Расчеты на жесткость при изгибе
В ряде случаев работающие на изгиб элементы машиностроительных и строительных конструкций должны быть рассчитаны не только на прочность, но и на жесткость. К деталям, рассчитываемым на жесткость, относятся, в частности, валы зубчатых и червячных передач и многие части металлорежущих станков.
Расчет на жесткость элемента конструкции, имеющего форму бруса, заключается в определении наибольших перемещений его поперечных сечений и сопоставлении их с допускаемыми, зависящими от назначения и условий эксплуатации данного элемента.
Рассмотрим простую консоль, нагруженную на свободном конце силой F, линия действия которой совпадает с одной из главных осей поперечного сечения балки (рис. 19.10).
Рис. 19.10. Линейное и угловое перемещения сечения при изгибе
При деформации балки центры тяжести ее поперечных сечений получают линейные перемещения, а сами сечения поворачиваются вокруг своих нейтральных осей. Допущение о малости перемещений позволяет считать, что направления линейных перемещений перпендикулярны продольной оси недеформированного бруса. Эти перемещения принято называть прогибами. Прогиб произвольного сечения обозначим ν, а наибольший прогиб – стрелу прогиба – f. Геометрическое место центров тяжести поперечных сечений деформированного бруса, т. е. ось изогнутого бруса, условно называют изогнутой осью, или, чаще, упругой линией.
Угол поворота θ поперечного сечения равен углу между касательной к упругой линии в данной точке и осью недеформированного бруса.
Вывод: ордината упругой линии и угол наклона касательной, проведенной к ней в данной точке, полностью определяют линейное и угловое перемещения соответствующего поперечного сечения балки.
В большинстве случаев условие жесткости выражается неравенством
т. е. максимальный прогиб (стрела прогиба f) не должен превышать допускаемого . Значение допускаемого прогиба зависит от назначения и условий работы рассчитываемой конструкции и колеблется в широких пределах. Обычно допускаемую стрелу прогиба указывают в долях пролета (межопорного расстояния l) балки. Например, для ручных грузоподъемных кранов
, для электрических
, для валов и шпинделей металлорежущих станков
= (0,0005–0,0010) l.
Для обеспечения нормальной работы подшипников скольжения и роликовых подшипников качения иногда ставится дополнительное условие жесткости – ограничение угла поворота опорных сечений:
При этом допускаемый угол поворота составляет в среднем 0,001 радиан.
19.6. Кручение вала (стержня) круглого поперечного сечения
Кручение– это такой вид деформации бруса, при котором в его поперечных сечениях возникает единственный внутренний силовой фактор – крутящий момент, обозначаемый Mz или Tk.
На рис. 19.11 изображен брус, работающий на кручение под действием приложенных к нему скручивающих моментов (M1, M2, M3, М4).
Во всех случаях будем считать, что алгебраическая сумма скручивающих моментов равна нулю, т. е. брус находится в равновесии.
Применяя метод сечений и рассматривая равновесие оставленной части (рис. 19.12), приходим к выводу, что внутренние силы, возникающие в поперечном сечении бруса, должны дать момент (крутящий момент), уравновешивающий внешние моменты, приложенные к оставленной части.
![]() | ![]() |
Рис. 19.11. Крутящие моменты вала | Рис. 19.12. Кручение вала |
Итак, крутящий момент, возникающий в произвольном поперечном сечении бруса, численно равен алгебраической сумме скручивающих моментов, приложенных к оставленной части.
При кручении бруса в его поперечных сечениях возникают только касательные напряжения.
Для расчета на прочность, так жекак и при растяжении (сжатии) бруса, надо найти его опасное сечение. В случае, если размеры поперечного сечения по длине бруса постоянны, опасными будут сечения, в которых крутящий момент максимален. График, показывающий закон изменения крутящих моментов по длине бруса, называется эпюрой крутящих моментов (см. рис. 19.12).
Правило знаков: будем считать крутящий момент положительным, если для наблюдателя, смотрящего на проведенное сечение, он представляется направленным по часовой стрелке (рис. 19.13). Соответствующий внешний момент направлен против часовой стрелки.
Рис. 19.13. Правило знаков для Mz
19.7. Расчеты на прочность и жесткость при кручении
Прочность бруса, работающего на кручение, считают обеспеченной, если наибольшие касательные напряжения, возникающие в его опасном сечении, не превышают допускаемых:
Конечно, незначительное (до 5–6 %) превышение расчетного напряжения над допускаемым не опасно.
