КОМПОЗИЦИОННЫЕ МАТЕРИАЛЫ
Традиционно применяемые металлические и неметаллические материалы в значительной мере достигли своего предела конструктивной прочности. Вместе с тем развитие современной техники требует создания материалов, надежно работающих в сложной комбинации силовых и температурных полей, при воздействии агрессивных сред, излучений, глубокого вакуума и высоких давлений. Зачастую требования, предъявляемые к материалам, могут носить противоречивый характер. Решение этой задачи можно осуществить путем использования композиционных материалов.
Композиционным материалом (КМ) или композитом называют объемную гетерогенную систему, состоящую из сильно различающихся по свойствам, взаимно нерастворимых компонентов, строение которой позволяет использовать преимущества каждого из них.
Принцип построения КМ человек заимствовал у природы. Типичными композиционными материалами являются стволы деревьев, стебли растений, кости человека и животных.
КМ позволяют иметь заданное сочетание разнородных свойств: высокой удельной прочности и жесткости, жаропрочности, износостойкости, теплозащитных свойств и др. Спектр свойств КМ невозможно получить при использовании обычных материалов. Их применение дает возможность создавать ранее недоступные, принципиально новые конструкции.
Благодаря КМ стал возможен новый качественный скачок в увеличении мощности двигателей, уменьшении массы машин и конструкций и повышении весовой эффективности транспортных средств и авиационно-космических аппаратов.
Важными характеристиками материалов, работающих в этих условиях, являются удельная прочность σв/ρ и удельная жесткость Е/ρ, где σв – временное сопротивление, Е – модуль нормальной упругости, ρ – плотность материала.
Традиционные методы металловедения путем легирования и термомеханической обработки позволяют существенно повысить прочность металлов и сплавов. Однако они не могут изменить модуль упругости высокопрочного материала. По удельной прочности и жесткости композиционные материалы превосходят все известные конструкционные сплавы (рис. 21).
|
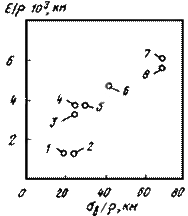
Рис. 21. Взаимосвязь удельной прочности и удельного модуля упругости некоторых неармированных и композиционных материалов, армированных волокнами
[50 об. %].
Высокопрочные сплавы, как правило, имеют низкую пластичность, высокую чувствительность к концентраторам напряжений и сравнительно низкое сопротивление развитию трещин усталости. Хотя композиционные материалы могут иметь также невысокую пластичность, они значительно менее чувствительны к концентраторам напряжений и лучше сопротивляются усталостному разрушению. Это объясняется разным механизмом образования трещин у высокопрочных сталей и сплавов. В высокопрочных сталях трещина, достигнув критического размера, в дальнейшем развивается прогрессирующим темпом.
В композиционных материалах действует другой механизм. Трещина, двигаясь в матрице, встречает препятствие на границе раздела матрица – волокно. Волокна тормозят развитие трещин, и их присутствие в пластичной матрице приводит к росту вязкости разрушения.
Таким образом, в композиционной системе сочетаются два противоположных свойства, необходимых для конструкционных материалов – высокая прочность за счет высокопрочных волокон и достаточная вязкость разрушения благодаря пластичной матрице и механизму рассеяния энергии разрушения.
КМ состоят из сравнительно пластичного матричного материала-основы и более твердых и прочных компонентов, являющихся наполнителями. Свойства КМ зависят от свойств основы, наполнителей и прочности связи между ними.
Матрица связывает композицию в монолит, придает ей форму и служит для передачи внешних нагрузок арматуре из наполнителей. В зависимости от материала основы различают КМ с металлической матрицей, или металлические композиционные материалы (МКМ), с полимерной – полимерные композиционные материалы (ПКМ) и с керамической – керамические композиционные материалы (ККМ).
Ведущую роль в упрочнении КМ играют наполнители, часто называемые упрочнителями. Они имеют высокую прочность, твердость и модуль упругости. По типу упрочняющих наполнителей КМ подразделяют на дисперсноупрочненные, волокнистые и слоистые (рис. 22).
Рис. 22. Схемы строения композиционных материалов: а) дисперсноупрочненные;
б) волокнистые; в) слоистые.
