Глубинное и высокоскоростное шлифование. Научные и технологические достижения и проблемы механической и физико-химической обработки деталей ГТД
Научные и технологические достижения и проблемы механической и физико-химической обработки деталей ГТД
Глубинное и высокоскоростное шлифование
Шлифование является одной из ключевых технологий современного машиностроительного производства, которая благодаря новым разработкам в области создания абразивных материалов и инструментов, а также новейшего технологического оборудования, оснащенного многокоординатными устройствами ЧПУ, в последние годы получила существенное развитие. Роль процессов шлифования значительно возросла с появлением новых материалов, в частности конструкционных керамик и керамо-композитов, получение точных деталей из которых без шлифования проблематично.
Процессы глубинного и высокоскоростного шлифования коренным образом изменили подходы к обработке хвостовиков лопаток турбин. Никелевые сплавы очень чувствительны к нагреву, прижогам и деформациям, имеющим место при традиционном шлифовании, поэтому обработка элементов хвостовика производилась очень медленно и тщательно, что требовало больших затрат времени. Используемая в настоящее время технология глубинного шлифования позволяет выполнять черновую и отделочную обработку с высокой производительностью и качеством. На современных станках все поверхности хвостовика шлифуются без какого-либо вмешательства оператора 3 ... 4 мин. Ранее аналогичная деталь обрабатывалась в течение 20 мин и более. С помощью традиционной технологии каждый элемент шлифовался отдельно, в несколько этапов с большой долей ручного труда и затратами времени на вспомогательные переходы. По этой причине большинство производителей лопаток турбин авиационных двигателей в настоящее время используют технологии глубинного шлифования.
Глубинное шлифование (Creep Feed Grinding) является сравнительно новым способом абразивной обработки. Если при традиционном шлифовании для удаления припуска и обеспечения точности обработки требуется множество проходов с глубиной резания порядка 0,002 ... 0,05 мм при подаче 50 ... 250 м/мин, то при глубинном шлифовании - 2 ... 3 прохода при глубине резания 1 ... 10 мм и скоростью подачи 0,7 ... 15 м/мин. Обычно выполняется один или несколько черновых проходов (в зависимости от величины удаляемого припуска) и последующий чистовой проход. За один установ детали, таким образом, выполняются операции черновой и чистовой обработки. Производительность глубинного шлифования может быть в 100 раз выше, чем традиционного. Глубинным шлифованием обрабатывается широкая номенклатура материалов, включая конструкционные и инструментальные стали, сплавы на никелевой основе, титановые сплавы и керамики.
Важнейшим достоинством глубинного шлифования является возможность с высокой точностью и качеством поверхностного слоя получать сложные фасонные поверхности деталей и детали из труднообрабатываемых материалов (высокопрочных сталей, титановых и никелевых сплавов).
Замена фрезерования и протягивания сложных фасонных поверхностей глубинным шлифованием позволяет получить экономию за счет меньшей стоимости режущего инструмента (фасонные фрезы и протяжки очень дороги) и сокращения технологического маршрута обработки (одна операция глубинного шлифования взамен фрезерования, удаления заусенцев и последующего традиционного шлифования). При глубинном шлифовании отсутствуют заусенцы, что является дополнительным преимуществом по сравнению с фрезерованием. Точность и стабильность процесса также выше, чем фрезерования. Формируемые при глубинном шлифовании остаточные напряжения сжатия позволяют отказаться от операций поверхностного пластического деформирования, часто выполняемых после шлифования.
Классическая схема глубинного шлифования, реализуемая при использовании высокопористого абразивного круга с его постоянной правкой, приведена на рис. 4.1. Типовые схемы глубинного шлифования замков лопаток турбины приведены на рис. 4.2.