Эпюры касательных напряжений для круглого сплошного и кольцевого поперечных сечений показаны на рис. 19.14.
Рис. 19.14. Эпюры касательных напряжений поперечных сечений вала
В точках, равноудаленных от центра сечения, напряжения одинаковы.
Наибольшего значения касательные напряжения достигают в точках контура поперечного сечения:
где – полярный момент инерции.
Введя обозначение , получим следующее выражение для максимального касательного напряжения:
Величину , мм3, равную отношению полярного момента инерции сечения к его радиусу, называют полярным моментом сопротивления сечения. Его размерность – L3. Очевидно, полярный момент сопротивления является геометрической характеристикой прочности бруса круглого поперечного сечения при кручении:
(19.4)
Эта формула служит для проверочного расчета на прочность.
При проектном расчете и при определении допускаемой нагрузки (момента) из формулы (19.4) соответственно находят или
.
Для кольца
и для круга
Для конструкционной углеродистой стали обычно = 20–35 МПа.
Во многих случаях вал должен быть рассчитан не только на прочность, но и на жесткость при кручении.
Рассмотрим брус, жестко защемленный одним концом и нагруженный на свободном конце скручивающим моментом М (рис. 19.15). При деформации бруса его поперечные сечения повернутся на некоторые углы по отношению к своему первоначальному положению или, что то же самое, по отношению к неподвижному сечению (заделке). Угол поворота будет тем больше, чем дальше отстоит данное сечение от заделки. Так, для произвольного сечения I, отстоящего от заделки на расстоянии z,он равен , для сечения II –
.Здесь
– угол поворота сечения II относительно I или угол закручивания элемента бруса длиной
.
Вообще, угол поворота вала при включении произвольного сечения равен углу закручивания части бруса, заключенной между этим сечением и заделкой. Таким образом, угол поворота φторцового сечения представляет собой полный угол закручивания рассматриваемого бруса.
За меру жесткости при кручении принимают относительный угол закручивания (угол закручивания на единицу длины) вала, обозначаемый φ0 (встречается обозначение θ):
Рис. 19.15. Деформации вала при кручении
Угол закручивания бруса постоянного диаметра при одинаковом во всех поперечных сечениях крутящем моменте равен
где l – длина рассматриваемого участка, мм.
В отличие от допускаемого напряжения, зависящего в первую очередь от материала вала, допускаемый угол закручивания зависит от назначения вала.
Значения допускаемых углов закручивания, встречающихся в различных отраслях машиностроения, весьма разнообразны; наиболее распространены значения [θ] = (4,38–17,5) · 103 рад/м = 0,25–1,0 град/м.
Условие жесткости при кручении имеет вид
где – условная жесткость сечения круглого бруса при кручении. Модуль сдвига G характеризует жесткость материала, а полярный момент инерции
является геометрической характеристикой жесткости бруса. Для стали G = 8 · 104 МПа.
При проектном расчете отсюда определяют требуемое значение Ip:
а затем вычисляют диаметр вала. Из двух значений диаметра вала, определенных из расчетов на прочность и жесткость, в качестве окончательного (исполнительного размера) должен быть, конечно, принят больший.
Для круга
19.8. Условие прочности вала при совместном действии
крутящего и изгибающего моментов
При ориентировочном расчете валов влияние изгиба не учитывалось, но допускаемые напряжения на кручение принимались весьма невысокими, что должно было в известной мере компенсировать ошибку, являющуюся следствием пренебрежения изгибом.
Применение гипотез прочности позволяет рассчитывать валы, учитывая совместное действие изгиба и кручения.
При расчете валов, а также других элементов конструкций, испытывающих одновременное действие изгиба и кручения, влиянием поперечных сил, как правило, пренебрегают, так как соответствующие им касательные напряжения в опасных точках бруса, невелики по сравнению с касательными напряжениями от кручения и нормальными напряжениями от изгиба.
