ТВЕРДЫЕ СПЛАВЫ
14.1. Классификация твердых сплавов и общая характеристика
их свойств
Применение методов порошковой металлургии в начале 1920-х годов в Германии привело к созданию новых материалов, обладающих уникальным сочетанием свойств, – твердых сплавов. Внимание исследователей привлекли соединения некоторых металлов с углеродом: карбиды вольфрама, титана, тантала, ниобия, обладающие высокими твердостью и температурой плавления (табл. 14.1).
Таблица 14.1
Температуры плавления и твердости карбидов
Карбиды | Температура плавления, °С | Твердость HV, ГПа |
WC | ||
TiC | ||
TaC | ||
NbC |
Карбид вольфрама WC имеет гексагональную решетку и по свойствам значительно ближе к металлам, чем к керамике: обладает хорошей электро- и теплопроводностью, имеет металлический вид. Другие карбиды, представленные в таблице 14.1, имеют кубическую кристаллическую решетку.
Карбид вольфрама смешивался с тонко размельченным порошком металла из подгруппы железа (железом, никелем или кобальтом). Смесь порошков спрессовывалась в компактную массу, которая спекалась в водороде при температуре 1300 °С. В результате был получен материал, состоящий из высокодисперсных зерен WC, связанных или «сцементированных» более вязким металлом. Позже было установлено, что наиболее эффективным металлом для связки является кобальт. Полученные материалы обладают уникальным сочетанием свойств, что и привело к выделению их во вторую основную группу инструментальных материалов – группу твердых сплавов.
Современные порошковые (спеченные) твердые сплавы – это композиции, состоящие из твердых, тугоплавких соединений (карбиды и карбонитриды титана, вольфрама, тантала и др.) в сочетании с цементирующей (связующей) составляющей (кобальт, никель, молибден и др.). Твердые сплавы, применяемые для оснащения режущего инструмента, по составу и областям применения можно разделить на четыре группы: вольфрамокобальтовые ВК (WC–Со), титановольфрамовые ТК (WC–TiC–Co), титанотанталовольфрамовые ТТК (WC–TiC–TaC–Co), безвольфрамовые БВТС (на основе TiС, TiCN с различными связками).
Общее количество твердосплавного инструмента, применяемого в механообрабатывающем производстве, составляет до 28–30 %, но этим инструментом снимается до 65 % стружки, т. к. производительность обработки твердосплавными инструментами в три – пять раз выше, чем быстрорежущими.
|
|
|
|
|
|
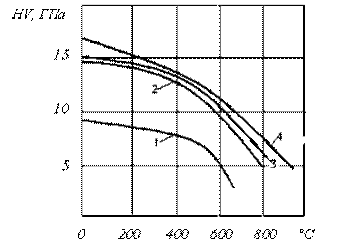
Рис. 14.1. Влияние температуры на твердость твердых сплавов и быстрорежущей стали: 1 – быстрорежущая сталь; 2 – WC+9 % Co; 3 – WC+6 % Co; 4 – WC–TiC–TaC–Co
Твердые сплавы имеют высокую твердость при комнатной температуре. При повышении температуры твердость твердых сплавов снижается, но остается все же значительно выше, чем у быстрорежущей стали (рис. 14.1). Твердые сплавы характеризуются высокими значениями модуля упругости (E = 500–700 ГПа) и предела прочности при сжатии (s–В = 6 ГПа). Вместе с тем они имеют относительно невысокую прочность при изгибе (sИ = 1–2,5 ГПа)
и меньшую, чем у быстрорежущих сталей, ударную вязкость.
Указанные физико-механические свойства обеспечивают твердосплавному инструменту высокий предел пластической прочности, повышенную сопротивляемость адгезионно-усталостному, химико-окислительному, диффузионному и абразивному изнашиванию. Такие свойства позволили существенно повысить производительность обработки сталей, чугунов, цветных сплавов и труднообрабатываемых материалов по сравнению с обработкой быстрорежущим инструментом.
Для оснащения режущего инструмента применяются вольфрамокобальтовые твердые сплавы с содержанием кобальта от 3 до 10 % (ВК3, ВК6, ВК6–М, ВК8, ВК10–ХОМ и др.).
