Корпусных конструкций
Производственный цикл в сборочно-сварочном цехе начинается с момента получения деталей с комплектовочного участка корпусообрабатывающего цеха и заканчивается испытанием на непроницаемость и окраской готовой корпусной конструкции (там, где есть окрасочные участки). При этом выполняются различные виды работ, основные из которых: сборочные (в том числе разметка и проверка), сварочные, с последующим контролем сварных соединений, пневматические (зачистка, рубка, сверление, клепка и чеканка), тепловая или холодная правка, работы по установке деталей насыщения, контроль, а также окраска корпусных конструкций.
Сборка под сварку. Процесс сборки под сварку заключается в подготовке и предварительном соединении простых элементов конструкций в более сложные для последующего окончательного скрепления их с помощью сварки. Промежуточное (до сварки) взаимное сочетание кромок и поверхностей собираемых частей, удовлетворяющее требованиям обеспечения последующего процесса сварки, называется сопряжением. Различают линейные и поверхностные виды сопряжении. При сборке более сложных конструкций, например, секций, часто подгоняется не единичное сопряжение, а одновременно несколько сопряжении, находящихся рядом или пересекающихся друг с другом.
Трудоемкость сборочных работ, включая пригонку деталей, составляет от 40 до 50 % всей трудоемкости изготовления корпусных конструкций.
Непременным условием успешного изготовления корпусных конструкций является настройка соответствующей оснастки. В большинстве случаев это сводится к проверке формы ее рабочей поверхности: для плоских конструкций она должна быть плоской, для криволинейных — соответствовать плазовым данным. Допускаемые при этом отклонения от заданной формы регламентируются соответствующим ОСТом.
Непосредственное изготовление корпусной конструкции начинается с разметки, которая не всегда обязательна. При сборке конструкций с применением сборочно-сварочных агрегатов разметка, как правило, отсутствует. Основными документами для выполнения разметки являются данные, полученные с плаза, чертежи конструкций и другие. Разметку чаще всего производят вручную, выполняя соответствующие геометрические построения с помощью простейшего измерительного (рулетки, метры, линейки, штангенциркули, транспортиры и др.) и разметочного (чертилки, циркули, меловая нить, кернеры) инструмента. Совершенствование способов разметочных работ связано с применением оптических, в том числе и лазерных систем.
Состав размечаемых линий и знаков определяется конструкцией данного узла и секции и способами их изготовления. Например, на полотнищах плоских секций намечают линии двух взаимно перпендикулярных базовых плоскостей, от которых будут выполнять все последующие измерения, линии положения набора и насыщения, устанавливаемого при изготовлении данной секции, линии контуров узла или секции и вырезов в них и так называемые контрольные линии. Все эти линии фиксируют кернением. Допускаемые отклонения линий разметки от их требуемого положения не более 2 мм.
Кромки деталей и прилегающие к ним поверхности, подлежащие сварке, а также места приварки временных креплений и сборочных приспособлений непосредственно перед сборкой необходимо очищать от ржавчины, окалины, влаги и т. п. до чистого металла. Ширина зачищаемой полосы на 5—10 мм превышает ширину сварного шва. Зачистку производят пневматическими машинками с вставными металлическими щетками, абразивными кругами и т. п. Толщина снимаемого слоя металла при этом не должна превышать допускаемых отклонений на толщину металла, предусмотренных техническими условиями на его поставку.
При установке и ориентировании деталей, их первичном наведении и проверке необходимы сборочные базы, т. е. поверхности, линии или точки, определяющие положение собираемых элементов конструкций. В качестве сборочных баз используют основные конструктивные и вспомогательные базы. Основные базы воспроизводят на сборочной оснастке (стендах или постелях); они соответствуют обычно ОП, ДП, ПМШ судна. Вспомогательные базы служат для установки некоторых элементов, а затем необходимость в них отпадает. Примерами вспомогательной базы являются торец ранее установленного листа, разметочные риски на месте устанавливаемой детали и др.
