Виды промышленного использования углей
В народном хозяйстве уголь используется для получения теплоты в энергетике, при производстве строительных материалов /кирпич, известь, цемент/. Уголь Донбасса применяется в газогенераторах, для получения термоантрацита, карбида кальция, электрокорунда и при агломерации руд, Кузбасса - при сжигании в отражательных печах, топках энергопоездов, при полукоксовании, в газогенераторах, при получении активного угля, Печорского бассейна - для сжигания в топках поездов, Правобережной Украины - для получения углещелочных реагентов, Восточной Сибири - для полукоксования.
Большая часть /70-80%/ добываемого в стране угля используется в энергетических целях, т.е. для слоевого сжигания, сжигания в пылевидном состоянии в отражательных печах, сжигания в топках судов и паровозов, энергопоездов, для коммунальных и бытовых нужд.
Слоевое сжигание производится в слоевых топках с ручной и механической подачей кускового топлива, используется в котлоагрегатах малой производительности. Пылевидное сжигание осуществляется в факельных топках, которыми снабжены котлоагрегаты высокой и средней производительности. Топливо предварительно размалывается до пылевидного состояния, газовоздушным потоком транспортируется по топочному объему и сгорает на лету. В отражательных печах теплопередача осуществляется "отражением" теплоты от факела горящего топлива и нагретого свода к нагреваемому материалу. В таких печах выплавляют сталь, цветные металлы, варят стекло.
Факельно-слоевые топки, представляющие собой сочетание двух типов, применяются в котлоагрегатах малой и средней производительности. В них топливо сжигается в факеле и дожигается в "кипящем слое" /вдуваемый снизу воздух обеспечивает возможность сжигания во взвешенном состоянии угольных обломков без предварительного размола/.
На технологические цели расходуется до 20% добываемого угля. Технологическое использование топлива включает в себя пиролиз/коксование и полукоксование/, газификацию /превращение угля в горючие газы/, гидрогенизацию /превращение угля в новые газообразные, жидкие и твердые горючие продукты/, производство углеродистого наполнителя /термоантрацита/, карбида кремния, электрокорунда и др.
Пиролиз - расщепление крупных молекул и вторичные превращения продукгов расщепления /полимеризация, конденсация, ароматизация и т.д./ при нагревании топлива в закрытых реакторах без доступа воздуха. Высокотемпературный пиролиз называется коксованием, низкотемпературный - полукоксованием.
Коксование - метод переработки каменных углей определенного состава и степени углефикации нагреванием до температуры 900-1050 °С без доступа воздуха. Измельченный уголь переходит сначала в пластическое состояние, а затем после отгона летучих веществ превращается в твердый пористый нелетучий остаток /кокс/. В процессе коксования из угля или шихты /смесь углей различных марок/ в среднем получается 65-80% кокса, 2,5-3,5% каменноугольной смолы, 1,0-1,1% бензола, 1,0-1,2% сульфата аммония, 15-18% коксового газа /из 1 т угля - 300-350 м3 газа/. Кокс - твердое пористое /пористость около 50%/ вещество с малым выходом летучиx и высокой удельной теплотой сгорания. Основные показатели качества кокса - ситовый состав /размер кусков и равномерность крупности/, механическая прочность, выход летучих, зольность, массовая доля серы и фосфора. По размеру кусков кокс подразделяется следующим образом: более 25 мм - металлургический /доменный и литейный/; 15-25 мм - орешек /коксик/; до 15 мм - мелочь. Орешек и мелочь используются при агломерации руд и как высокосортное энергетическое топливо.
В коксовом газе после конденсации каменноугольной смолы, бензольных углеводородов, воды и абсорбции аммиака объемная доля водорода составляет 54-59%; метана - 23-28%; оксида углерода - 5-7% и др. Коксовый газ применяется как топливо для обогрева доменных и коксовых батарей, а также как химическое сырье после разделения на водородную, метановую и другие фракции. Каменноугольная смола содержит до 1000 индивидуальных химических соединений и представляет собой сложную смесь ароматических веществ /бензол, толуол, ксилол, нафталин, фенол и др./, из которых получают медикаменты, взрывчатые материалы, пластмассы и т.д. Бензол - сложная смесь паров легких ароматических углеводородов, используется при получении ацетона, фенола, хлорбензола, анилина и других многочисленных химических продуктов.
Полукокс - слабоспекшийся хрупкий продукт, содержащий до 10% летучих веществ, применяется как энергетическое топливо и как составная часть шихты для коксования. Объемные доли компонентов газа, %: оксид углерода – 20-55; предельные углеводороды - 15-20; непредельные углеводороды 7-8; водород - 15-19 и др. Газ обладает высокой объемной теплотой сгорания, служит сырьем для химической промышленности. Массовые доли компонентов смолы, %:
предельные углеводороды - 0-27, фенолы - 8-20, карбоновые кислоты -1-2. Из смолы получают моторные топлива, растворители и органические мономеры. Пирогенетическая подсмольная вода содержит аммиак, цианистые соединения, ацетон, уксусную кислоту и газ /метан до 50%, водород 10-20% и оксид углерода.
