Структура и свойства углеродистой стали в равновесном состоянии
Под равновеснымпонимается такое состояние, при котором все фазовые превращения в сплаве полностью закончились в соответствии с диаграммой состояния [1, 2]. Это имеет место только при очень малых скоростях охлаждения (нагрева). Равновесное состояние соответствует минимальному значению свободной энергии и не подвергается самопроизвольному изменению во времени. Поэтому оно называется стабильным.
Превращения, протекающие в сталях в равновесном состоянии, описываются диаграммой «железо-цементит», представленной на рисунке1.1.
Рисунок 1.1 – Диаграмма «железо-цементит»
В железоуглеродистых сплавах могут присутствовать следующие твердые фазы: феррит, аустенит, цементит.
Феррит – твердый раствор внедрения углерода в a-железе, имеющем объёмно-центрированную кубическую решетку. На диаграмме «железо-цементит» существуют две области феррита – высокотемпературная область АNН и низкотемпературная область GPQ. Максимальная растворимость в высокотемпературной области составляет 0,10 % – точка Н, в низкотемпературной области 0,02 % – точка Р. Содержание углерода при комнатной температуре – 0,01 %. Феррит мягок и пластичен (sВ = 200–300 МПа, d = 20–50 %, 80–100 НВ).
Аустенит – твердый раствор внедрения углерода в g-железе, имеющем гранецентрированную кубическую решетку. На диаграмме «железо-цементит» аустенит занимает область NJESG. Максимальная растворимость углерода в аустените 2,14 % – точка Е. По механическим свойствам аустенит близок к ферриту. Горячую обработку давлением проводят в области существования аустенита (однофазный твердый раствор характеризуется высокой пластичностью).
Цементит – химическое соединение железа с углеродом – карбид железа, химическая формула которого Fe3С. Содержание углерода в цементите равно 6,67 %. Цементит обладает высокой твердостью (» 800 HV) и хрупкостью. Он имеет сложную ромбическую решетку. Она состоит из ряда октаэдров, оси которых расположены под некоторыми углами друг к другу.
Кристаллизация сплавов, содержание углерода в которых меньше 0,5 % (точка В), начинается с выделения из жидкого раствора кристаллов феррита. При содержании углерода больше 0,5 % стали кристаллизуются с выделением аустенита.
Сплавы, содержащие углерод от 0,1 % (точка Н) до 0,5 % (точка В), претерпевают при температуре 1499 oC (линия НJB) перитектическое превращение, заключающееся в том, что жидкий раствор, имеющий при этой температуре концентрацию, соответствующую точке В (0,5 % С), взаимодействуя с выделившимися из него кристаллами феррита концентрации точки Н (0,1 % С), образует новую фазу – кристаллы аустенита концентрации точки J (0,16 % С):
ФН + ЖВ ® АJ.
При дальнейшем снижении температуры феррит, оставшийся после перитектического превращения, перекристаллизовывается в аустенит. В сталях с содержанием углерода больше 0,16 % оставшаяся жидкость затвердевает с образованием аустенита. Ниже линий NJ и JE сплавы имеют однородную аустенитную структуру.
При температуре 727 oС (линия PSK) сплавы претерпевают эвтектоидное превращение. При эвтектоидном превращении аустенит, имеющий при этой температуре концентрацию углерода, соответствующую точке S (0,8 % С), распадается с образованием эвтектоидной смеси – перлита (феррита состава точки Р (0,02 % С) и цементита):
AS ® ФР + Ц.
Эвтектоидная смесь феррита и цементита, образующаяся в результате эвтектоидного распада аустенита называетсяперлитом.
В сплавах с содержанием углерода менее 0,8 % (точка S) эвтектоидному превращению предшествует выделение из аустенита феррита, которое протекает в интервале температур, ограниченных линиями GS и РS. При этом в оставшемся аустените концентрация углерода изменяется по линии GS. В сплавах с содержанием углерода более 0,8 % (точка S) эвтектоидному превращению предшествует выделение из аустенита цементита. Выделение цементита протекает в интервале температур, ограниченных линиями ES и SK. В этом случае концентрация углерода в оставшемся аустените изменяется по линии ES.
Железоуглеродистые сплавы в зависимости от содержания углерода делятся на три группы: техническое железо, стали, чугуны.
Техническое железо – это сплавы с содержанием углерода менее 0,02 %(точка Р). Как следует из диаграммы «железо-цементит», техническое железо имеет структуру феррита (или феррита и цементита третичного, который в виде отдельных мелких включений располагается по границам зерен феррита) (рисунок 1.2, а). Третичный цементит выделяется из феррита в результате снижения растворимости углерода при уменьшении температуры от эвтектоидной до комнатной. Предельная растворимость углерода в феррите ограничивается линией GPQ. По свойствам техническое железо подобно ферриту.
