ПОВЕРХНЕВИМ ПЛАСТИЧНИМ ДЕФОРМУВАННЯМ
50. Загальні відомості
Обробку пластичним деформуванням застосовують для надання заготовці потрібної форми і розмірів або для зміцнення поверхневого шару оброблених деталей без істотної зміни розмірів.
У деяких методах зміцнювальної обробки можна досягти підвищення точності та зменшення шорсткості і замінити ними інші методи чистової обробки (шліфування, хонінгування та ін.). Обробка поверхневим пластичним деформуванням забезпечує збільшення міцності від утомленості, стійкості до спрацювання.
Методи обробки поверхневим пластичним деформуванням поділяють на дві групи: формоутворювальні (накатування різьби і зубців) і зміцнювально-калібрувальні (обкатування, калібрування, дробоструминна обробка та ін.).
51. Формоутворювальні методи
1. Накатування різьби. При цьому методі обробки профіль різьби утворюється не вирізуванням, а витисканням витків унаслідок заглиблення в заготовку, що обертається, профілю інструмента. Принцип утворення різьби накатуванням полягає в тому, що заготовка 2 прокатується між двома плоскими різьбовими плашками 1 і 3 (рис. VI.62, а) або між круглими плашками (роликами), що обертаються (рис. VI.62, б). У разі накатування різьби роликами заготовка 2 розміщується на спеціальній підтримці 5 між роликами 4, один з яких здійснює рух подачі, перпендикулярний до осі заготовки.
|
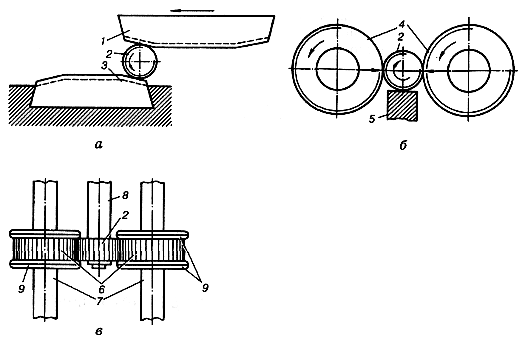
Накатування різьби відзначається високою продуктивністю (в 15...20 разів вища, ніж при нарізанні різальними інструментами), забезпечує високу міцність і якість поверхні накатаної різьби, а також економію металу і високу стійкість інструмента і широко використовується в масовому виробництві болтів, гвинтів, шурупів, шпильок.
2. Накатування зубців зубчастих колісздійснюють холодним, гарячим і комбінованим способами. У холодному стані накатують зубці дрібно-модульних (до 1 мм) шестерень.
Гаряче накатування після нагрівання заготовок струмами високої частоти до 1000...1200 °С виконують так (рис. VI.62, в). Валки (накатники) б, які розміщені на шпинделях 7, переміщаються у напрямі до заготовки 2, встановленої на валу 8. Щоб сформувався заданий евольвентний профіль з обох боків зубців, валкам надається змінний обертальний рух спочатку в одному, а потім у протилежному напрямі. Для обмеження осьової течії металу на обох торцях валків роблять обмежувальні реборди 9. Коли валки дійдуть до встановленої міжосьової відстані, подача автоматично виключиться.
Підвищити точність зубців після гарячого накатування можна наступним холодним калібруванням трьома валками на іншому стані. При такому комбінованому методі під холодне накатування залишають припуск 0,05...0,07 мм на сторону.
Накатування зубців при високій продуктивності, що перевищує зубо-фрезерування, забезпечує значну економію металу, зміцнення і сприятливе розміщення волокон матеріалу зубців. Холодним калібруванням можна замінити чистове зубофрезерування і навіть шевінгування.
