Алюминий и его сплавы
Алюминий – металл серебристо-белого цвета, имеет кристаллическую ГЦК решетку, температуру плавления 660 °С, удельный вес 2,7 г/см3, обладает высокой электропроводностью и теплопроводностью, коррозионной стойкостью за счет образования на поверхности защитной оксидной плёнки, малой прочностью (σВ = 60–80 МПа) и твёрдостью (250 НВ), но пластичен (δ = 35–50%). При пластической деформации значительно наклёпывается (σВ = 150–180 МПа, δ = 1,5%, 450 НВ).
Технический алюминий выпускается в виде деформируемого полуфабриката (листы, профили, прутки и др.).
Механические свойства алюминия зависят от его чистоты и состояния. Увеличение содержания примесей и пластическая деформация повышают прочность и твёрдость алюминия (табл. 16.1). Ввиду низкой прочности применяют для ненагруженных деталей и элементов конструкций, когда от материала требуется лёгкость, свариваемость, пластичность. Изготавливают рамы, трубопроводы, фольгу, цистерны для перевозки нефти и нефтепродуктов, посуду и др.
Свойство высокой теплопроводности используют для изготовления теплообменников в промышленных и бытовых холодильных установках. Свойство высокой электрической проводимости используют при изготовлении конденсаторов, проводов, кабелей, шин и т. п.
Таблица 16.1
Механические свойства алюминия
Марка
| Сумма примесей, %
| Состояние
| σВ,
МПа
| σ0,2,
МПа
| δ, %
| HB, МПа
|
A995
| 0,005
| Литье
|
| –
|
|
|
A5
| 0,5
|
| –
|
|
|
A0
|
|
| –
|
|
|
Деформированное и отожженное
|
|
|
|
|
Деформированное
|
|
|
|
|
Алюминий имеет высокую отражательную способность. Это позволяет использовать его в прожекторах, рефлекторах, экранах телевизоров.
Алюминий обладает высокой коррозионной стойкостью к морской воде, органическим кислотам, устойчив в нейтральных растворах солей магния, натрия. Химическая стойкость алюминия различной чистоты обуславливается образованием на его поверхности тончайшей, но плотной беспористой плёнки окиси алюминия Al2O3.
В машиностроении чистый алюминий практически не используется. Основное применение алюминия – это производство сплавов, достоинство которых в малом удельном весе.

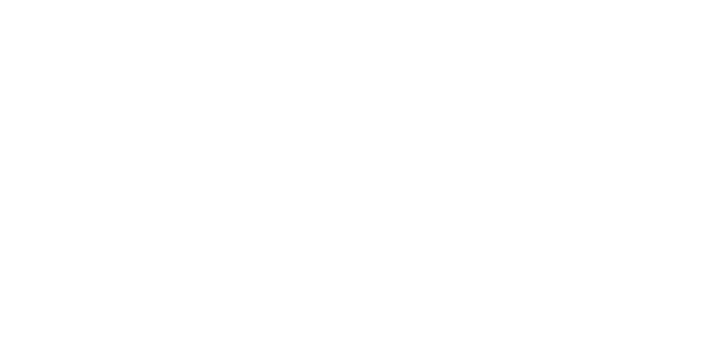
Рис. 16.1. Классификация алюминиевых сплавов
Алюминиевые сплавы классифицируют по технологии изготовления, способности к упрочнению термической обработкой и свойствам
(рис. 16.1). Технические алюминиевые сплавы подразделяют на две группы: применяемые в деформированном виде (прессованном, катаном, кованном) и в литом (деформированные и литейные сплавы). Границу между сплавами этих групп определяет предел насыщения твёрдого раствора при эвтектической температуре (рис. 16.2). Деформируемые и литейные алюминиевые сплавы подразделяются на не упрочняемые и упрочняемые в результате термической обработки.
Основными легирующими элементами алюминиевых сплавов являются медь, магний, кремний, марганец, цинк, реже литий, никель, титан. Легирующие элементы повышают температуру рекристаллизации алюминия (рис. 16.3). Многие легирующие элементы образуют с алюминием твёрдые растворы ограниченной переменной растворимости и промежуточные фазы СuАl2, Mg2Si и др. Это даёт возможность подвергать сплавы упрочняющей термической обработке, состоящей из закалки на пересыщенный твёрдый раствор и естественного или искусственного старения.
Рис. 16.2. Диаграмма состояния «Алюминий – легирующий элемент»
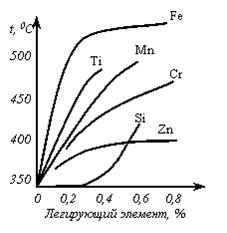
Рис. 16.3. Влияние легирующих элементов на температуру рекристаллизации алюминия
К деформируемым сплавам, не упрочняемым термической обработкой, относятся сплавы АМц и АМг.