Вольфрамокобальтовые сплавы наиболее эффективны преимущественно при обработке чугунов, цветных металлов, стеклопластиков, фарфора, труднообрабатываемых материалов (коррозионностойких, высокопрочных сталей, жаропрочных сплавов на основе никеля и титана и т. д.), т. е. материалов, дающих, как правило, дискретные типы стружек (элементная, стружка надлома).
Сплав ВКЗ с минимальным содержанием кобальта, как наиболее износостойкий, но наименее прочный, рекомендуют для чистовой обработки с повышенной скоростью резания и уменьшенной толщиной срезаемого слоя, а сплав ВК8 – для черновой обработки с пониженной скоростью резания и увеличенным сечением среза в условиях ударных нагрузок.
При одинаковом содержании кобальта физико-механические и режущие свойства в значительной мере определяются зернистостью карбидной фазы, главным образом, средним размером зерен карбида вольфрама. Разработанные технологические приемы позволяют получить твердые сплавы, в которых средний размер зерен карбидной составляющей может изменяться от долей микрона до 10–15 мкм. Особомелкозернистый сплав ВК10–ХОМ с успехом применяется при чистовой обработке жаропрочных никелевых сплавов, поскольку в этом случае инструмент должен хорошо противостоять пластическим деформациям при высоких напряжениях и температурах.
Еще одно направление совершенствования сплавов для резания конструкционных сталей, чугунов и труднообрабатываемых материалов связано с совершенствованием связки. Примером такого совершенствования сплава является разработка сплава ВРК15 с жаропрочной кобальторениевой связующей фазой для черновой и получистовой обработки. Сплав отличается высокой прочностью при повышенных температурах, низкой адгезией с обрабатываемым материалом и относительно высокой износостойкостью. Применение инструментов, оснащенных сплавом ВРК15, позволяет повысить производительность обработки резанием примерно в полтора раза даже в сравнении со сплавом ВК10–ХОМ.
Режущие инструменты из вольфрамовых твердых сплавов, показавшие высокую эффективность при обработке чугуна и цветных металлов, оказались недостаточно износостойкими и эффективными при обработке сталей. Эту проблему удалось решить путем добавки при спекании твердого сплава карбидов титана (TiC) и тантала (TaC). Наиболее перспективным оказался карбид титана, поскольку TiC намного дешевле, чем TaC: титан имеется в достаточном количестве, а тантал является редким металлом.
Титановольфрамовые сплавы (ТК) по сравнению со сплавами ВК обладают большей стойкостью против окисления, твердостью и теплостойкостью, но в то же время имеют меньшую теплопроводность и электропроводность, а также меньший модуль упругости.
Сплавы группы ТК стандартных марок имеют различный состав в зависимости от условий из применения. Содержание карбида титана колеблется в пределах 5–30 %, кобальта от 4 до 10 % (ТЗОК4, Т15К6, Т14К8, Т5К10).
Микроскопические исследования показали, что в структуре титановольфрамокобальтовых твердых сплавов, содержащих до 25 % TiC, присутствуют две карбидные фазы: угловатые голубовато-серые зерна карбидов WC, имеющих гексагональную решетку, и круглые зерна желто-корич-невых кубических карбидов. При этом относительное количество кубических карбидов TiC много больше, чем следовало ожидать в соответствии с их небольшим процентным содержанием по весу. Это объясняется тем, что карбиды WC могут находиться в твердом растворе в TiC в большом количестве (вплоть до 70 % по весу). Карбиды TiC и TaC имеют одинаковую кубическую структуру и полностью растворяются один в другом, но не полностью растворяются в WC. Поэтому видимые в структуре твердых сплавов округлые зерна представляют собой зерна карбидов с кубической кристаллической структурой, в которой имеются атомы металлов Ti, Ta и W и один атом углерода на каждый атом металла. Установлено, что кубические зерна «смешанных кристаллов» изнашиваются медленнее, чем зерна WC.
Так же, как и у сплавов WC–Co, предел прочности при изгибе и сжатии, а также ударная вязкость у сплавов ТК увеличивается с ростом содержания кобальта. У сплавов с одинаковым содержанием кобальта и одинаковым размером карбидных фаз предел прочности при изгибе и сжатии, ударная вязкость, пластическая деформация и модуль упругости уменьшаются при увеличении содержания карбида титана.
