Механизмы передвижения
1.4.1. Общая характеристика и параметры
Портальные краны перемещаются по рельсовому пути с помощью механизмов с приводными колесами. Согласно требованиям «Правил…» [12], ходовые колеса должны быть двухребордными и изготовливаться из стали коваными, катаными, штампованными или литыми. Допускается применять ходовые колеса, изготовленные из высокопрочного чугуна с шаровидным графитом. Типовая схема ходовых тележек механизма передвижения портального крана представлена на рис 1.19.
Число ходовых колес назначают в зависимости от нагрузок на опоры, число приводных колес — по условию сцепления [13]. Пример расположения приводных и неприводных колес приведен на рис. 1.20.
![]() Рис. 1.19. Ходовые тележки портального крана грузоподъемностью 10 т (а) и кинематическая схема его приводной тележки (б): 1 — буфер; 2 — приводная тележка; 3 —балансир; 4 — холостая тележка; 5 — противоугонный захват |
Рис. 1.20. Схемы расположения ходовых колес портальных кранов грузоподъемностью 10 и 16 т (а) и 80 / 50 т (б): ■ — приводное колесо; □ — холостое колесо; 2а — колея; 2b — база опорного контура
Механизмы передвижения современных портальных кранов состоят из приводных и неприводных тележек (рис. 1.19,а). В схемах двухколесных приводных тележек используют навесные вертикальные редукторы [15] или более компактные червячные (рис. 1.19,б). Если число тележек под опорой больше одной, то их объединяют системой балансиров (рис. 1.21). Длины плеч балансиров принимают при условии одинаковой вертикальной нагрузки на все колеса.
Рис. 1.21. Схема балансиров механизма передвижения
Механизмы передвижения портальных кранов должны оборудоваться тормозами нормально-замкнутого типа с тормозным моментом, достаточным для обеспечения остановки и удержания крана при действии максимально допустимой скорости ветра, принимаемой по ГОСТ 1451 для рабочего состояния крана, с учетом допустимого уклона [12].
1.4.2. Приборы и устройства безопасности
В соответствии с правилами [12] краны, передвигающиеся по рельсовым путям на открытом воздухе, должны быть оборудованы противоугонными устройствами. Эти устройства должны предотвращать самопроизвольное движение крана при давлении ветра, превышающем допустимое для рабочего состояния кранов. Делать тормоза механизмов передвижения слишком мощными нецелесообразно, так как при обычных условиях эксплуатации они будут работать резко, создавая повышенные динамические нагрузки на конструкцию.
Для портальных кранов можно выделить основные группы противоугонных устройств: фиксаторы, ручные и приводные рельсовые захваты принудительного и автоматического действия. На рис. 1.22,а,б приведены два варианта ручных клещевых захватов. Фиксаторы в простейшем случае имеют вид закладных пальцев (рис. 1.22,в), заводимых в гнездо рам ходовых тележек и проушины кронштейнов якорных блоков, размещаемых у стояночного участка кранового пути. Их применяют на портальных кранах, работающих в зоне частых ураганов и оборудованных рельсовыми захватами, и на доковых кранах.
Рельсовые захваты целесообразно выполнять автоматическими с приведением их в действие при достижении ветром заданной скорости вне зависимости от наличия на кране электропитания.
Захваты принудительного действия с машинным приводом могут работать только при наличии электропитания, что несколько снижает надежность защиты крана от угона ветром. Поэтому в соответствии с правилами [12], если противоугонное устройство имеет машинный привод, то оно должно быть оборудовано приспособлением для приведения его в действие вручную. Конструкция рельсового захвата должна допускать закрепление крана на всем пути перемещения.
Захваты автоматического действия опасны своим внезапным срабатыванием при частых в эксплуатации отключениях электроэнергии.
Приводные рельсовые захваты всех видов требуют особо тщательного регулирования и ухода; они весьма чувствительны к неисправностям крановых путей.