На рис. 19.16, а показан вал, на который насажены зубчатое колесо диаметром и шкив ременной передачи диаметром
. На зубчатое колесо действуют окружная
и радиальная
силы, на шкив – силы
и
натяжения ветвей ремня. Для составления расчетной схемы вала (рис. 19.16, б) все силы должны быть приведены к его оси. При переносе силы
к оси вала добавляется скручивающая пара с моментом
(рис. 19.17, а); аналогично при приведении сил
и
получается скручивающая пара с моментом
(рис. 19.17, б).
|
|
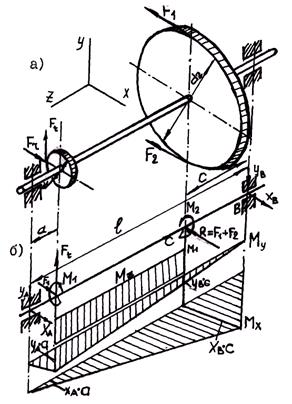
Рис. 19.16. Изгиб с кручением вала
|
|
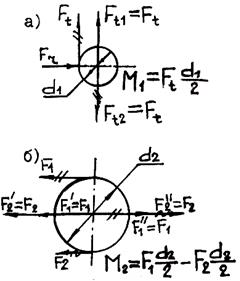
Рис. 19.17. Перенос сил к оси вала
При равномерном вращении вала (только такой случай и рассматривается) , что следует из основного уравнения динамики для вращательного движения.
На основе расчетной схемы определяют опорные реакции и строят эпюры , по которым определяют опасное сечение вала.
Для вала, диаметр которого по всей длине постоянен, опасным будет сечение, в котором одновременно возникают наибольшие крутящий и изгибающий
моменты. В рассматриваемом случае опасным будет сечение C под серединой шкива.
Валы, как правило, изготовляют из среднеуглеродистой конструкционной или реже – легированной стали. Их расчет выполняют на основе третьей или пятой гипотез прочности.
Составим расчетную зависимость по третьей гипотезе прочности.
По формуле
подставляя в нее значения и
, получаем
Учитывая, что для круглого (сплошного или кольцевого) сечения , имеем
Внешне эта формула аналогична расчетной зависимости для определения максимальных нормальных напряжений при изгибе, поэтому величину, стоящую в числителе, называют эквивалентным (или приведенным) моментом, при этом условие прочности имеет вид
Расчет бруса круглого поперечного сечения на изгиб с кручением ведется аналогично расчету на изгиб, но вместо изгибающего момента в расчетную формулу входит так называемый эквивалентный момент, который зависит от изгибающих и крутящего моментов, а также от принятой гипотезы прочности. По гипотезе наибольших касательных напряжений,
При проектном расчете определяют требуемое значение момента сопротивления поперечного сечения:
Учитывая, что для сплошного круглого сечения , получаем следующую формулу для определения требуемого диаметра вала:
Понятие «эквивалентный момент» не имеет смысла при изгибе с кручением бруса некруглого поперечного сечения. Неприменимо оно и в случае, если помимо изгиба и кручения брус круглого сечения испытывает растяжение или сжатие.
Для бруса с постоянным диаметром опасная точка находится в сечении, для которого эквивалентный момент имеет наибольшее значение. Это сечение также называют опасным. Для отыскания опасного сечения иногда помимо эпюр строят эпюру
, а затем эпюру
. Практически в этом нет необходимости; в случае, если по эпюрам
положение опасного сечения определить нельзя, проще вычислить
для нескольких сечений, чем строить эпюры
и
.
Глава 20. Устойчивость сжатых
элементов Конструкций
20.1. Понятие о критической силе для сжатого стержня.
Формула Эйлера
Из физики известно, что равновесие тела устойчиво, если при малом отклонении от равновесного положения возникает сила или пара сил, возвращающая его в положение равновесия. Кроме устойчивого известны также неустойчивое и безразличное равновесия, но для механических конструкций допустимы лишь случаи устойчивого равновесия. Если по каким-либо причинам упругое тело или конструкция при отклонении от равновесного положения не возвращается к исходному, то говорят, что произошла потеря устойчивости.
Явление потери устойчивости упругого тела рассмотрим на примере сжатого стержня. Представим, что на прямолинейный стальной стержень, зажатый одним концом в вертикальном положении (рис. 20.1, а) сверху надет шар. При небольшом значении силы тяжести G1, сжимающей стержень, он сохраняет прямолинейную форму и находится в устойчивом равновесии.
Действительно, если отклонить шар вместе с верхней частью стержня в сторону, то под действием упругих сил стержень, поколебавшись около положения равновесия, снова примет прямолинейную форму. Постепенно увеличивая сжимающую нагрузку путем установки более тяжелых шаров (рис. 20.1, б), увидим, что стержень хотя и сохраняет прямолинейную форму, но при отклонении от положения равновесия возвращается в исходное положение гораздо медленнее. Наконец, при некоторой нагрузке G3 (рис. 20.1, в) стержень изогнется, и прямолинейная форма устойчивого равновесия переходит в новую, криволинейную форму устойчивого равновесия.
|
|
|

Рис. 20.1. Потеря устойчивости
Если теперь стержень принудительно выпрямить или, наоборот, изогнуть еще больше, он после нескольких колебаний займет исходное равновесное положение в изогнутом состоянии.
