Материальный баланс процесса разделения
Если в аппарат для разделения гетерогенных систем подается некоторое количество исходной смесив количестве Gсм, кг, содержащей хсм (вес, %) дисперсной фазы, а после разделения образуется концентрированная дисперсная фаза в количестве Gос с концентрацией хос и очищенная дисперсионная среда в количестве Gф с концентрацией оставшейся дисперсной фазы фильтрата хф, материальный баланс такого процесса записывается в соответствии с уравнением (В.5) для входящих и выходящих материальных потоков
для содержащейся в них дисперсной фазы
Совместным решением уравнений (3.1) и (3.2) можно определить два необходимых для расчета технологического процесса параметра.
Разделение в поле сил тяжести (отстаивание)
Кинетика отстаивания. При определении скорости отстаивания частицы дисперсной фазы сделаем следующие допущения: частица имеет сферическую форму; на осаждение не оказывают влияния ни другие частицы, ни стенки аппарата; плотность частицы р,, больше плотности среды ρс, в которой она осаждается. Скорость движения частиц постоянна.
В этом случае на частицу, движущуюся в среде со скоростью w0, действуют следующие силы (рис. 3.1):
· сила тяжести
· подъемная сила (сила Архимеда)
·
|
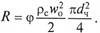
Поскольку движение частицы направлено вниз (ρч > ρс), запишем уравнение баланса сил (уравнение осаждения частицы под действием силы тяжести)
где g – ускорение свободного падения;
φ – коэффициент гидравлического сопротивления.
Отсюда скорость осаждения может быть выражена как
Входящий в уравнение (3.3) коэффициент гидравлического сопротивления определяется в зависимости от режима осаждения частицы (рис. 3.2).
1. При ламинарном режиме осаждения 10-4< Re < 1,0, обтекание носит плавный характер, φ = 24/Re (формула Стокса).
2. При переходном режиме осаждения 1,0 < Re < 500, плавность о6текания нарушается, φ = 18,5/Re0,6 (формула Аллена).
3. При турбулентном режиме осаждения Re > 500, движение становится неупорядоченным, траектории частиц – извилистыми, φ ≈ 0,44 (формула Ньютона).
В турбулентной области наступает автомодельный режим, т. е. режим не зависящий от изменяемого параметра (Re).
Поскольку осаждение в промышленных аппаратах-отстойниках осуществляется при ламинарном режиме, подставив в уравнение (3.3) коэффициент гидравлического сопротивления в виде формулы Стокса, получим
Для практических расчетов скорости осаждения используют также критериальную зависимость, учитывающую фактор формы частиц ψ,
где в качестве диаметра несферической частицы используется ее эквивалентный диаметр, полученный на основании ее веса Gч
Поскольку не всегда возможно предсказать, в каком режиме будет осаждаться частица и какую зависимость для определения скорости ее осаждения следует использовать, считается, что ламинарный режим наблюдается при Аг < 1,8; переходный – при 1,8 < Ar < 8,3*104; турбулентный – при Аг > 8,3*104.
На практике для приближенного определения скорости осаждения во всех режимах обтекания частиц можно воспользоваться зависимостью
Отстаивание является одним из самых дешевых процессов и осуществляется в аппаратах, называемых отстойниками.
Различают отстойники для разделения пылей, суспензий и эмульсий. Эти аппараты могут быть периодического, полунепрерывного и непрерывного действия.
По функциональному назначению отстойники для разделения суспензий делят на сгустители, осветлители и классификаторы.
Основной характеристикой отстойного оборудования является его производительность Vот, определяемая как
Vот = Fw0
где F – площадь поверхности осаждения.
Для отстойников с несколькими поверхностями осаждения (многополочные отстойники), каждая из которых имеет площадь fпоз,
F=nfпов,
где n – число поверхностей осаждения.
Для увеличения скорости осаждения мелкодисперсных частиц используют специальные растворы – коагулянты, способствующие объединению частиц между собой, что увеличивает массу осаждаемого агломерата.
|
Для автоматизации разгрузки полки могут устанавливаться с наклоном, а на слой осадка может оказываться вибрационное воздействие и т. п. Аппараты аналогичных конструкций могут применяться для разделения суспензий (полочные отстойники).
Одновременное воздействие сил тяжести и инерции на разделяемую пыль осуществляется
в отстойном газоходе (рис. 3.4), сна6женном вертикальными перегородками 1, о которые ударяются, не успевающие обогнуть их содержащиеся в газе твердые частицы. За счет этого они теряют скорость и под действием силы тяжести опускаются вдоль поверхности перегородок в сборники 2, откуда отводятся периодически или непрерывно.
