Получение углеводородов и галогенпроизводных
ПОЛУЧЕНИЕ БУТАДИЕНА-1,3 (ДИВИНИЛА)
Бутадиен-1,3 СН2=СН—СН—СН2 является основным мономером для получения синтетических каучуков.
Синтез бутадиена-1,3 из этанола, разработанный С. В. Лебедевым, был первым промышленным методом получения мономера, на основе которого в 1932 г. впервые в мире был пущен завод по производству синтетического каучука.
Суммарное уравнение реакции может быть записано в виде
2С2Н5ОН ® С4Н6 + Н2 + 2Н2О, ΔН = 85 кДж
Из уравнения видно, что суммарная реакция представляет собой сочетание конденсации, дегидрирования и дегидратации. Этим требованиям отвечает предложенный Лебедевым бифункциональный оксидный катализатор, содержащий дегидрирующие и дегидратирующие компоненты. Однако теперь метод утратил свое практическое значение. Принципиальный недостаток метода заключается в его низкой селективности (даже теоретический выход дивинила из 100% этанола составляет 58,7%).
В настоящее время основными способами синтеза дивинила являются дегидрирование n-бутана, выделенного из природного газа, и комплексная переработка бутан-бутиленовых фракций пиролиза нефтепродуктов, включающая извлечение бутадиена, выделение изобутилена и дегидрирование n-бутиленов в бутадиен.
При дегидрировании бутана существенную роль играют термодинамические ограничения, вследствие чего бутадиен-1,3 получить в одну стадию с технически приемлемым выходом в обычных условиях практически невозможно, и лишь с помощью специальных приемов (применение вакуума, окислительное дегидрирование) выход может быть поднят до требуемого уровня.
Большинство промышленных установок получения дивинила из бутана работает по двухстадийной схеме. Первая стадия дегидрирования бутана заключается в превращении его в бутилен, а вторая — это процесс получения дивинила из бутилена.
Дегидрирование бутана в бутилен на хромооксидном промотированном катализаторе, нанесенном на оксид алюминия, протекает по реакции
С4Н10 ® С4Н8 + Н2, ΔH = 131 кДж
Состав...... Al2O3 Fe2O3 Cr2O3 SiO2 KNO3 CaO H2O
Массовая доля, % 66,10 1,72 15,8 7,9 4,93 0,14 3,34
В процессе дегидрирования бутана катализатор покрывается углеродистыми отложениями и изменяет свой химический состав. Активность катализатора при этом резко снижается. С целью реактивации катализатор непрерывно отводят из реактора и обжигают в токе воздуха в регенераторе с кипящим слоем. Углеродистые соединения при этом выгорают, а низшие оксиды хрома окисляются до Сг2Оз. Технологическая схема установки дегидрирования бутана изображена на рис. 1.
Бутан в жидком виде поступает в осушитель 1, заполненный адсорбентом (А12О3, цеолиты) и затем в испаритель 2. Образовавшиеся пары нагреваются в трубчатой печи 3 до температуры 780— 820 К и поступают под распределительную решетку реактора 4 на дегидрирование. Необходимое для протекания реакции количество теплоты подводится с потоком нагретого регенерированного катализатора из регенератора 5. Температура в регенераторе 890—920 К. Регенерированный катализатор подают на верхнюю распределительную решетку и, следовательно, катализатор и реакционные газы движутся противотоком. В верхней части имеется змеевик для закалки реакционных газов. Благодаря этому температура газов быстро снижается до 720—750 К и предотвращается их дальнейшее разложение.
|
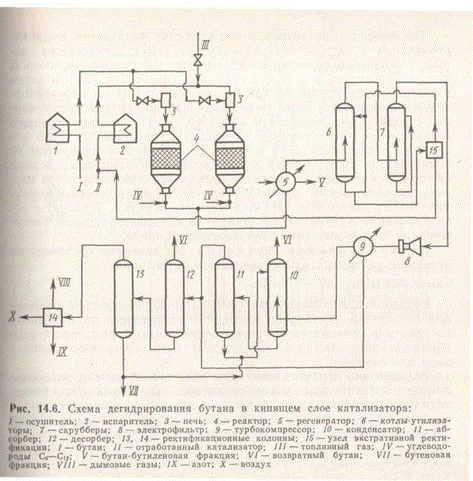
Транспортирование катализатора в регенератор осуществляется потоком воздуха, а в реактор — парами исходного углеводорода или азотом. Контактный газ из реактора направляется в котел-утилизатор 6 для получения вторичного пара, а затем для улавливания катализаторной пыли и дальнейшего охлаждения — в скруббер 7, орошаемый водой. Дымовые газы из регенератора освобождаются от катализаторной пыли в электрофильтре 8, затем проходят через скруббер и выбрасываются в атмосферу.
