Теплообменная аппаратура
Применяемая в промышленности теплоо6менная аппаратура разнообразна как по своему функциональному назначению, так и по конструктивному исполнению. В теплообменных аппаратах могут происходить различные тепловые процессы: нагревание, охлаждение, испарение, конденсация, кипение и др.
Учитывая большой диапазон температур и давлений рабочих сред, а также разнообразие свойств теплоносителей при различных параметрах тепловой обработки, к основным требованиям, которым должны удовлетворять современные теплоо6менные аппараты, относятся следующие:
· аппарат должен обеспечивать передачу требуемого количества теплоты от одной среды к другой с получением необходимых конечных температур и при возможно большей интенсивности теплообмена;
· при заданной тепловой нагрузке и других рабочих параметрах аппарат должен иметь меньшие габаритные размеры и низкую удельную материалоемкость;
· аппарат должен работать стабильно при изменении в процессе теплообмена физических (а возможно и химических) свойств рабочей среды (вязкость, плотность, теплопроводность, фазовое состояние и др.);
· поверхность теплообмена и другие элементы конструкции аппарата, омываемые рабочей средой, должны обладать высокой химической стойкостью;
· при обработке загрязненной среды или среды, образующей отложения на стенках, в конструкции аппарата должна быть предусмотрена возможность периодической очистки поверхностей теплообмена;
· аппарат должен обладать запасом прочности, гарантирующим его безопасное состояние при напряжениях, возникающих в результате давления рабочей среды и температурных деформаций;
· при заданных термодинамических параметрах рабочих сред (давление, температура, объем) аппарат должен быть работоспособным и надежным.
Теплообменные аппараты по принципу действия разделяют на поверхностные (рекуперативные), регенеративные и смесительные.
Поверхностные (рекуперативные) теплообменники бывают с трубчатой поверхностью теплообмена – кожухотрубные (кожухотрубчатые), погружные змеевиковые, типа «труба в трубе», оросительные; с плоской поверхностью теплообмена – пластинчатые, спиральные, с оребренной поверхностью теплообмена; с поверхностью теплообмена, образованной стенками аппарата; блочные; шнековые.
Регенеративные теплообменники можно разделить на теплообменники c неподвижной и движущейся насадкой.
Смесительные теплообменники подразделяют на градирни, конденсаторы смешения, аппараты с барботажем газа, аппараты с погружными горелками.
Поверхностные теплообменные аппараты представляют собой теплообменные устройства, в которых теплоносители разделены стенкой различной конфигурации, через которую передается тепловой поток.
Наибольшее распространение среди аппаратов этого типа получили кожухотрубные теплообменники. Они предназначены для работы с теплоносителями жидкость – жидкость, пар – жидкость, газ – жидкость, газ – газ и представляют собой аппараты, выполненные из рядов труб 1, собранных при помощи решеток в пучок и заключенных в кожух 2 (рис. 6.1). Концы труб для обеспечения плотности их соединения с трубными решетками (досками) развальцовывают, припаивают или приваривают к трубным решеткам, либо закрепляют с помощью сальниковых соединений и т.д. (рис. 6.2).
В стандартных кожухотрубных теплообменниках обычно применяют трубы с внутренним диаметром не менее 12 мм (для удобства чистки поверхностей) и не более 38 мм, так как дальнейшее увеличение диаметра труб снижает его компактность и увеличивает материалоемкость. Длина трубного пучка колеблется от 0,9 до 5...6 м. Толщина стенок труб – 0,5...2,5 мм. Поверхность теплообмена в них может достигать 2000 м2.
В теплообменнике (рис. 6.1, а) теплоносители, текущие внутри трубок 1 и по межтрубному пространству, проходят их за один проход. Такие конструкции называют одноходовыми. В одноходовых теплообменниках скорость движения потоков сравнительно невелика, поэтому они характеризуются пониженными коэффициентами теплопередачи.
Теплообменники жесткой конструкции применяют при незначительной разности температур теплоносителей (разность температур кожуха и трубок не должна превышать 40...50°С) во избежание разрушения в результате различного температурного расширения трубок 1 и кожуха 2.