Сплавы типа АМц (АМц1) относятся к системе «Аl – Мn»; структура состоит из α-твёрдого раствора и вторичных выделений фазы МnАl6, переходящих в твёрдый раствор при повышении температуры. При легировании железом вместо МnАl6 образуется сложная тройная фаза (Мn, Fе)Аl6, которая не растворяется в алюминии, поэтому эти сплавы не упрочняются термической обработкой. В отожженном состоянии обладают высокой пластичностью (δ = 18–22 %) и низкой прочностью (σВ = 130 МПа).
Сплавы типа АМг (АМг1, АМг5) относятся к системе «Аl – Мg». Магний образует с алюминием α-твёрдый раствор, концентрация которого при повышении температуры увеличивается от 1,4 до 17,4 % в результате растворения фазы Мg2Аl3. Сплав АМг в отожженном состоянии имеет
σВ = 190 МПа, δ = 23 %
Сплавы типа АМц и АМг упрочняют с помощью пластической деформации и используют в нагартованном (80 % наклёпа) и полунагартованном (40 % наклёпа) состояниях. Применение наклёпа ограниченно из-за резкого снижения пластичности, поэтому в большинстве случаев их используют в отожженном состоянии. Температура отжига: 350–420 °С.
Сплавы типа АМц и АМг применяют для изделий, получаемых глубокой вытяжкой или сваркой, от которых требуется высокая коррозионная стойкость (трубопроводы для бензина и масла, сварные баки и т. п.).
К деформируемым сплавам, упрочняемым термической обработкой, относятся сплавы системы «Аl – Сu». Они характеризуются хорошим сочетанием прочности и пластичности. Наиболее характерными представителями этих сплавов являются дуралюмины, широко применяемые в авиа-, судо- и ракетостроении. Согласно диаграмме «Аl – Сu» (рис. 16.4), медь с алюминием образуют твёрдый раствор, максимальная концентрация меди в котором 5,65 % при эвтектической температуре. С понижением температуры растворимость меди уменьшается, достигая 0,1 % при 20 °С. Из твёрдого раствора выделяется θ-фаза – СuАl2, содержащая 54,1 % Сu. Она имеет объёмноцентрированную тетрагональную кристаллическую решетку и обладает сравнительно высокой твёрдостью. В сплавах дополнительно легированных магнием образуется ещё ς-фаза (Аl2СuМg) с ромбической кристаллической решеткой.
Рис. 16.4. Диаграмма состояния «Al – Cu»
Маркируются дуралюмины буквой «Д» и цифрой, означающей номер сплава, например: Д1, Д16, Д20 и т. д. Поставляются в виде сортового проката в отожженном и термически упрочненном состоянии. Упрочняющая термическая обработка состоит из закалки и естественного старения. При закалке дуралюмины охлаждают в воде при 40 °С. После закалки структура состоит из пересыщенного раствора и нерастворимых фаз, образуемых примесями. При естественном старении образуются зоны Гинье-Престона, богатые медью и магнием.
Зоны Гинье-Престона – это скопление атомов меди, неразрывно связанных с α-твёрдым раствором. Они значительно тормозят перемещение дислокаций, что и является причиной возрастания прочности при старении. Старение продолжается пять – семь суток. Длительность старения значительно сокращается при увеличении температуры до 40 °С и особенно
до 100 °С. После закалки и искусственного старения сплавы обладают лучшей пластичностью и менее чувствительны к концентраторам напряжений. Искусственному старению (при 190 °С, в течение 10 часов) подвергаются детали, используемые для работы при повышенных температурах
(до 200 °С).
Кроме дуралюминов, к термически упрочняемым деформируемым сплавам относятся следующие алюминиевые сплавы: ковочные (АК4-1, АК6, АК8 и т. д.), маркируемые буквами АК, и высокопрочные (В95, В96 и т. д.), маркируемые буквой В.
По химическому составу ковочные сплавы близки к дуралюминам, отличаясь от них более высоким содержанием кремния. Детали из ковочных сплавов подвергают закалке от 500–575 °С и старению при 150–165 °С в течение 6–15 часов. Дополнительное легирование Ni, Fe, Ti повышает температуру рекристаллизации и жаропрочность этих сплавов до 300 °С, что позволяет использовать их при изготовлении поршней, лопаток, дисков осевых компрессоров турбореактивных двигателей и т. п.
