Хрупкое разрушение инструмента, пластическое течение и пластическая деформация режущего клина инструмента
В процессе резания может происходить хрупкое разрушение режущего инструмента, протекающее в виде выкрашивания режущих кромок и сколов режущей части режущего инструмента.
Выкрашивание представляет собой отделение мелких частиц материала режущей кромки, вызванное наличием на ней различного рода дефектов (микротрещин, микросколов и т.д.).
Сколы представляют собой отделение значительных объемов материала режущей части режущего инструмента, связанное со свойствами обрабатываемого и инструментального материала и толщиной срезаемого слоя.
При высоких температурах (900º-1200º для твердосплавного режущего инструмента) в поверхностных слоях режущего инструмента может происходить пластическое течение материала инструмента, оно сопровождается вырывом отдельных твердых включений инструментального материала и пропахиванием ими контактных площадок режущего инструмента, а также «намазыванием» инструментального материала на прирезцовые слои стружки.
При высоких температурах и удельных нагрузках может произойти пластическая деформация режущего клина (рис.81), которая сопровождается опусканием вершины режущего клина на величину hg, выпучиванием материала инструмента по передней и задней поверхности, что вызывает изменение геометрии режущего клина (задний угол становится равным нулю a=0, а передний угол g - отрицательным) и интенсифицирует износ режущего инструмента.
|
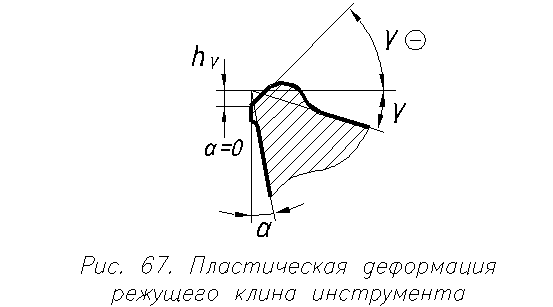
Развитие очагов износа на контактных площадках
режущего инструмента
В зависимости от условий резания износ режущего инструмента может происходить: преимущественно по задней поверхности; преимущественно по передней поверхности; равномерно протекать как по передней , так и по задней поверхности.
|
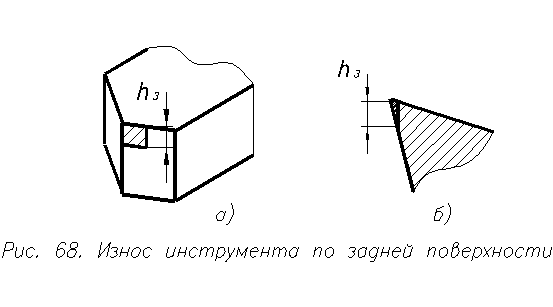
Износ режущего инструмента преимущественно по задней поверхности (рис.82) происходит при работе с малыми толщинами срезаемого слоя (а<0,1 мм), особенно при обработке хрупких материалов. На задней поверхности инструмента образуется фаска износа h3. Очертания фаски износа в главной секущей плоскости (рис.82,б) приблизительно копируют форму поверхности резания на заготовке.
Износ режущего инструмента преимущественно по передней поверхности происходит при работе с большими толщинами срезаемого слоя (а>0,4 мм) на высоких скоростях резания, когда тепловой источник на передней поверхности значительно превышает тепловой источник на задней поверхности. Под действием сходящей стружки на передней поверхности образуется лунка износа шириной bл и глубиной hл (рис.83). Края лунки располагаются приблизительно параллельно главной режущей кромки инструмента, а длина лунки равна рабочей длине режущей кромки.
Равномерный износ инструмента происходит при его работе с толщинами срезаемого слоя 0,1<=a<=0,4мм. Особенно при обработке материалов, подвергающихся упрочнению.
Рассмотрим схемы износа твердосплавного и быстрорежущего инструмента (рис.84). Как видно из рис.84, а, для инструмента из быстрорежущей стали между краем лунки и режущей кромкой имеется перемычка С. Наличие перемычки связано с наростом, предохраняющим часть передней поверхности от износа. По мере увеличения времени работы инструмента размер перемычки уменьшается и в какой-то момент времени прочность ее становится недостаточной и она «прорывается», что сопровождается резким увеличением износа инструмента по задней поверхности. Зависимость величины фаски износа быстрорежущего инструмента hз от времени его работы τ представлена на рис.84, в. На данной зависимости можно выделить три участка: участок интенсивного износа или участок приработки – участок № 1, участок нормального износа – участок № 2 и участок катастрофического износа – участок № 3, вызванный «прорывом» перемычки.
|
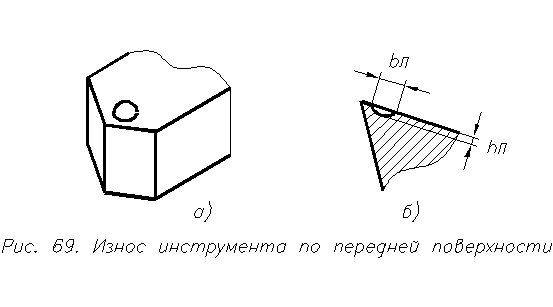
|
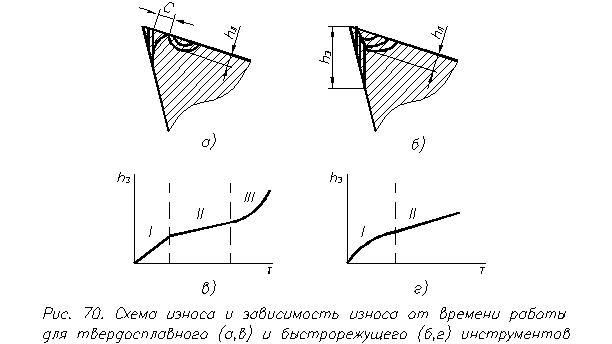
Твердосплавные инструменты работают на скоростях резания, при которых нарост не образуется. Поэтому при его износе край лунки сливается с режущей кромкой и перемычка отсутствует. При этом по мере работы инструмента происходит опускание вершины режущего клина инструмента (рис.84,б). На кривой зависимости величины износа по задней поверхности от времени работы инструмента имеется только два участка – участок приработки и участок нормального износа (рис.84,г).
