Перечень деталей и узлов вагонов, подвергающихся
испытанию на растяжение
Наименование деталей, диаметры, мм | Нагрузка при испытании, кН (тс) | В каких случаях производится испытание на растяжение | Технические требования |
Люлечные подвески тележек ЦВМ, подвески (в сборе) центрального рессорного подвешивания (тяги, серьги, валики) тележек КВЗ-5, КВЗ ЦНИИ-1 и КВЗ ЦНИИ-II: цапфы опорных балок центрального рессорного подвешивания; подвески и проушины остальных тележек пассажирских вагонов | 196 (20) | При изготовлении, при периодических видах ремонта вагонов (при деповском ремонте проушины должны испытываться на растяжение в случае необходимости их отклепки для ремонта) | Проушины и подвески испытываются комплектно (допускается испытание каждой детали отдельно) |
Круглые тормозные тяги пассажирских и грузовых вагонов диаметром, мм: | При изготовлении вновь и ремонте сваркой или электронаплавкой | При испытании прочих тормозных тяг нагрузки определяют по площади наименьшего сечения из расчета 157 МПа (16 кгс/мм2) |
Продолжение табл. 1.8
Наименование деталей, диаметры, мм | Нагрузка при испытании, кН (тс) | В каких случаях производится испытание на растяжение | Технические требования |
49 (5) | – | – | |
58,8 (6) | |||
78,4 (8) | |||
98 (10) | |||
107,8 (11) | |||
127,4 (13) | |||
176,4 (18) |
По диаграмме определяется, как минимум, три физико-механических характеристики:
– предел пропорциональности (в пределах нагрузок от 0 до Рр материал работает в зоне упругих деформаций);
– предел текучести (кристаллические решетки ма-териала деформируются так, что наступает их пластическая деформация);
– предел прочности .
В приведенных формулах Рр, Рs, Рв – растягивающие усилия, соответствующие точкам а, б, г, кгс; S0, S1, S2 – поперечные сечения образца в процессе испытания, соответствующие усилиям Рр, Рs, Рв.
Нагружение образца до предела пропорциональности вызывает упругое увеличение длины образца
пропорциональное нагрузке, при нагрузках превышающих Рр, зависимость между нагрузкой и удлинением носит нелинейный характер. Наступает пластическая деформация материала. При достижении нагрузки Рs образец удлиняется на величину Δ
(участок б–в диаграммы).
Предел текучести, как показатель прочности, позволяет вести расчёт деталей на прочность без угрозы возникновения в металле опасных остаточных деформаций. По этой величине определяют запас прочности.
При испытании вагонных деталей нагрузку надо выбирать такой, чтобы она была ниже предела текучести, так как при больших напряжениях деталь может получить остаточное удлинение, что недопустимо.
На заводах и в вагонных депо детали испытываются на специализированных стендах, оборудованных приспособлениями для крепления испытываемых деталей и манометрами для контроля усилий. При испытаниях фактическая удельная нагрузка должна (для стальных деталей) быть равной 16 кгс/мм2 (157 МПа), что значительно ниже предела текучести (для стали Ст.3 – 24 кгс/мм2, стали Ст.5 – 28 кгс/мм2).
Детали считаются выдержавшими испытания если:
– не нарушены сварные швы (нет разрывов, микротрещин);
– деталь не имеет пластической деформации;
– в детали нет видимых дефектов.
1.7.2. Испытания на твердость
Испытанию на твердость подвергаются пружины после изготовления, рессорные листы, тормозные колодки, фрикционные планки тележек, детали фрикционного аппарата и др.
Твердость – сопротивление металла местной, сосредоточенной в малом объеме деформации при заранее установленном механическом воздействии другого, более твердого тела заданной формы и размера.
Различают испытание на твердость по Бринеллю и по Роквеллу.
При испытании на твердость по Бринеллю стандартный наконечник (стальной шарик определенного диаметра) вдавливается на специальном прессе в исследуемый образец под действием заданной нагрузки в течение определенного периода времени.
Твердость детали определяет по диаметру отпечатка.
Твердость шарика должна быть не менее чем, в 1,7 раза больше твердости испытуемого образца. Центр отпечатка должен находиться от края образца на расстоянии не менее диаметра шарика, а от соседнего отпечатка – не менее двух диаметров.
После испытаний деталь вынимают из пресса и производят измерение отпечатка с помощью микроскопа в двух взаимно перпендикулярных направлениях. При диаметре шарика в 10 мм точность измерений должна быть не ниже 0,05 мм.
Твердость материалов, различных деталей вагонов неодинакова:
– пружин 440–460 НВ;
– фрикционных планок грузовых тележек – 286 НВ и т.д.
Другим способом определения твердости металлов является способ Роквелла. Он применяется при твердости более 450 единиц по Бринеллю.
При испытании по Роквеллу в исследуемый образец вдавливается алмазный конус (рис. 1.36). Величина твердости определяется следующим образом. Сначала прикладывают предварительную нагрузку в 10 кгс, а затем (в зависимости от твердости материала) увеличивают до 60–150 кгс) и снова снижают до 10 кгс.
Твердость материала характеризуется разностью глубин, на которые проникает конус под давлением этих двух последовательно приложенных нагрузок.
