МАГНИТОГРАФИЧЕСКИЙ МЕТОД ДЕФЕКТОСКОПИИ ИЗДЕЛИЙ
1. ЦЕЛЬ РАБОТЫ
1. Знакомство с понятиями дефектов металла типа нарушения сплошности.
2. Изучение физических основ магнитографического метода дефектоскопии.
3. Практическое освоение методик магнитографического контроля.
2. СОДЕРЖАНИЕ РАБОТЫ
1. Ознакомиться с физическими принципами магнитографии.
2. Изучить работу лабораторной установки для магнитографического контроля, включающую устройство для записи полей рассеяния на магнитную ленту и прибор МГК-1, служащий для воспроизведения и анализа записанных сигналов.
3. Экспериментально определить влияние на показания прибора МГК-1:
ü глубины линейных поверхностных дефектов (варьируя величину намагничивающего тока, настроить дефектоскоп на максимальную чувствительность к глубине поверхностных дефектов);
ü глубины залегания подповерхностных дефектов различной величины;
ü наличия и толщины сварного шва над дефектом.
4. Ознакомиться с устройством дефектоскопа-индикатора СТАТОСКАН и выполнить контроль фрагмента трубы с разделением обнаруженных дефектов по степени опасности.
5. Обработать и проанализировать результаты измерений.
3. ОСНОВНЫЕ ПОЛОЖЕНИЯ
3. 1. Дефекты сплошности металлов
Задачей дефектоскопии является обнаружение и измерение характеристик дефектов типа нарушения сплошности с целью последующего определения возможности использования по назначению проконтролированного изделия.
К дефектам сплошности металлов относятся, прежде всего, трещины различного происхождения (закалочные, усталостные, шлифовочные, рихтовочные), формы и размеров (волосовины, флокены, внутренние разрывы, рванины и т. д.), а также раковины, поры, включения, закаты, непровар, коррозионные поражения и многие другие дефекты [1–2] . Для примера на рис. 4. 1 приведен вид закалочной трещины, а на рис. 4. 2 – вид непровара на сварном шве. Визуализация дефектов получена при помощи магнитного порошка, наносимого на намагниченное изделие и скапливающегося вблизи дефекта (см. магнитопорошковая дефектоскопия [1, 3]).
По возможности выявления дефекты подразделяют на явные, видимые невооруженным глазом, и скрытые, выявляемые при помощи специальных средств.
В зависимости от возможного влияния на эксплуатационные свойства изделий дефекты подразделяются на критические, значительные и малозначительные. Критическим называется дефект, при наличии которого использование продукции по назначению невозможно по техническим причинам или из-за несоответствия требованиям безопасности или надежности; значительным – дефект, который существенно влияет на эксплуатационные свойства продукции и (или) на ее долговечность, но не является критическим; малозначительным – дефект, который не оказывает существенного влияния на возможность использования продукции по назначению. При классификации учитывают характер, размеры, место расположения дефекта на изделии, особенности изделий, их назначение, условия эксплуатации.
|
б
Рис. 4. 1. Поперечный разрез глубокой закалочной трещины (x120)
|
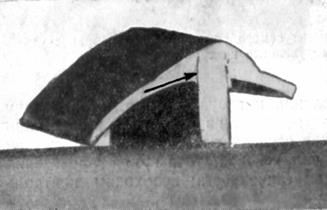
б
3. 2. Магнитные поля рассеяния вблизи дефектов
Полем рассеяния или полем дефекта называют изменение однородного намагничивающего поля вблизи дефекта. Точное вычисление поля дефекта возможно только для ряда простейших случаев. Аналитически решены задачи вычисления поля некоторых моделей дефектов в безграничном пространстве с постоянной магнитной проницаемостью m = const (линейный случай). Решение задачи получается на основе решения системы уравнений Максвелла:
, (4.1)
, (4.2)
с учетом граничного условия
, (4.3)
означающего непрерывность тангенциальной составляющей магнитного поля на границе среды дефекта 1 и пространства 2, а также граничного условия
или
, (4.4)
означающего непрерывность нормальной составляющей магнитной индукции ( – проницаемость среды, заполняющей дефект,
– проницаемость пространства).
На рис. 4. 3 представлены простейшие модели поверхностных дефектов.
а б в
Рис. 4. 3. Модели поверхностных дефектов
Для расчета полей поверхностных дефектов используют, например, следующий искусственный прием. Грани дефекта (рис. 4. 4) рассматриваются
Рис. 4. 4. Полюса на гранях дефекта
как торцы намагниченного изделия, на которых, как известно, образуются магнитные полюса. Магнитный полюс можно описать системой магнитных объемных и поверхностных зарядов (реально в природе не обнаруженных), распределенных соответственно с плотностями и
, в свою очередь зависящих от координат. Если известно распределение зарядов, то можно определить поле, которое они образуют в пространстве. При указанных выше условиях это и будет поле дефекта.
