Материальный баланс доменной плавки 2 страница
Преимущества “прямого восстановления” железа перед доменным:
- исключается дорогое и черезвычайно вредное производство кокса, почти отсутствуют характерные для коксового и доменного производства вредные выбросы серы, азота, канцерогенных органических соединений, пыли и шлака;
- отпадает надобность в энергоемких и вредных агломерационных и конвертерных цехах;
- транспортирование сырья осуществляется гидротранспортом и конвейерами, что значительно уменьшает загрязнение окружающей среды пылью по сравнению с традиционными видами транспорта с перегрузкой материалов.
Кроме указанных преимуществ, есть четвертое- перспективность усовершенствования процесса восстановления.
При улучшении энергетической ситуации в Украине экономически целесообразно получение восстановителя (Н2) электролизом из воды. В процессе восстановления водород, отбирая кислород у оксида, связывается в воду, которая снова вводится в цикл (на электролиз). То есть формируется действительно экологически чистое, практически безотходное производство (рис. 7.7).
Важным фактором такого процесса является уменьшение расхода воды и загрязнения рек и водохранилищ. Этот пример является ориентиром технико-экологического прогресса устаревших (по научной идее) технологий.
7.6. ПРОКАТНОЕ ПРОИЗВОДСТВО
Продукция прокатного производства. Прокатные станы. Сталеплавильные цехи металлургических заводов выпускают продукцию в виде стальных слитков, которые для дальнейшей переработки поступают в прокатные цехи. Здесь из слитков стали вырабатывают листы, сортовые и фасонные профили, трубы и т.д. Среди разнообразных видов прокатного производства имеются готовые изделия, например рельсы, балки, трубы и др., и заготовки, требующие дальнейшей обработки ковкой, штамповкой, волочением или резанием (рис. 7.8).
|
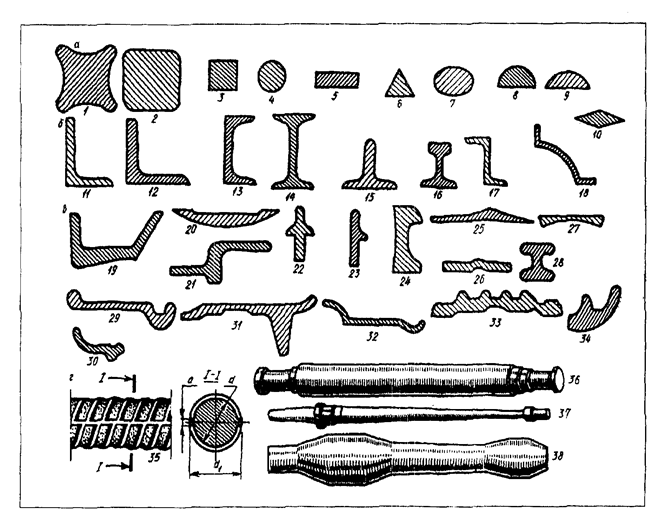
Совокупность профилей с различными формой и размерами сечений называется сортаментом проката.
Сортамент стального проката делится на пять групп: сортовой прокат, листовой прокат, трубы, периодический прокат и специальный прокат (в том числе гнутые профили).
Сортовой прокат разделяется на простой и фасонный (сложного профиля). К простому прокату относят профили с простой геометрической формой сечения – круг, квадрат, шестигранник, овал и т.д. (рис. 7.8, а)
К сортовому прокату фасонного профиля относятся угловая сталь, швеллер, двутавр, тавр, рельс, зетовая, колонная и ромбовидная сталь (рис.7.8,б)
К специальным видам проката относят продукцию законченной формы, изготовленную по заказам отдельных министерств (рис.7.8,в). Такой продукцией могут быть накладки (24) и подкладки (25) для рельсов, обод автомобильного колеса (29), бортовое кольцо (34), башмак гусеницы трактора (31) и т.д.
Прокат периодического профиля (рис. 7.8,г) представляет собой полосу или пруток, поперечное сечение которых изменяется по длине проката, воспроизводя форму будущей детали. Этот вид проката может с успехом применяться в качестве фасонных заготовок в кузнечном производстве и заготовок под окончательную механическую обработку. При этом значительно снижается объем работ и отходы металла в стружку.
