ПАРОВЫЕ КОТЛЫ
УСТРОЙСТВО ПАРОВЫХ И ВОДОГРЕЙНЫХ КОТЛОВ
ПАРОВЫЕ КОТЛЫ
Котлом называют устройство, в котором для получения пара или нагрева воды с давлением выше атмосферного используют теплоту, выделяющуюся при сгорании органического топлива.
Горение органического топлива (преобразование его химической энергии в тепловую) происходит в топочной камере котла. При этом носителем выделяющейся теплоты являются газообразные продукты сгорания — топочные газы. Поэтому конструктивно котлы представляют собой устройства для передачи теплоты от движущихся топочных газов к рабочему телу — пару или воде.
Передача теплоты от продуктов сгорания к рабочему телу происходит в системе трубчатых теплообменников, называемых поверхностями нагрева. Как правило, теплоноситель омывает трубки теплообменников снаружи, а рабочая среда движется внутри трубок.
Конструкции паровых котлов разнообразны, однако в основу их работы положен принцип непрерывного отвода теплоты от топочных газов. Для того чтобы непрерывно отводить теплоту от теплоносителя, необходимо организовать непрерывное движение рабочего тела. Известно, что для получения пара воду необходимо сначала подогреть до кипения, испарить, а образовавшийся пар перегреть. Подогрев воды до ~220°С происходит в теплообменнике, который называется экономайзером, кипение воды (образование пара) — в испарительной части нагрева, а перегрев пара — в пароперегревателе.
Движение рабочего тела в экономайзере и пароперегревателе происходит во всех конструкциях котлов одинаково: через экономайзер вода прокачивается насосом, а движение пара через пароперегреватель происходит из-за разности давлений между ним и конденсатором турбины. В трубах испарительных поверхностей нагрева различных котлов движение кипящей воды организовано по-разному. В зависимости от этого котлы бывают с естественной и принудительной циркуляцией, а также прямоточные.
Рассмотрим, как создается движение рабочей среды в котле с естественной циркуляцией (рис. 1, а). Система, состоящая из обогреваемых 5 и необогреваемых 2 труб, объединенных вверху барабаном 3, а внизу коллектором 1, представляет собой замкнутый контур, который принято называть циркуляционным. Этот контур заполняют водой до уровня, расположенного на 150—200 мм ниже диаметральной плоскости барабана. Объем барабана, заполненный водой, называют водяным, а занятый паром, — паровым. Поверхность, разделяющую водяной и паровой объемы, называют зеркалом испарения, а воду, находящуюся в циркуляционном контуре,— котловой.
Рисунок 1.
При подводе теплоты к обогреваемым трубам 5 вода в них закипает, поэтому во время работы они заполнены пароводяной смесью, а необогреваемые трубы 2 — некипящей водой, плотность которой больше плотности пароводяной смеси
Следовательно нижняя точка контура (коллектор) со стороны необогреваемых труб подвержена давлению столба воды, а со стороны обогреваемых труб—давлению столба пароводяной смеси. Разность давлений, возникающая в циркуляционном контуре в результате образования пара при подводе теплоты к обогреваемым (парообразующим) трубам, вызывает движение в нем и называется движущим напором естественной циркуляции.
Таким образом, в рассматриваемом котле движение рабочего тела в парообразующих трубах создается под действием движущего напора циркуляции, который возникает естественно, поэтому такие котлы называют котлами с естественной циркуляцией.
В обогреваемых трубах 5 пароводяная смесь движется вверх и, поступив в барабан, разделяется на воду и пар. Из барабана пар направляется в пароперегреватель 4, где перегревается до заданной температуры, а затем — к паровой турбине.
Взамен пара, отведенного из циркуляционного контура, в него непрерывно поступает вода, которая вводится в барабан через экономайзер 6 под действием напора, развиваемого питательным насосом 5. Количество поступающей воды должно быть равно количеству пара, отведенного из циркуляционного контура.
Особенностью котлов такого типа является то, что поступившая вода полностью превращается в пар лишь после многократного прохождения ее через циркуляционный контур. Как правило, в современных котлах количество воды, превращающейся в пар при однократном прохождении через циркуляционный контур, составляет 3—20%. Следовательно, для полного испарения воды, поступившей в контур, ей необходимо совершить многократное движение через него. Например, если за один цикл движения испаряется 20% воды, полное ее превращение в пар произойдет лишь через пять циклов.
Таким образом, количество движущейся в циркуляционном контуре воды в несколько раз больше количества образующегося пара. Отношение расхода циркулирующей воды к количеству образовавшегося в единицу времени пара называется кратностью циркуляции. В котлах с естественной циркуляцией кратность циркуляции лежит в пределах 5—30 и выше.
