Осаждение пленочных покрытий из газовой фазы
Нанопокрытия являются одним из видов активно используемых наноструктур.
Они находят применение в качестве пленок и слоев для микроэлектроники, оптики, наносистемной техники, пар трения, металлорежущего инструмента, антикоррозионной защиты, медицины, биологической защиты, гидрофобных покрытий и т.п.
На основе пленочных покрытий могут формироваться два вида нанообъектов:
Нанопленки (пленки или слои, толщиной менее 100 нм) и нанозерена или наногранулы в составе наноструктурированного покрытия.
Процесс получения тонких пленок физическим осаждением (PVD) включает:
- испарение (распыление) частиц испаряемых (распыляемых, осаждаемых) материалов из одного или нескольких источников, которое характеризуется энергией частиц (атомов, ионов), их скоростью и составом испаряемого вещества,
- перенос частиц к подложке (поверхности напыления (осаждения)), для которого желательно обеспечить пролет частиц испаряемого вещества до поверхности осаждения без столкновения с молекулами остаточных и рабочих газов, что реализуется при их давлении не выше 10-4Па,
- осаждение частиц и рост пленки, которые обусловлены скоростью осаждения, составом и строением пленки, равномерностью ее толщины, адгезией с подложкой.
Различают следующие возможности отделения частиц осаждаемого (напыляемого) материала и последующего их осаждения на подложку:
1. Испарение осаждаемого материала, сопровождающееся освобождением его атомов, за счет нагрева до оптимальной температуры испарения Tисп (как правило, больше Тпл, но меньше Ткип). Покрытие формируется за счет осаждаемых атомов.
2. Распыление осаждаемого материала за счет сообщения его атомам энергии больше энергии межатомной связи. Покрытие формируется за счет осаждаемых атомов.
3. Распыление осаждаемого материала, которое включает не только освобождение атомов, но и их ионизацию. Покрытие формируется за счет осаждаемых ионов.
Разновидности реализации испарения осаждаемого материала
Термическое испарение
При обычном термическом испарении (рис.1) производится подвод энергии (4) к испаряемому материалу (3), вызывающий его нагрев до температуры Tисп, при которой давление насыщенных паров рнас ~ 1,33 Па (0,01Торр). Это обеспечивает заметное испарение материала в вакуумной камере (2) со скоростью Vисп ~ 0,1 (мг/см2с) с перемещением атомов (5) испаряемого материала на подложку (7) для формирования покрытия (8).
Рис.1. Общая схема процесса нанесения покрытий в вакууме. Вертикальной стрелкой показано направление осаждения атомов испаряемого материала.. 1 – основание, 2 – вакуумная камера, 3 – испаряемый (распыляемый) материал, 4 – условный подвод энергии для испарения (распыления), 5 – осаждаемые частицы, 6 – заслонка, 7 – напыляемое изделие, 8 – образующееся покрытие, 9 – натекатель газа-реагента или рабочего газа, 10 – экран. L – расстояние до напыляемой поверхности
Повышение температуры на 10-15% приводит к повышению Vисп в 10 раз. Для ускорения испарения используют температуру на 30% больше Tисп, что повышает скорость испарения в 100 раз. При этом снижается степень загрязнения пленки молекулами остаточных газов. Для создания покрытия на основе химических соединений через натекатель (9) в вакуумную камеру может подаваться газ-реагент. Натекатель используют также для введения рабочего газа (как правило, аргона), ионы которого вызывают распыление испаряемого материала.
Способы нагрева при термическом испарении
Прямой нагрев с помощью резистивных элементов (TVD-процесс).
Нагрев резистивным способом обеспечивается за счет тепла, выделяемого при прохождении электрического тока через нагреватель (испаритель), на котором (в котором) помещается испаряемый материал (рис.2).
Рис.2 . Пример модуля резистивного испарителя. В клеммах верхней части модуля фиксируется резистивный элемент.
Резистивные испарители подразделяются на:
- проволочные испарители (рис.3) диаметром 0,5-1,5 мм, имеющие рациональную форму для удержания испаряемого материала в расплавленном состоянии; применяются, как правило, при хорошем смачивании испарителя испаряемым материалом.
Рис.3 . Проволочные испарители. а), б), в), г) U-, V-, W, волнообразные с навешенными заготовками из испаряемого материала, д), е), ж) спирали с длинными проволочными заготовками из испаряемого материала и в форме «улитки» для размещения порошка испаряемого материала.
- ленточные (фольговые) испарители (рис.4) из тонких листов или фольги толщиной 0,1-0,5 мм, в которых создают специальные углубления для размещения испаряемых металлов; могут применяться и при плохом смачивании испарителя.
.