В дисперсноупрочненные КМ искусственно вводят мелкие, равномерно распределенные тугоплавкие частицы карбидов, оксидов, нитридов и др., не взаимодействующие с матрицей и не растворяющиеся в ней вплоть до температуры плавления фаз. Чем мельче частицы наполнителя и меньше расстояние между ними, тем прочнее КМ. В отличие от волокнистых, в дисперсноупрочненных КМ основным несущим элементом является матрица. Ансамбль дисперсных частиц наполнителя упрочняет материал за счет сопротивления движению дислокаций при нагружении, что затрудняет пластическую деформацию. Эффективное сопротивление движению дислокаций создается вплоть до температуры плавления матрицы, благодаря чему дисперсноупрочненные КМ отличаются высокой жаропрочностью и сопротивлением ползучести.
Арматурой в волокнистых КМ могут быть волокна различной формы: нити, ленты, сетки разного плетения. Армирование волокнистых КМ может осуществляться по одноосной, двухосной и трехосной схеме (рис. 23, а).
Прочность и жесткость таких материалов определяется свойствами армирующих волокон, воспринимающих основную нагрузку. Армирование дает больший прирост прочности, но дисперсное упрочнение технологически легче осуществимо.
Слоистые композиционные материалы (рис. 23, б) набираются из чередующихся слоев наполнителя и матричного материала (типа «сэндвич»). Слои наполнителя в таких КМ могут иметь различную ориентацию. Возможно поочередное использование слоев наполнителя из разных материалов с разными механическими свойствами. Для слоистых композиций обычно используют неметаллические материалы.
Рис. 23. Схемы армирования волокнистых (а) и слоистых (б) композиционных материалов.
Дисперсноупрочненные композиционные материалы.При дисперсном упрочнении частицы блокируют процессы скольжения в матрице. Эффективность упрочнения, при условии минимального взаимодействия с матрицей, зависит от вида частиц, их объемной концентрации, а также равномерности распределения в матрице. Применяют дисперсные частицы тугоплавких фаз типа Al2O3, SiO2, BN, SiC, имеющие малую плотность и высокий модуль упругости. КМ обычно получают методом порошковой металлургии, важным преимуществом которого является изотропность свойств в различных направлениях.
В промышленности обычно применяют дисперсноупрочненные КМ на алюминиевой и, реже, никелевой основах. Характерными представителями этого вида композиционных материалов являются материалы типа САП (спеченная алюминиевая пудра), которые состоят из алюминиевой матрицы, упрочненной дисперсными частицами оксида алюминия. Алюминиевый порошок получают распылением расплавленного металла с последующим измельчением в шаровых мельницах до размера около 1 мкм в присутствии кислорода. С увеличением длительности помола пудра становится мельче и в ней повышается содержание оксида алюминия. Дальнейшая технология производства изделий и полуфабрикатов из САП включает холодное прессование, предварительное спекание, горячее прессование, прокатку или выдавливание спеченной алюминиевой заготовки в форме готовых изделий, которые можно подвергать дополнительной термической обработке.
Сплавы типа САП удовлетворительно деформируются в горячем состоянии, а сплавы с 6 – 9 % Al2O3 – и при комнатной температуре. Из них холодным волочением можно получить фольгу толщиной до 0,03 мм. Эти материалы хорошо обрабатываются резанием и обладают высокой коррозионной стойкостью.
Марки САП, применяемые в России, содержат 6 – 23 % Al2O3. Различают САП–1 с содержанием 6 – 9 %, САП–2 с 9 – 13 %, САП-3 с 13 – 18 % Al2O3. С увеличением объемной концентрации оксида алюминия возрастает прочность композиционных материалов. При комнатной температуре характеристики прочности САП–1: σв = 280 МПа, σ0,2 = 220 МПа; САП–3: σв = 420 МПа, σ0,2 = 340 МПа.
Материалы типа САП обладают высокой жаропрочностью и превосходят все деформируемые алюминиевые сплавы. Даже при температуре 500 °С их σв не менее 60 – 110 МПа. Жаропрочность объясняется тормозящим действием дисперсных частиц на процесс рекристаллизации. Характеристики прочности сплавов типа САП весьма стабильны. Испытания длительной прочности сплавов типа САП–3 в течение 2 лет практически не повлияли на уровень свойств как при комнатной температуре, так и при нагреве до 500 °С. При 400 °С прочность САП в 5 раз выше прочности стареющих алюминиевых сплавов.