Максимальная сжимающая нагрузка , при которой прямолинейная форма стержня устойчива, называется критической силой.
Смысл расчета на устойчивость сжатого стержня заключается в том, чтобы он при некотором значении F осевой нагрузки сохранял устойчивость прямолинейной формы и обладал при этом некоторым запасом устойчивости (рис. 20.2):
Рис. 20.2. К определению запаса устойчивости
Условие устойчивости сжатого стержня
где – коэффициент запаса устойчивости.
Допускаемая сжимающая сила
Задачу определения критической силы впервые чисто математически решил Л. Эйлер в 1744 г. Формула Эйлера имеет вид
(20.1)
где – минимальное значение момента инерции площадки поперечного сечения стержня, так как потеря устойчивости происходит в плоскости наименьшей жесткости;
–длина стержня;
– коэффициент приведения длины, т. е. число, показывающее, во сколько раз следует увеличить длину шарнирно закрепленного с обоих концов стержня, чтобы критическая сила для него была равна критической силе стержня в данных условиях закрепления.
Экспериментальные исследования, связанные с проверкой формулы Эйлера, показывают, что при прочих равных условиях (одинаковые материал, форма и размеры поперечного сечения, а также длина стержня) значение критической силы зависит от способа закрепления его концов.
|
|
|
|
|
|
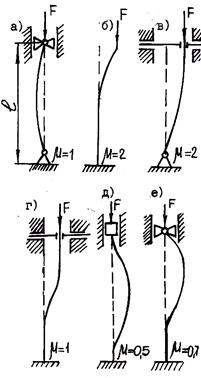
Рис. 20.3. Значения коэффициента приведения длины стержня
при различных способах закрепления его концов
На рис. 20.3 изображены несколько случаев закрепления стержня и указаны соответствующие значения коэффициента приведения μ:
– оба конца шарнирно закреплены (рис. 20.3, а);
– один конец жестко закреплен, другой – свободен (рис. 20.3, б);
– один конец закреплен шарнирно, второй имеет «плавающую» заделку (рис. 20.3, в);
– один конец заделан жестко, второй имеет «плавающую» заделку (рис. 20.3, г);
– оба конца заделаны жестко (рис. 20.3, д);
– один конец заделан жестко, другой закреплен шарнирно (рис. 20.3, е).
20.2. Критическое напряжение.
Пределы применимости формулы Эйлера
При осевом нагружении стержня в его поперечных сечениях возникают нормальные напряжения сжатия, которые возрастают по мере увеличения нагрузки. Нормальные напряжения, соответствующие критической силе, называются критическими:
После подстановки значения критической силы из формулы (20.1) получим
(20.2)
Линейную величину называют минимальным радиусом инерции сечения.
Таким образом, и формула (20.2) принимает вид
или
Безразмерная величина называется гибкостью стержня. Она характеризует сопротивляемость стержня потере устойчивости; с увеличением гибкости уменьшается сопротивляемость стержня потере устойчивости. Заметим, что гибкость λ стержня не зависит от материала стержня, а определяется его длиной, формой и размерами сечения.
Определяя значение критической силы, Эйлер исходил из рассмотрения упругой линии изогнутого стержня, поэтому формула
справедлива только в пределах применимости закона Гука, иначе говоря, до тех пор, пока критическое напряжение не превышает предела пропорциональности материала стержня, т. е. при условии
Отсюда
Стоящая в правой части неравенства постоянная для данного материала безразмерная величина называется предельной гибкостью:
Применимость формулы Эйлера определяется условием
Формула Эйлера применима только в тех случаях, когда гибкость стержня больше или равна предельной гибкости того материала, из которого он изготовлен. Как правило, многие конструкции имеют стержни с гибкостью меньше предельной.
РАЗДЕЛ 4
РАСЧЕТ И КОНСТРУИРОВАНИЕ ДЕТАЛЕЙ МАШИН
ОБЩЕГО НАЗНАЧЕНИЯ И ДЕТАЛЕЙ ОТРАСЛИ
Глава 21. ЗУБЧАТЫЕ ПЕРЕДАЧИ
21.1. Геометрический расчет
эвольвентных прямозубых передач
Рассмотрим сечение цилиндрического зубчатого колеса (рис. 21.1) с внешними зубьями плоскостью, перпендикулярной к оси колеса (главное, или торцовое сечение). Выделяют окружность вершин зубьев ( ) и окружность впадин (
), между которыми заключен зуб колеса. Высота зуба
.