Листовой прокат разделяют на толстолистовой, тонколистовой и фольгу. К толстолистовому прокату относится броневая, котельная, резервуарная сталь, к тонколистовому – кровельная, трансформаторная, электротехническая сталь, жесть и др. Стальные трубы разделяются на две группы: бесшовные (цельнотянутые) и сварные.
В последнее время большое развитие получило производство гнутых профилей из холодно- и горячекатаных полос и лент. Гнутые профили сложной конфигурации применяются в автотракторной, авиационной промышленности и в строительстве. Они изготовляются на специальных роликогибочных машинах и поставляются в виде отдельных заготовок или бухт ленты определенного профиля. Сортамент гнутых профилей превышает 400 разновидностей.
Для придания металлу соответствующей формы его в нагретом или холодном виде прокатывают, т. е. пропускают между вращающимися валками прокатных станов. Рабочие валки прокатных станов имеют либо ровную поверхность, если они прокатывают, например, лист, либо поверхность с более или менее сложным профилем для получения соответствующего проката. При прокате слитка или другой заготовки происходит изменение их формы; при этом уменьшается поперечное сечение и увеличивается длина. Для облегчения процесса прокатки крупные слитки или заготовки предварительно нагревают до температуры, при которой обычно производят ковку металла.
Прокатные цехи металлургических заводов оборудованы прокатными станами различных размеров, типов и назначения. Различают двух-, трех- и многовалковые станы (рис. 7.9). Валки располагают горизонтально или вертикально.
Рис. 7.9. Схема расположения валков в прокатных станах
а – в двухвалковом;
б – в трехвалковом;
в – в четырехвалковом
Крупнейшими из прокатных станов являются блюминг и слябинг. На блюмингах производят первую прокатку стальных слитков весом до 20 т и превращают их в заготовки (блюмы) сечением от 200х200 до 400х400 мм. Слябинги служат для прокатки из таких же крупных слитков стали листовых заготовок (слябей) толщиной до 225 мм и длиной до 5 м. Слябинги устанавливают главным образом в листопрокатных цехах металлургических заводов. Производительность крупнейших прокатных станов очень высока. Мощность блюмингов достигает 5000 кВт и более; диаметр их рабочих валков 800-1400 мм.
|

Волочение. Прокатные цехи оборудуют также волочильными станами, на которых заготовку протягивают обычно в холодном состоянии через отверстие (фильеру) с сечением, меньшим сечения заготовки (рис. 7.10). Методом волочения производят тонкую проволоку (от четырех до сотых долей миллиметра), калиброванные прутки, тонкие трубки и т. п. (рис. 7.11).
Рис. 7.11. Схема волочения труб
а – без уменьшения толщины стенки;
б – с уменьшением толщины стенки
Волочение обеспечивает высокую точность размеров и чистоту поверхности получаемых изделий, что имеет особое значение при малых их сечениях. В результате волочения металл уплотняется и приобретает лучшие свойства.
Трубопрокатное производство. Трубопрокатное производство часто выделяют в специальные трубопрокатные (трубные) предприятия, хотя по существу они являются металлургическими заводами со специализированным прокатным цехом.
Существуют три способа производства труб: литьем, прокаткой и прошивкой заготовки.
Литьем производят чугунные трубы; прокаткой и прошивкой – стальные. Стальные трубы могут быть сварными и цельнотянутыми (бесшовными). Для изготовления сварных труб предварительно прокатывают полосовую сталь нужной ширины. Затем полосы свертывают в трубу, нагревают и прокатывают на особых прокатных станах. При этом кромки свернутой полосы свариваются, образуя шов трубы. Применяют также газовую и электрическую сварку труб.
Для получения цельнотянутых труб заготовку в виде соответствующих размеров круглого стержня прошивают на прошивном стане. В результате получают гильзу, которую затем дополнительно прокатывают. Таким образом, получают бесшовные трубы, отличающиеся повышенной прочностью.
Созданы уникальные станы для непрерывной и автоматической прокатки труб. Ассортимент труб, выпускаемых трубными заводами, очень широк: от трубок диаметром в десятые доли миллиметра и толщиной стенки в сотые доли миллиметра (их получают методом волочения) до огромных газопроводных труб.
