МАТЕРИАЛЫ ЧЕРВЯЧНЫХ КОЛЕС И ЧЕРВЯКОВ
Червячные передачи имеют повышенную склонность к заеданию и износу рабочих поверхностей из-за неблагоприятных условий для образования масляного клина в полюсе зацепления. Для устранения заедания и повышения износостойкости рекомендуется для червячных колес применять материалы с высокими антифрикционными свойствами, использовать для смазывания передачи противозадирные масла, повышать твердость (H ³ 45HRCэ) и чистоту рабочих поверхностей витков червяка для сокращения времени приработки передачи. Червяки изготавливают из углеродистых и легированных сталей. Например: 40, 45, 50, Ст6, 40Х, 40ХН, 30ХГС, 35ХМ, 40Г2 (улучшение, нормализация H £ 350 HB или закалка до 45–55HRCэ); 15Х, 20Х, 12ХН3А, 18ХГТ, 20ХН3А, 20Х2Н4А (цементация, закалка до 56– 62HRCэ) и др. (см. табл. 2.1; [4, с. 171]). Выбором стали во многом предопределяется вид термической и механической обработки, а также условия работы передачи – износостойкость, склонность к заеданию и др.
Нелинейчатые и эвольвентные червяки обычно подвергаются цементации или закалке (H ³ 45HRCэ). Поверхности витков шлифуют и полируют. Высокая твердость и гладкость рабочих поверхностей витков червяка позволяет повысить износостойкость и контактную выносливость, уменьшить потери на трение и снизить возможность заедания. Подобные червяки применяют в ответственных и сравнительно нагруженных червячных передачах.
Рабочие поверхности витков архимедовых и конволютных червяков обычно не шлифуют.[2] Применяют их в малонагруженных и неответственных червячных передачах. Такие червяки изготавливают из относительно мягких (H < 350 HB) нормализованных или улучшенных сталей. Червяки с малой твердостью и нешлифованной рабочей поверхностью из-за повышенных потерь на трение имеют в 1,5 – 2 раза меньшую нагрузочную способность и более низкий к.п.д., чем червяки с высокой твердостью рабочих поверхностей (H ³ 45HRCэ) и шлифованными витками.
Червячные колеса изготавливают чаще из бронзы, реже из латуни или чугуна. Материалы, применяемые для изготовления червячных колес, по убыванию их противозадирных и антифрикционных свойств можно условно подразделить на три группы, табл.16.1 [29; 39; 40, c. 111 – 113].
Выбор группы и материала осуществляют по ожидаемой скорости скольжения vs (м /с) витков червяка по зубьям червячного колеса:
,
где n1 – частота вращения червяка, об/мин;
T2 – крутящий момент на валу червячного колеса, Н× м.
Таблица 16.1
Группа | Наименование материала | Способ отливки* | Механические свойства, МПа | Рекомендуемый предел скорости скольжения vs, м/с | |||
sb | sТ | sbи – предел прочности материала на изгиб | Е – модуль упругости первого рода | ||||
I | Бр ОНФ 10-1-1 | Ц | – | 1×105 | £ 35 | ||
Бр ОФ 10-1 | З К | – – | 0,75×105 | £ 25 | |||
Бр СуН 7-2 | К | – | |||||
Бр ОЦС 6-6-3 | З К | – | £ 12 | ||||
Бр ОЦС 5-5-5 | Ц | ||||||
II | Бр АЖ 9-4 | З К Ц | – | 1×105 | £ 5 | ||
Бр А9ЖЗЛ | З К Ц | ||||||
Бр АЖН 10-4-4 | К Ц | ||||||
Бр АЖМц 10-3-1,5 | К | ||||||
ЛАЖМц 66-6-3-2 | З К Ц | – | |||||
ЛМцС 58-2-2 | З | – | |||||
ЛМцОС 58-2-2-2 | К | ||||||
III | СЧ 10 (143-229НВ) СЧ 15 (163-229НВ) СЧ 18 (170-241НВ) | З З З | – – – | – – – | 1×105 | £ 2 |
* Примечание:З – в землю, К – в кокиль, Ц – центробежный.
· Группа I. Бронзы высокооловянистые (10 – 12 % Sn) с присадками фосфора и никеля считаются лучшим материалом для червячных колес, однако они дороги и дефицитны. Их применение ограничивают наиболее ответственными передачами с большими скоростями скольжения (vs до
25 м /с). Бронзы малооловянистые (3 – 6 % Sn) с присадками свинца и цинка и сурьмяно-никелевые обладают несколько худшими противозадирными свойствами и применяются при меньших окружных скоростях. Отличительная черта этих материалов – невысокая прочность (sВ £ 300 МПа). Для этой группы материалов червяк, как правило, должен быть тщательно отшлифован и отполирован и иметь высокую твердость рабочих поверхностей –
45-62 HRCэ (см. табл. 18.3).
· Группа II. Бронзы безоловянистые и латуни используются как заменители оловянистых бронз при vs до 3 – 5 м/с. При больших скоростях применение безоловянистых бронз и латуней становится неэффективным, т.к. необходимо снижать допускаемые контактные напряжения sНР для предупреждения ускоренного износа зубьев червячного колеса или задира рабочих поверхностей зубьев. При этом размеры передачи и расход материалов существенно возрастают. Механическая прочность безоловянистых бронз и латуней значительно выше, чем у оловянистых бронз (sВ » 350 – 700 МПа), а стоимость – ниже. Сравнительно низкие противозадирные и антифрикционные свойства ограничивают их применение при высоких скоростях скольжения. Во избежание заедания червяк рекомендуется подвергать термической обработке (45–50 HRCэ), а затем шлифовать и полировать. Допустимо применение нешлифованных червяков с Н£ 350НВ. Эксплуатационные возможности передачи при этом несколько снижаются.
· Группа III. Мягкие серые чугуны с твердостью 140 – 220 НВ по ГОСТ 1412 – 85 применяют при vs £ 2 м/с в механических и ручных приводах. Использование серых чугунов при более высоких скоростях становится неэффективным из-за существенного увеличения габаритов и опасности появления заедания. Заготовки колес получают литьем (рис.16.1,а, б). При необходимости подвергают термообработке [40, с.112–113]. Твердость рабочих поверхностей нешлифованных витков червяков, как правило, менее 350 НВ.
В целях экономии сплавов I и II групп червячные колеса выполняют составными: венец из бронзы или латуни, а колесный центр из чугуна или стали. В бандажированной конструкции (aw » 80 – 200 мм) венец насаживается на центр с натягом и обычно закрепляется дополнительно 3–8 винтами (рис.16.1, в), чтобы компенсировать недостаток конструкции – зависимость натяга от температуры среды и коэффициентов линейного расширения материалов. В болтовой конструкции (aw » 200 – 600 мм) венец, имеющий фланец с отверстиями, крепится к центру колеса 4 – 8 призонными болтами, устанавливаемыми в отверстия без зазора (рис.16.1, г). Биметаллическую конструкцию (рис.16.1, д) чаще применяют в серийном производстве и получают путем заливки расплавленного металла в форму, куда предварительно устанавливается центр колеса.
|
|
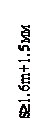
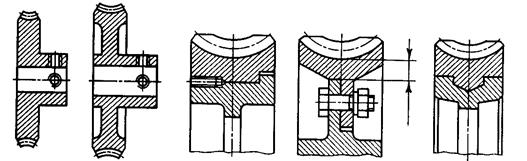
а б в г д
Рис. 16.1. Конструктивные формы червячных колес
(обозначения на рис. 16.1, г по п.18.1.8)
Дата добавления: 2015-07-22; просмотров: 16152;