При большей разности температур теплоносителей температурные напряжения необходимо компенсировать. Одним из способов компенсации является установка линзового компенсатора 3
на кожухе 2 (рис. 6.1, б). Линза компенсатора (торового профиля) может свариваться из двух полулинз. Полулнизы штампуются из шайбообразных заготовок. Наружный диаметр линзы обычно больше наружного диаметра кожуха на 250 мм. Линзы можно сваривать по 2, 3, 4, 5 и 6 штук подряд. Одна линза допускает растяжение или сжатие кожуха до 8 мм.
Теплообменники с линзовым компенсатором применяются при давлениях не выше 1,6 МПа. При более высоком давлении применяют линзу с большей толщиной стенки, что увеличивает ее жесткость и снижает компенсирующую способность. При давлении выше 1,6 МПа обычно применяют теплообменники с U-образными трубами 4 (рис. 6.1, в) и плавающей головкой 5 (рис. 6.1, г).
В кожухотрубных теплообменных аппаратах с плавающей головкой, или, как их иначе называют, с подвижной решеткой (см. рис. 6.1, г), трубчатый пучок со стороны плавающей головки не связан с корпусом и свободно меняет длину при изменении температуры труб. Это устраняет температурные напряжения в конструкции.
В теплоо6менных аппаратах с подвижной решеткой можно выполнять ремонт, замену трубного пучка, механическую чистку труб снаружи. Однако конструкция этих аппаратов относительно сложна, для их изготовления требуется большой расход металла на единицу поверхности теплообмена, при работе аппарата плавающая головка недоступна для осмотра.
В теплообменниках с U-образными трубами обеспечено свободное удлинение труб, что исключает возможность появления температурных напряжений вследствие разности температур труб и корпуса. Разность температур стенок труб по ходам не должна превышать 100°С. Преимущество конструкции с U-образными трубами – отсутствие разъемного соединения внутри корпуса. Такие аппараты успешно применяют при повышенных давлениях. При U-образной форме труб затруднена механическая чистка их внутренней и наружной поверхностей, поэтому, как правило, их применяют для теплообмена между чистыми средами.
Для увеличения скорости теплоносителя с целью повышения значения коэффициента теплоотдачи со стороны межтрубного пространства в нем часто устанавливают и сегментные 6, и кон‑
центрические 7 перегородки, которые удлиняют путь теплоносителя (рис. 6.1, д, е). При этом размеры и расстояние между перегородками выбирают так, чтобы скорость среды во всех сечениях была одинакова. Аналогично многоходовое движение теплоносителя по трубному пространству создается в результате разбивки труб на секции перегородками 8, установленными в крышке Й' днище теплообменника (рис. 6.1, ж).
Для кожухотру6ных теплообменников применяют, как правило, цельнотянутые трубы из сталей 10 или 20. При работе с агрессивными средами используют трубы из легированных и коррозионно-стойких сталей, меди, титана, алюминия, графита.
Наиболее распространено крепление труб в трубной решетке способом развальцовки (рис. 6.2, а, б), производимой путем пластической деформации конца трубы специальным инструментом – вальцовкой. При расширении трубы она плотно прижимается к внутренним стенкам отверстия в решетке.
При давлении сред внутри теплообменника более 0,6 МПа способ развальцовки, показанный на рис. 6.2, а, б, уже не может обеспечить герметичность соединения, поэтому используют другой способ (рис. 6.2, в). В этом случае на внутренних поверхностях отверстий в решетках делаются канавки глубиной 0,5...0,8 мм. Обычно делают две канавки, но при высоких давлениях их число увеличивают. Труба должна выступать из решетки на величину, равную толщине стенки трубы. При развальцовке материал трубы начинает течь, заполняя канавки решетки. Благодаря этому соединение оказывает максимальное сопротивление вырыву труб из решетки и становится более плотным (герметичным).
На прочность соединения влияет степень развальцовки, определяемая величиной расширения трубы в процессе крепления их в трубной решетке. Чем больше степень развальцовки, тем прочнее соединение трубы с решеткой. Однако эта зависимость справедлива до некоторого значения, выше которого прочность соединения падает. Более надежно соединение труб сваркой (рис. 6.2, г). Приварка труб к решетке используется при высоких давлениях (или температурах), а также в том случае, когда требуется повышенная герметичность соединения. Последнее условие обычно ставится, когда совершенно недопустимо соединение сред, текущих по трубам и межтрубному пространству, во избежание взрыва, пожара или порчи одного из продуктов.
Если требуется повышенная герметичность, трубы можно развальцевать и обварить. Обварка без развальцовки не рекомендуется, так как при этом возникают условия для щелевой коррозии, двусторонней коррозии сварного шва.
