ТЯГОДУТТЬОВЕ ОБЛАДНАННЯ
Основними характеристиками топкового обладнання є: теплові потужності топки та пальника, ККД топки, теплова напруга дзеркала горіння (перерізу топки) і об'єму.
Під тепловою потужністю топки Фт:т, МВт, розуміють кількість теплоти, що виділяється в одиницю часу у топці при спалюванні палива:
Фт.т.=ВQнр, (4.1)
де В — витрата палива у топці, кг/с; Qнр — нижча теплота згоряння палива, МДж/кг.
Теплова потужність пальника Фт:п, МВт, дорівнює:
Фт:п = (4.2)
де п—кількість пальників, встановлених у топці.
ККД топки:
ηт = 100 — q3 — q4— q5— q6. (4.3)
3. ПАРОВІ ТА ВОДОГРІЙНІ КОТЛИ.
3.1. ПАРОВІ КОТЛИ.
Парові котли, що застосовують у сільськогосподарському виробництві, поділяють на котли із надлишковим тиском пари до 70 кПа (до 0,7 аті) та котли із надлишковим тиском пари понад 70 кПа (понад 0,7 аті).
Котли низького тиску, що утворюють першу групу, використовують у сільському господарстві на тваринницьких фермах і комплексах, птахофермах для одержання пари і гарячої води з метою теплової обробки кормів, пастеризації молока, миття молочного посуду, санітарної обробки приміщень та на інші потреби гарячого водопостачання.
До їх числа відносять котли марок КТ-Ф-300, КТ-500, КТ-1000, КВ-300у, КЖ-Ф-500, КВ-ЗООЛ, Д-900, КУ-Ф-600, КГ-300, Д-721Г-Ф, КГ-1500.
Паровий котел КУ-Ф-600, розроблений на базі котла КЖ-1500, є котлом-утилізатором, що використовує теплоту газів, які викидаються газокомпресорними станціями магістральних газопроводів. Він застосовується на підприємствах з виробництва зневоднених кормів із трав та соломи і на відміну від інших названих вище котлів розвиває тиск пари до 150 КПа.
Технічна характеристика котлів вказаних марок наведена у таблиці 3.1.
3.1. Технічна характеристика парових котлів продуктивністю до 1,5т/год.
Марка котла | Паропродукти-вність, кг/год | Тиск пари, кПа | Температура пари, кПа | Витрата палива, кг/год | ККД,% |
КТ-Ф-300 | До 70 | Не менше 76 | |||
КТ-500 | До 70 | Не менше 120 | Не менше 76 | ||
КТ-1000 | До 70 | Не менше 120 | Не менше 76 | ||
КВ-300у | До 70 | -- | 26,3 | ||
КЖ-Ф-500 | До 70 | Не менше 120 | Не менше 85 | ||
Д-900 | До 70 | Не менше 120 | 63,5 | Не менше 91 | |
КУ-Ф-600 | До 150 | -- | |||
КГ-300 | До 70 | -- | Не менше 87 | ||
Д-721Г-Ф | До 70 | Не менше 120 | 62,5 | ||
КГ-1500 | До 70 | Не менше 120 | 90...94 |
Термін експлуатації котлів малої продуктивності, наведених у табл. 4.1, які мають власну топку, становить 5 років, котла-утилізатора — 7 років. Технологічна схема котла Д-900 зображена на рис. 4.6.
Рисунок 4.6. Технологічна схема котла Д-900.
1 – вентилятор; 2 – форсунка; 3 – жарова труба; 4 – перший газохід; 5 – другий газохід; 6 – передня димова камера; 7 – барабан; 8 – сухопарник; 9 – димова камера другого газоходу; 10 – блок пароперегріву (перегрівник); 11 – блок водонагріву (економайзер); 12 – димохід; 13 – димова камера першого газоходу; 14 – підривний клапан; 15 – паливний насос.
Котел — горизонтальний, триходовий по газу, жаротрубодимогарного типу. Всередині барабана 7 розміщені жарова труба 3, газоходи першого 4 і другого 5 ступеня, димові камери 6, 9, 13. До складу котла входять пальник, що має дуттьовий вентилятор 1 і форсунку 2, економайзер (блок підігріву води) 11, перегрівник (блок перегріву) 10, сухопарник 8, системи подачі палива і води, магнітний протинакипний пристрій, запірну арматуру (клапани, вентилі тощо), запобіжні клапани, рівнемір, манометри.
Котел має систему автоматичного регулювання і безпеки його роботи, вторинні прилади системи автоматичного регулювання розміщені в окремо розміщеній від котельного агрегату електрошафі.
Парові котли Д-563, Д-564 є пересувними. В іншому вони мало відрізняються від парогенератора Д-721.
Парогенератор Д-563 має власний хід, що приводиться у рух чотиритактним карбюраторним двигуном потужністю 2,9 кВт або електродвигуном потужністю 3 кВт. Котел Д-564 монтують на полозках і транспортують трактором або автомобілем.
Останнім часом розпочато серійне виробництво котлів марок КВ-300у, КВ-330л, КГ-300, Д-721Г-Ф, КТ-Ф-300.
Котел КВ-300у, що випускається серійно з 1986 р., має продуктивність 300 кг/год, тиск пари 0,05 МПа, температура пари 120 °С, ККД котла—83%. Котел працює на важких фракціях рідкого палива.
Котел КВ-300л, на відміну від котла КВ-300у, працює на легких сортах рідкого палива. Основні технічні характеристики його такі: паропродуктивність—370 кг/год, ККД—до 90%. Значення параметрів пари такі самі, як і у котла КВ-300у.
Котел КГ-300 працює на газовому паливі. Паропродуктивність його 3000 кг/год, тиск пари — 0,06 МПа, температура пари 120 °С, ККД—до 87 %.