Стали – это сплавы с содержанием углерода от 0,02 % (точка Р) до 2,14 % (точка Е). В структуре стали по мере увеличения содержания углерода возрастает доля цементита и уменьшается доля феррита. Это приводит к повышению твердости и прочности стали и снижению ее пластичности, изменению физических и технологических свойств. В зависимости от содержания углерода стали по своей структуре делятся на доэвтектоидные, эвтектоидные и заэвтектоидные.
Доэвтектоидные стали содержат от 0,02 % углерода (точка Р) до 0,8 % углерода (точка S). Они имеет структуру феррита (светлые зерна) и перлита (темные зерна) (рисунок 1.2, б, в). С увеличением содержания углерода прямо пропорционально увеличивается содержание перлита. При концентрации углерода в стали 0,8 % количество перлита равно 100 %. Зная площадь, занимаемую перлитом, можно определить содержание углерода в углеродистой стали:
С = ,
где А – площадь, занимаемая перлитом.
Эвтектоидная сталь содержит 0,8 % углерода (точка S) и состоит из перлита (рисунок 1.2, г).
Заэвтектоидная сталь содержит от 0,8 % углерода (точка S) до 2,14 % углерода (точка Е). Ее структура состоит из перлита и цементита (рисунок 1.2, д).
Таким образом, структура, а, следовательно, и свойства стали определяются количеством углерода в ней. Доэвтектоидные стали, содержащие до 0,8 % углерода, являются конструкционными, предназначенными для изготовления деталей машин (машиностроительные стали), конструкций и сооружений (строительные стали). В значительной мере свойства углеродистых сталей, а, следовательно, и область их применения зависят от содержания в них вредных примесей серы и фосфора. Чем меньше их в стали, тем выше ее качество.
Рисунок 1.2 – Микроструктура технического железа (а), доэвтектоидных сталей с содержанием углерода 0,20 % (б) и 0,45 % (в), эвтектоидной (г) и заэвтектоидной (д) сталей
Стали обыкновенного качества, наиболее дешевые, являются конструкционными сталями общего назначения и содержат до 0,07 % фосфора, 0,06 % серы, 0,06–0,49 % углерода. По гарантируемым свойствам они подразделяются на три группы – А, Б, В. В сталях группы А – гарантируются механические свойства, группы Б – химический состав; в сталях группы В гарантируются механические свойства и химический состав.
Сталь группы А маркируется буквами Ст и номером 0, 1, 2, ... 6, например, Ст1. В сталях группы Б перед буквами Ст ставится буква Б, например, БСт2. В сталях группы В перед буквами Ст ставится буква В, например, ВСт3. С увеличением условного номера повышается содержание углерода в стали, что приводит к увеличению прочностных свойств, к снижению пластичности и свариваемости.
Стали группы А применяются для изготовления рядового проката (швеллеров, уголков, листов, прутков, труб и др.) используемого для клепанных и болтовых конструкций, а также для малонагруженных деталей машин (валов, осей, зубчатых колес, болтов и т. д.) не подвергаемых нагреву в процессе обработки.
Стали группы Б применяются для изготовления изделий, подвергаемых нагреву (горячей обработке давлением, сварке, термической обработке).
Стали группы В применяются для изготовления сварных конструкций, подвергаемых расчетам на прочность.
В конце марки стали ставятся буквы «кп», «пс», «сп». Буквы «кп» показывают, что сталь кипящая, «пс» – полуспокойная, «сп» – спокойная.
Качественнаяконструкционная сталь по сравнению со сталью общего назначения содержит вдвое меньше серы и фосфора и отличается более высокими механическими свойствами. Она маркируется цифрами, например, 08, 10, … 80, показывающими содержание углерода в сотых долях процента.
Низкоуглеродистые стали, содержащие углерода до 0,25 %, обладают низкой прочностью, но высокой пластичностью и применяются для изготовления изделий листовой холодной штамповкой (05кп…10), а также для деталей, упрочняемых цементацией, и для различных сварных соединений (Сталь 15, Сталь 20). Кроме того, из них изготавливают болты, шпильки, гайки, валики и другие детали неответственного назначения.
Среднеуглеродистые стали марок 30-50 предназначаются для ответственных деталей высокой прочности с вязкой сердцевиной (зубчатые колеса, шатуны, коленчатые валы, распределительные валы, винты, оси, втулки, рычаги и др.). Как правило, детали из этих сталей подвергаются улучшению (вид термической обработки).
