Дислокационная структура и прочность металлов
Прочность металлов, получаемая при испытаниях, на 2, а то и 3 порядка ниже теоретической. Это объясняется наличием в реальном металле концентраторов напряжений, металлургических дефектов и дефектов кристаллической решетки, важнейшими из которых являются дислокации.
Теоретической прочностью обладает совершенно бездефектный материал, имеющий идеально построенную, однородную во всех ее частях кристаллическую решетку. При его нагружении возникающие напряжения стремятся разорвать все совершенно одинаковые межатомные связи плоскости.
При наличии дефектов кристаллической решетки после небольшой упругой деформации происходит пластическая, а точнее упруго-пластическая деформация. При этом начинает действовать принципиально иной, так называемый дислокационный механизм упруго-пластической деформации, развитие которой может завершиться разрушением металла. При наличии в металле металлургических дефектов или концентраторов напряжений разрушение наступает раньше и протекает в течение значительно более короткого времени.
1.5.1. Понятие о дислокациях и других дефектах
кристаллической решетки
Кристаллическая решетка реального металла не является геометрически идеальной. В ее узлах нередко отсутствуют атомы, а в зернах очень часто между полными кристаллографическими плоскостями, идущими от границы до границы зерна, находятся так называемые экстраплоскости, протяженность которых ограничивается только частью размера зерна. Существуют и другие дефекты.
Рассмотрим наиболее характерные дефекты КР металлов, известные под названием точечных и линейных.
К точечным дефектам относятся вакансии и внедренные атомы.
Вакансии – это «пустые» узлы КР, то есть места, где по той или иной причине отсутствуют атомы.
Атомы внедрения – это атомы, находящиеся не в узлах КР, а в ее междуузлиях. Ими могут быть атомы данного, или примесного элемента.
Наиболее распространенными, и очень важными с точки зрения формирования прочностных свойств металлов являются дефекты, имеющие протяженность только в одном направлении, или линейные дефекты. Их принято называть дислокациями.
Образуются дислокации в результате локальных или местных смещений кристаллографических плоскостей, происходящих в КР зерен на различных технологических этапах их формирования.
Наиболее распространенной и характерной разновидностью дислокации является краевая дислокация (рисунок 1.3). Это нижняя или верхняя линия атомов экстраплоскости.
|
Механизм генерирования (размножения) дислокаций был предсказан Френкелем в 1940 г., а разработан одновременно (и независимо друг от друга) Франком и Ридом.
Схема работы источника Франка-Рида (рисунок 1.4.):
А) закрепленная между точками А и В линия дислокации, совпадает с плоскостью (Закрепление может быть осуществлено при пересечении с другими дислокациями, чужеродными атомами и.т.п.);
Б) по мере возрастания напряжения отрезок дислокации выгибается до полуокружности;
В) при дальнейшем росте напряжений вокруг точек А и Б образуются спирали;
Г) расширение спиралей приводит к их смыканию;
Д) образуется новый цикл.
Рисунок. 1.4. Схема работы источника Франка-Рида.
Винтовая дислокация (рисунок 1.5.) формируется и перемещается при сдвиге одной части кристалла относительно другой, по какой-нибудь плоскости, под действием внешних сдвиговых сил, на один параметр решетки. При этом все атомные слои-плоскости представляют одну винтовую поверхность, закрученную вокруг линии АВ. Сама линия АВ, вокруг которой формируются геометрические и энергетические искажения в кристаллической решетке, и является винтовой дислокацией.
Рисунок 1.5. Схема винтовой дислокации.
На прочностные свойства металлов оказывают влияние и поверхностные дефекты КР. Ими являются криволинейные поверхности, ограничивающие зерна металла, а также почти плоские поверхности, разделяющие блоки (субзерна).
1.5.2 Дислокационный механизм
упругопластической деформации
|
Образованию и перемещению пачек скольжения в зернах предшествует лавинообразный процесс передвижения дислокаций по определенным плоскостям скольжения в кристаллической решетке.
