Обследование производства при автоматизации
2.7.1. Постановка задач обследования производства
Цель – выявление объектов автоматизации, их группирование, формирование ТТ на автоматизацию.
Направления обследования (задачи и объекты обследования):
изделия; ТП; оборудование, организационное построение.
Общий результат:
- выявление принципиальной возможности автоматизации;
- предварительный выбор направления автоматизации;
- формирование технических требований для корректировки ТЗ на перевооружение производства и корректировку конструкторской документации на изделия – объекты производства и технологической документации на имеющиеся и разрабатываемые ТП;
- создание перечней массивов (И, ТП, ТО) для автоматизированного проектирования и моделирования;
- корректировка проекта структуры проектируемой ИПС;
- формирование проекта общей инфраструктуры разрабатываемой ИПС;
- формирование обобщенной структуры системы управления;
- разработка ТТ на выбор ТО.
На нижнем уровне решаемых задач автоматизации результаты обследования нацелены на разработку автоматизированного технологического комплекса (АТК).
Сложность процессов анализа при обследовании изделий, ТП и оборудования состоит в сильной взаимосвязи и взаимозависимости этих трех элементов производственной системы. Отсюда – большое количество итераций процесса принятия технологических решений при проведении каждого анализа. Технологические решения в данном случае это основа для разработки технического задания на проектирование производственной системы определенного вида, масштаба, формы.
Формализованное представление процедур анализа и принятия технологических решений выглядит следующим образом.
Пусть
- множество изделий – объектов данного производства (запущенных и планируемых к запуску);
- множество изделий после проведения группирования, где
- число изделий, сгруппированных в классифицированные группы;
- множество деталей, группирование которых признано нецелесообразным;
- число установленных
Рис. 2.7. Схема задач, решаемых при анализе производственного процесса (предпроектные исследования)
|
Обследование и анализ производственного процесса
|
Обследование изделий – объектов производства
|
Обследование технологических процессов
|
Обследование оборудования
|
Обследование организационной структуры
|
Установление критериев оценки
|
Определение номенклатуры
изделий
|
Классификация и группирование объектов производства
|
Определение технологических схем процесса
|
Определение требований к складам
|
Определение требований к транспорту
|
Определение контролируемых параметров производственного процесса
|
Определение автоматизируемых функций
|
Определение перечня унифицированной и специальной оснастки
|
Определение перечня оборудования
|
Разработка технологических схем процессов обслуживания
|
Определение информационных каналов производственной системы
|
Расчет точностных и временных параметров обслуживания
|
Определение типов и количества транспортных средств
|
Формирование вариантов технологической оснастки и средств автоматизации
|
Разработка (или корректировка) структуры производственного процесса
|
Разработка технологического обеспечения производственного процесса
|
Расчет объема складских запасов и межоперационных заделов
|
классификационных групп;
- число наименований не сгруппированных изделий;
- множество технологических операций (или частных технологических процессов), где
- число разновидностей операций (частных технологических процессов);
- множество элементов технологической системы (или множество единиц технологического оборудования), где
- число разновидностей специализаций оборудования.
Требуется спроектировать технологическую систему, реализующую все множество V технологических операций для обеспечения изготовления всей номенклатуры D изделий на выбранном множестве элементов технологической системы (множестве оборудования) Q при выполнении условия
где КЗ, КИСП - коэффициенты загрузки и использования оборудования соответственно.
Технологические решения принимаются с использованием матриц «объекты – операции»
«объекты – оборудование»
«операции – оборудование»
Результатами решений является матрица, составленная из троек (
), использующаяся для выполнения процессов оптимизации и решаемая известными математическими методами в зависимости от размерности матрицы.
2.7.2. Обследование изделий – объектов изготовления в производственной системе
При обследовании изделий – объектов производства выполняется следующее:
1. Подробный конструктивно-технологический анализ изделия – объекта производства (или всей номенклатуры изделий);
2. Предварительное группирование изделий по главным классификационным признакам и определение принципиальной возможности изготовления изделия в действующем производстве;
3. Классификация и группирование изделия (множества изделий) по совокупности всех определяющих признаков (форма, размеры определяющих поверхностей, масса, точностные характеристики, технические требования на обработку отдельных поверхностей и др.);
4. Анализ возможных вариантов построения технологических схем изготовления изделия;
5. Анализ целесообразности автоматизации элементов технологических схем (или всего ТП в целом);
6. Обеспечение технологичности выполнения автоматизируемых операций (выбор поверхностей для ориентирования, захватывания, накопления и др.);
7. Формирование требований к технологическому оснащению операций.
