МЕТОДЫ ФИКСАЦИИ АТМОСФЕРНОГО АЗОТА
Технология связанного азота
Под связанным азотом понимают азот, находящийся в виде различных соединений — аммиака, азотной кислоты и ее солей, карбамида, аминов, аминокислот, белков и т. д.
Пополнение запасов азота в почве в усвояемом растениями виде, т. е. в виде минеральных азотных удобрений, составляет исключительно важную народнохозяйственную задачу, от решения которой во многом зависит благосостояние общества. Соединения азота играют весьма значительную роль в промышленности. Производства красителей, некоторых пластических масс, химических волокон, взрывчатых веществ и порохов, медикаментов других продуктов потребляют соединения азота. Источников связанного азота, имеющих промышленное значение, в природе крайне мало. В Чили и Южной Африке имеются крупные запасы натриевой селитры, истощающиеся в результате интенсивной добычи. Основным же практически неисчерпаемым источником азота служит атмосферный воздух. Однако сами растения или почвенные микроорганизмы, за исключением некоторых бактерий, поселяющихся в корнях бобовых, не в состоянии усваивать непосредственно азот атмосферы.
МЕТОДЫ ФИКСАЦИИ АТМОСФЕРНОГО АЗОТА
Вследствие большой инертности азота долгое время не удавалось найти способы фиксации его. Лишь в начале XX в. были найдены три метода синтеза соединений из элементного азота: дуговой, цианамидный и аммиачный.
Дуговой метод основан на соединении азота с кислородом при высокой температуре (в пламени электрической дуги). В основе этого метода лежит эндотермическая обратимая реакция взаимодействия азота и кислорода, протекающая без изменения газового объема:
N2 +O2 = 2NO,DH = +180 кДж
Высокая инертность азота приводит к тому, что эта реакция с заметной скоростью начинает протекать лишь при очень высоких температурах (более 1500 К). При повышении температуры одновременно увеличивается и выход оксида азота (II). При температуре электрической дуги (а именно при этой температуре скорость синтеза становится приемлемой для практического применения) выход NO тем не менее достигает лишь нескольких процентов (рис. 1). Поэтому дуговой метод, являясь слишком энергоемким, не нашел большого практического применения.
В настоящее время этот метод начинает возрождаться на основе применения плазменных процессов.
|
|
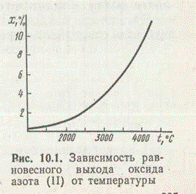
Цианамидный метод основан на способности тонкоизмельченного карбида кальция при температуре около 1000°С взаимодействовать с азотом по уравнению
СаС2 + N2 = CaCN2 + С, DH = 302 кДж
Образование цианамида кальция протекает через цианид, который разлагается по схеме
Са (CN)2 ® CaCN2 + С
Процесс синтеза CaCN2 любопытен тем, что он автокаталитичен — наличие цианамида кальция ускоряет процесс его получения и позволяет снизить температуру процесса.
Для азотирования карбида кальция применяют преимущественно периодические ретортные печи. Высокая энергоемкость процесса и общая отсталость производства привели к тому, что теперь доля выпуска связанного азота цианамидным методом весьма незначительна.
Аммиачный метод фиксации азота заключается в соединении азота и водорода с получением аммиака по уравнению реакции
N2+3H2 D 2NH3, DH = –112 кДж (при 500°С и 30 МПа)
Этот метод имеет экономическое и технологическое преимущество перед остальными способами связывания элементного азота.
Первый завод по производству синтетического аммиака был построен в 1913 г., и за короткий период (15—20 лет) аммиачный метод практически полностью вытеснил все остальные способы.
ТЕХНОЛОГИЯ АММИАКА
ХТС производства аммиака состоит из нескольких подсистем — получения азотоводородной смеси; ее очистки; собственно синтеза аммиака; отделения аммиака от непрореагировавшей азотоводородной смеси и т. п. Успешное функционирование каждой из подсистем и ХТС в целом зависит от многих факторов. Рассмотрим основные из них.