Системы скольжения включают те параллельные плоскости, по которым могут передвигаться дислокации. Насчитывается до трех действующих систем. Наиболее легкие условия скольжения в первой, самые трудные в третьей.
|
Знание дислокационной природы и особенностей механизма пластической деформации металла позволяет уяснить важный вопрос о причине более высокой прочности мелкозернистого металла по сравнению с крупнозернистым.
Вытягивание зерен в процессе деформации связано с выходом на их границы дислокаций, а также перемещением пачек скольжения. Оно сопровождается поворотом самих расслаивающихся зерен под действием внешней силы. Однако этим процессам препятствуют границы зерен. Чем мельче зерна, тем больше суммарная площадь их границ и тем больше сопротивление пластической деформации.
1.5.3. Основные элементы дислокационной структуры
К дислокационной структуре относятся все факторы, влияющие на передвижение дислокаций под действием приложенной силы. Основными из них являются: границы зерен и субзерен, атмосферы Коттрелла, атмосферы Сузуки и высокодисперстные твердые включения – стопоры.
Дислокации. Характеристикой, непосредственно влияющей на сопротивление сплава пластической деформации, является плотность дислокаций, то есть их суммарная длина, приходящаяся на единицу объема металла.
Согласно теории Одинга, зависимость между прочностью металла s и плотностью дислокаций r может быть представлена графиком (рисунок 1.8.).
|
На участке АБ по мере увеличения плотности дислокаций наблюдается снижение прочности.
В точке В, при плотности дислокаций уменьшение прочности прекращается и начинается ее постепенный рост. Это объясняется тем, что с увеличением r, перемещение дислокаций затрудняется в связи с тем, что они начинают передвигаться не по параллельным, а по пересекающимся плоскостям, тем самим препятствуя перемещению друг друга.
|
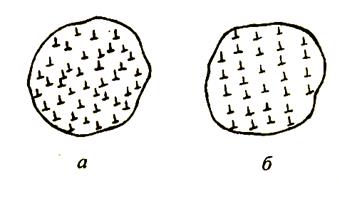
При наличии таких стенок, расположенных вдоль границ зерен, прочность металла выше.
Атмосферы Котттрела. Эти элементы дислокационной структуры формируются в результате диффузии к дислокациям атомов, с очень малыми радиусами (для стали это атомы углерода и азота).
Атмосферы Сузуки образуются на основе поверхностных дефектов упаковки кристаллической решетки. Эти дефекты оказывают влияние на процесс прохождения дислокаций во время время пластической деформации.
К атмосфере Сузуки относят также искажения в кристаллической решетке, которые имеют большую протяженность в двух измерениях, и незначительную в третьем.
Высокотвердые включения – стопоры. Представляют собой очень мелкие частицы очень твердых химических соединений – карбидов, нитридов. Они препятствуют свободному движению дислокаций. Дислокации вынуждены или продираться между стопорами или переползать через них благодаря образующимся над ними вакансиями. Но для этого требуется наращивание внешней силы.
|
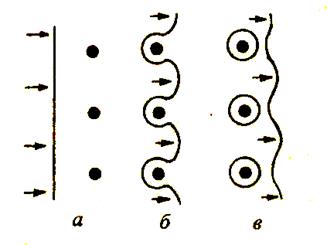
В случае нагрева происходит коагуляция частиц, размеры их возрастают, увеличиваются и расстояния между ними. Перестаренный сплав разупрочняется.
Упрочнением сплавов за счет стопоров можно управлять, подбирая химический состав и подвергая сплав соответствующей термической обработке.
Наклеп металла.
Из многолетнего опыта известно, что после ковки холодного металла, заметно возрастают его прочность и твердость. В то же время он становится хрупким, то есть уменьшается его пластичность. Это явление получило название наклеп. Наклепом называют как сам процесс, так и получающийся при этом результат.
В машиностроении наклеп используется для поверхностного упрочнения деталей. Наклеп уменьшает вероятность усталостного разрушения.
Тема 2. МЕХАНИЧЕСКИЕ СВОЙСТВА МАТЕРИАЛОВ
И МЕТОДЫ ИХ ОПРЕДЕЛЕНИЯ
Дата добавления: 2016-02-02; просмотров: 5257;