Выход дистиллятов на двухступенчатых атмосферно-вакуумных установках перегонки нефти
Дистиллат | Температуры отбора, °С | Выход, массовые доли в % | ||
Туймазинская нефть | Ромашкин- ская нефть | Грозненская (парафини-стая) нефть | ||
Бензин | До 170 | 20,0 | 18,6 | 14,5 |
Лигроин | 160—200 | —, | — | 7,5 |
Керосин | 200—250 | 10,0 | 9,5 | 18,0 |
Дизельное топливо | 240–350. | 17,5 | 17,5 | 5,0 |
Масла | 230—370 | 25,0 | 25,4 | 25,0 |
Остаток — гудрон | 350—370 | 25,0 | 26,5 | 27—30 |
Схема атмосферно-вакуумной установки показана на рис. 3.
|
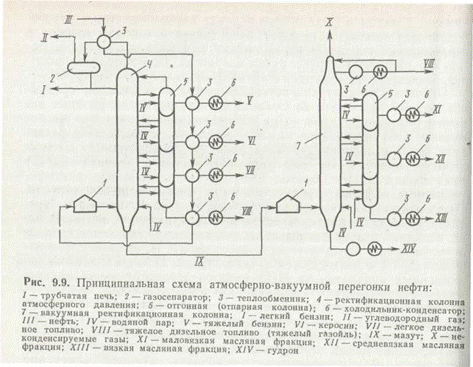
Мазут (~55% от массы сырья) из нижней части первой колонны нагревают в трубчатой печи до 400—420°С и направляют в ректификационную колонну, работающую при остаточном давлении 0,005—0,008 МПа. Пары летучих продуктов поднимаются вверх, отбираются по высоте колонны и конденсируются в виде широких масляных фракций различной вязкости. Сверху колонны выводят на охлаждение и конденсацию пары тяжелого газойля, часть его возвращают на орошение колонны. Снизу колонны отводится жидкийостаток — гудрон. В нижнюю часть обеих ректификационных колонн подают острый пар для снижения температуры внизу колонны и облегчения условий испарения легких фракций.
Нефтепродукты, получаемые на атмосферно-вакуумных установках, — бензиновые, лигроиновые, керосиновые, газойлевые и масляные дистиллаты — очищают от сернистых и кислородных соединений и после добавления присадок, улучшающих их качество, используют как топлива и смазочные масла. Бензины прямой перегонки содержат главным образом парафиновые и нафтеновые углеводороды и характеризуются низкими октановыми числами в пределах 50—70; бензины с более высоким октановым числом получают путем крекинга.
Крекинг нефти и нефтепродуктов.Процессы крекинга делят на термические и термокаталитические. При термических процессах расщепление углеводородов (собственно крекинг) происходит под действием высоких температур и давления; наряду с расщеплением происходят вторичные процессы синтеза углеводородов, более стабильных в этих условиях, в том числе непредельных углеводородов. При всем многообразии химических превращений при термическом крекинге можно установить закономерность распада и синтеза углеводородов. При высокой температуре наиболее устойчивы ароматические соединения и олефины, которые склонны к вторичным реакциям, например полимеризации. Таким образом, высокие температуры ведут к накоплению ароматических углеводородов, а также простейших олефинов в продуктах крекинга. При высоких температурах термодинамически возможен распад углеводородов на элементы, в результате чего общее равновесие системы сдвигается со временем в сторону водорода, метана и углеродистых веществ — кокса, смол.
Большинство реакций термического крекинга протекает по цепному механизму с образованием более легких парафинов и олефинов.
Распад нафтеновых углеводородов происходит по молекулярному механизму с отрывом боковых цепей (деалкилирование), при более жестких условиях с разрывом кольца и образованием моноциклических нафтенов и олефиновых углеводородов. При температурах выше 600°С происходит дегидрирование моноциклов до соответствующих ароматических углеводородов.
От разветвленных ароматических углеводородов, образующихся в процессе крекинга, отщепляются боковые цепи с образованием олефинов.