Рис. 21.1. Сечение цилиндрического зубчатого колеса
Эвольвентный профиль и окружность впадин соединяются переходной кривой. Общая точка L эвольвенты и переходной кривой называется граничной точкой профиля.
Расстояние между одноименными профилями двух соседних зубьев, измеренное по дуге окружности, называется окружным шагом зубьев. Для окружности произвольного радиуса
где py – окружной шаг;
Sy – окружная толщина зуба;
ey – окружная ширина впадины.
Длину окружности можно выразить через шаг py и число зубьев z:
откуда
где –окружной модуль.
Модуль и шаг зависят от окружности, к которой они относятся.
На колесе выделяется расчетная окружность, на которой шаг и модуль зубьев равны шагу и модулю зуборезного инструмента. Эта окружность называется делительной (r, d), а модуль зубьев на делительной окружности называется расчетным модулем зубчатого колеса:
где p – шаг по делительной окружности (делительный шаг). Значения m регламентированы СТ СЭВ 310–76, ГОСТ 9563–80:
1-й ряд – 0,8; 1; 1,25; 1,5; 2; 2,5; 3; 4; 5 и т. д.;
2-й ряд – 0,9; 1,125; 1,375; 1,75; 2,25; 2,75 и т. д.
Диаметр делительной окружности
Центральный угол называется угловым шагом зубьев.
В основе зуборезного инструмента, используемого для нарезания эвольвентных цилиндрических колес по методу обкатки, лежит исходный производящий контур, под которым понимается контур зубьев зуборезной рейки в сечении плоскостью, перпендикулярной к направлению ее зубьев. Параметры этого контура стандартизованы (СТ СЭВ 308–76 для ), ГОСТ 13755–81 (рис. 21.2).
Рис. 21.2. Параметры исходного контура зубчатой рейки
Высота зуба исходного производящего контура
где – коэффициент высоты головки зуба;
– коэффициент радиального зазора.
Угол α = 20° называется углом главного профиля.
Прямая, по которой толщина зуба равна ширине впадины, называется делительной. Зубчатые колеса бывают:
1) без смещения исходного контура (некорригированные);
2) со смещением.
Если делительная прямая исходного производящего контура касается делительной окружности нарезаемого колеса, то нарезается колесо без смещения, в противном случае нарезается колесо со смещением (рис. 21.3).
Рис. 21.3. Колеса со смещением и без смещения
В зависимости от коэффициентов смещения зацепляющихся колес различают следующие типы передач:
1) передача без смещения (x1 = x2 = 0);
2) равносмещенная передача (x1 = –x2 ≠ 0, x∑ = x1 + x2 = 0);
3) положительная передача (x∑ > 0);
4) отрицательная передача (x∑ < 0).
В передачах без смещения и равносмещенных[1] (угол зацепления равен углу главного профиля),
(делительные окружности одновременно являются и начальными), высота зуба h = 2,25m. В передачах без смещения
Межосевые расстояния для стандартных редукторов нормированы:
= 40; 50; 63; 80; 100; 125; 160; 180; 200; 225; 250; 280; 315 и т. д.
При нарезании зубьев без смещения можно изготовить колесо лишь с z1min ≥ 17 (если x∑ > 0, то z1min = 12).
При окружных скоростях колес , z1 и z2 принимают кратными друг другу; при
, для z1 и z2 принимают взаимно простые числа зубьев.
Расчет геометрических параметров цилиндрических зубчатых передач выполняется по ГОСТ 16530–83.
21.2. Особенности геометрии косозубых,
шевронных и конических передач
Развернем на плоскость поверхность делительного цилиндра (рис. 12.4). Угол β называется углом наклона линии зуба. Два колеса в зацеплении должны иметь одинаковые углы β, причем при внешнем зацеплении направление винтовых линий у них разное (на одном колесе – правое, а на другом – левое).
Рис. 12.4. Развертка поверхности делительного цилиндра на плоскость
У косозубых колес различают окружной шаг pt (в торцовом сечении), нормальный шаг pn ( в нормальном сечении) и соответственно окружной (торцовый) модуль , нормальный модуль
.
Стандартным расчетным модулем является нормальный модуль, т. е. m = mn.