Газификация - превращение органической массы твердого топлива в газогенераторе в генераторные газы. Этому процессу могут быть подвергнуты любые виды твердого топлива - низкосортные угли, торф, горючие сланцы, полукокс и др. Твердый остаток представляет собой золу. В зависимости от вида дутья получают генераторный газ определенного состава. Дутье воздухом дает воздушный газ /60% азота, 30% оксида углерода и др./ с объемной теплотой сгорания 4950 кДж/м3 , водяным паром - водяной газ /50% водорода, 36% оксида углерода и др./ с объемной теплотой сгорания 10000 кДж/м3, воздухом и водяным паром - смешанный или генераторный газ /48% азота, 30% оксида углерода , 16% водорода и др./ с объемной теплотой сгорания 6300 кДж/м3, водяным паром и кислородом - парокислородный газ /66% оксида углерода, 31% водорода/ с теплотой сгорания 9850 кДж/м3. Одно из перспективных направлений в развитии газификации - создание мощного газогенератора для паровой газификации углей с внешним источником теплоты /атомный реактор, сжигание топлива в отдельном аппарате/.
Представляет интерес воплощение идеи Д.И.Менделеева о подземной газификации углей. Органическая масса теплива превращается в газ, на месте угольного пласта в выгоревшем пространстве остаются зола и шлак /рис.18/. Впервые в мире процесс подземной газификации угольного пласта был осуществлен в СНГ в Горловке /Донбасс/. Полученный газ имел состав, %: оксид углерода /IV/ - 9-11; оксид углерода /II/ - 15-19, водород - 14-17; метан - 1.4-1,5; азот - 53-55. Объемная теплота сгорания достигала 1000 ккал/м3 /4,2 МДж/м3. В настоящее время работают Южно-Абаканская /Канско-Ачинский бассейн/ и Ангренская /Заападный угленосный район Средней Азии/ станции подземной газификации. За рубежом действующие подземные газогенераторы имеются в США, Великобритании и Чехии. Намечаются программы исследований процесса подземной газификации в Канаде, Бельгии и ФРГ. Недостатки этого способа - низкая объемная теплота сгорании /3000-4000 кДж/м3/ получаемого газа и высокие /до 20%/ потери угля в недрах. Повышение теплоты сгорания газа может быть достигнуто применением паро-кислородного и кислородного дутья под давлением более 25 Па и совершенствования системы подземной газификации.
|


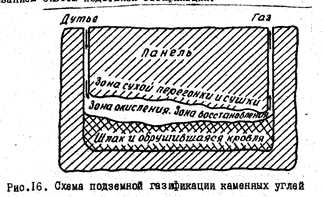
Гидрогенизация заключается в разрушении внутримолекулярных и межмолекулярных связей в органической массе твердого топлива /бурый и низкометаморфизованный каменный уголь марок Д, ДГ, Г, ГЖ, горючие сланцы и др./ при воздействии на него водородом под высоким давлением (20-30 МПа/ в условиях повышенных температур /380-650 °С/ в присутствии катализаторов с целью получения горючесмазочных материалов и газов. При температуре 500-700 °С и давлении водорода 3,5-5 МПа конечным продуктом будет метан и процесс называется гидрогазификацией угля. Ископаемое топливо, предназначенное для гидрогенизации, должно быть малозольным и малосернистым с долей углерода не более 85%. водорода - не менее 4,5%.
Термоантрацит получают термообработкой антрацита при температура 1200-1400 °С, в результате чего существенно увеличивается механическая прочность и электрическая проводимость. Он используется в литейном производстве и в качестве основного наполнителя при изготовлении электродов, углеродистых блоков для доменных печей и футеровочных материалов в алюминиевой и химической промышленности.
В промышленности строительных материалов при производстве извести, цемента и кирпича используют малодефицитные низкосортные угли.
Ископаемый уголь также используется при производстве углеродных адсорбентов, активного угля, углещелочных реагентов, термографита, в процессе агломерации руд и как поделочный камень. Активный /активированный/ уголь - пористое вещество, обладающее высокими адсорбционными свойствами и гидрофобностью, предназначается для поглощения поровой поверхностью газов, паров и растворенных веществ.
Порошкообразные углещелочные реагенты применяются при бурении скважин для повышения качества бурового глинистого раствора, изготавливаются из бурых и окисленных каменных углей.
Термографит получают в процессе длительной термообработки анграцита при температуре более 2500 °С и используют в основном для производстве смазочных материалов.
Агломерация руд - термическое окускование мелких руд и концентратов путем их спекания. Исходным продуктом является шихта, включающая помимо руд и концентратов коксовую мелочь /до 3 мм/, антрацитовый штыб /до 3 мм/, тощий уголь /до 3 мм/, известь и возврат /бракованный к мелкий агломерат/.
Стойкие к выветриванию, вязкие и крепкие, хорошо принимающие полировку угли используются как поделочный материал /для изготовления художественных изделий, ваяния/, а также в качестве облицовочных плит. Такие угли известны в Восточной Сибири, Китае и Вьетнаме.
Дата добавления: 2015-12-01; просмотров: 2524;