Вместе с тем практически можно обеспечить безопасность крана против угона ветром ручными противоугонными захватами при исправном состоянии механизма передвижения крана и крановых путей.
|
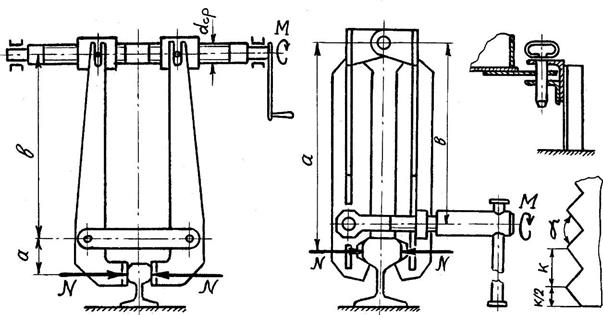
Рис. 1.22. Ручные клещевые рельсовые захваты (а, б), фиксатор (в) и рекомендуемый профиль насечки губок (г)
Практически во всех случаях при увеличении скорости ветра исправно действующие тормоза механизма передвижения при наличии работоспособной ветровой сигнализации позволяют крановщику оставить кабину и привести в действие ручные противоугонные захваты.
На рис. 1.23 представлен приводной клещевой захват принудительного действия.
Электродвигатель мощностью 1…1,5 кВт через редуктор 1 вращает вертикальный винт 2. Гайка 7 этого винта заключена в коробке ползуна 6, перемещающегося по вертикальным направляющим корпуса захвата.
При движении крана с захватом в нерабочем состоянии гайка 7 находится в верхнем положении; при этом крышка коробки ползуна опирается на верхний торец гайки.
Ролики верхних концов рычагов 5 находятся на нижних участках пазов ползуна; при этом рычаги совместно с их траверсой находятся в верхнем положении, а их губки не соприкасаются с головкой кранового рельса. При срабатывании ветровой защиты или при выводе крана в нерабочее состояние электродвигатель приводит во вращение винт. Гайка начинает вместе с ползуном и подвешенными к нему рычагами перемещаться вниз до упора траверсы 4 в головку кранового рельса.
При дальнейшем вращении винта ползун начинает смещаться относительно рычагов, действуя на их ролики и отводя верхние концы рычагов в стороны. Губки рычагов входят во взаимодействие с головкой рельса и стопорят рычаги. Винт продолжает вращаться, и гайка перемещается вниз, преодолевая сопротивление пружины, нажатие которой через клиновые поверхности полностью передается на рычаги. При высоте пружины в сжатом состоянии, соответствующей заданному усилию прижатия губок, предусмотренный на гайке упор воздействует на смонтированный на ползуне концевой выключатель 3. В результате этого двигатель захвата отключается от сети.
Рис. 1.23. Приводной клещевой захват принудительного действия, объяснения см. в тексте
Установленный в верхней части корпуса выключатель 8 обеспечивает остановку двигателя при подъеме ползуна в верхнее положение. Срабатывание этого выключателя также позволяет включить приводы крановых механизмов. Наличие в кинематической цепи захвата тарированной пружины обеспечивает стабильность усилия зажатия.
Удерживающее усилие FУ, которое должны развивать все противоугонные устройства крана, должно быть не менее чем FУ0 , определяемое по формуле
FУ0 = n PВIII – Gкwmin – Fтор; (1.14)
если соблюдается условие (1.16); в противном случае по формуле
FУ0 = n Pв – Gк wmin – GПР (m0 – wmin). (1.15)
Условие сцепления приводных (т.е. тормозных) колес с рельсом при сдвиге крана ветром имеет вид
Fтор < Gпр (m0 – wmin). (1.16)
В формулах (1.14) – (1.16) n = 1,2 – коэффициент запаса; PВIII – ветровая нагрузка на кран в нерабочем состоянии; Gк – вес крана; Gпр – нагрузка на приводные колеса крана; Fтор – тормозное усилие, приведенное к ходовым колесам; m0 – коэффициент сцепления колес с рельсом (для кранов, работающих на открытом воздухе, m0 = 0,12); wmin – минимальный коэффициент сопротивления передвижению (при коэффициенте kр, учитывающем трение реборд колес, равном kp = 1).