Например, для дефекта, изображенного на рис. 4. 3а, вводя систему обозначений, приведенную на рис. 4. 5, при условии однородного
Рис. 4. 5. К расчету поля трещины
распределения поверхностных зарядов на гранях дефекта , расчеты дают следующие выражения для тангенциальной и нормальной составляющих поля дефекта:
, (4.5)
. (4.6)
Графическое представление зависимостей (4. 5) и (4. 6) приведено на рисунках 4. 6 и 4. 7.
![]() | |||
![]() | |||
Рис. 4. 6. Поле рассеяния трещины Рис. 4. 7. Составляющие поля трещины
Составляющая имеет экстремум при x=0. Если x=0 и y=0, то:
. (4.7)
Если x=0, y 0, то:
. (4.8)
Если x=0, y=0, , то:
. (4.9)
Составляющая проходит через ноль в точках:
. (4.10)
Составляющая имеет экстремумы при:
, (4.11)
где ;
.
Составляющая проходит через ноль при x=0.
Формулы (4. 5) и (4. 6) позволяют проанализировать следующие предельные случаи.
1. Пусть , т. е. уменьшается глубина трещины. Тогда если принять
(линейная плотность зарядов), то формулы (5) и (6) переходят в формулы для двух равномерно заряженных нитей, расположенных в точках x=-b, y=0 и x=b, y=0 и бесконечных по оси Z:
, (4.12)
. (4.13)
Тангенциальная составляющая поля такого дефекта достигает экстремума при x=0, причем:
. (4.14)
На практике этот случай встречается редко.
2. Пусть , т. е. уменьшается раскрытие трещины. Этот случай практически всегда выполняется на практике. При условии b<<y, h формулы (4.5) и (4.6) можно разложить по малому параметру b. Пренебрегая членами разложения с b2 и более высокими степенями, получим:
, (4.15)
. (4.16)
Полученные формулы эквивалентны формулам для суперпозиции полей, создаваемых двумя токами разного знака, расположенных в точках x=0, y=0 и x=0, y=h . При этом величина токов равна . Графически эта суперпозиция представлена на рис. 4. 8. При увеличении глубины дефекта экстремумы обратного знака исчезают.
![]() | |||
![]() | |||
Рис. 4. 8. Суперпозиция полей двух токов
(тангенциальная составляющая поля прямоугольной трещины)
3. 3. Магнитографическая дефектоскопия
Процесс магнитографического контроля [3–5] состоит из двух операций: записи полей рассеяния над объектом контроля (рис. 4. 9а) и считывания магнитного отпечатка с ленты (рис. 4. 9б). При записи лента 4 укладывается на объект контроля 1 (прижимается к его поверхности) и контролируемый участок намагничивается (обычно электромагнитом). Считывание производится в специальном аппарате (он называется магнитографическим дефектоскопом), который снабжен вращающимся барабаном с закрепленным на нем преобразователем. Лента протягивается
Рис. 4. 9. Процесс магнитографической дефектоскопии:
а – запись, б – воспроизведение; 1 – объект контроля, 2 – электромагнит, 3 – магнитные силовые линии, 4 – лента, 5 – дефект, 6 – преобразователь, 7 – линия сканирования, 8, 9 – представление информации
вплотную к барабану – происходит построчное сканирование. В качестве преобразователей используются магнитные головки или феррозонды [3].
Для записи полей рассеяния обычно применяют двухслойные ленты, состоящие из немагнитной основы (ацетилцеллюлозы, полихлорвинила, лавсана) и магнитоактивного слоя – магнитного порошка, взвешенного в лаке. Для изготовления рабочего слоя используют гамма-окисел железа g-Fe2O3, железокобальтовый феррит CoFe2O3, двуокись хрома CrO2 .
Преимущества магнитографии:
- лента легко деформируется, поэтому можно контролировать изделия сложной формы, например, сварные швы с валиком;
- процессы записи и считывания разнесены в пространстве и времени, поэтому запись можно осуществлять в сложных условиях (например, под водой), а считывание – в оптимальных условиях;
- лента является документом.
Однако у метода имеется специфическая особенность – магнитная лента является существенно нелинейным звеном. Одна из важнейших магнитных характеристик ленты – функция , т. е. зависимость остаточной намагниченности от приложенного магнитного поля. На рис. 4. 10 цифрой 1 обозначена кривая намагничивания некоторой ленты. Если намагнитить ленту до насыщения полем
, а затем его отключить, то лента будет иметь максимальную остаточную намагниченность
, но если приложить поле
, то лента приобретет остаточную намагниченность
. Кривая 2 на рис. 4. 10 показывает зависимость остаточной намагниченности
от приложенного поля
.
