Учебный вопрос № 2. Рекуперативные теплообменники
Рекуперативные теплообменные аппараты воздухоразделительных установок в соответствии с конструктивным оформлением могут быть разделены на три основные группы: прямотрубные, из витых труб и пластинчаторебристые.
Прямотрубные теплообменники наиболее просты по конструкции и чаще всего служат для нагревания и охлаждения газа низкого давления. Такие теплообменники работают, как правило, при сравнительно небольших перепадах температур по длине аппарата и при относительно высоких температурных напорах между потоками.
Теплообменники из витых труб применяют обычно для охлаждения воздуха высокого и среднего давления, а также для переохлаждения сжиженных газов.
Если коэффициент теплоотдачи со стороны потока, протекающего в межтрубном пространстве витого теплообменника, существенно ниже коэффициента теплоотдачи от потока в трубках (теплообменники высокого давления, переохладители сжиженных газов и др.), то намотка теплообменника может быть выполнена из оребренных труб. Когда величина коэффициентов теплоотдачи с обеих сторон теплообменной поверхности сравнительно невелика (теплообмен между потоками газов низкого давления) целесообразнее применять двустороннее оребрение. Наиболее рациональной конструкцией с двусторонним оребрением являются пластинчато-ребристые теплообменники, которые по сравнению с аппаратами трубчатого типа имеют следующие преимущества: компактность поверхности, небольшие вес и габариты теплообменника; возможность автоматизации изготовления и создания оптимальных конструкций в отношении теплообмена и гидравлического сопротивления и др.
Трубчатые теплообменные аппараты
В виде прямотрубных теплообменников изготовляют подогреватели азота и воздуха, идущих; на отогрев кислородных установок низкого давления, а также детандерные теплообменники. В виде кожухотрубных аппаратов с прямыми трубами изготовляют вымораживатели паров воды и вымораживатели двуокиси углерода (установка БР-6). В прямотрубных теплообменниках коэффициенты теплоотдачи в межтрубном пространстве обычно ниже, чем внутри труб. Поэтому для улучшения теплообмена в аппаратах данного типа каждый ряд трубок, расположенный по окружности,
стягивают проволокой, при этом зазор между трубками в межтрубном пространстве получается равным диаметру проволоки (детандерные теплообменники установок БР-1, БР-5) или устанавливают в межтрубном пространстве поперечные перегородки (вымораживатели двуокиси углерода установки БР-6).
Вход воздуха |
Выход воздуха |
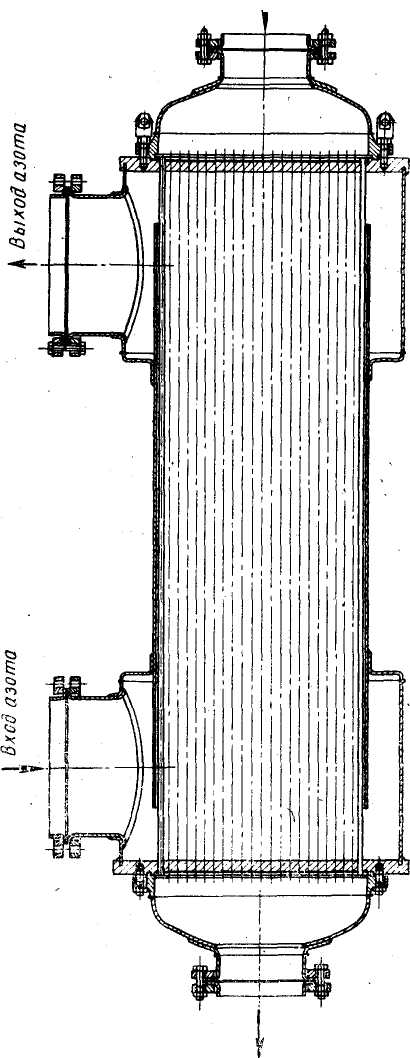
Рис. 1. Подогреватель азота
На рис. 1 изображен подогреватель азота установки БР-1, предназначенный для подогрева 19000–24000 м3/ч азота от 95 до 120–190˚К. Теплообменник имеет поверхность теплообмена 70 м2. Азот под давлением до 0,13 Мн/м2 проходит по межтрубному пространству, а воздух под давлением до 0,6 Мн/м2 – по трубам d = 8 × 0,5 мм.
Витые теплообменники воздухоразделительных установок могут быть выполнены в виде одно- и многосекционных, а также двух- и многопоточных аппаратов.