Рис.4. Фольговые испарители. а) лента с углублением, б) в) с вертикально и горизонтально расположенными направляющими для потока пара, г) – лодочного типа (для не смачивающих испаряемых материалов), д) – трубчатого типа с щелью для направления потока пара.
Материалом для изготовления испарителей служат тугоплавкие металлы (вольфрам, молибден, ниобий, тантал). Они должны удовлетворять следующим требованиям:
- давление насыщенного пара материала испарителя при температуре испарения должно быть существенно меньше давления пара испаряемого вещества,
- хорошее, как правило, смачивание испаряемым веществом материала испарителя для лучшей теплопередачи и сцепления с испарителем,
- отсутствие химического взаимодействия между материалом испарителя и испаряемым веществом во избежание загрязнения паров и разрушения испарителей.
Рекомендации по совместимости испаряемых материалов и материалов испарителя даны в таблице (Выбор материала испарителя).
Достоинства:
- простота реализации,
- использование, как правило, низковольтного электрического питания.
Недостатки:
- данные способы применяют для испарения веществ при температурах до 1900°С, ограниченный температурой плавления испарителя,
- малое количество испаряемого материала,
- возможное загрязнение паров за счет прямого контакта испаряемого материала и испарителя,
- ограниченный ресурс резистивного нагревателя,
- необходимость частой дозагрузки испаряемого материала,
- малая энергия атомов пара (~0,3эВ), что характерно для испарения,
- низкая адгезионная и когезионная прочность покрытия.
Косвенный резистивный нагрев через тигель
Косвенный резистивный нагрев испаряемого материала, находящегося в тигле (рис. 5) из тугоплавких материалов: тугоплавких металлов, графита или керамики (SiO2, BeO, ZrO2, Al2O3, BN) и др. Применяется для испарения объемов вещества больших, чем в случае проволочных и ленточных испарителей.
Рис. 5. Косвенный нагрев в тигле. Тигель 1 окружен вольфрамовой проволокой 2, закрепленной на футеровке 3.
При одновременном (или поочередном) испарении различных веществ на поверхности подложки происходит осаждение атомов различных элементов, при котором образуются пленки сложного состава и структуры (химические соединения, твердые растворы, смеси, градиентные и послойные пленки).
Достоинства:
- большая производительность,
- отсутствие (в большинстве случаев) контакта с резисторным нагревателем.
Недостатки:
- данный способ используют для испарения веществ при температурах до 1900°С,
- контактное взаимодействие испаряемого материала и тигля,
- ограниченный ресурс материала резисторного нагревателя,
- малая энергия атомов пара (~0,3эВ), что характерно для испарения,
- низкая адгезионная и когезионная прочность покрытия.
Сублимационный нагрев
Испарение при сублимационном нагреве происходит из твердого состояния, вследствие чего возможно отсутствие контакта между испаряемым материалом и испарителем (рис.6). Применяется для материалов (Cr, Mo, Pd, V, Fe и Si), которые при температурах меньше Tпл имеют достаточное для испарения рнас (1,33 Па).
Рис.6. Схема сублимационного нагрева. 1 - держатель, 2 – тепловые экраны, 3 – резистивный нагреватель, 4 – испаряемый материал, 5 – поток пара.
Широко применим для испарения хрома. Очень важен для кремния, который в расплавленном состоянии легко вступает в химические реакции. Применим для материалов с рнас ~ 0,13 Па (Ni, Rh, Ti), но для испарения с малой скоростью, что может быть достаточно для напыления нанопокрытий.
Достоинство: отсутствует загрязнение испаряемого материала материалом резистивного нагревателя.
Недостатки:
- невысокая производительность,
- ограниченный набор испаряемых материалов,
- ограниченный ресурс резистивного нагревателя,
- малая энергия атомов пара (~0,3эВ), что характерно для испарения,
- низкая адгезионная и когезионная прочность покрытия.
Индукционный нагрев токами высокой частоты
Индукционный нагрев (рис.7) токами высокой частоты реализуется за счет движения зарядов в испаряемом материале (7) (или материале тигля) под действием электромагнитного поля индуктора (3), спираль которого, конструктивно выполненная в виде металлического трубопровода, охлаждается проточной водой.
http://elektroas.ru/laboratornyj-invertor-dlya-levitacionnoj-plavki-metallov-video#more-5194
Рис.7. Испарение индукционным нагревом. 1 - тигель, 2 - теплоизоляция, 3 – индукционный нагреватель, 4 – основание, 5 - центрирующий стержень, 6 – электроизоляция, 7 – расплавленный испаряемый материал.
Индукционный нагрев применяется также в левитационно-струйных установках, где под его действием расплавляется и испаряется проволока, капля которой удерживается в зоне нагрева неоднородным высокочастотным полем и силами поверхностного натяжения.
