Виробництво збірних залізобетонних виробів та конструкцій
Незалежно від засобу виготовлення, номенклатури виробляємої продукції та технологічної схеми виробництва, процес виробництва збірних залізобетонних виробів та конструкцій включає такі головні операції – підготовку форм або формуючої стрічки (встановлення форми, очищення, змазка внутрішньої поверхні форм або формуючої стрічки); виготовлення арматурних сіток, каркасів, закладних виробів і їх встановлення у форму (в разі використання попередньо напруженої арматури виконується натяжіння арматури); виготовлення бетонної суміші; її укладання і ущільнення у формах; тепловологісна обробка відформованих виробів; розпалубка вироблених виробів; опорядження виробів; контроль якості виробів; транспортування виробів на склад; їх зберігання і відправлення на будівництво. Як правило, підприємства виробничої бази забезпечують одночасне виробництво багатьох видів конструкцій і виробів, і тому мають декілька спеціалізованих технологічних ліній, які відрізняються по складу операцій, послідовності їх виконання.
В теперішній час залежно від взаємного розміщення у просторі засобів праці (технологічного обладнання), предметів праці (форм, матеріалів, напівфабрикатів та робітників) можливі два варіанти організації виробництва на заводах залізобетонних виробів і конструкцій:
1) технологічне обладнання та робітники не переміщуються, а форми з виробами переміщуються;
2) форми нерухомі, переміщуються обладнання та робітники.
До першого варіанта процесу належать агрегатне та конвеєрне виробництво, до другого – стендове та касетно-стендове.
При агрегатному способі всі частини процесу здійснюються на спеціалізованих постах, обладнаних машинами для виконання відповідної роботи. Форми з виробами для виконання всіх стадій обробки послідовно переміщуються від поста до поста. Формують вироби на спеціально обладнаних установках – агрегатах, що складаються з формоукладача, бетоноукладача, віброплощадки чи центрифуги. Відформовані вироби піддають тепловій обробці в камерах прискореного твердіння періодичної дії. Завершальною стадією виробництва є видача виготовлених виробів і конструкцій та вивезення до складу готової продукції. Принципова схема агрегатного способу виробництва наведена на рис.3.1. Агрегатна технологія дозволяє суміщувати операції в часі і значно підвищити продуктивність використовуємих машин і механізмів. Перехід з виробництва одного виду виробів на другий не потребує переналадки обладнання, а здійснюється тільки за рахунок заміни форм. Агрегатне виробництво потребує відносно незначних капітальних вкладень. У зв’язку з цим, цей метод отримав найбільше розповсюдження на заводах ЗБВ, які виготовляють широку номенклатуру виробів і конструкцій. Недоліками агрегатного способу є необхідність виконання значної кількості немеханізованих робіт, порушення робочого ритму при тепловологій обробці виробів у камерах ямного типу, необхідність переміщення технологічного оснащення від поста до поста за допомогою вантажопідйомних механізмів. Це вимагає посилення конструкцій форм, призводить до надмірного збільшення їхньої маси та є причиною утворення технологічних тріщин у затверділому бетоні.
![]() |
Рис.3.1. Принципова схема агрегатного способу виробництва залізобетонних конструкцій
Конвеєрний спосіб виробництва передбачає переміщення виробів у процесі їх виготовлення від одного спеціалізованого технологічного поста до іншого із заданою швидкістю. Переміщення може бути пульсуючим або безперервним. За кожним постом закріплюють обладнання і ланку робітників для виконання відповідної роботи. Конвеєрна технологія найбільш ефективно використовується при масовому виготовленні однотипних виробів на великих спеціалізованих підприємствах. Перевагами цієї технології є висока ступінь механізації і автоматизації головних технологічних процесів. До недоліків конвеєрної технології можна віднести великі капітальні вкладання, а також необхідність складної переналадки обладнання при переході на виробництво нових видів виробів. Головною умовою ефективного здійснення конвеєрного виробництва є однакові витрати часу для виконання робіт на кожному посту. Після закінчення цього часу форми переміщують до іншого робочого поста. Цей період часу зветься ритмом конвеєра. Залежно від виду руху розрізняють конвеєри безперервної дії (пластинчаті, ланцюгові) та крокової дії (візкові).
