверхности не менее 30 HRC.
Длинные полые валы иногда выполняют (намоткой) из композиционных материалов.
25.2. Опоры валов и осей. Классификация подшипников
Подшипники бывают:
– скольжения;
– качения.
Подшипник скольжения является парой вращения, он состоит из опорного участка вала (цапфы) 1 и соответственно подшипника 2, в котором скользит цапфа (рис. 25.1).
Рис. 25.1. Подшипник скольжения
Подшипники качения являются основным видом опор вращающихся (качающихся) деталей. Подшипник состоит из наружного 1 и внутреннего 2 колец, между которыми расположены тела качения 3. Для предохранения тел качения от соприкосновения между собой их отделяют друг от друга сепаратором 4, который существенно уменьшает потери на трение (рис. 25.2).
Подшипники качения стандартизованы, их изготовляют подшипниковые заводы в условиях высокоспециализированного массового производства. Поэтому инженеру приходится проектировать подшипники качения крайне редко. Гораздо чаще требуется подобрать подшипник для узла опоры, спроектировать корпус опоры, обеспечивая технологичность, контроле- и ремонтопригодность узла, а также оценить остаточную долговечность подшипника при модернизации или форсировании режима работы оборудования.
Классификация. Подшипники качения классифицируют по нижеперечисленным признакам.
I. По форме тел качения подразделяют:
– на шариковые;
– роликовые с короткими цилиндрическими, коническими, бочкообразными, игольчатыми и витыми роликами (рис. 25.3).
II. По направлению воспринимаемых относительно оси вала сил разделяют на типы:
– радиальные (см. рис. 25.2, а, 25.3, а), воспринимающие преимущественно радиальные нагрузки, действующие перпендикулярно оси вращения подшипника;
– радиально-упорные (см. рис. 25.2, б, 25.3, б), воспринимающие одновременно действующие радиальные и осевые нагрузки;
– упорно-радиальные, воспринимающие осевые нагрузки при одновременном действии незначительной радиальной нагрузки;
– упорные, воспринимающие только осевые силы.
|
|
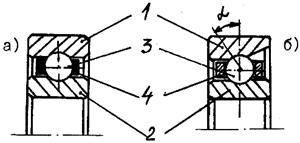
Рис. 25.2. Шарикоподшипники
|
|
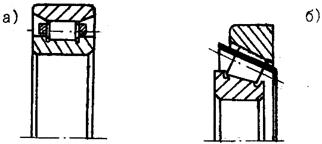
Рис. 25.3. Роликоподшипники
III. По способности самоустановки подшипники подразделяют на несамоустанавливающиеся и самоустанавливающиеся, допускающие поворот оси внутреннего кольца по отношению к оси наружного кольца.
IV. По числу рядов тел качения, расположенных по ширине,
подшипники делят наоднородные (см. рис. 25.2, 25.3), двухрядные,четырехрядные и многорядные.
Основными потребительскими (внешними) характеристиками подшипников являются грузоподъемность, быстроходность, масса, габариты, потери энергии.
Подшипники одного и того же диаметра отверстия по наружному диаметру и ширине подразделяют на серии: сверхлегкую, особо легкую, легкую, легкую широкую, среднюю, среднюю широкую и тяжелую (рис. 25.4).
Рис. 25.4. Сравнительные параметры радиальных шарикоподшипников
и радиально-упорных роликоподшипников различных серий
при одинаковом диаметре отверстия d = 80 мм:
1 – масса m; 2 – динамическая грузоподъемность C;
3 – предельная частота вращения n
Для особо высокой частоты вращения и легких нагрузок целесообразно использовать подшипники сверхлегкой и особо легкой серий. Для восприятия повышенных и тяжелых нагрузок при высокой частоте вращения используют подшипники легкой серии, а при недостаточной их грузоподъемности в одной опоре размещают по два подшипника.
Кроме стандартных подшипников по специальному обоснованию изготовляют особые подшипники.
Достоинства и недостатки подшипников. Подшипники качения имеют ряд достоинств по сравнению с подшипниками скольжения:
– меньшие (в два-три раза) осевые размеры;
– меньшее трение и сопротивление пуску под нагрузкой и вращению при небольших и средних частотах вращения, постоянство сопротивления вращению;
– простоту технического обслуживания и подачи смазочного материала;
– низкую стоимость и взаимозаменяемость.
