Лабораторная работа № 15. Химико-термическая обработка стали
Цель работы: ознакомление с основными положениями теории химико-термической обработки; изучение технологических процессов важнейших видов химико-термической обработки и структуры слоев стали после ХТО.
Химико-термической обработкой (ХТО) называют технологические процессы, приводящие к диффузионному насыщению поверхностного слоя деталей различными элементами. ХТО применяют для повышения твердости, износостойкости, сопротивления усталости и контактной выносливости, а также для защиты от электрохимической и газовой коррозии. При данном виде обработки деталь помещают в среду, богатую насыщающим элементом. При ХТО происходят три элементарных процесса: диссоциация, абсорбция и диффузия. Диссоциация протекает в газовой среде и состоит в распаде молекул и образовании активных атомов диффундирующего элемента. Степень распада молекул газа называется степенью диссоциации. Абсорбция происходит на границе «газ–металл» и заключается в поглощении поверхностью металла насыщающего элемента. Под диффузией понимают проникновение элемента вглубь насыщаемого металла. В результате ХТО образуется диффузионный слой.
Наибольшая концентрация насыщаемого элемента наблюдается на поверхности изделия, по мере удаления от поверхности она снижается. Фазовые и структурные изменения, происходящие при ХТО в диффузионном слое, и его строение определяются изотермическим разрезом диаграммы состояния «обрабатываемый металл – насыщающий элемент» при температуре диффузионного насыщения.
Предположим, что системе «обрабатываемый металл А – насыщающий элемент В» соответствует диаграмма состояния, представленная на рисунке 15.1, а насыщение происходит при температуре t1. Если процессы диссоциации, абсорбции и диффузии протекают активно и времени насыщения достаточно, то на поверхности образуется слой твердого раствора А и В переменной концентрации. Под ним будет находиться слой твердого раствора А и В в химическом соединении АnВm переменной концентрации и далее твердый раствор В и А, убывающий от предела насыщения до нуля. На границах раздела слоев концентрация изменяется скачкообразно в соответствии с диаграммой состояния системы. Распределение насыщающего элемента по толщине диффузионного слоя и его строение приведены на рисунке 15.2. Двухфазные области в диффузионном слое в процессе ХТО не образуются. Однако эти области возникают при медленном охлаждении от температуры диффузионного насыщения в сплавах, испытывающих вторичную кристаллизацию. Наиболее распространенными видами химико-термической обработки являются цементация, азотирование, цианирование (нитроцементация), борирование, хромирование.
|
|

|



|





|




|
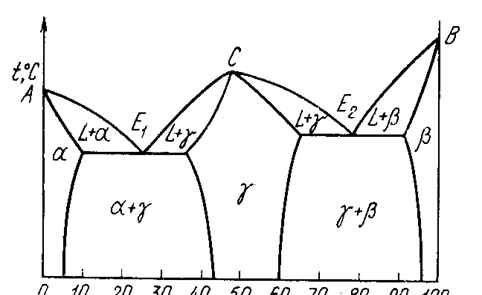
Рисунок 15.1 – Диаграмма состояния сплавов с ограниченной растворимостью и химическим соединением
![]() ![]() ![]() ![]() ![]() ![]() ![]() ![]() ![]() ![]() ![]() ![]() ![]() ![]() ![]() ![]() | AnBm | A(B) | A |
|
![]() | |||
| |||
![]() | |||
|
l, мм
Рисунок 15.2 – Изменение концентрации диффундирующего элемента по толщине слоя
Цементация стали. Технологический процесс диффузионного насыщения углеродом называется цементацией. Цель ее – получить детали машин и механизмов с твердой и износоустойчивой поверхностью при сохранении вязкой, хорошо выдерживающей динамические нагрузки сердцевины. Цементированные изделия предназначены для работы при знакопеременных нагрузках и в условиях трения и износа. Цементации подвергают зубчатые колеса, валы, оси, распределительные валики, кулачки, червяки, изготовленные, как правило, из малоуглеродистой стали с содержанием углерода не более 0,3 %. Данный технологический процесс осуществляется путем нагрева и длительной выдержки деталей в науглероживающей среде при температуре аустенитного состояния стали (900–950 оС). Цементацию наиболее часто проводят в газовой среде или в твердом карбюризаторе. При газовой цементации образование атомарного углерода происходит в результате диссоциации предельных углеводородов
СnH2n+2 « nC + (n+1)H2.