Схема анализа, поясняющая составляющие проводимого при обследовании изделий процесса, приведена на рис. 2.8.
Формализованные выражения, характеризующие перечисленные технологические решения выглядят следующим образом.
Пусть Xq – совокупность изделий, отнесенных к группе с индексом q;
– множество изделий x, назначенных на выполнение операции j с применением i-го комплекта технологической оснастки. Тогда
где 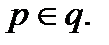
В результате выполнения работ, предусмотренных пунктами 4-7, для рассматриваемой операции получим
(
- знак включения), что означает реальную ситуацию, при которой часть деталей
исходного множества
возможно (целесообразно) обрабатывать на данном оборудовании с применением переналаживаемой (сменной) оснастки, в то время как часть деталей
требует применения другого оборудования в связи с невозможностью или нецелесообразностью изготовления на данном оборудовании.
Группирование изделий при мелкосерийном и единичном характерах производства выполняется с целью увеличения серийности и определения номенклатуры изделий, изготовление которых экономически оправданно на данном оборудовании с применением определенного комплекта технологической оснастки и с минимальными затратами времени на переналадку при переходе к изготовлению другого изделия данной группы. В группу объединяются изделия, обладающие так называемым конструктивно-технологическим подобием.
Существует несколько специальных методов определения оптимальных групп или партий изделий. Отличаются методы используемыми критериями оптимизации, например, такими как: минимум средних затрат времени на изготовление; минимум затрат на хранение («пролеживание») изделий; минимум совокупных затрат на производство и хранение; отношения между временными затратами на подготовку изготовления и непосредственно изготовление партии изделий и др.
2.7.3. Обследование технологических процессов, реализуемых в производственной системе
Данное обследование выполняется с целью обеспечения технологической гибкости, максимальной типизации, возможности использования одного процесса для изготовления как можно большего числа групп изделий из имеющейся номенклатуры.
Существует два направления достижения этой цели. Первое заключается в выявлении возможности изготовления каждого конкретного изделия из некоторой совокупности классификационных групп изделий по определенным (базовым, «классическим») типовым ТП. Если изделие не может, по каким-либо причинам, быть изготовлено по типовой технологии, а требует в каких-то ее элементах применения специфических операций, его исключают из группы и дальнейшее проектирование ведется индивидуально для единичного ТП. Второе направление реализует обратную задачу: для каждого изделия предварительно формируется принципиальная технологическая схема изготовления, состоящая из отдельных законченных элементов (операций) частных ТП.
При больших и средних размерах партий изделий, подлежащих изготовлению, предпочтительно первое направление, при мелких сериях и в единичном производстве целесообразно использование второго направления, которое в силу большой вариативности, а следовательно и трудоемкости, требует применения вычислительной техники. Укрупненная схема реализации второго направления разработки ТП (производственная типизация на базе частных ТП) представлена на рис. 2.9.
Рассмотренные направления определяют содержание задач обследования ТП. При использовании первого направления технологическая схема, составленная для определенной группы изделий, сравнивается с маршрутом освоенного типового ТП. Следовательно, при обследовании выполняется анализ конструкции изделия, группирование, составление технологической схемы, обеспечение технологичности конструкции под условия типового ТП и комплекта технологической оснастки.
При втором направлении последовательность обследования иная. Выполняется составление технологической схемы изготовления для каждой конструкции из определенной группы, полученные технологические схемы группируются по технологической общности, проводится отработка технологичности конструкции под условия ТП, образованного из частных ТП.