52. Зміцнювально-калібрувальні методи
1. Обкатування зовнішніх і внутрішніх поверхонь роликами.Процес обробки полягає в тому, що поверхню деталі, яка обертається, обкатують притиснутими до неї одним, двома або трьома гладенькими роликами, виготовленими з загартованої сталі. Обкатування можна проводити на поширених металорізальних верстатах (токарних, револьверних та ін.) з використанням простого оснащення. На рис. VI.63, а показано схему обкатування роликами циліндричної заготовки на токарному верстаті. В процесі накатування поверхня вигладжується і наклепується. Обкатуванням іноді замінюють менш продуктивну операцію шліфування. Залежно від оброблюваного матеріалу і режимів процесу глибина наклепаного шару може становити близько 0,2...20 мм, а твердість поверхневого шару збільшуватись на 40...50 %. Границя втомлюваності обкатаних деталей зростає на 80 % і більше. Дуже часто як чистову обробку отворів використовують роз-катування їх спеціальними пристроями - розкатками (рис. VI.63, б), яка замінює інші методи чистової обробки, наприклад хонінгування.
2. Калібрування отворів.Найбільш поширеними методами калібрування отворів є дернування і калібрування їх кулькою, що здійснюються на протяжних верстатах і пресах.
Дернування полягає в тому, що калібрувальний інструмент (дорн), який є прошивкою або протяжкою певної форми без різальних зубців, проштовхується або протягується крізь оброблюваний отвір (рис. VI.63, в). Отвір повинен мати дещо менший розмір, ніж калібрувальний дорн. За рахунок пластичних деформацій діаметр отвору при дернуванні збільшується, поверхневий шар металу в отворі зміцнюється і мікронерівності згладжуються. Дернування забезпечує точність ІТ7.
Калібрування кулькою полягає в проштовхуванні крізь попередньо досить точно оброблений отвір сталевої загартованої кульки. Діаметр її має бути дещо більшим за діаметр отвору після проходження кульки для компенсації пружного відновлення матеріалу. Цей спосіб дає змогу калібрувати отвори з криволінійною віссю.
Рис. VI.63. Схеми зміцнювально-калібрувальних методів обробки
Запитання і завдання для самоконтролю
1. Які основні методи обробки поверхневим пластичним деформуванням?
2. Наведіть основні схеми накатування різьби.
3. Дайте характеристику обробки циліндричних поверхонь обкатуванням і
розкатуванням.
4. Наведіть схеми калібрування отворів.
Глава 11. ЕЛЕКТРОФІЗИЧНІ ТА ЕЛЕКТРОХІМІЧНІ МЕТОДИ ОБРОБКИ
53. Загальні відомості
Методи електрофізичної та електрохімічної обробкиґрунтуються на різних фізико-механічних процесах енергетичної дії на тверде тіло, при яких від нього відокремлюються частинки і утворюється деталь з потрібними розмірами і формою.
Залежно від використовуваних фізико-хімічних процесів ці методи обробки можна поділити на чотири групи:
1. Електроерозійні методи обробки струмопровідних матеріалів ґрунтуються на використанні енергії електричних розрядів, які збуджуються між інструментом і деталлю. Розрізняють чотири основних різновиди електроерозійної обробки: електроіскрову, електроімпульсну, електроконтактну та анодно-механічну.
2. Електрохімічна обробка металів і сплавів, що ґрунтується на явищі анодного розчинення в електролітах.
3. Ультразвукова обробка.
4. Променеві способи обробки із застосуванням світлових, електронних або іонних променів.
Ці методи порівняно з іншими мають такі переваги: ними можна обробляти матеріали, які іншими методами обробляються важко або навіть зовсім не можуть оброблятися; завдяки простоті кінематики формоутворення цими методами можна обробляти деталі, які неможливо обробити іншими способами (наприклад, глухі фасонні отвори, порожнини складної форми, отвори з криволінійною віссю, отвори діаметром порядку сотих часток міліметра); можливість відтворення (копіювання) форми інструмента відразу по всій оброблюваній поверхні заготовки при звичайному поступальному русі інструмента; відсутність силової дії на заготовку; обробку цими методами легко автоматизувати.