Основными факторами, определяющими эффективность глубинного шлифования, являются:
- базирование, обеспечение жесткости и надежности закрепления заготовки;
- характеристика шлифовального круга;
- размеры и скорость вращения круга, продольная подача заготовки, глубина резания;
- давление, температура и объем подаваемой СОЖ, ее тип, место расположения охлаждающих сопел и их форма;
- способ и условия правки круга;
- жесткость, мощность и точность технологического оборудования.
| |||||||
| |||||||
| |||||||
| |||||||
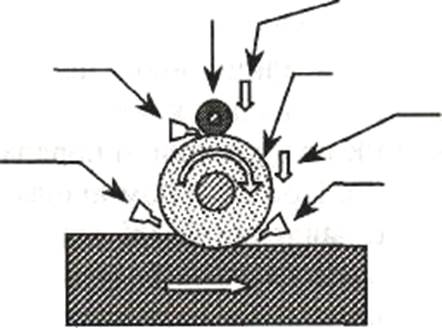
![]() | |||
| |||
Рис. 4.1. Схема глубинного шлифования
При глубинном шлифовании вследствие того, что дуга контакта круга с заготовкой значительная, в 10 ... 30 раз увеличивается мощность резания. Поэтому используемое оборудование должно иметь высокую жесткость. Необходимо также надежное и жесткое крепление заготовки. В ряде случаев при обработке маложестких деталей с целью уменьшения силы резания используют несколько проходов или уменьшают скорость перемещения стола.
Увеличение глубины резания приводит к увеличению длины контакта и как следствие пути, проходимого абразивной частицей в контакте с деталью, а также количества зерен, одновременно находящихся в контакте. Каждое абразивное зерно срезает более тонкую, но более длинную стружку, чем при обычном шлифовании.
Так как при глубинном шлифовании скорость детали ниже, чем при традиционном, глубина врезания единичного зерна и нагрузка на него при микрорезании снижаются. Это дает возможность применять абразивные круги самой низкой твердости -ВМ1, ВМ2.
![]() |
|
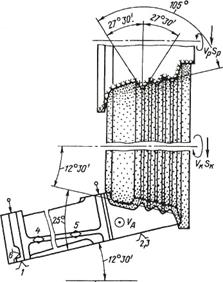
![]() |
|
Однако, поскольку в контакте с деталью одновременно находится больше частиц, чем при традиционном шлифовании, наблюдается сильное тепловыделение, что приводит к необходимости эффективного охлаждения путем подачи СОЖ под давлением порядка 0,6 ... 1,3 МПа при расходе около 100 ... 300 л/мин. При обычном шлифовании расход составляет 5 ... 10 л/мин. Высокое давление СОЖ способствует преодолению воздушного барьера, образующегося из-за большой скорости шлифовального круга, и обеспечивает эффективное охлаждение зоны резания.
![]() |
Выбором оптимальных параметров процесса глубинного шлифования (вид, состав и способ подачи СОЖ, характеристики круга, способ и частота правки, режимы резания и др.) могут быть созданы условия, исключающие возникновение термопластических деформаций поверхностного слоя и снижающие интенсивность протекания фазовых, структурных и диффузионных процессов. Исследования показывают, что при реально создаваемой интенсивности охлаждения количество теплоты, уходящее в обрабатываемую поверхность, в зависимости от условий обработки составляет 32 ... 83 % от всего выделившегося тепла. При этом чем больше угол наклона (3 (чем больше глубина шлифования) и меньше скорость заготовки, тем большее количество теплоты уходит в снимаемые с заготовки слои металла и тем ближе смещаются максимальные значения на ее поверхности к точке А (рис. 4.3).
Рис. 4.3. Схема контакта круга при глубинном шлифовании
Интенсивный отвод тепла от зоны резания обеспечивается обильной подачей СОЖ под давлением. При такой интенсивности теплоотдачи температура составит 300...500°С, что является гарантией отсутствия прижогов и трещин на обработанной поверхности. Соотношение скорости круга и заготовки 60...200.
Снижение сил резания, действующих на единичное зерно при шлифовании, и эффективное охлаждение обеспечивают минимальное тепловое и силовое воздействие на поверхностный слой.