АНАЛИЗ НОМЕНКЛАТУРЫ ИЗДЕЛИЙ
|
Анализ изделий – объектов автоматизированного изготовления
|
Исследование выполняемых операций
|
Наличие в технологическом процессе операций, автоматизация которых нецелесообразна
|
А н а л и з п р о и з в о д с т в е н н о й п р о г р а м м ы
|
Выбор изделий для изготовления в АТК
|
Рис. 2.8. Схема исследования номенклатуры изделий предприятия
|
Формирование множества технологических решений
|
Вывод технологической информации, документации, программ изготовления
|
Рис. 2.9. Схема последовательности разработки процесса изготовления изделий на базе частных ТП
|
Исходные данные по изделию
|
Формирование технологических схем процессов для каждого i-го изделия
|
Формирование массивов частных процессов
|
Формирование последовательностей частных процессов { j*i }
|
Разработка операционной технологии выполнения частных процессов
|
Определение маршрутов выполнения { j*i } и оптимальных последовательностей запуска
|
Корректировка технологичности конструкции изделия
|
Технико-экономический анализ и оптимизация технологических решений
|
2.7.4. Обследование оборудования производственной системы
Эта задача обследования заключается в формировании данных по каждой единице имеющегося (или необходимого) оборудования. Данные включают в себя: возможные виды выполняемых операций; минимальные и максимальные определяющие размеры обрабатываемых изделий; точностные характеристики; режимы обработки; инструментальное обеспечение; временные затраты на переналадку и др. Элементы анализа основного технологического оборудования (ОТО) и вспомогательного технологического оснащения (ВТО) представлены на рис. 2.10. Данные, сведенные в форму карт или машинных массивов по каждой единице ОТО дополняются при обследовании изделий и ТП. Дополнения заключаются в закреплении за оборудованием конкретного изделия (группы изделий) с указанием его кода, вида операций, временных затрат на обработку на данном оборудовании, размеров партий и др. По каждому оборудованию определяется среднее время восстановления (ТВ) по характерным видам отказов, поломок и временные затраты на переналадку для изготовления каждого из закрепленных видов изделий.
На последующих этапах определяется общая номенклатура ВТО, необходимого для изготовления всей номенклатуры и количества закрепленных изделий, оптимальная последовательность запуска партий (по критерию минимального суммарного времени переналадки) и загрузка данного оборудования.
Коэффициент загрузки КЗ определяется выражениями:
или 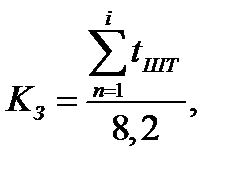
где tф - заданное время функционирования; tо.п - организационные потери; tшт - штучное время изготовления одного изделия; j - количество видов изделий, закрепленных за данной единицей оборудования.
Если: КЗ < 1, то данное оборудование недогружено и за ним можно закреплять изделия на изготовление; КЗ
1 соответствует максимальной загрузке оборудования; КЗ > 1 недопустимо.
2.7.5. Области экономически эффективного использования оборудования
Необходимость экономической оценки целесообразности применения того или иного типа (модели) технологического оборудования возникает в тех случаях, когда какое-либо изделие может изготавливаться с помощью нескольких взаимозаменяемых средств или методов. При этом взаимозаменяемые средства или методы, обеспечивая качественно одинаковые конечные результаты, могут обладать разной производительностью, мощностью приводов, стоимостью, различными производственными условиями эксплуатации и т.п. Современный уровень развития производства технологического обеспечения операций изготовления изделий, как правило, по любой операции предполагает использование нескольких взаимозаменяемых типов (моделей) оборудования. Таким образом, существует проблема выбора технологического оборудования, которую в общем виде можно сформулировать следующим образом: предпочтение в использовании той или иной модели из ряда взаимозаменяемого технологического оборудования должно быть отдано той из них, применение которой обеспечивает получение изделий с заданными параметрами качества при наименьших (по сравнению с другими моделями ряда) затратах.
Взаимосвязанность и взаимозависимость данной проблемы с другими проблемами создания ИПС, обуславливает ее решение на нескольких этапах проектирования производственной системы. На первом этапе (предпроектные исследования и анализ) строятся ряды взаимозаменяемого оборудования для изготовления технологически однородных (однотипных) групп изделий по типовым операциям технологических процессов. В качестве исходных данных для выбора оборудования по одному из критериев на рис. 2.11 приведены области рационального применения видов технологического оборудования в зависимости от серийности производства. На рисунке ОТО – основное технологическое оборудование, ВТО -
Анализ Qi моделей технологического оборудования
|
Анализ основного технологического оборудования
|
Рассматриваемая совокупность технологических операций
|
Анализ вспомогательного технологического оборудования
|
Анализ конструктивных характеристик
|
Анализ технологических показателей
|
Анализ экономических показателей
|
Уровень автоматизации цикла работы станка
|
Вид и размеры рабочей зоны
|
Распространенность и перспективность модели
|
Номенклатура обрабатываемых деталей
|
Уровень автоматизации утилизации отходов
|
Выбор модели ОТО и комплекта ВТО
Выбор совокупности оборудования
для АТК
|
Компоновка производственной зоны
|
Конструктив-ное исполнение
|
Рис. 2.10. Составляющие анализа технологического оборудования
|
- вспомогательное технологическое оснащение, включающее и средства автоматизации.