Недостатки подшипников качения по сравнению с подшипниками скольжения следующие: большие радиальные размеры; малая радиальная жесткость и, как следствие, склонность к возникновению колебаний вала из-за ритмичного прокатывания через нагруженную зону опоры; более сложный монтаж; большее сопротивление вращению (из-за трения между телами качения, кольцами, сепаратором и гидравлических потерь) при высоких частотах вращения и, как следствие, низкая долговечность (из-за перегрева).
Промышленность изготовляет подшипники качения пяти классов точности: 0, 6; 5; 4 и 2. Обозначения даны в порядке повышения точности, определяемой допусками на изготовление элементов, а также нормами плавности вращения (хода).
Основные размеры подшипников установлены ГОСТ 3478–79 (СТ СЭВ 402–76). В них входят: внутренний d и наружный D диаметры, ширина B (высота Н) и радиус r фасок колец.
Материалы деталей подшипников. Кольца и тела качения подшипников изготовляют в основном из шарикоподшипниковых высокоуглеродистых хромистых сталей ШХ15 и ШХ15СГ, ШХ20СГ, а также цементуемых легированных сталей 18ХГТ, 20Х2Н4А и др. При рабочей температуре до 100 °С тела качения и кольца обычно имеют твердость 60–64 HRC, шарики – 62–65 HRC.
Кольца и тела качения подшипников, работающих при повышенных температурах (до 500 °С), в агрессивных средах, изготовляют из жаропрочных и коррозионно-стойких сталей.
Сепараторы подшипников подвержены интенсивному изнашиванию из-за трения скольжения с телами качения и кольцами, поэтому сепараторы изготовляют из антифрикционных материалов. Сепараторы массовых подшипников изготовляют штамповкой из мягкой углеродистой стали, обладающей неплохими антифрикционными свойствами. Сепараторы высокоскоростных подшипников выполняют массивными из текстолита, фторопласта, дуралюмина, латуни и бронзы (материалы перечислены в порядке увеличения быстроходности подшипника).
Основные типы подшипников и их характеристики приведены в справочниках.
25.3. Динамическая грузоподъемность подшипников качения. Выбор подшипников и определение их ресурса
Динамическая грузоподъемность подшипников. Расчет удобнее выполнять по действующей нагрузке R:
где L – номинальная долговечность подшипника, млн оборотов;
С – динамическая грузоподъемность, Н;
R – эквивалентная нагрузка, Н;
q – показатель степени кривой усталости подшипника;
– расчетная долговечность подшипника, млн оборотов;
n – частота вращения кольца, мин–1;
Lh – расчетная долговечность подшипника, ч.
Под динамической грузоподъемностью Срадиальных и радиально-упорных подшипников понимают (по договоренности) постоянную радиальную нагрузку (в ньютонах), которую подшипник с неподвижным наружным кольцом может воспринимать в течение номинальной долговечности в 1 млн оборотов. Динамическая грузоподъемность упорных и упорно-радиальных подшипников – постоянная центральная осевая нагрузка (в ньютонах), которую подшипник может воспринимать в течение номинальной долговечности в 1 млн оборотов одного из колец.
Принимают q = 3 (m = 9) для шарикоподшипников и q = 3,33 (m = 6,66) для роликоподшипников.
Эквивалентную нагрузку для подбора подшипников определяют с учетом особенности их работы в эксплуатационных условиях:
где x – коэффициент радиальной нагрузки;
V – коэффициент вращения (V = 1 при вращении внутреннего кольца, V = 1,2 при вращении наружного кольца);
Fr – радиальная сила;
y – коэффициент осевой нагрузки;
Fа – осевая сила;
Kб – коэффициент безопасности, учитывающий влияние на долговечность подшипников характера внешних нагрузок;
Kт – температурный коэффициент.
Выбор подшипников и определение их ресурса.Выбор подшипников качения производят по приведенной нагрузке R и расчетному ресурсу L (в млн оборотов) по формуле
Используя полученное расчетное значение динамической грузоподъемности, по справочнику или каталогу выбирают подшипник; при этом должно быть соблюдено условие (С – динамическая грузоподъемность подшипника по каталогу).
Если подшипник принят по конструктивным соображениям, то расчетом проверяют его ресурс:
1 с–1 ( ) ≈ 10 мин–1 (n).
25.4. Муфты механических приводов.