Котел Д-721Г-Ф працює на природному газі. Основні техніко-економічні показники такі: паропродуктивність —750 кг/год, тиск пари—0,07 МПа, температура — 120 °С, ККД - до 87 %.
Котел КТ-Ф-300 працює на твердому паливі. Паропродуктивність котла 300 кг/год, тиск і температура пари відповідно 0,05 МПа і 120 °С, ККД—до 76 %.
Котли серії Е вертикальні, водотрубні двобарабанні із природною циркуляцією, розраховані для роботи на твердому, рідкому та газоподібному паливі (їм відповідно присвоюються індекси І, ІМ, ІГ). Продуктивність котлів 1 т/год. Вироблювана пара тиском 0,78 МПа використовується підприємствами сільського господарства для виробничих та опалювальних потреб.
Екранні труби зв'язані із верхнім та нижнім барабанами двома вертикальними колекторами і двома нижніми колекторами.
Топка котла, що працює на твердому паливі, обладнана колосниковою решіткою. Топки, призначені для спалювання мазуту, комплектують пальниковим пристроєм АР-90.Для спалювання газу є змішувальний пальник із вентилятором
Автоматизовані котлоагрегати МЗК-7 (Е-1, 0-9)* і МЗК-8 (Е-0,4-9) являють собою вертикальні водотрубні котли з природною циркуляцією. Вони призначені для вироблення насиченої пари при тиску до 0,7 МПа. Пара використовується для виробничих та побутових потреб.
* Перша цифра вказує на паропродуктивність (т/год), друга—на абсолютний тиск пари (кгс/см2); букви — на вид палива.
Котли випускаються двох типорозмірів по паропродуктивності: на 1000 кг/год (МЗК-7) та 400 кг/год (МЗК-8).
Вони працюють на природному газі—МЗК-7Г (Е-1, 0-9Г), МЗК-8Г (Е-0.4-9Г); на рідкому паливі (дизельному, пічному паливі та соляровому маслі)—МЗК-7Ж (Е-1.0-9Ж), МЗК-8Ж (П-0.4-9Ж).
Вода у котел подається насосом типу ПН, що приводиться у дію електродвигуном АОЛ-2-12-4.
Котел обладнаний дуттьовим вентилятором типу ВД-2,7, що працює від електродвигуна АОЛ-2-12-2.
Котельні агрегати МЗК-7 та МЗК-8 повністю автоматизовані.
Основні технічні дані котлів серії Е наведені у таблиці 3.2.
3.2. Технічна характеристика котлів типу Е.
Марка котла | Паропродуктивність, т/год | Теплова потужність, кВт | Загальна площа поверхні нагріву, м3 | Вид палива | Витрата палива, кг/год (для газу (м3/год) | ККД, % | Маса, кг |
Е-1/9-1 | 1,0 | 30,0 | Вугілля | 134,5 | 72,8 | ||
Е-1/9-1М | 1,0 | 30,0 | Мазут | 82,6 | 80,5 | ||
Е-1/9-1Г | 1,0 | 30,0 | Газ | 90,1 | 86,0 | ||
Е-1/9-1Г (МЗК-7Г) | 1,0 | 17,1 | Газ | 86,0 | |||
Е-0,4-9Г (МЗК-8Г) | 0,4 | 7,4 | Газ | 86,0 | |||
Е-1,0-9Ж (МЗК-7Ж) | 1,0 | 17,1 | Дизельне | 84,0 | |||
Е-0,4-9Ж (МЗК-8Ж) | 0,4 | 7,4 | Дизельне | 84,0 |
Котли типу ДКВР (стаціонарні двобарабанні водотрубні реконструйовані) випускаються продуктивністю 2,5; 4;6,5; 10 і 20 т/год на надлишковому тиску 1,27 МПа. Котли (крім тих, що мають продуктивність 2,5 т/год) призначені для вироблення як насиченої, так і перегрітої пари температурою 250 °С. Крім того, випускаються котли продуктивністю 6,5; 10; 20 т/год на тиск 2,25 МПа і температуру пари 440 °С.
Всі котли на надлишковий тиск 1,27 МПа виконують за єдиною конструктивною схемою. Схема котла ДКВР-4-13 наведена на рис. 4.7. Котел складається з верхнього 5 і нижнього 8 барабанів, розміщених паралельно і з'єднаних пучками труб, що складають конвективну поверхню нагріву. Поперечною перегородкою конвективний пучок верхнього барабана поділено на дві частини. Від передньої частини верхнього барабана виходять екранні труби топки.
Рисунок 4.7. Паровий котел ДКВР-4-13 з топкою ПМЗ-РПК.
1 – колосникова решітка з поворотними колосниками РПК; 2 – пневмозакидач ПМЗ; 3 – вугільний ящик; 4 – топковий екран; 5 – верхній барабан; 6 – труби конвективного пучка; 7 – обдувний пристрій; 8 – нижній барабан; 9 – інжектор; 10 – шлаковий бункер; 11 – повітропровід.
Топкова камера складається із власне топки і камери догоряння. Призначення останньої — усунути можливість досягнення полум'ям конвективного пучка, а також поліпшити догоряння палива. Котли випускають із топками для спалювання газоподібного, рідкого і твердого (у шарі) палива. Наприклад, на рис. 4.6 топка, що обладнана пневмозакидачем, призначена для спалювання твердого палива. Температура відхідних газів 300...400 °С, а при установці економайзера 140...180 °С.
Утворювана в екранних трубах пароводяна суміш надходить у водяний простір верхнього барабана. По трубах з першого газоходу пароводяна суміш із нижнього барабана піднімається у верхній, а по трубах другого газоходу, навпаки, опускається з верхнього у нижній барабан. Тим самим забезпечується природна циркуляція води у котлі.