Высокоуглеродистые стали 55-85 применяются для пружин, рессор, а также деталей высокой прочности: прокатных валков (сталь 60), крановых колес (сталь 75), дисков муфт сцепления (сталь 85) и др. Детали из этих сталей подвергаются упрочнению методами термической обработки (закалке и отпуску).
Для изготовления различных инструментов применяется углеродистая инструментальная сталь, содержащая углерода от 0,7 до 1,3 %. Эта сталь производится следующих марок: У7 - У13 (качественная) или У7А - У13А (высококачественная). Здесь «У» означает «углеродистая инструментальная сталь», число после «У» - содержание углерода в десятых доля процента (например, У12 содержит углерода 1,2 %). Стали марок У7 и У8 вязче других, так как не имеют в структуре цементита, и они идут на изготовление ударных инструментов – молотков, зубил, топоров, кернеров, стамесок, долот, штампов и т. д.
Стали У10 и У11 имеют несколько меньшую вязкость и немного большую твердость (т.к. в их структуре содержится небольшой количество цементита) и используются для изготовления резцов, сверл, метчиков, лерок.
Стали У12 и У13 обладают низкой вязкостью и высокой твердостью и используются для изготовления инструмента, не испытывающего ударных нагрузок (напильников, бритв, рашпилей и т. п.).
Закалка стали
Закалкой называется вид термической обработки, который заключается в нагреве стали на 30–50 оС выше температур критических точек Ас1 или Ас3 ( рисунки 2.1 и 2.2), выдержке при этих температурах для завершения фазовых превращений и последующем охлаждении в область мартенситного превращения со скоростью выше критической Vк (рисунок 2.3).
|

|
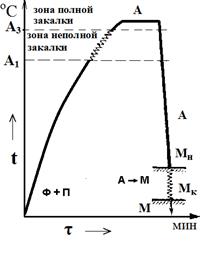
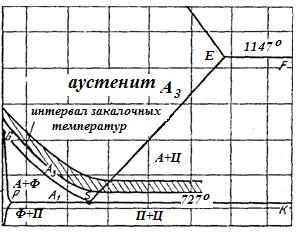
0,2 0,6 1,0 1,4 1,8 2,2 2,6 %
С
Рисунок 2.1 – Температурный режим закалки стали | Рисунок 2.2 – «Стальной» участок диаграммы «Fe–Fe3C» |
Рисунок 2.3 – Диаграмма изотермического превращения переохлажденного аустенита
Под критической скоростью закалки понимается минимальная скорость охлаждения, обеспечивающая бездиффузионное превращение аустенита в мартенсит [3, 4]. Целью закалки является повышение твердости, прочности и долговечности механизмов машин и инструмента.
В зависимости от температуры нагрева закалку подразделяют на полную и неполную. В первом случае сталь нагревается выше температур Ас3 или Асm в область аустенита. Во втором – выше температуры Ас1, но ниже Ас3 или Асm в область, где наряду с аустенитом в доэвтектоидной стали присутствует феррит, а в заэвтектоидной – цементит (рисунок 2.2).
Все доэвтектоидные стали (< 0,8 % С) должны подвергаться полной закалке. Нагрев осуществляется на 30–50 оС выше точки Ас3 (рисунок 2.2, линия GS). При этом сталь с исходной структурой феррита и перлита при нагреве переходит в аустенитное состояние. При последующем охлаждении со скоростью выше критической (рисунок 2.3) аустенит превращается в закалочную структуру – мартенсит. Такой нагрев является оптимальным, так как обеспечивает мелкое зерно аустенита при нагреве и мелкоигольчатый мартенсит с вязким изломом после охлаждения. Нагрев доэвтектоидной стали значительно выше точки Ас3 приводит к перегреву (укрупнению зерна аустенита), а последующее быстрое охлаждение приводит к получению крупноигольчатого мартенсита, что ухудшает вязкость стали. Перегрев стали, кроме того, способствует обезуглероживанию поверхности и образованию трещин при закалке. Этого следует избегать.
Нагрев доэвтектоидной стали в область межкритических температур (выше Ас1, но ниже Ас3) не обеспечит растворения исходного феррита в аустените. Аустенит при закалке превратится в мартенсит, а оставшийся феррит снизит прочностные свойства стали. Поэтому такой нагрев для доэвтектоидной стали является недостаточным (неполная закалка), структурные изменения в доэвтектоидных сталях при закалке происходят по схеме:
Заэвтектоидные стали (> 0,8 % С) подвергаются неполной закалке, т. е. нагреваются до температуры на 30...50 оС выше точки Ас1 (727 оС). При таком нагреве из перлита образуется аустенит, а избыточный цементит сохраняется. После охлаждения со скоростью выше критической аустенит превращается в структуру закаленной стали – мартенсит, а цементит без изменения сохраняется в мартенситной основе и обеспечивает большую твердость и износостойкость инструментальных сталей.