Пайка и заливка концов труб мягким припоем (рис. 6.2, д) используется при изготовлении медной аппаратуры. Реже, в связи с высокой трудоемкостью сборки, применяют крепление с сальни-
|
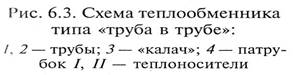
ковым соединением (рис. 6.2, е). Трубы из полимерных материалов и графита соединяются с трубными решетками с помощью склейки (рис. 6.2, ж).
Кожухотру6ные теплообменники имеют условные обозначения.
В зависимости от назначения: Т – теплообменники, Х - холодильники; К – конденсаторы, И – испарители.
По конструкции: Н - аппараты с неподвижными трубными решетками, К – с температурным компенсатором на кожухе, П – с плавающей головкой, У - с U-образными трубами.
Теплообменники типа «труба в трубе» (рис. 6.3) смонтированы из труб 1, каждая из которых установлена внутри трубы 2 большего диаметра. Одна среда I течет по внутренней трубе, другая – по кольцевому каналу. Внутренние трубы соединены последовательно «калачами» 3, наружные – патрубками 4.
|
Змеевиковый теплообменник (рис. 6.4) представляет собой изогнутую в виде спирали трубу (змеевик) 1, установленную изнутри сосуда 2. Одна из сред I
|
Змеевиковые теплообменники имеют обычно низкие коэффициенты теплопередачи, величина которых лимитируется значением наименьшего частного коэффициента теплоотдачи среды, омывающей змеевик снаружи. В этом случае их обычно снабжают мешалками, которые не только интенсифицируют технологический процесс, но и повышают общий коэффициент теплопередачи в результате увеличения скорости движения среды.
В ряде случаев емкостные аппараты обогреваются или охлаждаются через стенку 1, снабженную внешней рубашкой 2 (рис. 6.5). По самой конструкции рубашечного теплообменного аппарата скорость среды I внутри него невелика, поэтому коэффициент теплопередачи будет определяться именно этим малым коэффициентом теплоотдачи. Кроме того, они имеют небольшую поверхность нагрева на единицу объема аппарата. Рубашечные аппараты применяются главным образом для осуществления химичес‑
ких реакций, процессов кристаллизации, растворения, требующих нагрева или охлаждения в ходе их проведения.
Пластинчатые теплообменники (рис. 6.6, а) имеют щелевидные каналы в параллельно установленных пластинах 1. Пластины подвешиваются на направляющих балках (штангах) 2 между неподвижной 5 и подвижной 3 плитами. Последняя прижимает пластины друг к другу и герметизирует пространство между ними. В каждой пластине (рис. 6.6, б) и плитах просверлены совпадающие отверстия, образующие сплошные каналы: два – для подвода и отвода одной из теплообменивающихся сред I, два – для другой П. Первая среда, поступая через патру6ок 4 в плите 3 в один их этих каналов, направляется в каналы между чередующимися (через одну) нечетными пластинами и, перемещаясь по ним, выходит в отводящий канал. Вторая среда движется также по чередующимся четным каналам. Для создания жесткости, увеличения теплопередающей поверхности и турбулентности потока пластины снабжены штампованными выступами.
К достоинствам пластинчатого теплообменника относятся:
· большая удельная теплопередающая поверхность (200 м2/м3 и более), компактность и значительная экономия материала;
· большие значения коэффициентов теплоотдачи, а следовательно, и коэффициента теплопередачи благодаря использованию фасонной формы пластин;
·
|
· легкость разборки и сборки теплообменника, обеспечивающие возможность чистки теплопередающей поверхности.
Блочные теплообменники, показанные на рис. 6.7, выполнены из графитовых прямоугольных или цилиндрических блоков 8, имеющих проточные вертикальные 5 и горизонтальные 1 каналы для охлаждающего и нагревающего теплоносителя. Блоки
|

устанавливаются один на другом с прокладками 2 между ними.
По сторонам блоков имеются прокладки 3 и 7 перед распределительными крышками 4 и 6, которые прижимаются с помощью болтов. В качестве прокладок применяют теплостойкую резину, комбинированные прокладки из резины и фторопласта, а также фторопластовый уплотнительный материал (ФУМ), допускающие температуру агрессивной среды в пределах -18°...+150°С. Рабочее давление греющего пара – не более 0,3 МПа.