Для восполнения потерь и поддержания активности к циркулирующему в системе катализатору ежесуточно добавляется свежий. Очищенный контактный газ поступает в турбокомпрессор 9, давление нагнетания которого составляет около 0,5 МПа, и затем в систему конденсации 10, где в качестве хладагента последовательно применяются вода и кипящий пропан. Несконденсированный продукт направляется в абсорбер 11. Поглощение производится смесью углеводородов С6—C12. Растворенный бутилен отгоняется в десорбере 12 и всмеси со сжиженным продуктом из конденсатора 10 поступает в систему ректификационных колонн 13 и 14. В колоннах от продукта дегидрирования отгоняются низко- и высококипящие примеси (последние добавляются к циркулирующему абсорбенту для компенсации потерь.). Продукты дегидрирования бутана направляются на блок экстративной ректификации 15 для выделения бутиленовой фракции.
Дегидрирование бутилена до дивинила протекает на
хромкальцийфосфатном катализаторе по реакции
C4Н8 ® C4Н8 + H2, ΔН=119кДж.
Технологическая схема дегидрирования бутиленов изображена на рис.2.
|
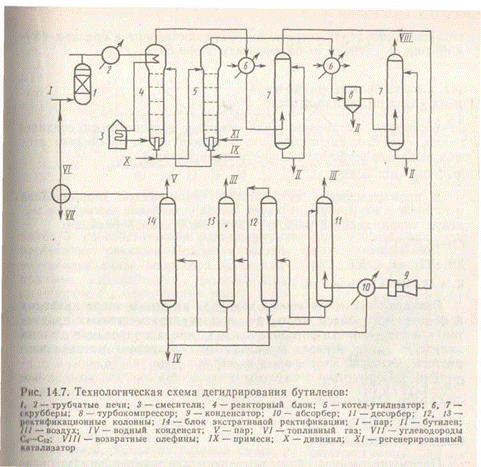
ХЛОРИРОВАНИЕ ПАРАФИНОВ И ИХ ГАЛОГЕНПРОИЗВОДНЫХ
В промышленности осуществляют термическое хлорирование в газовой фазе при температуре, необходимой для активации молекул хлора, дающей начало радикальной цепной реакции: С12 ® С1× + С1×
RH + С1× ® R + HCl
R + Cl2 ® RCl + С1× и т. д.
Реакция замещения атомов водорода на атомы хлора приводит
к образованию смеси моно-, ди- и полихлорзамещенных продуктов и выделению хлороводорода.
Преимущественное образование того или иного продукта определяется условиями реакции; температурным режимом и молекулярным соотношением углеводорода и хлора (рис. 3).
|

Для получения наибольшего выхода хлористых метила и метилена за счет уменьшения хлороформа и тетрахлорида углерода (которые в основном получают другими способами) процесс проводят в температурном интервале 670—520 К при 8—12-кратном избытке метана в хлорметановой смеси. При этом улучшается отвод теплоты из зоны реакции.
|
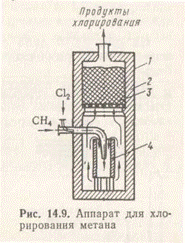
Хлорирование метана проводят в хлораторе (рис. 4), представляющем собой стальной цилиндрический корпус, футерованный изнутри шамотным кирпичом 2, в верхней части которого расположена насадка из фарфоровых колец 3, способствующая равномерному протеканию реакции. Половина высоты внутренней части хлоратора занята открытым керамическим вертикальным цилиндром 4 с отверстиями внизу, в который опущена суженным кольцом керамическая труба, подающая сырье. Процесс начинают предварительным разогреванием внутренней части хлоратора (для возбуждения реакции). Разогревание производят сжиганием части метана в смеси с воздухом, с последующей заменой воздуха хлором. В дальнейшем реакция идет автотермично. Продукты хлорирования отводятся из верхней части аппарата, затем из газовой смеси в кислотных абсорберах улавливается водой хлороводород (получается соляная кислота), газовая смесь нейтрализуется щелочью, высушивается вымораживанием, сжимается и сжижается методом глубокого охлаждения. Из жидкой смеси, содержащей хлористого метила 28—32%, хлористого метилена 50—53%, хлороформа 12—14% и тетрахлорида углерода 3—5% при помощи ректификации выделяют индивидуальные продукты.
Все хлорзамещенные метана находят широкое применение. Так, хлористый метил СН3С1 используют как растворитель в производстве бутилкаучука, в качестве метилирующего вещества в органическом синтезе, для получения метилхлорсиланов, которые служат исходным сырьем в производстве кремнийорганических полимеров — силиконов. Хлористый метилен СН2С12 является ценным промышленным растворителем ацетилцеллюлозы, жиров, масел, парафина, каучуков; он не горюч и не образует взрывчатых смесей с воздухом.