Влияние температуры испытаний на механические свойства сплавов типа САП показано в табл. 15.
Таблица 15. Механические свойства САП при разных температурах.
Тисп, °С | ||||||
σ0,2, МПа | ||||||
σ0,2, МПа | ||||||
δ, % | 7,0 | 6,5 | 5,0 | 3,5 | 2,0 | 2,5 |
Сплавы типа САП применяют в авиационной технике для изготовления деталей с высокой удельной прочностью и коррозионной стойкостью, работающих при температурах до 300 – 500 °С. Из них изготавливают штоки поршней, лопатки компрессоров, оболочки тепловыделяющих элементов и трубы теплообменников.
Методом порошковой металлургии получают КМ с использованием дисперсных частиц карбида кремния SiC. Химическое соединение SiC обладает рядом положительных свойств: высокой температурой плавления (более 2650 °С), высокой прочностью (около 2000 МПа) и модулем упругости (Е 450 ГПа), малой плотностью (3200 кг/м3) и хорошей коррозионной стойкостью. Выпуск абразивных порошков кремния освоен промышленностью.
Порошки алюминиевого сплава и SiC смешивают, подвергают предварительному компактированию под небольшим давлением, затем горячему прессованию в стальных контейнерах в вакууме при температуре плавления матричного сплава, т.е. в твердо-жидком состоянии. Полученную заготовку подвергают вторичной деформации с целью получения полуфабрикатов необходимой формы и размера: листов, прутков, профилей и др.
В табл. 16 приведены свойства КМ в зависимости от содержания порошка SiC.
Таблица 16. Свойства КМ в зависимости от содержания порошка SiC.
Свойство | Объемная доля SiC | |||
r, кг/м3 | ||||
σв, МПа | 500–550 | 600–650 | 620–670 | 620–670 |
E, ГПа | 90–100 | 100–110 | 110–120 | 130–140 |
δ, % | 5–7 | 3–4 | ||
α 10–6, град–1 |
Температурные зависимости прочности и модуля упругости КМ Д16 – 20 % SiC представлены на рис. 24.
Рис. 24. Температурная зависимость прочности и модуля упругости КМ Al(Д16) – 20 % SiC.
Эвтектические композиционные материалы на металлической матрице – сплавы эвтектического или близкого к нему состава, в которых армирующей фазой служат ориентированные волокнистые или пластинчатые кристаллы, образовавшиеся в процессе направленной кристаллизации.
Структура таких материалов формируется естественным путем, а не в результате искусственного введения армирующих компонентов в матрицу. Проблемы в химической несовместимости между матрицей и упрочняющей фазой не существует вследствие равенства химических потенциалов компонентов и равновесных условий кристаллизации таких систем.
Технология формирования эвтектических композиционных материалов на металлической матрице включает операции, сущность которых заключается в создании плоского фронта кристаллизации, т.е. плоской поверхности раздела между расплавом компонентов композиционных материалов на металлической матрице и кристаллизующимся телом.
Номенклатуру эвтектических композиционных материалов на металлической матрице делят на две части. Первую составляют материалы конструкционного назначения – на основе легких сплавов, жаропрочные – на основе тугоплавких металлов. Вторую образуют материалы с особыми физическими свойствами – полупроводниковые, ферромагнитные и др.
Углерод – углеродные композиционные материалы.Поиск высокопрочных, высокотемпературных абляционно и химически стойких материалов привел к созданию углерод - углеродных композиций (УКМ), армирующий каркас которых изготавливают из углеродных волокон, а матрицу – из монолитного углерода.
Углерод – углеродные материалы химически стойки в большинстве агрессивных сред до 227 ºС, при 402 ºС происходит окисление поверхности изделий кислородом воздуха. При армирующих элементах в виде ткани трехмерной структуры детали из углеродных композиционных материалов по теплозащитным свойствам не уступают деталям из графита, но значительно превосходят их по прочности. Углеродные композиционные материалы, армированные высокомодульными волокнами, имеют высокие характеристики удельной прочности.