Пара, утворювана у верхньому барабані (барабан має паровий простір) надходить споживачеві. При наявності перегрівника пара надходить у пароперегрівник, а потім — до споживача.
Парові котли ДКВР відрізняються досить високою економічністю, невеликою масою, простотою конструкції і транспортабельністю. Основні технічні характеристики ДКВР наведені у таблиці 3.3.
3.3.Технічна характеристика котлів ДКВР.
Марка котла | Теплопродуктивність, т/год | Теплова потужність, МВт | Поверхня нагріву екранів, м3 | Поверхня нагріву конвективних поверхонь, м3 | Поверхня нагріву економайзера, м3 | ККД, %, при роботі на | Маса, кг | ||
вугіллі | мазуті | газі | |||||||
ДКВР 2,5-13 | 2,5 | 1,75 | 16,7 | 70,8 | 88,5 | 90,0 | |||
ДКВР 4-13 | 4,0 | 2,91 | 21,0 | 106,0 | 89,8 | 90,8 | |||
ДКВР 6,5-13 | 6,5 | 4,88 | 27,0 | 165,0 | 89,8 | 91,8 | |||
ДКВР 10-13 | 7,56 | 37,0 | 248,0 | 88,5 | 91,8 | ||||
ДКВР 20-13 | 15,0 | 59,7 | 168,0 | 90,0 | 90,6 | -- |
Останнім часом на зміну котлам ДКВР розроблені котли ДЕ продуктивністю 4; 6,5; 10; 16 і 25 т/год ;для роботи на газі та мазуті і котли КЕ продуктивністю 2,5; 4; 6,5; 10;25 т/год із шаровими топковими пристроями для роботи на твердому паливі.
Котли КЕ-2,5 обладнують напівмеханічннми топками (з ручними поворотними колосниками) та пневмомеханічними закидувачами палива. У котлах КЕ великої паропродуктивності встановлені пневмомеханічні закидувачі і стрічкові ланцюгові решітки.
Для потреб сільського господарства промисловість випускає вертикальні водотрубні парові котли ПКН-1с і ПКН-2с, що працюють на рідкому паливі. Котел ПКН-1с призначений для одержання пари тиском 0,9 МПа. Робочий тиск котла 0,784 МПа, паропродуктивність 1 т/год.
Котли двобарабанні з екранами. Останні з’єднані із двома верхніми і двома нижніми колекторами. Котли оснащені блоками для докотлової обробки води.
3.2. ВОДОГРІЙНІ КОТЛИ
Чавунні секційні котли призначені для теплопостачання опалювально-виробничих приміщень споживачів. Вони працюють із тиском у системі до 0,51 МПа і температурою нагрівної води до 95 °С. Допускається робота водогрійних котлів з температурою гарячої води до 115 °С Циркуляція води у котлах природна. Водогрійні чавунні котли поділяють на три групи: КЧ-1, КЧ-2 і КЧ-3. До першої групи (КЧ-1) відносять котли з тепловою потужністю однієї секції 11,6 кВт (загальна теплова потужність котла дорівнює 81.5...232 кВт) Площа умовної поверхні нагріву (УПН*) цих котлів коливається в межах 7,1...20 м2. Їх використовують в основному для опалення окремих квартир та малоповерхових споруд.
Теплова потужність котлів КЧ-2 коливається у межах 328...1300 кВт (однієї секції - 23,2 кВт), площа умовної поверхні нагріву 29...112м2. До котлів КЧ-2 відносяться котли типу “Універсал”.
Для котлів КЧ-3 характерні такі дані: теплова потужність – 652...1815 кВт (однієї секції – 34,8 кВт); площа умовної поверхні нагріву 56...166 м2. До цієї групи відносять котли типу «Энергия», «Тула», «Минск» та ін. При встановленні парозбірників котли груп КЧ-2 та КЧ-,3 можуть бути використані для одержання насиченої пари із надлишковим тиском 0,068 МПа.
Чавунний спеціальний водогрійний котел «Универсал-6» (рис. 4.8) залежно від кількості секцій випускають семи типорозмірів за потужністю у водогрійному та паровому виконанні. Він пристосований для спалювання різних видів палива. При цьому змінюють висоту топки шляхом регулювання положення колосникової решітки по висоті. У сільській місцевості для опалення використовують малометражні водогрійні котли ВНИИСТО-Мч та інші (табл. 3.4). Топки цих котлів пристосовані для спалювання твердого палива.
3.4. Технічна характеристика чавунних водогрійних котлів.
Марка котла | Площа поверхні нагріву дійсна, м2 | Кількість секцій, шт. | Теплова потужність котла, МВт | Маса, кг | |
ВНИИСТО-Мч | 1,18...3,74 | 4...11 | 0,012...0,049 | 214...479 | |
“Универсал” | 12,4...36,8 | 12...32 | 0,130...0,360 | 1393...3012 | |
“Универсал-2” | 26,7 | 0,267 | |||
“Универсал-3” | 18,2...40,6 | 14...30 | 0,192...0,424 | 1628...3108 | |
“Универсал-4” | 21,4...55,4 | 14...34 | 0,215...0,558 | 1707...3597 | |
“Универсал-5” | 15,2...42,1 | 14...38 | 0,229...0,520 | 1545...3595 | |
“Универсал-6” | 8,4...15,8 | 9...17 | 0,151...0,286 | 972...1580 | |
“Энергия-3” | 36,8...73,6 | 18...34 | 0,419...0,537 | 3062...4203 | |
“Энергия-6” | 27,9...52,7 | 20...36 | 0,436...0,735 | 2860...4758 |
Стальні водогрійні котли мають велику надійність роботи у разі перегріву. Недоліком є піддатливість до корозії.