В реальных условиях наблюдаются нарушения режимов нагрева и имеет место неполная закалка изделий из доэвтектоидных сталей (вследствие недостаточной температуры печи), а также полная закалка изделий из заэвтектоидных сталей (вследствие повышенной температуры печи), приводящие к браку термообработки – снижению твердости.
В заэвтектоидных сталях структурные превращения при закалке происходят по следующей схеме:
Таким образом, для заэвтектоидных сталей оптимальной будет неполная закалка.
Нагрев выше точки Асm (линия SE) приводит к образованию высокоуглеродистого аустенита (вследствие растворения в нем цементита), обеспечивающего после охлаждения крупноигольчатый (вследствие перегрева) мартенсит и большее количество остаточного аустенита в связи с тем, что в таком (высокоуглеродистом) аустените конец мартенситного превращения (рисунок 2.4, точки Мк) сдвигаются в область отрицательных температур.
Рисунок 2.4 – Изменение температурного интервала мартенситного превращения в зависимости от содержания углерода в аустените
В соответствии с этой схемой после закалки сталей с содержанием углерода более 0,5 % в структуре всегда будет присутствовать остаточный аустенит (см. точку пересечения линий конца мартенситного превращения и температуры охлаждающей жидкости). Остаточный аустенит ухудшает свойства закаленной стали.
Нагрев под закалку производится в печах периодического и непрерывного действия. Для предотвращения обезуглероживания и окисления поверхностного слоя заготовок применяются ванны, в которых изделие нагревается в расплавленных солях или металлах.
Скорость охлаждения регулируется видом охлаждающей среды, в качестве которой наиболее часто применяются минеральное масло, вода, водные растворы солей, кислот, щелочей. Для углеродистых сталей необходимая скорость достигается при охлаждении в воде (в водных растворах), для легированных – в масле или на воздухе.
Мартенситное превращение носит бездиффузионный характер, т. е. не сопровождается диффузионным перераспределением углерода и железа в решетке. При мартенситном превращении происходит лишь переход кубической гранецентрированной решетки аустенита (g-твердого раствора) в тетрагональную объемно-центрированную решетку a-твердого раствора. Особенность мартенситного превращения состоит в том, что весь углерод, находящийся в аустените (g-твердом растворе), переходит в a-твердый раствор. Пересыщение углеродом a-твердого раствора вызывает искажение ОЦК решетки Fea, т. е. приводит к образованию тетрагональной (с/а > 1) кристаллической решетки. Поэтому структура закаленной стали – мартенсит – представляет собой пересыщенный твердый раствор углерода в a-железе.
Особенностью мартенсита является его высокая твердость и прочность. В сталях с содержанием 0,6...0,7 % С твердость мартенсита достигает ~60 HRC. Высокая твердость мартенсита объясняется большими внутренними напряжениями в растянутой решетке Fea, созданием микро- и субмикроскопической неоднородности строения с равномерным ее распределением по объему, т. е. большим числом нарушений кристаллического строения.
В случае охлаждении аустенита со скоростями меньшими критической вместо мартенсита в интервале температур 720–550оС образуются феррито-цементитные смеси (рисунок 8.3), получившие название перлит, сорбит, троостит (П, С, Т). По мере увеличения скорости охлаждения дисперсность смеси возрастает, что приводит к повышению твердости и прочности. Наиболее грубой смесью является перлит, максимальной дисперсностью обладает троостит.
Внутренние напряжения, возникающие при закалке. Поверхности раздела кристаллитов мартенсита – представляют собой труднопреодолимые препятствия для скольжения дислокаций при деформации кристалла. Перемещению дислокаций тормозят находящиеся в решетке мартенсита атомы углерода, создающие статические искажения решетки (напряжения III рода). Все это определяет высокую твердость структуры закаленной стали – мартенсита. С увеличением содержания углерода в мартенсите наряду с повышением твердости возрастает и хрупкость.
Мартенситное превращение, происходящее при закалке стали, приводит к увеличению удельного объема, что является одной из основных причин возникновения больших внутренних (структурных) напряжений II рода, вызывающих деформацию изделий или даже появление трещин. Перепад температур по сечению закаливаемого материала приводит к образованию термических внутренних напряжений (I рода). Эти напряжения, возникающие при закалке (структурные и термические), тем больше, чем выше температура закалки и скорость охлаждения в мартенситном интервале температур (Мн–Мк).
Дата добавления: 2018-11-25; просмотров: 2240;