Изучение зависимости между структурой и свойствами стали после различных видов термической обработки
Термической обработкой называют технологические процессы, состоящие из нагрева и охлаждения металлических изделий с целью изменения их структуры и свойств. При термической обработке стали протекают фазовые превращения. Они вызваны тем, что вследствие изменившихся условий (температуры) новое состояние оказывается более устойчивым, чем старое, так как обладает меньшим запасом свободной энергии. Характер фазовых превращений зависит от скорости охлаждения. Превращения, протекающие при медленном охлаждении, близкие к равновесным; описываются диаграммой «железо-цементит». Диаграмма является также основой для изучения термической обработки. Она указывает каким видам термической обработки может быть подвергнут сплав и до каких температур требуется производить нагрев. Участок диаграммы «железо-цементит», необходимый для назначения термической обработки стали, представлен на рисунке 5.1.
|
|
|
|
|
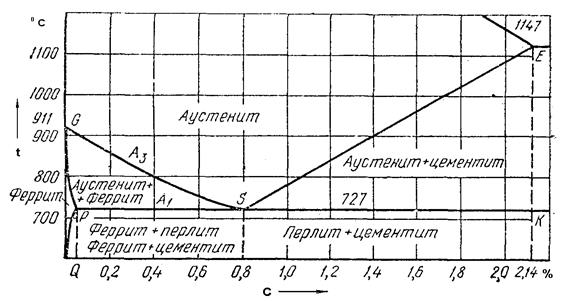
Рисунок 5.1 – «Стальной» участок диаграммы «железо-цементит»
Приведем общепринятые обозначения критических точек, необходимых для термической обработки стали. Критические точки обозначаются буквой А (фр. Arret – остановка). Точка А1 лежит на линии РSК и соответствует превращению аустенит – перлит. Точка А3 лежит на линии GSЕ и соответствует началу выделения (или окончанию растворения) феррита в доэвтектоидных сталях или цементита вторичного в заэвтектоидных сталях. Чтобы отличить критическую точку при нагреве от критической точки при охлаждении, после буквы А ставят буквы «с» и «r», соответственно (Аc1, Аr1, Аc3, Аr3). Точку Аc3 для заэвтектоидной стали часто обозначают как точку Асm.
Основными видами термической обработки стали являются отжиг первого рода, отжиг второго рода, закалка, отпуск.
Отжиг первого рода. Отличительная особенность отжига первого рода состоит в том, что его проведение не обусловлено фазовыми превращениями. Основными параметрами отжига первого рода являются температура нагрева и время выдержки при этой температуре. Скорости нагрева и охлаждения при этом имеют второстепенное значение. Отжиг первого рода частично или полностью устраняет отклонения от равновесного состояния, имеющиеся в стали после литья, обработки давлением, сварки и других технологических операциях. В зависимости от того, какие отклонения от равновесного состояния устраняются, различают гомогенизационный, рекристаллизационный иотжиг для снятия внутренних напряжений.
Гомогенизационный отжиг предназначен для устранения дендритной ликвации в литой стали. При этом сталь подвергается длительной выдержке (до 48 часов) при 1000 оС. При высокой температуре подвижность атомов в кристаллической решетке высокая и с течением времени за счет процессов диффузии происходит постепенное выравнивание химического состава. Однако усреднение химического состава происходит в пределах одного зерна, т.е. устраняется в основном дендритная ликвация. После гомогенизации металл обладает повышенной пластичностью и легко поддается пластической деформации.
Рекристаллизационный отжиг.Холодная пластическая деформация вызывает изменение структуры металла и его свойств. Сдвиговая деформация вызывает увеличение плотности дефектов кристаллической решетки, таких как вакансии, дислокации. Все эти процессы ведут к тому, что прочность металла постепенно увеличивается, пластичность падает, т. е. возникает наклеп (нагартовка). Дальнейшая деформация такого металла невозможна, т. к. происходит его разрушение. Для снятия эффекта упрочнения применяют рекристаллизационный отжиг, т.е. нагрев металла до температур выше начала рекристаллизации, выдержку с последующим медленным охлаждением. Температура отжига на 100–200 оС выше температуры рекристаллизации, определяемой из выражения Трек = 0,4×Тпл.
Продолжительность такого отжига зависит от размеров детали и в среднем составляет от 0,5 до 2 часов. В процессе рекристаллизационного отжига происходит образование зародышей новых зерен и последующий рост этих зародышей. Постепенно старые деформированные зерна исчезают. Количество дефектов в кристаллической решетке уменьшается, наклеп устраняется, и металл возвращается в исходное состояние.
Рекристаллизационный отжиг может применяться как предварительная, промежуточная, так и как окончательная термообработка. Как предварительная термообработка он применяется перед холодной деформацией, если исходное состояние металла неравновесное и имеет какую-то степень упрочнения. Как промежуточная операция рекристаллизационный отжиг применяется между операциями холодной деформации, если суммарная степень деформации слишком велика и запасов пластичности металла не хватает. Как окончательный вид отжига его применяют в том случае, если потребитель требует поставки полуфабрикатов в максимально пластичном состоянии.