Движущий напор тем больше, чем выше циркуляционный контур. В котлах с естественной циркуляцией движущий напор обычно не превышает 0,1 МПа (1 кгс/см2). Этого достаточно, чтобы возникло и существовало движение в циркуляционном контуре, парообразующие трубы которого расположены вертикально. Однако иногда парообразующие трубы приходится располагать не только с подъемным движением пароводяной смеси, но и с горизонтальным и даже опускным. При этом гидравлическое сопротивление контура возрастает настолько, что естественного движущего напора циркуляции оказывается недостаточно для движения рабочего тела. Подобные условия возникают, например, при конструировании котлов для судов, размеры которых не позволяют сооружать котлы большой высоты. В этом случае движение рабочего тела осуществляется принудительно, например насосом, который включается в контур циркуляции. Такие агрегаты называют котлами с многократной принудительной циркуляцией (рис. 1, б); кратность циркуляции при этом лежит в пределax 3-10.
Характерной особенностью рассмотренных котлов с естественной и многократной принудительной циркуляцией является наличие барабана (емкости), который позволяет разделить поступающую пароводяную смесь на пар и воду и обеспечивает поступление в необогреваемые (опускные) трубы только воды, плотность которой всегда больше плотности пароводяной смеси. Однако при давлении, равном критическому и выше него, разделение на пар и воду невозможно. Поэтому котлы с барабанами могут работать лишь при давлении, меньшем критического. Обычно давление, при котором работают барабанные котлы, не превышает 16 МПа (160 кгс/см2).
Пар закритических параметров получают в котлах, не имеющих барабана (рис. 1, в). В таких котлах вода проходит через парообразующие трубы однократно и полностью превращается в пар.
Другими словами, количество воды, проходящей через контур (в данном случае контур разомкнут), равно количеству пара, которое в нем образуется, т. е. кратность циркуляции равна единице. Котлы, работающие по такому принципу, получили название прямоточных. В этом случае движение рабочей среды осуществляется под действием напора питательного насоса. Следует отметить, что в этих котлах можно получать не только пар закритических, но и докритических параметров.
Наибольшее распространение получили котлы с естественной циркуляцией и прямоточные. Технологическая схема прямоточного котла показана на рис. 2.
|

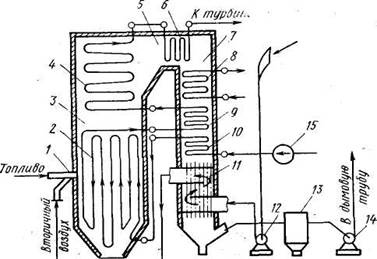
Рис. 2. Технологическая схема прямоточного котла:
1 - горелка, 2 - топочный экран, 3 - топочная камера, 4, 6, 8 - радиационный, конвективный и промежуточный пароперегреватели, 6, 7 - горизонтальный и вертикальный опускной газоходы, 9 - переходная зона, 10- водяной экономайзер, 11 - воздухо- подогреватель, 12 - дутьевой вентилятор, 13 - золоуловитель, 14 - дымосос, 16 - питательный насос.
Подавляющее большинство конструкций котлов отечественного производства, как прямоточных, так и барабанных, имеет П-образный профиль, который образуется двумя вертикальными шахтами прямоугольного сечения, соединяющимися в верхней части горизонтальной шахтой такого же сечения. Первая шахта представляет собой топочную камеру 3, стены которой внутри покрыты огнеупорным материалом, а снаружи — тепловой изоляцией. Внутри непосредственно у стен по всему периметру топочной камеры расположены трубы, которые часто являются парогенерирующими поверхностями нагрева, получают теплоту от топочных газов (теплоносителя) прямым излучением и называются топочными экранами 2. Движение рабочей среды в трубах может быть подъемным, опускным или горизонтальным. Температура газов в топочной камере достигает 1600—1800° С.
Продукты сгорания топлива, отдав часть своей теплоты топочным экранам, имеют температуру 900—1200°С и поступают в горизонтальную шахту, называемую горизонтальным газоходом 5, а затем в следующую шахту — в вертикальный газоход 7. В этих газоходах теплота передается поверхностям нагрева конвекцией, отчего они получили название конвективных.