Проверка положения элементов корпусных конструкций заключается в определении линейных или угловых отклонений относительно базовых плоскостей или линий, т. е. предусматривает линейные измерения, горизонтальное и вертикальное нивелирование.
Чтобы компенсировать возможные погрешности, возникающие при изготовлении корпусных конструкций и их последующем монтаже на построечном месте по части кромок деталей и узлов, а также монтажных кромок готовых конструкций, оставляют припуск (избыточная часть металла) шириной 20—30 мм.
По результатам проверки положения деталей и узлов производят их подгонку, в процессе которой частично или полностью тепловой резкой удаляют имеющийся по их кромкам припуск.
Для разделки кромок под сварку после удаления припуска, корня сварного шва, удаления электроприхваток и временных креплений применяют строжку — разновидность тепловой резки металлов. Существует несколько способов строжки, из которых наиболее распространены газовая и воздушно-дуговая.
Газовая строжка заключается в том, что подогретый кислородно-ацетиленовым пламенем специального резака (строгача) обрабатываемый металл частично расплавляется и сжигается в струе режущего кислорода, образующиеся окислы выдуваются на поверхность конструкции в направлении строжки. В результате на поверхности металла образуется канавка в форме полуцилиндра.
Процесс воздушно-дуговой строжки основан на расплавлении металла электрической дугой, горящей между угольным электродом и обрабатываемой деталью. Расплавленный металл удаляется из образовавшейся канавки струёй сжатого воздуха, направляемой параллельно электроду.
В отдельных случаях, когда невозможно применение тепловой резки или строжки, при подгонке деталей для удаления припусков не более 5 мм, временных креплений, а также для разделки кромок деталей под сварку допускается применять пневматическую рубку.
При выполнении сборки необходимо прилагать усилия к собираемым деталям для их смещения в требуемое положение, а также для стягивания сопрягаемых деталей. В процессе стягивания сопряжении происходит частичное упругое деформирование кромок. Необходимые стягивающие усилия зависят от типа сопряжении, зазора между сопрягаемыми элементами, формы и геометрических характеристик самих элементов, а также от характера закрепления участков, смежных с местом сопряжения.
Сборочные усилия можно прилагать по открытой или замкнутой схемам (рис. 5.3). При открытой схеме реакция сборочного усилия воспринимается внешними элементами сборочно-сварочной оснастки. При замкнутой схеме усилия воспринимаются смежными участками собираемой конструкции и на оснастку не передаются. Во втором случае требуются обычно меньшие усилия, что объясняется податливостью обоих элементов сопряжения.
Рис. 5.3. Открытая (а) и замкнутая (б) схемы обжатия
скулового листа при сборке
Для создания усилий при сборке широко применяют различные ручные приспособления (рис. 5.4). Стягивающие и прижимные приспособления закрепляют за планки или обуха, приваренные к собираемым деталям. Прихватка обухов и планок увеличивает трудоемкость сборки и вызывает опасность повреждения поверхности конструкции короткими, зачастую некачественными швами. Поверхность портится также при неизбежном удалении планок и обухов после сборки. Поэтому рациональнее использовать приспособления, исключающие приварку временных планок и обухов. Такие приспособления могут иметь механические (рис. 5.4, ж, з), вакуумные или электромагнитные захваты.
Существующие механизированные инструменты и приспособления для сборки корпусных конструкций можно разделить на специализированные и универсальные. Специализированные приспособления входят в состав механизированного оборудования участков и поточных линий, предназначенных для определенных видов собираемых конструкций, например, для изготовления тавровых балок, плоских секций и др. Универсальные механизированные сборочные инструменты представляют собой переносные стяжки (талрепы), распорки или домкраты. Они могут иметь гидравлический, пневмогидравлический или пневматический привод.
Закрепление деталей при сборке конструкций под сварку выполняют с помощью электроприхваток (жесткое закрепление) или эластичных креплений (гребенки, скобы, талрепы, струбцины). При изготовлении конструкций на механизированных линиях и участках закрепление деталей при сборке должно производиться, как правило, с помощью штатных устройств (прижимов) механизированного оборудования.