Специфические условия процесса глубинного шлифования требуют использования специального инструмента.
Шлифовальные круги, применяемые при глубинном шлифовании, можно разделить на две группы: с традиционными абразивными материалами и сверхтвердыми абразивными материалами (суперабразивами). Обычные абразивы имеют форму зерен или частиц, а суперабразивы -форму кристаллов. Типичными традиционными абразивами являются корунд (А12О3, твердость по Кнупу 2500) и карбид кремния (SiC, твердость по Кнупу 2700). К суперабразивам относят кристаллы кубического нитрида бора (твердость по Кнуру 4700) и алмазов (твердость по Кнупу 7000).
Основным требованием к инструменту для глубинного шлифования является наличие и равномерное распределение одинаковых по размеру пор, соединенных друг с другом каналами, обеспечивающими подвод СОЖ через тело круга. Считается, что наилучшими кругами для глубинного шлифования являются мягкие круги с высокой пористостью и открытой структурой. Для их получения в связку добавляют частицы, которые при спекании выгорают, образуя поры. Например, для глубинного шлифования лопаток турбин газотурбинных двигателей применяются круги диаметром 500 мм, зернистостью от 10 до 40, твердостью ВМ. Размер крупных пор составляет 0,3 ... 0,4 мм, объем пор - до 50 % объема круга. Обычные абразивные круги для традиционного шлифования имеют пористость, не превышающую 25 ... 30 %.
![]() |
Рис. 4.4. Пористая структура круга, используемого для глубинного шлифования
Пористая структура, обеспечивая подвод СОЖ в зону обработки, улучшает условия охлаждения, уменьшает силы резания и способствует удалению из наружных открытых пор стружки. Кроме того, открытые поры, выходящие на поверхность, обеспечивают выход стружки, образующейся в процессе шлифования (рис. 4.4). Следует отметить, что при большой глубине резания подвод СОЖ в зону обработки возможен иногда только через поры. Равномерное распределение пор обеспечивает равномерную плотность и как следствие минимальный дисбаланс шлифовального круга.
На эффективность шлифования значительное влияние оказывают размеры пор круга. При больших размерах улучшаются условия подвода СОЖ, однако уменьшается количество одновременно работающих абразивных частиц и увеличивается нагрузка на них. Очевидно также, что с увеличением размеров пор сложнее обеспечить прочность закрепления абразивных зерен в связке. Допустимые размеры пор определяются размерами абразивных зерен. При больших размерах пор сложнее обеспечить их равномерное распределение. При малом размере пор ухудшаются условия охлаждения и выхода стружки. От размера пор зависит способность круга сохранять форму. Если размеры пор значительно больше размеров абразивных зерен, становится трудно поддерживать форму круга.
Большое значение имеет и твердость круга. Абразивные зерна по мере их затупления должны обновляться путем скалывания и выкрашивания частиц. При слишком твердом круге связка продолжает удерживать затупившиеся и потерявшие режущую способность зерна. При этом на работу по удалению материала расходуется большая мощность, изделия нагреваются, возможно их коробление, на поверхности появляются следы огранки, царапины, прижоги и другие дефекты. При слишком мягком круге зерна, еще не утратившие свою режущую способность, выкрашиваются, круг теряет правильную форму, увеличивается его износ, в результате чего трудно получить детали необходимых размеров и формы. В процессе обработки появляется вибрация, необходима более частая правка круга. Таким образом, в обоих случаях снижается интенсивность съема материала и повышается шероховатость поверхности обрабатываемого изделия.
Зернистость кругов выбирается в основном в зависимости от требований, предъявляемых к шероховатости обрабатываемой поверхности. Например, при зернистости 63 ... 200 шероховатость поверхности составляет Ra = 0,63 ... 0,32 мкм, а при зернистости 40 ... 63 - Ra = 0,16 ... 0,32 мкм.
Для большинства материалов используются круги на основе электрокорунда (шлифование сталей и никелевых сплавов) и карбида кремния (шлифование сталей и титановых сплавов).