Питательная вода, из которой образуется пар, содержит примеси. По мере движения воды в экранных трубах количество пара в них увеличивается, а воды — уменьшается. Следовательно, концентрация примесей в воде в процессе парообразования постоянно нарастает и в конце зоны парообразования достигает предельных значений, при которых эти примеси выпадают из воды в виде твердой фазы, что приводит к образованию накипи на стенках труб. Появление накипи в парообразующих трубах — крайне нежелательное явление, так как низкая ее теплопроводность (в десятки раз меньше теплопроводности стали) снижает теплопередачу и приводит к перегреву стенок труб, что ухудшает прочностные свойства стали. Под воздействием большого внутреннего давления трубы могут разорваться.
Чтобы облегчить условия работы металла труб, часть поверхности нагрева, в которой выпадает накипь, иногда располагают не в топочной камере, а в конвективном газоходе, где интенсивность обогрева значительно слабее. В этой части поверхности, называемой переходной зоной 9, завершается парообразование, пар слегка перегревается (на 10—15° С) и поступает в радиационный пароперегреватель 4.
Окончательный перегрев пара до заданной температуры происходит в поверхности нагрева, которая расположена в конвективном газоходе иназывается конвективным пароперегревателем 6. Далее пар направляется в паровую турбину. Температура продуктов сгорания за конвективным пароперегревателем 550—650°С. Для повышения кпд электростанций частично отработавший в турбине пар подвергают промежуточному (вторичному) перегреву. В этом случае перед переходной зоной располагают так называемый промежуточный пароперегреватель 8.
После переходной зоны температура продуктов сгорания еще достаточно высока — 400—500°С. Содержащаяся в них теплота отбирается поверхностью нагрева, называемой экономайзером 10. В экономайзер под действием питательного насоса 15 поступает вода, которая подогревается до температуры, не превышающей температуру насыщения (вода не кипит), и далее направляется в топочные экраны.
Температура продуктов сгорания за экономайзером 300-4000.С. Дальнейшее ее снижение происходит в конвективной поверхности нагрева (воздухоподогревателе) 11,используемой для подогрева воздуха, подаваемого дутьевым вентилятором 12. После этого температура воздуха повышается от 30 до 250—420° С. Горячий воздух разделяется на два потока, один из которых (первичный) используют для подсушки топлива при размоле и транспортирования полученной пыли, а другой (вторичный) направляют непосредственно в топочную камеру через горелку 1 для обеспечения полного его сгорания.
![]() |
|

|
|
Горелка, 2 - необогреваемые опускные трубы, 3 - топочные экраны, 4 - топочная камера, 5 - барабан, 6, 10 - горизонтальный и опускной газоходы, 7, 8 - конвективный и промежуточный пароперегреватели, 9 - водяной экономайзер, 11 - воздухоподогреватель, 12 - дутьевой вентилятор, 13 - золоуловитель, 14 - дымосос, 15 - питательный насос, 16 - коллектор.
После сгорания топлива образуется зола, которая частично остается в топочной камере, откуда ее удаляют в твердом или жидком состоянии системой золоудаления. Основная же масса золы уносится с уходящими газами. Для очистки продуктов сгорания от уносимой ими золы служит золоуловитель 13. Уловленная зола отводится устройствами золоудаления.
Технологическая схема барабанного котла с естественной циркуляцией (рис. 3) отличается лишь конструкцией топочных экранов, представляющих собой системы вертикальных, параллельно включенных подъемных труб, нижние концы которых вварены в коллекторы 16, а верхние — в барабан 5. Движение рабочей среды в них только подъемное. В барабанном котле отсутствует переходная зона и образующаяся пароводяная смесь поступает в барабан, где происходит сепарация (разделение) пара от воды. Пар, выделившийся в барабане, направляется в пароперегреватель, а затем в турбину.
-----------------------------------------------------------------------------------------------------------------------1.1. Устройство котлоагрегатов с естественной циркуляцией
Принципиальная схема современного мощного котлоагрегата с естественной циркуляцией, работающего на угольной пыли, показана на рис. 1. Угольная пыль вдувается в топочную камеру вместе с необходимым для горения воздухом через горелки.
Мелкие частицы угля в топочной камере сгорают, образуя факел, в ядре которого температура достигает 1500–2000 °С.
Стены топочной камеры покрыты трубами, образующими радиационные поверхности нагрева (экраны). По ним циркулирует вода и пароводяная смесь, образующаяся под действием излучения факела. При этом продукты сгорания охлаждаются, на выходе из топочной камеры их температура обычно снижается до 1000–1200 °С.