Олефины, образующиеся при крекинге, подвергаются дальнейшим превращениям, зависящим от температуры и давления. При умеренной температуре (до 500°С) и при высоком давлении идет полимеризация олефинов, а также их циклизация. Высокая температура и низкое давление способствуют разложению олефинов по цепному механизму с образованием простейших олефинов, водорода и метана.
В зависимости от условий проведения применяемого сырья и целевых продуктов различают термический жидкофазный крекинг, высокотемпературный крекинг (пиролиз) и коксование нефтяных остатков.
Термический крекинг ведут в зависимости от вида сырья при температуре в пределах 450—540°С под давлением 2— 7 МПа. Продукты — крекинг-газ, крекинг-бензин, керосиногазойлевая фракция (термогазойль) и крекинг-остаток. Крекинг-газ содержит этан, пропан, этилен, пропилен и служит ценным сырьем органического синтеза. Бензины термического крекинга характеризуются сравнительно небольшим октановым числом (около 70) и низкой химической устойчивостью и не могут непосредственно использоваться в автомобильных двигателях. Для этого необходима дополнительная переработка и стабилизация крекинг-бензина. Крекинг-остаток служит высококачественным котельным топливом.
Все химико-технологические системы термического крекинга, а также пиролиза и коксования нефтяных остатков включают трубчатые печи, служащие реактором для нагрева сырья и химических превращений. На рис. 4 представлена упрощенная технологическая схема термического крекинга с рециркуляцией жидких потоков — средней и тяжелой фракций.
Пиролиз проводят в широком интервале высоких температур (600—1000°С) в зависимости от вида сырья — углеводородные газы, газовый бензин (конденсат), керосин, газойль. Давление при пиролизе применяют от атмосферного до 0,2—0,3 МПа. Целевые продукты пиролиза — этилен и другие непредельные углеводороды, а также ароматические углеводороды — бензол, толуол, ксилол.
Коксование нефтяных остатков — это термический крекинг мазута, гудрона, крекинг-остатков при 400—500°С с целью получения жидкого топлива и электродного кокса.
К термокаталитическим процессам относятся каталитический крекинг, риформинг, гидрокрекинг и другие каталитические процессы переработки нефтепродуктов.
Каталитический крекинг ведут при 450—500°С и 0,05— 3,1 МПа. С расщеплением углеводородных цепей на катализаторе идут и реакции деалкилирования, изомеризации, циклизации, гидрогенизации, дегидрогенизации и изомеризации. Деалкилирование ароматических углеводородов ведет к образованию олефинов и простейших ароматических соединений. Нафтеновые углеводороды дегидрируются и расщепляются по С—С-связи с разрывом кольца и деалкилированием. Олефины, образовавшиеся при крекинге, расщепляются по С—С-связям, изомеризуются и гидрируются с образованием циклических и ароматических соединений. Гидрирование олефинов идет за счет дегидрирования тяжелых продуктов уплотнения; оно способствует повышению стабильности бензинов. Парафиновые углеводороды подвергаются расщеплению и изомеризации. Таким образом, в жидких продуктах каталитического крекинга накапливаются изомерные соединения и простейшие ароматические углеводороды, повышающие октановое число крекинг-бензина. Одновременно образуются твердые продукты уплотнения. Зависимость выхода бензина от режимных условий — времени контакта реагентов с катализатором и температуры — показана на рис. 4.
|
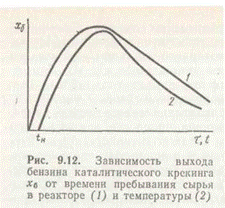
Из рисунка видно, что начавшийся процесс разложения углеводородов ускоряется с повышением температуры и выход бензина увеличивается (при постоянных давлении и времени пребывания в реакторе). Максимальный выход бензина соответствует оптимальной температуре, при которой еще не происходит распад легких углеводородов. С увеличением времени пребывания выход бензина повышается до определенного максимума; затем начинают преобладать процессы газо- и коксообразования. Обычно степень превращения поддерживают в пределах 50—70% за один проход реагентов через реактор.
Сырьем каталитического крекинга служат широкие фракции прямой гонки нефти в двухступенчатых установках, в первую очередь газойль. Катализаторами являются аморфные и кристаллические алюмосиликаты (цеолиты). Сферические зерна катализатора содержат обычно 15% цеолита, включенного в аморфную алюмосиликатную матрицу.