На рис. 3.5 представлен отстойник для разделения суспензий непрерывного действия с гребковой мешалкой. Отстойник состоит из цилиндрического корпуса 1 с коническим днищем, кольцевым желобом 2 и патрубком 5 для отвода очищенной жидкости, мешалки 7 с гребками 6 для перемещения постоянно образующегося осадка к разгрузочному устройству 8. Подача суспензии осуществляется через центральный патру6ок 3. Вращение мешалки с низкими скоростями, не разрушающими осадок, осуществляется с помощью электродвигателя 4.
Разделение суспензий в поле сил давления (фильтрование)
Фильтрование – процесс разделения суспензий и пылей с помощью пористых перегородок, задерживающих дисперсную – твердую фазу и пропускающих дисперсионную среду (жидкость или газ). При этом фильтрование может осуществляться как с образованием осадка, так и с за6ивкой пор (отложение осадка внутри перегородки). В дальнейшем будем рассматривать чаще встречаемое в практике фильтрование с образованием осадка.
В этом случае скорость процесса фильтрования прямо пропорциональна разности давлений, создаваемых по обеим сторонам фильтровальной перегородки (движущая сила), и обратно пропорциональна сопротивлению, испытываемому средой при ее движении через поры перегородки и слой образовавшегося осадка:
где Vф – объем фильтрата; Fф - площадь фильтрования; τ - время проведения процесса; Rф.п, Rос - сопротивление фильтровальной перегородки и слоя осадка; µс - динамическая вязкость среды (фильтрата).
Сопротивление осадка является величиной переменной, так как фильтрование происходит с непрерывным увеличением толщины слоя осадка и, следовательно, ростом его сопротивления:
Здесь rос – удельное сопротивление осадка; lос – толщина осадка; хос – отношение объема осадка к объему фильтрата.
В зависимости от изменения удельного сопротивления осадка при увеличении давления различают несжимаемые (rос = const) и сжимаемые (rоc ≠ const) осадки.
Движущая сила в процессе фильтрования суспензий может создаваться: гидравлическим давлением столба жидкости над перегородкой; использованием насосов для подачи суспензии в фильтр; энергией сжатого газа над суспензией или созданием вакуума под фильтрующей перегородкой.
При этом процессы фильтрования могут осуществляться при постоянной разности давлений (Δр = const), при постоянной скорости (jф = const) и при переменных значениях Δр и jФ.
Для несжимаемых осадков с учетом зависимости (3.5) уравнение (3.4) может быть записано в виде
Для случая Δр = const результат интегрирования уравнения (3.6) в пределах 0 – VФ и 0 – τ после разделения переменных запишется в виде
где С и К – постоянные фильтрования, определяемые для конкретных систем экспериментальна.
Из уравнения (3.7) время на получение объема фильтрата VФ через поверхность фильтрования Fф при перепаде давлений Δр составит
В случае jф = const в уравнении (3.6) можно заменить на тождественное значение
и, преобразовав к виду, аналогичному (3.7), получим
или
где С' и К' – постоянные фильтрования, определяемые экспериментально.
Аналогично (3.8) получим
Сравнительный анализ уравнений (3.8) и (3.9) показывает, что процессы фильтрования с постоянным перепадом давлений при одинаковых VФ и FФ осуществляются быстрее, чем при jФ = const.
Аппараты для осуществления процессов фильтрования называются фильтрами.
По способу организации процесса фильтры подразделяются на периодически действующие и непрерывнодействующие.
|
К наиболее распространенным конструкциям для разделения пылей относится рукавный фильтр (рис. 3.б), содержащий фильтрующие элементы 1 в виде матерчатых рукавов, подвешенных к раме 2. Запыленный газ подается через патрубок 7 внутрь рукавов, в которых накапливается пыль. Расход удаляемого газа регулируется заслонкой 3. Регенерация рукавов осуществляется встряхивающим механизмом 5, а также обратным током чистого газа, подаваемого через заслонку 4 при закрытой заслонке 3. Отделенная пыль ссыпается в конический бункер и выгружается через патрубок 6.
Рукавные фильтры обеспечивают высокую степень разделения, однако име‑
ют значительное гидравлическое сопротивление, а фильтрующая ткань чувствительна к высокой температуре и наличию паров химически агрессивных веществ.
К непрерывнодействующим фильтрам с постоянным перепадом давлений для разделения суспензий относится барабанный вакуум-фильтр (рис. 3.7), состоящий из вращающегося полого барабана 5 с перфорированной боковой поверхностью, разделенной внутренними перегородками 1 на отдельные ячейки 2 и покрытого снаружи фильтровальной тканью. Его вал имеет полую цапфу, торец которой пришлифован к распределительному устройству (головке) 8. Поверхность барабана частично погружена в суспензию, находящуюся в корыте 7, уровень которой поддерживается постоянным с помощью сливного порога 9. Образуемый на поверхности барабана слой осадка снимается ножом 4. При помощи трубок каждая ячейка барабана сообщается с распределительным устройством, служащим для последовательного соединения их с источником вакуума и сжатого воздуха. Под барабаном расположена медленно качающаяся маятниковая мешалка 6, предотвращающая осаждение суспензии на дно корыта.