При обробці звичайних конструкційних матеріалів механічна обробка різанням забезпечує більш високу продуктивність і точність, ніж електрофізичні і електрохімічні методи обробки, тому вона переважно використовується для виготовлення деталей з важкооброблюваних матеріалів і складних за формою.
54. Електроерозійні методи обробки
1. Електроіскрова обробкаґрунтується на явищі руйнування металу в колі постійного струму під дією іскрового розряду. При наближенні металевих електродів у рідкому діелектричному середовищі (гасі, маслі) до відстані пробійного зазора виникає потужний короткочасний іскровий розряд, температура якого становить 6000... 11 000 °С. Це призводить до миттєвого розплавлення, випаровування, вибухів і викидання частинок, які, направляючись до катода, охолоджуються і осідають. Обробка йде без стикання заготовки з інструментом, що дає змогу обробляти струмо-провідний матеріал будь-якої твердості інструментом з м'якого металу (латуні, графіту).
На рис. VI.64, а наведено схему верстата для прошивання отворів. На станині 8 розміщена ванна 5 з діелектричною рідиною, в якій перебуває установчий пристрій 7 із заготовкою 6. Як тільки зазор між електродами - інструментом (катодом) 4 і заготовкою (анодом) 6, які підключені до генератора імпульсів 1, дорівнюватиме пробійному зазору, виникає електричний розряд, на який витрачається вся енергія, накопичена в батареї конденсаторів К. Після розряду конденсаторів, щоб знову їх зарядити, електричний ланцюг переривається. Для цього за допомогою спеціального соленоїдного регулятора 2 і механізму подачі затискний пристрій 3 з інструментом 4 здійснюють під час вертикальної подачі коливальний рух.
Електроіскрова обробка використовується для виготовлення штампів, прес-форм, кокілів, фільєрів з інструментальних сталей і твердих сплавів і забезпечує шорсткість поверхні Rz = 20 - при чорновому режимі і Ra = 1,6...0,63 - при чистовому.
Рис. VI.64. Електроерозійні методи обробки
2. Електроімпульсний метод обробкизначно продуктивніший за електроіскровий. На відміну від електроіскрового методу при цій обробці заготовка є катодом, а інструмент - анодом, між якими досягається послідовне збудження розрядів під дією імпульсів напруги, які виробляються спеціальним генератором. Температура в робочій зоні значно нижча (4000...5000 °С), ніж при електроіскровій обробці, отже, і спрацювання інструмента менше.
Низькочастотна електроімпульсна обробка з живленням від машинного генератора забезпечує шорсткість поверхні Rz = 40, а високочастотна - від транзисторного генератора (з частотою 7... 25 кГц) до Ra = 1,25. Ця обробка застосовується переважно для трикоординатної обробки штампів, прес-форм, турбінних лопаток тощо.
3. Електроконтактна обробкаґрунтується на електромеханічному руйнуванні металу під впливом електродугових розрядів інструментом, що переміщується. Зняття металу з заготовки 1 (рис. VI.64, б) здійснюють у повітряному середовищі обертовим диском-електродом 2. Диск і заготовку сполучено із джерелом живлення - знижувальним трансформатором. При обертанні зі швидкістю до 30 м/с диска, до якого заготовка притискується тиском 20...50 кПа, відбувається періодичний розрив контактів, виникають дугові розряди, під дією яких і руйнується метал заготовки. Інтенсивність процесу досить висока і в ряді випадків може перевищувати продуктивність обробки різанням. Проте він не дає високої точності, а шорсткість поверхні не перевищує Rz = 80...20. Тому цю обробку використовують в основному для грубих операцій, наприклад зачищення виливків і штамповок з важкооброблюваних сплавів.
4. Анодно-механічна обробкаґрунтується на одночасній дії електромеханічного і електроіскрового процесів, що відбуваються в середовищі електроліту, яким є водний розчин рідкого скла.