Электроприхватки выполняют электродами той же марки, которые будут применяться при сварке данного соединения. Электроприхватки должны выполняться качественно, поскольку они входят в состав сварного шва.
Установка при сборке эластичных креплений обеспечивает свободное укорочение сварных соединений в плоскости свариваемых листов и противодействует развитию угловых деформаций. Сборочные гребенки имеют длину порядка 350—450 мм и высоту около 80 мм. Их толщина должна быть в пределах 0,5S<S2<:S, но не более 24 мм (S — минимальная толщина стыкуемых листов, 52—толщина гребенки). Гребенки при сборке устанавливают параллельно друг другу под углом около 45° к сварному шву, как правило, со стороны, обратной выполнению первого прохода с приваркой к обеим сторонам листа. Удаляют гребенки после выполнения первого прохода сварного шва.
|
|
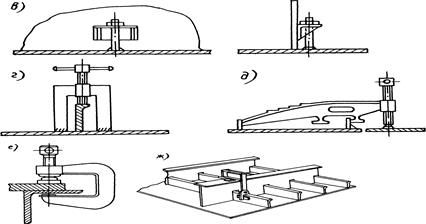
Рис. 5.4. Прижимные приспособления: а, б — Г- и П-образные скобы с клиньями;
в — болт-угольник; г — скоба с нажимным винтом; д — скоба «рыбий хвост»; е — струбцина; ж — клиновой прижим; з — прижим с талрепом
Сварка узлов и секций. Сварку узлов и секций, изготавливаемых в сборочно-сварочном цехе, выполняют в основном механизированными способами. Объем ручной сварки обычно не превышает 10 % протяженности выполняемых швов. Высокий уровень механизации объясняется использованием тех преимуществ, которые создает предварительная сборка, а именно:
конструкции можно кантовать, чтобы перевести швы в удобное для сварки положение, в закрытых помещениях исключается влияние атмосферных условий, благодаря доступности швов можно применять специализированные более производительные сварочные установки и т. д.
Все стыковые соединения в нижнем положении протяженностью более 2 м, а также имеющие наклон вдоль продольной оси не более 8° и поперек оси до 20° обычно сваривают автоматической сваркой под слоем флюса, характеризующейся высокой производительностью и качеством швов. Применяется также автоматическая сварка в среде защитных газов.
Швы тавровых соединений в нижнем положении в цехе можно выполнять полуавтоматической и автоматической сваркой под слоем флюса, а также полуавтоматической и автоматической сваркой в среде защитных газов.
Автоматическую сварку швов тавровых соединений (под флюсом и в среде углекислого газа) выполняют с помощью автоматов наклонным электродом, т. е. направленным под углом в вершину угла, образованного свариваемыми деталями. Полуавтоматической сваркой в среде углекислого газа выполняют все короткие швы стыковых и тавровых соединений. Этим способом выполняют и длинные швы пересечений элементов друг с другом, имеющие пространственное положение, отличное от нижнего. Все большее применение получает сварка порошковой проволокой.
Сварные соединения конструкций подвергают контролю, с тем чтобы убедиться в отсутствии недопустимых наружных и внутренних дефектов. Погрешности формы и внутреннего строения всегда могут встречаться в реальных сварных соединениях. Однако, если эти погрешности превышают пределы, установленные техническими условиями, то они считаются дефектами. Размеры допустимых погрешностей сварных швов оговариваются в правилах контроля, в частности, в Правилах Регистра России.
Контроль сварных соединений узлов и секций корпуса включает:
тщательный внешний осмотр и измерение сечения швов всех сварных соединений по всей протяженности;
проверку некоторых швов проникающим излучением (рентгено- или гамма-графированием); перечень таких швов приведен в Правилах Регистра;
ультразвуковой контроль некоторых швов, осуществляемый вместо контроля проникающим излучением или параллельно с ним;
проверку плотности отдельных швов путем смачивания керосином поверхности одной из их сторон после промазывания мелом другой стороны шва.