Секційний котел «НИИСТУ-5» призначений для вироблення гарячої води температурою 155 °С. Він може бути переобладнаний у паровий котел із надлишковим тиском 0,068МПа. Паливом служить антрацит, високоякісне кам’яне вугілля або газ.
Котел марки НР-18 працює на газі, антрациті, бурому вугіллі. Його виготовляють у трьох модифікаціях—з площею поверхні нагріву 27, 40 і 53 м2. Максимальне значення температури гарячої води — 115 °С.
Для централізованого теплопостачання великих господарств використовують водогрійні котли типу ТВГ, що працюють на природному газі.
Останнім часом промисловість випускає котли нової уніфікованої серії трьох модифікацій: КВ-ГМ (КВ — котел водогрійний, ГМ— газомазутний); КВ-ТС (КВ — котел водогрійний, Т — тверде паливо, С — шаровий спосіб спалювання); КВ-ТК (КВ—котел водогрійний, Т—тверде паливо, К—камерний спосіб спалювання), їх поділяють на чотири групи. До першої відносять котли невеликої теплопродуктивності (теплової потужності 4,6 та 7,5 МВт).
|
Рисунок 4.8. Чавунний секційний водогрійний котел “Універсал-6”
1 – ніпель на виході гарячої води; 2 – середня секція; 3 - крайня секція; 4 – обмурування; 5 – ніпель на вході зворотної води; 6 – газохід.
Технічні характеристики сталевих водогрійних котлів наведені у табл. 3.5.
3.5.Технічна характеристика сталевих водогрійних котлів.
Марка котла | Поверхня нагріву, м2 | Теплова потужність, МВт | ККД, % | Габаритні розміри, мм | ||
довжина | ширина | висота | ||||
НИИСТУ-5 | 46,5 | 0,733 | 72...85 | |||
ТВГ-4 | -- | 5,0 | ||||
ТВГ-8 | -- | 9,55 | ||||
КВ-ГМ-4 | 127,3 | 4,64 | 86...90 | |||
КВ-ГМ-6,5 | 199,3 | 7,54 | 87...91 | |||
КВ-ГМ-10 | 282,3 | 11,63 | 89...90 | |||
КВ-ГМ-20 | 323,4 | 23,25 | 87...90 | |||
КВ-ГМ-30 | -- | 34,9 | 90...91 |
План заняття.
1. Допоміжні поверхні нагріву котельних агрегатів.
2. Водне господарство та водний режим котлів. Внутрішньо котлові процеси у котельних агрегатах.
3. Тягодуттьове обладнання.
4. Живильні пристрої.
5. Шлакозоловидалення.
6. Золоуловлювачі.
7. Контрольно-вимірювальні прилади. Арматура котлів і трубопроводів. Гарнітура котлів.
8. Компоновка котельних.
Література: Б.Х.Драганов., О.Ф.Буляндра., А.В.Міщенко. “Теплоенергетичні установки і системи в сільському господарстві”. К.: “Урожай”., 1995р.
1. ДОПОМІЖНІ ПОВЕРХНІ НАГРІВУ КОТЕЛЬНИХ АГРЕГАТІВ
До допоміжних поверхонь нагріву відносять водяні економайзери, повітропідігрівники та пароперегрівники.
Економайзер для нагріву живильної води та повітропідігрівник для нагріву дуттьового повітря розташовані у кінці конвективного газоходу і обмиваються газоподібними продуктами згорання, що виходять із котельного агрегату, із відносно низькою температурою. Тому їх називають також низькотемпературними або хвостовими поверхнями нагріву. При встановленні економайзерів та повітропідігрівників знижується температура продуктів згорання на виході із котла, через що зменшуються втрати із відхідними газами і підвищується ККД котлоагрегату.
1.1. ЕКОНОМАЙЗЕРИ
Залежно від конструктивного виконання економайзери поділяють на чавунні, стальні гладкотрубні та стальні із оребрених труб.
|
Рисунок 5.1. Чавунний економайзер.
Внаслідок ребристої поверхні економайзери чутливі до забруднення золою. Ребристі труби очищають обдуванням парою або повітрям.
|
Рисунок 5.2. Стальний економайзер.
1 – змійовик із труб; 2 – вихідний колектор; 3 – вхідний колектор; 4 – опора змійовиків.
В економайзерах киплячого типу поряд із підігрівом води утворюється пара (звичайно не більше 20...25 % всієї води).
Економайзери обладнані контрольно-вимірювальними приладами, арматурою і запобіжними пристроями. У найвищій точці економайзера встановлений пристрій для видалення повітря (вантуз) у період заповнення економайзера водою. Крім того, наявна дренажна труба для видалення води економайзера після зупинки котла.
1.2. ПОВІТРОПІДІГРІВНИКИ
Застосування для дуття гарячого повітря підвищує температуру у топці, полегшує підсушку і займання палив, прискорює процес їх згоряння. Крім того, зменшуються втрати теплоти від хімічної неповноти згоряння. Тому застосування повітропідігрівників дає значний тепловий та економічний ефект.
За принципом роботи повітропідігрівники поділяють на рекуперативні і регенеративні. Регенеративні повітропідігрівники застосоують лише у котлах із великою продуктивністю. У котлах малої та середньої продуктивності встановлюють рекуперативні трубчасті повітропідігрівники (рис. 5.3). Для їх виготовлення використовують стальні труби діаметром 51х1,5; 40х1,5; 25х1,5 мм. Труби вставляють в отвори трубних дощок, а їх кінці приварюють.
Пучки труб повітропідігрівників розміщені у шаховому порядку. Міжтрубний простір ділиться на кілька ходів.
|
Рисунок 5.3. Трубчастий стальний повітропідігрівник.
а – з одним ходом для повітря; б – з трьома ходами для повітря.