Достоинства:
- отсутствие контакта с испарителем,
- отсутствие разрушения испарителя при эксплуатации.
Недостатки:
- миграция испаряемого материала через верхнюю границу тигля на наружную поверхность,
- газовыделение, сопровождающееся выбросом испаряемого материала из тигля,
- сложность используемого оборудования
- малая энергия атомов пара (~0,3эВ), что характерно для испарения,
- низкая адгезионная и когезионная прочность покрытия.
Испарение электронным пучком (EBVD-процесс).
На поверхность испаряемого материала, помещенного в тигель, направляется высокоэнергетический (~104 эВ) поток электронов, который доводит ее до плавления и испарения (рис. 8). Во всех случаях присутствует:- источник электронов (3), - ускоряющий анод,- система фокусировки пучка,- система управления пучком.
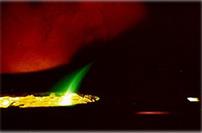
- наличие высокого напряжения (до 60 кВ), что требует соблюдения определенных требований техники безопасности,
-значительная часть энергии непроизводительно расходуется на образование вторичных электронов,
- малая степень ионизации испаряемых атомов (~0,1%),
- малая энергия атомов пара (~0,3эВ), что характерно для испарения,
- низкая адгезионная и когезионная прочность покрытия.
Испарение лазерным лучом
Лазерное воздействие на поглощающие среды приводит к нагреву и последующему испарению. Луч лазера поступает в вакуумный объем через кварцевое окно, пропускающее излучение в широком диапазоне.
При применении лазеров используется как непрерывный, так и импульсный режим. Импульсный режим позволяет более эффективно выносить пары из зоны испарения, увеличивать интенсивность излучения, получать кластеры меньших размеров и способствует одновременному испарению атомов элементов с разными давлениями насыщенных паров.
Достоинства:
- большая мощность пучка, сфокусированная в малом пятне, дает возможность испарять любые, даже самые тугоплавкие, материалы с достаточно большой скоростью испарения,- возможность поддержания высокого вакуума,- отсутствие загрязнения материалом испарителя и минимизация загрязнения материалом тигля за счет его охлаждения,- высокая плотность потока пара за счет высокой плотности энергии,- возможность испарять тугоплавкие материалы.Недостатки:
- эффективен для испарения только оптически поглощающих сред,
- даже при больших коэффициентах поглощения толщина испаряемого слоя весьма мала и составляет от единиц до нескольких десятков нанометров,
- низкий электрический КПД лазера,
- малая энергия атомов пара (~0,3эВ), что характерно для испарения,
- низкая адгезионная и когезионная прочность покрытия.
Молекулярно-лучевое испарение
Молекулярно-лучевой способ испарения при использовании резистивного нагрева реализуется с помощью эффузионной ячейки Кнудсена (рис. 9) и капиллярных источников, в которых через малые (~1 мм) отверстия медленно истекает поток атомов испаряемого вещества. При этом обеспечивается строгий контроль температуры, тепловые экраны, ламинарность потока, диаграмма испарения, соответствующая косинусному закону Кнудсена, что позволяет добиться равномерности толщины пленки. Применяется при электронно-лучевой эпитаксии.
а б
Рис. 9. Эффузионные испарители. а – эффузионная ячейка 1- тигель, 2 – нагреватель, 3 – тепловой экран, 4 – термопара, б) капиллярный испаритель. Через малые отверстия ~1мм (1) при нагреве спиралью (5) ламинарно истекает поток атомов испаряемого материала (7), который помещен в емкость для загрузки (2). Емкость геметизирована прокладкой (3) с заглушкой (4) и окружена тепловым экраном (6).
Достоинства:
-высокая стабильность потока пара, испускаемого через малые отверстия,
- диаграмма испарения, близкая к идеальной,
- получение равномерных по толщине слоев.
Недостатки:
- данный способ используют для испарения веществ при температурах до 1900°С,
- малая энергия атомов пара (~0,3эВ), что характерно для испарения,
- низкая адгезионная и когезионная прочность покрытия,
- низкая производительность процесса.
Применение напыления термическим испарением
Вакуумноенапыление без использования ионизации напыляемых атомовприменяют в планарной технологии полупроводниковых микросхем, в производстве тонкопленочных гибридных схем, изделий пъезотехники, акустоэлектроники и др. (нанесение проводящих, диэлектрических, защитных слоев, масок и др.), в оптике (нанесение просветляющих, отражающих и др. покрытий), ограниченно - при металлизации поверхности пластмассовых и стеклянных изделий.