ХЛОРИРОВАНИЕ БЕНЗОЛА
Хлорированием бензола получают монохлорбензол или другие хлорпроизводные в зависимости от условий хлорирования. Так, при 310—330 К и молярном отношении бензола и хлора 1:0,6 на железном катализаторе образуется монохлорбензол; при более низком соотношении и катализаторе А1С13 получается в основном о-дихлорбензол (используется в синтезе красителей и средств борьбы с сельскохозяйственными вредителями); при той же температуре в условиях ультрафиолетового облучения получают гексахлорциклогексан. На рис. 5 дана схема получения хлорбензола с отводом теплоты экзотермической реакции за счет испарения избыточного бензола.
Хлорирование проводят в стальном цилиндрическом аппарате,
|
ПРОБЛЕМА ИСПОЛЬЗОВАНИЯ ХЛОРОВОДОРОДА, ОБРАЗУЮЩЕГОСЯ В ПРОЦЕССАХ ХЛОРИРОВАНИЯ УГЛЕВОДОРОДОВ
Хлороводород является отходом хлорирования парафиновых и ароматических углеводородов нефтепереработки, широко применяемого в промышленном органическом синтезе. Утилизация представляет собой актуальную задачу, связанную с удешевлением продуктов хлорирования, улучшением санитарных условий, борьбой с коррозией металлов.
Часть хлороводорода используется для производства соляной кислоты путем противоточной абсорбции НС1 водой. Однако местные потребности в соляной кислоте обычно много меньше, чем возможности ее производства из хлороводорода. Транспорт соляной кислоты на дальние расстояния затруднен ввиду ее большой коррозионной способности.
Перспективным путем утилизации НС1 является метод окислительного хлорирования. Этим методом в современной промышленности синтезируют из этилена винилхлорид: в реакторе окислительного хлорирования этилен превращается в 1,2-дихлорэтан, каталитическим разложением которого получают хлористый винил; образующийся при этом НС1 вновь направляют в реактор:
2СН2 = СН2 + 4НС1 + О2 ® 2СН2С1—СН2С1 + 2Н2О, ΔН = –238 кДж/моль СН2С1—СН2С1 ® СН2 = CHCI + НС1.
Процесс окислительного хлорирования идет при 530—570 К в присутствии катализатора (хлорная медь на инертном носителе); пиролиз дихлорэтана проводят при 770 К на пористом катализаторе (пемза).
|

На рис. 6 показана упрощенная схема синтеза винилхлорида из этилена. В смесителе 1 этилен, рециркулирующий газ и хлороводород смешиваются с кислородом и поступают в реактор 2 с псевдоожиженным катализатором; пары образовавшегося дихлорэтана и непрореагировавшие этилен, кислород и НС1 охлаждаются в холодильнике непосредственного смешения 3 смесью воды и дихлорэтана, поступающих из холодильника 4. Затем газопаровая смесь проходит горячий щелочной скруббер 5, в котором очищается от НCl и СО2, охлаждается в холодильнике и, проходя газоотделитель 6, отделяется от газов — смеси этилена и кислорода, которые возвращаются в реактор (рециркулирующий газ). Дихлорэтан в сепараторе 7 отделяется от воды, поступает в осушительную колонну 8, где с помощью азеотропной перегонки окончательно обезвоживается и подается в ректификационную колонну 9; дихлорэтан собирается в сборнике 10. Последующий пиролиз дихлорэтана с получением винилхлорида происходит в трубчатой печи 11; реакционная смесь из печи поступает в холодильник непосредственного смешения, охлаждается циркулирующим охлажденным дихлорэтаном и, пройдя холодильник 4, поступает в ректификационную колонну 12, где отделяется НС1, который возвращается в реактор окислительного хлорирования, а винил-хлорид и непревращенный дихлорэтан разделяются в ректификационной колонне 13; дихлорэтан возвращается в колонну 9, а винилхлорид поступает на полимеризацию.
Значительный интерес для утилизации представляет комбинирование предприятий на базе газов нефтепереработки, в частности совместная переработка этилена и ацетилена и винилхлорид; хлороводород, образующийся при получении винилхлорида из этилена, используют для гидрохлорирования ацетилена:
СН2=СН2 + С12® СН2С1—СН2С1(пиролиз)® СН2 = СНС1 + HCI
СНºСН + НС1 ® СН2 = СНС1
Экономичным способом утилизации хлороводорода является комбинирование хлорирования метана с окислительным хлорированием в целях получения хлорзамещенных метана:
СН4 + 4С12 ® CCI4 + 4HCI
СН4 + 4НС1 + О2 ® СС!4 + 2Н2О
В этом процессе кроме тетрахлорида углерода получают метиленхлорид и хлороформ. Тетрахлорид углерода применяют как растворитель, в сельском хозяйстве (фумигант), для тушения пожаров и др. Хлороформ — ценный промежуточный продукт в синтезе фенолов, фторопластов и др.