1.7.3. Испытание на ударную вязкость
Испытанию на ударную вязкость подвергаются вагонные
оси и колеса при их изготовлении
Испытание осей
Одну (из партии до 100 осей) вагонную ось черновую или механически обработанную при проверке подвергают испытанию на ударную вязкость (копровым испытаниям). Ось без образования трещин и надрывов должна выдержать пять ударов бабы массой 1 тс, свободно падающей с высоты Н, м.
Высота Н определяется из выражения
, (1.18)
где D – фактический диаметр оси посредине, мм.
Тогда
м
При испытаниях ось после первого и третьего ударов поворачивается на 180° вокруг ее продольной оси. Расстояние между опорами составляет 1,5 м. Вырезанные из оси образцы (Ø = 10, 15 или 20 мм, длиной в 5 раз больше диаметра) подвергают испытанию на растяжение. Термически обработавшая ось должна иметь временное сопротивление 55–61 кгс/мм2.
Испытание колес
Одно колесо из каждой партии, составленной из колес одной плавки, одного размера и одинаково термически обработанных, подвергают испытаниям на ударную вязкость с целью определения механических свойств материала. Колесо располагают горизонтально гребнем вверх, опирая его на металлическое кольцо ободом (рис. 1.37). Колесо должно выдержать без образования трещин и надрывов удары бабы массой 1000 кг, свободно падающей с высоты 1,5; 3 и 4,5 м и т.д. через 1,5 т, до тех пор, пока суммарная работа не достигнет величины Q = 10692 кГм.
, (1.19)
где R – радиус колеса, измеренный от центра, мм;
ℓ – величина прогиба диска, мм.
Прогиб диска колеса от падающего груза, определяемый по смещению ступицы относительно внутренней боковой поверхности обода, должен быть не менее 25 мм.
1.7.4. Испытания пружин
После окончательной термообработки каждая пружина подвергается осмотру, обмеру, испытанию на твердость. Годные пружины испытываются под пробной нагрузкой для выявления остаточной деформации и под рабочей статической нагрузкой с целью проверки соответствия фактического прогиба расчетному.
Испытание на остаточную деформацию выполняется следующим образом.
1. Пружина сжимается один раз пробной нагрузкой.
2. Снимается пробная нагрузка. Величина пробной нагрузки определяется из выражения:
, (1.20)
где τmax – максимально допустимые напряжения в пружинах, τmax = 7500 кгс/см2 ;
d – диаметр прутка, мм;
Индекс пружины
, (1.21)
К – коэффициент, учитывающий кривизну витка.
3. Измеряется высота пружины в свободном состоянии H1.
4. Пружина сжимается пробной нагрузкой вторично.
5. Снимается пробная нагрузка.
6. Измеряется высота пружины H2 .
7. Должно выполняться условие H1 – H2 = 0.
Испытание на прогиб под рабочей статической нагрузкой выполняется в такой последовательности: пружина нагружается до рабочей нагрузки и измеряется прогиб f1. Разность между фактическим прогибом f1 и расчетным fр отнесенная к расчетному прогибу, не должна быть более чем
|
|
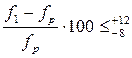
1.8. Диагностирование поглощающих аппаратов
автосцепного устройства вагонов
1.8.1. Классификация и принцип действия поглощающих
аппаратов
Поглощающие аппараты обеспечивают гашение части энергии удара, уменьшение продольных растягивающих и сжимающих усилий, которые передаются через автосцепку на раму кузова вагона. Принцип их действия основан на возникновении в аппаратах сил сопротивления и преобразовании части энергии удара в другие виды энергии. Аппараты смягчают удары, рывки, предохраняя конструкцию подвижного состава, грузы и пассажиров от вредных динамических воздействий при различных режимах движения и маневровых работах.
В зависимости от применяемого рабочего элемента, создающего силы сопротивления, и принципу действия поглощающие аппараты делятся на [11, 12, 13]:
пружинные;
пружинно-фрикционные;
с резинометаллическими элементами;
гидравлические;
эластомерные.
Поглощающие аппараты, независимо от их конструкции, характеризуются следующими основными показателями:
рабочим ходом подвижных частей, выходящих за пределы его корпуса;
энергоемкостью, то есть количеством поглощаемой энергии при полном ходе усилий 2 МН (200 тс);
усилием начального сопротивления.
К дополнительным показателям относятся стабильность работы (характеризует способность сохранять основные параметры при многократных нагружениях), период приработки, срок службы, готовность аппарата к работе (показатель заклинивания) и др.
Работа пружинных аппаратов основана на возникновении сил сопротивления упругой деформации пружин при их сжатии. Такие аппараты применяются только в упругих площадках пассажирских вагонов.
Работа пружинно-фрикционных аппаратов основана на превращении кинетической энергии соударяемых вагонов в работу сил трения фрикционных элементов и потенциальную энергию деформации пружин.
В гидравлических (гидрогазовых), эластомерных аппаратах кинетическая энергия удара затрачивается на преодоление сил вязкого сопротивления жидкости при перетекании ее из одной камеры в другую через калиброванные отверстия. Подробное описание конструкций и принципов действия поглощающих аппаратов приведено в [12].
Отраслевым стандартом ОСТ 32.175-2001 определены общие технические требования к поглощающим аппаратам. Стандарт предусматривает 4 класса аппаратов по основным технологическим показателям: Т0, Т1, Т2, Т3.
Типоразмерный ряд поглощающих аппаратов автосцепного устройства грузовых вагонов приведен в табл. 1.9.
Таблица 1.9.
Дата добавления: 2017-12-05; просмотров: 1601;