Высокопрочные алюминиевые сплавы принадлежат к системе
«Аl – Ζn – Мg – Сu» и содержат добавки марганца, хрома, циркония. Эти элементы увеличивают неустойчивость твердого расплава, ускоряют
его распад и усиливают старение сплава. Наибольшее упрочнение вызывают закалка с температур 465–475 °С и старение при 140 °С, в течение
16 часов. После такой обработки сплав В95 имеет σВ = 569–600 МПа,
δ = 9–12 %, 1500 НВ. Сплавы применяют для высоконагруженных деталей и конструкций, работающих в условиях напряжения сжатия.
Рис. 16.5. Диаграмма состояния системы «Al – Si»
Основные требования к литейным алюминиевым сплавам – сочетание хороших литейных свойств (высокой жидкотекучести, небольшой усадки, малой склонности к образованию горячих трещин и пористости) с оптимальными механическими и химическими (сопротивление коррозии) свойствами. К литейным относятся сплавы эвтектического состава на основе систем «Al – Si», «Al – Cu», «Al – Mg».
Лучшими литейными свойствами обладают эвтектические сплавы на основе «Al – Si» (силумины) (рис. 16.5), например: АЛ2, АЛ4, АЛ9. Наиболее распространён сплав, содержащий 10–13 % Si (АЛ2), обладающий высокой коррозионной стойкостью, большой плотностью отливок. В структуре содержит эвтектику, состоящую из α-твёрдого раствора кремния в алюминии и кристаллов практически чистого кремния. Кремний при затвердевании эвтектики выделяется в виде грубых кристаллов игольчатой формы, которые играют роль внутренних надрезов в пластичном α-твёрдом растворе. Такая структура обладает низкими механическими свойствами.
Силумины обычно модифицируют натрием, который в виде хлористых и фтористых солей вводят в жидкий сплав в количестве 2–3 % от массы сплава. В этом случае в структуре сплава вместо избыточного кремния появляются кристаллы α-твёрдого раствора. Это приводит к увеличению пластичности и прочности (рис 16.6).
Рис. 16.6. Зависимость механических свойств для модифицированного (штриховые
линии) и немодифицированного (сплошные линии) силумина от содержания кремния
Для легирования силуминов используют магний, медь, марганец, титан. Растворяясь в алюминии, они повышают прочность, твёрдость. Медь улучшает обрабатываемость резанием, титан оказывает модифицирующее действие. Медь и магний, обладая переменной растворимостью в алюминии, способствует упрочнению силуминов при термической обработке, состоящей из закалки и искусственного старения. Температура закалки различных силуминов находится в пределах 515–535 °С, температура старения – 150–180 °С.
Из легированных силуминов наибольшее применение имеют сплавы с добавками магния АК7ч, (ч – содержание примесей 0,1–0,3 %), магния и марганца (АК9ч). Наибольшее упрочнение вызывает метастабильная
β’-фаза (Mg2Si). Легированные силумины применяют для средних и крупных литых деталей ответственного назначения: корпусов компрессора, картеров, головок цилиндров.
Сплавы системы «Al – Cu» характеризуются высокой прочностью при обычных и повышенных температурах, хорошо обрабатываются резанием и свариваются, но (из-за отсутствия эвтектики) обладают плохими литейными свойствами. Сплавы склонны к хрупкому разрушению вследствие выделения по границам зерен грубых частиц θ-фазы: CuAl2 и Al7Cu2Fe, поэтому их применяют в закалённом состоянии, когда эти соединения переведены в твёрдый раствор. Во время нагрева сплава под закалку наряду с растворением θ-фазы из твёрдого раствора выпадают мелкодисперсные частицы фазы Al12Mn2Cu, увеличивающие прочность при обычных и повышенных температурах. После закалки: σВ = 320 МПа, σ0,2 = 180 МПа, 800 НВ.
Сплавы системы «Al – Cu» используют для деталей, работающих при температурах до 300 °С. Так как эти сплавы малоустойчивы против коррозии, то отливки подвергают анодированию, химическому оксидированию и окраске.
Сплавы системы «Al – Mg» обладают высокой коррозионной стойкостью во многих агрессивных средах, обрабатываются резанием и свариваются. Дополнительное легирование бериллием, титаном и цирконием вызывает измельчение зерна и затормаживание процесса естественного старения, приводящего к снижению пластичности и коррозионной стойкости. Термообработка состоит из закалки с охлаждением в масле (40–50 °С). Выдержка при температуре закалки составляет 12–20 часов, что обеспечивает растворение частиц Al3Mg2 в α-твёрдом растворе и получение однородного раствора. Добавление до 1,5 % Ѕi улучшает литейные свойства.
Сплавы системы «Al – Mg» применяют для изготовления деталей, работающих в условиях высокой влажности, в судо-, самолето- и ракетостроении.
Дата добавления: 2015-04-25; просмотров: 2015;