ПОЛУЧЕНИЕ И ОЧИСТКА АЗОТОВОДОРОДНОЙ СМЕСИ
Азот для приготовления азотоводородной смеси получают методом сжижения воздуха с последующей ректификацией, осуществление которой возможно благодаря различной температуре кипения отдельных компонентов. Под атмосферным давлением азот кипит при —195,8°С, кислород — при —183°С. Разница в 12,8°С вполне достаточна, чтобы жидкий воздух разделить ректификацией на технически чистые азот и кислород.
Чаще всего процесс синтеза аммиака ведут не из азота и водорода, полученных раздельно, а из азотоводородной смеси, которую обычно готовят конверсией метана и оксида углерода с водяным паром и кислородом воздуха.
Катализаторы получения синтез-газа и синтеза аммиака отравляются некоторыми веществами, присутствующими в исходном сырье — сероводородом, органическими соединениями серы (COS, CS2, C4H4S, C6H5HS и др.), а катализаторы синтеза аммиака еще и СО2, СО. Поэтому газы, идущие на производство синтез-газа, должны быть тщательно очищены от соединений серы, а синтез-газ необходимо полностью освободить от СО и СО2. Рассмотрим основные приемы очистки газов.
Очистка природного газа от сернистых соединений в современных высокопроизводительных агрегатах осуществляется в две стадии. Первой стадией является каталитическое гидрирование сернистых соединений на алюмокобальтмолибденовом или алюмоникельмолибденовом катализаторах при 350—400°С и давлении около 3 МПа. При этом происходит образование сероводорода:
COS + Н2 ® H2S + СО
CS2 + 4H2®2H2S + CH4
C2H4S + 4Н2 ® H2S + С4Н10
На второй стадии происходит хемосорбционное поглощение сероводорода специальным поглотителем (ГИАП-10), содержащим оксид цинка, с которым сероводород при 390—410°С образует сфалерит
H2S + ZnO ® ZnS + Н2О
Поскольку произведение растворимости ZnS равно 1,9×10–22, этот метод обеспечивает высокую степень очистки. При повышенном содержании сернистых соединений в исходных газах применяют дополнительно адсорбционную очистку с использованием синтетических цеолитов (молекулярных сит), таких, например, как NaX. Сорбция производится при комнатной температуре, а регенерация сорбента (десорбция) при нагревании до ~200°С.
Очистка конвертированного газа. В конвертированном газе наряду с азотом и водородом содержатся оксиды углерода, которые являются сильными ядами для катализатора синтеза аммиака, поэтому синтез-газ должен быть тщательно очищен от этих примесей.
Очистку газа осуществляют различными методами: 1) адсорбцией примесей твердыми сорбентами; 2) абсорбцией жидкими сорбентами; 3) конденсацией примесей глубоким охлаждением; 4) каталитическим гидрированием. Очистка твердыми сорбентами в промышленной практике встречается редко. Очистка методом конденсации с применением глубокого холода используется при получении азотоводородной смеси из коксового газа. Каталитическое гидрирование применяется как завершающаяся стадия очистки для удаления небольших количеств СО, СО2 и О2. Большое значение в промышленной практике имеет метод очистки жидкими сорбентами, в основе которого лежат типичные абсорбционно-десорбционные процессы.
Очистка от СО2 в отечественных схемах осуществляется преимущественно двумя способами — поглощением растворами моноэтаноламина и горячими активированными растворами поташа (К2СО3). Рассмотрим очистку раствором моноэтаноламина, в основе которой лежит способность моноэтаноламина (NH2CH2СН2ОН или для краткости R—NH2) образовывать с СО2 карбонаты и гидрокарбонаты:
R—NH2 + СО2 + Н2О D (RNH3)2CO3
(RNH3)2СО3 + СО2 + Н2О D 2RNH3HCO3
На практике обычно применяют 20%-ный раствор моноэтаноламина, который обладает высокой поглотительной способностью к СО2. Если очистку ведут при атмосферном давлении, то степень карбонизации моноэтаноламина не превышает 50%, а под давлением 2,5—3,0 МПа доходит до 75%. Отработанные растворы подвергаются нагреву, в результате которого происходит смещение равновесия в обратную сторону, т. е. отдувается диоксид углерода, который используется, например, в производстве мочевины, и регенерируется моноэтаноламин, возвращаемый в процесс. Содержание СО2 после очистки не превышает 0,1%. Последующая тонкая очистка газа осуществляется метанированием оксидов углерода (см. далее). После этого газ поступает на очистку от оксида углерода.