Общие сведения и классификация
Муфтами называют устройства, предназначенные для передачи вращения между валами совместно работающих узлов (агрегатов) машин, между частями составных валов (в валопроводах, трансмиссиях), атакже для соединения валов с расположенными на них деталями (зубчатыми колесами, звездочками и т. д.).
Муфты бывают:
– общего назначения.
– управляемые;
– предохранительные.
1. Простейшую конструкцию имеют втулочные муфты (рис. 25.5, а, б), применяемые для соединения валов диаметрами до 60–70 мм(здесь рассматриваются лишь приводные механические муфты). В качестве муфт используют также торсионы со шлицевыми хвостовиками, входящими в шлицевые отверстия в хвостовиках соединяемых валов. Для облегчения монтажа приводов муфты выполняют обычно сборными, состоящими из полумуфт, которые соединяют после установки узлов на раме (станине и т. п.) с помощью болтов (рис. 25.5, в) и другими способами. Широко распространены муфты в виде автономных устройств (узлов), изготовляемых на специализированных предприятиях (производствах). Это упрощает стандартизацию муфт. Для фиксирования их на хвостовиках соединяемых валов обычно используют шпоночные и шлицевые соединения (муфты общего назначения).
|
|
|
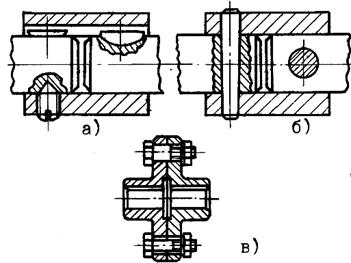
Рис. 25.5. Глухие муфты
2. Управляют работой (включают и выключают исполнительный механизм при работающем двигателе, облегчают пуск машины и др.) управляемые муфты.
3. Регулируют параметры (ограничивают частоты вращения (максимальную и минимальную), предохраняют детали и машины от случайных (недопустимых) перегрузок) предохранительные муфты.
Основной нагрузкой для муфт является вращающий момент. В связи с этим их нагрузочную способность принято оценивать допустимым вращающим моментом Tn, значения которого вместе с размерами, массой и другими данными указывают в паспортах муфт.
Наибольший длительно действующий момент Tдлдля муфт может быть определен теоретически или экспериментально. В упрощенном расчете, используя опыт проектирования и эксплуатации машин, принимают
где – коэффициент режима работы;
Kб= 1,0–1,8 – коэффициент безопасности, учитывающий характер последствий при выходе муфты из строя;
Kд = 1,0–1,5 – коэффициент, учитывающий характер передаваемой нагрузки (меньшие значения принимают при спокойной нагрузке, большие – при ударной и реверсивной).
Муфты разнообразны по конструкции. Наиболее распространенные из них стандартизованы и рассмотрены ниже. Выбор типа муфт производят в соответствии с конструктивными особенностями и требованиями, предъявляемыми к приводу (машине) в целом.
25.5. Муфты общего назначения. Особенности расчета
Муфты общего назначения:
– глухие;
– упругие;
– компенсирующие.
Глухими называют муфты, образующие жесткое соединение валов (составной вал). К их числу относят втулочные и фланцевые муфты(см. рис. 25.5), которые компенсируют радиальные смещения осей валов до 5 мкм для исключения чрезмерных дополнительных сил.
Несущая способность втулочных муфт обычно ограничена прочностью соединений (шпоночных, штифтовых, болтовых).
Для передачи больших вращающих моментов применяют фланцевые муфты, у которых полумуфты снабжены торцовыми зубьями. Такие муфты соединяют с валами с помощью сварки или эвольвентных шлицевых соединений.
Упругие муфты за счет использования своих упругих силовых элементов способны не только компенсировать радиальные и угловые смещения, но и демпфировать колебания, амортизировать толчки и удары.
Упругие втулочно-пальцевые муфты типа МУВП по ГОСТ 21424–75 применяют в приводе от электродвигателя и в других случаях для валов диаметрами 9–160 мм при вращающих моментах 6,3–16000 Н∙м. Стандартом предусмотрены муфты типа I (с цилиндрическим отверстием для валов) и типа II (с коническим отверстием для валов); они могут быть выполнены в двух исполнениях: для длинных и коротких концов валов. Вращающий момент между полумуфтами передается через резиновые гофрированные втулки 1, надетые на пальцы 2. Муфты, в зависимости от типоразмера, допускают радиальное смещение осей валов на 0,2–0,4 мм, продольное смещение валов на 10–15 мм и угловое смещение на 1º. Их работоспособность определяется стойкостью втулок. Диапазон рабочих температур – от минус 40 до плюс 50 °С.
