КОНТАКТНЫЙ СПОСОБ ПРОИЗВОДСТВА СЕРНОЙ КИСЛОТЫ
Контактным способом производится большое количество сортов серной кислоты, в том числе олеум, содержащий 20% свободной SO3, купоросное масло (92,5% H2SO4 и 7,5% Н2О), аккумуляторная кислота примерно такой же концентрации, как и купоросное масло, но более чистая. Контактный способ производства серной кислоты из сернистого газа включает три стадии: 1) очистку газа от вредных для катализатора примесей; 2) контактное окисление диоксида серы в триоксид; 3) абсорбцию триоксида серы серной кислотой. Главной стадией является контактное окисление SO2в SO3; по названию этой операции именуется и весь способ.
Контактное окисление диоксида серы является типичным примером гетерогенного окислительного экзотермического катализа.
Равновесие обратимой реакции
2SO2 + О2 D 2SO3, ΔН= –2×96, 7 кДж (500°С) (а)
в соответствии с принципом Ле Шателье сдвигается в сторону образования SO3при понижении температуры и повышении давления; соответственно увеличивается равновесная степень превращения SO2 в SO3. Повышение давления увеличивает и скорость реакции (а).
Открыты сотни веществ, ускоряющих реакцию окисления SO2, но были применены в производстве лишь три катализатора: 1) металлическая платина; 2) оксид железа; 3) пентаоксид ванадия.
Однако платина вышла из употребления вследствие дороговизны и легкой отравляемости примесями обжигового газа, особенно мышьяком. Оксид железа дешевый, не отравляется мышьяком, но при обычном составе газа (7% SO2 и 11% О2) он проявляет каталитическую активность только выше 625 °С, и поэтому применялся лишь для начального окисления SO2. Ванадиевый катализатор менее активен, чем платиновый, но дешевле и отравляется соединениями мышьяка в несколько тысяч раз меньше, чем платина; он оказался наиболее рациональным, и только он применяется в производстве серной кислоты в РФ. Ванадиевая контактная масса содержит в среднем 7% V2O5; активаторами являются оксиды щелочных металлов, обычно применяют активатор К2О; носителем служат пористые алюмосиликаты или диоксид кремния. Обычные ванадиевые контактные массы представляют собой пористые гранулы, таблетки или кольца. При катализе оксид калия превращается в K2S2O7, а контактная масса представляет собой пористый носитель, поверхность пор которого смочена пленкой раствора пентаоксида ванадия в жидком пиросульфате калия.
Ванадиевая контактная масса эксплуатируется при 400—600°С. При увеличении температуры выше 600 °С начинается необратимое снижение активности катализатора вследствие изменения структуры зерна и состава активного компонента. При понижении температуры активность катализатора резко снижается вследствие превращения V+5 в V+4 с образованием малоактивного сульфата ванадила VOSO4.
Процесс катализа слагается из диффузионных и кинетических стадий. В крупных гранулах контактной массы суммарная скорость процесса определяется диффузией реагентов в порах. Обычно применяют гранулы около 5 мм в поперечнике, при этом на первых стадиях окисления лимитирует скорость диффузии в порах, а на последних скорость самого катализа, точнее активированной сорбции кислорода.
Максимальный выход SO3 для данного времени контакта получается при определенной оптимальной температуре. Следовало бы начинать процесс при максимально возможной температуре 600°С, а затем непрерывно отводить теплоту реакции, с тем чтобы закончить катализ при минимально возможной температуре 400 °С.
В трубчатых аппаратах теплота отводится непрерывно, но такие аппараты при испытаниях оказались неудобными в эксплуатации. Применяют полочные аппараты со ступенчатым отводом теплоты между полками.
На ряде заводов эксплуатируются четырех- или пятиполочные контактные аппараты с теплообменниками между полками производительностью от 50 до 500 т/сут в пересчете на H2SO4. Цилиндрический корпус аппарата диаметром до 12 м и высотой до 30 м по габаритам и металлоемкости много меньше системы реакторов. Однако для современных мощных сернокислотных систем производительностью 1000—1500 т/сут H2SO4 необходимо было бы устанавливать в теплообменниках несколько тысяч труб, что создало бы трудности для ремонта аппарата и понизило бы надежность работы всей химико-технологической системы. Поэтому в составе мощных сернокислотных систем устанавливают полочные аппараты без внутренних теплообменников. На рис. 4 представлена схема производства серной кислоты по способу двойного контактирования (ДК) из природной или газовой серы, не содержащей контактных ядов (соединений мышьяка, селена и др.).