При цементации в твердом карбюризаторе атомарный углерод образуется в результате диссоциации оксида углерода
2CO « CO2 + C.
Содержание углерода в поверхностной зоне определяется пределом его растворимости в аустените при температуре цементации (линия SE диаграммы «железо–цементит»). Обычно цементацию проводят таким образом, чтобы содержание углерода в поверхностной зоне диффундирующего слоя не превышало 1,2 %. По мере удаления от поверхности в глубину изделия содержание углерода постепенно снижается, доходя до исходного состояния в цементируемой стали. После медленного охлаждения от температуры цементации поверхностная зона имеет структуру заэвтектоидной стали и состоит из перлита и карбидов (цементита). Это так называемая заэвтектоидная зона. Далее следует эвтектоидная зона, представляющая собой перлит. Содержание углерода в эвтектоидной зоне углеродистых сталей составляет около 0,8 %. Под эвтектоидной находится доэвтектоидная зона со структурой перлита и феррита. Микроструктура поверхностной области стали после цементации приведена на рисунке 15.3.
Рисунок 15.3 – Микроструктура поверхностной области стали, подвергнутой цементации
После цементации изделия подвергаются неполной закалке с последующим низким отпуском. В результате термической обработки высокоуглеродистая поверхностная зона приобретает структуру отпущенного мартенсита с включением карбидов (цементита). Твердость ее достигает значения HRC 62.
После термической обработки твердость сердцевины определяется химическим составом стали и находится в пределах HRC 15–35. В зависимости от упрочнения сердцевины цементируемые стали делятся на три группы: углеродистые стали с неупрочняемой сердцевиной, низколегированные стали со слабо упрочняемой сердцевиной, высоколегированные стали с упрочняемой сердцевиной. К первой группе относятся стали 10, 15, 20. В этом случае даже после закалки в воде сердцевина имеет феррито-перлитную структуру. При закалке в масле сердцевина низколегированных сталей второй группы, к которым относятся 15Х, 20Х,15ХР,20ХН, претерпевает бейнитное превращение и заметно упрочняется. В сердцевине высоколегированных цементируемых сталей 20ХГР, 20ХНР, 18ХГТ, 30ХГТ, 12ХНЗ, 12Х2Н4, 18Х2Н4В после охлаждения в масле и далее на воздухе образуется структура нижнего бейнита или мартенсита, что приводит к весьма интенсивному упрочнению.
Азотированием называется процесс поверхностного насыщения стали азотом. Оно применяется в целях повышения твердости, износостойкости и предела усталости, а также коррозионной стойкости деталей машин. Процесс азотирования проводится при 480–650 оС в течение 1–90 ч в среде газообразного аммиака, диссоциирующего по реакции
2NH3 « 2N + 3H2.
Образовавшийся атомарный азот адсорбируется поверхностью и диффундирует в металл. Изменения микроструктуры поверхностной зоны (рисунок 15.4, б), происходящие при азотировании, можно представить на основании диаграммы «железо–азот» (рисунок 15.4, а). В этой системе возможно образование следующих фаз: a – азотистый феррит; g – азотистый аустенит; g¢ – нитрид Fe4N; e – нитрид Fe3N. Со многими легирующими элементами азот также образует химические соединения – нитриды (CrN, Cr2N, MnN, TiN, MoN, AlN и др.).
а) б)
|

|
|
|
|
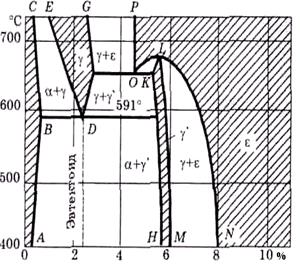
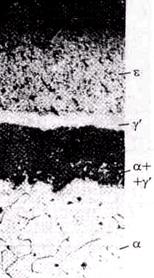
N
Рисунок 15.4 – Диаграмма системы Fe–N (а) и микроструктура поверхностной области стали, подвергнутой азотированию (б)
При температуре азотирования железа ниже эвтектоидной (591 оС) азотированный слой состоит из трех последовательно расположенных друг за другом фаз: e (Fe3N), g¢ ( Fe4N) и a (Feα(N)). В процессе медленного охлаждения с этих температур g-фаза при 591 оС испытывает эвтектоидное превращение на a и g¢, а при быстром охлаждении претерпевает мартенситное превращение.
В отличие от железа наличие углерода в стали приводит к образованию на поверхности диффузионного слоя карбонитридных фаз типа Fe3(C, N).
