Службове призначення станин.
Станини і рами є основою для компоновки різних машин. Станини служать для координування вузлів і механізмів машини, а в деяких випадках і для направлення їхнього руху. СП станин повинно включати вимоги щодо відносних положень складальних одиниць, їх відносного руху, допустимих статичних і динамічних навантажень, допустимих змін теплових дій, параметрів оточуючого середовища, періоду експлуатації, регламенту обслуговування, значення маси, габаритів, ергономічних та інших показників. У перелічених характеристиках повинні бути задані номінали та допуски (наприклад, ...). СП станини безпосередньо залежить від СП верстату, яке в свою чергу випливає з необхідної точності оброблення.
//На прикладі токарного верстату (рис. 1) продемонструвати зв’язок параметрів СП станини з параметрами СП верстату. У першій графі показано, що СП залежить від точності виготовлення деталі у вертикальній та горизонтальній площинах. У наступній графі схематично показано технічні вимоги щодо положення осей шпинделя та задньої бабки в обох площинах. В останній частині наведено СП станини, де шпиндель розглядається в площині X1Y1Z1, а задня бабка – в X2Y2Z2. Коротко охарактеризувати перелічені вище показники.//
![]() ![]() | ![]() | Необхідна точність оброблення деталі на верстаті |
ТВ до верстата | ![]() | Необхідна точність відносного положення і руху виконавчих поверхонь верстата |
![]() |

СП станини | Необхідна точність
положення і руху
приєднуваних до станини
складальних одиниць
![]() | СП приєднуваних складальних одиниць | Необхідна точність
положення і руху
виконавчих поверхонь
відносно основних баз
![]() | |
![]() | ||||
ТВ до станини | Точність баз і
їх відносного положення
![]() |
Рис. 2.1. Зв’язок параметрів СП станини з параметрами СП верстату.
Необхідні параметри СП станини забезпечуються сукупністю певних властивостей станини, до яких відносяться:
- геометрична точність поверхонь основних і допоміжних баз і точність їх відносного положення;
- статична і динамічна жорсткість станини;
- зносостійкість напрямних;
- теплова стабільність;
- відсутність жолоблення;
- малий і стабільний коефіцієнт тертя по напрямних.
Класифікація базових поверхонь.Незважаючи на велику кількість видів станин, їх можна розділити на два основні класи:
1. Станини без напрямних, які призначені тільки для забезпечення необхідного відносного положення приєднуваних складальних одиниць та деталей.
2. Станини з напрямними, які призначені також для забезпечення необхідних взаємних рухів вузлів: кареток, супортів, столів тощо (основний вид станин для металорізальних верстатів).
Усі станини мають: основну базу (рис. 2.2 – пов. А) – поверхню, на якій орієнтується верстат у цеху; допоміжну базу (пов. Б) – поверхню, по якій орієнтуються деталі і вузли на самій станині; кріпильні отвори (пов. Г) – поверхні, практично незмінні для усіх видів станин. У станин другого класу, окрім перелічених поверхонь, є напрямні - поверхні, призначення яких полягає у направленні руху окремих вузлів. Поперечний перетин таких поверхонь показаний на рис. 2.3.
|

|
|
|
|
|





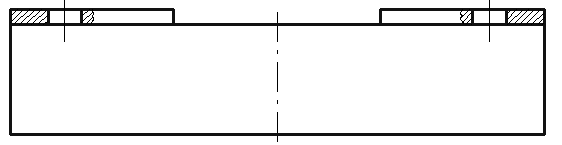
Рис. 2.2. Основні поверхні деталей типу станин.
Рис. 2.3. Поперечний перетин станини з напрямними.
2. Технічні вимоги (ТВ) на виготовлення станин.
ТВ на станини напряму пов’язані з її СП. ТВ складаються із вимог до матеріалу та параметрів точності станини (рис. 2.4).
Рис. 2.4. ТВ на виготовлення станин.
3. Матеріали і способи отримання заготовок.
Заготовки станин можуть бути литими або зварними при виготовленні їх з металів. При виготовленні з неметалів матеріалом є бетон, залізобетон, полімербетон.
Матеріали і способи отримання заготовок можна представити схемою (рис. 2.5).
Рис. 2.5. Матеріали і способи отримання заготовок станин.
Металеві заготовки виготовляють з чавуну, сталі, алюмінієвих сплавів.