Стекла и ситаллы
Стеклом называется прозрачное аморфное вещество, получаемое из различных неорганических веществ с последующей переработкой расплавленной стекломассы в изделия. Стекло, в отличие от кристаллического тела, не имеет определенной температуры плавления. При охлаждении стекло из жидкого состояния переходит в аморфно-твердое без упорядочения структуры атомов и молекул при затвердевании. Стекло состоит из микрообластей с различной пространственной структурой и химически неоднородным строением.
Сырьем для получения стекла являются природные и искусственно получаемые вещества, которые подразделяются на следующие группы:
1. Стеклообразующие вещества – окислы кремния, бора, фосфора, германия, мышьяка. Эти окислы участвуют в образовании структуры стекла.
2. Модифицирующие вещества – окислы натрия, лития, кальция, магния, бария и др., расширяющие в сочетании со стеклообразующими диапазон физико-химических свойств стекол в какую-либо сторону.
3. Промежуточные вещества – окислы алюминия, свинца, железа, титана, бериллия. Сами они не образовывают стабильной стекловидной структуры, но могут заменять часть стеклообразующих окислов в структурном каркасе стекла.
4. Красители – окислы и соли металлов, образующие в стекле коллоидные растворы и обеспечивающие различный цвет стеклу. Например, в красный цвет стекло окрашивают Cu2O, AuCl, в синий – CoO, CuSО4, в зеленый – Cr2O3, FeO и др.
5. Глушители – вещества, делающие стекло матовым, молочным. К этой группе относятся окислы и сернистые соединения мышьяка, олова, сурьмы и др.
6. Обесцвечиватели – вещества, добавление которых в стекломассу, устраняют желтую или другую слабую окраску. Например, введение MnО2 удаляет зеленую окраску, полученную от FeO.
7. Осветители – вещества, удаляющие из стекломассы газовые включения. К ним относятся NaNO3, As2O3, NH4Cl и др.
Вредной примесью в сырье являются окислы Fe, придающие стеклу зеленый оттенок.
Компоненты шихты промывают, сушат, измельчают, просеивают. При промывке удаляются глинистые частицы и органические примеси. измельчение сырья производится в щековых, а затем в молотковых дробилках или в бегунах. Сырье сушат в барабанных сушилках.
Просеянные сырьевые материалы смешиваются в определенных соотношениях, получается шихта, которая направляется на варку в стекловаренную печь.
Варка стекломассы. Процесс осуществляется в ваннах или в горшковых печах. Ванна – непрерывно действующая печь, конструктивно аналогична мартеновской печи. Она имеет ванну длиной около 30 метров, над которой в пламенном пространстве сжигается топливно-генераторный или природный газ. Топливо и воздух, необходимый для горения, предварительно нагреваются в регенераторах, а затем подаются через форсунки в пламенное пространство печи. Варка стекла – сложный физико-химический процесс, состоящий из следующих стадий:
1. Удаление гигроскопической и кристаллизационной влаги и выгорание органических соединений при температурах ниже 500 ºС.
2. Силикатообразование, заканчивающееся при 900 – 1000 ºС; шихта при этом превращается в спекшуюся массу, состоящую из силикатов Ca, Na, Mg и других металлов и свободного кремнезема.
3. Стеклообразование происходит при температурах 1000 – 1200 ºС. Масса плавится и происходит взаимное растворение кварца и силикатов в щелочном силикатном расплаве. К концу этой стадии образуется прозрачная жидкая стекломасса, но еще не однородная по химическому составу и содержащая растворенные газы.
4. Дегазация и гомогенизация происходит при 1450 – 1500 ºС. Вязкость стекломассы уменьшается, из нее выделяются пузырьки газа. Для гомогенизации, т.е. полной однородности, стекломассу выдерживают при указанных температурах в течении нескольких часов.
5. Охлаждение стекломассы (студка) заключается в постепенном повышении вязкости расплава до пределов, допускающих формование изделий. В этот период температура стекломассы снижается на 200 – 300 ºС.
Горшковые печи по устройству сходны с ванными печами, но варка стекломассы в них производится в горшках, установленных в ванне. Такие печи применяются для варки хрустального стекла и стекол особого назначения.