Суммируя изложенное, следует отметить, что основными качественными показателями кругов для глубинного шлифования из обычных абразивов являются:
- оптимальное соотношение между размерами зерен и пор для обеспечения выхода стружки и условий охлаждения;
- равномерное распределение пор в материале круга для минимизации дисбаланса;
- увеличенная прочность связки, удерживающая зерна при высокой концентрации пор, и минимальные размеры мостиков связки, соединяющих соседние абразивные зерна;
- контролируемое разрушение связки с целью обеспечения самозатачивания и правки кругов.
В настоящее время все более широкое применение получает глубинное и высокоскоростное шлифование абразивными кругами из алмаза и кубического нитрида бора (КНБ). Круги из КНБ особенно эффективны при шлифовании деталей сложной формы из труднообрабатываемых материалов (твердых сплавов, сплавов на никелевой, кобальтовой и титановой основе), а также в тех случаях, когда форма круга не допускает его правки. Алмазные круги используются для шлифования твердых сплавов и деталей из конструкционных керамик. Некоторые керамики могут обрабатываться только суперабразивами.
Стойкость кругов из КНБ с металлической связкой значительно выше, чем обычных. Коэффициент стойкости абразивных кругов - отношение объема удаленного материала к объему износа круга - для обычных кругов из электрокорунда составляет 1 ... 5; для кругов из КНБ - 60 ... 120. Такая высокая стойкость кругов их КНБ обеспечивает работу без правки или только с предварительной правкой.
Основными достоинствами КНБ являются высокая скорость удаления материала, незначительные силы резания, низкие температуры в зоне резания и способность сохранять форму от начала до конца обработки. КНБ, в частности, целесообразно использовать для шлифования профилей с углами малого радиуса.
Шлифовальные круги из суперабразивов изготавливаются из пластиков, сталей и алюминиевых сплавов, а абразивный слой формируется на периферии круга. Он может состоять из нескольких слоев абразивных зерен (многослойные круги) или в случае использования металлической связки из одного слоя кристаллов абразива (однослойные круги). Такой подход связан с тем, что стоимость сверхтвердых абразивов в настоящее время остается довольно высокой.
Однослойные круги имеют слой кристаллов абразива, закрепленных на поверхности гальваническим покрытием. Например, шлифовальные круги для обработки никелевых сплавов изготавливают нанесением слоя КНБ на стальной диск. Зерна абразива гальваническим способом заращиваются слоем никеля. Точности формы таких кругов добиваются тщательной сортировкой кристаллов абразива по размеру. Вершины абразивных зерен выступают над уровнем закрепляющего покрытия на величину ~ 0,1 ... 0,15 мм, что обеспечивает выход образующейся при шлифовании стружки. Такие круги имеют различное применение. В частности, они эффективны при глубинном шлифовании зубьев зубчатых колес и при обработке деталей из никелевых сплавов. В связи с высокой твердостью, износостойкостью, теплостойкостью и прочностью крепления зерен круги имеют большой срок службы. Скорость удаления материала достигает величин, сравнимых с лезвийной обработкой. Снижается риск образования прижогов.
Круги из суперабразивов обеспечивают высокую эффективность при шлифовании деталей с износостойкими покрытиями - плазменными, детонационными и др., а также конструкционных керамик. Следует отметить, что шлифование керамик имеет определенную специфику. Шлифованная поверхность покрыта кратерами, размеры которых зависят от размеров зерен. Они образуются в связи с выкрашиванием частиц керамики при шлифовании. Для устранения этого эффекта шлифование необходимо производить с малыми подачами на очень жестком оборудовании.
Многослойные круги из суперабразивов получают с использованием бакелитовых металлических и керамических связок. Для глубинного шлифования могут применяться пористые круги с керамической связкой. Точность формы таких кругов достигается предварительной правкой. Толщина абразивного слоя, наносимого на металлический круг, определяется планируемым сроком службы. Круги из КНБ обычно имеют небольшие размеры (0 75 ... 200 мм при ширине ~ 25 мм). Однако при необходимости изготавливают и круги больших размеров.