Окислительным хлорированием получают также хлорбензол из парогазовой смеси бензола, хлороводорода и воздуха (кислорода) при 500 К на смешанном катализаторе (А12О3—СuС12— FeCl3):
С6Н6 + НС1 + 1/2О2 ® С6Н5С1 + Н2О
Для утилизации хлороводорода можно применять электрохимическое окисление его в хлор.
Предложен хромцезиевый катализатор и способ применения его для окисления хлороводорода до хлора, т. е. регенерации хлора из отходящих газов хлорирования органических соединений.
ПРОИЗВОДСТВО АЦЕТИЛЕНА И ЕГО ПЕРЕРАБОТКА
Производство ацетилена разложением карбида кальция осуществляют в ацетиленовых генераторах мокрым и сухим способами по уравнению реакции:
СаС2 + 2Н2О ® С2Н2 + Са (ОН)2 ΔH= –127 кДж.
При мокром способе в генераторах, работающих по принципу «карбид в воду», дробленый карбид кальция равномерно подается в генератор, содержащий большое количество воды, за счет нагревания которой и отводится выделяющаяся в ходе процесса теплота. Применяемая по этой схеме аппаратура и особенно коммуникации для удаления образующегося шлама и циркуляция воды очень громоздки. Кроме того, большие затруднения вызывают транспортировка и использование жидкого известкового молока, содержащего до 70% воды.
Разработаны также эффективные промышленные способы получения ацетилена из углеводородов. Ацетилен из парафинов образуется по следующим обратимым эндотермическим реакциям:
2СН4 D С2Н2 + Н2 ΔН = 376 кДж
С2Н6 D С2Н2 + 2Н2 ΔН = 311 кДж
С3Н8 D С2Н2 + СН4 + Н2 ΔН = 255 кДж
СН4 D С + 2Н2 ΔН = 88 кДж
Реакция (г) является побочной.
Равновесие реакций при увеличении температуры смещается в сторону образования ацетилена. Высокая степень равновесной конверсии для метана достигается при Т>1670 К, для этана — 1170 К. Но при температурах >1680 К ацетилен и углеводороды становятся неустойчивыми и разлагаются на сажу и углерод.
Реакция превращения метана в ацетилен при принятых в производстве температурах 1670—1770 К идет быстрее реакции распада ацетилена на элементы, поэтому продукты реакции быстро охлаждают, что позволяет предупредить разложение ацетилена, с этой же целью применяют высокие объемные скорости газа, при которых сырье должно находиться в реакционной зоне только тысячные доли секунды.
По способу подвода теплоты для осуществления экзотермической реакции образования ацетилена различают следующие методы проведения процесса: 1) электрокрекинг газообразных углеводородов или жидких продуктов; 2) гомогенный пиролиз; 3) термоокислительный пиролиз.
Электрокрекингпроводится при помощи вольтовой дуги в электродуговых печах постоянного тока.
Гомогенный пиролиззаключается в разложении сырья в потоке горячих топочных газов при температуре около 2200 К.
В термоокислительном пиролизе необходимая теплоиа получается за счет сжигания части метана.
Основными недостатками карбидного метода получения ацетилена являются большой расход электроэнергии при производстве карбида кальция и значительное количество потребляемого сырья (известняка и кокса), перерабатываемого в несколько стадий. В то же время при карбидном способе получается концентрированный ацетилен, очистка которого от небольших примесей не вызывает затруднений.
В методах термического расщепления углеводородов используется меньшее количество сырья, которое превращается в ацетилен в одну стадию, но ацетилен получается разбавленным и требуется сложная система его очистки и концентрирования. Необходимо отметить, что карбидный способ дает около 70% мирового производства ацетилена.
Существуют следующие основные методы первичной переработки ацетилена.
Гидратация:
а) с получением ацетальдегида и уксусной кислоты (катализатор(HgSO4):
б) с получением ацетона (катализатор ZnO на активированном угле)
2СН = СН + 3Н2О ® СН3СОСН3 + СО2 + 2Н2
Полимеризацияв линейные и циклические вещества для получения мономеров синтетического каучука и волокон.
Хлорированиес получением растворителей и мономеров.
Винилирование ацетиленомразличных веществ с получением мономеров:
+ ROH ® ROCH=CH2
+ RCOOH ® RCOOCH=CH2
+ HCN ® CH2=CHCN
<== предыдущая лекция | | | следующая лекция ==> |
СИНТЕЗ МЕТИЛОВОГО СПИРТА | | | Химико-технологический процесс |
Дата добавления: 2016-01-20; просмотров: 1783;