Цель работы: изучение основ теории и технологии закалки сталей.
Закалкой называется вид термической обработки, который заключается в нагреве стали на 30–50 оС выше температур критических точек Ас1 или Ас3 диаграммы состояния «Fe–Fe3С» в соответствии с рисунками 10.1 и 10.2, выдержке при этих температурах для завершения фазовых превращений и последующем охлаждении в область мартенситного превращения со скоростью выше критической Vк (рисунок 10.3).
|

|
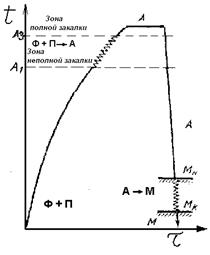
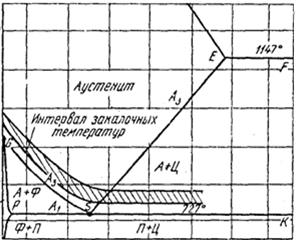
0,2 0,6 1,0 1,4 1,8 2,2 % 2,6
С
Рисунок 10.1 – Температурный Рисунок 10.2 – Диаграмма Fe–Fe3C
режим закалки стали
Рисунок 10.3 – Диаграмма изотермического превращения переохлажденного аустенита
Под критической скоростью закалки понимается минимальная скорость охлаждения, обеспечивающая бездиффузионное превращение аустенита в мартенсит. Целью закалки является повышение твердости, прочности и долговечности механизмов машин и инструмента.
В зависимости от температуры нагрева закалку подразделяют на полную и неполную. В первом случае сталь нагревается выше температур Ас3 или Асm в область аустенита. Во втором – выше температуры Ас1, но ниже Ас3 или Асm в область, где наряду с аустенитом в доэвтектоидной стали присутствует феррит, а в заэвтектоидной – цементит (см. рисунок 10.2).
Все доэвтектоидные стали (< 0,8 % С) должны подвергаться полной закалке. Нагрев осуществляется на 30–50 оС выше точки Ас3 (рисунок 10.2, линия GS). При этом сталь с исходной структурой феррита и перлита при нагреве переходит в аустенитное состояние. При последующем охлаждении со скоростью выше критической (см. рисунок 10.3) аустенит превращается в мартенсит. Такой нагрев является оптимальным, так как обеспечивает мелкое зерно аустенита при нагреве и мелкоигольчатый мартенсит с вязким изломом после охлаждения. Нагрев доэвтектоидной стали значительно выше точки Ас3 приводит к перегреву (укрупнению зерна аустенита), а последующее быстрое охлаждение приводит к получению крупноигольчатого мартенсита, что ухудшает вязкость стали. Перегрев стали, кроме того, способствует обезуглероживанию поверхности и образованию трещин при закалке. Этого следует избегать.
Нагрев доэвтектоидной стали в область межкритических температур (выше Ас1, но ниже Ас3) не обеспечит растворения исходного феррита в аустените. Аустенит при закалке превратится в мартенсит, а оставшийся феррит снизит прочностные свойства стали. Поэтому такой нагрев для доэвтектоидной стали является недостаточным (неполная закалка), структурные изменения в доэвтектоидных сталях при закалке происходят по схеме:
Заэвтектоидные стали (> 0,8 % С) подвергаются неполной закалке. Нагрев осуществляется до температуры на 30...50 оС выше точки Ас1 (727 оС). При таком нагреве образуется аустенит из исходной структуры перлита, а избыточный цементит сохраняется. После охлаждения со скоростью выше критической аустенит превращается в структуру закаленной стали – мартенсит, а цементит без изменения сохраняется в мартенситной основе (цементит обеспечивает большую твердость и износостойкость инструментальных сталей).
В реальных условиях наблюдаются нарушения режимов нагрева и имеет место неполная закалка изделий из доэвтектоидных сталей, а также полная закалка изделий из заэвтектоидных сталей (вследствие повышенной температуры печи), приводящие к браку термообработки – снижению твердости.
Нагрев выше точки Асm (линия SE) приводит к образованию высокоуглеродистого аустенита (вследствие растворения в нем цементита), обеспечивающего после охлаждения крупноигольчатый (вследствие перегрева) мартенсит и большее количество остаточного аустенита в связи с тем, что в таком (высокоуглеродистом) аустените конец мартенситного превращения (рисунок 10.4, точка Мк) сдвигается в область отрицательных температур.