Очистка от СО осуществляется промывкой газа жидким азотом и метанированием. При промывке одновременно с оксидом углерода жидкий азот конденсирует и растворяет метан, аргон, кислород, оставшийся СО2. После такой очистки содержание СО в газе не превышает 0,002%. Дальнейшая тонкая очистка газа от СО2 и СО осуществляется метанированием.
Метанирование представляет собой каталитическое гидрирование указанных оксидов, в основе которого лежат следующие реакции:
СО + 3Н2 ® СН4 + Н2О, ΔН = –206 кДж
СО2 + 4Н2 ® СН4 + 2Н2О, ΔН = –165кДж
О2 + 2Н2 ® 2Н2О, ΔН = –483 кДж
Процесс гидрирования осуществляют при температурах ~300°С и давлении ~2,8 МПа на восстановленном таблетированном никельалюминиевом катализаторе.
ФИЗИКО-ХИМИЧЕСКИЕ ОСНОВЫ СИНТЕЗА АММИАКА
В основе процесса синтеза аммиака лежит обратимая экзотермическая реакция, протекающая с уменьшением газового объема
Равновесие этой реакции в соответствии с принципом Ле Шателье может быть смещено вправо снижением температуры и повышением давления. Причем для получения примерно 97% превращения азота и водорода в аммиак при 400°С необходимо применять давление выше 350 МПа. С понижением температуры равновесный выход также увеличивается. Зависимость равновесного выхода аммиака от температуры и давления приведена на рис. 2.
|
|
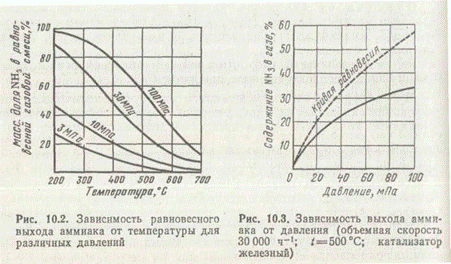
При 450°С и 10 МПа в равновесной газовой смеси содержится всего лишь около 16% NH3, а при давлении 30 МПа равновесный выход уже составляет 36%. Но влияние давления на фактический выход аммиака характеризуется затухающей кривой (рис. 3). Поэтому применять очень высокие давления экономически невыгодно.
Выход аммиака увеличивается с уменьшением температуры. Однако при этом падает скорость процесса катализа, а, следовательно, и общая производительность цеха. Даже при сравнительно высоких температурах активационный энергетический барьер молекул азота слишком велик и образование аммиака протекает крайне медленно. Для снижения энергии активации процесс синтеза ведут на твердых катализаторах при 400—500°С.
Каталитически на реакцию синтеза действуют многие металлы — марганец, железо, родий, вольфрам, рений, осмий, платина, уран и др., т. е. элементы, имеющие не полностью застроенныеd- и f-ячейки. Наиболее высокую активность проявляют железо, осмий, рений и уран. Однако осмий, рений и уран дороги и опасны в работе.
В промышленности используют разработанный ГИАП железный катализатор, промотированный А12О3, К2О, СаО и SiO2, который достаточно активен и стоек к местным перегревам. Соединения серы отравляют катализатор необратимо, а кислород и некоторые его соединения, особенно СО,— обратимо, но очень быстро и даже в ничтожно малых концентрациях.