1.3. ПАРОПЕРЕГРІВНИКИ
Пароперегрівники являють собою систему включених по парі змійовиків, що обмиваютьсяіз зовнішнього боку продуктами згоряння палива, і призначену для перегріву насиченої пари до заданої температури.
Для виготовлення пароперегрівників використовують високолеговану сталь, оскільки теплові напруження у перегрівнику дуже великі. Діаметр труб змійовиків — 30...40 мм.
Розміщення змійовиків пароперегрівників може бути вертикальним (у вертикально-водотрубних котлах) і горизонтальним (у горизонтально-водотрубних котлах).
За умовами зовнішнього теплосприйняття розрізняють конвективні, радіаційні та коннективно-радіаційні пароперегрівники. Останні пароперегрівники розміщують у зоні високої температури продуктів згоряння, тому тепловий потік до них передається здебільшого за рахунок випромінювання.
За взаємним напрямком потоків газу і пари пароперегрівники поділяють на паралельнотокові, протитокові та із змішаним током (рис.5.4). Найбільше застосування знайшли змішані схеми включення пароперегрівника.
У котельних агрегатах застосовують конвективні та комбіновані пароперегрівники. Конвективний пароперегрівник розміщують у газоході котельного агрегату за топкою. Пароперегрівник відділяється від топки невеликим фестоном, що складається із двох-трьох рядів кип'ятильних труб. Ці підігрівники знайшли застосування у котлах низького та середнього тиску. При тиску пари 1,4 і 2,3 МПа конвективні пароперегрівники виконують одноходовими; при тиску 4,0 МПа — двоходовими.
|
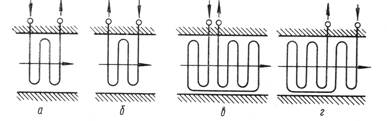
Рисунок 5.4. Схема взаємного руху пари і газу в пароперегрівниках.
Конвективний пароперегрівник для котлів ДКВР та Е зображений на рис. 5.5. Конвективний пароперегрівник котельних агрегатів екранного типу виконують із двох послідовно розміщених груп змійовиків (рис. 5.5). У котлах типу КВ-300М перегрів пари до температури 130 °С відбувається у вертикальному перегрівнику, розміщеному за котлом.
![]() |
Рисунок 5.5. Конвективні пароперегрівники.
а – типу ДКВР та Е; б – екранного типу;
1 – труби пароперегрівника; 2 – камери перегрітої пари; 3, 4 – барабани котла; 5 – камера насиченої пари; 6 – камера ненасиченої пари; 7 – проміжні камера; 8 – вихідна камера; 9 – змійовик; 10 – перша ступінь перегрівника.
У парових котлах низького тиску перегрів пари регулюють газовою заслінкою, за допомогою якої змінюють кількість парів, що протікають через пароперегрівник.
У котлах середнього тиску для цієї мети застосовують спеціальні пристрої (так звані пароохолодники).
2. ВОДНЕ ГОСПОДАРСТВО ТА ВОДНИЙ РЕЖИМ КОТЛІВ.
ВНУТРІШНЬОКОТЛОВІ ПРОЦЕСИ У КОТЕЛЬНИХ АГРЕГАТАХ
2.1. ХАРАКТЕРИСТИКИ КОТЛОВОЇ ВОДИ
Робочим тілом у котлах є вода. Якість води має велике значення для нормальної роботи котлоагрегатів. Тому вода, що безпосередньо використовується для виробництва пари або гарячої води, заздалегідь обробляється. Вона проходить систему попереднього обігріву, очистки від механічних та розчинених хімічних та газоподібних домішок.
У циклі котлоагрегату на різних стадіях процесу розрізняють: вихідну воду, що готують в установках хімічної очистки води і додають до конденсату, що повертається в котел; живильну воду, що подають насосом в котел, вона дорівнює сумі конденсату, що повертається, і підживлювальної води; котлову воду, що циркулює в котлі.
Якість живильної, додаткової та котлової води характеризується такими показниками.
Завислі речовини, що виражаються у міліграмах на кг (мг/кг) — це механічні домішки, що видаляють із води шляхом фільтрування. Сухий залишок, мг/кг, вказує на кількість розчинених у воді речовин. Його отримують випарюванням відфільтрованої води при температурі 105...110°С.
Окислюваність характеризує вміст у воді органічних речовин. Останні, потрапляючи у котлову воду, спінюють її та погіршують якість одержуваної пари.
Жорсткість води визначається вмістом накипоутворюючих речовин (солей магнію).
Лужність визначається концентрацією у воді гігроксильних ОН, бікарбонатних НСОз, карбонатних СОз, силікатних SіОз-іонів, а також деяких слабких органічних кислот, які називають гуматами.
Кремнієвміст, мг/кг, характеризується концентрацією у воді сполук кремнію.
Крім того, у воді містяться розчинені гази. Вони визначають корозійні властивості води. За крупністю мінеральні та органічні домішки, що знаходяться у природній воді, розділяють на грубо дисперсні речовини розміром частинок більше 0,1·10-2 мм і на колоїдні домішки із частинками від 0,1·10-2 до 0,1·10-4мм.
До живильної води парогенераторів і до підживлювальної води водогрійних котлів ставлять певні вимоги (табл.2.1).
Для зменшення концентрації речовин, що забруднюють котлову воду, проводять продувку. Для зниження вологості пари у барабані котла передбачені спеціальні сепарувальні пристрої.
2.1.Норми якості живильної води для водотрубних парових котлів.