Очевидны следующие соотношения:
Зацепление косозубых колес в торцовом сечении аналогично зацеплению прямозубых колес. Поэтому геометрический расчет косозубых колеc производится по формулам для прямозубых колес с подстановкой в них параметров торцового сечения. Например, диаметры делительных окружностей определяются по формулам
В косозубой передаче каждый зуб входит в зацепление не сразу по всей длине, а постепенно.
Для передач ( ) x1 = x2 = 0
Угол наклона линии зуба назначают β=8–15º, для шевронных β = 30–45°. Угол β < 8° выполнять не следует, так как утрачиваются преимущества косозубых передач перед прямозубыми.
21.3. Особенности геометрии конических колес
Конические зубчатые передачи служат для передачи вращения между валами с пересекающимися осями. Угол между осями (межосевой угол) теоретически может быть в диапазоне 10°<
<170º. Наибольшее распространение получили передачи с углом
= 90°.
и
– углы делительного конуса шестерни и колеса. Конические прямозубые колеса нарезаются на зуборезных станках инструментами, в основу которых положен зуб исходной рейки (ГОСТ 13754–81,
= 1;
;
) (рис. 21.5).
Рис. 21.5. Основные геометрические параметры конических колес
Так как зубья на боковых поверхностях конусов отличаются от зубьев цилиндрических колес тем, что их размеры (толщина, высота) по мере приближения к вершине конуса уменьшаются, то соответственно изменяются шаг и модуль зацепления, а также и диаметры вершин, делительный и впадин зубьев.
Основные параметры зацепления конической прямозубой передачи
где – средний делительный диаметр;
de – внешний делительный диаметр;
z – число зубьев шестерни и колеса;
– средний окружной модуль;
–внешний окружной модуль, значения которого согласуют с СТ СЭВ 310–76, ГОСТ 13755–81.
где –коэффициент ширины зубчатого венца;
–ширина зубчатого венца;
–внешнее конусное расстояние.
Внешнее конусное расстояние
Модуль определяет выбор параметров режущего инструмента. Высота головки зуба
и ножки
.
Диаметры вершин зубьев и впадин конического зубчатого колеса:
Передаточное число при = 90°
Среднее конусное расстояние .
21.4. Усилия в зацеплении зубчатых передач
При определении сил в зацеплении используют методы теоретической механики, а силами трения пренебрегают ввиду их малости.
Нормальная сила Fn направлена по линии зацепления (как по общей нормали к рабочим поверхностям зубьев).
Прямозубая цилиндрическая передача (рис. 21.6).
Рис. 21.6. Силы, действующие в зацеплении прямозубых цилиндрических колес
Силу Fn раскладывают на окружную Ft и радиальную Fr составляющие:
где – сила, изгибающая зуб;
– сила, сжимающая зуб;
Т – вращающий момент на колесе (шестерне);
– угол главного профиля;
–угол зацепления.
Векторы радиальных сил у колес с внешним зацеплением направлены к центру, а у колес с внутренним зацеплением – от центра зубчатого колеса.
Косозубая и шевронная цилиндрические передачи. Силу в зацеплении передачи раскладывают на окружную Ft , осевую Fa и радиальную Fr составляющие (рис. 21.7, а):
где –угол зацепления косозубой передачи внормальном сечении;
β – угол наклона линии зуба.
|
|
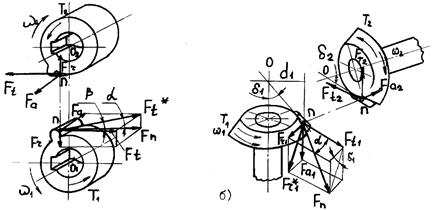
Рис. 21.7. Усилия в зацеплениях цилиндрических косозубых (а)
и конических (б) колес
Осевая сила Fa, стремящаяся сдвинуть колесо вдоль оси вала, дополнительно нагружающая опоры валов, детали корпусов, является недостатком косозубых передач.
Направление окружной и радиальной сил такое же, как и в прямозубой передаче. Осевая сила параллельна оси колеса, а направление вектора зависит от направления вращения колеса и направления линии зуба (рис. 21.8)
Рис. 21.8. Направления сил на ведущем колесе
цилиндрической косозубой передачи
Конические зубчатые передачи. В зацеплении прямозубой конической передачи (см. рис. 21.7, б) нормальная сила Fn также раскладывается на три составляющие, рассчитываемые по среднему делительному диаметру d:
Направления сил на ведущем и ведомом колесах противоположны, и имеют место равенства .