Для ограничения износа среднее контактное давление пальца на втулку
где z = 6 – число пальцев;
Dm – диаметр окружности расположения осей пальцев;
dп – диаметр пальцев;
l – длина упругого элемента;
[P] – допускаемое давление для резиновых втулок (обычно 2 МПа).
25.6. Предохранительные муфты
Включение и выключение предохранительных муфт обычно происходит автоматически, поэтому иногда их называют самодействующими или самоуправляющимися.
Основные требования к таким муфтам – точность срабатывания, быстродействие, надежность.
Предохранительные муфты служат для защиты механизмов, машин от перегрузок. Они срабатывают, если вращающий момент на ведомом валу механизма превышает некоторую предельную величину.
Предохранительные муфты бывают двух типов.
1. Фрикционные предохранительные муфты.
2. Предохранительные муфты с разрушающимся элементом – штифтом (рис. 25.6). Они просты и надежны в работе, обладают сравнительно высокой точностью срабатывания. Штифты изготовляют из хрупких материалов (высокоуглеродистой стали, чугуна, бронзы и др.), чтобы повысить быстродействие, и размещают в закаленных до высокой твердости втулках из сталей 40Х, У8А, У10А и др.
Рис. 25.6. Предохранительная муфта
с разрушающимся элементом
Для обеспечения чистого среза штифтов торцы втулок в собранной муфте должны соприкасаться друг с другом.
После разрушения штифта (штифтов) от перегрузки муфта разъединяет кинематическую цепь и полумуфты вращаются относительно друг друга.
Диаметр штифта
где R1 – радиус муфты до оси срезного штифта;
z – число штифтов (обычно z = 1–2);
– предел прочности штифта на срез.
Для закаленных штифтов из стали 45 и Ст 5 =420 Н/мм2.
Глава 26. СОЕДИНЕНИЯ ДЕТАЛЕЙ И УЗлОВ МАШИН
Неразъемные соединения бывают сварные, паяные, клеевые, заклепочные, с натягом.
26.1. Сварные соединения. Общие сведения
и характеристика. Изображения и обозначения
на чертежах швов сварных соединений
Соединение деталей сваркой широко применяется в технике. При помощи сварки соединяются детали машин, механизмов, металлоконструкций, мостов, гражданских и промышленных зданий и т. п.
Сварное соединение может быть выполнено в основном двумя способами: сваркой плавлением и сваркой давлением.
При сварке плавлением поверхности кромок свариваемых деталей плавятся и после остывания образуют прочный сварной шов. Чаще всего сварка плавлением осуществляется газовой или дуговой (электродуговой) сваркой (рис. 26.1).
При газовой сварке горючий газ (например, ацетилен), сгорая в атмосфере кислорода, образует пламя, используемое для плавления. В зону плавления вводится прутковый присадочный материал, в результате плавления которого образуется сварной шов.
Сварка давлением осуществляется при совместной пластической деформации предварительно нагретых поверхностей свариваемых деталей. Эта деформация происходит за счет воздействия внешней силы. Сварка давлением осуществляется, как правило, одним из видов контактной электросварки: точечной (рис. 26.2, а), шовной-роликовой (рис. 26.2 и) и др.
|
|
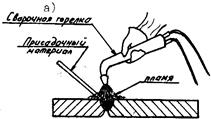
|

Рис. 26.1. Выполнение сварных соединений
|
|
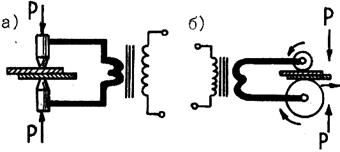
Рис. 26.2. Схемы сварки давлением
Помимо упомянутых способов в современной технике применяются и многие другие способы сварки: электрошлаковая, в защитных газах, ультразвуковая, лазером, индукционная и др.
ГОСТ 2.312–72 устанавливает условные изображения и обозначения на чертежах швов сварных соединений. Штриховка изображения сечений свариваемых деталей выполняется в разные стороны.
Сварные швы делятся на однопроходные и многопроходные в зависимости от числа проходов сварочной дуги.