При азотировании легированных сталей наряду с вышеперечисленными фазами – e, g¢, g, a, – одновременно образуются нитриды легирующих элементов. Для повышения твердости и износоустойчивости процессу азотирования подвергают специальные стали, получившие название нитраллои. Они содержат алюминий, хром, молибден, которые образуют стойкие против коагуляции и роста нитриды. Наиболее часто азотированию подвергают стали 35ХМЮА, 38ХМЮА, 38Х2МЮА,35ХМА. Азотирование проводится при 500–520 оС. В процессе охлаждения нитраллоев от температуры азотирования до комнатной, вследствие уменьшения растворимости легирующих элементов, в a-зоне происходит образование очень дисперсных спецнитридов CrN, MoN, AlN. Эти дисперсные частицы препятствуют движению дислокаций и тем самым повышают твердость азотированного слоя до 1000 HV.
Твердость обычных конструкционных сталей после азотирования невысока. Для повышения усталостной прочности азотируют обычные конструкционные хромоникелевые стали.
С целью повышения коррозионной стойкости азотированию могут подвергаться любые стали. Процесс проводится при 600–700 оС в течение 0,5–1,0 ч. Коррозионная стойкость повышается в результате образования на поверхности изделия сплошной зоны из e-фазы.
Азотирование является окончательной обработкой. Термическая обработка – улучшение, заключается в закалке и высоком отпуске, предшествует азотированию. Азотированию подвергают такие детали, как гильзы гидроцилиндров и коленчатые валы дизелей, валы, шпиндели, ходовые винты и трубчатые изделия в станкостроении, зубчатые колеса.
Цианированием называется процесс одновременного насыщения поверхности деталей углеродом и азотом. Различают высокотемпературное и низкотемпературное цианирование.
Высокотемпературное цианирование проводят при 800–900 оС. Цель его – повысить твердость, износостойкость и усталостную прочность деталей машин из малоуглеродистых и среднеуглеродистых простых и легированных сталей. После высокотемпературного цианирования следует закалка и низкий отпуск.
Низкотемпературное цианирование проводят при 540–580 оС и применяют в основном для повышения стойкости окончательно термически обработанного инструмента из быстрорежущей стали.
Процесс цианирования осуществляется в жидких и газообразных средах; жидкое цианирование – в ваннах в смеси расплавленных цианистых солей типа NaCN, KCN с нейтральными солями типа NaCl, BaCl2, BaCO3. Недостатками процесса жидкостного цианирования являются большая ядовитость цианистых солей и высокая их стоимость.
Газовое цианирование называют нитроцементацией. Этот процесс осуществляют в смеси науглероживающих и азотирующих газов. В качестве науглероживающего может быть любой газ, применяемый при газовой цементации. Азотирующим газом является аммиак. Структура цианированного слоя определяется количеством углерода и азота, находящихся в нем. На состав и свойства цианированного слоя особое влияние оказывает температура цианирования. Повышение ее увеличивает содержание углерода в слое, снижение –содержание азота.
После цианирования на поверхности возникает тонкий карбонитридный слой Fe3(C, N), который часто металлографически не обнаруживается. Под ним лежит слой азотистого феррита. После закалки и низкого отпуска цианированный слой представляет собой карбонитридный мартенсит с включениями карбонитридных фаз.
В настоящее время высокотемпературное газовое цианирование (нитроцементация) широко внедряется вместо газовой цементации. Высокотемпературное цианирование проводят при более низких температурах, не вызывающих рост зерна как, например, при газовой цементации. Кроме этого, цианированные изделия по твердости и износостойкости превосходят цементированные. Это объясняется наличием в диффузионном слое не только углерода, но и азота.
Борирование – это диффузионное насыщение поверхностного слоя бором. Процесс проводится с целью повышения поверхностной твердости и износостойкости, а также коррозионной стойкости. Наиболее перспективны для промышленного использования борирования в порошкообразных смесях, в расплавах солей и газовое борирование.
Твердое борирование проводят в порошковых смесях на основе технического карбида бора (B4C) или в металлотермических смесях, основу которых составляют оксид бора (B2O3) и алюминий. Борирование из обмазок целесообразно применять при необходимости упрочнения крупногабаритных изделий или для местного борирования отдельных участков деталей. Поставщиками бора при насыщении из обмазок являются карбид бора или оксид бора. На поверхность обрабатываемого изделия обмазки наносят кистью. Наиболее часто применяются обмазки, состоящие из двух слоев – активного и защитного. Защитный слой предохраняет активный от окисления в процессе борирования в кислородосодержащей атмосфере.