Механизм действия катализатора в процессе синтеза аммиака может быть представлен как ряд элементарных актов: 1) диффузия азота и водорода из газового объема к поверхности зерна катализатора и в его порах; 2) активированная адсорбция азота поверхностью катализатора; 3) адсорбция водорода на адсорбированном азоте, обусловливающее химическое взаимодействие азота и водорода через промежуточные соединения их с катализатором. В соответствии с представлениями электронной теории катализа водород передает свои электроны катализатору, а азот воспринимает их от катализатора, восстанавливая электронное равновесие. Перегруппировка поверхностных соединений проходит последовательно через низшие соединения азота с водородом: имид NH, амид NH2 и, наконец, аммиак NH3; 4) десорбция аммиака с поверхности катализатора; 5) диффузия газообразного аммиака в общий газовый объем.
Многочисленными исследованиями установлено, что лимитирующей стадией собственно катализа является активированная адсорбция азота,
Зависимость выхода аммиака от объемной скорости и температуры катализа показывает, что для каждой объемной скорости имеется оптимальная температура, которой соответствует максимальный выход аммиака, а также с увеличением объемной скорости выход аммиака уменьшается. Увеличение объемной скорости от 15 000 до 120 000 ч–1, т. е. в 8 раз, снижает максимальный выход аммиака менее чем в 2 раза. Следовательно, увеличение, объемной скорости повышает производительность катализатора. Таким образом, увеличение объемной скорости газа приводит к росту производительности всей установки в целом, но к некоторому уменьшению выхода аммиака за один цикл. Это характерно для многих процессов, при осуществлении которых используют циклические схемы производства. Поэтому в таком процессе возможно значительное увеличение объемной скорости. С увеличением объемной скорости производительность в целом возрастает, но при этом возрастает и объем непрореагировавших газов, которые необходимо возвращать в цикл, что вызывает увеличение расхода электроэнергии на транспортировку газов, их нагревание, охлаждение, увеличение размеров трубопроводов и реакционной аппаратуры. Другим серьезным препятствием к увеличению скоростиявляется нарушение автотермичности процесса синтеза. При больших объемных скоростях газа в реакцию вступает меньшая доля азота и водорода и теплоты реакции оказывается недостаточно для поддержания необходимой температуры в колонне синтеза.
ПРОИЗВОДСТВО АММИАКА
Промышленные способы синтеза аммиакав зависимости от применяемого давления можно разделить на три группы: 1) под низким давлением до 10 МПа; 2) средним до 20—30 МПа и 3) высоким давлением до 75—100 МПа. В настоящее время в мировой азотной промышленности большая часть синтетического аммиака производится в системах среднего давления.
В современных агрегатах синтеза аммиака большой единичной мощности процесс ведут на плавленых железных катализаторах при 420—500°С и давлении ~32 МПа, объемной скорости 15—25 тыс. ч–1; производительность 1 м3 контактной массы составляет 20—40 т/сут.
На рис. 4 приведена схема агрегата мощностью 1360 т/сут, включающая двухступенчатую паровоздушную конверсию метана, высокотемпературную конверсию СО, моноэтаноламиновую очистку от СО2, окончательную очистку от СО и СО2 каталитическим гидрированием (метанирование) и синтез аммиака.