Независимо от способа сварки видимый шов условно изображается сплошной основной линией, а невидимый – штриховой. От изображения шва проводят линию-выноску, заканчивающуюся односторонней стрелкой (рис. 26.3).
Рис. 26.3. Изображение сварных швов на чертежах
ГОСТ 2.312–72 устанавливает вспомогательные знаки, входящие в обозначение шва и характеризующие его.
1. Знак, проставляемый перед размером катета | ![]() |
2. Шов прерывистый с цепным расположением. Угол наклона линии около 60º | ![]() |
3. Шов прерывистый с шахматным расположением | ![]() |
4. Шов по незамкнутой линии. Знак применяют, если расположение шва неясно из чертежа | ![]() |
5. Шов по замкнутой линии. Диаметр знака 3–5 мм | ![]() |
6. Шов выполнить при монтаже изделия, т. е. при установке его по монтажному чертежу на месте применения | ![]() |
Знаки выполняются сплошными тонкими линиями.
Знаки (за исключением знака 5) должны быть одинаковой высоты с цифрами, входящими в обозначение шва.
Рис. 26.4. Структура условного обозначения стандартного шва
Структура условного обозначения стандартного сварного шва приведена на схеме (рис. 26.4). На схеме применены следующие обозначения:
1) обозначение стандарта на типы и конструктивные элементы швов сварных соединений;
2) буквенно-цифровое обозначение шва по предыдущему стандарту;
3) условное обозначение способа сварки по этому же стандарту (допускается не указывать);
4) для швов, тип которых характеризуется катетом шва, проставляют:
а) знак 1;
б) размер катета в миллиметрах;
5) для прерывистого шва проставляют (рис. 26.5):
а) размер длины элемента провариваемого участка l, мм;
б) знак 2 или 3;
в) размер шага t, мм;
6) знак 4.
В сварочном производстве применяются стандартные сварные швы, параметры которых определяются соответствующими стандартами.
Типы швов определяет ГОСТ 5264–80. Сварные соединения из алюминия и алюминиевых сплавов выполняются швами по ГОСТ 14806–69. ГОСТ 16310–70 предусматривает типы швов для сварки изделий из винипласта и полиэтилена. Кроме того, существует еще ряд стандартов (ГОСТ 11533–75; ГОСТ 15164–78; ГОСТ 14776–69; ГОСТ 15878–70 и т. д.), определяющих типы и конструктивные элементы швов иных сварных соединений, а также способы их сварки.
|
|
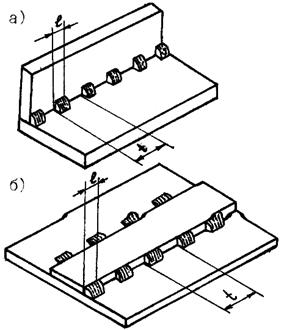
Рис. 26.5. Прерывистые сварные швы
Каждый стандартный шов имеет буквенно-цифровое обозначение, полностью определяющее конструктивные элементы шва. Буквенная часть обозначения определяется видом сварного соединения.
1. Стыковое соединение (С) – свариваемые детали соединяются по своим торцовым поверхностям.
2. Угловое соединение (У) – свариваемые детали расположены под углом и соединяются по кромкам.
3. Тавровое соединение (Т) – торец одной детали соединяется с боковой поверхностью другой детали.
4. Соединение внахлестку (Н) – поверхности соединяемых деталей частично перекрывают друг друга.
Между кромками свариваемых деталей предусматривается зазор величиной 0–5 мм. В зависимости от требований, предъявляемых к сварному соединению, кромки свариваемых деталей подготавливаются по-разному. Сварка может выполняться во всех четырех видах сварного соединения без скоса кромок и со скосом одной или двух кромок. Скосы могут быть симметричными и несимметричными, прямолинейными и криволинейными.
Совокупность всех конструктивных особенностей стандартного шва обозначается цифрой, которая совместно с буквенным обозначением вида сварного соединения определяет буквенно-цифровое обозначение типа шва по соответствующему стандарту, например: C1, C2, С3, ..., У1, У2, У3,..., T1, Т2, Т3,..., H1, H2,... и т. п.
По способу осуществления механизации технологического процесса различают ручную, полуавтоматическую и автоматическую сварку. Соответствующие стандарты (ГОСТ 2.312–72, ЕСКД) устанавливают условные обозначения способов сварки. Например:
П – полуавтоматическая сварка под флюсом;
А – автоматическая сварка под флюсом;
П3 – полуавтоматическая сварка плавящимся электродом в защитных газах;
АН3 – автоматическая сварка неплавящимся электродом в защитных газах;
А3 – автоматическая сварка плавящимся электродом в защитных газах и др.