Следующая задача – определение области экономически эффективного использования оборудования, включенного в ряды и разработка карт выбора оборудования. На этапе синтеза структуры ИПС решаются задачи определения состава технологического оборудования (или комплектов), проектирования необходимого оборудования, создание на его основе автоматизированных комплексов и линий, выполнение расчетов технико-экономических характеристик оборудования в конкретных производственных условиях.
Необходимо учитывать, что экономической оценке предшествует детальный анализ технических характеристик взаимозаменяемого оборудования, рассматриваемого как альтернативное. Наиболее важные технические характеристики – точностные, временные, размерные (габаритные, рабочей зоны, производственной площади), инструментальные (виды и количество инструментов и инструментальных наладок), параметры совместимости и сопряжения с устройствами управления, контроля, транспортирования, загрузки-разгрузки и др.
Только после выбора оборудования по техническим характеристикам целесообразно, если остались альтернативные варианты, проводить экономическую их оценку.
Для сравнительной оценки экономической эффективности оборудования используются показатели минимума годовых приведенных затрат П и удельных дополненных приведенных затрат ПД, определяемые по известным формулам:
П = Сi + Ен Кi min , (2.1)
где Сi – текущие затраты по i –у варианту; Кi - капитальные вложения по этому же варианту; Ен – нормативный коэффициент эффективности капитальных вложений.
(2.2)
где С – себестоимость изготовления изделия с применением того или иного варианта оборудования; К – капитальные вложения в производственные фонды, необходимые для изготовления изделия с применением того или иного варианта оборудования (включая затраты на охрану окружающей среды и утилизацию отходов);
– текущие затраты, связанные с использованием живого труда, не учитываемые в составе себестоимости изделий;
– капитальные вложения в инфраструктуру потребления, обусловленные использованием живого труда; R- количество рабочих, необходимых для реализации варианта технологического оборудования.
Расчет по формуле (2.1) целесообразен для выбора оборудования со значительной долей ручного труда. Для условий автоматизированного производства рекомендуется использование выражения (2.2).
Наряду с проведением расчета затрат по тому или иному варианту, для создания более наглядной и достоверной сравнительной оценки необходимо определить экономические границы, разделяющие области экономически эффективного использования оборудования. Область экономически эффективного использования технологического оборудования представляет собой интервал изменения объема производства продукции, ограниченный минимальными и максимальными его значениями, в котором применение данного способа или средства обеспечивает по сравнению с другими способами или средствами относительно меньшие затраты.
График изменения удельных дополненных приведенных затрат ПД в зависимости от изменения годового объема производства продукции Q приведен на рис. 2.12.
Объем
производства
тыс. шт./год
|
Номенклатура
изделий, шт.
|
Специальные
автоматические линии
и специальное агрегатное оборудование
КА 0,9
|
Агрегатное переналаживаемое оборудование с цикловой автоматикой
КА 0,9
|
Переналаживаемые
автоматические линии, обрабатывающие и сборочные центры
КА < 0,9
|
Гибкие автоматизированные технологические модули
КА > 0,5
|
Гибкие автоматизированные
технологические
комплексы
КА > 0,5
|
Универсальное оборудование с ЧПУ.
Автоматическое выполнение основной операции. КА 0,5
|
Роторные
комплексы и
линии.
КА > 0,9
|
Рис. 2.11. Области рационального применения технологического оборудования
Рис. 2.12. Области экономически эффективного использования технологического оборудования
|
На графике: кривые, характеризующие функцию f (ПД , Q) при использовании оборудования моделей М1 и М2; Qmin , Qmax , Qкрит - минимальный, максимальный и критический объемы производства соответственно. Точка пересечения кривых Qкрит соответствует критическому объему производства (при котором ПД М1 = ПД М2 ) и выделяет две области экономически эффективного использования средств: первая область – область эффективного использования оборудования М1 – представляет собой интервал [Qmin, Qкрит ] ; вторая область – область эффективного использования оборудования М2 – представлена интервалом [Qкрит , Qmax ]. Применение в первой области средства М1 так же, как и применение во второй области средства М2, обеспечивает относительно меньшую величину дополненных приведенных затрат, приходящихся на единицу продукции.