Правка сварных корпусных конструкций. Изготовление сварных корпусных конструкций сопровождается образованием так называемых сварочных деформаций, возникающих от неравномерного нагрева конструкций при сварке в условиях, исключающих свободное образование и развитие тепловых деформаций металла. Остаточные сварочные деформации корпусных конструкций разделяются на общие и местные. Общими называют деформации, которые вызывают изменение размеров и формы всей конструкции. Они проявляются в виде продольного и поперечного укорочений и изгиба конструкции как жесткой балки. Местные деформации приводят к изменению формы отдельных элементов конструкций. К местным деформациям относятся: бухтиноватость полотнищ, «домики» по стыкам и пазам свариваемых листов и др.
В тех случаях, когда остаточные сварочные деформации превышают допускаемые, конструкции подвергаются правке. Правку корпусных конструкций можно осуществить холодными способами или с применением местных нагревов.
Холодные способы правки основаны на принципе удлинения волокон сварных соединений, которые при сварке получили пластические деформации укорочения. Правка этими способами может осуществляться прокаткой сварных полотнищ в вальцах или растягиванием полотнищ на специальных растяжных машинах, правкой сварных балок на гидравлических прессах по схеме изгиба сосредоточенной силой на двух опорах, проколачиванием зон сварных соединений конструкций пневматическим молотком со специальным зубилом, а также прокаткой зоны сварного соединения в специальных установках. Физическая сущность методов правки, основанных на применении местных нагревов, заключается в следующем.
При нагреве металла волокна нагреваемых участков в процессе теплового расширения встречают противодействие со стороны окружающего холодного металла и получают пластические деформации сжатия. Толщина металла в нагретой зоне несколько (на десятые и сотые доли миллиметра) увеличивается. Утолщенная зона после охлаждения вызывает стягивание окружающих ее участков металла, в результате чего стрелка прогиба бухтины будет уменьшаться.
Нагрев конструкций в форме полос или пятен осуществляют чаще всего кислородно-ацетиленовым пламенем до температуры 650—750 °С. Применяются установки с индукционным нагревом. Ширина полос нагрева зависит от толщины металла и составляет 8—10 мм при толщине 2—3 мм и 35—40 мм при толщине 16—20 мм. Длина полос обычно не превышает тридцати толщин металла. При правке пятнами диаметр видимого пятна нагрева должен быть равен примерно четырем толщинам металла. Расстояние между полосами и пятнами нагрева принимают не более 6b, где b — ширина полосы или диаметр пятна нагрева.
Пневматические работы. К пневматическим относятся работы, выполняемые с помощью инструмента, приводимого в действие энергией сжатого воздуха. Сжатый воздух давлением 0,4— 0,6 МПа поступает к потребителю по специальным магистральным трубопроводам от заводской компрессорной станции. Пневматические инструменты могут быть ударного действия с прямолинейным поступательно-возвратным движением или с вращательным движением. К ударным инструментам относятся пневматические молотки, которые в зависимости от назначения можно разделить на рубильно-чеканные и клепальные. К пневматическим инструментам вращательного действия относятся различные пневматические машины (сверлильные, шлифовальные и др.).
Рубильно-чеканные молотки служат для подрубки кромок листов и других деталей, срубания временных сборочных приспособлений, чеканки заклепочных соединений и т. п. Клепальные молотки в отличие от рубильно-чеканных имеют, как правило, большие мощности, габариты и массу. В качестве вставного инструмента к рубильно-чеканным молоткам применяют зубила, крейцмейсели, чеканы и пр. (рис. 5.5), а к клепальным—бойки, обжимки и пр. Для прижима закладной головки заклепки в процессе клепки применяют поддержки, форма, размеры и масса которых зависят от конструкции склепываемого соединения.
Рис 5.5 Вставной инструмент к пневматическим молоткам а — зубило, б — крейцмейсель, в — чекан, г — обжимка, д — боек для клепки
Работа пневматического молотка сопровождается вибрацией, повышающей утомляемость рабочих и влияющей на их здоровье, поэтому рекомендуется применять молотки, снабженные виброгасящим устройством.