Литі заготовки повинні володіти високою зносостійкістю і твердістю монолітних напрямних. Матеріал - сірий чавун: СЧ20, СЧ25, СЧ,30, модифікований чавун СЧ2І, СЧ32. Модифікування чавуну сприяє отриманню необхідної кулевидної форми графіту, створенню однорідної структури і підвищення його міцності. Модифікування здійснюється шляхом введення в сірий чавун присадок феросиліцію, силікоалюмінію, церію, магнію тощо. В деяких випадках для поверхонь напрямних виконують легування за допомогою спеціальних паст. Легований чавун використовують для виливання напрямних. Для економії вартісного легованого чавуну широко використовують поверхневе виливання. Суть такого виливання заключається в тому, що пасту з легуючими елементами наносять в місце, де повинні бути напрямні. Можливий метод литва, коли у форму заливають спочатку легований чавун, а потім – нелегований. Масивні станини виливають з використаним кокільних пластин (холодильників), які мають форму напрямних і розташовані у місцях напрямних (отримання вибіленого чавуну, де вільний вуглець знаходиться у зв’язці Fe3C ). Для зняття внутрішніх напружень обов’язково проводять штучне або природне старіння заготовок. Штучне старіння – заготовка станини масою 2 ... 4 т з матеріалу СЧ21 нагрівається у печі з 200...230 °С до 550 °С з швидкістю 80...100 °С/год + витримка 4...5 год + охолодження з піччю 6...8 год + вивантаження з печі при 150 °С. Природне старіння – заготовка знаходиться на відкритому повітрі терміном до 9 міс. Для пришвидшення практикують закопування заготовок у землю.
Сталь для виливків застосовується рідко, коли є великі ударні навантаження, Заготовки у такому випадку отримують на горизонтально-кувальних машинах. Для зварних заготовок застосовують сталь Ст.З, Ст.5 товщиною 3-12 мм. Крім листа широко використовують профільний прокат; швелери, кутники тощо. Перевагами, у порівнянні з литими чавунними заготовками є:
- менша (на 30 ... 40%) маса при однаковій жорсткості;
- менша собівартість механічного оброблення;
- більш висока універсальність і гнучкість у виборі методів і засобів виготовлення (швидке переналагоджування; скорочений цикл підготовки виробництва, мінімальні затрати при внесенні змін у конструкцію).
4. Вибір технологічних баз при обробленні станин.
Чистовою базою при обробленні станин є площина її основи. Цю поверхню виходячи із СП станин взагалі не потрібно було б обробляти, але вона використовується у комплекті технологічних баз.
При виборі баз розрізняють їх призначення при обробленні по розмітці та обробленні настроєним на розмір інструментом (при виготовленні у спеціальних пристроях). В обох випадках при виборі баз необхідно розрахувати операційні розміри, що отримуються після оброблення. //Для пояснення цього вирисовується ескіз в поперечному перетині станини, на якому наносяться розмірні ланцюги за якими вирішуються поставлені задач (рис. 2.6)//.
При оброблені по розмітці можливі два варіанти: розмічаються товщини основи та напрямних або товщини основи і загальна висота станини.
![]() | А1 = 30±0,5 А2 = 5 А3 = 590±3,0 А4 = 5 А5 = 600±0,8 А6 = 25±1,0 z1=z2=6±1,0 |
Рис. 2.6. Розмітка станин під оброблення.
На робочому кресленні станини можуть бути нанесені розміри однієї з двох груп: А1, А2, А4, А5 або А1, А2, А3, А4.
При розмітці можливі два варіанти
1. Розмічені розміри А1, А4 (розмір А1 отриманий на першій операції від бази М, розмір А4 отриманий на другій операції). Розмір А5, який необхідно досягнути, визначиться з рівняння розмірного ланцюга (див. рис. 2.6):
А5 = А1 - А6 + А3 + А4
Похибка базування у цьому випадку:
wА5 = wА1 + wА6 + wА3 + wА4 = 1,0 + 2,0 + 6,0 + 1,0 = 10 мм
2. Розмічені розміри А1 (отриманий на першій операції від бази М) і розмір А5. Розмір А4, який необхідно досягнути:
А4 = А5 – А1 + А6 – А3
wА4 = wА5 + wА1 + wА6 + wА3 = 1,6 + 1,0 + 2,0 + 6,0 = 10,6 мм
Висновок: при призначенні баз за одним з двох вище наведених варіантів допуск на ланку (розмір) А4 буде рівний 10,0 (10,6) мм. //Порівняти з номіналом А4 = 5 і А5 = 600±0,8 мм. (допуск на А4 = 5 більший за номінал, допуск на А5 можна збільшити//. У випадку, якщо вказаний допуск не перевищуватиме допуску, заданим конструктором (див. робоче креслення), задачу призначення баз можна вважати вирішеною. При наявності кількох варіантів робочим приймається той, який передбачає зручніше базування заготовки в ході виконання технологічного процесу.