|
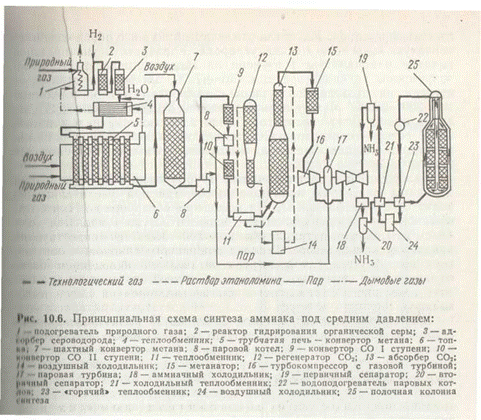
Природный газ под давлением 4 МПа после очистки от серосодержащих соединений смешивается с паром в соотношении 3,7:1, подогревается в теплообменнике отходящими газами и поступает в трубчатый конвертор с топкой, в которой сжигается природный газ. Конверсия метана с водяным паром до образования оксида углерода протекает на никелевом катализаторе при 800—850°С. Содержание метана в газе после первой ступени конверсии составляет 9—10%. Далее газ смешивается с воздухом и поступает в шахтный конвертор, где происходит конверсия остаточного метана кислородом воздуха при 900—1000°С и соотношение пар:газ=0,8:1. Из шахтного конвертора газ направляется в котел-утилизатор, где получают пар высоких параметров (10 МПа, 480°С), направляемый в газовые турбины центробежных компрессоров. Из котла-утилизатора газ поступает на двухступенчатую конверсию оксида углерода. Конверсия осуществляется вначале в конверторе I ступени на среднетемпературном железохромовом катализаторе при 430—470°С, затем в конверторе II ступени на низкотемпературном цинкхромомедном катализаторе при 200—260°С. Между первой и второй ступенями конверсии устанавливают котел-утилизатор. Теплота газовой смеси, выходящей из II ступени конвертора СО, используется для регенерации моноэтаноламинового раствора, выходящего из скруббера очистки газа от СО2.
Далее газ поступает на очистку от СО2 в скруббер, орошаемый холодным раствором моноэтаноламина, где при 30—40°С происходит очистка газа от СО2. На выходе из абсорбера газ содержит примеси кислородсодержащих ядов (СО до 0,3%, СО2 30— 40 см3/м3), которые гидрируют при 280—350°С в метанаторе на никелевом катализаторе. Теплота очищенного газа после метанатора используется для подогрева питательной воды, дальнейшее охлаждение и сепарация выделившейся воды проводятся в аппарате воздушного охлаждения и влагоотделителе.
Для сжатия азотоводородной смеси до 30 МПа и циркуляции газа в агрегате синтеза используют центробежный компрессор с приводом от паровой конденсационной турбины. Последнее циркуляционное колесо компрессора расположено в отдельном корпусе или совмещено с IV ступенью. Свежая азотоводородная смесь смешивается с циркуляционной смесью перед системой вторичной конденсации, состоящей из аммиачного холодильника и сепаратора, проходит далее два теплообменника и направляется в полочную колонну синтеза. Прореагировавший газ при 320—380°С проходит последовательно водоподогреватель питательной воды, «горячий» теплообменник, аппарат воздушного охлаждения и «холодный» теплообменник, сепаратор жидкого аммиака и поступает на циркуляционное колесо компрессора. Жидкий аммиак из сепараторов направляется в хранилище жидкого аммиака.
Содержание аммиака в оборотной азотоводородной смеси над жидким аммиаком зависит от температуры и давления. Так, при давлении 30 МПа и температуре —5°С в азотоводородной смеси остается приблизительно 2,5% NH3.
Основным агрегатом установки синтеза аммиака служит колонна синтеза. Колонны синтеза изготовляют из специальных легированных сталей. При высоких температурах и давлении аммиак и особенно водород взаимодействуют со сталью, ухудшая ее механические свойства.
Для снижения температуры стенок холодная азотоводородная смесь, поступающая в колонну синтеза, проходит вдоль внутренней поверхности цилиндрического корпуса колонны. Применяют полочные и трубчатые колонны.
|
В связи с тем что реакция синтеза экзотермична, на катализаторных полках газ сильно нагревается. При этом температура значительно отклоняется от оптимальной. Для регулирования температурного режима катализа предусмотрена подача байпасного холодного синтез-газа (патрубок 5) в каждый слой катализатора (на схеме показан только в первый). При рабочей температуре 300—520°С и давлении 32 МПа колонна синтеза указанных габаритов имеет производительность по аммиаку около 1360 т/сут.
<== предыдущая лекция | | | следующая лекция ==> |
СПОСОБЫ КРУПНОМАСШТАБНОГО ПРОИЗВОДСТВА ВОДОРОДА | | | ТЕХНОЛОГИЯ АЗОТНОЙ КИСЛОТЫ |
Дата добавления: 2016-01-20; просмотров: 7478;