Изготовление стеклянных изделий. Изготовление изделий из стекла осуществляется вытягиванием, выдуванием, отливкой в формы, прокатом и прессованием.
Вытягивание применяют для изготовления листового стекла, например, оконного, труб и стержней. Широкое применение получил так называемый лодочный способ вытягивания стекла. При лодочном способе используется машина вертикального вытягивания стекла. В последнее время применяется безлодочный метод вытягивания стекла. В настоящее время скорость вытягивания ленты достигает 80 – 100 м/час, а в отдельных случаях – 145 м/ч.
Выдувание – применяют для изготовления химико-лабораторной и тарной посуды. Изделия выдуваются машинным способом или при помощи специальной стеклодувной трубки с резиновым баллоном на конце для нагнетания воздуха газодувной или автоматически действующими машинами.
Отливка в формы используется для изготовления различных архитектурно-строительных и художественных изделий, а также дисков объективов оптических приборов.
Прокат применяется для получения листового полированного стекла. Производство полированного стекла методом проката включает два самостоятельных процесса: выработку стекла методом проката и шлифовку и полировку стекла. Полированное стекло применяется для остекления витрин, окон в вагонах, автомашинах, самолетах, для изготовления зеркал.
Прессованием изготавливают банки, стаканы, изоляторы, бусы, пуговицы и др. Расплавленная стекломасса помещается в чугунную пресс-форму с сердечником, при опускании которого стекломасса равномерно заполняет пространство между формой и сердечником.
Виды стекол и их свойства.
Механические свойства стекла в основном зависят от его химического состава. Обычное силикатное стекло (состав стекла примерно 72 % окиси кремния, 14 – 15 % окиси натрия, 3 – 4 % окиси магния, 6 – 8 % окиси кальция и 1 – 1,9 % окиси алюминия) имеет предел прочности при растяжении 3 – 9 кг/мм2; предел сжатия примерно 60 – 70 кг/мм2, но низкими другими свойствами, применяется для остекления зданий и сооружений.
Кварцевое стекло содержит не менее 99,5 % окиси кремния (кремнезема). Его получают плавлением горного хрусталя или кварцевого песка. Имеет наивысшую термостойкость (около 800 ºС) и низкий коэффициент теплового расширения, благодаря которому может без разрушений резко охлаждаться (от температуры более 1000 ºС в воде) и нагреваться без разрушений.
Применяется для изоляторов, разрядников, колб радиоламп, химически стойкой аппаратуры в химической промышленности, а также как огнеупорный материал в металлургии. σв = 12 – 12,5 кг/мм2; σсж > 100 кг/мм2
Закаленное стекло или сталинит получают закалкой обычного листового стекла от температуры равной 650 – 670 ºС равномерным (с обеих сторон) быстрым охлаждением. При этом в поверхностных слоях возникают равномерно распределенные остаточные напряжения, что придает стеклу высокую механическую и термическую прочность. Предел прочности в несколько раз больше, чем у обычного силикатного стекла. Это стекло выдерживает разность температуры до 275 ºС, что втрое больше обычного силикатного стекла и в 5 – 7 раз прочнее при ударе. Применяется для остекления средств транспорта и др.
Безосколочное стекло (триплекс) получают склеиванием обычного стекла с промежуточным слоем эластичного органического полимера (поливинилбутироля и т.п.). Безосколочное стекло обладает повышенной прочностью при изгибе и ударе, а при разрушении не образует осколков. Применяется в приборах и аппаратах, работающих при повышенном давлении, а также для остекления средств транспорта.
Пеностекло – это пористое стекло, изготавливаемое в виде плит, блоков и других деталей и применяется в качестве строительного, теплоизоляционного и звукоизоляционного материала. 80 – 95 % объема этого стекла занимает газ и только от 20 до 5 % стекло.
Пеностекло получают сплавлением шихты с газообразователями (до 3 вес %), например с известняком, пиролюзитом, коксом и др. При выгорании кокса и разложении газообразователей выделяются газы вспенивающие массу. При охлаждении массы обеспечивается ячеистое строение стекла.