К преимуществам этих аппаратов относятся сравнительная простота изготовления и компактность, высокая теплопроводность материала (графита) и его коррозионная стойкость.
В шнековых теплообменниках (рис. 6.8) интенсификация теплообмена осуществляется путем непрерывного обновления поверхности нагреваемого или охлаждаемого материала (высоковязкие среды, суспензии, пасты и др.), который соприкасается со стенками аппарата. Обновление поверхности происходит в результате вращения винтообразных валов навстречу друг другу с одновременным перемешиванием и перемещением материала вдоль шнека.
Эти устройства предназначены в первую очередь для тепловой обработки высоковязких жидкостей и сыпучих материалов, обладающих низкой теплопроводностью.
Материал поступает через загрузочное отверстие в корпус 1,
теплообменника с рубашкой 2 и перемещается с помощью шнеков 3 и 4 к противоположному концу корпуса, т. е. к разгрузочному бункеру. При этом происходит тепловая обработка (нагревание или охлаждение) материала.
Иногда для увеличения поверхности теплообмена валы шнеков делают полыми и внутрь по всей длине шнека и в пустотелые витки также подают теплоноситель.
Шнековые теплообменники занимают мало места, высокоэффективны и могут быть приспособлены к различным производственным условиям путем объединения нескольких аппаратов в один агрегат. Однако шнековые теплообменники требуют затрат сравнительно большого количества энергии.
|
другому происходит с помощью теплоаккумулирующей массы, называемой насадкой. Различают регенеративные теплообменники с неподвижной и циркулирующей насадками.
В первом случае неподвижная насадка периодически омывается потоками горячего и холодного теплоносителей. В течение первого периода (периода нагревания насадки) через аппарат пропускают горячий теплоноситель, при этом отдаваемая им теплота расходуется на нагревание насадки. В течение второго периода (периода охлаждения насадки) через аппарат пропускают холодный теплоноситель, который нагревается за счет теплоты, аккумулированной насадкой.
Периоды нагревания и охлаждения насадки продолжаются от нескольких минут до нескольких часов.
Для осуществления непрерывного процесса теплопередачи от одного теплоносителя к другому необходимы два регенератора 1 и 3 с неподвижной насадкой, схема соединения и переключения которых приведена на рис. 6.9. В то время как в одном из них происходит охлаждение горячего теплоносителя, в другом нагревается холодный теплоноситель. Затем аппараты переключаются, после чего в каждом из них процесс теплопередачи протекает в обратном направлении. Переключение производится поворотом клапанов (шиберов) 2 и 4.
Регенеративный теплообменник с циркулирующей насадкой (рис. 6.10). В качестве насадки 2 используется зернистый материал, который непрерывно перемещается сверху вниз через два регенератора 1. В верхнем регенераторе насадка нагревается благодаря охлаждению горячей среды I, например топочных газов, а в нижнем - холодная среда II, например технологические газы, нагревается при соприкосновении с горячей насадкой. Охлажденная зернистая насадка непрерывно выводится из нижнего регенератора и передается в верхний обычно сжатым воздухом (пневматическим транспортом) по трубе 3.
В таких теплообменниках можно нагревать технологические газы до 1500 °С. Регенераторы и зернистая насадка должны быть жаростойкими.
|
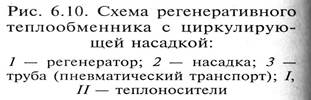
К недостаткам теплообменников этого типа следует отнести необходимость установки
пылеулавливающих устройств, герметизации охлаждаемого и нагреваемого газов и абразивное изнашивание трактов движения насадки.
Теплообменники смешения применяют в тех производствах, в которых нет необходимости получать чистые конденсаты и продукты нагрева для их последующего использования, они достаточно просты и относительно дешевы. По конструктивным признакам различают следующие типы теплообменников смешения:
· полые колонны, в которых жидкость распыливается форсунками в газовую среду;
· насадочные колонны, в которых смешение газа с жидкостью происходит на смоченной поверхности насадки;
· каскадные аппараты, имеющие внутри горизонтальные или к наклонные перегородки, по которым стекает жидкость;
· струйные аппараты, где нагревание воды происходит эжектируемым и инжектирующим паром;
· пленочные подогреватели, в которых вода нагревается водяным паром почти до температуры насыщения пара;
· пленочные аппараты, используемые для улавливания из газов плохо смачиваемой (гидрофобной) пыли.