Технология непрерывного слитка и бесслитковой прокатки.В металлургической промышленности внедряется новая технология прокатного производства - технология непрерывного слитка и бесслитковой прокатки. В основе этой технологии лежит получение при помощи специальной разливочной машины методом вытягивания охлаждаемого металла непрерывного слитка стали, который либо разрезается на заготовки требуемых размеров, либо проходит через систему прокатных станов, превращающих непрерывный слиток в соответствующие виды проката. Таким образом, исключается ряд обычных для старой технологии операций – разливка стали в изложницы, охлаждение слитков, их повторный нагрев, обрезка, обжим на блюминге и т.д. Это упрощает и значительно ускоряет процессы прокатки, делает их непрерывными и концентрирует в одном комплексном агрегате, соединяющем сталеплавильную печь, разливочную машину и систему прокатных станов. При этом резко сокращаются неизбежные при обычной прокатке большие отходы металла.
7.7. Цветная металлургия
Цветная металлургия включает в себя добычу и обогащение руд, производство и обработку цветных металлов и сплавов. Как и в черной металлургии, производственный комплекс состоит из горнодобывающих предприятий (рудников, карьеров), обогатительных фабрик, металлургических и металлообрабатывающих заводов.
Цветные металлы и сплавы получили широкое применение в современном машиностроении. Особенно возросла их роль в связи с развитием реактивной техники и атомной энергии, освоением космического пространства и развитием радиоэлектроники. Это обусловлено их особыми свойствами: высокой электро- и токопроводностью, коррозийной стойкостью, жаропрочностью, малой удельной массой и др.
В настоящее время цветная металлургия извлекает из руд цветные металлы более 70 наименований. Цветные металлы делят на 4 группы: тяжелые – медь, никель, свинец, цинк, олово; легкие – алюминий, магний, титан, кальций и др.; благородные – золото, серебро, платина; редкие – молибден, вольфрам, ванадий, уран и др. Наибольшее применение в промышленности находят медь, алюминий, цинк, свинец, олово, никель, титан, магний.
Содержание цветных и редких металлов в рудах крайне низко. Для получения одной тонны цветного металла добывается и перерабатывается от сотен до десятков тысяч тонн сырья. В связи с этим в цветной металлургии особое значение имеет подготовка руд, которая включает процессы дробления, измельчения, усреднения, обогащения и окускования.
В результате такой подготовки исходное сырье получают в виде концентратов с высоким содержанием металла и его оксидов.
В рудном сырье вместе с «основными» элементами (алюминием, медью, свинцом, никелем и др.) содержатся попутные – золото, серебро, платина, кобальт, кадмий и др., причем их ценность иногда превосходит ценность «основных» металлов. Это требует комплексной переработки руд для извлечения из них всех ценных компонентов. При промышленной переработке руд рациональнее используются природные ресурсы, и предотвращается загрязнение окружающей среды.
В результате этого металлургическое производство цветной металлургии характеризуется большим разнообразием технологических процессов получения металлов. Основными способами получения цветных металлов являются пирометаллургические, гидрометаллургические и электрометаллургические процессы.
Пирометаллургические процессы проводят при высоких температурах. Основные процессы: обжиг, плавка, конвертирование, рафинирование и дистилляция. Эти процессы применяются при производстве меди, никеля, кобальта, свинца, олова и др. Рафинирование заключается в обработке расплавленных черновых металлов с помощью присадок (солей, щелочей), окислением примесей, вакуумированием расплава и т.д. Ряд металлов, которые относятся к легкоиспаряющимся, получают методом дистилляции и последующую их очистку от примесей осуществляют методом многократной перегонки. Дистилляцию проводят в ретортных печах (производство цинка), шахтных печах (производство свинца, цинка, олова), в печах кипящего слоя (производство титана).
Гидрометаллургические процессы заключаются в извлечении металлов из руд, концентратов и отходов различных производств при температуре 20-200°С и обычном или повышенном давлении с помощью водных растворов химических реактивов (кислот, щелочей или солей). В процессе извлечения металла из сырья, помещенного в раствор, происходит химическое взаимодействие металлов с реагентом и растворение образующихся при этом продуктов реакции (обычно солей) в воде. Эти процессы широко применяются при производстве цинка, меди, никеля и др.
Электрометаллургические процессы основаны на использовании электрического тока для проведения окислительных или восстановительных реакций. Они подразделяются на электротермические и электромеханические.
Электротермические процессы используются для извлечения цветных металлов из руд и концентратов, производства и рафинирования металлов и сплавов на их основе. В этих процессах электроэнергия является источником технологического тепла. Электротермические процессы получили широкое применение при плавке и возгонке металлов в никелевой промышленности, при переработке цинковых концентратов, в производстве свинца, олова, редких металлов.