В соответствии с этим меняются и режущие свойства сплавов: увеличение содержания кобальта приводит к снижению износостойкости сплавов при резании, а с ростом содержания карбида титана (при постоянном объемном содержании кобальта) повышается износостойкость, но одновременно снижается эксплуатационная прочность. Поэтому такие марки сплавов, как ТЗОК4 и Т15К6, обладающие максимальным запасом пластической прочности, применяют в условиях чистовой и получистовой обработки стали с высокой скоростью резания, малыми и умеренными нагрузками на инструмент. Сплавы Т5К10, Т5К12 с наибольшим содержанием кобальта и запасом хрупкой прочности предназначены для работы в тяжелых условиях ударных нагрузок с пониженной скоростью резания.
Введение в сплавы карбида тантала улучшает их физико–механические и эксплуатационные свойства, что выражается в увеличении прочности при изгибе и твердости при комнатной и повышенной температурах, увеличении работы деформации при повышенных температурах. Карбид тантала в сплавах снижает ползучесть, существенно повышает предел усталости трехфазных сплавов при циклическом нагружении, а также повышает термостойкость и стойкость против окисления на воздухе.
Отечественный стандарт (ГОСТ 3882-74) включает пять марок сплавов этой группы – ТТ8К6, ТТ10К8Б, ТТ7К12, ТТ20К9 и Т8К7, в которых содержание карбида тантала колеблется от 2 до 12 %.
Исследование режущих свойств сплавов ТТК показало, что увеличение в сплаве содержания карбида тантала повышает его износостойкость при резании. С учетом отмеченных свойств, сплавы ТТК рекомендуют для тяжелой обработки, резания труднообрабатываемых материалов при значительном термомеханическом нагружении инструмента, а также операций прерывистого резания, особенно фрезерования, отличающихся переменным сечением среза и циклическими термомеханическими нагрузками на режущую часть инструмента.
К группе танталосодержащих сплавов следует отнести и так называемые сплавы МС, выпуск которых освоен по лицензии, закупленной у фирмы "Sandvik Coromant" (Швеция).
Исследования режущих свойств сплавов МС показали их высокую надежность по сравнению со стандартными сплавами, что связано с повышенной стабильностью их физико-механических характеристик. Поэтому более высокая (на 40–60 %) стоимость сплавов МС по сравнению со стандартными сплавами вполне оправдана высокой стабильностью режущих свойств и эксплуатационной надежностью инструмента, оснащенного пластинами МС.
В связи с высокой дефицитностью основных компонентных составляющих твердого сплава и, прежде всего, W и Со, в развитых странах мира и СНГ развернуты широкие изыскания по разработке экономно-легированных твердых сплавов, обычно не содержащих или содержащих в небольших количествах вольфрам; такие твердые сплавы получили наименование безвольфрамовых. Перспективным направлением оказалось создание сплавов на основе карбидов или карбидонитридов титана с никельмолибденовой связкой (например, ТН20, КНТ16). Сплав ТН20 содержит 15 % Ni и 6 % Mo, остальное – TiC, а КНТ16 – 19,5 % Ni и 6,5 % Mo, остальное – TiCN.
Сплавы отличаются высокой твердостью, окалиностойкостью, имеют низкий коэффициент трения по стали и пониженную склонность к адгезионному взаимодействию, что уменьшает износ инструмента, особенно по передней поверхности, позволяет получить при обработке сталей низкую шероховатость обработанной поверхности и высокую размерную точность. Вместе с тем, безвольфрамовые твердые сплавы по сравнению со стандартными вольфрамосодержащими сплавами имеют более низкий модуль упругости, меньшую теплопроводность и ударную вязкость, поэтому хуже сопротивляются ударным и тепловым нагрузкам, упругим и пластическим деформациям, имеют пониженную жаропрочность, более интенсивно разупрочняются при повышенных температурах.
Указанные свойства определяют и области рационального применения безвольфрамовых твердых сплавов при обработке материалов резанием.
В настоящее время их рекомендуется использовать, главным образом, для чистовой и получистовой обработки (точение, фрезерование) углеродистых и легированных сталей с высокой скоростью резания и относительно небольшим сечением среза взамен титановольфрамовых сплавов.
Эффективно применение безвольфрамовых твердых сплавов в виде сменных многогранных пластин, так как при напайке и заточке из-за низкой теплопроводности возможно появление внутренних напряжений и, как следствие, трещин на пластинах, а также снижение их эксплуатационной стойкости.
Дата добавления: 2015-04-25; просмотров: 1404;