Конденсаторы смешения применяют для создания вакуума в различных аппаратах путем конденсации отсасываемых из них паров. Для отвода теплоты конденсации паров служит холодная вода, которая, смешиваясь с конденсатом, сливается в канализацию.
Полочный барометрический конденсатор (рис. 6.11) работает при противоточном движении охлаждающей воды и пара. В цилиндрический корпус 1 с сегментными полками 2 снизу через штуцер 6 поступает пар. Вода подается через штуцер 7 и перетекает по полкам, имеющим невысокие борта. При соприкосновении с водой пар конденсируется.
Смесь конденсата и воды сливается самотеком через штуцер 3 в барометрическую трубу 4 и далее – в барометрический ящик 5. Поскольку остаточное давление в конденсаторе поддерживается в пределах (1...2)*104 Па за счет постоянного отсасывания неконденсируемых газов через штуцер 8, барометрические труба и ящик играют роль гидравлического затвора, препятствующего прониканию наружного воздуха в аппарат.
Высота барометрической трубы (Нтр, м) определяется равенством
где hз – высота столба (затвор) воды в барометрической трубе, уравновешивающего разность давлений в конденсаторе и атмосферного; hдин – высота столба воды в барометрической трубе, создающего динамический напор, который обеспечивает движение жидкости по трубе; 0,5 м – запасная высота, предотвращающая заливание водой штуцера, для ввода пара при колебаниях атмосферного давления.
|
где b — разрежение в конденсаторе, Па;
где w – скорость жидкости в барометрической трубе, которую принимают равной 1...2 м/с; λ – коэффициент трения при дви‑
жении жидкости по барометрической трубе; dтр - диаметр барометрической трубы, м.
Диаметр барометрической трубы определяется из уравнения расхода
где D – количество конденсирующегося в аппарате пара, кг/с; W – расход воды, кг/с; ρв – плотность воды, кг/м3.
В барометрических конденсаторах иногда вместо сегментных полок 2 (рис. 6.11, а) применяются полки, представляющие собой чередующиеся круглые диски и кольца (рис. 6.11, б), а также ситчатые сегментные полки. Через отверстия последних вода стекаем каплями, вследствие чего увеличивается поверхность ее соприкосновения с паром.
Прямоточные конденсаторы (рис. 6.12) применяются в установках с умеренной производительностью. Вода засасывается в аппарат под действием созданного в нем разрежения и впрыскивается в корпус 2 через сопло 1. Пары поступают в конденсатор сверху через патру6ок 5. Охлаждающая вода и конденсат удаляются центробежным насосом 3, а воздух отсасывается воздушным насосом 4.
Такие конденсаторы значительно компактнее противоточных барометрических. Однако основной недостаток противоточных аппаратов (большая высота) компенсируется в прямоточных конденсаторах меньшим расходом охлаждающей воды и меньшим объемом отсасываемого воздуха, а также более простым и дешевым способом отвода удаляемой воды.
Насадочные аппараты (рис. 6.13) применяются для конденсации паров и охлаждения газов какой-либо жидкостью. Охлаждающая вода подается через раз6рызгиватель 3 в верхней части корпуса 1 аппарата. Далее она растекается по насадке 2, при этом поверхность воды значительно увеличивается. Пар движется противотоком к воде. Вода и конденсат выводятся из нижней части аппарата, а воздух отсасывается из верхней части.
Теплообменные аппараты с погружными горелками (рис. 6.14). В этих аппаратах продукты сгорания непосредственно соприкасаются с нагреваемой жидкостью.
В горелку 3, опущенную в жидкость, находящуюся в корпусе 1, подаются газ и воздух для горения. При барботаже образующихся продуктов сгорания через решетку 2 происходит равномерное диспергирование потока газа на мелкие пузырьки, которые, всплывая, отдают свою теплоту жидкости и одновременно насыщаются парами воды. Благодаря этому значительно повышается интенсивность теплоотдачи.
При непосредственном контакте продуктов сгорания с жидкой средой теплообмен протекает с малыми потерями. Коэффициент использования теплоты сгорания топлива в погружной горелке при испарении жидкостей достигает 95...96%.
Наиболее часто аппараты с погружными горелками применяются в выпарных установках для выпаривания коррозионно-активных жидкостей.
Дата добавления: 2015-08-14; просмотров: 3325;