21.5. Материалы и термообработка для зубчатых колес
Зубчатые колеса изготовляют из сталей, чугуна и неметаллических материалов. Колёса из неметаллических материалов имеют небольшую массу и не корродируют, а передачи с ними бесшумны в работе. Но невысокая прочность материалов и, как следствие, большие габариты передачи, сравнительно высокая стоимость изготовления колес ограничивают их применение в силовых механизмах.
Чугунные зубчатые колеса дешевле стальных, их применяют в малонагруженных открытых передачах. Они имеют малую склонность к заеданию и хорошо работают при слабой смазке, но не выдерживают ударных нагрузок.
Наибольшее распространение в силовых передачах имеют колёса из сталей Ст5, Ст6, 35, 35Л, 40, 40Л и др., которые, как правило, подвергают, термообработке для повышения нагрузочной способности.
Колеса малонагруженных передач в машинах общего назначения, а также колёса передач, габариты которых не ограничены, подвергают объемной закалке с высоким отпуском до твердости 300–350 НВ при диаметре колес до 150 мм. Колёса диаметром свыше 150 мм имеют твердость не менее 200 НВ. Зубья колес, подвергнутых такой обработке, имеют приблизительно одинаковую твердость по всему сечению и могут быть нарезаны после термообработки, благодаря этому отпадает необходимость выполнения доводочных операций.
Для предотвращения заедания рабочих поверхностей нижний предел твердости шестерни (меньшего колеса), как показывает практика, должен быть на 30–50 единиц выше верхнего предела твердости колеса.
Колёса высоконагруженных передач в транспортных машинах и передач ограниченных габаритов должны иметь твердость зубьев более 400 НВ.
21.6. Расчеты зубьев на сопротивление усталости
по изгибным и контактным напряжениям
1. Расчет зубьев на прочность при изгибе.Условие прочностной надежности зуба:
где –максимальное напряжение в опасном сечении зуба;
– допускаемое напряжение изгиба для материала зуба.
Для оценки прочностной надежности зубчатой передачи необходимо иметь уравнение, связывающее максимальные напряжения в опасном сечении с внешней нагрузкой на зуб и размерами опасного сечения (параметрами передачи).
А. Прямозубые цилиндрические передачи.Расчет выполняют для наиболее опасного случая – однопарного зацепления, когда вся внешняя нагрузка передается одной парой зубьев:
где yF – коэффициент формы зуба;
Ft – окружная сила;
bw –ширина венца колеса;
m –модуль зацепления;
KFα – коэффициент, учитывающий одновременное участие в передаче нагрузки нескольких пар зубьев (KFα= 1);
KFβ –коэффициент концентрации нагрузки;
KFυ –коэффициент динамической нагрузки.
Б. Косозубые цилиндрические передачи.Напряжения в зацеплении косозубого цилиндрического колеса
где – коэффициент, учитывающий наклон зубьев;
– коэффициент перекрытия;
где – коэффициент ширины колеса;
для колес низкой твердости (не более 350 НВ);
(для колес твердости более 350 НВ).
Ширину зубчатых колес принимают в зависимости от диаметра шестерни.
В. Конические передачи.В опасном сечении зуба конического колеса максимальные напряжения
где – экспериментальный коэффициент, учитывающий пониженную нагрузочную способность конических передач по сравнению с цилиндрическими передачами из-за конструктивных особенностей;
= 0,85 – для конических прямозубых передач;
1–1,2 – для передач с круговыми зубьями;
m –модуль в среднем нормальном сечении зуба.
2. Расчет на контактную прочность активных поверхностей зубьев.Расчет зубьев выполняют для фазы зацепления в полюсе:
где –максимальное контактное напряжение на активной поверхности зубьев;
–допускаемое контактное напряжение.
Контактные напряжения одинаковы для обоих колес, поэтому расчет выполняют для того колеса, у которого
меньше.
Для расчета зубчатой передачи на контактную прочность необходимо иметь уравнение, связывающее максимальное напряжение с внешней нагрузкой и параметрами передачи.
А. Прямозубые и косозубые передачи.Предел контактной выносливости:
где ZH –коэффициент, учитывающий форму сопряженных поверхностей;
Zm –коэффициент, учитывающий механические свойства материалов колес (модули упругости Е1 и Е2 и коэффициенты Пуассона, и
);
Zm = 275 – для стальных колес;
Zε – коэффициент, учитывающий суммарную длину контактных линий:
– для прямозубых передач.
– для косозубых передач.