На промышленных установках контакт катализатора с парами сырья осуществляется: 1) в плотном слое движущегося сверху вниз катализатора; 2) во взвешенном (кипящем) слое катализатора; 3) в восходящем потоке взвеси катализатора.
|
|
|
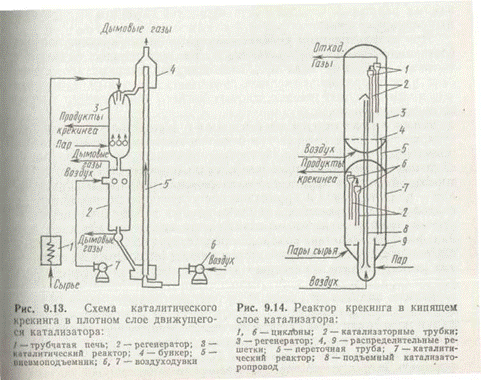
На рис. 5, 6 показаны схемы установки каталитического крекинга с плотным слоем движущегося катализатора и реактора с кипящим слоем катализатора. На агрегате с движущимся катализатором сырье из трубчатой печи направляют в реактор, куда из бункера поступает регенерированный катализатор. Проходя через реактор, катализатор крекирует сырье и за счет теплопередачи поддерживает температуру в реакторе на уровне 450—500°С. Перед поступлением в регенератор катализатор обрабатывают паром для десорбции легких углеводородов с его поверхности. Продукты крекинга отводят из реактора в ректификационную колонну для разделения газовой, бензиновой и тяжелой фракций. В регенератор воздуходувкой непрерывно подают воздух для выжигания кокса. Образующиеся дымовые газы направляют в котел-утилизатор для выработки пара.
На рис. 6 показан один из типов реакторов с кипящим слоем катализатора, в котором зона регенерации расположена над зоной катализа. Пары сырья подают в нижнюю часть реактора под распределительную решетку. Отработанный, блокированный коксом катализатор под давлением горячего воздуха эжектируется и подается из зоны катализа в зону регенерации по катализатороводу. Туда же под распределительную решетку регенератора подают воздух, необходимый для образования взвешенного слоя и выжигания кокса с поверхности катализатора. Дымовые газы, проходя через циклон регенератора, освобождаются от унесенных частиц катализатора, который по трубам возвращается в кипящий слой. Регенерированный катализатор опускается в зону катализа по переточным трубам — катализаторопроводам. В нижней части реактора (отпарная зона) отработанный катализатор обрабатывают острым водяным паром для удаления паров нефтепродуктов с его поверхности. Парогазовую смесь продуктов крекинга выводят из верхней части реактора (зона катализа), направляют на разделение и переработку. Время пребывания катализатора в зоне катализа составляет от 1,5 до 6 мин.
При каталитическом крекинге октановое число крекинг-бензина составляет 78—85. Для получения высококачественных бензинов с высоким октановым числом, а также индивидуальных ароматических углеводородов применяют риформинг. Исходным продуктом риформинга служат низкооктановые бензины термического и каталитического крекинга.
Каталитический риформингосуществляют в водородсодержащей среде при участии бифункциональных алюмомолибденовых (MoO+Al2О3) или платиновых катализаторов, нанесенных на активные алюмосиликатные или оксидные носители. На катализаторах риформинга происходят одновременно реакции дегидрирования — циклогексанов в ароматические углеводороды, парафинов — в олефины; дегидроциклизации нормальных парафинов в ароматические углеводороды; изомеризации нормальных парафинов в изопарафины. Воздействие водорода препятствует коксообразованию, и длительность работы катализаторов возрастает поэтому до нескольких месяцев. Водород насыщает непредельные углеводороды и гидрирует сернистые соединения, что способствует стабильности и обессериванию получаемого бензина. В результате риформинга образуется водородсодержащий газ, циркулирующий в системе, и жидкая фракция, которая используется как высококачественное топливо для двигателей или как высокооктановая добавка (октановое число ~95) к автомобильным бензинам. Из жидкофазного продукта риформинга выделяют также ароматические углеводороды.