Методом вакуумного напылениянаносят покрытия из металлов (Al, Au, Cu, Cr, Ni, V, Ti и др.), сплавов (например, NiCr, CrNiSi), химических соединений (силициды, оксиды, бориды, карбиды и др.), стекол сложного состава (например, I2О3 ∙ В2О3 ∙ SiO2 ∙ Аl2О3 ∙ СаО, Та2О ∙ В2О3 ∙ I2О3 ∙ GeO2), керметы.
Общие достоинства способов термического испарения:
- возможность нанесения пленок металлов (в том числе тугоплавких), сплавов, полупроводниковых соединений и диэлектриков,
- простота реализации (отлаженное оборудование),
- возможность изменения скорости испарения вещества в широких пределах за счет изменения подводимой к испарению мощности,
- возможность получения покрытий, практически свободных от загрязнения.
Общие недостатки способов термического испарения:
- нерегулируемая и невысокая скорость и энергия осаждаемых частиц (плохая адгезия), кроме случая использования эффузинного источника (ячейка Кнудсена) и капиллярных испарителей, где испарение происходит с постоянной скоростью и ламинарно, что позволяет получать равномерные и стехиометрически однородные пленки,
- практически отсутствует ионизация испаренных частиц, что не позволяет эффективно управлять их потоками при осаждении, используя электрическое и магнитное поле.
Разновидности метода распыления осаждаемого материала с освобождением атомов
Метод ионного распыления
Общая характеристика метода ионного распыления
Ионное распыление основано на использовании ионов инертных газов для освобождения атомов из поверхностных слоев твердого материала-мишени (распыления). Освобожденные атомы переносятся к напыляемой поверхности подложки за счет градиента концентрации данных атомов между мишенью и подложкой. Формирование положительных ионов происходит за счет ионизации атомов инертных (рабочих) газов (чаще всего, аргона) в дуге тлеющего разряда между мишенью (катодом) и специальным анодом.
При этом:
- используется плотность тока от 0,1 - 50 мА/см2 и напряжения 500 – 1500 В,
- расстояние до напыляемой поверхности от 40 до 150мм,
- максимальная энергия ионов рабочего газа до 1000 эВ,
Достоинства:
- относительно высокая скорость напыления >1 мкм/мин,
- энергия, приобретаемая атомами мишени при распылении, составляет ~ 3 – 5 эВ, но может достигать 200эВ при магнетронном распылении, что обеспечивает лучшую адгезию и когезию при осаждении,
- состав напыленного материала соответствует составу мишени, так как освобождение атомов происходит по механизму распыления, при котором давление насыщенных паров не имеет большого значения,
Неодстатки:
-поддерживается довольно низкий вакуум - рабочее давление в камере 10 - 10-2 Па, что необходимо для обеспечения тлеющего разряда, поэтому напыляемое покрытие загрязнено частицами рабочего и остаточных газов,
- низкий КПД (~1%), так как почти вся энергия идет на нагрев мишени,
- напыляемое покрытие загрязнено частицами рабочего и остаточных газов,
- вторичные электроны бомбардируют поверхность напыления, вызывая ее перегрев,
- степень ионизации атомов распыляемых материалов недостаточна для эффективного управления потоком частиц.
Разновидности метода ионного распыления
Ионно-плазменное распыление
Диодный вариант на постоянном токе
Ионно-плазменное распыление (рис.10), при котором в присутствии рабочего инертного газа (Ar), поступающего через натекатель (3) под действием постоянного высокого напряжения между катодом (1) и анодом (8) возникает тлеющий разряд (2) с образованием плазмы, состоящей из положительных ионов Ar+ и электронов. Ионы, ускоряемые электрическим полем, бомбардируют катод (мишень), состоящий из распыляемого материала (1), выбивая из него атомы (4), осаждающиеся в виде покрытия (6) на подложку (5).
Рис.10. Принципиальная схема установки ионно-плазменного распыления. 1 – катод, 2 – зона тлеющего разряда, 3 – натекатель рабочего газа, 4 – атомы испаряемого газа, 5 – подложка, 6 – покрытие, 8 - анод.
В диодном варианте ионизации для обеспечения тлеющего разряда используют высокие напряжения (>1 кВ) и давление в камере ~ 1Па. Однако плотности ионного тока (~1мА/см2) и соответствующие скорости напыления (~1нм/с) будут малы и поэтому диодную схему применяют для нанесения тонких, в частности, нанослоев проводящих материалов.
Достоинство метода:
- относительная простота реализации,
Недостатки:
- нагрев и частичное распыление анода электронами плазмы,
- малая энергия осаждаемых частиц и загрязнение покрытия атомами рабочего и остаточных газов,
- степень ионизации атомов испаряемого материала для диодной схемы ~1%, что не создает условий для управления потоком распыляемых атомов,
- диодная схема на постоянном токе не применима для распыления диэлектриков, так как на их поверхности в процессе ионной бомбардировки накапливается сформированный ионами рабочего газа положительный заряд, мешающей дальнейшей ионизации атомов рабочего газа.