Пневматическая рубка связана с применением тяжелого физического труда, оказывает вредное воздействие на работающего и окружающих (шум, вибрация) и характеризуется низкой производительностью. Чтобы сократить применение этой операции, стремятся повысить точность изготовления деталей, узлов, секций, кроме того, заменяют рубку тепловой резкой и строжкой, зачисткой кромок с применением фрез создают неприварные сборочные приспособления и т. п.
Изготовление узлов
Конструктивно-технологическая классификация узлов представлена на рис. 5.1, некоторые примеры узлов показаны на рис. 5.8. Узлы каждой группы имеют специфические особенности, что предопределило различные подходы к разработке технологических процессов их изготовления.
Рис. 58. Узлы корпусных конструкций
а—балка таврового сечения, б— кницы с прямолинейными и криволинейными поясками,
в - бракета с вырезом и пояском, г — широкая полоса с ребрами,
д — полотнище из трех листов, е — фундамент, ж — кингстонная коробка
Сварные балки. Балками называют узлы с соотношением длины к большему размеру поперечного сечения, превышающем 4,5—5,0. На современных морских транспортных судах с продольной или смешанной системой набора протяженность всех балок (сварных и прокатных) составляет от 250 до 450 длин корпуса. Из них от 6 до 20 % приходится на сварные балки, главным образом таврового профиля. К технологическим особенностям таких балок относятся: простота сборки из-за небольшого числа деталей; значительная протяженность продольных швов, что делает целесообразным применение автоматической сварки; склонность балок к приобретению остаточных сварочных деформаций вследствие большого отношения длины к размерам поперечного сечения
Простота конструкции предопределила достаточно широкие возможности механизации процесса изготовления балок Так, для сборки и сварки прямолинейных тавровых балок (длиной 3500— 12000 мм, с высотой стенки 100—710 мм, шириной пояска 60— 250 мм) с предотвращением общих сварочных деформаций была создана механизированная линия МИБ-700 (рис 5 9)
В состав линии входят сборочно-сварочный станок 3, снабженный консолью 7 с вертикальными и горизонтальными роликами для взаимного центрирования пояска и стенки и их движения в рабочую клеть станка, приемный рольганг 6, на который выходит сваренная балка, передний перегружатель 2 с поворотными
Рис 5 9 Механизированная линия МИБ 700
электромагнитными захватами для подачи на консоль станка поясков и стенок балок; задний перегружатель 5 для снятия готовых балок с приемного рольганга и укладки их в контейнер. Кроме того, рядом с линией имеются столы: передний — для установки кассеты 1 поясками и стенками и задний 4 — для контейнера готовых балок.
Сварочные деформации балок предотвращаются путем создания в зоне сварки напряжений растяжения в нижних волокнах балки. Это достигается за счет поворота консоли, обеспечивающего поворот конца свариваемой балки. Величина поворота консоли заранее задается в табличной форме для каждого размера балки. Годовой выпуск линии при двухсменной работе составляет 80 000 пог. м балок. Учитывая такую высокую производительность, линию МИБ-700 применяют только на крупных заводах, обеспечивающих ее достаточную загрузку.
В условиях ограниченного использования прямолинейных и криволинейных тавровых балок симметричного и несимметричного профиля экономически эффективнее применять агрегат СКТ-12-1, предназначенный для изготовления балок длиной 2500—12000 м, высотой стенки 170—1000 мм, шириной пояска 80—450 мм, наибольшей стрелкой прогиба балки 900 мм.
При отсутствии средств механизации или низкой их загрузке балки можно изготавливать на плоских стендах с использованием упрощенных кондукторов, фиксирующих положение пояска и стенки балки. Собранную балку затем передают для автоматической или полуавтоматической сварки на отдельную позицию.
Короткие тавры, бракеты и кницы с поясками чаще всего имеют тавровую или Г-образную форму поперечного сечения. Если поясок тавра прямой, то для сборки можно использовать те же кондукторы, что и для сборки балок. Узлы этой группы с прямолинейными поясками целесообразно сваривать целой партией, укладывая каждый узел по непрерывной линии один за другим вдоль хода головки сварочного автомата.