Различают несколько видов риформинга — в частности платформинг и гидроформинг. Платформингпроизводят в фильтрующем слое платинового катализатора, нанесенного на фторированный оксид алюминия, при 480—510°С и давлении водорода 2—4 МПа. Гидроформингведут в кипящем слое алюмомолибденового катализатора под давлением водородсодержащего газа 1,7—1,9 МПа.
К гидрогенизационнымкаталитическим процессам нефтепереработки относятся также гидрокрекинг и гидроочистка нефтяных фракций. Гидрокрекинг — процесс деструктивного гидрирования тяжелых нефтяных фракций с насыщением продуктов расщепления водородом. Продукты гидрокрекинга — бензин, реактивное и дизельное топлива, не содержащие сернистых и азотистых соединений, а также олефинов. Процесс ведут в две стадии: на первой гидрокрекинг происходит на катализаторах, устойчивых к действию сернистых соединений, — алюмокобальтмолибденовых катализаторах, на которых происходит гидрооблагораживание сырья (гидрирование сернистых и азотистых соединений) и его частичный крекинг. На второй стадии — на катализаторах, содержащих металлы VI и VIII групп (Со, Ni, W, Pt), нанесенных на алюмосиликатные носители, происходят глубокие превращения углеводородов и их насыщение водородом. Гидроочистка служит основным, наиболее эффективным способом очистки нефтепродуктов.
Очистка нефтепродуктов.Нефтепродукты, полученные прямой гонкой и крекингом, содержат примеси, недопустимые в условиях эксплуатации моторных топлив и смазочных масел: олефины, сернистые, кислородные и азотистые соединения. Эти примеси — причина нестабильности свойств нефтепродуктов, полимеризации и окисления углеводородов с образование осадков, нагара в цилиндрах двигателей, коррозии их металлических частей. Очистка нефтепродуктов — необходимая, завершающая стадия их производства. Применяют химические и химико-физические методы очистки — обработка щелочами и серной кислотой, гидроочистка, абсорбция, адсорбция.
Очистка щелочами (NaOH) применяется для удаления
кислых и сернистых соединений — нафтеновых и жирных кислот, сероводорода.
Сернокислотную очистку нефтепродуктов производят концентрированной (90—93%-ной) серной кислотой с целью удаления олефинов, смолистых, азотистых и сернистых соединений. В результате очистки образуются большие количества отходов — «кислого гудрона», который трудно утилизировать. Аппаратура громоздкая, требуются большие количества реагента — серной кислоты.
Наибольшее распространение получила гидроочистка, основанная на гидрировании нефтепродуктов при участии селективных катализаторов (алюмокобалымолибденовых или алюмоникельмолибденовых) при температуре 350—400°С и давлении 3— 4 МПа. В этих условиях происходит гидрирование соединений серы, азота и кислорода с образованием очищенных углеводородов и продуктов гидрирования, легко удаляемых в газовую фазу — сероводорода, аммиака, паров воды. Одновременно гидрируются ненасыщенные углеводороды — олефины и диены с образованием стабильных предельных соединений. Применение гидроочистки позволяет использовать для переработки высокосернистые нефти.
Абсорбционные методы основаны на избирательном растворении вредных примесей с помощью селективных растворителей— нитробензола, дихлорэтилового эфира, фурфурола и др. Регенерация растворителей производится их перегонкой. Очистка с помощью избирательных растворителей наиболее широко применяется для смазочных масел.
Адсорбционные методы заключаются в смешении нефтепродуктов с адсорбентами, состоящими из оксидов кремния, алюминия и других металлов, «отбеливающими» глинами, бокситами, силикагелем, синтетическими цеолитами; на поверхности адсорбентов сорбируются примеси — соединения серы, азота, полициклические соединения, смолы, диолефины, а также остаточные компоненты предыдущих ступеней очистки — растворители, кислый гудрон и др. Очистку производят в адсорберах колонного типа при противоточном движении адсорбента и нагретой очищаемой фракции. Этот метод применяется в основном как завершающая стадия очистки нефтепродуктов, в частности масел, так как адсорбция обеспечивает высокую ступень очистки.
Дата добавления: 2016-01-20; просмотров: 1616;