Особую группу витых аппаратов представляют собой теплообменники типа «труба в трубе», которые применяют обычно в кислородных установках малой производительности. Навивка такого теплообменника выполняется из труб малого диаметра, вставленных в трубы большего диаметра. Например, в теплообменнике установки АКДС-30 воздух высокого давления охлаждается,
Рис. 2. Типы навивки витых теплообменников
проходя по кольцевому зазору, образованному трубами диаметром 10×1,5 мм и вставленными в них трубами диаметром 5,0×1,0 мм. Воздух охлаждается кислородом, проходящим по внутренним трубам, и отбросным азотом, поступающим в межтрубное пространство.
При изготовлении витых теплообменников трубы навивают по винтовой линии на сердечник. Диаметр сердечника Dс во избежание сплющивания труб при навивке выбирают в зависимости от их наружного диаметра Dс = (10÷20) dн. Чем тоньше стенки труб, тем больше должен быть диаметр сердечника. Для создания наиболее рациональной конструкции и размеров навивки витые теплообменники делают многозаходными. Число заходов в каждом ряду труб выбирают таким, чтобы обеспечить одинаковый нагрев или охлаждение потоков газа, протекающих во всех трубах; длина труб (в соответствии с задаваемыми скоростями движения газа и с допустимым гидравлическим сопротивлением) может быть от 5 до 50 м.
По характеру применяемых труб и способу их навивки витые теплообменники разделяют на следующие типы (рис. 2): из гладких труб с плотной (тип I а), разряженной (тип I б), шаговой (тип I в) навивкой и навивкой из оребренных труб (тип II).
Теплообменники с плотной навивкой менее эффективны, чем с разряженной и шаговой навивками, но более компактны и просты в изготовлении. Теплообменники с шаговой навивкой обладают сравнительно высокими коэффициентами теплоотдачи в межтрубном пространстве, но имеют более высокое гидравлическое сопротивление. В теплообменниках с плотной и разряженной навивками между рядами труб при их намотке ставят прокладки, толщина которых определяется заданным гидравлическим сопротивлением потоку в межтрубном пространстве. На сердечнике и на наружном ряду труб прокладка делается в 2 раза тоньше. Прокладку толщиной меньше I мм делать не рекомендуется. Шаговую навивку выполняют без дистанционных прокладок с изменением направления навивки труб от ряда к ряду.
Теплообменники из оребренных труб применяют в тех случаях, когда коэффициенты теплоотдачи в межтрубном пространстве значительно ниже коэффициентов теплоотдачи от потока, протекающего в трубах, например, в теплообменниках высокого давления в 5–8 раз или в переохладителях жидкости в 8–10 раз.
Применяя в этих аппаратах оребренные трубы с соответствующим коэффициентом оребрения от 5 до 10, можно существенно уменьшить массу и габариты аппаратов. Наиболее рациональными в отношении изготовления являются трубы с поперечными винтовыми ребрами, полученными накаткой, т. е. пластической деформацией металла из толстостенных гладких труб. Способ накатки ребер дает возможность получать оребренные трубы из меди и алюминия, практически любых требующихся диаметров и длин и непосредственно из бухты.
Пластинчато-ребристые теплообменники
Пластинчато-ребристые теплообменники по своим весовым, габаритным и эксплуатационным характеристикам являются наиболее совершенными аппаратами. Для низкотемпературных установок такие теплообменники изготовляют из алюминиевых сплавов. Основной частью пластинчато–ребристого теплообменника является многослойный пакет, в
а) |
б) |
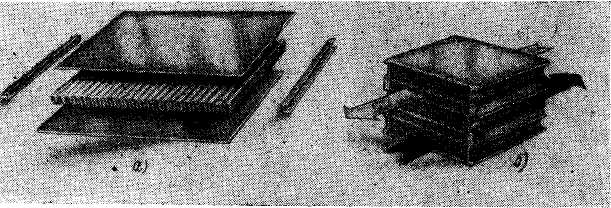
Рис. 3. Элементы пластинчато-ребристого теплообменника:
а – отдельный канал; б – элементы в собранном виде
котором между проставочными листами толщиной 0,5–1,0 мм расположена ребристая насадка. Проставочные листы плакированы силумином, который является припоем. Отдельный канал и собранный пакет пластинчато-ребристого теплообменника показаны на рис. 3. По периметру каждого канала, оставляя свободными лишь места для входа и выхода потока, укладывают проставочные элементы, которые могут быть выполнены в виде различных профилей: швеллеров, брусков различной формы и др.