Показник | Норма для котлів, що працюють при тиску МПа | |
до 1,4 | до2,4 | |
Загальна жорсткість, мкг·екв/кг | 10/21 | 15/10 |
Вміст у воді компонентів: | ||
| ||
| 50/30 | 50/20 |
Значення рН при t=250С | 8,5...9,5 | 8,5...9,5 |
2.2. ПІДГОТОВКА ВОДИ ДО ЖИВЛЕННЯ КОТЛА
Завислі та колоїдні речовини, що містяться у природній воді, можуть бути видалені шляхом відстоювання, коагуляції та фільтрування. Для відстоювання води використовують відстійники, об'єм яких дорівнює полуторній або подвійній годинній продуктивності котла. Після відстоювання воду піддають фільтруванню, для чого її пропускають через напірні фільтри, заповнені дрібнодисперсним матеріалом (кварцевий пісок, мармур, доломіт) із розмірами частинок 0,6...1 мм.
Ефективнішим є процес коагуляції, завдяки якому за рахунок спеціальних реагентів-коагулянтів відбувається укрупнення колоїдних частинок і зависей та виділення їх у осад. Як коагулянти використовують солі алюмінію та залізосульфат алюмінію АІ2(SO4) з, сульфат заліза FeSO4х7Н2О і хлорне залізо FeCl3·6H2O.
Для видалення гумінових речовин рекомендується підтримувати рН=3,5...4,5. У разі коагуляції води солями заліза рН має бути більше 8,5. У процесі коагуляції температура води повинна бути рівною плюс 35...40 °С.
Залежно від жорсткості води і продуктивності котла застосовують різні способи водопідготовки. У дрібних котельних установках застосовують внутрішньокотельну обробку води; при значній жорсткості у котельнях середньої та великої потужності — докотлову водопідготовку. Найпоширенішими є методи Nа-катіонування та Н-катіонування. Ці методи відрізняються високим ступенем зм'якшення, компактністю апаратури і -простотою обслуговування.
Водопідготовка у Nа-катюнітових установках полягає у фільтруванні через шар природного натрієвого матеріалу (катіоніту). При цьому кальцієві або магнієві солі, що містяться у воді, вступають в обмінні реакції із названим мінералом, у результаті чого замість накипоутворюючих катіонів утворюються еквівалентні кількості легко розчинних натрієвих солей.
У процесі експлуатації катіонітова маса забруднюється і ущільнюється. Для очистки та попереднього спушування катіонітової маси її промивають зворотним потоком води.
Регенерацію катіоніту здійснюють розчином NаСІ. Тривалість регенерації для нового фільтру 12...15 хв; а для експлуатованого— 1,5...2 год.
В установках Н-катіонування як катіоніт використовують сульфовугілля. Цей метод катіонування поєднують із Nа-катіонуванням.
|
Рисунок 5.6. Схема послідовного Н- і Na-катіонування.
Останнім часом, крім традиційних способів, використовують магнітний метод очистки води. Цей метод полягає в тому, що після впливу на воду магнітного поля певної напруженості і полярності та при наступному її нагріванні у котлі не утворюються накипні відкладання на поверхнях нагріву.
У воді, що надходить після фільтрів або інших видів очистки, можуть міститися гази: кисень, двоокис вуглецю, аміак, азот тощо. Ці гази спричиняють посилення корозії поверхні нагріву котла, а також сприяють порушенню циркуляції води. Все це знижує строк служби і надійність роботи котла.
Для видалення газів із живильної води застосовують деаерацію останньої. Цей процес ґрунтується на фізичному законі, згідно із яким розчинність газів із підвищенням температури знижується і для будь-якого тиску при температурі кипіння дорівнює нулю. Такий процес деаерації називають термічним. Залежно від величини тиску, при якому відбувається деаерація, деаератори поділяють на вакуумні (працюють при вакуумі 0,06...0,093 МПа і температурі 40...75°), атмосферні (температурою 95...100 °С) і підвищеного тиску (температурою понад 100 °С). Для досягнення найкращої деаерації необхідно, щоб різниця між температурою кипіння і кінцевою температурою, так званим недогрівом води, у деаераторі була мінімальною, тобто становила 0,1...0,2 °С.
Принципова схема деаераторної установки наведена на рис. 5.7.
| |||
![]() | |||
Рисунок 5.7. Схема деаераторної установки.
Деаератор складається із деаераторної колонки і деаераторного бака 10. Живильна вода надходить по трубі 2 на розподільні тарілки, із яких струмками стікає донизу. Знизу вверх по трубі надходить пара для підігріву води. При нагріві води виділяються гази, що відходять через вестову трубу. Вивільнена від газів вода стікає у бак 10, звідки живильним насосом подається в котел. Для уникнення підвищення тиску у деаераторі на ньому встановлюють запобіжний клапан. На випадок утворення у деаераторі розрідження передбачають гідравлічний затвор. Його встановлюють висотою 3,5...4 м.
Для зменшення концентрації речовин, що забруднюють воду, проводять продувку, тобто видаляють із котла частину води і замінюють її живильною водою.
Розрізняють безперервну та періодичну продувки. Безперервну продувку проводять із місць з найвищим солевмістом, тобто до змішування котлової води із підживлювальною. Об'єм безперервної продувки становить 0,5...3 % паропродуктивності котла. Періодична продувка ефективна тільки в котлах із грязьовиками, в яких відбувається відокремлення шламу.
Грязьовики включені у систему циркуляції води.
2.3. ВНУТРІШНЬОКОТЛОВА ГІДРОДИНАМІКА.
У процесі підігріву води і пароутворення необхідно безперервно відводити теплоту, що передається продуктами згоряння поверхням нагріву котельного агрегату. Для цього забезпечують рух води або пари в елементах котла. У випарювальних поверхнях нагріву рух відбувається за рахунок природної циркуляції, а в прямотокових котлах — примусово під впливом живильних насосів (прямо токові котли застосування у сільському господарстві не знаходять).
В еконономайзерах або пароперегрівниках рух води забезпечується насосом або різницею напорів у барабані і пароперегрівнику.
| |||
![]() | |||
Рисунок 5.8. Схема природної циркуляції.