Широкие полосы с ребрами или поясками. К ним относятся стрингеры, флоры, рамные бимсы и т. д. Сборку и сварку широких полос с ребрами осуществляют на плоских стендах, оборудованных передвижными порталами (рис. 5.10). На портал навешивают отдельные устройства для наведения и прижима ребра к листам и для сварки ребер с листами. При приварке ребер к широким полосам характерным видом деформации являются так называемые «домики». Для их предупреждения может использоваться сосредоточенный обратный выгиб листа с помощью ряда роликов, встроенных в стенд и выдвигаемых снизу (рис. 5.10, б), и верхних упоров или роликов, нажимающих на лист сверху. Высоту нижних роликов и расстояние между верхними нажимными выбирают такими, чтобы создать в кромке
Рис. 5 10. Схема передвижного портала над сборочным стендом (а)
и схема выгиба листа на нем (б)
1—несущая балка, 2 - балка навесного устройства, 3 -пневмоцилиндр для прижима
ребра, 4— захват ребра, 5—захват балки, 6—опорное колесо балки, 7 — верхние
нажимные ролики, 8 - нижние выдвижные ролики
листа поперечные растягивающие напряжения, достигающие 0,50т.
Существуют проекты механизированных участков для изготовления этих двух групп узлов. На рис. 5.11 показана схема такого участка, на котором могут изготавливаться кницы, бракеты, короткие прямолинейные и криволинейные тавры, флоры и стрингеры длиной от 1,5 до Юме вырезами, подкрепленными поясками и ребрами жесткости.
Полотнища секций. Это весьма распространенный тип узлов корпусных конструкций. Предельная стрелка прогиба, при которой полотнище выделяется в самостоятельный узел, равна 1/50 меньшего размера секции в плане. При больших стрелках прогиба полотнища собирают в постелях, в которых изготавливают соответствующие секции.
Полотнища можно изготавливать по двум организационно-технологическим вариантам: 1) сборка и сварка полотнища в виде отдельного самостоятельного узла, подаваемого в накопитель, а затем поступающего на участок сборки секций; 2) сборка и сварка полотнищ на первых позициях механизированной поточной линии изготовления плоских секций; после сварки полотнище
Рис. 5.11. Схема механизированного участка для изготовления узлов набора
1 — контейнеры, 2 - поворотный стол сварщика, 3 - светозащитная ширма, 4 — винтовой
стул, 5—стол сборщика, 6 — стол для правки узлов, 7— накопитель узлов вертикального
типа, 8 —сварочный стол, 9—универсальный стенд для сборки узлов, 10—стрела сварочная,
11 — полукозловый кран
подается на следующие позиции для установки и сварки элементов набора и насыщения.
Рассмотрим первый вариант изготовления полотнищ, поскольку второй будет подробно изложен в составе механизированной поточной линии изготовления плоских секций в следующем параграфе. В этом случае сборка и сварка полотнищ осуществляется на специальном участке цеха, оборудованном плоскими металлическими стендами различной конструкции. Сварка листов — наиболее трудоемкая и ответственная технологическая операция при изготовлении полотнищ, поэтому много внимания уделяется совершенствованию сварки и в первую очередь — ее механизации. К настоящему времени создано и освоено промышленностью несколько способов сварки стыков листов полотнищ.
Распространенным является способ, при котором сварка собранного на электроприхватках на металлическом стенде полотнища осуществляется «на весу» (рис. 5.12, г). В этом случае производят автоматическую сварку (под слоем флюса) с одной стороны полотнища, а затем после кантовки полотнища и строжки корня шва подваривают обратную сторону шва. При сварке «на весу» требуется тщательно подгонять стыкуемые соединения и применять ограниченные режимы сварки во избежание прожогов. В то же время при таком способе сварки легко обеспечить качественный шов по всей его длине благодаря хорошему формированию его обратной стороны после кантовки.
Более предпочтительным следует считать способ, в котором предусматривается автоматическая сварка полотнищ на специализированном стенде с желобами, заполненными флюсом, т. е.
Дата добавления: 2015-10-26; просмотров: 7979;