Ребристая насадка представляет собой гофрированную поверхность. С помощью штамповки на поверхности наносятся прорези, перемычки между которыми отгибаются, и им придается та или иная форма; перемычки являются ребрами. Материалом для насадки служит фольга толщиной 0,1–0,5 мм.
Проставочные элементы, ребристую насадку и листы соединяют пайкой при погружении собранного пакета в ванну с расплавленными солями, которые проникают во все каналы пакета, разогревают и флюсуют поверхность. После пайки пакет отмывают от солей и испытывают на герметичность. Коллекторы к пакету присоединяют с помощью аргоно-дуговой сварки. Изготовленный таким образом пластинчато-ребристый теплообменник представляет собой легкую, но жесткую конструкцию, способную работать при давлении до 3,0 Мн/м2 и выше.
В технике низких температур пластинчато-ребристые теплообменники широко применяют в воздухоразделительных и криогенных установках, в процессах синтеза аммиака, получения этилена, разделения природных газов и др. В воздухоразделительных установках такие теплообменники применяют в качестве реверсивных теплообменников вместо регенераторов, предварительных и основных теплообменников, теплообменников- подогревателей, переохладителей, конденсаторов.
В зависимости от назначения и условий работы теплообменника при его изготовлении могут быть использованы различные ребристые насадки, которые можно разделить на шесть типов (с гладкими непрерывными ребрами, волнистыми, прерывистыми, чешуйчатыми, шиповыми и перфорированными ребрами (рис. 4)).
Гладкие ребра обеспечивают безотрывное течение газа в каналах, аналогичное в основном течению в гладких трубах.
Волнистые ребра турбулизируют поток, вследствие чего увеличиваются коэффициент теплоотдачи α и коэффициент сопротивления f. Применение волнистых ребер вместо гладких существенно уменьшает длину теплообменника при некотором увеличении поперечного сечения.
Прерывистые ребра характеризуются сравнительно высокими значениями α и f. Можно предположить, что при набегании потока газа на каждое ребро при определенных режимах течения пограничный слой формируется заново и при малой длине ребра вдоль потока (прорези, нанесены через 1–2 мм) имеет сравнительно небольшую среднюю толщину. Это приводит,
Рис. 4. Схематичное изображение пластинчато-ребристых поверхностей:
а – с гладкими непрерывными ребрами; б – с волнистыми;
в – с прерывистыми; г – с чешуйчатыми; д – с шиповыми;
е – с перфорированными ребрами.
с одной стороны, к малому термическому сопротивлению пограничного слоя, с другой – к дополнительной потере энергии, связанной с частным разрушением и формированием пограничного слоя.
Чешуйчатые ребра, характеризуемые также сравнительно высокими значениями α и f, имеют несколько большую длину вдоль потока, чем прерывистые, но отогнуты таким образом, что создают условия для перемешивания потока в поперечном направлении.
Шиповые ребра обеспечивают поперечное обтекание шипов, аналогичное, в некоторой степени, обтеканию пучка труб поперечным потоком. Шипы могут быть круглого поперечного сечения либо иметь профиль, более благоприятный в аэродинамическом отношении. Для шиповых ребер характерны высокие значения α и f.
Перфорированные, т. е. непрерывные ребра, изготовленные из перфорированного листа, характеризуются несколько более высокими значениями α и f, чем гладкие непрерывные ребра.
Внутри каждого типа ребер могут существенно изменяться такие размеры, как толщина ребер, шаг, расстояние между прорезями и др.
Размеры теплообменника зависят как от типоразмера выбранного оребрения, так и от тепловой нагрузки, температурного режима и допускаемого падения давления в аппарате, определяемых условиями работы установок. Серийное производство пластинчато-ребристых теплообменников по известной технологии требует разработки и создания определенных типоразмеров секций, соединяя которые с помощью коллекторов последовательно и параллельно, можно скомпоновать теплообменник с необходимым поперечным сечением и поверхностью.
В табл. 1 приведены габаритные размеры секций, которые могут быть использованы для крупных воздухоразделительных и криогенных установок. Высота пакета секции, определяемая числом каналов, выбирается так же, как и число параллельно соединяемых секций, в зависимости от величины требуемого поперечного сечения теплообменника и исходя из условий наивыгоднейшей компоновки параллельно соединяемых секции. Однако высота пакета не может быть больше максимальной, определяемой размерами технологического оборудования. Коллектирование теплообменников из отдельных секций требует тщательного анализа гидравлических сопротивлений самих секций, распределителей и коллекторов.