- малая производительность процесса, за счет малой плотности потока напыляемых атомов.
Диодный вариант на токе высокой частоты
На поверхности диэлектриков в процессе ионной бомбардировки накапливается положительный заряд, уменьшающий область ионизации атомов рабочего газа. Для устранения этого недостатка используется высокочастотное изменение полярности электродов, которое обеспечивает нейтрализацию положительных ионов электронами в полупериод изменения полярности катода на обратную.
Рис.11. Принципиальная схема высокочастотного ионно-плазменного распыления. 1 – катод, 2 – зона тлеющего разряда, 5 – подложка, 6 – покрытие.
В течение полупериода распыления (рис.11) положительные ионы рабочего газа, разгоняясь между положительным и отрицательным электродами, ударяются о поверхность диэлектрической мишени, выбивая из нее атомы. При этом не происходит нейтрализация ионов электронами, которые не могут пройти от отрицательного электрода через диэлектрик мишени. Ионы рабочего газа, накапливаясь на поверхности мишени, экранируют положительный электрод, препятствуя образованию и ускорению других ионов рабочего газа. При смене полярности электродов наступает полупериод нейтрализации ионов рабочего газа, так как они будут двигаться под действием положительного потенциала мишени через плазму, где произойдет их нейтрализация электронами.
Высокочастотное ионное распыление применяют для нанесения тонких диэлектрических пленок.
Достоинства:
- возможность напыления диэлектриков
Недостатки:
- более сложное оборудование для реализации процесса напыления.
- малая энергия осаждаемых частиц и загрязнение покрытия атомами рабочего и остаточных газов.
Триодный вариант на постоянном токе
Для повышения степени ионизации рабочего газа используют триодную схему (рис.12), в которой присутствует еще один отрицательный электрод в виде термоэмиссионного катода (7). Он обеспечивает эмиссию электронов, пролетающих под действием высокого напряжения к аноду (8), ионизируя атомы рабочего газа. Для повышения вероятности встречи электронов с атомами рабочего газа используют движение электронов по спирали под действием магнитного поля, создаваемого электромагнитными катушками (9).
Рис. 12. Принципиальная схема установки триодного напыления. 1 – катод, 2 – зона тлеющего разряда, 3 – натекатель рабочего газа, 4 – атомы испаряемого газа, 5 – подложка, 6 – покрытие, 7 – термоэмиссионный катод, 8 – анод, 9 - электромагнит
Достоинства:
- схема позволяет в большей степени изменять потенциал на катоде (1) распыляемого материала, давая возможность гибко управлять величиной потока испаряемых атомов,
- электроны не бомбардируют напыляемую поверхность, уменьшая ее нагрев, за счет дополнительного создания разности потенциалов с отрицательным смещением напыляемой поверхности относительно анода,
- процесс можно вести при лучшем вакууме ~10-1 Па, так как электроны эмитируются термоэмиссией, а не за счет электрического пробоя остаточных газов,
- степень ионизации рабочего газа увеличивается за счет высокой концентрации электронов и усложнения их траектории, что вызывает увеличение плотности потока напыляемых атомов,
- повышение производительности по сравнению с диодной схемой
- снижается нагрев анода, за счет уменьшения концентрации бомбардирующих его электронов, которые, не долетая до анода, ионизируют рабочий газ.
Недостатки:
- степень ионизации атомов испаряемого материала для триодной схемы ~1%, что не создает условий для управления потоком распыляемых атомов,
- термоэмиссионный катод недолговечен,
- уменьшается возможность использовать химически активные газы-реагенты,
- малая энергия осаждаемых частиц и загрязнение покрытия атомами рабочего и остаточных газов.
Магнетронный вариант катодного распыления
Магнетронная схема (рис.13) дает возможность дальнейшего повышения степени ионизации рабочего газа (до 100%) созданием вблизи распыляемой поверхности (1) магнитного поля (В) кольцевым магнитом (10) и перпендикулярного силовым линиям магнитного поля электрического поля (Е) между кольцевым анодом (8) и распыляемой поверхностью катода (1).
Рис.13. Принципиальная схема установки магнетронного распыления. 1 – катод, 2 – зона тлеющего разряда, 3 – натекатель рабочего газа, 4 – атомы испаряемого газа, 5 – подложка, 6 – покрытие, 8 – анод, 10 – магнит.