1 – верхній барабан; 2 – нижній барабан; 3 – тепло сприймальні поверхні.
При сталому режимі роботи котельного—агрегату тиск, який забезпечує природну циркуляцію, врівноважується гідравлічними опорами, що дорівнюють сумі опорів підйомних та опускних труб:
Ррух=ΣΔРпід+ΣΔРоп. (5.1)
Це рівняння носить назву розрахункового рівняння циркуляції.
Відношення витрати води, що увійшла до циркуляційного контуру, до кількості утвореної у ньому пари, називають кратністю циркуляції К у контурі. Величина К більша за одиницю.
Для забезпечення нормальної роботи циркуляційних контурів необхідно створити умови рівномірного обігріву водопідйомних труб. Одним із ефективних експлуатаційних заходів у цьому відношенні є запобігання шлакуванню і заносу леткою золою водопідйомних труб.
ТЯГОДУТТЬОВЕ ОБЛАДНАННЯ
Для нормальної роботи котельного агрегату необхідно забезпечити безперервну подачу повітря у топкову камеру, переміщення продуктів згоряння по газоходах та їх наступне видалення із агрегату. При русі по газоповітряному тракту продукти згоряння мають подолати аеродинамічний опір, на що витрачається певна кількість енергії.
Рух повітря і продуктів згоряння здійснюється за допомогою тяги. Тяга може бути природною і штучною.
Природна тяга використовується у котельних агрегатах малої потужності (до 2,5 т/год) без хвостових поверхонь нагріву і з невеликим опором газового тракту (50...60 Па).
У цьому випадку тяга забезпечується рушійною силою, зумовленою різницею статичних тисків між повітрям, що надходить у топкову камеру, і продуктами згоряння, що залишають котельну установку. Силу тяги, тобто рушійну силу, необхідну для подолання гідравлічних опорів, створює димар.
Тяга тим більша, чим вищий димар, більша температура відхідних газів і чим нижча температура зовнішнього повітря. Для зміни режиму тяги використовують заслінки.
Залежно від потужності котельних агрегатів або котельної установки димарі будують стальними, цегляними або залізобетонними. Для тимчасових і невеликих котелень стальні димарі можуть мати висоту до 40 м. Для котельних установок середньої потужності—цегляні труби до 80 м.
Висоту труби вибирають залежно від виду тяги (природна або штучна) та вимог санітарно-технічних норм.
При штучній тязі димар призначений для відведення продуктів згоряння в атмосферу на висоту, що визначається санітарно-гігієнічними та протипожежними вимогами.
Діаметр труби залежить від сумарної кількості продуктів згоряння, що залишають котельні агрегати і швидкості газів на виході з труби. Значення швидкості знаходиться у межах 6...10 м/с.
У сучасних котлоагрегатах, обладнаних хвостовими поверхнями нагріву, природна тяга не може забезпечити потрібну швидкість руху газоповітряного потоку і його видалення в атмосферу. У цьому випадку застосовують штучну тягу із встановленням дуттьових вентиляторів та димососів. Вибір димососів і вентиляторів здійснюють із розрахунку на максимальне навантаження котельного агрегату (номінальну продуктивність). Це забезпечує їх нормальну роботу при різноманітних режимах котельної установки.
Для подачі повітря у топку застосовують найчастіше радіальні дуттьові вентилятори. Вентилятори однобічного всмоктування ВД (при температурі всмоктуваного повітря 20 °С) і димососи Д, що видаляють продукти згоряння з температурою до 250 °С, виготовляють правого та лівого обертання.
Димосос піддається впливові високих температур та механічному зносу золою. Якщо спалюється багатозольне паливо, лопатки димососів мають бути наплавлені спеціальними твердими сплавами для їх захисту від можливого зносу.
Потужність N, Вт, двигуна для привода димососа або вентилятора визначають за формулою:
N=1,1LPn/η (5.2)
де 1,1—коефіцієнт запасу по потужності; L—продуктивність димососа або вентилятора, м3с; Рn— повний тиск димососа або вентилятора, Па; η — ККД димососа або вентилятора.
При штучній тязі застосовують кілька способів регулювання.
Дросельне регулювання полягає у тому, що у газоповітряному тракті за допомогою спеціального пристрою — шибера — створюється додатковий опір. Цей спосіб дуже простий, але малоекономічний.
Регулювання сили тяги зміною частоти обертання димососа і вентилятора є більш ефективним. Проте це вимагає застосування електродвигуна із регульованою частотою обертання.
Найбільше поширення знайшов спосіб регулювання продуктивності димососів і вентиляторів напрямними лопатковими апаратами, що встановлюють на всмоктувальних патрубках агрегатів.
4. ЖИВИЛЬНІ ПРИСТРОЇ
Воду в котли подають живильними пристроями. При цьому використовують насоси різних типів: поршневі або відцентрові із електричним або паровим приводом. Крім того, у невеликих опалювальних котельнях як живильні пристрої застосовують інжектори і ручні насоси.
У котельних установках повинно бути передбачено не менше двох живильних насосів із різними приводами. Допускається установка обох живильних насосів із паровими приводами. Подача кожного насоса має бути не менше 120 % потрібної максимальної подачі робочих котлів.
Для живлення парових котлів продуктивністю до 150 кг/год і тиском не більше 0,4 МПа допускається застосовувати один ручний насос. Другий ручний насос передбачають для живлення водогрійних котлів із загальною поверхнею нагріву до 150 м2.
У виробничих опалювальних котельнях для подачі води в агрегати в основному застосовують поршневі насоси із паровим приводом і відцентрові — із електричним приводом.