Рисунок 10.4 – Изменение температурного интервала мартенситного превращения в зависимости от содержания углерода в аустените
Согласно этой схемы после закалки сталей с содержанием углерода более 0,5 % в структуре всегда будет присутствовать остаточный аустенит (см. точку пересечения линий конца мартенситного превращения и температуры охлаждающей жидкости). Остаточный аустенит ухудшает свойства закаленной стали. В заэвтектоидных сталях структурные превращения при закалке происходят по следующей схеме:
Таким образом, для заэвтектоидных сталей оптимальной будет неполная закалка. Нагрев под закалку производится в печах периодического и непрерывного действия. Широко применяются ванны, в которых изделие нагревается в расплавленных солях или металлах.
Скорость охлаждения регулируется видом охлаждающей среды, в качестве которой наиболее часто применяются минеральное масло, вода, водные растворы солей, кислот, щелочей. В приведенном ряду скорость охлаждения от первой охлаждающей среды к последней увеличивается. Для углеродистых сталей необходимая скорость достигается при охлаждении в воде (в водных растворах), для легированных –в масле или на воздухе.
Мартенситное превращение имеет ряд особенностей по механизму и кинетике. Оно носит бездиффузионный характер, т. е. не сопровождается диффузионным перераспределением углерода и железа в решетке. При мартенситном превращении происходит лишь коллективное смещение, сдвиг атомов на небольшое расстояние при наличии когерентной связи решеток аустенита (г. ц. к.) и мартенсита (тетрагональная).
Наличие этой связи (общей атомной плоскости) приводит практически к мгновенному во времени превращению. При мартенситном превращении происходит лишь переход кубической гранецентрированной решетки аустенита (g-твердого раствора) в тетрагональную объемно-центрированную решетку a-твердого раствора. Особенность мартенситного превращения в сталях состоит в том, что весь углерод, находящийся в аустените (g-твердом растворе), переходит в a-твердый раствор. Пересыщение углеродом a-твердого раствора вызывает искажение решетки (о. ц. к.) a-Fe, т. е. приводит к образованию тетрагональной (с/а > 1) кристаллической решетки. Поэтому структура закаленной стали – мартенсит – представляет собой пересыщенный твердый раствор углерода в a-железе.
Особенностью мартенсита является его высокая твердость и прочность. В сталях с содержанием 0,6...0,7 % С твердость мартенсита достигает ~60 HRC, это в 6 раз больше равновесного a-твердого раствора – феррита. Высокая твердость мартенсита объясняется созданием микро- и субмикроскопической неоднородности строения с равномерным ее распределением по объему, т. е. большим числом нарушений кристаллического строения.
Поверхности раздела кристаллитов мартенсита – представляют собой труднопреодолимые препятствия для скольжения дислокаций при деформации кристалла. Перемещения атомов тормозят находящиеся в решетке мартенсита атомы углерода, создающие статические искажения решетки (напряжения III рода). Все это определяет высокую твердость структуры закаленной стали – мартенсита. С увеличением содержания углерода в мартенсите наряду с повышением твердости возрастает и хрупкость.
Мартенситное превращение, происходящее при закалке стали, приводит к увеличению удельного объема, что является одной из основных причин возникновения больших внутренних (структурных) напряжений II рода, вызывающих деформацию изделий или даже появление трещин. Перепад температур по сечению закаливаемого материала приводит к образованию термических внутренних напряжений (I рода). Эти напряжения, возникающие при закалке (структурные и термические), тем больше, чем выше температура закалки и скорость охлаждения в мартенситном интервале температур (Мн–Мк).
В случае охлаждении аустенита со скоростями меньшими критической вместо мартенсита в интервале температур 720–550о С образуются феррито-цементитные смеси, получившие название перлит, сорбит, троостит. По мере увеличения скорости охлаждения дисперсность смеси возрастает, что приводит к повышению твердости и прочности. Наиболее грубой смесью является перлит, максимальной дисперсностью обладает троостит.
Контрольные вопросы
1. Дать определения закалке, полной и неполной, указать область их применения.
2. Описать превращения, протекающие в до - и заэвтектоидных сталях при полной и неполной закалках, и указать образующиеся при этом структуры.
3. Дать определение мартенситу, указать особенности мартенситного превращения и причины повышения его прочностных свойств.
4. Описать превращения, протекающие в стали в случае охлаждения аустенита со скоростями меньшими критической.
5. Указать, от чего зависит количество остаточного аустенита в закаленной стали и причины его появления.
6. Дать классификацию внутренних напряжений и причины их возникновения.
Дата добавления: 2015-02-10; просмотров: 1163;