Критерии износа режущего инструмента
Выбрать критерий износа режущего инструмента – это значит определить время, когда его необходимо отдать на переточку. Используют два основных критерия износа: критерий оптимального износа и критерий технологического износа. В обоих критериях за основу принимают износ по задней поверхности, так как задняя поверхность инструмента изнашивается при любых условиях резания и измерение фаски износа hз значительно проще, чем глубины лунки износа по передней поверхности.
Критерий оптимального износа. Инструмент считается затупленным, когда величина износа по задней поверхности достигает значения, равного оптимальному износу. Под оптимальным износом понимается такой, при котором полный период стойкости режущего инструмента получается максимальным. Для определения оптимального износа строится зависимость полного периода стойкости ∑Т от изменения величины фаски износа (рис.85). Величина фаски износа по задней поверхности, при которой полный период стойкости будет максимален, и будет оптимальным износом.
|
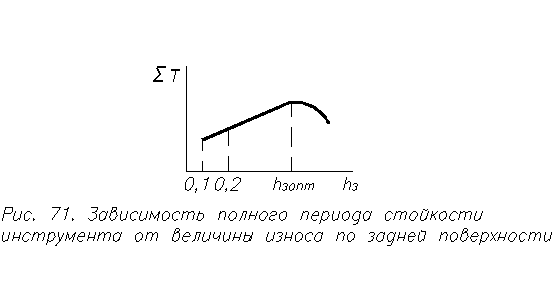
Критерий технологического износа. Данный критерий используется для режущего инструмента, предназначенного для чистовой (окончательной) обработки. Режущий инструмент считается затупленным, когда обработанная поверхность заготовки перестает отвечать технологическим требованиям, заданным на ее изготовление. К ним относятся требования по шероховатости и точности. Для определения величины износа по задней поверхности, соответствующего критерию технологического износа, строится зависимость параметра шероховатости обработанной поверхности Rа от времени работы инструмента (рис.86). При этом задаются величиной Rа , при превышении значения которой, инструмент отдают на переточку (например, по рис.86 при величине Rа, равной 3,2 мкм). Величина фаски износа по задней поверхности, соответствующая времени работы инструмента до заданного
параметра шероховатости, и будет соответствовать критерию технологического износа.
|
Влияние различных факторов на износ и стойкость
режущего инструмента
Все факторы, действующие в сторону увеличения температуры резания, увеличивают износ инструмента и снижают период стойкости режущего инструмента.
Для инструмента из быстрорежущей стали повышение скорости резания вызывает монотонное снижение периода стойкости (рис.87,а, кривая 2). Это объясняется тем, что увеличение скорости резания ведет к росту интенсивности износа (рис.87, б, кривая 2).
Для инструмента из твердого сплава зависимость между скоростью резания и периодом стойкости имеет более сложный характер (рис.87,а, кривая 1). Период стойкости с увеличением скорости резания сначала уменьшается, затем увеличивается и вновь снижается. Наличие перегибов на данной зависимости связано с изменением интенсивности адгезионного износа (минимум периода стойкости на кривой Т = f (V)) и переходом адгезионного износа в диффузионный (максимум периода стойкости на кривой Т = f (V)).
Увеличение подачи и глубины резания (рис.88,а) повышает силы резания и количество образующейся теплоты, что ведет к росту температуры резания, увеличению износа инструмента и уменьшению его периода стойкости.
Из геометрических параметров на износ и стойкость режущего инструмента влияют передний угол, главный задний угол и главный угол в плане. Увеличение переднего угла снижает силы резания, количество теплоты и температуру резания. В результате износ инструмента снижается, а период стойкости возрастает. При дальнейшем росте угла γ массивность режущего клина снижается, что ведет к росту температуры резания, увеличению износа и снижению периода стойкости инструмента (рис.88,б). Влияние главного заднего угла α на величину износа и период стойкости инструмента аналогично влиянию переднего угла.
![]() |
Увеличение главного угла в плане φ вызывает рост температуры резания. Это в свою очередь увеличивает износ инструмента и снижает его период стойкости (рис.89,а).
Рис.89 Влияние главного угла в плане φ (а) и инструментального материала (б)
на период стойкости инструмента
Влияние инструментального материала на период стойкости инструмента проявляется через его фрикционные и теплофизические свойства. Так, например, нанесение износостойких покрытий приводит к снижению коэффициента трения на передней поверхности, что вызывает уменьшение источника теплоты трения на передней поверхности и в конечном итоге увеличивает период стойкости инструмента (рис.89,б: кривая 1 – инструмент с покрытием, кривая 2 – инструмент без покрытия).
Дата добавления: 2015-08-14; просмотров: 1034;