Технологічність складання–розбирання конструкції
Один із важливих напрямів відпрацювання конструкції на технологічність – це забезпечення зручності і простоти процесу складання–розбирання конструкції. Складання конструкції – завершальний і один із найвідповідальніших етапів виготовлення виробу. При виконанні складально–розбиральних робіт використовують, як правило, великий обсяг ручних операцій. Якість складальних робіт, простота та зручність їх виконання суттєво залежить від конструктивних особливостей окремих деталей і вузлів, від їх виконання.
Крім того, процес складання–розбирання конструкції в багатьох випадках певним чином визначає трудомісткість ремонту обладнання. Особливо це стосується бурового і нафтогазопромислового обладнання, яке характеризується специфічними властивостями.
Практикою машинобудування набутий великий досвід проектування і використання різноманітних конструктивних елементів, які підвищують технологічність процесу складання–розбирання виробів. Далі наведено деякі рекомендації і поради з цього приводу.
1) Конструкція обладнання повинна забезпечувати принцип вузлового складання, тобто складання виробу з попередньо складених блоків. Це дає можливість проводити паралельно складальні роботи, що скорочує терміни виготовлення виробу, підвищує ефективність виробництва. Важливо розчленувати виріб на раціональні технологічні вузли, які можуть виконувати певні функції. В такому випадку для оцінки їх якості можна використати більш ефективні способи контролю і випробування.
2) Передбачати в конструкції установочні мітки, контрольні штифти та інші конструктивні елементи для забезпечення певного і єдино можливого відносного розміщення деталей і вузлів, що складаються.
На рис. 5.1 зображено спосіб фіксації взаємного розміщення деталей з використанням контрольного цилінд-ричного штифта. Штифти виготовляють з високовуглецевих конструкційних або легованих сталей з наступним гартуванням до твердості HRC 50 – 55. Робочі поверхні штиф-
тів обробляються до шорсткості Ra 0,32 – 0,63лмкм. В один з отворів циліндричний штифт встановлюють з натягом. Більш повна інформація про установочні штифти міститься в [9].
Рисунок 5.1 – Фіксація деталей (вузлів) з використанням установочних штифтів
3) Забезпечувати (де це можливо) складання і розби-рання спряжених деталей і вузлів без використання допо-міжних монтажних пристроїв. Установлення спряжених деталей повинно здійснюватися шляхом простих переміщень.
4) Передбачувати в конструкції виробу різноманітні конструктивні елементи (отвори, канавки, отвори з різьбою тощо) для спрощення розбирання спряжених деталей і вузлів. Наприклад, конструкцію “а” (рис. 5.2) розбирати незручно. При наявності кільцевого зазору між втулкою і корпусом (рис.5.2, б) або різьбових отворів у втулці (рис.5.2, в) розби-рання конструкції спрощується. Для знімання втулки без перекосів необхідно передбачити в ній не менше трьох різьбових отворів, розміщених один відносно одного під кутом 120о.
5) Передбачати конструктивні елементи на деталях виробу, які зменшують імовірність неправильного складання конструкції або виключають неправильне складання взагалі.
Роглянемо це правило на прикладі підшипника ковзання (рис.к5.3).
|
|

Рисунок 5.2 – Приклади використання спеціальних конструктивних елементів для демонтажу втулки з
корпусу ( б – кільцевої канавки; в – різьбових отворів):
1 – корпус; 2 – втулка
| |
|
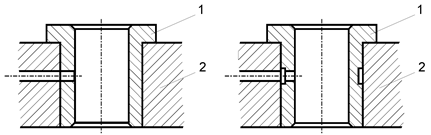
Рисунок 5.3 – Нетехнологічна (а) та технологічна (б) конструкції підшипникового вузла ковзання:
1 – втулка; 2 – корпус
Підшипникова втулка повинна бути встановлена таким чином, щоб отвори для підведення масла в корпусі і втулці
співпадали. Конструкція, представлена на рис. 5.3, а є нетех-нологічною взагалі. Навіть при незначному кутовому зміщенні втулки в корпусі при складанні отвір для підведення масла буде перекрито.
Для забезпечення технологічності складання цього вузла можна запропонувати різні конструктивні варіанти. Зупинимо-
ся на одному з них (рис.5.3, б). На втулці виконана кільцева канавка, яка забезпечує подачу масла при будь-якому кутовому відхиленні втулки відносно отвору в корпусі.
6) В деталях, які будуть складатися з гарантованим натягом передбачувати західні фаски на внутрішній і зовнішній спряжених поверхнях. Аналогічні фаски повинні бути і на кріпильних деталях.
7) При проектуванні нестандартних кріпильних деталей розмір “під ключ” (в мм) головок болтів і гайок вибирати із нормалізованого ряду: 3; 3,2; 3,5; 4; 4,5; 5; 5,6; 6; 7; 8; 9; 10; 11; 12; 13; 14; 17; 19; 22; 24; 27; 30; 32; 36; 41; 46; 50; 55; 60; 65; 70; 75; 80; 85; 90; 95; 100; 110; 115; 120; 125; 130; 135; 140; 145; 150; 155; 160; 165; 170; 175; 180; 185; 190; 200; 210; 220; 230; 240; 250.
8) Передбачати різноманітні конструктивні елементи для надійної фіксації болта від провертання при затягуванні гайки.
9) Для зручності демонтажу призматичних шпонок передбачати отвір з різьбою під демонтажний гвинт (рис. 5.4,ра). Можна також змінити форму шпонкового пазу (рис. 5.4, б) або зробити косий зріз на шпонці (рис. 5.4, в). В першому випадку шпонку вибивають осьовою силою, в другому – радіальною.
Слід відмітити, що використання сегментних шпонок також суттєво спрощує їх демонтаж.
Рисунок 5.4 – Конструктивні елементи для зручності демонтажу призматичних шпонок:
1 – шпонка; 2 – вал
10) Не допускати центрування деталей зразу по двох поверхнях (рис. 5.5, а). Центрувати необхідно лише по одній поверхні, залишаючи на другій гарантований зазор (рис. 5.5, б та 5.5, в)
11) Для зручності складання-розбирання масивних конструкцій передбачати в складових частинах, маса яких
більша 16 кг такелажні конструктивні елементи (отвори, виступи, провушини, отвори під рим-болти). Кількість і місце розміщення вказаних вище конструктивних елементів зале-жить від форми деталі і розміщення лінії центру ваги деталі.
Рисунок 5.5 – Центрувальні з’єднання (а – по двох поверхнях;
б, в – по одній поверхні):
1 – палець; 2 – корпус; 3 – гайка
|
Дата добавления: 2015-01-10; просмотров: 1201;