Принцип виготовлення виробів на конвеєрі безперервної дії застосовано на ВПС – вібропрокатних станах, усі технологічні операції (від укладання бетонної суміші до теплової обробки та видачі готового виробу) тут здійснюють на одному устаткуванні – пластинчатому конвеєрі, що рухається з постійною швидкістю.
Найпоширеніші візкові конвеєри крокової дії. Вироби на них виготовляють на пересувних піддонах, які утворюють безперервну конвеєрну лінію з 6-15 постів. Камери теплової обробки є частиною замкненого конвеєрного кільця. Залежно від типу теплових агрегатів розрізняють конвеєрні лінії з щілинними підземними і надземними камерами, з камерами вертикального типу, з безкамерною тепловою обробкою виробів у пакетах теплоформ. Залежно від взаємного розміщення теплового агрегату та підготовчо-формувальної гілки розрізняють вертикально-замкнений, горизонтально-замкнений та похило-замкнений конвеєр.
На конвеєрних лініях виготовляють майже 40% загального виробництва збірного залізобетону для промислового та цивільного будівництва: зовнішні та внутрішні стінові панелі, плити перекриттів та покриттів, колони та ригелі промислових будівель. На кругових конвеєрах виготовляють вироби добору та санітарно-технічні кабіни. Принципова схема виробництва збірних залізобетонних виробів конвеєрним способом наведена на рис.3.2.
При стендовому способі вироби і конструкції виготовляють у нерухомих формах або на спеціально обладнаних для цього робочих місцях – стендах. Під час формування і до набуття бетоном потрібної міцності вироби залишаються нерухомими тоді, як технологічне обладнання та робітничі ланки, які його обслуговують, переміщаються від однієї форми на стенді до другої. Стендова технологія виробництва використовується при виготовленні конструкцій, габаритні розміри і маса яких перевищують розміри і вантажність віброплощадок – ферм, двосхилих балок великих прогонів, колон завдовжки більш, як 12 м. Особливо ефективний цей спосіб для виготовлення попередньо-напружених конструкцій. Стенди можуть бути незаглибленими або лотковими та заглибленими. Незаглиблений стенд зручно використовувати для формування великорозмірних елементів у стендових термоформах. Лотковий стенд заглиблюється відносно рівня підлоги, його перекривають кришками і здійснюють у ньому теплову обробку. Недоліками стендового способу виробництва є низьке використання виробничої площі і те, що всі джерела матеріальних та енергетичних ресурсів треба підводити до кожного стенду окремо.
Особливість касетного способу виробництва полягає в тому, що вироби формують у вертикальному положенні в металевих формах-касетах, де вони перебувають до набуття бетоном заданої міцності. Розрізняють два способи організації касетного виробництва – касетно-стендовий і касетно-конвеєрний. Касета – це ряд формувальних та парових відсіків. Під час виробництва, послідовно пересуваючи відсіки, здійснюють розпалублення і підготовку кожного формувального відсіку касетної установки. Після цього всі формувальні відсіки одночасно заповнюють бетонною сумішшю. Ущільнюють суміш навісними або глибинними вібраторами. Теплова обробка виробів проходить безпосередньо в касеті.
При касетно-стендовому способі виробництва ланка робітників переходить від однієї касетної форми до іншої, виконуючи всі технологічні операції. При касетно-конвеєрному способі вироби формують у вертикальному положенні, а потім їх переміщують із заданим ритмом по технологічних постах. Касетним способом виготовляють внутрішні стінові панелі, плити перекриттів, сходові марші. Виготовлені у касетних формах вироби мають точні розміри і порівняно високу якість поверхонь. Теплова обробка виробів у касетах здійснюється за інтенсивним режимом, оскільки основна маса бетону перебуває у замкненому просторі і вироби мають невелику частину відкритої поверхні. За показниками питомих капіталовкладень, собівартості касетні лінії близькі до агрегатних, але забезпечують більш високу продуктивність праці, менші витрати пари та електроенергії. Недоліками касетної технології є необхідність застосування рухливих бетонних сумішей, що веде до надмірних витрат цементу, неоднорідності виробів, а також несприятливі умови праці.