Электроны, выбитые из катода с некоторой скоростью, находясь в скрещенных полях, будут совершать движение по циклоиде. После нескольких ионизирующих столкновений с атомами рабочего газа электроны теряют скорость и притягиваются к аноду. Скорость распыления соизмерима со скоростью испарения электронным пучком. Необходимо интенсивное охлаждение катода для предотвращения расплавления мишени.
Рис.14. Магнетронное распыление и последующее осаждение на подложку нитрида алюминия. Кольцевая мишень после распыления. Свечение тлеющего разряда
.
.
Достоинства:
- высокая плотность ионного тока (~15 мА/см2), соизмеримая с электронно-лучевым распылением,
- увеличивается степень ионизации распыляемых атомов (до 20%),
- снижается нагрев анода, за счет уменьшения концентрации бомбардирующих его электронов, которые, не долетая до анода, ионизируют рабочий газ,
- энергия распыленных атомов достигает ~ 200 эВ,
Недостатки:
- необходимость интенсивного охлаждения катода, чтобы не произошло его расплавление,
Ионное распыление с помощью автономных источников ионов
Источник ионов с горячим катодом типа «Кауфман»
Источник «Кауфман» (рис.15) представляет собой автономный источник с широким ионным пучком, диаметром 350 мм и равномерностью интенсивности потока ионов +/-5%. Электроны, эмитированные катодом (1), перемещаясь под действием электрического и магнитного полей в пространстве между катодом 1 и анодом 2 по сложным траекториям, ионизируют атомы рабочего газа. Поток ионов выводится с помощью ускоряющей сетки (5) в рабочую камеру.
http://www.platar.ru/P2R.html
![]() ![]() |
Рис.14. Источник ионов «Кауфман». 1. термоэмиссионный катод, 2. анод, 3. магнит, 4. ионно-оптические сетки, 5 – ускоряющая сетка, 6. ионный пучок, А- зона возникновения плазмы.
Достоинства источника:
- малое напряжение формирования плазмы (~20в), при котором ионизируется только рабочий газ, причем одинарно, что способствует уменьшению разброса ионов по энергиям,
- возможность управления потоком ионов, при котором осуществляется, в частности, его фокусировка и сканирование,
Недостатки источника:
- присутствие высокотемпературного катода не позволяет использовать источник при наличии в рабочей камере химически активных газов-реагентов.
Источник ионов с холодным катодом типа «ИОН-4»
Источник «ИОН-4» (рис.15) представляет собой многоячеистую матрицу из 61 ячейки, каждая из которых состоит из магнитной системы, включающей полюсные наконечники (3) и сердечник (2), являющиеся катодом. Магнитное поле в ячейках создается общим соленоидом (6) и составляет 0,05 - 0,1 Тл. Анод (1), охлаждаемый водой, является общим для всех ячеек. При поступлении атомов рабочего газа между катодом и анодом происходит их ионизация за счет соударения с электронами, циркулирующими в скрещенных магнитном и электрическим полях. Ионный ток каждой ячейки, имеющей диаметр 12 мм, составляет ~ 10 мА, что соответствует плотности ионного тока 2 мА/см2на расстоянии 200 мм при ускоряющем напряжении от 1 до 4 кВ. В результате формируется ионный пучок диаметром 200 мм.
![]() ![]() |
Рис.15. Источник ионов «ИОН-4». 1. анод, 2. катод, 3. катод, 4. экран, 5 – корпус, 6. соленоид
Достоинства источника:
- малый разброс ионного потока по энергиям с малым углом расходимости (~ 7о),
- использование холодного катода,
- стабильно работает в химически активных средах и остаточном давлении ( 10-3 Па),
Недостатки источника:
- ограниченная плотность ионного тока.
Разновидности метода осаждения с освобождением и ионизацией атомов осаждаемого материала
Осаждение методом дугового разряда
В основе метода лежит (рис.16) сочетание генерации плазмы из ионов и электронов распыляемого вещества с последующим ускоренным движением полученных ионов к подложке за счет электрического поля.
Процесс напыления имеет несколько стадий:
- Пробой в атмосфере разреженных остаточных газов начинается с ускорения случайного электрона, который при соударении с атомами ионизирует их.
- При этом количество освобожденных электронов нарастает лавинообразно, что приводит к пробою междуэлектродного промежутка.
- При наличии мощного низковольтного источника (~40В, ток~200А) возникает дуга низкого давления (7).
- Положительные ионы остаточных газов ударяются о распыляемую мишень (2), являющуюся катодом, выбивая из нее атомы.
- Атомы мишени положительно ионизируются при столкновениях с электронами.
- В процессе напыления дуга поддерживается за счет ионизации выбиваемых из мишени атомов.