При оброблені настроєним на розмір інструментом також розглядають можливі способи базування на першій операції. Для цих способів розраховуються коливання розмірів одержаних в результаті оброблення основи та напрямних. //Ці розрахунки супроводяться поопераційними ескізами з технологічними розмірними ланцюгами. В кінці проводиться аналіз отриманих результатів, переваги та недоліки варіантів базування з точки зору точності окремих розмірів, складності конструкції пристроїв//
Варіант 1.
![]() | Перша операція: Оброблення чистової технологічної бази. Необхідно витримати розмір А2 (див. рис. 2.6). При такому базуванні розмір А2 регулюється розміром А7: 1) А7 = А5 + z1; 2) А7 = А2 + А3 + А4 + z1; А2 = А7 - А3 - А4 – z1; А2min = А7min - А3max - А4max – z1max = А2max = А7 max - А3min - А4min – z1min = А7 = А5 + z1; А7min = А5min + z1min; А7max = А5max + z1max; Тут: 1) – заданий розмір А5; 2) – задані розміри А2, А3, А4. |
![]() | Друга операція: Оброблення напрямної. Необхідно витримати розмір А4 1) А8 = А5; 2) А8 = А2 + А3 + А4; А4 = А8 – А2 – А3; А4min = А8min – А2max – А3max = А4max = А8max – А2min – А3min = А8 = А5; А8min = А5min; А8max = А5max; |
Варіант 2. | Варіант 3. |
![]() |
Рис. 2.7. Похибка базування при обробленні станини.
5. Типові технологічні маршрути оброблення станин.
При побудові ТП виготовлення станин необхідно враховувати особливості, пов’язані з відносно великими розмірами і масою, а також наявністю напрямних:
- необхідність проведення старіння для попередження короблення станини і, як наслідок, необхідність розділення у часі повного чорнового і чистового оброблення заготовки литої станини, а для маложорстких станин прецизійних верстатів – ще й напівчистового оброблення;
- бажаність скорочення до мінімуму кількості встановлень і перевстановлень заготовки до повного оброблення, враховуючи особливо великі втрати часу на міжопераційне транспортування, встановлення і зняття з верстата (з вивірюванням), складність досягнення необхідної точності встановлення через великі контактні деформації і власні деформації заготовки;
- специфіку наявного поздовжньо-оброблювального устаткування, яке необхідне для високоточного оброблення напрямних, що вимагає виділення таких операцій як самостійних і призводить до збільшення кількості перевстановлення заготовки.
Скорочення кількості перевстановлень заготовки можна забезпечити за рахунок:
- скорочення кількості етапів оброблення заготовки (чорнового, напівчистового, чистового і викінчувального) в результаті підвищення розмірної точності заготовок, покращення їх якості, зменшення здатності станин до жолоблення;
- використання плит-супутників чи палет;
- застосування верстатів з ЧПК і багатоцільових верстатів, у т.ч. для п’ятистороннього оброблення заготовок;
- підвищення технологічності конструкції станини.
Всі типові маршрути обробки станин починаються з оброблення основи - технологічної бази для оброблення більшості поверхонь.
Загалом, типовим ТП оброблення станин є такий (//Правила єдності і постійності баз!//).
1. Розмітка заготовки.
2. Оброблення основи (чорнове, чистове).
3. Оброблення напрямних (чорнове, чистове).
4. Оброблення боковин (чорнове, чистове).
5. Повторна розмітка.
6. Оброблення головних отворів.
7. Оброблення кріпильних отворів.
8. Старіння.
9. Термічне оброблення напрямних.
10. Викінчувальне оброблення основи.
11. Викінчувальне оброблення напрямних.
12. Викінчувальне оброблення головних отворів.
6. Чорнове оброблення заготовок станин проводиться з метою:
- зняття ливарної кірки та дефектного шару (який вміщує відбілений чавун)з оброблюваних поверхонь;
- забезпечення необхідних розмірів заготовки; оптимального припуску для чистового оброблення;
- забезпечення рівномірності припуску під подальше чистове оброблення напрямних;
- забезпечення потрібних зв’язків у станині між усіма обробленими поверхнями.
- виявлення можливих дефектів на всіх відповідальних поверхнях.
Чорнове оброблення може бути виконане торцевим фрезеруванням, струганням (один з основних методів оброблення напрямних в серійному виробництві), фрезеруванням на карусельно-фрезерних верстатах, точінням на токарно-карусельних верстатах, обдирним шліфуванням, шліфуванням абразивною стрічкою на стрічко-шліфувальних верстатах.
Вибір методу оброблення основи здійснюється з врахуванням контуру оброблюваної поверхні (рис. 2.8), припуску, кількості заготовок у партії, наявності устаткування та інших умов виробництва. Вибір оптимального методу оброблення здійснюється за мінімумом приведених витрат чи собівартості оброблення.