|
|
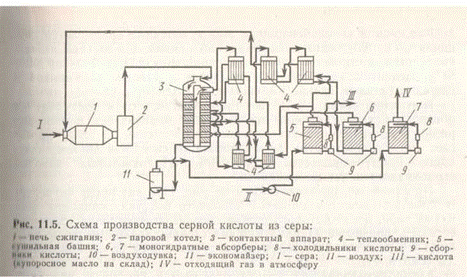
Расплавленная и отфильтрованная от минеральных примесей сера сжигается в потоке предварительно высушенного воздуха. Полученный сернистый газ с массовой долей около 10% SO2 с температурой свыше 1000 °С охлаждается в паровом котле до 420 °С и поступает в пятислойный контактный аппарат. В трех верхних слоях катализатора происходит окисление диоксида серы примерно на 60% в каждом и адиабатическое повышение температуры. Охлаждением газа в теплообменниках между полками достигается ступенчатое приближение к оптимальной кривой. На выходе из третьего слоя достигается степень превращения SO2 в SO3 на 93— 95%, при этом адиабата приближается к равновесной кривой и скорость реакции сильно уменьшается. Поэтому в способе двойного контактирования (ДК) газ после третьего слоя поступает на абсорбцию, триоксид серы поглощается практически полностью; равновесие не лимитирует процесс; соотношение О2: SO2 достигает 10 : 1 и в четвертом слое содержащийся в газе диоксид серы (около 0,5%) окисляется на 90—95%.
По схеме, представленной на рис. 4, газ после четвертого слоя охлаждается добавкой холодного воздуха, проходит еще пятый слой, после которого общая степень превращения составляет 99,5% или выше. Однако и такая степень превращения не полностью удовлетворяет современным требованиям по охране природы.
Абсорбция триоксида серы проводится в башнях с насадкой, орошаемых раствором кислоты, которая содержит 98,3—98,6% H2SO4. Такая кислота в технике называется моногидратом. Она, являясь азеотропной смесью, обладает наилучшей поглотительной способностью. Степень абсорбции свыше 99%. При небольшом разбавлении кислоты над нею появляются водяные пары, образующие с SO3 мельчайшие капельки сернокислотного тумана, которые плохо улавливаются в башнях с насадкой. Степень абсорбции резко снижается. Для улучшения абсорбции кислоту, поступающую в абсорберы, охлаждают в трубчатых холодильниках воздухом или водой до 60—70°С. В абсорберах и сушильной башне количество циркулирующей орошающей кислоты во много раз больше, чем необходимо для поглощения SO3, и определяется тепловым балансом. Схема циркуляции кислоты показана на рис. 5.
Небольшая доля кислоты передается на сушильную башню и с нее отбирается готовая продукция — купоросное масло.
Теплота реакции используется для подогрева воздуха, поступающего в печь сжигания серы, и для нагревания газа, направляемого в аппарат после первой стадии абсорбции.
Расходные коэффициенты на 1 т моногидрата H2SO4 составляют примерно: серы — 0,34 т, электроэнергии — 85 кВт×ч, воды — 70 м3. Коэффициент использования серы — 0,95.
Технологическая система производства сильно усложняется при переработке газа от обжига колчедана, сульфидов цветных металлов и газовой серы, полученной из колчедана. Эти газы содержат остатки пыли после сухой очистки в печном отделении, контактные яды в виде оксидов мышьяка, селена, аэрозолей цветных металлов, а также водяные пары.
В схему производства входит промывное определение, включающее башни с насадкой и мокрые электрофильтры.
При охлаждении газа имеющийся в нем триоксид серы и пары воды конденсируются в виде мельчайших капелек. В этих капельках растворяется оксид мышьяка. Образуется мышьяковокислотный туман, который частично улавливается в промывных башнях. Одновременно улавливаются остатки пыли (первая башня), селен и другие примеси. Образуется грязная серная кислота (до 5% от общей выработки), которую выдают как нестандартную продукцию. Окончательная очистка газа от трудноуловимого мышьяковокислотного тумана производится в двух последовательно установленных мокрых электрофильтрах. Капельки тумана заряжаются отрицательно и осаждаются на трубчатых осадительных электродах, изготовленных из свинца или углеродсодержащей пластмассы. Очистка газа завершается осушкой его от паров воды концентрированной серной кислотой в башне с насадкой.
Сухой чистый газ после сушильной башни транспортируется через всю аппаратуру турбокомпрессором.
Дата добавления: 2016-01-20; просмотров: 2574;