Расчет клещевых захватов (рис. 1.22, 1.23) выполняют по усилию N нажатия на рельс, определяемому из выражения
N = Fy / (2 i m1), (1.17)
где Fy – по формулам (1.14) или (1.15); i – количество захватов; m1 –коэффициент сцепления губок захвата с рельсом. Для незакаленных губок без насечки (из стали 45,50) m1 = 0,12…0,15. Для закаленных губок в виде гребенки с острой насечкой (из сталей 65Г, 60С2, У8А, У10А) при твердости больше 55HRC m1 = 0,3…0,35, но нужно тщательно наблюдать за состоянием насечки, так как ее притупление до площадки шириной 0,15 мм дает значение m1= 0,15…0,18.
Габаритную площадь рабочей поверхности губки назначают по допускаемому удельному давлению 200…250 МПа для закаленных губок, 50…80 МПа для незакаленных. Рекомендуемый профиль насечки показан на рис. 1.22,г (k = (5…6) мм, g = 90…110o).
Ручные клещевые захваты (см. рис. 1.22,а,б) должны иметь на оси винта момент М, определяемый по формуле
M = N a dср tg (a + r) / (2 b),
где dср – средний диаметр резьбы; a = 4…5o – угол подъема винтовой линии для самотормозящего винта; r = 4…6o или 8…9o – угол трения при бронзовой или стальной гайке; a и b – плечи рычажной системы.
Усилие винта Fв (и пружины) в захвате с винтовым приводом (рис. 1.23) определяется из выражения
FВ = 2 N a sin(b + r1) / (b h),
где b = 4…8o – угол между рабочей поверхностью клинового паза и вертикалью; r1 – приведенный угол трения с учетом сопротивления роликов клещей; r = 1 или 3o при роликах на подшипниках качения или скольжения; h = 0,95 – КПД шарниров; a / b = 1/4…1/3. По усилию Fв винта определяют потребный момент электродвигателя при времени закрытия захвата t = 20…50 с.
Механизмы передвижения портальных кранов в соответствии с правилами [12] должны быть снабжены ограничителями рабочих движений для автоматической остановки, которые обеспечивают отключение двигателей механизма на расстоянии от упора не менее полного пути торможения.
Портальные краны для смягчения возможного удара об упоры должны быть снабжены упругими буферными устройствами [12], которые могут быть резиновыми, из полимерных материалов, пружинными, пружинно-фрикционными и гидравлическими.
Резиновые буферы изготовляют из морозостойкой резины средней твердости монолитными или наборными из ряда пластин (до 20) [15, 16]. Они крепятся к торцевому щиту ходовой тележки с помощью приварного воротника (рис. 1.19). К их недостаткам относится сравнительно быстрое изнашивание при частых ударах. За рубежом находят применение буферы из пористых полимерных материалов; при работе такого буфера воздух выдавливается через поры внутренних поверхностей, что повышает эффективность работы буфера.
Пружинным буферам свойственна резкая отдача и сравнительно малая энергоемкость. При больших нагрузках буфер состоит из плиты, опирающейся на несколько пружин. Более совершенны пружинно-фрикционные буферы (рис. 1.24,а), в которых 60…70 % энергии гасится внутренним трением. Для пружинно-фрикционных буферов требуются смазка подвижных трущихся частей и более тщательный уход.
|
Рис. 1.24. Пружинно-фрикционный (а) и гидравлический (б) буферы
Гидравлические буферы (рис. 1.24,б) весьма компактны, способны поглотить значительное количество энергии, работают без отдачи. В них можно обеспечить плавное нарастание, а затем постоянство силы сопротивления по всей длине хода. Однако сложность конструкции и необходимость постоянного ухода ограничивают их применение в краностроении.
При расчете буферов, если принять металлическую конструкцию крана абсолютно жесткой, используется равенство
0,5 mк V12 = (Gk wmin + Fтор) S + n ò Fб dS,
где mK – масса движущихся частей крана и его механизма передвижения, приведенная к ходовым колесам; S – ход буфера; n – количество буферов, Fб – усилие буфера; V1 – скорость крана в момент удара, V1 = 0,5V, где V –номинальная скорость движения крана; остальные обозначения, как в формулах (1.14) и (1.15).
Значение энергоемкости ò Fб dS для пружинных, пружинно-фрикционных и приближенно резиновых буферов равно 0,5 Fбmax S; для гидравлических, обеспечивающих постоянное усилие – Fбmax S.
Дата добавления: 2015-02-19; просмотров: 10613;