Электрохимические процессы используются для производства цветных металлов на основе электролиза водных растворов (при обычных температурах) и расплавленных солей (при повышенных температурах). Эти процессы широко используются в производстве алюминия, магния и др.
Обычно электрометаллургическим процессам предшествуют гидрометаллургические, реже пирометаллургические процессы.
Металлообрабатывающие заводы цветной металлургии производят прокатно-тянутую продукцию: различные полуфабрикаты – от плит массой 5 т до фольги толщиной 5 мкм; от медных труб диаметром до 500 мм до никелевых с толщиной стенки 0,05 мм.
Всего на заводах цветной металлургии изготавливается более 200 тыс. типоразмеров листов, лент, труб, прутков, проволоки, профилей и фольги, полуфабрикатов, отличающихся точностью размеров, однородностью свойств, заданными физико-механическими характеристиками.
7.8. Технология порошковой металлургии
Порошковая металлургия – это отрасль техники, включающая изготовление порошков из металлов и их сплавов и получения из них заготовок и изделий без расплавления основного компонента. Этим путем можно создавать материалы из различных компонентов с резко отличающимися свойствами и температурами плавления, новые материалы с разнообразным комплексом физико-механических свойств. Порошковая металлургия используется как для создания принципиально новых материалов и изделий из них, так и для изготовления самой широкой номенклатуры конструкционных деталей общего назначения.
Процесс изготовления деталей из порошковых материалов заключается в получении порошка исходного материала, составлении шихты, прессовании и спекании изделий. Методами порошковой металлургии получают:
- твердые сплавы для режущего, бурового, волочильного инструмента, а также детали, подвергающиеся интенсивному изнашиванию;
- высокопористые материалы для изготовления фильтров, используемых для очистки жидкостей от твердых включений, пыли, воздуха, газа и т.д.;
- антифрикционные материалы для производства подшипников скольжения, втулок, вкладышей и других деталей, работающих в тяжелых условиях эксплуатации;
- фрикционные материалы для получения деталей узлов трения, сцепления и тормозных систем машин;
- жаропрочные и жаростойкие материалы для производства изделий, работающих в условиях высоких температур и сильно агрессивных газовых средах;
- материалы сложных составов (псевдосплавов) для изготовления электрических контактов, которые получить другими способами невозможно;
- магнитные материалы для изготовления постоянных магнитов, магнито-электриков, ферритов и т.д.
Получение металлических порошков является важнейшей операцией технологического процесса изготовления деталей и порошковых материалов, от которых зависят их основные свойства.
В настоящее время существуют различные методы изготовления порошков, каждый из которых обеспечивает определенные их характеристики. Все известные способы производства порошков условно разделяют на механические и физико-механические.
Механические методы получения порошков – дробление и размол, распыление, гранулирование – характеризуются переработкой материалов в порошок без изменения их химического состава.
Физико-химические методы – восстановление, термическая диссоциация карбонатных соединений – отличается тем, что получаемый порошок по химическому составу существенно отличается от исходного материала.
Иногда с целью улучшения характеристик материала применяют комбинированные методы получения порошков: при распылении расплавленный металл сначала гранулируют, затем обжигают в защитной среде водорода, при электролизе получают плотные, но хрупкие продукты, которые затем размалывают.
К технологическим свойствам порошков относятся: насыпная плотность, текучесть, прессуемость и формуемость.
Насыпная плотность – отношение массы свободно насыпанного порошка к занимаемому объему. Чем крупнее частицы и правильнее их форма, тем больше насыпная плотность порошка.
Текучесть порошка определяется скоростью истечения его через отверстия заданного размера. Хорошая текучесть порошка необходима для быстрого и равномерного заполнения им пресс-формы.
Прессуемость порошков – это способность их уплотняться при формовании изделий в зависимости от давления.
Формуемость порошка характеризуется способностью заготовок сохранять заданную форму после уплотнения порошка при минимальном давлении.
От технологических свойств порошков зависит их дозирование, заполняемость полостей пресс-форм, процесс прессования изделий и их усадка после спекания.
Физические свойства порошков характеризуются формой частиц, гранулометрическим составом порошков, их удельной поверхностью и микротвердостью частиц. Эти свойства порошков существенно влияют на плотность, прочность и однородность свойств формируемых изделий, давление прессования, а также на процессы уплотнения и спекания порошковых материалов.