Борирование в расплавах солей и окислов делится на электролизное и безэлектролизное. Электролизное борирование проводят в расплаве буры (Na2B4O7). Обрабатываемая деталь является катодом. Безэлектролизное борирование осуществляют в расплавах боросодержащих веществ (В, В4C и др.) и нейтральных солей.
Газовое борирование проводят в среде, полученной разложением газообразных соединений бора. Наиболее часто применябт диборан (В2Н6) и треххлористый бор (BCl3), которые разбавляют газами, не содержащими бор (Н2, Ar, N2).
Борирование сталей проводят при температурах 800–1050 oС в течение 2–10 ч. Борированный слой состоит из двух зон: зоны боридов и переходной зоны (рисунок 15.5, а). Зона боридов имеет характерное игольчатое строение и представляет собой химические соединения бора и железа. При жидкостном борировании зона имеет однофазное строение и состоит из фазы Fe2B, во всех остальных случаях – из двух фаз – FeB и Fe2B. Углерод резко снижает содержание борида FeB в слое, а легирующие элементы, за исключением алюминия к меди, – увеличивают. Легирующие элементы в сталях собственных боридов не образуют, а легируют бориды железа.
Под зоной боридов располагается переходная зона, отличающаяся по своей структуре от сердцевины. Она представляет собой твердый раствор бора, а также углерода и легирующих элементов в железе. Толщина переходной зоны определяется глубиной проникновения бора. Легирующие элементы уменьшают толщину переходной зоны.
Средне-, тяжелонагруженные детали после борирования подвергаются закалке и отпуску.
Борирование используют для упрочнения различных деталей машин, технологической оснастки и инструмента, работающих в условиях интенсивного износа.
Хромирование – это процесс диффузионного насыщения поверхностных деталей хромом. Хромирование железа и сталей с содержанием углерода менее 0,2 % проводят с целью повышения коррозионной стойкости в различных агрессивных средах и жаростойкости. Стали с содержанием углерода более 0,3 % подвергают хромированию, прежде всего, для повышения твердости и износостойкости, а также коррозионной стойкости и жаростойкости.
Хромирование осуществляют в порошковых смесях, в газовой и жидкой средах. Порошковая смесь для хромирования состоит из поставщика хрома, в качестве которого используют порошки хрома, феррохрома, оксиды хрома и веществ, предотвращающих спекание хромосодержащих частиц и прилипание их к поверхности изделий. При хромировании в газовой среде так же, как и при насыщении в порошковых смесях, источником активных атомов хрома служат галлогениды хрома, находящиеся в газообразном состоянии.
Жидкой средой при хромировании являются расплавы солей хлоридов хрома (CrCl2 и CrCl3), а также соли-стабилизатора, в качестве которой используют одно из следующих соединений: BaCl2, CaCl2 или MgCl2.
Диффузионное превращение хромом проводится при температурах 900–1200 оС в течение 4–10 ч.
При хромировании железа и стали с содержанием углерода менее 0,2 % образующийся диффузионный слой представляет собой твердый раствор хрома в a-железе. Содержание хрома на поверхности слоя достигает 70 %. Толщина слоя не превышает 0,2 мм. Диффузионный слой сталей, содержащих более 0,3 % углерода, состоит из трех зон: карбидной, промежуточной и обезуглероженной. С увеличением углерода до 0,8 % толщина карбидной и промежуточной зон возрастает. Карбидная зона представляет собой сплошной слой карбидов хрома (Cr23C6, Cr7C3) толщиной до 0,02 мм. Промежуточная зона имеет перлитное строение и состоит из феррита и карбидов хрома. Содержание углерода в обезуглероженной зоне ниже, чем в сердцевине. Микроструктура стали У8 после хромирования представлена на рисунке 15.5, б. При необходимости после хромирования средне- и тяжелонагруженные детали подвергают закалке с последующим отпуском. Хромирование применяется для повышения стойкости штампового инструмента, пресс-форм литья под давлением алюминиевых сплавов, различных деталей двигателей и газовых турбин, работающих при высоких температурах, фильтров нефтяных скважин, деталей насосов и турбобуров, крепежных деталей.
а) б)
Рисунок 15.5 – Микроструктура поверхностной области стали, подвергнутой борированию (а) и хромированию (б)
Дата добавления: 2015-02-10; просмотров: 2887;