Омывая разреженный пучок труб (фестон) или отдельные змеевики пароперегревателя (ширмы), дымовые газы передают им теплоту частично, конвекцией, частично радиацией и далее поступают в горизонтальный газоход, в котором располагаются змеевики, конвективного пароперегревателя. По змеевикам движется пар, который, отнимая теплоту от продуктов сгорания, перегревается до температуры 510–560 °С. Продукты сгорания, охлажденные в пароперегревателе до 500–600 °С, направляются в вертикальный опускной газоход, в котором расположены трубы водяного экономайзера. По трубам проходит питательная вода, которая нагревается и поступает в барабан котлоагрегата для пополнения испарившейся в экранах воды. Далее продукты сгорания поступают в воздухоподогреватель, где, проходя внутри трубок, подогревают воздух, подаваемый затем через
горелки в топку. Продукты сгорания охлаждаются в воздухоподогревателе до температуры 110–180 °С и поступают в золоуловитель, в котором отделяется летучая зола, а затем дымососом выбрасываются в атмосферу через дымовую трубу. Холодный воздух забирается дутьевым вентилятором вверху котельной и подается через воздухоподогреватель и воздухопроводы в топку.
К барабану присоединены многочисленные трубы экранов, по которым в него поступает пароводяная смесь. Пар в барабане отделяется от воды и поступает в пароперегреватель, а оставшаяся вода смешивается с подаваемой питательной водой и по опускным необогреваемым трубам, расположенным снаружи топочной камеры, поступает к нижним коллекторам экранов. Из коллекторов вода распределяется по трубам экрана и, поднимаясь по ним, частично испаряется за счет излучения факела; образовавшаяся пароводяная смесь поступает в барабан.
Подъем пароводяной смеси по трубам экранов и опускание воды по опускным трубам, т. е. естественная циркуляция, происходят за счет разности плотностей воды в опускных трубах и пароводяной смеси в трубах экрана. Поэтому барабанные котлоагрегаты называются котлами с естественной циркуляцией.
Для большего охлаждения факела у многих современных котлоагрегатов паропроиз-водительностью 400 т/ч и выше топочную камеру делят на две части двухсветным экраном, трубы которого обогреваются лучистой теплотой факела с обеих сторон (рис. 2). В такой топке – две холодные воронки, в которых происходят охлаждение и затвердевание выпавших из факела частиц спекшейся золы, образующих шлак.
Пароперегреватель современного котлоагретата, в который поступает пар из барабана, называется первичным пароперегревателем. Расширение пара в турбине приводит к тому, что из него выделяются капли влаги, т. е. пар частично конденсируется на последних лопатках турбины, что недопустимо, так как в результате сильных ударов этих капель быстрее изнашиваются детали турбин. Во избежание этого, а также для повышения экономичности работы установки в современных котлоагрегатах с рабочим давлением 13,7
МПа (140 кгс/см2) и выше применяется вторичный перегрев пара в промежуточном пароперегревателе, служащем для перегрева пара, возвращаемого из промежуточных ступеней турбины.
В котлоагрегатах среднего давления на перегрев первичного пара затрачивается около 20 % всей теплоты, воспринимаемой котлоагрегатом от дымовых газов. В котлоагрега-тах с рабочим давлением 13,7 МПа (140 кгс/см2) на долю пароперегревателя приходится около 35 % воспринимаемой котлоагрегатом теплоты, а при наличии промежуточного перегрева пара – до 50 % теплоты.
В котлоагрегатах сверхкритического давления выше 22,1 МПа (225 кгс/см2) на перегрев пара затрачивается еще большая доля теплоты. Поэтому первичные пароперегреватели современных котлоагрегатов высокого и сверхкритического давления имеют три части: радиационную, полурадиационную и конвективную.
Радиационная часть пароперегревателя может покрывать часть стен и потолок топочной камеры.
Полурадиационную часть выполняют в виде ширмового пароперегревателя и обычно располагают в зоне выхода дымовых газов из топки.
Конвективная часть состоит из змеевиков, которые собирают в пакеты и размещают в газоходах котлоагрегата за топочной камерой.
С повышением рабочего давления обеспечение надежной естественной циркуляции воды в котлоагрегате из-за уменьшения разности плотностей воды и пара становится все более затруднительным.
В настоящее время принято считать, что создание надежно работающих котлоагрега-тов с естественной циркуляцией возможно лишь для рабочего давления не выше 18,1 МПа (185 кгс/см2). В России серийные котлоагрегаты с естественной циркуляцией выпускаются с наибольшим рабочим давлением 13,5 МПа (140 кгс/см2). Котлоагрегаты с давлением выше 18,1 МПа (185 кгс/см2) выполняют прямоточными.
Дата добавления: 2015-07-10; просмотров: 6250;