Возможности абразивных инструментов, выполненных как из традиционных, так и из сверхтвердых материалов, далеко не исчерпаны, и работы в этой области приводят к новым, более высоким результатам. Например, расширяется применение керамических (минералокерамических) абразивов, получаемых спеканием или реакционным спеканием дисперсных порошков керамик (SiC, Al2O3, Si3N4 и др.). Они значительно превосходят по прочности, твердости, износостойкости и остроте граней традиционные абразивные материалы. В настоящее время в основном используются круги, содержащие корундовые и керамические зерна в различных процентных соотношениях. Технология производства керамических абразивов допускает управление формой зерен и их размерами. В настоящее время на их основе ведутся разработки шлифовальных кругов с заданной ориентацией кромок абразивных зерен, что позволит добиться максимальной эффективности шлифования.
Правка шлифовальных кругов имеет следующие цели: предварительная правка обеспечивает требуемую форму, устранение биений и дисбаланса; правка в процессе шлифования обеспечивает поддержание формы круга, удаление изношенных (засаленных) абразивных зерен и обнажение новых, острых зерен.
Круги глубинного шлифования правят: алмазным карандашом или диском, перемещаемым относительно круга по копиру или по заданной программе; алмазным правящим профилированным роликом; выкрашиванием. Каждый из этих методов имеет свои достоинства и недостатки и применяется в зависимости от требуемой точности обработки, стойкости и формы периферии круга, времени, необходимого для выполнения правки, применяемого технологического оборудования и др. Правка алмазным роликом может выполняться при рабочих скоростях круга.
Правку производят периодически или постоянно в процессе работы круга. В первом случае частота правок определяется экспериментально в зависимости от объема снимаемого материала, стойкости круга, требуемой точности обработки.
Иногда правка производится после выполнения черновых проходов перед окончательным проходом. Если круг быстро теряет форму, частота правок увеличивается. Периодическая правка может выполняться всеми вышеперечисленными методами.
При глубинном шлифовании пористыми мягкими кругами из обычных абразивов наиболее часто используется постоянная правка круга, выполняемая алмазными профилированными роликами. В этом случае станок должен быть специально приспособлен. Прижатый к шлифовальному кругу ролик перемещается в радиальном направлении с постоянной скоростью Sp (рис. 4.5). Ее величина назначается в зависимости от условий обработки (вида круга, обрабатываемого материала и др.). Очевидно, что она должна быть минимальной, обеспечивающей затачивание круга и компенсацию потери формы. Например, если скорость естественного износа круга составляет 20 мкм/мин, то скорость перемещения ролика принимается равной 24 мкм/мин. Постоянная правка круга приводит к сокращению срока его службы, однако обеспечивает форму инструмента и упрощает контроль за процессом шлифования.
![]() |
|
Вследствие малого износа алмазный правящий ролик не теряет свою форму в течение нескольких месяцев непрерывной работы. Чтобы получить скорость правки, необходимую для восстановления профиля, без значительного сокращения числа оборотов шлифовального шпинделя, нужен привод ролика. Благодаря вращению ролика можно регулировать изменение скорости его проскальзывания относительно шлифовального инструмента.
По мере перемещения ролика диаметр шлифовального круга уменьшается, поэтому в программу обработки вводится компенсация в виде радиальной подачи круга Sy, обеспечивающая минимизацию погрешностей обработки, связанных с изменением диаметра круга. Для поддержания постоянной скорости резания устройство ЧПУ увеличивает частоту вращения круга. Одновременно с уменьшением диаметра круга увеличивается длина дуги контакта, а следовательно, и нагрузка на отдельные абразивные зерна. По этой причине вводится еще одна коррекция на скорость перемещения стола (продольную подачу).
В процессе правки в зону между роликом и кругом подается СОЖ. Это позволяет увеличить стойкость алмазного ролика и минимизировать тепловые деформации, ведущие к снижению точности обработки.