Стекловолокно характеризуется высокой прочностью, малой гигроскопичностью, негорючестью и неспособностью к гниению, влагостойкостью, химической устойчивостью и хорошими диэлектрическими свойствами.
Существует два вида стеклянного волокна:
1. текстильное волокно, перерабатываемое в пряжу и ткани (длина нити 20 км и более);
2. теплоизоляционное волокно – стеклянный войлок и стекловата; диаметр стекловолокна в зависимости от назначения колеблется от 0,1 до 30 мкм.
Применяется также как наполнитель в стеклопластиках.
Тканные стекломатериалы применяются как фильтры и огнеупорные материалы, а также как наполнители в стеклопластиках.
В настоящее время стекольная промышленность выпускает различные виды специального стекла: стекло с содержанием 1 – 1,5 % закиси железа, которое поглощает тепловые лучи, увиолевое стекло, содержащее не более 0,01 % окиси железа, которое пропускает ультрафиолетовые лучи.
Особое место среди специальных видов стекол, созданных за последние годы, занимают электропроводящие стекла. Они получаются двумя путями:
1. введение в их состав элементов или окислов, обладающих свойствами полупроводников;
2. повышение их поверхностной электропроводности за счет нанесения тонких прозрачных полупроводниковых покрытий из двуокиси олова, окиси индия и окиси титана.
Эти стекла могут использоваться в полупроводниковых приборах и устройствах, для термосопротивлений (термисторов), для фотосопротивлений и светофильтров, а также как электрообогреваемые, в качестве незапотевающих и необледеняемых в транспорте и во влажных помещениях. Из них могут быть изготовлены электрообогреваемые стеклянные панели и камины; посуда, приборы и аппараты для кипячения жидкостей и т.д.
Ситаллы – стеклокристаллические материалы. Они тверже высокоуглеродистой стали, легче алюминия, в 5 раз прочнее обычного стекла. По химической стойкости ситаллы уступают только золоту и платине, разрушаясь лишь под воздействием плавиковой кислоты. Термостойкость ситаллов до 1000 ºС и их износоустойчивость очень высокая.
Ситаллы получают контролируемой кристаллизацией стекла. Это новый класс материалов, разработанный примерно в начале 60-х годов.
От стекла, ситаллы отличаются, главным образом, микрокристаллическим строением, которое получается вследствие почти полной кристаллизации исходной массы в присутствии катализаторов – Ag, Au, Cu, Pt в коллоидно-дисперсном состоянии.
Кристаллы растут на многочисленных поверхностях зародышей, и процесс кристаллизации облегчается до такой степени, что его можно вести при температуре ниже точки размягчения. В качестве зародышей (затравок) – кристаллизаторов могут применяться микрочастицы металлов или мельчайшие капельки расплавов, не смешивающихся с основным стеклом.
Термообработка, следующая за процессом формовки традиционным для стекла методами, состоит из двух стадий. На первой стадии создается большое число центров, а на второй – температура повышается с тем, чтобы вызвать рост кристаллов. Эта стадия продолжается до тех пор, пока не останется очень мало (около 2 %) стеклообразной фазы. Типичный размер кристаллов составляет 1 мкм, но можно получать кристаллы размером до 0,02 мкм. Рост кристаллов, их размеры и последовательность выделения кристаллических фаз на второй ступени, кристаллы можно регулировать температурой и продолжительностью выдержки. В зависимости от состава стекол, типа кристаллизаторов и назначения стеклокристаллических материалов применяют одно-двух и трехступенчатые режимы кристаллизации.
В процессе термообработки изменяются свойства стекла. Стекло становится непрозрачным из-за рассеяния света на границах раздела между появившимися кристаллами и оставшейся стеклообразной фазой, которые характеризуются различными показателями преломления. Поверхность приобретает некоторую шероховатость. Изменение объема достигает 3 %. Коэффициент термического расширения обычно уменьшается, однако его можно варьировать в широких пределах – от 10-7 до 10-5 град-1, подбирая равным термическому расширению металла.