![]() |
Рис.3.2. Схема виробництва залізобетонних виробів конвеєрним способом
Формування виробів є однією з найважливіших переробок, яка передбачає, складання форм, установлення арматури, укладання у форму арматурного каркасу та бетонної суміші. Перед формуванням форму очищають, збирають і змазують спеціальними мастилами. Мастило має повністю виключити зчеплення бетону з формою, добре утримуватись на поверхні форми під час всіх технологічних операцій. Бетон вкладають у форму за допомогою бункерів, бетонороздавачів чи бетоноукладачів.
Основний спосіб ущільнення бетонної суміші в процесі виготовлення збірного залізобетону - вібрування. Віброущільнення бетонної суміші виконують переносними та стаціонарними вібромеханізмами. Переносні вібромеханізми використовують під час формування великорозмірних масивних виробів на стендах. На заводах, які працюють за потоково-агрегатною та конвеєрною схемами, застосовують віброплощадки. Вона уявляє собою плоский стіл, який через пружинні опори чи спеціальні амортизатори опирається на нерухомі опори чи станину. У нижній частині до столу жорстко прикріплено вібровал з розміщеними на ньому ексцентриками. Коли вал обертається від електродвигуна, ексцентрики збуджують вимушені коливання столу віброплощадки, які передаються далі формі з бетонною сумішшю, внаслідок чого остання ущільнюється. Заводи збірного залізобетону обладнані уніфікованими віброплощадками вантажністю 2…24 т, які працюють з частотою 3000 кол/хв. та амплітудою коливань 0,3…0,6 мм.
При формуванні труб та опор ліній електромереж застосовують центрифугування, яке полягає в тому, що бетонна суміш, яка завантажена у форму, піддається швидкому обертанню. При виготовленні цим способом труб додатково виконується навивка на трубу арматурної проволоки і нанесення на неї захисного шару цементного розчину.
Литтьове формування ефективне для виготовлення виробів у вертикальних стендових касетах. При цьому поверхні панелей не потребують опорядження.
Для формування штучних виробів невеликого розміру застосовують пресування. Воно дає змогу одержати бетон особливо високих (цільності й міцності при мінімальній витраті в’яжучих. У технології збірного залізобетону можуть використовувати додаткове навантаження до бетонної суміші при її вібруванні. Виконують вібропресування плоскими та профільними штампами. Так формують сходові марші, деякі види ребристих панелей. Різновидом пресування є прокатування.
Щоб надати особливо високої щільності поверхневому шару конструкцій застосовують вакуумування, яке поєднують, як правило, з вібруванням при формуванні залізобетонних виробів.
|
|
|
|
|
|
|
|
|
|
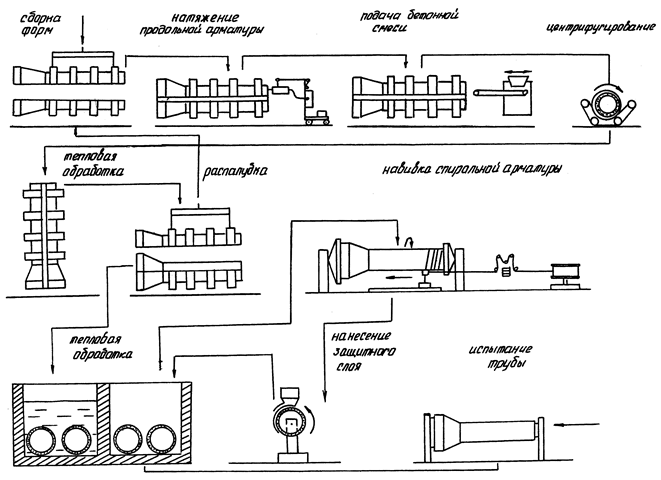
Рис.3.3. Технологічна схема виробництва напірних труб.