в предварительных расчетах;
–из таблиц;
–межосевое расстояние;
–ширина колеса;
u – передаточное число.
принимают в зависимости от межосевого расстояния:
где – коэффициент ширины колеса;
= 0,315–0,5 – при симметричном положении колес;
= 0,25–0,4 – при несимметричном;
= 0,2–0,25 – при консольном расположении.
Б. Конические передачи (прямозубые).Расчет производят по формуле (21.1), где вместо коэффициента подставляют коэффициент
(установлен экспериментально, учитывает особенности прочности конических передач). Для прямозубых передач
0,85.
Глава 22. ЧЕРВЯЧНЫЕ ПЕРЕДАЧИ
22.1. Общие сведения. Геометрические и кинематические
особенности червячных передач
Червячная передача представляет собой передачу, у которой ведущее колесо (червяк) выполнено с малым числом зубьев (z1 = 1–4), а ведомое (червячное) колесо имеет большое число зубьев (z2 > 28). Угол скрещивания осей обычно составляет 90°.
Червяки бывают следующих видов:
– архимедов червяк, торцовым профилем которого является архимедова спираль (рис. 22.1);
– конволютный;
– эвольвентный, представляющий собой косозубое зубчатое колесо с очень большим углом наклона и малым числом зубьев.
Червяки имеют стандартный угол профиля α = 20° в осевом сечении.
Рис. 22.1. Передача с цилиндрическим червяком
Достоинства червячных передач состоят в возможности получения больших передаточных отношений в одной ступени (обычно
i = 10–60, реже i = 60–100), плавности и бесшумности работы, возможности самоторможения.
Основной недостаток передач – низкий КПД, который ведет к большому тепловыделению и для отвода теплоты часто требует применения специальных устройств (обдув, оребрение корпуса и др.). Это, а также необходимость применения цветных металлов существенно ограничивают области использования червячных передач (мощность до 50–60 кВт, окружная скорость – до 15 м/с).
Диаметры колес определяются, как для цилиндрических зубчатых колес при коэффициенте высоты головки = 1 и коэффициенте радиального зазора
.
Диаметр делительного цилиндра червяка (рис. 22.2)
где q – коэффициент диаметра червяка, принимаемый в зависимости от модуля mдля обеспечения жесткости;
– осевой модуль червяка, стандартизован ГОСТ 19642–74 (m = 1; 1,25; 1,6; 2; 2,5; 3,15; 4; 5; 6,3; 8; 10; 12.5 и т. д.);
p – шаг червяка.
Рис. 22.2. Зацепление червячной передачи
Делительный угол подъема винтовой линии γ(обычно 5–20°) определяется по формуле
где z1= 1; 2; 4 – число витков (заходов) червяка.
При меньшем числе заходов z1угол γбудет меньше, ниже будет и КПД; при больших z1увеличиваются радиальные габариты и стоимость передачи. В передачах мощных приводов из-за больших потерь и сильного нагрева не рекомендуют использовать однозаходные червяки.
При u = 10–18, 18–40 число заходов соответственно 4 и 2, а при u > 40 число заходов 1.
Диаметры окружностей вершин и впадин червяка
где = 1,0 – коэффициент высоты головки;
–коэффициент высоты ножки;
= 0,2 – коэффициент радиального зазора.
Червячное колесо является косозубым с углом наклона линии зуба . Диаметр колеса
где z2 – число зубьев колеса.
Межосевое расстояние
Длина b1нарезной части червяка принимается такой, чтобы обеспечить зацепление с возможно большим числом зубьев колеса.
Ширина колеса b2назначается из условия получения угла обхвата червяка колесом:
За один оборот червяка зуб колеса, контактирующий с некоторым его витком, переместится по окружности на расстояние подъема витка и колесо повернется на угол
. Передаточное отношение червячной передачи
Обычно i = 20–60 в силовых передачах, i ≤ 300 в кинематических цепях приборов и делительных механизмов.
В червячном зацеплении наблюдается скольжение. Витки червяка скользят при движении по зубьям колеса.
Для уменьшения износа материалы червяка и колеса должны образовывать антифрикционную пару, имеющую минимально возможный коэффициент трения. Для повышения прочности и жесткости червяки обычно изготовляют из стали 40ХН, 12XH3A, 3ОХГСА и др., а колеса – из бронз БрА9Ж3Л, БрА10Ж4Н4Л или венцы колес – из бронзы БрО10Ф1.
Дата добавления: 2015-06-17; просмотров: 5599;