- При подаче на электрод напыляемой подложки большого отрицательного потенциала (~ 1кВ) ионы мишени (5) переносятся на подложку (6).
- При подаче через натекатель газа-реагента (например, азота) вблизи поверхности подложки происходит реакция с ионами мишени (например, ионами титана), в результате которой образуется соединение, например, нитрид титана.
Анод и катод интенсивно охлаждают водой (9).
Поле электромагнитной катушки (8) не позволяет катодному пятну выйти за границу мишени. Поле электромагнитной катушки (3) призвано дополнительно ускорить ионы мишени.
Рис.16. Принципиальная схема установки для дугового разряда: 1 – источник напряжения для образования дуги, 2 - расходуемый электрод (катод), 3 – электромагнит, 4 - нерасходуемый электрод (анод), 5 – напыляемые ионы, 6 – напыляемое покрытие на подложке, 7 - дуга разряда, 8 – электромагнит, 9 - охлаждение.
Достоинства метода:
- регулируемая энергия и скорость осаждения за счет возможности управления потоком ионов электрическим полем,
- высокая адгезия покрытий за счет улучшения взаимодействия ионов с напыляемой поверхностью и возможности оптимизации их энергии,
- отсутствие рабочего газа, загрязняющего покрытие,
- высокая производительность процесса (более 3 мкм/мин),
- энергия ионов до 40 эВ,
- высокая степень ионизации,
Недостатки метода:
- относительная сложность применяемого оборудования,
- необходимость низкого вакуума (10-2) для зажигания дуги,
- присутствие в потоке конденсированной фазы.
Перенос осаждаемых частиц от поверхности испаряемого (распыляемого материала) до напыляемой поверхности подложки
Процесс переноса частиц испаряемого материала на осаждаемую поверхность происходит, за счет градиента концентрации частиц, а также (если частицы ионизированы) за счет действия электрических и магнитных полей.
Перенос частиц по первому механизму не обеспечивает им достаточной энергии для прочного сцепления с напыляемой поверхностью. Поэтому для получения высокопрочных износостойких покрытий предпочтительно осаживание ионов, которые могут быть ускорены и направлены электрическим и магнитным полем.
Так как процессы осаждения происходят в вакууме необходимо иметь представление о степени вероятности столкновения переносимых частиц с частицами остаточных и рабочих газов.
В зависимости от величины отношения длины свободного пробега частицы λ к размеру рабочей камеры (или расстоянию между источником и подложкой) различают низкий (λ /d<<1), средний (λ /d~1), высокий (λ /d>>1) вакуум. В низком вакууме преобладают столкновения молекул друг с другом, в высоком вакууме преобладают столкновения молекул со стенками камеры. В обычных вакуумных установках и приборах (d=10 см) низкому вакууму соответствуют давления р>102 Па (1 мм рт. ст.), среднему вакууму - от 103 до 10-1 Па l-10-3 мм рт. ст.), высокому вакууму - р<10-1 Па (10-3 мм рт. ст.).
Средняя длина свободного пробега может быть оценена по формуле
λ ср = 0,68/p (см)
Если в рабочей камере реализуется высокий вакуум (менее 10-2Па), то длина свободного пробега частицы без столкновения значительно больше размера рабочей камеры (или расстояния между источником и подложкой).
Важным условием для создания ламинарного потока и уменьшения вероятности столкновения частиц между собой при испарении является поддержание оптимального давления насыщенных паров 1,33 Па, которое соответствует Tисп, определенной для каждого материала.
В случае выполнения условия идеального испарения, при котором поток частиц испаряемого материала ламинарно движется из локального источника от испаряемой к осаждаемой поверхности без столкновения частиц между собой и с другими частицами, выполняются законы Ламберта-Кнудсена.
1) Концентрация частиц в потоке уменьшается пропорционально косинусу угла между нормалью к поверхности испаряемого материала и направлением распыления (рис.).
2) Плотность потока осаждаемых частиц обратно пропорциональна квадрату расстояния между поверхностями испарения и осаждения.
Условия максимально приближенные к идеальным реализуются при ламинарном испарении частиц из отверстий малых размеров эффузионных ячеек Кнудсена или капиллярных источников (рис. 9) и достаточно высоком вакууме 10-3Па. Знание закономерности осаждения позволяет регулировать равномерность и толщину осаждаемых слоев за счет изменения расстояния между источником и поверхностью осаждения, применением заслонок, перемещением подложки.
В процессе реального испарения при пролете через пространство рабочей камеры до напыляемой поверхности напыляемые частицы могут сталкиваться между собой и с частицами остаточных и рабочих газов, что приводит к неравномерному осаждению частиц на поверхность и снижению скорости осаждения. Например, при прохождении потока частиц через плазму рабочего газа плотность потока в направлении нормали к поверхности осаждения будет меньше, чем на периферии.