Приготовление шихты производят в мельницах, смесителях и др., прессование – в стальных пресс-формах, спекание – в три этапа (при температуре 150°С, при половинной температуре плавления и при температуре, большей температуры рекристаллизации) в печах различного типа, работающих периодически или непрерывно.
При необходимости порошковые изделия подвергают отделочным операциям: калиброванию, обработке резанием, термической и химико-термической обработке, повторному спеканию и повторному прессованию (для изделий сложной формы).
Применение методов порошковой металлургии для изготовления изделий позволяет достигать высокой производительности труда и значительной экономии средств как за счет повышения качества и прочности изделий, так и за счет снижения потерь металла. Изделия, изготовленные методами порошковой металлургии, обладают более высокими качествами, чем изделия, полученные на металлорежущих станках. Порошковая металлургия позволяет создавать материалы и изделия с особыми свойствами, которые нельзя получить другими методами.
В Украине производство порошков налажено на Броварском заводе порошковой металлургии.
ОСНОВНЫЕ ПОНЯТИЯ
Металлургический комбинат
Чугун
Сталь
Флюсы
Агломерат
Окатыши
Доменная печь
Доменный шлак
Кислородный конвертер
Дуговая электропечь
Индукционная электропечь
Прямое восстановление железа
Прокатка
Сортовой прокат
Ассортамент
Блюминг
Слябинг
ВОПРОСЫ ДЛЯ ОБСУЖДЕНИЯ
1. Чем отличается металлургический завод от металлургического комбината?
2. Дайте определение термину «чугун».
3. Сырье для производства чугуна.
4. Назначение кокса при производстве чугуна.
5. Агломерат и окатыши, их производство и использование.
6. Прямое и косвенное восстановление железа.
7. Маркирование чугунов.
8. Основные технико-экономические показатели доменного производства.
9. Дайте определение термину «сталь».
10. Сырье, используемое в кислородном конвертере при производстве стали.
11. В чем суть производства стали в кислородном конвертере.
12. Технология производства стали в мартеновских печах, выплавление стали и их использование.
13. Особенности производства стали в электродуговых и индукционных печах, выплавляемые стали.
14. Маркирование сталей.
15. Назначение прокатных станов.
16. Перечислите группы сортамента стального проката.
17. Что относится к простому прокату?
18. Что относится к сортовому прокату?
19. Чем отличаются блюминги от слябингов?
20. С какой целью применяется волочение?
21. Особенности трубопрокатного производства.
ГЛАВА 8. СИСТЕМА ТЕХНОЛОГИЙ МАШИНОСТРОЕНИЯ
8.1. Понятие о машиностроительном комплексе
Машиностроительный комплекс– это совокупность отраслей промышленности, изготовляющих важнейшие средства производства, предметы потребления (автомобили, бытовая техника, инвентарь и др.), а также продукцию оборонного значения. В его состав входят: станкостроение, приборостроение, электротехническая и электронная промышленность, энергетическое, транспортное, строительно-дорожное, химическое, нефтяное, сельскохозяйственное машиностроение, авиационная, автомобильная, тракторная промышленность и ряд других отраслей машиностроения.
Этот комплекс охватывает тысячи предприятий, институтов, конструкторских, технологических организаций. По своим масштабам и численности работающих машиностроение – самая крупная отрасль промышленности; в ней занято около 1/3 всех работающих, а номенклатура выпускаемых изделий составляет десятки тысяч наименований.
По масштабам выпуска продукции различают три вида машиностроительного производства: массовое, серийное, единичное. К массовому производству относится выпуск таких широкоиспользуемых машин и изделий, как автомобили, трактора, электродвигатели, холодильники,
![]() |
|
часы, стиральные машины, подшипники и т.д. Серийно выпускаются насосы, компрессоры, вентиляторы, металлорежущие станки, прессы, летательные аппараты и др. Единичным (индивидуальным), как правило, является производство особо крупных и уникальных машин и оборудования, таких как прокатные станы, тепловые и гидравлические турбины, мощные прессы, крупные морские суда, космические аппараты и др.
Научно-технический прогресс в машиностроении определяет уровень и производственные базы всех отраслей народного хозяйства, а степень развития самого машиностроения является показателем технической зрелости современного индустриального производства. Технологический переворот во всех сферах производства немыслим без совершенствования машин, оборудования, приборов, средств механизации и автоматизации.