Алмазные ролики имеют стойкость от 10 000 до 180 000 условных правок.
На эффективность глубинного шлифования значительное влияние оказывают тип и способ подачи охлаждающей жидкости. Подача СОЖ имеет следующие основные цели:
- отвод тепла из зон шлифования и правки;
- смазывание зон шлифования и правки для снижения сил резания;
- вымывание стружки и продуктов износа круга из зон шлифования правки;
- очистка шлифовального круга;
- защита деталей от коррозии (за счет добавления ингибиторов коррозии).
На практике в зависимости от обрабатываемого материала и применяемого круга используют различные типы СОЖ, которые можно разделить на следующие группы:
- синтетические;
- полусинтетические;
- масляные эмульсии;
- масла (нефтяные и синтетические).
Наибольшее применение при глубинном шлифовании на российских авиадвигателестроительных предприятиях нашел 1,5 ... 2 %-й водный раствор эмульсола Аквол-2. Он содержит противозадирные хлорные и серные присадки, смесь которых обеспечивает снижение интенсивности адгезионных и диффузионных процессов, особенно в случае труднообрабатываемых материалов. Вода обеспечивает высокую эффективность отвода теплоты.
Перспективной является синтетическая СОЖ, представляющая собой 2 ... 3 %-й раствор концентрата Аквол-10М, который содержит анионо- активные и неионогенные эмульгаторы и жировые присадки. Последняя снижает шероховатость на 15 ... 20 % и силы резания на 10 % по сравнению с СОЖ на основе Аквол-2. За рубежом широко используется СОЖ Relubro S60, специально разработанная для процессов глубинного шлифования.
Для кругов из КНБ целесообразно использовать жидкости не на водной основе с повышенным смазочным и охлаждающим эффектом. Такие жидкости уменьшают тепловыделение и устраняют химическое разрушение КНБ, связанное с воздействием высоких температур. Оксид В2О3, формирующий на поверхности зерна КНБ, создает защитный слой, препятствующий дальнейшему окислению. В водной среде при воздействии температур этот оксид разрушается. Несмотря на малую скорость этих реакций, в определенных условиях они могут значительно снижать стойкость абразивных зерен. Специальные жидкости позволяют минимизировать эти эффекты.
Эффективное использование СОЖ обеспечивается системой ее подачи и очистки. СОЖ подается в зону обработки под давлением 0,5 ... 0,6 МПа с расходом 80 ... 200 л в минуту на один круг. Положение охлаждающего и дополнительного очистного сопла относительно обрабатываемой заготовки автоматически сохраняется по мере изнашивания круга. Баки для СОЖ вмещают не менее 1500 ... 3000 л и снабжены холодильными устройствами для стабилизации температуры на уровне 20 ... 30 °С. Предусмотрены системы фильтрации СОЖ. На эффективность охлаждения и очистки круга значительное влияние оказывают форма и расположение сопел. Обычно они подбираются в зависимости от конкретных условий шлифования. Давление СОЖ в разных соплах (основном, очистном, для охлаждения правильного круга) может существенно различаться. Их выбор определяется конкретными условиями обработки.
Станки для глубинного шлифования стоят в 10 и более раз дороже, чем обычные станки. Однако технология глубинного шлифования позволяет выполнять на одном станке несколько операций, что способствует ускорению их окупаемости.
Глубинное шлифование требует очень мощного и жесткого оборудования (15 ... 150 кВт), имеющего высокую точность перемещений.
Современное оборудование для глубинного шлифования оснащается устройствами для автоматической смены шлифовальных кругов и их балансировки, системами активного контроля размеров, контроля процесса на основе накопленных статистических данных, поддержания температуры и фильтрации охлаждающей жидкости, полного контроля процесса устройством ЧПУ.
