Примеры систем автоматического управления
Отметим, что первыми промышленными системами автоматического управления считаются регулятор уровня воды в котле паровой машины и центробежный регулятор скорости вращения вала паровой машины.
На рис. 1.9 представлена простейшая структура системы регулирования скорости вращения двигателя постоянного тока, которая содержит объект управления – двигатель (Дв), скорость вращения которого y является управляемой координатой (возмущение f характеризует влияние момента нагрузки на скорость вращения); управляющее устройство включает тахогенератор (Тг), напряжение на выходе которого пропорционально скорости вращения y; устройство сравнения e = v – x, вкачестве которого может применяться суммирующий операционный усилитель или потенциометрический мостик; УП – усилительно-преобразовательные устройства, включающие предварительные усилительные каскады и корректирующие устройства, которые придают системе определенные свойства; УМ – усилитель мощности. Входной сигнал v ввиде напряжения задает режим работы системы. Если v = const, то система будет системой стабилизации. Изменяя v во времени, можно изменять скорость вращения, и систему можно рассматривать как систему программного управления или следящую.
|
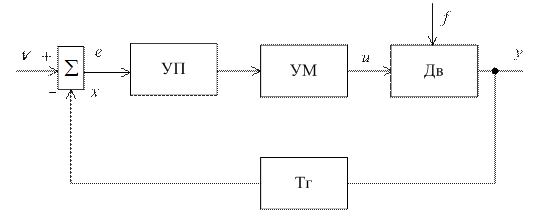
Рис. 1.9
Если v = const при заданной величине f, то на выходе имеем некоторую номинальную скорость yН, которой будут соответствовать номинальное значение напряжения тахогенератора хН, ошибка еН и соответственно напряжение управления uН, поддерживающее номинальную скорость вращения. Увеличение момента нагрузки f приведет к уменьшению величин y и x, возрастанию сигнала ошибки e, что обусловит увеличение подаваемого напряжения u на двигатель. Таким образом, скорость возрастет до номинальной (или близкой к номинальной). Если f уменьшить, то процесс регулирования будет идти в обратном направлении. Таким образом, происходит автоматическая компенсация влияния нагрузки на скорость двигателя и поддержание скорости в заданных пределах.
В качестве следующего примера рассмотрим цифровой электропривод, структура которого представлена на рис. 1.10.
Рис. 1.10
Управляемой координатой является угол поворота y некоторого механизма (M), подсоединенного к двигателю (Дв) через редуктор (P) (например одна из степеней подвижности промышленного робота). ДУ – датчик угла, выходом которого является напряжение, пропорциональное углу поворота. Это напряжение поступает на аналого-цифровой преобразователь (АЦП). Сигнал x представляет собой цифровой код угла и поступает на микроЭВМ (или микропроцессор). На микроЭВМ поступает (например от ЭВМ более высокого уровня) требуемый код угла поворота. В простейшем случае микроЭВМ производит сравнение сигналов v и x , т. е. выступает в роли устройства сравнения. В более общем случае микроЭВМ реализует некоторый закон управления (например ПИД-закон) в цифровой форме. Далее сигнал е в цифровом коде поступает на цифроаналоговый преобразователь (ЦАП), после которого через элементы УП и УМ воздействует на двигатель. Такая система может работать в режиме позиционирования, отрабатывая заданный угол v = const, либо в режиме непрерывной отработки угла, изменяющегося по определенной программе.
Существенным отличием этой системы является наличие элементов цифровой техники (ЦАП, АЦП, микроЭВМ), для которых характерно квантование сигналов по уровню и по времени.
Дата добавления: 2015-02-07; просмотров: 886;