Швы сварных соединений могут выполняться усиленными (рис. 26.6). Усиление (выпуклость) шва определяется величиной q. Некоторые типы швов (отдельные швы тавровых, нахлесточных и угловых соединений) характеризуются величиной К (рис. 26.6, а), называемой катетом шва.
Условное обозначение шва, изображенного на рис. 26.7, расшифровывается следующем образом:
1) – шов выполняется при монтаже изделия;
2) ГОСТ 5264–80 – шов для сварки деталей из углеродистой стали ручной дуговой сваркой (в условном обозначении шва способ сварки не указан);
3) C18 – стыковой двусторонний шов со скосом двух кромок. Размеры скоса кромок приведены в ГОСТ 5264–80, который устанавливает форму кромок;
4) знаки 4 указывают, что усиление снято с обеих сторон;
5) шероховатость поверхности шва: с лицевой стороны – Rz20, с обратной стороны – Rz80.
а б
Рис. 26.6. Усиленные сварные швы
Рис. 26.7. Стыковые сварные соединения
Рис. 26.8. Тавровое сварное соединение
На рис. 26.8 представлен сварной шов, характеризуемый следующими данными:
1) – шов выполнен по замкнутой линии;
2) ГОСТ 14806-80 – шов для сварки алюминия;
3) Т5 – тавровый двусторонний шахматный шов без скоса кромок (любая сторона принимается за лицевую);
4) РН3 – ручная сварка неплавящимся электродом в защитных газах (допускается не указывать);
5) 6 – катет шва 6 мм;
6) длина провариваемого участка l 50 мм;
7) шаг t 100 мм.
Диаметр сварной точки устанавливают в зависимости от толщины S свариваемых деталей: d = 1,2S + 4 мм. Рекомендуемое расстояние между точками a = 3d при сварке двух элементов и a = 4d при сварке трех элементов.
26.2. Расчет на прочность и проектирование
сварных соединений при постоянных нагрузках
Расчет и проектирование сварных соединений (конструкций) сводится к выбору вида соединения, способа сварки, марки электрода, рациональному размещению сварных швов, определению сечения и длины швов из условия равнопрочности наплавленного металла и материала соединяемых деталей. Размеры соединяемых деталей обычно известны заранее из условий прочности, жесткости, устойчивости или конструктивных соображений.
Сварные швы бывают:
1) стыковые;
2) лобовые;
3) фланговые (угловые);
4) комбинированные.
Стыковые швы рассчитывают на прочность по номинальному сечению соединяемых деталей (без учета утолщения швов) как целые детали. От внешней растягивающей силы F в сечении шва возникают напряжения растяжения
(26.1)
где l и S – соответственно длина шва и толщина соединяемых деталей.
Условие прочностной надежности
(26.2)
В расчетах принимают = (0,9–1,0)
, где
–допускаемое напряжение при растяжении основного материала.
Допустима растягивающая сила при обращении неравенства (26.2) в равенство
Нормальные напряжения в швепри совместном действии внешней силы F и изгибающего момента М (рис. 26.9)
(26.3)
где M – момент сопротивления сечения шва (детали) при изгибе.
Лобовые и фланговые (угловые) швы разрушаются по сечению, проходящему через биссектрису прямого угла (рис. 26.10).
Рис. 26.9. К расчету сварного соединения встык
Рис. 26.10. К расчету лобовых и фланговых сварных швов
Площадь расчетного сечения
где L – общая длина (периметр) сварного шва;
Kp – расчетный катет шва.
Угловой шов при нагружении испытывает сложное напряженное состояние. Однако в упрощенном расчете такой шов условно рассчитывают на срез.
Условие прочности шва по допускаемым напряжениям:
где – номинальное напряжение среза;
– допускаемое напряжение в сварном шве при срезе.
В расчетах принимают
Kp = (0,9–1,2) · Smin,
где Smin – наименьшая толщина свариваемого элемента Kpmin > 3 мм при S > 3 мм.
l ≥ 30 мм; la ≥ 30 мм; lφ ≤ 50K.
Дата добавления: 2015-06-17; просмотров: 1406;