Отечественное и зарубежное станкостроение выпускает широкий спектр станков для глубинного шлифования. В производстве деталей ГТД в настоящее время широко используются одношпиндельные станки плоскопрофильного шлифования типа ЛШ-220, специализированные -типа ЛШ-262, ЛШ-265, ЛШ-236 и специальные двухшпиндельные станки типа ЛШ-233. Для всех этих станков характерно наличие механизма непрерывной правки шлифовального круга. Полуавтомат с ЧПУ ЛШ-233 предназначен для одновременного двустороннего шлифования заготовок с непрерывной правкой кругов. Эти станки используют для шлифования хвостовиков лопаток.
Принципиально новым этапом в развитии глубинного шлифования, радикально расширяющим введение в область производства высокоответственных деталей эффективных процессов обработки, явится использование метода высокоскоростного глубинного шлифования. Этот метод, будучи дальнейшим развитием метода глубинного шлифования с традиционными скоростями резания (V = 20...30 м/с), позволит не только повысить скорость съема материала более чем в 5...10 раз, но и снизить (вдвое и более) толщину слоя материала, несущего остаточные напряжения пластического деформирования. Непременным следствием процесса станет практически полное сохранение первичных физико-химических свойств конструкционных материалов в поверхностном слое деталей и увеличение их долговечности.
Использование метода высокоскоростного глубинного шлифования связано с решением двух групп задач. Первая группа задач связана с использованием новых видов технологических средств: шлифовальных кругов из сверхтвердых абразивных материалов, правящих средств для них, масляных смазочно-охлаждающих жидкостей. Одна часть этих средств уже создана, другая - требует разработки. Вторая группа задач связана с адаптацией к конкретным типам технологических процессов и использованием новых станков, обеспечивающих все необходимые условия скоростного резания. Такие станки нового поколения имеются в производстве ряда зарубежных фирм, но, к сожалению, в отечественном станкостроении отсутствуют.
Фирмой CCJ (Германия) разработана серия станков «Скоростное резание 2000» («Speed cut 2000») многоцелевого назначения. Имея блочную компоновку, эти станки легко поддаются переналадке: смене, а если необходимо, и увеличению числа шлифовальных бабок, замене рабочих столов и др. Конструкция станков системы «Скоростное резание 2000» чрезвычайно проста. Жесткая виброустойчивая станина из полигранита несет направляющие основных исполнительных узлов.Для всех трех осей используются прецизионные линейные роликовые направляющие. Исключительно совершенная конструкция суппортов в каждой позиции исполнительных узлов обеспечивает между всеми тремя осями «магический» угол 90°. Станки снабжены специальной системой «балансирования температуры», которая отводит излучаемое из зон приводов и направляющих тепло, равномерно распределяет его по всей массе станка и выравнивает температуру его узлов с помощью жидкости, температура которой поддерживается постоянной.В результате в течение всего времени работы станка гарантированы весьма высокие показатели точности (параллельности, плоскостности и др.) и шероховатости обрабатываемых поверхностей деталей. Станки «Скоростное резание 2000» оснащены системой управления PC/CNC, которая способна вести одновременное управление по 1...8 осям движения. Эта система управления поставляется с современным программным обеспечением для реализации прецизионных процессов шлифования.
Совершенная конструкция шпинделя шлифовального круга и созданный спектр конструкций приводов для каждого из исполнительных узлов позволяют использовать в станках новой системы значения режимных параметров в диапазоне от маятникового, в том числе высокоскоростного, до глубинного и высокоскоростного глубинного шлифования. Скорость резания может быть реализована от ее традиционных значений и до 110 м/с. Скорость рабочей подачи может достигать 1500 мм/с. Кинематика станка позволяет осуществлять как вертикальный, так и горизонтальный способы шлифования. Таким образом, станки системы «Скоростное резание 2000» представляют неограниченные возможности для оптимизации технологических параметров и использования самой современной технологии, гарантируя качественно новый уровень показателей эксплуатационных характеристик деталей.
<== предыдущая лекция | | | следующая лекция ==> |
Преимущества и недостатки наблюдения | | |
Дата добавления: 2016-03-30; просмотров: 1928;