Отжиг для снятия внутренних напряжений. Внутренние напряжения в металле могут возникать в результате различных видов обработки. Это могут быть термические напряжения, образовавшиеся в результате неравномерного нагрева, различной скорости охлаждения отдельных частей детали после горячей деформации, литья, сварки, шлифовки и резания. Могут быть структурными, т. е. появившиеся в результате структурных превращений, происходящих внутри детали в различных местах с различной скоростью. Внутренние напряжения в металле могут достигать большой величины и, складываясь с рабочими, т. е. возникающими при работе, могут неожиданно превышать предел прочности и приводить к разрушению. Этот отжиг проводится при температурах ниже температуры рекристаллизации: tотж=0,2-0,3Тпл. Повышенная температура облегчает скольжение дислокаций и, под действием внутренних напряжений, происходит их перераспределение, т. е. из мест с повышенным уровнем внутренних напряжений дислокации перемещаются в области с пониженным уровнем. Происходит как бы разрядка внутренних напряжений. При комнатной температуре этот процесс будет длиться в течение нескольких лет. Увеличение температуры резко увеличивает скорость разрядки, и продолжительность такого отжига составляет несколько часов.
Отжиг второго рода.При отжиге второго рода сталь нагревается на 30–50 оС выше критических точек Аc1 или Аc3 с последующим медленным охлаждением, как правило, вместе с печью. На диаграмме изотермического превращения аустенита (рисунок 5.2) скорость охлаждения при отжиге соответствует кривой V1.
В зависимости от температуры нагрева стали различают полныйинеполный отжиг. При полном отжиге нагрев ведется на 30–500 выше точки Ас3, при неполном – в область меж критических температур (Ас1 < tнагрева < Ас3). Основными целями отжига являются, перекристаллизация стали и устранение внутренних напряжений. Полный отжиг приводит к полной перекристаллизации (все составляющие исходной структуры при температуре нагрева переходят в аустенит). При неполном отжиге перекристаллизацию испытывает только перлит; феррит (в доэвтектоидной стали) и цементит вторичный (в заэвтектоидной стали) перекристаллизовываются частично.
|
Рисунок 5.2 – Диаграмма изотермического превращения аустенита эвтектоидной стали
Отжиг приводит к снижению твердости, повышению пластичности и получению однородной мелкозернистой структуры. При медленном охлаждении стали, нагретой в аустенитную область, все фазовые превращения проходят в соответствии с диаграммой «железо-цементит». Для доэвтектоидных сталей, как правило, проводится полный отжиг, для заэвтектоидных – неполный.
На структуру стали оказывает влияние температура отжига. Отжиг при температурах, значительно превышающих Ас3, приводит к перегреву стали. У перегретой стали величина, форма и расположение зерен будут иными. Так, при нагреве стали 45 до 1000 оС (нормальный отжиг проводится при 860 оС) зерна аустенита вырастают до значительных размеров. В результате этого при охлаждении образуются крупные зерна перлита, а феррит выделяется в виде крупных игл (пластин) внутри перлита по определенным кристаллографическим плоскостям (рисунок 5.3). Такая структура носит название видманштетовой. Сталь с видманштетовой структурой имеет низкую ударную вязкость. Перегретую крупнозернистую сталь можно исправить путем нормального отжига. Видманштетова структура характерна также для литой стали, для сварных швов, для кованой стали, если ковка закончилась при высокой температуре.
При неполном отжиге заэвтектоидных сталей нагрев проводится на 30–50 оС выше Ас1. Так как в заэвтектоидных сталях количество цементита вторичного по сравнению с перлитом относительно невелико, при неполном отжиге они испытывают практически полную перекристаллизацию. Не растворившиеся при нагреве частицы цементита вторичного (присутствующие в структуре в небольшом количестве) являются центрами кристаллизации для цементита, образующегося при последующем охлаждении ниже точки Ас1 в результате эвтектоидного распада аустенита. В этом случае цементит принимает зернистую форму. Такой отжиг часто называют сфероидизирующим.
а) – при 860 оС (правильный режим); б) – при 1000 оС (перегрев)
Рисунок 5. 3 – Микроструктура стали 45 после отжига
В результате сфероидизирующего отжига образуется зернистый перлит (рисунок 5.4). Изменение формы включений цементита позволяет повышать вязкость стали; облегчает процесс обработки резанием. Такая структура стали является идеальной перед закалкой.
В заводской практике с целью экономии времени и получения более стабильных результатов все большее распространение получает так называемый изотермический отжиг. В этом случае сталь, нагретая выше критических точек Ас1 или Ас3, охлаждается с любой скоростью до температуры, лежащей на 50–100 оC ниже равновесной точки А1, и при этой температуре выдерживается в течение времени, необходимого для полного распада аустенита. Так как превращение А®П идет при постоянной температуре и во всем объеме детали одновременно, такой способ отжига позволяет получить равномерную структуру по всему объему детали. Такой вид отжига применяется для крупногабаритных деталей ответственного назначения. В дальнейшем охлаждение до комнатной температуры ведется с любой скоростью.