В зоне фильтрования I, когда поверхность фильтра погружена в корыто, каждая ячейка последовательно соединяется со сборником фильтрата, находящимся под разрежением. Затем в зоне первого обезвоживания II осадок выходит из суспензии, и филь‑
трат, отжимаемый из осадка вследствие вакуума в ячейках, собирается в том же сборнике фильтрата. После этого осадок попадает в зону промывки III, где на него из разбрызгивающих устройств подается промывная жидкость, которая с остатками фильтрата собирается в сборнике, находящемся под разрежением. В зоне второго обезвоживания IV из осадка отжимается остаток промывной жидкости. В некоторых случаях для предотвращения растрескивания, лучшей промывки и отжима на осадок накладывается непрерывная тканевая лента 3. В зоне удаления осадка V ячейка сообщается с ресивером сжатого воздуха, а в зоне регенерации 1/1 ткань продувается сжатым воздухом или промывается обратным током жидкости.
Ленточные вакуум-фильтры (рис. 3.8) непрерывного действия и постоянного перепада давлений предназначены для фильтрования агрессивных и неагрессивных быстро осаждающихся суспензий с различными размерами частиц твердой фазы.
Традиционный ленточный вакуум-фильтр состоит из бесконечной резинотканевой ленты 4, натянутой на два вращающихся барабана 1 и 6. В верхней части между барабанами лента скользит по горизонтальным направляющим (столу) 3 с прорезями, соединяющими область фильтровальной перегородки с вакуум-камерами.
Суспензия поступает на фильтр из лотка 5. Осадок либо удаляется c ленты ножом, либо сползает в бункер 7 при огибании лентой приводного барабана 1. Жидкость для промывания подается из специальных устройств 2, которые могут быть закреплены в любом месте по длине фильтра. Регенерация ткани осуществляется при ее движении в нижнем положении.
К преимуществам ленточных фильтров относятся возможности реализации оптимальных технологических режимов фильтрования и промывки осадка, регулирования толщины слоя осадка и скорости движения фильтровальной ленты, а также простота обслуживания.
Вертикальный рамный фильтр-пресс (рис. 3.9) периодического действия применяют для разделения труднофильтрующихся суспензий. Работают они, как правило, при постоянной скорости, дешевы, компактны, обладают большой поверхностью фильтрования, приходящейся на единицу объема, хорошо приспособлены к изменяющимся свойствам суспензии.
Рамный фильтр-пресс (рис. 3.9, а) состоит из заключенного между упорными плитами 1 и 5 набора вертикально расположенных чередующихся рам 2 и плит 3 (рис. 3.9, б), опирающихся боковыми ручками на горизонтальные направляющие 6. Между ними расположена фильтровальная ткань 4.
Герметизация фильтра-пресса осуществляется зажимным винтом 7. При сборе, отверстия, выполненные в рамах и плитах, образуют каналы: 8 – для подачи суспензии, соединенные с рамами 2, и 9 – для подвода жидкости для промывки, соединенные с плитами 3. Кроме того, в плитах выполнены каналы 10 для отвода фильтрата и жидкости для промывки.
Цикл работы фильтра-пресса состоит из следующих операций: сборка; заполнение камер осадком (фильтрование); промывка осадка; отжим осадка (отдувка); разборка и разгрузка фильтра.
Механизированный камерный фильтр-пресс (рис. 3.10) периодического действия предназначен для фильтрования труднофилътруемых суспензий с высокоэффективной промывкой. Он состоит из набора горизонтальных плит 6, верхняя 1 из которых закреплена неподвижно, а остальные, включая нажимную 2, могут перемещаться вверх и вниз по специальным направляющим с помощью механизма зажима 3. Фильтровальная ткань 7 непрерывной лентой проходит между плитами 6, огибая ролики 8.
Цикл работы камерного фильтра-пресса аналогичен рамному фильтру-прессу, однако сборка, разборка и разгрузка осадка выполняются специальными механическими устройствами. В процессе движения загрязненная ткань очищается специальными ножами или щетками и промывается в специальных устройствах камеры регенерации 4. Осадок при движении ткани перегибается вместе с нею через ролики и под действием собственного веса или ножей, прижатых к ткани пружинами, удаляется с ткани и падает либо в бункер 5, либо на транспортер (на схеме не показан).
|
Дата добавления: 2015-08-14; просмотров: 4885;