Рис.3.4. Схема намотування спіральної арматури на осердя труби: 1 – передня бабка; 2 – осердя труби; 3 – пересувна каретка; 4 – задня бабка; 5 – натягувальний пристрій; 6 – гальмівний ролик; 7 – правильний пристрій; 8 – бухта з дротом.
При виробництві залізобетонних виробів на залізобетонних заводах твердіння виробів при звичайній температурі (15…20ºС) неефективно тому, що зменшує оборотність форм, затримує випуск готової продукції. Щоб прискорити твердіння виробів головним чином застосовують спосіб його теплового прискорення. Цей спосіб можна реалізувати паропрогріванням насиченою водяною парою в ямних чи тунельних камерах, під ковпаками або при контакті відкритої поверхні виробу з теплоносієм; у термоформах чи касетних установках при прогріванні бетону від стінок форм за рахунок теплопровідності.
Камери ямного типу використовують у агрегатній та напівконвеєрній технологіях виготовлення збірних залізобетонних конструкцій. Вони можуть бути розташовані на підлозі, бути напівзаглиблені, або заглиблені, в залежності від рівня грунтової води. Ямну камеру будують з керамзитобетону, її кришку вкладають на гідрозасув. Подавання пари у камеру, його розподіл у ній і відведення здійснюється по трубопроводам. Внутрішні розміри камери залежать від розмірів форм з виробами. Камери розташовують блоками по 6…8 штук для скорочення витрат теплоти у навколишнє середовище. Висота камер залежить від системи паророзподілу у ній й дорівнює від 3 до 4 м. Відстань між формами складає від 50 до 75 мм, між днищами нижньої форми і камери – 150…200 мм, між верхнім виробом та кришкою камери – 50…100 мм.
У конвеєрній технології виробництва збірного залізобетону у поєднанні з вертикально або горизонтально замкненим конвеєром використовують щільові або тунельні камери теплової обробки безперервної дії. Вони можуть бути одно- або багатоярусними довжиною від 60 до 127 м, висотою від 0,7 до 1,2 м. Як теплоносії використовують “гостру” пару, яка стикається з поверхнею бетону, та “глуху”, коли нагрів здійснюється за допомогою регістрів. У щільових камерах з метою поліпшення умов теплообміну монтують у зонах нагріву і охолодження рециркуляційні вентиляційні системи.
З метою інтенсифікації твердіння бетону також застосовують інші види теплового впливу, так, наприклад, електротермообробку бетону. Одним з різновидів електротермообробки є електродний прогрів, який проводять безпосередньо в конструкції за рахунок пропускання електричного струму через бетон, або бетонну суміш. Одним з головних параметрів при розрахунку електропрогріву є питомий електричний опір, значення якого залежить від складу та кількості рідкої фази (вода з розчиненими в ній мінералами цементного клінкеру). Так, наприклад, при збільшенні вмісту води у бетоні від 140 до 230 л на м3 питомий електричний опір знижується в 2,5 рази. Коливання питомого електричного опору у бетонах на портландцементі складає від 3 до 19 Ом на м. При електропрогріві використовують пластинкові та струнні електроди. Найбільш ефективними є пластинкові електроди. Контактну електротермообробку застосовують для безпосередньої теплопередачі від гріючих поверхонь до бетону. Розподіл теплоти у бетоні здійснюється за рахунок теплопровідності. Конструкцію теплоформи вибирають таким чином, щоб поверхня нагрівача максимально перекривала поверхню виробу. Відстань між нагрівачами повинна бути не більш 15 см. Контактний електропрогрів виконується за допомогою сітчатих нагрівачів, які являють собою смугу сіток, послідовно з’єднаних з шинами. Вибір оптимальних режимів прискорення твердіння бетонів залежить від виду цементу, складу бетонів, розмірів конструкції.
Дата добавления: 2016-03-04; просмотров: 5693;