Разновидностью отжига является нормализация. Особенностью нормализации является то, что охлаждение проводится на воздухе. После нормализации среднеуглеродистые стали имеют тот же фазовый состав, что и после отжига, однако дисперсность фаз в этом случае выше (рисунок 5.5), вместо перлита образуется структура близкая к сорбиту. Это приводит к повышению твердости и прочности материала. Нормализация является более дешевой термической обработкой, чем отжиг. Для низкоуглеродистых сталей (С < 0,3 %) разница в структуре и свойствах материалов, подвергнутых отжигу и нормализации, невелика. Эти стали рекомендуется подвергать не отжигу, а нормализации.
![]() | ![]() |
Рисунок 5.4 – Микроструктура зернистого перлита заэвтектоидной стали | Рисунок 5.5 – Микроструктура доэвтектоидной стали 45 после нормализации |
Для среднеуглеродистых сталей различие в свойствах нормализованной и отожженной сталей более значительно. В этом случае нормализация не может заменить отжиг. Для этих сталей нормализацией часто заменяют более дорогую операцию – улучшение, состоящую в двойной обработке, включающей закалку и высокий отпуск.
Закалка. Закалкой называется такой вид термической обработки, который заключается в нагреве на 30–50 оС выше точки Ас3 или Ас1, выдержке для завершения фазовых превращений и последующем охлаждении со скоростью, как правило, выше критической Vк. При охлаждении со скоростью, выше критической, аустенит переохлаждается ниже температуры точки Мн, при которой атомы железа и углерода практически теряют диффузионную подвижность, и происходит бездиффузионная перестройка гранецентрированной решетки аустенита в тетрагональную объёмно-центрированную решетку мартенсита. При этом весь углерод остается в твердом растворе Fеg(С) ® Fеa(С). Таким образом, мартенсит является пересыщенным твердым раствором углерода в a-железе. Мартенсит имеет игольчатое строение. Размер игл мартенсита определяется величиной исходного зерна аустенита. Чем больше зерно аустенита, тем крупнее размер игл образовавшегося мартенсита. При нормальной закалке образуется мелкоигольчатый мартенсит. Высокая твердость и прочность мартенсита объясняется искажением решетки вследствие образования пересыщенного твердого раствора. Вследствие образования большого количества дефектов кристаллического строения пластическая деформация закаленной стали затруднительна и она склонна к хрупкому разрушению.
В зависимости от температуры нагрева различают полную и неполную закалку. В случае нагрева под неполную закалку (выше Ас1, но ниже Ас3) доэвтектоидная сталь имеет структуру аустенита и феррита, а заэвтектоидная – аустенита и цементита вторичного. Количество избыточных фаз (феррита или цементита) зависит от температуры закалки. Чем ближе температура нагрева к точке Ас3, тем меньше в структуре закаленной стали избыточных фаз.
Отпуск.После закалки сталь подвергают отпуску. Под отпуском понимается совокупность операций, заключающихся в нагреве закаленной стали до температуры ниже критической точки Ас1, выдержке и охлаждении до комнатной температуры.Практическими целями отпуска являются уменьшение закалочных напряжений, получение нужного комплекса механических свойств (прочности, пластичности и вязкости).
Отпуск приводит к снижению твердости, прочности и повышению пластичности. Причем влияние на указанные свойства тем больше, чем выше температура отпуска.
В зависимости от температуры нагрева различают три разновидности отпуска: низкий, средний и высокий.
Низкий отпуск проводят путем нагрева закаленной стали до 200 оС. При этом образуется структура мартенсита отпущенного. Низкий отпуск частично снимает внутренние напряжения и несколько повышает вязкость. Твердость при низком отпуске практически не снижается. Такой отпуск наиболее часто применяется при термической обработке инструментальных сталей и изделий после цементации.
При среднем отпуске нагрев закаленной стали производится до температур 350–450оС, при этом образуется структура троостита отпуска. Троостит отпуска состоит из дисперсных частиц феррита и цементита. Сталь со структурой троостита отпуска имеет высокий предел упругости. Поэтому средний отпуск обычно применяют при термической обработке рессор и пружин.
При высоком отпуске нагрев закаленной стали производится до температур 500–650 оС; образуется структура – сорбит отпуска, представляющий собой смесь укрупненных частиц феррита и цементита округлой формы. Сорбит отпуска имеет хорошее сочетание свойств: прочность, пластичность и вязкость. Твердость сорбита составляет 300–350 НВ. Закалка стали с последующим высоким отпуском на сорбит носит название термического улучшения. Эта обработка рекомендуется для среднеуглеродистых конструкционных сталей.
Дата добавления: 2018-11-25; просмотров: 2341;