2.7.6. Определение состава оборудования новых и реконструируемых предприятий
Оснащение проектируемого (реконструируемого) предприятия или части его технологическим оборудованием является весьма существенным фактором перспективного развития производства. Как правило, проектант подбирает состав оборудования для проектируемого предприятия, руководствуясь различными каталогами, перечнями рекомендуемых для данной технологии агрегатов, установок, контрольно-измерительной аппаратуры, нормами технологического проектирования и другой нормативно-технической документацией.
Наличие карт экономически эффективных областей использования оборудования позволяет выбирать наиболее подходящее для заданных условий производства оборудование без дополнительных расчетов экономической эффективности. В общем виде карта выбора оборудования представляет собой систематизированное изложение типового маршрутного ТП, разработанного применительно к изготовлению определенной технологически однородной группы изделий.
По каждой типовой операции ТП в карте приводится ряд взаимозаменяемого технологического оборудования, применяемого для выполнения этой операции, с указанием областей экономически эффективного использования каждой модели ряда, часовой производительности данной модели, а также величины удельных приведенных затрат, связанных с применением оборудования на границах областей его экономически эффективного использования.
В карте дается краткая характеристика технологически однородной группы изделий, для которых она предназначена, а также единица измерения объемов производства этих изделий.
В зависимости от степени универсализации конкретного вида оборудования, оно может использоваться в разных ТП изготовления технологически однородных групп изделий. Кроме того, в едином технологическом комплексе могут одновременно применяться разные модели оборудования, различающиеся производительностью, стоимостью, величиной эксплуатационных расходов и т.п. Вследствие этого их совместное использование по-разному влияет на суммарную величину дополненных приведенных затрат, приходящихся на единицу продукции. На уровень затрат оказывают также влияние формы и методы организации производства.
Таким образом, возникает необходимость в оптимизации комплекта технологического оборудования. Для этого опять же целесообразно использовать карты экономически эффективного использования оборудования. Если на предварительном этапе в состав комплекта вошли модели как специального и специализированного оборудования, так и универсального, то образование оптимального (экономически целесообразного) комплекта из такого оборудования осуществляется на основе дополнительно разрабатываемых карт выбора универсального оборудования. Для разработки таких карт выбирается типовой объект производства и для выбора области экономически эффективного использования оборудования при изготовлении конкретных изделий, отличающихся от типового (или нескольких типовых) объекта производства предварительно приводят эти изделия к типовому с помощью коэффициентов приведения. Коэффициенты приведения рассчитывают как отношение производительности той или иной модели оборудования при изготовлении конкретного объекта производства ωК к производительности этого же оборудования при изготовлении типового объекта производства ωТ , т.е. kпр = ωК / ωТ , где kпр - коэффициент приведения. Коэффициент приведения применяют для получения приведенного объема производства конкретного изделия Qпр и с этой целью фактический объем производства этого изделия Qф делят на коэффициент приведения, т.е. Qпр = Qф / kпр .
Применение карт выбора универсального оборудования осуществляется на основе приведенных объемов производства в следующем порядке:
анализируя программу выпуска конкретных изделий, определяют номенклатуру изделий, подлежащих совместному изготовлению на данной типовой технологической операции;
по каждому объекту производства определяют приведенный объем производства;
суммируют приведенные объемы производства для совместного изготовления по данной технологической операции;
по суммарному приведенному объему производства выбирают по карте модели оборудования обычным методом, применяемым для карт выбора специального оборудования.
2.7.7. Обследование организационной структуры производства
Решение данной задачи заключается в определении параметров, характеристик и изменений, которые могут возникнуть в производственной системе в результате запуска новых изделий. Параметры и характеристики организационной структуры составляют планово-организационную информацию, характеризующую производство и его эффективность (коэффициент сменности, пропускная способность участков и линий, формы специализации производственных подразделений, характеристики потоков, ритмичность, параметры системы планирования, характеристики «узких» мест и др.).
Дата добавления: 2015-09-11; просмотров: 1179;