Рис. 2.8.Контури оброблюваних поверхонь основ станин.
Чорнове оброблення напрямних здійснюється відразу після оброблення технологічних баз. Прямолінійні чавунні напрямні оброблюють звичайно струганням чи фрезеруванням. Кругові напрямні – обточування на токарно-карусельному верстаті.
Фрезерування напрямних може здійснюватися на універсальних і спеціальних багатошпиндельних поздовжньо-фрезерних верстатах, а також на багатоцільових верстатах з ЧПК різними методами. //Схеми оброблень наводяться рисунками на дошці//.
6.1. Фрезерування стандартними торцьовими, циліндричними і дисковими фрезами.Приклад оброблення напрямних токарного верстату (рис. 9) на чотирьохшпиндельному поздовжньо-фрезерному верстаті показано на рис. 10.
Рис. 2.9. Напрямні токарного верстата.
На кожному шпинделі закріплена одна стандартна фреза. Для повного оброблення усіх поверхонь необхідно (у даному випадку) сім окремих переходів зі зміною фрез і зміною положення шпиндельних бабок. Оброблення напрямних може здійснюватися за одне чи декілька встановлень заготовки станини. При фрезеруванні за одне встановлення збільшується допоміжний час на переналагодження шпиндельних бабок і досягнення точності пробними проходами. При обробленні заготовки за декілька встановлень вся партія станин оброблюється при одному настроюванні бабок. Оптимальний варіант встановлюється за допомогою економічних розрахунків (мінімум собівартості оброблення). Фрезерування стандартними фрезами може ефективно здійснено за одне встановлення заготовки на багатоцільових верстатах, споряджених ЧПК.
Рис. 2.10. Фрезерування прямолінійних напрямних заготовки стандартними фрезами (І – IV – номери шпинделів (шпиндельних бабок)).
6.2. Фрезерування напрямних спеціальним набором фрез.Здійснюється на поздовжньо-фрезерних верстатах. У цьому випадку дві горизонтальні шпиндельні бабки приводять у рух одну оправку з набором профільних фрез, що забезпечує майже повне оброблення профілю напрямних за один робочий хід (рис. 11).
Рис. 2. 11. Фрезерування прямолінійних напрямних заготовки спеціальним набором фрез.
Залишаються необробленими нижні платики і канавки (див. рис. 2.9), які оброблюються на окремій операції ще чотирма фрезами. Набір фрез (рис. 2.11) має тільки чотири стандартні тристоронні фрези, інші фрези є спеціальними (вартість). Висока вартість наборів фрез та їх експлуатації робить економічно доцільним використання цього способу фрезерування напрямних тільки за достатньо великої серійності виготовлення станин.
При обробленні напрямних складного профілю в набір фрез доводиться включати фрези з швидкорізальної сталі, по яких в подальшому встановлюються режими різання (v – за Dmax, sz – за zmin). Внаслідок цього продуктивність оброблення помітно знижується. Велика ширина фрезерованої поверхні вимагає високої потужності приводу і досить високої жорсткості оправки з набором фрез (підвищення собівартості оброблення).
6.3. Фрезерування напрямних кількома наборами фрез.Цей спосіб є проміжним варіантом між фрезеруванням одиночними стандартними фрезами і фрезеруванням одним складним набором фрез. Повне чорнове оброблення напрямних може здійснюватися або на двох чотиришпиндельних поздовжньо-фрезерних верстатах, або на одному восьмишпиндельному (рис. 2.12).
Рис. 2.12. Фрезерування прямолінійних напрямних заготовки декількома наборами фрез (Ф – спеціальні фрези у наборі)..
Невеликі набори з декількох фрез можуть бути в основному отримані з стандартних фрез.
Цей спосіб фрезерування є економічним у серійному виробництві, коли спеціальний фрезерний верстат використовується для оброблення станин одного найменування чи декількох найменувань при малій кількості переналагоджень. При уніфікації профілів напрямних фрезерування наборами фрез може ефективно використовуватися у серійному виробництві при фрезеруванні напрямних на багатоцільових верстатах при суміщенні з фрезеруванням одиночними фрезами.
6.4. Фрезерування на багатоцільових верстатах.За допомогою такого способу оброблення можна виконати чорнове оброблення за два (а в ряді випадків – і за одне) встановлення (якщо бокова сторона станини, наприклад, А – див. рис. 2.13) не потребує чорнового оброблення).
Рис. 2.13. Схеми встановлення литої заготовки на палеті при чорновому обробленні на багатоцільовому верстаті: а) – оброблення заготовки за два встановлення; б) - оброблення заготовки за одне встановлення.
Дата добавления: 2017-01-29; просмотров: 1080;