Рис. 4. 10. Кривая намагниченности (1) и зависимость остаточной
намагниченности магнитной ленты (2)
Рассмотрим процесс формирования на ленте магнитного отпечатка. На рис. 4. 11а в упрощенном виде (в форме треугольника) изображена тангенциальная составляющая поля дефекта от координаты x. На рис. 4.11б приведены упрощенные зависимости
для лент 1 и 2. Для примера выберем ленту 1. Поле дефекта
не оставит на ленте отпечатка, т. к. согласно зависимости 1 на рис. 4.11б при приложении такого поля остаточная намагниченность не возникает. Кроме того, при превышении полем дефекта величины
(при
) остаточная намагниченность также перестанет меняться, достигнув величины
. Заметим, что поле
равно полю дефекта
в точках с
Рис. 4. 11. Запись поля дефекта (а) на ленты с характеристиками 1 и 2 (б),
остаточная намагниченность (в) и поляризация (г) лент
координатами , а поле
. Таким образом, остаточная намагниченность на ленте будет меняться при изменении x в пределах
, а также при
. На участке
будет иметь место равенство
. Указанная зависимость остаточной намагниченности ленты от координаты x отражена кривой 1 на рис. 4. 11в. В тех местах, где происходит изменение величины остаточной намагниченности Mr, образуются магнитные заряды (рис. 4. 11г). Величина зарядов:
. (4.17)
Зная величину и распределение зарядов на ленте, можно рассчитать то магнитное поле, которое они создают в окружающем пространстве.
Следует отметить, что, проведя аналогичные построения для ленты 2, мы получим (как видно из рис. 4. 11) другую систему зарядов, отличающуюся и по величине, и по расположению, а поэтому и другое поле отпечатка.
Поскольку магнитные заряды на лентах расположены вдоль, а у дефекта – по вертикальным граням, то поле отпечатка обеих лент будет отличаться и по топографии, и по величине от записанного поля.
Суммируя все сказанное, можно отметить, что на величину и топографию поля отпечатка влияют:
ü крутизна характеристики ленты dMr/dH;
ü величина Mrs ленты;
ü величина участка Hs – H0;
ü величина H0;
ü локализация поля дефекта – на одной и той же ленте равное по величине, но более «узкое» поле (т. е. имеющее больший градиент dHx/dx) создает более высокие заряды.
4. МЕТОДИЧЕСКИЕ УКАЗАНИЯ
1. Изучить данное руководство.
2. По техническим описаниям изучить порядок работы с приборами МГК-1 и СТАТОСКАН.
3. Практически ознакомиться с устройством измерительной установки и продумать последовательность действий при измерениях.
4. Получить у преподавателя персональное задание, составить план выполнения лабораторной работы.
5. Провести необходимые измерения. С целью уменьшения
случайной погрешности каждое измерение повторять не менее 3 раз и находить среднее.
5. СОДЕРЖАНИЕ ОТЧЕТА
1. Структура отчета:
ü название и цель работы;
ü краткие теоретические сведения (не более 2 страниц);
ü принципиальные схемы экспериментальной установки, приборов МГК-1 и «СТАТОСКАН» с кратким описанием порядка проведения измерений;
ü таблицы результатов измерений и расчетов (ГОСТ 2.105-85);
ü графики экспериментально определенных зависимостей
ü (ГОСТ 2.319-81);
ü анализ результатов работы;
ü заключение.
2. Отчет должен быть представлен на бумаге формата А4. Графики и формулы должны быть выполнены разборчиво. Рекомендуется использовать компьютерные технологии обработки результатов измерений и оформления отчета (в отчете должно быть указано использованное программное обеспечение).
6. КОНТРОЛЬНЫЕ ВОПРОСЫ
1. Дефекты сплошности металлов, их характеристики.
2. Топография магнитного поля дефекта типа “прямоугольная щель”.
3. Схема магнитографического метода контроля.
4. Характеристики магнитных лент.
5. Назначение и основные технические характеристики дефектоскопов МГК-1 и «СТАТОСКАН».
БИБЛИОГРАФИЧЕСКИЙ СПИСОК
1. Неразрушающий контроль металлов и изделий: Справочник / Под ред. Г. С. Самойловича. М.: Машиностроение, 1976. 456 с.
2. Ермолов И. Н., Останин Ю. Я. Методы и средства неразрушающего контроля качества. М.: Высшая школа, 1988. 368 с.
3. Щербинин В. Е., Горкунов Э. С. Магнитный контроль качества металлов. Екатеринбург: Изд-во УрО РАН, 1996. 265 с.
4. Приборы для неразрушающего контроля качества материалов и изделий: Справочник. В 2 кн./ Под ред. В. В.Клюева. М.: Машиностроение, 1976. Кн. 2. 326 с.
5. Хусаинов Д. М. Контроль качества сварных изделий трубопроводов для нефти и газа. М.: Недра,1981. 176 с.
Дата добавления: 2015-03-19; просмотров: 2370;