Під час пропускання крізь ванну постійного струму на поверхні заготовки (анода) утворюються плівки продуктів розчинення металу, які механічно видаляються інструментом (катодом). Оскільки вершини шорсткості на оброблюваній поверхні анода відділені від катода невеликою відстанню, через неї проходить короткочасний дуговий розряд. При цьому мікроскопічна ділянка поверхні деталі оплавляється і розплавлені часточки також видаляються катодом, що рухається, тобто відбуваються електроерозійні процеси. Заготовка та інструмент набувають руху подачі. При м'якому режимі, коли густина струму не перевищує 15 А/см2, здійснюють анодно-механічне шліфування і досягають шорсткості Ra = 0,32...0,04.
Цей метод ефективно використовується при відрізанні заготовок з важкооброблюваних високоміцних сплавів. На рис. VI.64, в показано схему анодно-механічного відрізання. Інструмент-катод 2, яким є тонкий диск з м'якої сталі, обертається з великою швидкістю і стикається з деталлю-анодом 1. У зону контакту по трубі 3 подається розчин рідкого скла. Диск і деталь підключають до генератора постійного струму.
55. Електрохімічна обробка
Електрохімічна обробкаґрунтується на явищі анодного розчинення металів, яке полягає в тому, що при проходженні електричного струму крізь електроліт метал анода (заготовки) розчиняється і виноситься електролітом із робочої зони.
Великого поширення набуло електролітичне полірування для ретельної обробки деталей складної форми з високолегованих сталей (лопатки турбін, клапани двигунів, інструменти та ін.). На поверхні деталі-анода
при проходженні струму в електроліті утворюється плівка, що захищає западини мікрошорсткостей від впливу струму. Однак вона не перешкоджає розчиненню мікровиступів, на які діє струм більшої густини, і поверхня деталі згладжується. Звичайно у виробничих умовах досягають Ra = 0,63...0,08, а після попереднього шліфування - Ra = 0,04...0,01.
У практиці використовують також інші методи електрохімічної обробки металів. На рис. VI.65 показано електрохімічне прошивання отворів. До заготовки 7, що є анодом, подається електроліт крізь трубку-катод 2. Сталий зазор між торцем трубки й оброблюваної поверхні утворюється протидією пружини 3 і тиску електроліту. Продукти розчинення виносяться електролітом крізь отвір у ванночці 4.
Різновидом електрохімічної обробки є електроабразивне шліфування, яке виконують електроабразивним кругом. Крім абразивних зерен до його складу входить електропровідний наповнювач. Круг сполучають з негативним полюсом джерела струму, заготовку - з позитивним, а в робочу зону струменем подається електроліт. Плівка, що утворюється внаслідок анодного розчинення, знімається абразивними зернами круга. Порівняно зі звичайним шліфуванням цей процес більш продуктивний при меншому спрацюванні круга, не приводить до появи мікротріщин і забезпечує шорсткість поверхні Ra = 0,2...0,05.
56. Ультразвуковий і променеві методи обробки
1. Ультразвукова обробкадеталей відбувається під дією пружних механічних коливань із частотою близько 20 кГц. При цьому заготовка зазнає ударів завислих у рідині (воді, маслі) зерен абразиву, що набувають великих швидкостей від вібратора, а також внаслідок кавітації. Основни-
Рис. VI.66. Схема ультразвукової обробки
ми елементами ультразвукового верстата є магнітострикційний вібратор 4 (рис. VI.66), на обмотку якого подається струм високої частоти від ультразвукового генератора, і концентратор 3, що підсилює амплітуду коливань до 0,1. ..0,12 мм і передає їх інструменту 2. Інструмент при вертикальному переміщенні з подачею sb прошиває в заготовці 7 отвір відповідної форми.
Ультразвуковою обробкою досягається шорсткість Ra = 0,63...0,16; за її допомогою можна обробляти не тільки метали, а й діелектрики (скло, кварц, силіцій, германій, ферити, рубіни та ін.).
2. Променеві методи обробкиґрунтуються на безпосередній дії пучка електронів або потужного світлового променя на поверхню оброблюваної деталі.