Процесс осаждения осаждаемых частиц на подложку
Поток атомов (ионов) напыляемого материала осаждается на напыляемую поверхность подложки (рис.17), после чего атомы либо покидают ее, либо задерживаются, перемещаясь вдоль поверхности и вступая во взаимодействие с другими мигрирующими атомами.
Рис. 17. Формирование покрытия осаждаемыми атомами. Формирование зародышей и рост кристаллов.
В результате формируется устойчивый зародыш кристаллизации критического размера, который оказывается тем больше, чем выше температура подложки. Кристаллизация5.gif, Кристаллизация5.swf
При этом теряется способность атомов мигрировать по поверхности и они закрепляются на подложке в виде островков, увеличивающихся в процессе дальнейшего осаждения атомов. При низкой температуре испарителя плотность потока атомов невысокая, что не способствует зарождению новых центров кристаллизации. В результате пленка растет, в основном, за счет роста уже образовавшихся кристаллов, то есть скорость роста кристаллов оказывается больше скорости их образования.
Снижение температуры подложки и повышение температуры испарения способствует уменьшению критического размера центров кристаллизации и увеличению их концентрации, когда скорость зарождения кристаллов опережает их рост. Это приводит к формированию все более дисперсной кристаллической структуры, переходящей в нанокристаллическую и аморфную. Кроме этого наблюдается неравномерный рост толщины пленки.
Такие мелкокрисаталлические структуры, как правило, энергетически не равновесны и со временем при благоприятных условиях (повышенная температура, слабое сцепление с поверхностью) переходят в более равновесные, крупнокристаллические структуры. В случае пленочных резисторов это со временем снижает величину сопротивления пленки. Поэтому для формирования тонких плёнок, стабильных в процессе эксплуатации, необходимо подложку подогревать и не ускорять процесс напыления за счёт повышения температуры на испарителе.
Для получения контролируемых по толщине, структуре, составу и свойствам нанопокрытий, не загрязненных примесями остаточных газов, окислов и т.п., хорошо сцепленных с поверхностью, необходимо учитывать следующие факторы:
- напыляемая поверхность при вакууме 133,3 *10-6 Па и 20оС за ~2 секунды покрывается монослоем молекул остаточных адсорбированных газов, поэтому для обеспечения чистой поверхности используется предварительный нагрев для дегазации и поддерживается сверхвакуум с давлением меньше 133,3 *10-8 Па;
- расстояние до напыляемой поверхности выбирается 150 – 250 мм,
- плотность потока частиц составляет ~10201/см2с при средней кинетической энергии 0,2 – 0,5 эВ,
- скорость напыления до 1мкм/мин,
- температуры подложки меньше 0,3 Тпл обеспечивают слабую адгезию частиц с поверхностью и между атомами пленки, и малую скорость частиц перемещения вдоль подложки,
- при взаимодействии между поверхностью и осаждаемыми атомами могут образоваться физические - ВдВ связи (адсорбция) или химические - ионные, ковалентные, металлические связи (хемособция), при этом энергия физической связи, как правило, на порядок меньше энергии химической связи,
- возникновение физической связи происходит мгновенно и не требует сообщения дополнительной энергии активации,
- для формирования химической связи требуется энергия активации, которая появляется в течение некоторого времени при возникновении соответствующей флуктуации энергии;
- образованию связей способствует нагрев подложки, но не больше температуры, называемой критической температурой вакуумного напыления,
- при некоторых критически малых потоках осаждаемых атомов они не образуют пленки и испытывают десорбцию,
- химическая связь осаждаемых атомов с химически чистой (ювенильной) поверхностью металла формируется также быстро, как и физическая;
- при повышении температуры адсорбция может перейти в хемосорбцию за счет увеличения частоты возникновения флуктуаций, равных энергии активации;
- при взаимодействии атомов с поверхностью происходит экзотермическая реакция, что может привести к повышению температуры подложки с появлением энергии, достаточной для десорбции адсорбированных атомов;
- термически испаряемые атомы имеют небольшую энергию ~0,2 эВ, которая не обеспечивает при их осаждении достаточную прочную связь с напыляемой поверхностью;
- для повышения энергии испаряемых атомов применяют, в частности, ионное распыление (до 5эВ), ионное осаждение (до 100 эВ), однако при слишком больших энергиях частиц они упруго отражаются от поверхности, не участвуя в образовании пленки,
- после образования сплошной пленки для снятия остаточных напряжений и увеличения адгезии с поверхностью производят нагрев в вакууме при температуре большей температуры поверхности при напылении.
Дата добавления: 2015-06-22; просмотров: 2245;