Распределители служат для равномерного распределения потока по сечению пакета и должны иметь по возможности наименьшее гидравлическое сопротивление и достаточную механическую прочность. Конструкция распределителя определяется назначением и условиями работы теплообменника. Применительно к воздухоразделительным и криогенным установкам могут быть рекомендованы два основных типа распределителей: переключающихся и непереключающихся потоков. Распределители первого типа должны обеспечивать одинаковые по форме и размерам каналы на всем протяжении теплообменника (рис. 5, б). Распределители второго типа могут быть выполнены различными по конструкции. В секции двухпоточного нереверсивного теплообменника в каналах обратного потока распределители можно вообще не ставить (рис. 5, а), что позволяет существенно сократить сопротивление по тракту обратного потока. В секциях многопоточных реверсивных теплообменников обычно используют распределители обоих типов.
При последовательном соединении нескольких секций гидравлическое сопротивление теплообменников увеличивается за счет сопротивления коллектора и распределителей, которое зависит от их конструкции и может составлять значительную долю в общем сопротивлении теплообменника.
При параллельном соединении секций на работу теплообменника существенно влияет равномерность распределения потока между секциями.
В пластинчато-ребристых теплообменниках в каждой секции и между секциями, соединенными параллельно, распределение газа может быть неравномерным. Высокая теплопроводность металла в известной степени компенсирует неравномерность распределения газа в каждой секции. Более
Габаритные размеры типовых секций, мм
Таблица 1
Секции | Ширина листа (секции) | Длина пакета | Длина рабочей поверхности | Максимальная высота набора пакета |
А | ~1000 | ~400 | ||
Б | ~2600 | ~400 | ||
В | ~1000 | ~500 | ||
Г | ~2200 | ~850 |
серьезной проблемой является обеспечение равномерного распределения газа между параллельными секциями, так как неравномерность распределения потоков здесь может вызывать значительное увеличение недорекуперации и привести к возрастанию потерь холода установки. Это особенно относится к теплообменникам, работающим при больших перепадах температур по длине и малых температурных напорах между потоками.
Рис. 5. Схема каналов пластинчато-ребристых теплообменников.
1 – рабочая поверхность – прерывистые ребра; 2 – распределитель – гладкие ребра; 3 – распределитель – перфорированные ребра; 4, 5 – «косые срезы» на входе в рабочую поверхность и выходе из нее.
Во избежание недопустимого увеличения недорекуперации секции перед коллектированием подвергаются гидравлическим испытаниям. К параллельному коллектированию допускаются только секции, имеющие практически одинаковые сопротивления.
Реверсивные пластинчато-ребристые теплообменники
Пластинчато-ребристые теплообменники можно использовать в воздухо-разделительных установках в качестве реверсивных для одновременного охлаждения и очистки исходного газа. Особенно целесообразно их применение в установках для производства чистых продуктов, так как в теплообменниках такого типа сравнительно легко осуществляется теплообмен между несколькими потоками газа.
В реверсивном теплообменнике сжатый газ охлаждается чистым обратным потоком, идущим противоточно и имеющим давление, близкое к атмосферному. При этом одновременно с теплообменом происходит вымораживание паров влаги и двуокиси углерода. Через определенное время потоки переключаются, и чистый обратный поток, проходя по каналам, нагревается и возгоняет примеси, отложившиеся из прямого потока. Период между переключениями потоков определяется допустимым повышением сопротивления на обратном потоке и обычно принимается от 15 до 30 мин.
Одной из главных задач, возникающих при проектировании теплообменников, является выбор габаритов и режима работы аппарата, обеспечивающих необходимую продолжительность рабочей кампании установки. Продолжительность кампании зависит от тщательности очистки рабочего газа в теплообменниках, определяющей забиваемость коммуникаций и аппаратов, расположенных за теплообменниками, и от скорости накопления примесей в теплообменниках. В условиях установок разделения воздуха возможны два варианта работы реверсивных теплообменников: в режиме максимально длительной кампании, при котором все примеси, вымерзающие в аппарате, возгоняются обратным потоком, и в режиме сокращенной кампании (в небольших и транспортных установках), при котором допустимо накапливание примесей в аппарате.
Дата добавления: 2015-08-11; просмотров: 1254;