При електронно-променевій обробці електрони, які випромінюються катодною гарматою, прискорюються в потужному електричному полі і фокусуються у вузький пучок, спрямований на оброблювану заготовку. При цьому кінетична енергія електронів перетворюється на теплову. Ефективність дії електронного пучка підвищується фокусуванням його на дуже малих площах (до 10-7 см2). Такий промінь миттєво нагріває поверхню деталі до 6000 °С, внаслідок чого навіть найбільш важкоплавкий метал випаровується. Система керування переміщенням електронного променя забезпечує обробку заготовки потрібного профілю за наперед заданою програмою. Електронно-променевим методом роблять отвори, пази тощо малих розмірів (до 0,005 мм) у важкооброблюваних сплавах.
При лазерній обробці потужний світловий промінь, який випромінюється лазером, фокусується на оброблюваній поверхні заготовки на площі діаметром до 0,01 мм. При цьому концентрація енергії досягає 105 кВт/см2, температура - кількох тисяч градусів, тому відбувається миттєве розплав-лення і випаровування матеріалу. За допомогою лазерів можна вести обробку малих отворів, пазів тощо в різноманітних матеріалах незалежно від їхніх фізико-механічних властивостей (кераміка, алмази, тверді сплави та ін.).
Запитання і завдання для самоконтролю
1. Які ви знаєте основні електрофізичні методи обробки?
2. Дайте характеристику основних методів електроерозійної обробки.
3. Які особливості електрохімічної обробки?
4. Наведіть схему ультразвукової обробки.
Глава 12. ОСНОВНІ НАПРЯМИ АВТОМАТИЗАЦІЇ ВИРОБНИЦТВА В МЕХАНІЧНИХ ЦЕХАХ
57. Загальні відомості
Механізацією називають застосування у виробництві машин, механізмів, пристроїв, які замінюють тяжку фізичну працю і керування якими здійснюють вручну.
Під автоматизацієюрозуміють заміну ручного керування виробничими процесами керуванням за допомогою автоматичних пристроїв, що працюють без участі людини і забезпечують підвищення продуктивності праці. Комплексна автоматизація - це комплекс заходів автоматизації всіх стадій виготовлення виробу.
Автоматизацію металорізальних верстатів залежно від характеру виробництва здійснюють за кількома напрямами.
Масове та великосерійне виробництва зумовили появу універсальних напівавтоматів і автоматів високої продуктивності. Наприклад, багатошпиндельний токарний автомат може замінити до 20 універсальних токарних верстатів. Прагнення максимально підвищити продуктивність при масовому виробництві однотипових деталей привели до появи спеціальних автоматів значно простішої конструкції і більш продуктивних, ніж універсальні.
Технічний прогрес зумовив швидку змінюваність машин і їхніх деталей. Прагнення мати верстати, що мають продуктивність автоматів і технологічні можливості універсальних верстатів, привело до створення агрегатних верстатів.
Поєднання в одній системі верстатів і допоміжних (транспортувальних, завантажувальних) пристроїв, які автоматично здійснюють технологічні операції у певній послідовності, дало можливість створити автоматичні верстатні лінії.
Наступним етапом розвитку автоматизації стало створення автоматичних цехів і заводів. Проте цим шляхом не вирішити проблему автоматизації у дрібносерійному та одиничному виробництві, де найбільш широко застосовують універсальні верстати. Ця проблема може бути вирішена із застосуванням верстатів з програмним керуванням.
Останнім часом все більше поширюються гнучкі виробничі системи (ГВС), які компонуються з верстатів з ЧПК, транспортувальних пристроїв, роботизованих завантажувальних, розвантажувальних, складальних засобів та іншого обладнання, узгоджена робота яких в автоматичному режимі здійснюється від керуючої системи на основі ЕОМ. Це дає можливість швидко переналагодити ГВС на виготовлення різноманітних деталей.
Дата добавления: 2016-02-09; просмотров: 2933;