Ситаллы подразделяются на фотоситаллы, термоситаллы и шлакоситаллы.В отличие от обычных стекол, свойства которого определяются в основном его химическим составом, для ситаллов решающее значение имеет структура и фазовый состав. Причина ценных свойств ситаллов заключается в их исключительной мелкозернистости, почти идеальной поликристаллической структуре. Свойство ситаллов изотропны. В них совершенно отсутствует вязкая пористость. Усадка материала при его переработке незначительна. Большая абразивная стойкость делает их малочувствительными к поверхностным дефектам. Плотность ситаллов лежит в пределах 2400 – 2950 кг/м3, прочность при изгибе 70 – 350 МПа, временное сопротивление 112 – 161 МПа, сопротивление сжатию 7000 – 2000 МПа. Модуль упругости 84 – 141Гпа. Прочность ситаллов зависит от температуры. Твердость их близка к твердости закаленной стали (7000 – 10500 МПа). Они весьма износостойки (fтр = 0,07 – 0,19). Коэффициент линейного расширения лежит в пределах (7 – 300) 10-7 с-1. По теплопроводности ситаллы в результате повышенной плотности превосходят стекла. Термостойкость высокая t = 50 – 900 ºС. Применение ситаллов определяется их свойствами.
Производство ситаллов.Технология ситаллов включает стадии варки стекла, формовки изделий и специальной термической обработки.
Технические ситаллы получают на основе искусственных шихт тех частей силикатных систем, в которых кристаллизуются фазы, обладающие заданными свойствами. Для термостойких ситаллов такими фазами являются кордиерит, сподумен LiAlSi2O6, эвкриптит LiAlSiO4; для высокопрочных – шпинель, муллит; для диэлектриков -кордиерит, диопсид, волластонит и т.д. Такие свойства, как плотность, коэффициент термического расширения, теплопроводность, модуль упругости и диэлектрическая проницаемость зависят от свойств фаз и аддитивно меняются с изменением содержаний этих фаз. Поэтому важнейшую задачу технической петрологии составляет изучение диаграмм состояния соответствующих систем. На фазовый состав ситаллов влияют малые (до 1,5%) добавки модификаторов (Na, K, Ca, Ba и др.), стеклообразователей (В, Р и др.) и окислов промежуточного типа, введение которых не меняет состав основных фаз, но заметно увеличивает или снижает их содержание. Необходимыми добавками являются вещества, служащие катализаторами и центрами кристаллизации стекол.
В качестве последних применяются: металлические Au, Ag, Cu, Pt, Pd в количествах от сотых до десятых долей %; окисные TiO2, P2O5, Cr2O3, ZrO2, ZnO и др. (первые %), фторидные Na3AlF6, Na2SiF6, CaF2 и др. (обязательно совместно с Al2O3), сера или сульфаты с добавкой кокса , сульфиды. В состав фотоситаллов вводят в качестве светочувствительных добавок Au, Ag, Cu в сочетании с сенсибилизаторами. Сенсибилизаторы – вещества, способствующие более полному протеканию фотохимических процессов – повышению фоточувствительности с образованием скрытого поверхностного изображения. При получении фотохромных и других светочувствительных стекол в качестве сенсибилизаторов используются GeO2, одновалентное золото, сернистые соединения щелочных металлов и др. Применение элементов платиновой группы (Pt, Re, Pd, Os, Ir) не требует присутствия сенсибилизаторов.
С целью удешевления производства и комплексного использования сырья для изготовления ситаллов привлечены: доменный шлак вместе с кварцевым песком – для получения шлакоситаллов; магматические эффузивные и интрузивные горные породы основного состава (базальты, габбро, траппы), метаморфические породы (тремолитовые и тальковые сланцы), осадочные породы (лессовые суглинки, известковая глина), нефелиновый концентрат – для получения петроситаллов. Оценка пригодности шлаков и горных пород для этих целей наиболее просто и эффективно осуществляется петрографическими методами по их минеральному составу. Не последнюю роль играют знания петрохимических особенностей и использование возможностей методов петрохимических пересчетов.
Главной в технологии ситаллов является двухстадийнаятермообработка. Первая стадия – образования центров кристаллизации – осуществляется для большинства составов шихт выдержкой при температуре, оптимальной для этого процесса. Для фотоситаллов изделия после отжига облучают ультрафиолетовыми, рентгеновскими или – лучами. Проявление скрытого изображения происходит при нагревании стекол в интервале между температурой размягчения и отжига в течение 8 – 60 мин. Далее термообработка продолжается при более высоких температурах для завершения процесса кристаллизации и получения ситалла. На второй стадии изделия отжигают при температуре, наиболее благоприятной для роста кристаллов.