Машиностроение Украины должно осуществить быстрый переход к производству новых поколений машин и оборудования, способных обеспечить внедрение прогрессивных технологий, и в первую очередь энерго- и ресурсосберегающих, открыть путь к автоматизации всех стадий производства. Первостепенное внимание должно быть уделено выпуску современных станков, кузнечно-прессового, литейного, сварочного и другого прогрессивного оборудования, компьютеризации, механизации и автоматизации машиностроительного производства.
8.2. Понятие о технологии машиностроения
Для изготовления любой машиностроительной детали необходимо разработать технологию (см. рис. 8.1.), т.е. решить сложную многовариантную задачу – учесть исходные данные и условия, оценить возможные технико-экономические и социальные параметры различных решений. Объем производства, традиции, уровень квалификации кадров, состояние оборудования – все это влияет на рациональность принимаемого решения. В одном случае выгодной оказывается слесарная обработка заготовок, в другом – на токарном автомате, в третьем – штамповка. В разных условиях какие-то этапы отсутствуют, какие-то становятся трудоемкими и сложными, но «сумма технологий» в машиностроении (рис. 8.2) сохраняется для деталей самого различного назначения, размеров, свойств материалов – сближаются технологии изготовления коленчатого вала для мощного двигателя судна и для легкового автомобиля, шестерен мощного редуктора и обычных часов, огромных труб и обода велосипедного колеса. Меняются станки, инструменты, но главное остается: перемещают части объема заготовки (обработка давлением, литье), либо с заготовки снимают лишний материал (обработка металлов резанием).
Рис. 8.2. «Сумма технологий» в машиностроении,
или путь от руды до машины
Любая технологическая структура состоит из одних и тех же элементов, т.е. имеется общность структуры токарного или шлифовального станка, пресса и автомобиля (рис. 8.3). Различия же лишь в движениях заготовки и инструмента, величине и характере приложения технологического усилия. Однако применение различных машин и технологий приводит к разным результатам. Разница особо заметна в заготовительном производстве, а от качества, прогрессивности заготовки существенно зависят все последующие этапы обработки и даже сборка машин.
![]() |
Рис. 8.3. Универсальная структурная схема технологической машины
8.3. Литейное производство
Одним из основных способов изготовления заготовок в машиностроительном производстве является получение их заливкой расплавленного металла в соответствующие формы. Ввиду того, что литьем можно получить заготовки и для очень сложных по форме деталей и что получение их таким способом экономически эффективно, литье имеет очень широкое применение. Литые части составляют половину, а иногда и до 80% общего веса машин.
Соответственно большое значение в составе машиностроительного завода имеет литейный цех (или специализированный литейный завод, снабжающий отливками ряд машиностроительных предприятий).
Большую часть отливок производят из чугуна. Сырьем для чугунолитейного производства служит главным образом литейный (серый) чугун, получаемый в виде чушек с металлургических заводов. Кроме чушкового чугуна в шихту добавляют также чугунный лом, отходы литья, стружку и другие отходы металлообработки. Стружку и другие мелкие отходы во избежание сильного выгорания их в процессе плавки прессуют для получения из них брикетов. Крупный лом, наоборот, разбивают на куски при помощи копра.
|

Литье производят не только из чугуна, но также из стали и сплавов цветных металлов.
Плавку производят главным образом на коксе (иногда на термоантраците) с применением флюса (известняка). По сравнению с доменной плавкой руды расход топлива и флюса при плавке шихты в литейных цехах невелик: кокса расходуется примерно 10% от веса металлической части шихты, флюса – 2,5-5%.
Плавку чугуна производят преимущественно в вагранках, подобных по конструкции доменным печам, но значительно меньших размеров (рис. 8.4). В отличие от доменной печи шахта вагранки имеет цилиндрическую форму. Внутренний диаметр шахты бывает от 0,5 до 3 м, а высота – 3,5-5,5 м. Загрузку вагранки отдельными слоями шихты производят через колошник, а расплавленный чугун скапливается в горне и копильнике, откуда его выпускают в ковш для разливки в формы.
Производительность вагранок в зависимости от их размеров составляет 1,5-10 т и более жидкого металла в час.
Дата добавления: 2016-03-27; просмотров: 966;