Поршневі насоси встановлюють у котельних установках невеликої потужності. Найширше насоси ПВД і ПДГ використовують для живлення котлів водою при температурі до 100 °С. Так, вертикальні двоциліндрові парові насоси типу ПДД призначені для живлення парових котлів ДКВР.
На поршневому насосі повинні бути розміщені манометр і запобіжний клапан на нагнітальному трубопроводі, засувки на нагнітальному і всмоктувальному трубопроводах, вентиль на паропровідному та вихлопному трубопроводах, продувальні клапани для випуску конденсату з циліндрів при прогріві насоса парою.
Відцентрові насоси є найпоширенішими у системі живлення котлів. Вони подають воду рівномірно, відзначаються високою економічністю, зручністю регулювання продуктивності. До недоліків відносять: необхідність тримати насос під заливом або заповнювати його перед пуском; зменшення ККД при малій продуктивності. Відцентрові живильні насоси виготовляють одно- або багатоступінчастими залежно від подачі і робочого тиску.
На відцентровому насосі встановлюють манометри і засувки на всмоктувальному та нагнітальному трубопроводах, приймальний клапан на всмоктувальному трубопроводі, зворотний клапан на нагнітальному трубопроводі, крани для випуску повітря у верхній частині корпусу кожного ступеня.
Для живлення водою дрібних опалювальних котелень застосовують інжектори, що є пароструминними пристроями. Витрата пари становить 7...9 % кількості води, що подається. Температура води, що надходить у інжектор, не повинна перевищувати плюс 40 °С. Висота подачі води інжектором — не більше 2 м. Інжектори мають просту будову, займають мало місця.
У насоси вода надходить із живильних або деаераторних баків. При температурі води понад плюс 70 °С вода повинна надходити у насос під деяким напором. Тому баки встановлюють вище живильного насоса.
Живильні насоси вибирають із умови забезпечення потрібної продуктивності і необхідного напору.
Продуктивність живильного насоса Lжн, м3/с, визначають за формулою:
Lжн=1,2(D/ρ) (5.3)
де 1,2—коефіцієнт запасу па продуктивності; D—максимальна продуктивність всієї котельні, кг/с; ρ—густина, кг/м3.
Повний напір, необхідний для подачі води у котел:
Нжн=(Рн-Рп) (5.4)
де Рн—тиск у нагнітальному патрубку насоса, Па; Рп — тиск у приймальному патрубку насоса. Па.
У першому наближенні для розрахунку напору, що розвивається живильним насосом, можна користуватися формулою:
Нжн=1,1[Рб+(0,15...0,20)] (5.5)
де 1,1—коефіцієнт запасу по напору; Рб—робочий тиск у барабані котельного агрегату, Па; 0,15...0,20—число, що враховує втрати напору у трубопроводах і живильній арматурі, Па.
Потужність N, Вт, потрібну для привода насоса, визначають із виразу:
N=(Lжн Нжн) /η (5.6)
де Lжн—продуктивність насоса, м3/с; Нжн—повний напір насоса, Па; ηн—ККД насоса, що дорівнює 0,70...0,85.
5. ШЛАКОЗОЛОВИДАЛЕННЯ
У процесі спалювання палива виділяються шлак, що залишається у топці, і зола, що провалюється через колосникову решітку або виноситься із продуктами згоряння.
Остання частково осідає у газоводах і зупиняється золоуловлювачами, а частково через димову трубу викидається в аьмосферу. При камерному спалюванні твердого палива основна маса золи іде з газами.
Процес шлакозоловиділення складається із видалення золи та шлаку із котельних агрегатів, прибирання та їх транспортування з території. У котельних установках застосовують такі способи шлакозоловидалення: ручний, механічний, пневматичний та гідравлічний.
Ручне шлакозоловидалення застосовують тільки у котельних установках паропродуктивністю до 2 т/год. Шлак і зола потрапляють у бункер, розміщений під колосниковими решітками. Із бункера шлак і золу вагонеткою вивозять із приміщення котельні.
Механізоване шлакозоловидалення провадиться кількома способами. Найпростіший із них полягає у переміщенні вагонеток по похилій естакаді за допомогою електролебідки. Більш широко застосовують скреперні установки, що забезпечують сухе або мокре золовидалення (рис. 5.9).
Шлак і зола, попередньо залиті водою (при мокрому способі) надходять у шлаковий канал 2, звідки скреперами 3 по похилій естакаді подаються в бункер 6, встановлений за межами будівлі котельні. Із бункера шлак і зола потрапляють у кузов автомобіля. Скрепер пересувається по вузькоколійних рейках за допомогою лебідки та канатів.
Пневматичні системи шлакозоловидалення застосовують при виході вогнищевих залишків 0,3...10 т/год.
Рисунок 5.9. Схема скреперного шлакозоловидалення.
1 – топки котлів; 2 – шлаковий канал; 3 – скрепер; 4 – система канатів; 5 – шибер; 6 – затвор; 7 – шлаковий бункер.
Вони можуть бути нагнітального або всмоктувального типу. Перевага віддається схемі пневматичної системи шлаковидалення всмоктувального типу. Швидкість повітря у трубопроводі при пневмотранспорті шлаку і золи повинна бути не менше 25 м/с. Концентрація завислих у повітряному потоці частинок не повинна перевищувати 3,5...7,0 кг на 1 кг повітря. Попередньо шлак подрібнюється у дробарці до розміру не більше 20 мм.
Системи пневмошлаковидалення відрізняються компактністю, простотою побудови і обслуговування. Основний недолік цих систем — велика витрата електроенергії на транспортування шлаку та золи.
Гідравлічні системи шлакозоловидалення застосовують при необхідності видалення шлаку і золи понад 10 т/год при достатній кількості води і близькості золовідвалу. У цій системі транспортуючим агентом є вода.
Дата добавления: 2014-12-16; просмотров: 2369;