Рис. 25 Схема режима термообработки стекла для получения ситаллов.
Жаропрочность, электропроводность, механическая прочность зависят не только от свойств фаз, но в большей степени от структуры и потому не являются аддитивными. Плотная микростуктура обеспечивает высокую твердость и сопротивление абразивному износу. Повышение степени закристаллизованности увеличивает модуль упругости. Улучшению механических, термических, электроизоляционных свойств материала и химической стойкости способствует низкое содержание стекловидной фазы. Хотя контроль за фазовым составом и структурой в связи с тонкозернистостью ситаллов осуществляется в основном методами рентгенофазового анализа и электронной микроскопии, при активном участии петрологов проводится исследование кинетики зародышеобразования и роста кристаллов, являющихся теоретической основой главных стадий производства ситаллов.
Применение ситаллов.Синтез ситаллов может быть осуществлен с учетом заранее заданных свойств. Благодаря этому ситаллы могут отличаться каким-либо одним главным свойством, например, механической или термической прочностью, химической устойчивостью, износостойкостью, прозрачностью и др., или обладать комплексом необходимых свойств. Это предопределило широкий спектр использования этих кристаллических материалов. В промышленных масштабах ситаллы стали широко использовать с начала 1960-х гг. Сегодня они широко используются в промышленности в качестве облицовочного материала, элементов слоистых панелей в конструкциях промышленных зданий. Незаменим ситалл и в быту. Из него изготавливают жаропрочную хозяйственную посуду – кастрюли, жаровни, сотейники. Стеклокерамику применяют в авиационной промышленности, например, в обтекателях ракет. Очень большое распространение в химическом машиностроении получили стеклокристаллические покрытия, наносимые на поверхность различных металлов для защиты их от коррозии, окисления и износа при обычных и повышенных температурах. На предприятиях химической, коксохимической и нефтеперерабатывающей отраслей промышленности используют ситалловые трубы.
Все шире области применения ситаллов в электронной промышленности. Их используют в качестве диэлектрической изоляции микросхем и межслойной изоляции печатных схем на керамических и других подложках. Ситаллы на основе горных пород (перлита и доломита) рекомендуются для изготовления высоковольтных стержневых и штыревых электроизоляторов. Стеклокерамические корпуса нашли применение для герметизации полупроводниковых приборов и интегральных схем. Литиево-алюмосиликатная стеклокерамика в сочетании с барийалюмосиликатным стеклом в наши дни служит наполнителем в материалах для пломбирования зубов.
Стеклокристаллические материалы разделяют на ряд видов, важнейшими из которых являются ситаллы, получаемые из технически чистых материалов, и шлакоситаллы, получаемые на основе дешевого сырья – металлургических шлаков. Родиной шлакоситалла считают Советский Союз, где впервые были разработаны механизированная технология и оборудование для непрерывной варки шлакоситаллового стекла в ванной печи непрерывного действия, формования ленты и кристаллизации ее в конвейерной печи с целью получения черного, белого и светлоокрашенного шлакоситалла. В основе всех работ в этом направлении лежат исследования профессора И. И. Китайгородского, впервые введшего в обиход само слово «ситалл» и разработавшего концепцию использования отходов различных производств, включая доменные шлаки, для получения нового вида материала из стекла. Следует заметить, что первые шлакоситаллы в зависимости от чистоты шлакового сырья и его состава получались серых, коричневых, зеленовато-бурых тонов. Их применяли в основном в технике и строительстве (например, в виде листов и плиток для настила полов в химических цехах, гражданских сооружениях). Но для того, чтобы получить из них декоративные материалы, необходимо было расширить цветовую гамму. Естественно, любые цветные материалы можно создать на основе белого с использованием красителей. А белый шлакоситалл долго не удавалось получить. Лишь в 1970 г. был налажен выпуск белой разновидности шлакоситаллов. Панели и плиты из этого материала стали широко применять при облицовке фасадов
Дата добавления: 2015-06-17; просмотров: 3190;